Физика металлов и металловедение, 2022, T. 123, № 12, стр. 1275-1282
Повышение усталостной долговечности ЭЛС-соединения 3D-напечатанного сплава Ti–6Al–4V путем ультразвуковой электроимпульсной ударной обработки
О. Б. Перевалова a, *, А. В. Панин b, Е. Н. Боянгин c, М. С. Казаченок a, С. А. Мартынов a
a Институт физики прочности и материаловедения СО РАН
634055 Томск, просп. Академический, 2/4, Россия
b Национальный исследовательский политехнический университет
634050 Томск, просп. Ленина, 30, Россия
c Томский научный центр СО РАН
634055 Томск, просп. Академический, 10/4, Россия
* E-mail: perevalova52@mail.ru
Поступила в редакцию 11.07.2022
После доработки 25.10.2022
Принята к публикации 28.10.2022
- EDN: HLKNEN
- DOI: 10.31857/S001532302260085X
Аннотация
Методами рентгеноструктурного анализа показано, что ультразвуковая электроимпульсная ударная обработка образцов со сварным соединением сплава Ti–6Al–4V, полученного по электронно-лучевой проволочной аддитивной технологии, с использованием ударника из твердого сплава (Co–WC) приводит к увеличению в поверхностных слоях объемной доли β-фазы и образованию интерметаллидных фаз систем Ti–Co и Ti–Co–Al, увеличению микротвердости, а также увеличению в 1.5 раза усталостной долговечности по сравнению с исходным необработанным состоянием. После обработки в поверхностных слоях образца возникают упругие макронапряжения сжатия, причем в зоне основного материала они становятся больше, чем в зоне шва. Увеличение усталостной долговечности образцов со сварным соединением после обработки обусловлено значительным упрочнением поверхностных слоев за счет образования интерметаллидных фаз. Разрушение образца со сварным соединением после обработки происходит в зоне шва. В поверхностных слоях образца излом характеризуется как хрупкий, вдали от поверхности – преимущественно, как ямочный вязкий.
ВВЕДЕНИЕ
Сварные швы металлов и сплавов являются предпочтительным местом образования трещин при усталостных испытаниях [1]. Для увеличения усталостной долговечности образцов со сварным соединением высокопрочных титановых сплавов используется ультразвуковая электроимпульсная ударная обработка [2], особенно в титановых сплавах с высоким содержанием β-фазы (ВТ23). Увеличение усталостной долговечности обработанного сплава сопровождается увеличением вязкой составляющей на фрактографии излома. Авторы работы [2] полагают, что факторами, определяющими увеличение усталостной долговечности образцов титановых сплавов после ультразвуковой электроимпульсной ударной обработки, являются образование нанокристаллической и аморфной структур в поверхностных слоях, а также нанокристаллических прослоек α"-фазы в β-фазе вследствие фазового превращения β → α". Известно [3], что образование вязкого ямочного рельефа на поверхности излома происходит по механизму слияния пор, образующихся на межфазных границах раздела между частицей и матрицей. В связи с этим авторы [2] полагают, что образование частиц α"-фазы в β-фазе титановых сплавов при ультразвуковой электроимпульсной ударной обработке приводит к увеличению вязкой (ямочной) составляющей на фрактограмме излома, при этом скорость движения трещин уменьшается.
На место зарождения трещины в образце со сварным соединением влияют тип и величина упругих плоских макронапряжений, а также прочностные свойства сплава. Макронапряжения сжатия в образце и высокие прочностные свойства задерживают начало образования трещины, тем самым увеличивая усталостную долговечность [2]. Ультразвуковая ударная обработка приводит к снятию растягивающих макронапряжений в сварных швах и созданию в их поверхностных слоях макронапряжений сжатия [4]. В сочетании с высокочастотным электроимпульсным воздействием ультразвуковая ударная обработка или ультразвуковая обработка с током (УЗОТ) повышает глубину и интенсивность модификации [2], при этом добавляется электроискровое легирование обрабатываемой поверхности металлом ударного бойка [5].
Сварные швы образцов сплава Ti–6Al–4V, напечатанных с использованием электронно-лучевой проволочной аддитивной технологии, характеризуются повышенными значениями микротвердости и макронапряжений растяжения по сравнению с основным металлом [6]. Микроструктура шва принципиально не отличается от микроструктуры основного металла, однако поперечные размеры пластин α-фазы меньше, чем в основном металле, и внутри пластин присутствует нанокристаллическая α"-фаза.
