Физика металлов и металловедение, 2022, T. 123, № 12, стр. 1334-1346
Прогноз разрушения материалов с неоднородной структурой
А. В. Кудря a, *, Э. А. Соколовская a
a Федеральное государственное автономное образовательное учреждение высшего образования
“Национальный исследовательский технологический университет “МИСиС”
119049 Москва, Ленинский просп., д. 4, стр. 1, Россия
* E-mail: avkudrya@misis.ru
Поступила в редакцию 04.08.2022
После доработки 19.10.2022
Принята к публикации 27.10.2022
- EDN: DROJHB
- DOI: 10.31857/S0015323022601088
Аннотация
Рассматриваются структурные и металлургические факторы, оказывающие влияние на различия в сопротивлении сталей и сплавов разрушению, необходимые для прогноза разрушения сред с неоднородной структурой. Рассматриваются перспективы цифровизации измерения параметров структуры и поверхностей разрушения путем применения алгоритмов “Big Data”.
ВВЕДЕНИЕ
Прогноз разрушения конструкций во многом определяется полнотой оценки качества исходных материалов, это также влияет и на оценку остаточного ресурса. В своей основе стали и сплавы представляют собой среду, неоднородность морфологии которой может быть весьма велика, особенно при промышленном производстве. Разнообразие структур и их геометрии затрудняет выработку общих подходов к выделению критических параметров структуры, лимитирующих свойства материалов [1–3]. Неоднородность морфологии структуры определяет разброс вязкости не только между изделиями, но и различие в механизмах разрушения в пределах одного изделия (образца). Для решения задач, связанных с получением объективной оценки поведения материала в конструкции, требуется понимание механизмов разрушения среды с неоднородной структурой. Стандартной техники измерений не всегда достаточно для оценки разрушения таких структур. Для этого необходимы цифровые процедуры измерения характеристик неоднородности структуры и разрушения, и сопоставление полученных результатов. Неотъемлемое условие успешного применения такого подхода – соответствующее метрологическое обеспечение.
Свойства металла являются – результатом совокупности операций, выполняемых на протяжении всей технологической цепочки: от выплавки до конечной термической обработки. Однако прогноз его прочности, пластичности и вязкости могут дать “раскопки данных” (data mining) контроля технологического процесса и конечного продукта. Это важно и для выработки рекомендаций, направленных на улучшение качества продукции. Средства “интеллектуального анализа данных” пассивных наблюдений, “раскопки данных”, “Big Data” [4] стали быстро развивающейся областью прикладной статистики. Однако выбор алгоритмов для конкретной задачи производства требует анализа ее содержания технологом, что предполагает знание механизмов эволюции структур и дефектов по всей технологической цепочке и закономерностей разрушения металла, как среды с неоднородной структурой. Это предполагает возможность измерений параметров структур и разрушения с целью их прямого сопоставления и выделения на этой основе критических элементов структуры, лимитирующих неоднородность качества металла. В этой связи очевидно, что для прогноза разрушения материалов необходимо знание закономерностей разрушения материалов, как среды с неоднородной структурой, ее формирования в соответствии с разнообразными проявлениями технологической наследственности в рамках промышленной технологии [1].
1. МАСШТАБЫ НЕОДНОРОДНОСТИ СРЕДЫ СО СТРУКТУРОЙ И ЕЕ РАЗРУШЕНИЕ
Формирование различий в строении номинально однотипных структур в сталях, определяемых многообразием сценариев технологической наследственности (механизмов эволюции структур и дефектов) в рамках промышленной технологии, начинается со стадии выплавки металла. В соответствии с диаграммой фазового равновесия затвердевающий металл и расплав различаются по составу. Появление первых кристаллов от поверхности к оси слитка дает разницу в составе по его сечению (зональная ликвация). Ее масштабы – производная типа диаграммы состояния, скорости затвердевания и направления теплоотвода при кристаллизации, которые зависят от размеров и формы слитка или непрерывнолитой заготовки.
Кристалл растет из расплава как дендрит, который может быть размером до 1–10 см. У дендритного скелета имеется два параметра: расстояние между осями дендритов Λ и отношение наибольшей и наименьшей концентрации элемента (в осях и в межосьях дендритов) K = cmax/cmin – коэффициент ликвации. В зависимости от размеров слитка и зон ликвации в нем шаг осей дендритов первого порядка может быть равен Λ1 = 0.1–3 мм, а второго – Λ2 = 3–100 и даже до 400 мкм, обычно на практике используют средний шаг (период) осей дендритов на случайной секущей Λ ≈ Λ2. Дендритную ликвацию определяют скорость фронта кристаллизации w и градиент температуры на этом фронте grad T. От поверхности к оси слитка градиент температуры grad T убывает и шаг дендритов Λ растет. Отсюда наблюдаемое различие морфологии дендритной структуры не только между зонами ликвации, но и в пределах каждой из них.
