Физика металлов и металловедение, 2022, T. 123, № 12, стр. 1267-1274
Микроструктура и электропроводность медно-алюминиевых композитов, полученных ротационной ковкой
С. О. Рогачев a, b, Р. В. Сундеев a, c, *, В. А. Андреев b, d, Н. В. Андреев a, Н. Ю. Табачкова a, e, Н. О. Короткова a
a Национальный исследовательский технологический университет “МИСиС”
119049 Москва, Ленинский просп., 4, Россия
b Институт металлургии и материаловедения им. А.А. Байкова РАН
119334 Москва, Ленинский просп., 49, Россия
c РТУ МИРЭА
119454 Москва, просп. Вернадского, д. 78, Россия
d ООО “Промышленный центр МАТЭК-СПФ”
117449 Москва, ул. Карьер, 2А/1, Россия
e Институт общей физики им. А.М. Прохорова РАН
119991 Москва, ул. Вавилова, д. 38, Россия
* E-mail: sundeev55@yandex.ru
Поступила в редакцию 30.05.2022
После доработки 31.08.2022
Принята к публикации 03.10.2022
- EDN: BMKCMV
- DOI: 10.31857/S0015323022600551
Аннотация
Методом электронной микроскопии исследована эволюция микроструктуры медно-алюминиевых композитов при увеличении степени обжатия холодной ротационной ковкой и измерена их электропроводность. Изучено влияние армирования медно-алюминиевых композитов стальными волокнами на электропроводность.
ВВЕДЕНИЕ
Сегодня для электротехники актуальной является задача создания композиционного материала, обладающего одновременно повышенной прочностью, запасом пластичности, электропроводностью и малой плотностью. В качестве основы для такого материала предложены композиты на медно/алюминиевой основе, а в качестве метода их изготовления – ротационная ковка [1–6].
Ротационная ковка является одним из методов больших пластических деформаций, наиболее подходящих для производства изделий в виде длинномерных прутков или проволок [7–10]. Благодаря достижению очень высоких степеней деформации в ходе обжатия заготовки ротационной ковкой, в обрабатываемой металлической заготовке формируется ультрамелкозернистая структура и достигается комплекс высоких механических свойств [4].
В работах [5, 6, 11] медно/алюминиевые композиты разного дизайна подвергали ротационной ковке с разными степенями обжатия. В качестве компонентов композита в основном использовали чистые медь и алюминий. Целесообразно применение в качестве одного из компонентов композита алюминиевых сплавов, обладающих большей прочностью по сравнению с чистым алюминием. Например, в работе [4] ротационной ковкой были получены композиционные образцы “алюминиевый сплав Д16/медь” с прочностью около 400 МПа. Учитывая, что переменный электрический ток высокой частоты преимущественно идет вблизи поверхности проводника, представляет интерес создания композита “медь/алюминиевый сплав”, т.е. с обратным порядком расположения компонентов, ввиду более высокой электрической проводимости меди по сравнению с алюминием. В то же время формирование ультрамелкозернистой структуры в компонентах такого композиционного проводника может повлиять на электропроводящие свойства.
Поэтому целью работы было изучение эволюции микроструктуры медно-алюминиевых композитов при увеличении степени обжатия ротационной ковкой и оценка их электропроводности.
МАТЕРИАЛЫ И МЕТОДИКИ ИССЛЕДОВАНИЯ
Композиционная заготовка представляла собой стержень из алюминиевого сплава Д16 (Al–Cu–Mg) диаметром 12 мм, помещенный в оболочку из чистой меди (99.97%) с внешним диаметром 20 мм. С целью изучения влияния на электропроводящие свойства дополнительного стального компонента в составе композита, часть композиционных заготовок была армирована волокнами из стали типа 12Х18Н10Т диаметром 0.7 мм в количестве 5 шт., уложенными продольно между оболочкой и стержнем на одинаковом расстоянии друг от друга [12].