Ранее авторами статьи было показано, что УЗОТ с использованием стального бойка значительно изменяет микроструктуру и фазовый состав как основного металла [7], так и металла шва [8]. Происходит легирование поверхностных слоев железом, образование под поверхностным нанокристаллическим оксидным слоем слоев со структурой β-фазы и фазы Ti4Fe и измельчение α + β-структуры в нижележащих слоях и, как следствие, увеличение микротвердости.
В настоящей работе поставлена задача исследовать влияние УЗОТ с использованием бойка из твердого сплава (Co–WC) на фазовый состав, микротвердость и усталостную долговечность напечатанного сплава Ti–6Al–4V.
МАТЕРИАЛЫ И МЕТОДЫ ИССЛЕДОВАНИЯ
Заготовки из сплава Ti–6Al–4V были получены на установке 6Е400 (ООО “НПК ТЭТА”) с использованием электронно-лучевой проволочной аддитивной технологии [9]. Технология электронно-лучевой сварки (ЭЛС) описана в разд. Материалы исследования в работе [6].
На рис. 1 представлено изображение микроструктуры поперечного сечения образца со сварным швом, наблюдаемое методом оптической металлографии. Выделяются три зоны: зона сплавления (ЗС), или зона шва, зона термического влияния (ЗТВ), зона основного металла (ОМ). В зонах сплавления и термического влияния наблюдаются столбчатые первичные β-зерна с поперечным размером около 1 мм. Основной металл, как показано методами ПЭМ [6], имеет пластинчатую структуру основной α-фазы с прослойками вторых фаз (β и α") по границам зерен. Фазовый состав зернограничных прослоек зависит от локальной концентрации ванадия. Экспериментально α"-фаза в прослойках наблюдается, как правило, при концентрации ванадия менее 9 ат. %, β + α" – при концентрации ванадия от 17 до 25 ат. %. Зависимость образования фаз β или α″ от концентрации ванадия в сплаве Ti–6Al–4V показана также в работе [10] в рамках теории функционала плотности.
Рис. 1.
Оптическое изображение микроструктуры поперечного сечения напечатанного образца сплава Ti–6Al–4V со сварным швом: ЗС – зона сплавления, ЗТВ – зона термического влияния, ОМ – зона основного металла [6].
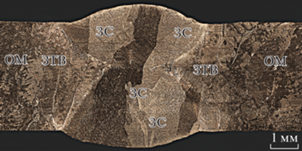
УЗОТ образцов со сварным соединением проводили на комплексе оборудования [7]. Материалом ударного бойка был высокопрочный сплав Co–WC следующего химического состава (вес. %): 11.47% Co, 78.07% W, 8.60% C, 1.86% O. Направление движения ударника было перпендикулярно поверхности образца. Обрабатывали обе поверхности образца со сварным швом.
Микроструктуру поверхности образцов после УЗОТ, а также микроструктуру в поперечном сечении образцов изучали в оптическом микроскопе AXIOVERT-200MAT, фрактографию излома разрушенных образцов после циклических испытаний – в сканирующем электронном микроскопе EVO-50.
Фазовый состав образцов определяли с использованием рентгеновского дифрактометра ДРОН-7. Рентгеноструктурный анализ (РСА) поверхности образцов сплава как до, так и после УЗОТ проводили в CоKα-излучении по симметричной геометрии Брэгга–Брентано [11]. Оценку упругих плоских макронапряжений σ1 + σ2 [12] в образцах после УЗОТ проводили с использованием пика 211, за эталон принимали исходный 3D-напечатанный образец.
Микротвердость по Виккерсу измеряли с использованием твердомера ПМТ-3 при нагрузке 0.4905Н.
Циклические испытания проводили на сервогидравлической испытательной машине Biss UTM 150, в режиме малоцикловой усталости (максимальное напряжение 600 МПа, минимальное – 60 МПа, асимметрия цикла составляла 0.1, частота 20 Гц). Рабочая часть образцов имела размеры 2 × 4 × 40 мм. Сварной шов располагался в центре рабочей части образцов.