Важен не только размер дендритов, но и связанная с ним степень дендритной ликвации. Дисперсность дендритов ограничивает диффузионное перераспределение примесей и уменьшает неоднородность состава. Степень ликвации может быть достаточно велика, например, в слитках легированных конструкционных сталей с 0.1–0.4% С находили степень ликвации KCr = 1.3–2.1; KMn = 1.2–1.9; KSi = 1.3–1.7 [5]; KNi = 1.2–1.8 (поковки из стали 38ХН3МФА-Ш). Ликвацию усиливает углерод, одновременно перераспределяясь вслед за основными легирующими элементами (уже после затвердевания): выравнивая свою термодинамическую активность и уходя в объемы с избытком карбидообразователей (W, Mo, Cr, Mn), покидая объемы с избытком ферритообразователя (Si) [1].
Примеси и обогащенный серой легкоплавкий ликват оттесняется в межосные и междендритные промежутки слитка. Отсюда дальние последствия ликвации в слитке – неравномерность геометрии неметаллических включений (НВ): размеров, формы и размещения. Чем мельче дендриты, тем меньше ликвация серы [1] и мельче сульфиды. Статистику геометрии включений в масштабах изделия (образца) может дать серный отпечаток по Бауману. Так, например, для поковки из стали 38ХН3МФА измерения параметров его темных пятен (на серии последовательных кадров площадью 100 мм2, вырезанных в масштабе сечения поковки в горизонтальном, вертикальном и диагональном направлениях) дали следующие данные о загрязненности сульфидами по сечению поковки (центральная, промежуточная и периферийная зоны поковки): плотность ρ – от 1.15–1.50 до 0.60–0.90 и 0.60–0.97 шт./мм2; объемная доля Vтп – от 3.5–5.0 до 1.5–2.7 и 0.9–2.0%; средний диаметр ❬dтп❭ – от 0.18–0.21 до 0.16–0.18 и 0.11–0.16 мм. Распределение темных пятен по размерам имеет асимметричный характер (рис. 1) [6], он отражает характер распределения НВ в целом, чем больше их размер, тем меньше вероятность появления в поле зрения. Вид распределения важен для оценки эффективности применения средних значений размеров НВ при сопоставлении различных выборок результатов измерения их геометрии.
Рис. 1.
Распределение пятен серного отпечатка по размерам в различных зонах поковки из стали 38ХН3МФА.
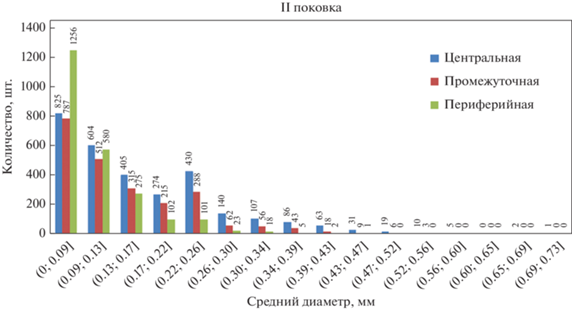
Следующий важный фактор – корреляция в размещении включений, например, строчечность хрупких оксидов из-за их дробления при прокатке. Возможна также неоднородность распределения частиц, в частности, сульфидов вследствие зональной ликвации или образования более компактного кластера в объеме грязного ликвата, локализованного в междуветвиях дендрита на завершающем этапе кристаллизации. Выделить из случайной россыпи частиц плотную цепочку точек вдоль некоторой кривой (известного вида) можно, используя конформные преобразования плоскости [7]. Оценку различий между случайными множествами точек на плоскости (или центров частиц, малых в сравнении с расстоянием r между ними) можно провести, например, с помощью алгоритмов, использующих разбиение плоскости на полиэдры Вороного [8]: все точки внутри каждого из полиэдров лежат ближе к его центру, чем к центрам всех других соседних полиэдров. Такое разбиение позволяет определить ближайших соседей каждой частицы и измерить расстояние между ними. Левый и правый хвосты такого распределения характеризуют высокую вероятность образования вязкого излома и благоприятные условия для развития пластической деформации соответственно. Отличие в размещении НВ может быть достаточно велико даже в пределах одного изделия. Например, в пределах поковки из стали 38ХН3МФА, для двух случайных мест вырезки фрагментов изображений НВ (одинаковой площади), средние значения расстояний между частицами ❬r❭ составили 447 ± 14 и 314 ± 12 мкм. Отличаются не только средние значения, но и выборки измерений в целом (рис. 2): по критерию Колмогорова–Смирнова [9, 10] при риске 0.001 λэксп = 12.98 > λтабл = 1.95, следовательно, отличие выборок значимое. Такое различие также может внести вклад в появление разброса ударной вязкости по сечению поковки.
Рис. 2.
Различие в статистике распределения расстояний между НВ – по разбиениям на полиэдры Вороного их изображений (×100) в масштабе образцов, вырезанных из различных мест зон крупной поковки из улучшаемой стали 38ХН3МФА.