Начальная длина заготовок составила 200 мм. Перед сборкой заготовки ее компоненты подвергали смягчающему отжигу в вакууме: при температуре 400°С с выдержкой 2 ч для алюминиевого сплава и при температуре 500°С с выдержкой 40 мин для меди. Сталь использовали в состоянии поставки (твердость 258 HV).
Ковку заготовок осуществляли на трех модернизированных двухбойковых ротационно-ковочных машинах РКМ последовательно с начального диаметра 20 мм до конечного диаметра 2.5 мм при комнатной температуре. Между проходами осуществляли периодический низкотемпературный отжиг заготовки при 180°С для снятия наклёпа. Первый отжиг проводили после достижения диаметра заготовки 5.0 мм; второй – 3.5 мм. Продолжительность каждого отжига 1 ч. Более подробно технология изготовления композиционных образцов описана в работе [12]. Для исследований были взяты образцы с диаметрами 5.0; 3.5 и 2.5 мм (рис. 1).
Рис. 1.
Поперечный шлиф композиционного образца Cu/Al после ротационной ковки до диаметра 2.5 мм (а) и фрагмент поперечного сечения композиционного образца Cu/Fe/Al после ротационной ковки до диаметра 5.0 мм (б) (СЭМ).
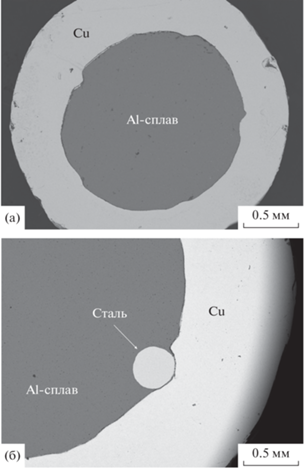
Микроструктуру компонентов композиционных образцов (медной оболочки и алюминиевого стержня) в продольном направлении после разных степеней обжатия изучали методом просвечивающей электронной микроскопии (ПЭМ) на микроскопе JEM-2100 с энергодисперсионным микроанализатором (EDS). Подготовку проб для исследования микроструктуры проводили на сканирующем ионном микроскопе Strata 201 SIMSmapIII × P с помощью галлиевой жидкометаллической ионной пушки.
Удельную электрическую проводимость композиционных образцов измеряли согласно ГОСТ 7229–76 с использованием цифрового миллиомметра GOM-802 (GP + RS).
РЕЗУЛЬТАТЫ И ИХ ОБСУЖДЕНИЕ.
Влияние ротационной ковки на микроструктуру. Структура компонентов композиционного материала (меди и алюминия) в исходном отожженном состоянии изучена ранее [4, 13]. Оба компонента характеризуются рекристаллизованной структурой со средним размером зерна 36 мкм в меди и 3 мкм в алюминии. В структуре алюминиевого сплава присутствовали частицы типа Al2Cu, Al2CuMg, Al20Cu2Mn3 с преимущественным размером 100–500 нм. Кроме этого присутствовали многочисленные частицы Al2CuMg со средним размером 3.5 мкм, а также отдельные (не более 2 об. %) крупные (5–20 мкм) частицы типа Al6(CuFeMn) или (CuFeMn)3Si2Al15. Все указанные частицы являются типичными для сплава Д16 [14, 15].
По данным ПЭМ и EDS ротационная ковка композиционного образца до диаметра 5.0 мм привела к формированию в медной оболочке ячеисто-субзеренной структуры с высокой плотностью дислокаций с размером ячеек 0.15–0.40 мкм и вытянутыми субзернами с минимальной шириной до 0.15–1 мкм (рис. 2а, 2б).
Рис. 2.
Микроструктура медной оболочки (а, б) и алюминиевого стержня (в–е) композиционного образца после ротационной ковки до диаметра 5.0 мм (ПЭМ): а, б, в, д, е – светлопольные изображения; г – темнопольное изображение в рефлексе типа (200)Al.