Удельное сопротивление образцов определяли четырехзондовым методом [13], рассчитывая по формуле ρunit = U2πL/I, где U – напряжение на центральных зондах, L = 0.0022 м – расстояние между зондами, I – сила тока, подаваемого на крайние зонды. Для измерений использовали источник постоянного тока Б5-48, с шагом по току 0.01 А, и микровольтметр В7-38 с разрешением 10 мкВ.
РЕЗУЛЬТАТЫ И ОБСУЖДЕНИЕ
Метод оптической металлографии. УЗОТ поверхности образцов сплава как в зоне основного металла, так и в зоне шва приводит к образованию кратеров, что свидетельствует об оплавлении поверхностного слоя (рис. 2). В поперечном сечении образца на поверхности также наблюдается оплавленный слой (рис. 3). Толщина этого слоя в зоне основного металла вдвое больше, чем в зоне шва, и достигает 10 мкм.
Рис. 3.
Оптические изображения микроструктуры поперечного сечения образца после УЗОТ в зонах основного металла (а) и шва (б).
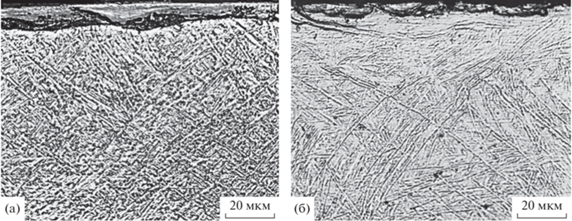
Микроструктура под оплавленным слоем на всей площади поперечного сечения образца как в зоне шва, так и в зоне основного металла является пластинчатой, что является типичным для напечатанного сплава Ti–6Al–4V.
Рентгеноструктурное исследование микроструктуры образца в зонах основного металла и шва. Участки дифрактограмм образца сплава со сварным швом до и после УЗОТ в зоне основного металла представлены на рис. 4, в зоне шва – на рис. 5. На дифрактограмме исходного необработанного образца в зоне основного металла присутствуют пики только α-фазы (рис. 4а). Однако методом ПЭМ показано, что β-фаза присутствует [6]. Отсутствие пика 011β или его малая интенсивность свидетельствуют о том, что объемная доля β-фазы не превышает 3%. Как правило, объемная доля β-фазы в образцах сплава Ti–6Al–4V, напечатанных с использованием электронно-лучевой проволочной аддитивной технологии, не превышает 5%.
Рис. 4.
Участки дифрактограмм напечатанных образцов сплава Ti–6Al–4V в зоне основного металла до (а) и после УЗОТ (б).
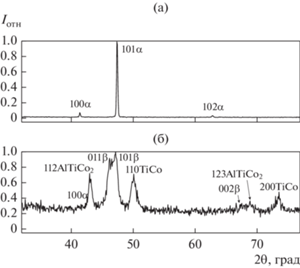
Рис. 5.
Участки дифрактограмм напечатанных образцов сплава Ti–6Al–4V в зоне шва до (а) и после УЗОТ (б).
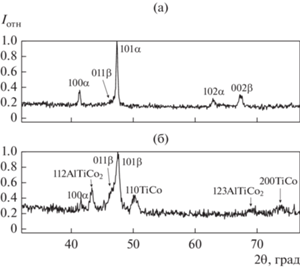
В зоне шва необработанного образца пик 101 α-фазы становится асимметричным слева, что свидетельствует о появлении пика 011 β-фазы (рис. 5а). Объемная доля β-фазы, оцененная по пику 011, в зоне шва составляет 7% (табл. 1). Кроме того, на дифрактограмме зоны шва появляется пик 002 β-фазы с межплоскостным расстоянием, равным 0.161 нм. Такое же значение межплоскостного расстояния имеет пик 113 TiO2 (брукит). В работе [6] методами ПЭМ было показано, что на поверхности образца в зоне шва возникает слой оксидов титана. Там же отмечали увеличение объемной доли β-фазы в металле шва по сравнению с основным металлом в напечатанном сплаве Ti–6Al–4V.
Таблица 1.