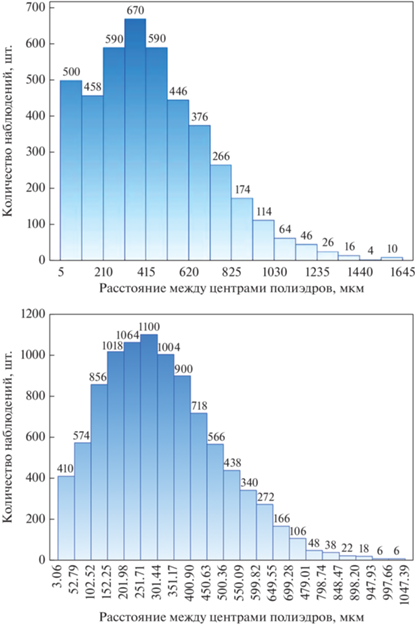
Переменное содержание легирующих элементов (а с ними и углерода) в литой структуре приводит к разнице в критической скорости охлаждения аустенита, в результате чего при одной и той же скорости охлаждения стали в осях дендритов и между ними можно получить разную структуру. Отсюда влияние ликвации на прокат – структурная полосчатость среднеуглеродистой стали: мартенсит-бейнитная, бейнит-перлитная, феррит-перлитная, и карбидная строчечность в высокоуглеродистой стали.
Другая причина полосчатости микроструктуры также связана с ликвацией: размещение легкоплавких неметаллических включений (сульфидов и силикатов) внутри ячейки дендрита и “раскатка их в нить” прокаткой. В месте соприкосновения с силикатом аустенит обогащен кремнием, отчего термодинамическая активность растворенного углерода здесь выше, и он отсюда вытесняется. Это приводит к феррито-перлитной полосчатости, в структуре возникают ферритные строчки с нитью силиката на оси ферритной полоски.
Слой вблизи нитей MnS обогащен марганцем, из-за чего туда “втягивается” углерод, что после охлаждения приведет к образованию полос перлита. В итоге получается тот же результат – чередующиеся полосы феррита и перлита вдоль направления прокатки.
При описании структуры и морфологии изломов важное значение имеет выбор информативных параметров их геометрии. Ручные измерения объективно ограничены трудоемкостью, отсюда преобладание эталонных шкал или словесного описания в нормативных документах. При этом необходимо знание механизмов деформации и разрушения неоднородных структур и статистика распределения отдельных элементов структуры по размерам. Например, при оценке неоднородности морфологии включений НВ в подшипниковой стали представляет интерес не весь их размерный ряд, наблюдаемый в световом микроскопе (от 1 мкм и выше), а включения поперечного размера от 10 до 20 мкм. Это те “крупные” включения, вероятность попадания которых в приповерхностный слой, где действуют максимальные контактные напряжения, будет максимальна. Именно они будут определять массовое качество подшипников, в отличие от частиц большего размера, которые будут вызывать провал свойств отдельного подшипника, но такой дефект можно будет выявить средствами неразрушающего контроля.
При вязком разрушении сплавов отслой НВ (пластичных) от матрицы или их растрескивание (хрупких) приводит к появлению пор, а пластический рост и слияние последних обеспечивает рост макротрещины. Это приводит к ямочному строению вязкого излома в виде половинок слившихся пор (нередко с включением в центре). В условиях плоской деформации зависимость вязкости разрушения KIс от поперечного размера d и объемной доли включений V (одинаковых и равноосных) выражается через среднее (в трех измерениях) расстояние Λ ≈ d/V1/3 между частицами [11].
Однако особенность неметаллических включений заключается в широком диапазоне их размеров (от 1 до 106 мкм) при незначительной объемной доле ~0.01–0.1%. Причем с увеличением размера НВ снижается вероятность их наблюдения на шлифе. Распределение размеров ямок в вязком изломе повторяет распределение НВ [8, 11]. При этом нет оснований считать, что их размещение всегда будет иметь случайный характер, в силу протекания различных сценариев технологической наследственности возможно образование их скоплений или областей с пониженной концентрацией. Это облегчает зарождение вязкого излома и протекание пластической деформации соответственно.
Такое многообразие различий в загрязненности стали неметаллическими включениями (наряду с неоднородностью микроструктуры) приводит к различиям в уровне энергоемкости вязкого разрушения. Качественной оценки морфологии сопутствующих однотипных вязких изломов обычно недостаточно для выявления причин такого разброса, например, более чем двукратного роста различия ударной вязкости сталей с разнородной структурой (сорбит отпуска в сортовом прокате, разномасштабная ферритно-перлитная полосчатость в микроструктуре листовых сталей, различие в неоднородности морфологии НВ и неоднородности областей феррита в сталях, где после малого укова сохранился рисунок дендритной структуры; стали 40Х2Н2МА, 09Г2С, 16Г2АФ, 15Х2НМФА и 38ХН3МФА соответственно) [8]. Различия в строении изломов смогла выявить только представительная статистика результатов измерений параметров изломов средствами 2D- и 3D-размерности. К их числу, например, относится различие значений коэффициентов асимметрии эмпирических распределений количества соседей ямок, определяемых на основе разбиения 2D-изображений изломов на полиэдры Вороного, значений диаметров и глубин ямок, толщин перемычек между соседними ямками, определенных из 3D-моделей рельефа, полученных методами стереофотограмметрии.