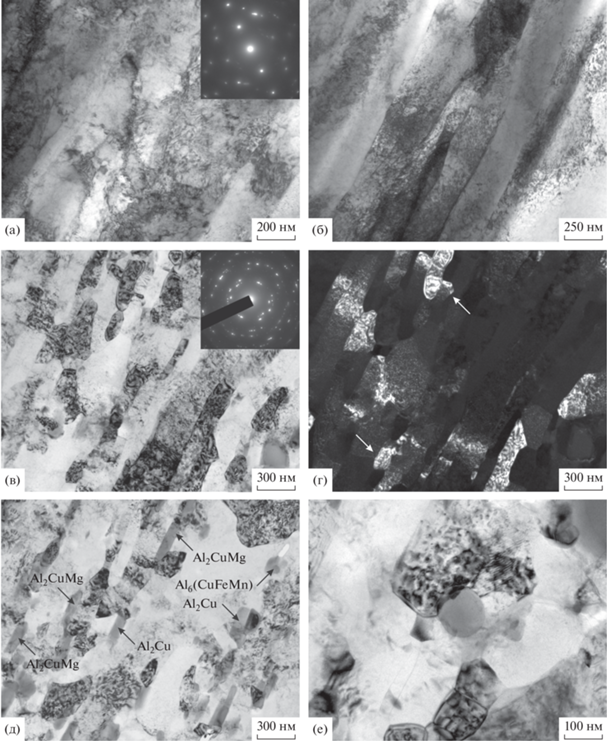
В алюминиевом стержне сформировалась ультрамелкозернистая зеренно-субзеренная структура, вытянутая вдоль направления оси заготовки (рис. 2в–2е). Угол разориентировки структурных элементов определяли качественно на основе анализа нескольких темнопольных изображений.
Преобладающая ширина вытянутых субзерен, разделенных малоугловыми границами, составила 0.13–0.35 мкм (рис. 2в, 2г), а диаметр равноосных кристаллитов с больше- и малоугловыми границами – 0.08–0.25 мкм (рис. 2г, 2е, указаны белыми стрелками). На наличие ультрамелкозернистой структуры в алюминиевом сплаве указывают и кольцевые электронограммы. Кольца образованы как точечными рефлексами, свидетельствующими о большеугловой разориентировке, так и рефлексами, имеющими азимутальное размытие, свидетельствующими о наличии малоугловой разориентировки. В структуре алюминиевого сплава выявлены многочисленные частицы типа Al2Cu, Al2CuMg и Al6(CuFeMn) с преимущественной длиной 0.10–0.40 мкм и шириной 0.05–0.10 мкм (рис. 2д; указаны черными стрелками). Эти частицы имели выраженную направленность вдоль вытянутых субзерен. Химический состав частиц приведен в табл. 1. Кроме этого, встречаются частицы овальной формы или неправильной формы размером 0.10–1 мкм. Отметим, что частицы разных фаз могли иметь одинаковые морфологию и размеры и наоборот; в связи с чем разделить частицы разных фаз в структуре по их морфологии/размерам невозможно.
Таблица 1.