Параметры кристаллической решетки α-фазы (а и с) и их отношение (с/a), объемные доли β + α"-фаз (δβ + α") и интерметаллидных фаз системы Ti–Co (δTi–Co), параметр решетки β-фазы (аβ)
Состояние образцов решетки, нм | Место съемки | Параметры | с/a | δβ+α″, % | δTi–Co, % | аβ, нм | |
---|---|---|---|---|---|---|---|
а | с | ||||||
Исходный | Основной металл | 0.2923 | 0.4676 | 1.599 | 3 | – | 0.3217 |
Шов | 0.2922 | 0.4662 | 1.595 | 7 | – | 0.3211 | |
Исх + УЗОТ | Основной металл | 0.2929 | 0.4677 | 1.597 | 25 | 42 | 0.3235 |
Шов | 0.2933 | 0.4644 | 1.583 | 7 | 38 | 0.3215 |
Параметры кристаллических решеток α- и β-фаз в основном металле и в металле шва образца напечатанного сплава Ti–6Al–4V практически не различаются (табл. 1). После УЗОТ параметр решетки а α-фазы возрастает как в основном металле так и в зоне шва. Поскольку параметр а α-фазы зависит от концентрации элементов замещения, то его увеличение после УЗОТ вероятнее всего обусловлено увеличением концентрации кобальта в твердом растворе на основе α-Ti. Использование сплава Co–WC в качестве материала ударника при УЗОТ приводит к легированию поверхностных слоев сплава Ti–6Al–4V кобальтом, который является β-стабилизатором [14, 15]. В двухфазных (α + β)-сплавах системы Ti–Co (2–4 вес. % Co) уменьшение объемной доли β-фазы сопровождается незначительными увеличением параметра а и уменьшением параметра с α-фазы [16]. Это означает, что в твердом растворе на основе α-Ti возрастает концентрация кобальта. Предельная концентрация кобальта в α-фазе составляет 0.8 ат. %. Однако значительное уменьшение объемной доли β-фазы в шве обработанного образца по сравнению с основным металлом обусловлено прежде всего тем, что из-за меньшей глубины оплавления объем поверхностного слоя, легированного кобальтом, меньше, чем в основном металле. Объемная доля интерметаллидных фаз, образующихся при эвтектоидном распаде первичной β-фазы, также в шве меньше, чем в основном металле, что обусловлено меньшим объемом поверхностного слоя, легированного кобальтом.
На рис. 4 видно, что в основном металле пик 101 α-фазы после УЗОТ смещается в сторону меньших углов дифракции 2θ. Смещение пика обусловлено прежде всего возникновением упругих плоских макронапряжений сжатия. Оценка макронапряжений показала, что их величина составляет 3 ГПа относительно необработанного основного металла. В металле шва (рис. 5б) пик 101 α-фазы после УЗОТ также смещен в сторону меньших углов дифракции по сравнению с основным металлом необработанного образца (рис. 4а), но в меньшей степени, чем в основном металле. Макронапряжения сжатия в металле шва составляют 1 ГПа. Меньшие значения макронапряжений сжатия в шве, чем в основном металле после УЗОТ, обусловлены тем, что в металле шва необработанного образца имеются упругие макронапряжения растяжения по сравнению с основным металлом [6]. При УЗОТ шва происходит их компенсация.
После УЗОТ в основном металле образца значительно возрастает интенсивность пика 011 β‑фазы по сравнению с исходным необработанным состоянием (рис. 4), что соответствует увеличению объемной доли этой фазы до 25% (табл. 1).
Кроме того, появляются пики интерметаллидных фаз TiCo, TiCo2 и AlTiCo2, интенсивность которых сопоставима с интенсивностью пиков основной α-фазы (рис. 4б).
На дифрактограмме зоны шва также наблюдается появление пиков интерметаллидных фаз (рис. 5). Фазы TiCo [12], TiCo2 [17–19] и AlTiCo2 [18] являются упорядоченными, тип сверхструктуры которых указан в табл. 2.
Таблица 2.