Было обнаружено, что сопротивление разрушению связано с долей перемычек и их толщиной в изломе между смежными ямками. Снижению их доли с 0.50 до 0.27 сопутствует изменение относительного сужения ψ с 40 до 80% и ударной вязкости от 0.52 до 2.72 МДж/м2 (коэффициенты корреляции линейных зависимостей R составили 0.81 и 0.96 соответственно). При этом в зависимости от уровня ударной вязкости соотношение доли перемычек, разрушившихся по механизмам мезоотрыва νмо и среза νср (νмо/νср), изменялось в диапазоне от 0.65 до 1.9. Максимальным значениям вязкости соответствовало разрушение перемычек по линии действия касательных напряжений (разрушение срезом). В развитии микропластической деформации металлической матрицы, предшествующей слиянию смежных пор, что определяет работу распространения трещины по дну макрохрупкого квадрата (хрупкая составляющая в изломе ударных образцов, окруженная по периметру вязкой составляющей – ГОСТ 4543), существенную роль играет также уровень пластичности самой матрицы отсюда наблюдаемая корреляция параметров изломов с характеристикой пластичности ψ.
Вариация значений характеристик распределения неоднородностей структуры и их связь с ударной вязкостью показывает, что для выявления различий в морфологии изломов необходимо применение более широкого спектра характеристик, в частности, тех, что оценивают статистику их распределения по размерам.
Морфология вязких изломов прямо связана со структурой, например, с размещением НВ. Так, статистика полиэдров Вороного выявила взаимосвязь между размещением ямок в изломах (трех образцов, вырезанных из различных мест крупной поковки из стали 38ХН3МФА) и темных пятен серного отпечатка по Бауману [6]. Это указывает на возможность прогноза вязкого разрушения на основании анализа структуры стали.
Для прогноза разрушения неоднородных структур необходимы соответствующие количественные оценки сопротивления разрушению, в первую очередь хладноломкости и вязкости разрушения. Существующие подходы, например, сериальные ударные испытания по методике Давиденкова обычно фиксируют значительный разброс значений ударной вязкости в интервале температур вязко-хрупкого перехода. Например, для листовой стали 09Г2С (по результатам приемо-сдаточных испытаний ~1200 плавок) размах значений KCU Δ = KCUmax – KCUmin при температурах –40, –60 и –70°С составил 200, 340 и 280 Дж/см2 соответственно. Это косвенный признак неоднородности структур, как в масштабах образца, так и от образца к образцу, что порождает “размытие” порога хладноломкости. Развитая структурная неоднородность, в частности, в крупных поковках из улучшаемой стали 38ХН3МФА-Ш приводит к значительному разбросу ударной вязкости во всем диапазоне температур испытания, отчего порог хладноломкости “размывается”, и сериальные кривые удовлетворительно описываются линейной функцией (коэффициент детерминации в диапазоне 0.84–0.92). Это затрудняет оценку степени влияния различных аномалий структуры на хладноломкость [1].
В таких случаях могут быть перспективны микромеханические сериальные испытания на микрообразцах, габариты которых сопоставимы с масштабом структурной неоднородности, где критерием перехода от вязкого к хрупкому разрушению является изменение пиковой амплитуды акустической эмиссии не менее, чем на порядок [12]. Именно они, в частности, позволили показать [13], что в крупных поковках из улучшаемой стали 38ХН3МФА-Ш в интервале от –130 до –100°С хрупко разрушается только межосевое пространство, а ниже –130°С хрупко разрушаются и оси дендритов. При этом наблюдаемая в этих же поковках аномалия вязкого разрушения – камневидный излом (разрушение по кластерам субмикронных и микронных НВ, выделившихся по границам перегретого зерна аустенита), с хладноломкостью не связана.
Разрушение среды с неоднородной структурой достаточно сложно оценить в терминах механики разрушения, особенно при развитой пластической деформации, когда не удается достоверно оценить критический коэффициент интенсивности напряжений при плоской деформации KIC. Например, при определении критериев нелинейной механики разрушения: деформационного – критическое раскрытие трещины (КРТ) δс, и энергетического – интеграл Черепанова–Райса (J-интеграл), в соответствии с ГОСТ 25-506–85 не всегда однозначен выбор максимального значения нагрузки (точка С на регистрируемой в процессе испытания диаграмме “нагрузка–смещение берегов трещины”) при нахождении величин δ и J-интеграла. Если исходить из концепции КРТ, как максимального раскрытия в устье трещины, при котором начинается ее распространение, то очевидно, что только мониторинг разрушения способен объективно выделить критические стадии статического роста трещины. Этот же подход правомерно отнести и к определению J‑интеграла.
Не исключено, что при нахождении КРТ более корректным будет применение классической концепции [14], исходящей из представления о том, что раскрытие трещины происходит путем вращения ее берегов относительно некоторого центра. При таком подходе есть возможность определения величины δс с привязкой к структуре, при условии учета геометрии раскрытия и кинетики распространения трещины [15]. Показано, в частности, что для крупных поковок из улучшаемой стали 38ХН3МФА-Ш разброс значений δс только в пределах одного положения переднего фронта статической трещины (по толщине образца), при учете не только его кривизны, но и изрезанности, отражающей неоднородность морфологии разнородных структур, может достигать 10–20% и более.