Результаты химического анализа выборочных включений в структуре алюминиевого сплава после ротационной ковки с разным обжатием (по данным ПЭМ с EDS)
Номер спектра | Элемент, ат. % | Соединение | |||||
---|---|---|---|---|---|---|---|
Al | Cu | Mg | Mn | Fe | Si | ||
Диаметр 5.0 мм | |||||||
1 | 67.3 | 15.3 | 0 | 2.5 | 14.9 | 0 | Al6(CuFeMn) |
2 | 84.4 | 15.6 | 0 | 0 | 0 | 0 | Al2Cu |
3 | 58.1 | 20.2 | 21.7 | 0 | 0 | 0 | Al2CuMg |
4 | 67.1 | 16.6 | 0 | 16.4 | 0 | 0 | Al20Cu2Mn3 |
Диаметр 3.5 мм | |||||||
1 | 71.4 | 17.5 | 0 | 8.7 | 1.5 | 1.0 | Al6(CuFeMn) |
2 | 68.7 | 15.8 | 15.4 | 0 | 0 | 0 | Al2CuMg |
3 | 80.3 | 12.3 | 0 | 7.4 | 0 | 0 | Al20Cu2Mn3 |
Диаметр 2.5 мм | |||||||
1 | 62.7 | 17.3 | 0 | 3.6 | 16.5 | 0 | Al6(CuFeMn) |
2 | 82.1 | 17.9 | 0 | 0 | 0 | 0 | Al2Cu |
3 | 66.1 | 16.6 | 16.7 | 0 | 0.6 | 0 | Al2CuMg |
4 | 84.6 | 8.5 | 0 | 6.2 | 0.7 | 0 | Al20Cu2Mn3 |
При уменьшении диаметра композиционного образца до 3.5 мм (с промежуточным отжигом при 180°С) в медной оболочке вытянутые субзерна заняли преимущественно весь объем образца (рис. 3а). В то же время в некоторых областях структуры сформировались кристаллиты с формой близкой к равноосной, а их размер составил 0.15–0.40 мкм (рис. 3б). Такие кристаллиты образовались, по-видимому, при пересечении нескольких систем субзерен в результате действия локальных деформаций разных направлений – сдвиговых и радиальных. Структура алюминиевого стержня не претерпела дальнейших изменений (рис. 3в, 3г, табл. 1).
Рис. 3.
Микроструктура медной оболочки (а, б) и алюминиевого стержня (в, г) композиционного образца после ротационной ковки до диаметра 3.5 мм (ПЭМ): а–г – светлопольные изображения. Стрелками указаны интерметаллидные частицы.
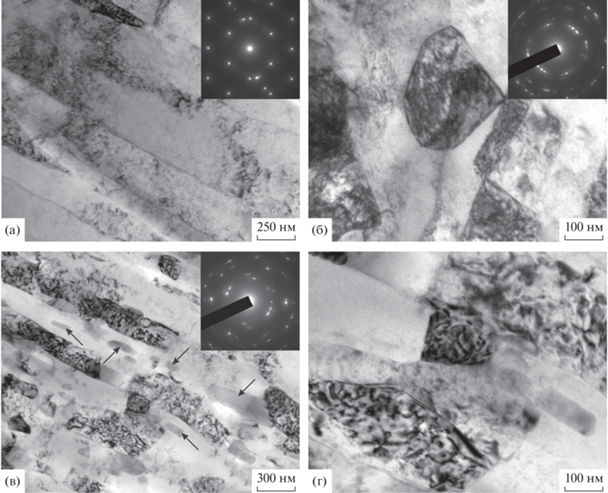
Подобная структура медной оболочки и алюминиевого стержня сохраняется при дальнейшем обжатии композиционного образца до диаметра 2.5 мм (с промежуточным отжигом при 180°С) (рис. 4, табл. 1).
Рис. 4.
Микроструктура медной оболочки (а, б) и алюминиевого стержня (в, г) композиционного образца после ротационной ковки до диаметра 2.5 мм (ПЭМ): а–в – светлопольные изображения; г – темнопольное изображение в рефлексе типа (200)Al. Черными стрелками указаны интерметаллидные частицы, белой – равноосный кристаллит.