Сингонии, пространственные группы, типы сверхструктур и параметры решеток фаз в системах Ti–Co и Al–Ti–Co
Фаза | Сингония | Пространственная группа | Сверхструктура | Параметр решетки, нм | Источник | |
---|---|---|---|---|---|---|
а | с | |||||
TiCo | Кубическая | Pn3m | B2, тип CsCl | 0.2994 | [12] | |
TiCo2* | Кубическая | Fd3m | Фаза Лавеса, тип MgCu2 | 0.6704 | [17–19] | |
TiCo2** | Гексагональная | С6/mmc | Фаза Лавеса, тип MgNi2 | 0.4372 | 1.5427 | [17–19] |
AlTiCo2 | Кубическая | Pn3m | B2, тип CsCl | 0.585 | [18] |
При развертке участка дифрактограммы в интервале углов дифракции 2θ от 41° до 53° становится видно (рис. 6), что справа от пика 112 AlTiCo2 располагается пик 022 TiCo2 с пространственной группой Fd3m, и между пиками 011 β и 101 α пик 112 TiCo2 с пространственной группой С6/mmc. На полной дифрактограмме наблюдаются и другие пики TiCo2 фазы. Фаза TiCo2 в двух модификациях является фазой Лавеса [12, 19] (табл. 2).
Рис. 6.
Участки дифрактограмм зоны основного металла (а) и зоны шва (б) в образцах сплава Ti–6Al–4V после УЗОТ.
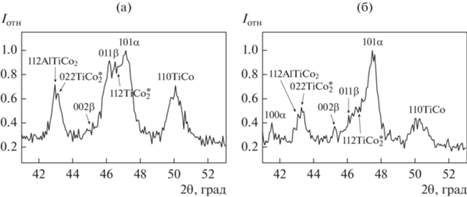
Объемная доля интерметаллидных фаз и β-Ti в основном металле больше, чем в металле шва (табл. 1). Это обусловлено тем, что глубина поверхностного оплавленного слоя в зоне основного металла больше, чем в зоне шва (рис. 3). Из-за большей глубины оплавления в зоне основного металла объем поверхностного слоя, легированного кобальтом, больше, чем в зоне шва.
Взаимосвязь между удельным электрическим сопротивлением и глубиной оплавленного поверхностного слоя при УЗОТ. В исходном необработанном состоянии металл в зоне шва в напечатанном образце сплава Ti–6Al–4V имеет более высокие значения микротвердости, чем в зоне основного металла (рис. 7, [6]). Удельное электросопротивление металла в зоне шва (ρЗС = 1.82 × 10–6 Ом м) больше, чем в зоне основного металла (ρОМ = 1.56 × × 10–6 Ом м) (рис. 8). Таким образом, увеличение микротвердости металла в зоне шва по сравнению с зоной основного металла для исследуемого сплава сопровождается увеличением удельного электросопротивления и уменьшением электропроводности, и соответственно, уменьшением теплопроводности, что в свою очередь приводит к уменьшению глубины оплавления поверхностного слоя образца при УЗОТ.
Рис. 7.
Зависимости микротвердости от расстояния от оси шва на поверхности необработанного образца (–⚫–) и этого же образца, подвергнутого УЗОТ (–◆–).
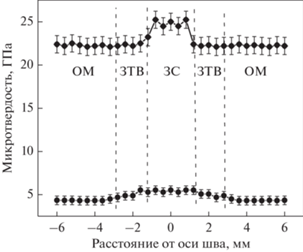
Рис. 8.
Вольт-амперные зависимости для напечатанного образца сплава Ti–6Al–4V со сварным соединением в зоне основного металла (–⚫–) и в зоне шва (–♦–).
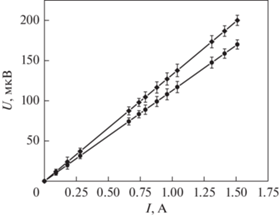
Влияние УЗОТ на микротвердость сварного соединения напечатанного сплава Ti–6Al–4V. После УЗОТ увеличивается микротвердость как металла в зоне шва, так и основного металла (рис. 7). Значительное увеличение микротвердости сварного соединения после УЗОТ обусловлено прежде всего образованием в поверхностных слоях упорядоченных фаз со сверхструктурой B2 и фаз Лавеса, обладающих стабильностью и высокими прочностными характеристиками [19, 20].
Влияние УЗОТ на усталостную долговечность сварного соединения напечатанного сплава Ti–6Al–4V. УЗОТ приводит к увеличению количества циклов до разрушения от 4.7 × 104 в необработанном состоянии образца до 7 × 104 – в обработанном. В образцах в исходном необработанном состоянии разрушение при циклических испытаниях возникает в зоне основного металла (рис. 9а), тогда как в образце после УЗОТ – в зоне шва (рис. 9б).
Рис. 9.