Понимание механизмов разрушения среды с разнородной структурой важно не только для прогноза ее сопротивляемости разрушению по имеющемуся ее строению – post factum, но и для выработки принципов конструирования оптимальной конфигурации структур и размеров (формы) отдельных ее элементов под заданный уровень свойств. Такой подход был реализован при определении оптимального состава умеренно легированной быстрорежущей стали 17М6Ф5Б (“под гранульную технологию”) для мелкого фасонного инструмента, режущего труднообрабатываемые материалы [16]. Так же “конструировались” жаропрочные интерметаллидные композиты с сотовой структурой – “драже”, из алюминидов никеля внутри и тугоплавкого металла снаружи [17].
Для твердых сплавов – наплавок рабочих органов почвообрабатывающих сельскохозяйственных машин, обычно характерна сложная структура, состоящая из достаточно прочной матрицы, в которой размещены упрочняющие частицы (бориды, карбиды различной природы и др.) [18]. Многократное воздействие на сплав абразивных частиц почвы приводит к достижению в локальных объемах наплавки предела прочности матрицы и к появлению в них трещин (очагов разрушения).
Сопоставление результатов измерения геометрии строения структуры и морфологии изломов в масштабе наплавок [19] выявило зависимость критической степени локальной деформации ε прослоек материала, окружающего упрочняющие частицы, от средней толщины вязких прослоек и коэффициента асимметрии распределения значений их толщин. Из полученного соотношения можно определить геометрические параметры структуры, при которых достигается необходимый уровень критической деформации ε, при котором начинается разрушение матрицы. Или решить обратную задачу: по имеющимся типам морфологии структуры твердых сплавов составить прогноз риска преждевременного разрушения наплавки.
2. ЦИФРОВИЗАЦИЯ ИЗМЕРЕНИЙ ПАРАМЕТРОВ СТРУКТУР И РАЗРУШЕНИЯ
Для прогноза разрушения конструкционных материалов есть три источника информации: изображения структуры и изломов, результаты испытаний (механических и физических), базы данных производственного контроля процесса и конечного продукта. До последнего времени оценка изображений структуры и поверхностей разрушения предусматривала в основном их сравнение с эталонными изображениями, сейчас современные вычислительные мощности и программное обеспечение дают возможность получения принципиально иной информации об их строении. Однако ее объективность будет определяться уровнем метрологического обеспечения процедуры анализа изображения. На этой основе оказывается возможным прогноз свойств неоднородной структуры из описания геометрии ее составляющих в сопоставлении с морфологией изломов.
Цифровые изображения структуры и изломов представляют собой поле яркости z (x, y) – однозначной функции координат на плоскости кадра в 256 оттенках серого, где светлые и темные участки отвечают той или иной составляющей структуры или излома. Отдельные точки изображения – пиксели со своим уровнем яркости (серого) объединены чаще всего в прямоугольную матрицу размера m × n.
При прочих равных условиях (оптические параметры, характеристики светочувствительной матрицы) качество цифрового изображения лимитируется контрастом K – отношением разности яркостей Bo различных элементов изображения и фона Bf к одной из этих яркостей K = (Bo – Bf)/Bf. Варьирование в пределах переходной зоны “объект – фон” на первичном цифровом изображении в 256 уровнях серого с целью его перевода в бинарное (матрица вида “1-0”, где элементу структуры отвечает “1”, а фону – “0”) может привести к изменению геометрии отдельных однотипных элементов (размеров, площадей и формы), а в результате дробления или слияния нескольких элементов – к изменению их количества [20]. Это может исказить статистику измерений геометрических характеристик объектов. Например, измерения объемной доли мелких включений сопоставимы лишь при едином алгоритме и параметрах настройки для опознавания "края” частиц. Меняя аппаратуру (различные модификации одного и того же автоматического анализатора изображений), на одних и тех же шлифах (полях зрения) получали разницу в объемной доле мелких частиц до 2–3-кратной, а вытянутых включений – до 4–5 раз [1].
Существующее многообразие алгоритмов бинаризации, например, [21] указывает на различные подходы к выбору порогового значения. В частности, для одних и тех же изображений (полей зрения) типичных структур: дендритной, феррито-перлитной полосчатости в микроструктуре, НВ сталей 38ХН3МФА, 09Г2С, использование таких распространенных алгоритмов бинаризации, как метод среднего, локального среднего и Оцу [21] выявило существенное различие результатов. Так, максимальное и минимальное средние значения (для трех бинарных изображений, полученных таким образом) поперечных размеров дендритов ❬d❭max/❬d❭min различались в 5 раз; этому соответствовало и различие в количестве дендритов – 2.7 раз; средний шаг полос перлита отличался более чем в 7 раз; количество НВ – в 43 раза, а их объемная доля V – почти в 30 раз.
Их этого вытекает, что обоснованный выбор уровня (порога) бинаризации в значительной мере определяет воспроизводимость и сопоставимость результатов измерения элементов изображения. Для изображений со сложным иерархическим строением, например, таких как дендритная структура, в этой связи полезным оказалось построение зависимости площади дендритов F от их периметра Р, при последовательном варьировании порога бинаризации c шагом, соответствующим одному уровню серого от 0 до 255 (рис. 3а). Полученная в результате С-образная кривая отражает характер изменения морфологии изображения с изменением порога бинаризации: от абсолютно черного (уровень серого равен нулю) с последующим его “собиранием” в цельную бинарную картину за счет добавления составляющих структуры исходно более светлого цвета.