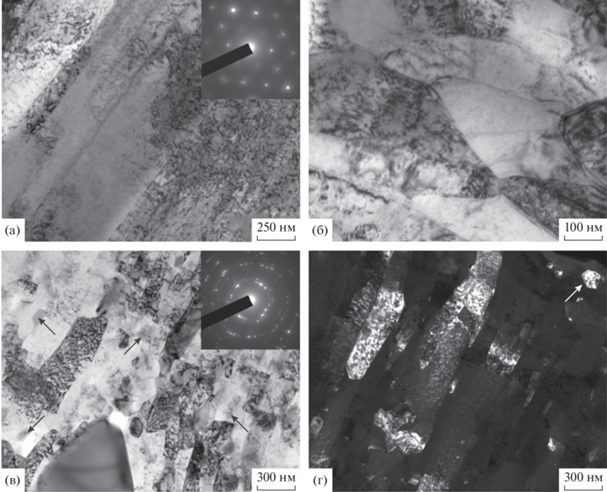
Из анализа табл. 1 видно, что данные EDS для частиц в структуре алюминиевого сплава композита после разных степеней обжатия несколько отличались. Например, в структуре алюминиевого сплава в композите диаметром 3.5 мм не выявлена фаза Al2Cu. Однако это, по-видимому, объясняется методологическими особенностями проведения химического анализа, а не свидетельствует об изменении фазового состава сплава в процессе ковки. Учитывая очень малый (5 × 15 мкм2) размер пробы для ПЭМ, а также случайный характер проведения химического анализа, некоторые частицы могут либо не попасть в поле зрения электронного микроскопа, либо не учитываться в анализе. Кроме этого, состав частиц отличается от стехиометрического. Причиной этого является то, что несколько частиц разного состава могут находиться рядом или друг под другом, в результате чего анализ EDS покажет усредненный химический состав.
Полученные результаты показывают, что эволюция структуры компонентов композита при его обжатии отличается для композитов алюминиевый сплав/медь и медь/алюминиевый сплав (т.е. с обратным расположением компонентов) [4]. Так, в композите медь/алюминиевый сплав диаметром 5.0 мм сформировавшаяся структура в алюминиевом стержне не меняется при дальнейшем обжатии, в то время как в алюминиевой оболочке композита алюминиевый сплав/медь наблюдалось принципиальное изменение типа структуры при переходе от диаметра 5.3 мм к диаметру 2.4 мм. При этом структура алюминиевой оболочки композита алюминиевый сплав/медь диаметром 2.4 мм так же, как и структура алюминиевого стержня в композите медь/алюминиевый сплав диаметром 5.0–2.5 мм, была представлена вытянутыми субзернами и частицами, но содержала очень малую долю равноосных структурных элементов. Кроме этого, сформировавшаяся в медном стержне композита алюминиевый сплав/медь диаметром 2.4 мм структура была в основном ячеисто-субзеренной, и тем самым отличалась от структуры медной оболочки композита медь/алюминиевый сплав диаметром 2.5 мм, представленной вытянутыми субзернами и равноосными кристаллитами.
Таким образом, независимо от материала компонентов композитов, изменения структуры в оболочке обоих композитов при увеличении обжатия более выражены, чем в стержне композита. В ряде работ на основе компьютерного моделирования методом конечных элементов показано, что в результате обжатия ротационной ковкой в середине заготовки деформация больше, чем на поверхности [16]. По-видимому, в этих работах не учитывалась сдвиговая составляющая деформации, которая возникает в момент соприкосновения бойка ротационно-ковочной машины с поверхностью вращающейся заготовки. Результаты эволюции микроструктуры композита, полученные в данной работе, а также в других работах [4], могут объясняться большими сдвиговыми деформациями в поверхностных слоях обрабатываемой заготовки в ходе ротационной ковки, в то время как в центре образца будет велика радиальная деформация.
Влияние ротационной ковки на электропроводность. Результаты измерения электрической проводимости композиционных образцов приведены на рис. 5.
Рис. 5.
Изменение удельного электрического сопротивления (а) и удельной электрической проводимости (б) композиционных образцов после ротационной ковки до разных диаметров.