Вид боковой поверхности рабочей части необработанных (а) и после УЗОТ (б) разрушенных образцов со сварным соединением напечатанного сплава Ti–6Al–4V в результате циклических испытаний на растяжение.
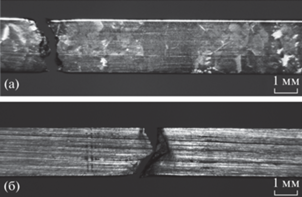
Фрактография излома в зоне основного металла необработанного образца со сварным соединением показала, что как вблизи поверхности (рис. 10а), так и в центральной части образца (вдали от поверхности) (рис. 10б) рельеф преимущественно вязкий ямочный. На фрактографии излома в сварном шве образца, подвергнутого УЗОТ, в поверхностном слое наблюдается хрупкий скол (рис. 10в), тогда как в центральной части образца – вязкий ямочный (рис. 10г). Размер ямок излома обработанного образца (рис. 10г) меньше, чем у необработанного (рис. 10б). Уменьшение размеров ямок излома свидетельствует об усилении тенденции к хрупкому разрушению образца [2].
Рис. 10.
Фрактография излома вблизи поверхности (а, в) и в центральной части образцов вдали от поверхности (б, г) в необработанном образце в зоне основного металла (а, б) и в образце, подвергнутом УЗОТ (в, г), в зоне шва.

Как отмечали выше, в необработанных образцах сплава Ti–6Al–4V в зоне шва имеются упругие макронапряжения растяжения по сравнению с основным металлом [6]. Металл в зоне шва имеет более высокие значения микротвердости и предела текучести, чем основной металл. Напряжение при циклических испытаниях составляло ≈0.8σ0.2, где σ0.2 – предел текучести для необработанного сплава Ti–6Al–4V без сварного соединения. Поэтому эволюция деформационных процессов в зоне основного металла значительно опережает эволюцию процессов в зоне шва, и образование трещины в образце со сварным соединением с большой вероятностью происходит в зоне основного металла. В обработанных образцах напечатанного сплава Ti–6Al–4V со сварным соединением макронапряжения сжатия больше в зоне основного металла, чем в зоне шва, что приводит к задержке образования трещины в основном металле и ее образованию в зоне шва.
ВЫВОДЫ
В результате ультразвуковой обработки с током с использованием ударника из твердого сплава (Co–WC) напечатанного сплава Ti–6Al–4V со сварным соединением происходит:
1. Оплавление поверхностного слоя образца и легирование кобальтом. Глубина оплавления в зоне шва меньше, чем в зоне основного металла. Это связано с тем, что удельное электросопротивление в зоне шва больше, чем в зоне основного металла напечатанного сплава.
2. Увеличение объемной доли β-фазы и образование фаз систем Ti–Co и Ti–Co–Al в поверхностном слое образца.
3. Возникновение упругих макронапряжений сжатия. В зоне основного металла их величина больше, в зоне шва.
4. Образование трещины в зоне шва, тогда как в необработанном образце – в зоне основного металла.
5. Увеличение микротвердости, что обусловлено образованием интерметаллидных фаз после УЗОТ.
6. Увеличение усталостной долговечности при циклических испытаниях в 1.5 раза по сравнению с необработанным образцом.
Работа выполнена в рамках государственного задания ИФПМ СО РАН, тема номер FWRW-2021-0010. Исследования выполнены с использованием оборудования ЦКП “Нанотех” ИФПМ СО РАН.
Список литературы
Pleshanov V.S., Kibitkin V.V., Panin V.E. Mesomechanics of fatigue fracture for polycrystals with macroconcentrators // Theor. Appl. Fract. Mech. 1998. V. 30. № 1. P. 13–18.
Панин В.Е., Панин С.В., Почивалов Ю.И., Смирнова А.С., Еремин А.В. Структурно-масштабные уровни пластической деформации и разрушения сварных соединений высокопрочных титановых сплавов // Физическая мезомеханика. 2018. Т. 21. № 4. С. 33–44.
Трефилов В.И., Моисеев В.Ф., Печковский Э.П., Горная И.Д., Васильев А.Д. Деформационное упрочнение и разрушение поликристаллических металлов // Киев: Наукова думка, 1989. 256 с.