Рис. 3.
Бинаризация изображений дендритной структуры стали 38ХН3МФА (а) и твердого сплава на основе железа (б) на основе построения зависимости площади светлых структурных составляющих F от их периметра Р, при последовательном варьировании порога бинаризации c шагом, равным одному уровню серого (от 0 до 255). Итоговые изображения при уровнях бинаризации 124 и 157 соответственно.
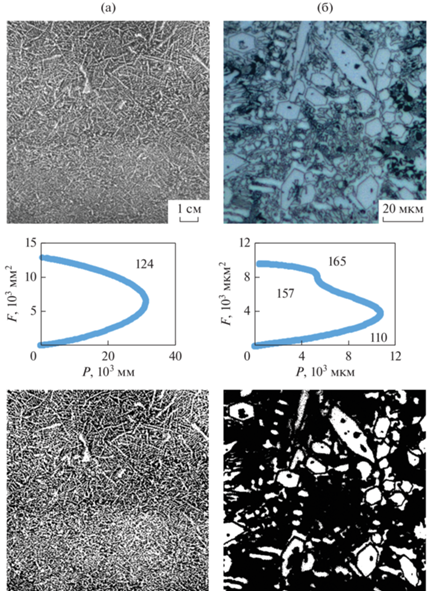
Перегибу на кривой соответствует начало перехода к постепенному “вымыванию” темной составляющей на изображении, которое завершается формированием абсолютно белого изображения. Линейный характер двух составляющих кривой отражает самоподобность изображений структуры [22], полученных при пошаговом изменении контраста.
“Нос” кривой соответствует смене механизма формирования бинарного изображения, и отвечающий ему уровень контраста может быть использован в качестве величины порога бинаризации [23].
В тех структурах, где есть несколько составляющих, отличающихся уровнем интенсивности яркости, на С-образной кривой может появиться несколько перегибов (рис. 3б), которые будут определять индивидуальные условия контраста для каждой из них. Применение такого подхода может обеспечить поэтапное выделение групп объектов идентичной природы для последующего их измерения.
Для изображений объектов точечной природы, например НВ, предпочтительнее будет применение локальных алгоритмов бинаризации. В таких случаях решение об уровне бинаризации принимается на основе анализа полей яркости частиц, фона и переходной зоны “частица–фон”. Очевидно, что выбор процедуры бинаризации предполагает индивидуальную “настройку” под определенный тип структуры, основанную на изучении закономерностей строения ее поля яркости.
При количественном анализе изображений в материаловедении важное значение играет “отсечение” шумов, интенсивность яркости которых может соответствовать оттенкам серого одной или нескольких структурных составляющих, однако при этом наблюдается их отличие в размерах и форме. Для этого эффективным может оказаться сочетание процедур “эрозия–дилатация”, проводимых с учетом имеющихся представлений о природе структур, представленных на рассматриваемых изображениях. Например, для изображений сохранившейся литой структуры в крупных поковках из улучшаемой стали 38ХН3МФА в зонах ликвации с грубыми равноосными дендритами, метод “случайной хорды” на длине 250 мм дал среднее расстояние между осями первого порядка 1.6 ± 0.1 мм. На них наблюдались “наросты”, отдаленно напоминавшие зародыши осей первого, возможно, второго порядка. Локальные измерения содержания хорошо ликвирующих элементов в этих областях не выявили закономерности в их размещении. При обычном визуальном наблюдении наличие таких составляющих не должно сказаться на оценках строения структуры. Однако при массовых автоматических измерениях геометрии дендритной структуры, например, методом “случайной хорды”, такие артефакты могут исказить результаты определения средних значений поперечных размеров дендритов или их шага. Это делает необходимой фильтрацию артефактов на изображении.
Аналогичная ситуация наблюдается при измерении геометрии НВ. ГОСТ 1778 предусматривает их просмотр при увеличении 100 крат, при этом 1 мм на изображении соответствует 10 мкм в масштабе образца. Сопутствующее разрешение такого цифрового изображения обычно достаточно высоко (1 пкс ~ 0.40–0.60 мкм) устанавливает нижнюю границу регистрируемых размеров темных объектов. Однако меру их соответствия НВ в спорных случаях металлограф может установить только визуально. Для выделения единичных объектов друг от друга глазом человека на изображении, их минимальный размер должен составлять 0.1–0.3 мм. Большее значение уже используется для нанесения мелких деталей на карты и технические планы, но в металлографии важно не только различить объект, но и идентифицировать его. Поэтому возможные противоречия при оценке загрязненности стали НВ могут быть устранены при ограничении минимальных размеров поперечника частиц величиной d ≥ 10 мкм (или при подтверждении их природы в случае рассмотрения этих же полей зрения при больших увеличениях).