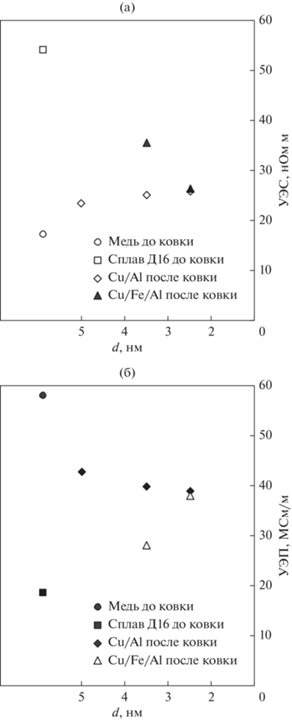
Видно, что удельная электрическая проводимость композита медь/алюминиевый сплав после ротационной ковки до диаметра 5.0 мм достигает 42.70 МСм/м, что составляет 73.6% от удельной электрической проводимости отожженной меди (58.00 МСм/м) и в ~2.3 раза превышает удельную электрическую проводимость отожженного сплава Д16 (18.52 МСм/м). С уменьшением диаметра композиционного образца до 3.5 и 2.5 мм удельная электрическая проводимость слабо уменьшается, соответственно, до 68.7 и 67% от удельной электрической проводимости отожженной меди. Низкая чувствительность электрической проводимости чистой меди при комнатной температуре к дефектам масштаба дислокаций и границ зерен отмечена в работе [17]. Это связано с малой длиной волны электрона при комнатной температуре. Таким образом, значение удельной электрической проводимости композита находится между значениями удельной электрической проводимости медной оболочки и алюминиевого стержня.
Наличие дополнительных стальных волокон между оболочкой и стержнем в композиционном образце диаметром 3.5 мм отрицательно влияет на удельную электрическую проводимость, понижая ее до 28.11 МСм/м, что составляет 48.5% от удельной электрической проводимости отожженной меди. Однако с уменьшением диаметра композита до 2.5 мм удельная электрическая проводимость резко повышается до 65% от удельной электрической проводимости отожженной меди. Это может быть связано с тем, что при обжатии композита диаметром 3.5 мм до диаметра 2.5 мм происходит утонение стальных волокон и их обрывы [12]. В результате непрерывные волокна трансформируются в дискретные, тем самым оказывая меньшее отрицательное влияние на электрическую проводимость.
ВЫВОДЫ
Холодная ротационная ковка композиционного образца медь/алюминиевый сплав Д16 с диаметра 20 мм до диаметра 5.0 мм привела к формированию в медной оболочке ячеисто-субзеренной структуры с высокой плотностью дислокаций. В алюминиевом стержне сформировалась ультрамелкозернистая вытянутая зеренно-субзеренная структура с частицами интерметаллидных фаз нано- и субмикронного размера. Формирование подобной структуры в компонентах композиционной заготовки является следствием высоких степеней сдвиговой деформации при ротационной ковке.
При уменьшении диаметра композиционного образца до 3.5 и 2.5 мм (с промежуточными отжигами при 180°С) структура алюминиевого сплава не претерпевает дальнейших изменений, а в медной оболочке увеличивается доля вытянутых субзерен и формируются отдельные мелкие равноосные кристаллиты.
Композиционные образцы медь/алюминиевый сплав Д16 после ротационной ковки характеризуются высокой удельной электрической проводимостью, которая варьируется от 73.6 до 67% от удельной электрической проводимости отожженной меди при уменьшении диаметра композита с 5.0 до 2.5 мм. Наличие дополнительных стальных волокон между оболочкой и стержнем в композиционном образце отрицательно влияет на удельную электрическую проводимость, понижая ее до 48.5–65% от удельной электрической проводимости отожженной меди.
Исследование выполнено при финансовой поддержке РФФИ и Правительства Москвы в рамках научного проекта (грант № 21-32-70015). Исследование структуры выполнено на оборудовании ЦКП “Материаловедение и металлургия” при финансовой поддержке РФ в лице Минобрнауки (№ 075-15-2021-696). Благодарим магистранта Е.В. Николаева и инженера А.А. Токаря за помощь в изготовлении образцов.
Список литературы
Kim I.K., Hong S.I. Effect of heat treatment on the bending behavior of tri-layered Cu/Al/Cu composite plates // Mater. & Design. 2013. V. 47. P. 590–598.
Ahmed N. Extrusion of copper clad aluminum wire // J. Mechan. Working Techn. 1978. V. 2. P. 19–32.