Liu Ch., Liu D., Zhang X., Yu Sh., Zhao W. Effect of the ultrasonic surface rolling process on the fretting fatigue behavior of Ti–6Al–4V alloy // Materials. 2017. № 10. P. 833–845.
Yang Liu, Dongpo Wang, Caiyan Deng, Lixing Huo, Lijun Wang, Rui Fang. Novel method to fabricate Ti–Al intermetallic compound coatings on Ti–6Al–4V alloy by combined ultrasonic impact treatment and electrospark deposition // J. Alloys Compounds. 2015. V. 628. P. 208–212.
Боянгин Е.Н., Перевалова О.Б., Панин А.В., Мартынов С.А. Влияние электронно-лучевой сварки на микроструктуру и микротвердость 3D-напечатанных изделий из титанового сплава Ti–6Al–4V // ФММ. 2021. Т. 122. № 2. С. 152–158.
Перевалова О.Б., Панин А.В., Боянгин Е.Н. Влияние поверхностной ультразвуковой электроимпульсной ударной обработки на микроструктуру, фазовый состав и микротвердость 3D-напечатанного сплава Ti–6Al–4V // ФММ. 2021. Т. 122. № 7. С. 737–744.
Перевалова О.Б., Панин А.В., Боянгин Е.Н., Мартынов С.А. Влияние ультразвуковой электроимпульсной ударной обработки на микроструктуру, фазовый состав и микротвердость ЭЛС-соединения 3D-напечатанного сплава Ti–6Al–4V // ФММ. 2022. Т. 123. № 9. С. 955–961.
Panin A., Kazachenok M., Perevalova O., Martynov S., Panina A., Sklyarova E. Continuous Electron Beam Post-Treatment of EBF3-Fabricated Ti–6Al–4V Parts // Metals. 2019. V. 9(6). P. 699–715.
Panin A., Dmitriev A., Nikonov A., Perevalova O., Kazantseva L., Bakulin A., Kulkova S. Transformations of the microstructure and phase compositions of titanium alloys during ultrasonic impact treatment. Part II Ti–6Al–4V // Metals. 2022. V. 12. P. 732–748.
Горелик C.С., Расторгуев Л.Н., Скаков Ю.А. Рентгенографический и электронно-оптический анализ. М.: Металлургия, 1970. 328 с.
Миркин Л.И. Справочник по рентгеноструктурному анализу поликристаллов. М.: ФИЗМАТГИЗ, 1961. 863 с.
Sorger Gonçalo L., Oliveira J.P., Inácio Patrick L., Enzinger Norbert, Vilaça Pedro, Miranda R.M., Santo Telmo G. Non-destructive microstructural analysis by electrical conductivity: Comparison with hardness measurements in different materials // J. Mater. Sci. Techn. 2019. V. 35. Issue. 3. P. 360–368.
Гиржон В.В., Смоляков А.В., Здоровец А.Ф. Лазерное легирование титана переходными металлами группы железа // Металлофизика и новейшие технологии. 2017. Т. 39. № 4. С. 507–515.
Добромыслов А.В. Бейнитные превращения в титановых сплавах // ФММ. 2021. Т. 122. № 122. С. 255–284.
Горнакова А.С., Прокофьев С.И., Страумал Б.Б., Колесникова К.И. Рост зернограничной прослойки (α-Ti) в сплавах Ti–Co // Металловедение и термич. обработка. 2016. № 5. С. 69–77.
Диаграммы состояния двойных металлических систем. Справочник в 3 Т.: Т. 2 под общ. Ред. Н.П. Лякишева. М.: Машиностроение, 1997. 1024 с.
Буханько Н.Г., Казакова Е.Ф., Соколовская Е.М. Взаимодействие алюминия с кобальтом и титаном // Вестник московского ун-та. Сер. 2. Химия. 2002. Т. 43. № 1. С. 51–57.
Бонар А.А., Великанова Т.Я., Даниленко В.М., Дементьев В.М., Козлов Э.В., Лукашенко Г.М., Сидорко Р.Р., Штерн Д.М. Стабильность фаз и фазовые равновесия в сплавах переходных металлов. Киев: Наукова думка, 1991. 200 с.
Попов Л.Е., Козлов Э.В. Механические свойства упорядоченных твердых растворов. М.: Металлургия, 1970. 217 с.
Дополнительные материалы отсутствуют.
Инструменты
Физика металлов и металловедение