В ряде случаев задача фильтрации состоит в разделении или выделении объектов различной (однотипной) природы. Например, “кучность” пятен серного отпечатка, оцениваемая по уменьшению их периметра при слиянии вследствие дилатации (попиксельного последовательного смещения с шагом 1 пиксел их контуров в сторону увеличения размеров каждого пятна), помогла выявить преимущественное местонахождение сульфидов в крупных поковках из улучшаемой стали 38ХН3МФА –междендритные области [13] Однако, только в графическом редакторе Adobe PHOTOSHOP ™ существует более десятка фильтров, реализующих процедуру различных схем дилатации, и только 3–4 из них позволяют реализовать процедуру с учетом геометрии размещения пятен серного отпечатка (в междендритных областях).
Эти фильтры были уже не столь эффективны при обработке изображения серного отпечатка в листе из стали 16Г2АФ (рис. 4а), где наблюдалась слабо выраженная ориентация темных пятен вдоль направления прокатки. Ее причиной могли быть крупные сульфиды марганца, вытянутые при прокатке в нитку, поперечником ~2 мкм, суммарной длиной 100–300 мкм и более, сохранившиеся в изломе шиферообразного типа – последовательности чередующихся выступов и впадин, вытянутых вдоль направления прокатки. Отслой по границе раздела ниток сульфидов марганца и примыкающих к ним полосок перлита с образованием вытянутых пор и их слиянием-сопутствует снижению ударной вязкости (рис. 4б). Однако только комбинация последовательной дилатации и фильтрации (с шагом 1 пкс) темных пятен на бинарном изображении серного отпечатка, сначала в направлении прокатки, а затем – в перпендикулярном ему, позволила оценить степень вытянутости темных объектов и их преимущественную ориентацию в направлении прокатки. Это означает, что по серному отпечатку возможно оценить риск образования шиферообразного излома.
Рис. 4.
Размещение сульфидов в листовой стали 16Г2АФ – по изображению серного отпечатка по Бауману (а), приводящих к зарождению на границе их раздела с полосками перлита в микроструктуре шиферообразного излома (б); ориентация всех изображений относительно направления прокатки идентичная.
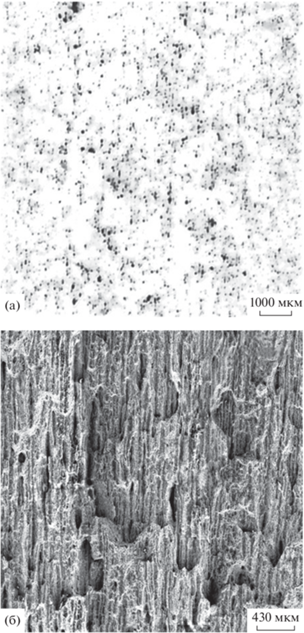
При измерении по изображению параметров разномасштабных структур и изломов неизбежно возникает необходимость проведения оценки масштабов измерений, дающих воспроизводимые результаты. Это обстоятельство уже достаточно давно нашло свое отражение при классификации структур и изломов в требованиях нормативных документов к минимальным площадям объектов наблюдения, например, шлифов. Они сохраняют свою актуальность и при работе с цифровыми изображениями структур и изломов, где выбор минимально необходимого объема измерений, обеспечивающего воспроизводимость результатов, может быть строго обоснован. В качестве такого критерия может явиться достижение значений геометрического параметра какого-либо элемента структуры или обобщенной характеристики морфологии всего изображения в целом, инвариантных по отношению к последующему увеличению объема наблюдения. Такой подход был, в частности, реализован для металла крупных поковок с сохранившимся рисунком дендритной структуры (рис. 5), где была установлена минимальная площадь изображения для каждой из зон ликвации. Ее можно оценить, например, по объемной доле Vd – количеству “светлых” объектов (дендритов) (%) на единице площади, и по соотношению числа “белых” точек в двух взаимно перпендикулярных направлениях – анизотропии А изображения макроструктуры. Минимальная площадь изображения S, начиная с которой объемная доля дендритов Vd и их анизотропия А значимо не изменялись составила 130–190; 260–790 и 200–450 мм2 (в масштабе образца) для периферийной, промежуточной и центральной зон поковок соответственно. Для каждой из зон такая площадь кадра оказалась в 1.7–10 раз больше площади рабочих сечений стандартных ударных образцов и восьмикратных тангенциальных образцов типа III (∅10 мм) на растяжение, что уже предполагает возможность разброса значений прочности, пластичности и вязкости металла из-за различий в строении структуры от образца к образцу.
Рис. 5.
Зоны столбчатых (периферийная – 1), мелкодисперсных (промежуточная – 2) и грубых (центральная – 3) дендритов в макроструктуре крупной поковки из улучшаемой стали 38ХН3МФА.
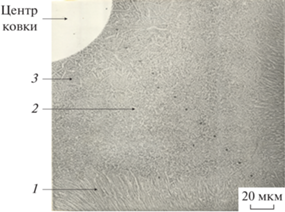
Это означает, что прогноз свойств материалов на основе результатов стандартных испытаний может содержать в себе существенные риски, связанные со значительным разбросом экспериментальных данных вследствие неоднородности структуры.