Mitani Y., Balmori H. Fabrication of a Cu–Al Composite Wire and its Mechanical Properties (Part I) // Proceedings of the 6th International Conference Strength of Metals and Alloys (ICSMA 6), Melbourne, Australia, 1982. P. 983–988.
Rogachev S.O., Andreev V.A., Yusupov V.S., Bondareva S.A., Hatkevich V.M., Nikolaev E.V. Effect of rotary forging on microstructure evolution and mechanical properties of aluminum alloy / copper bimetallic material // Met. Mater. International. 2022. V. 28. P. 1038–1046.
Kocich R., Kunčická L., Král P., Strunz P. Characterization of innovative rotary swaged Cu–Al clad composite wire conductors // Mater. & Design. 2018. V. 160. P. 828–835.
Kocich R., Macháčková A., Kunčická L., Fojtík F. Fabrication and characterization of cold-swaged multilayered Al–Cu clad composites // Mater. Design. 2015. V. 71. P. 36–47.
Андреев В.А., Юсупов В.С., Перкас М.М., Просвирнин В.В., Шелест А.Е., Прокошкин С.Д., Хмелевская И.Ю., Коротицкий А.В., Бондарева С.А., Карелин Р.Д. Механические и функциональные свойства промышленных полуфабрикатов из сплава ТН-1, полученных теплой ротационной ковкой и РКУП // Деформация и разрушение материалов. 2017. № 4. С. 43–48.
Klumpp A., Kauffmann A., Seils S., Dietrich S., Schulze V. Influence of cold rotary swaging on microstructure and uniaxial mechanical behavior in alloy 718 // Metall. Mater. Trans. A. 2021. V. 52. P. 2021–4331.
Панов Д.О., Смирнов А.И., Перцев А.С. Структурообразование метастабильной аустенитной стали при холодной пластической деформации методом радиальной ковки // ФММ. 2019. Т. 120. № 2. С. 198–204.
Симонов М.Ю., Симонов Ю.Н., Шайманов Г.С. Структура, динамическая трещиностойкость и микромеханизм роста трещин в трубных заготовках после деформационно-термической обработки // ФММ. 2018. Т. 119. № 1. С. 54–62.
Kunčická L., Kocich R. Optimizing electric conductivity of innovative Al-Cu laminated composites via thermomechanical treatment // Mater. & Design. 2022. V. 215. P. 110441.
Рогачев С.О., Сундеев Р.В., Андреев В.А., Юсупов В.С., Хаткевич В.М., Николаев Е.В., Бондарева С.А. Механическое поведение медно-алюминиевого плакированного композита в процессе ротационной ковки // Деформация и разрушение материалов. 2021. № 11. С. 15–22.
Рогачев С.О., Андреев В.А., Юсупов В.С., Хаткевич В.М., Николаев Е.В., Перкас М.М., Бондарева С.А. Структура и механические свойства биметаллических проводов “алюминиевый сплав/медь” после ротационной ковки” // Металловедение и термич. обр. металлов. 2020. № 12. С. 26–31.
Арчакова 3.Н., Балахонцев Г.А., Басова И.Г. Структура и свойства полуфабрикатов из алюминиевых сплавов: справочник. М.: Металлургия, 1984. 408 с.
Мондольфо Л.Ф. Структура и свойства алюминиевых сплавов. М.: Металлургия, 1979. 640 с.
Асфандияров Р.Н., Рааб Г.И. Исследование метода ротационного обжатия в условиях больших деформаций // Вестник УГАТУ. 2016. Т. 20. № 3. С. 3–6.
Фаизов И.А., Мулюков Р.Р., Аксенов Д.А., Фаизова С.Н., Землякова Н.В., Cardoso K.R., Zeng Y. Растворение частиц вторых фаз в низколегированном медном сплаве системы Cu–Cr–Zr при обработке методом равноканального углового прессования // Письма о материалах. 2018. Т. 8. № 1(29). С. 110–114.
Дополнительные материалы отсутствуют.
Инструменты
Физика металлов и металловедение