При измерении параметров феррито-перлитной микроструктуры с полосчатостью стали 09Г2С (при увеличении 200 крат) было показано, что с увеличением объема измерений значения коэффициента асимметрии изменялись от 1.0 до 2.6, эксцесса – от 4.7 до 10.4, и стабилизировались, начиная с полей зрения площадью 0.5–4.3 мм2 (в масштабе образца). Размеры таких площадей определяются масштабом неоднородности микроструктуры, которая может изменяться как по толщине листа, так и от листа к листу, от партии к партии.
Масштаб измерений важен и при оценке морфологии изломов. Их цифровая обработка на любых масштабах наблюдения (макро-, мезо- и микро) характеризуется высокой трудоемкостью, что лимитирует объем измерений. Отсюда известные трудности в описании изломов, например, в связи с попытками применить понятие фрактальной размерности D для объективной ранжировки изломов различной морфологии, например [24]. Полученные результаты оказались противоречивыми: на изломах идентичной природы значения D могли отличаться и практически совпадать, например, для хрупких и вязких изломов. Цифровизация измерений параметров поверхностей разрушения обеспечила быстрое накопление необходимого массива воспроизводимых результатов в широком диапазоне масштабов (от микро- до мезо-), обработка которых не выявила существенных различий в значениях фрактальной размерности изломов различной природы: вязкого, хрупкого, смешанного и камневидного [25]. Получаемые на практике значения тангенса угла наклона (фрактальной размерности D) логарифмической зависимости длины профиля трещины Lk, измеренной с шагом δk, размах которого отличался более чем на два порядка, от величины шага, видимо, не имеют практического смысла, поскольку даже при их совпадении (при условии корректного их определения), это не означает, что механизмы разрушения будут идентичны. Полученные результаты еще раз подтверждают необходимость обоснования объема цифровых измерений, обеспечивающих достоверность и воспроизводимость результатов.
Таким образом, практика разработки и применения процедур цифровой обработки и измерений параметров структур и изломов показывает возможность получения воспроизводимых характеристик их морфологии, отражающих природу рассматриваемых объектов. Для этого при их обработке важен обоснованный выбор критериев бинаризации и фильтрации – на основе физических закономерностей формирования поля яркости изображений. При измерении – представительных объемов объектов измерений, с учетом их статистической природы. Из прямого сопоставления морфологии структур и изломов возможно выделение критических элементов, определяющих разрушение.
Это основа не только для совершенствования существующих технологий получения материалов с целью улучшения их качества, но и для разработки принципиально новых материалов (конструирование структур под заданные свойства), прогноза разрушения материалов в конструкциях [1–3, 13, 26, 27].
3. ПРОГНОЗ СОПРОТИВЛЕНИЯ РАЗРУШЕНИЮ НА ОСНОВЕ “РАСКОПОК ДАННЫХ” ПРОИЗВОДСТВЕННОГО КОНТРОЛЯ
Ранний прогноз разрушения материала можно сделать еще на стадии его получения, на основе рассмотрения взаимосвязей между вариацией значений управляющих параметров технологии, включая химический состав стали, и характеристик материала, отвечающих за сопротивление разрушению. Металлургическая промышленность оснащена средствами измерения и сбора информации по всей технологической цепочке, в т. ч. в реальном времени. Это существенно расширило объем информации о технологии производства и конечном продукте. Если раньше такой анализ ограничивался статистическим обоснованием выборочного приемочного контроля, то затем он распространился на локальный мониторинг производственных операций. Сегодня же это анализ всей последовательности технологических операций производственного цикла (сквозной – от исходных материалов до конечного продукта). Его конечная цель – на основе разнообразных процедур обеспечить обнаружение слабых мест производства, прогноз качества продукта и непрерывное управление им на основе оптимизации технологии. Прогноз основывается на анализе различных сценариев выполнения технологических операций (в пределах нормативного поля допуска). Его главная сложность – в выдвижении различных вариантов обоснованных (и в принципе проверяемых) гипотез о различных цепочках событий, траекториях технологии (эволюции структур и дефектов), приводящих к широкой вариации качества металла.
При этом следует учитывать разнообразие статистической природы рассматриваемых объектов. В частности, распределения значений управляющих параметров (состава и технологии) не принадлежат к нормальному в принципе, поскольку формирование их хвостов ограничено снизу и сверху полем допуска. Нередко наблюдаются асимметричные распределения, например, из-за поддержания химического состава на верхнем или нижнем пределе марки сплава, и встречаются бимодальные распределения [28]. Это ограничивает применение классической статистики. Однако основное препятствие – отсутствие единого пространства параметров технологии: попадание в зону риска значений параметров (например, содержание фосфора на верхнем пределе) не обязательно приводит к негативным последствиям, ровно также, как и попадание их в благоприятную зону не гарантирует положительного прогноза.
У снижения качества металла обычно много причин, и нередко это происходит неожиданно, когда все параметры технологии не выходят за пределы поля допуска (так называемые “внезапные вспышки брака”). В существующей последовательности технологических операций измеряемы и отчасти управляемы K ~ 100 параметров процесса ξk (“режимы”). На выходе регистрируется от десятка параметров качества yi и более, у них свой уровень допуска di (свойства, структура, излом).
При наличии разветвленных сложно связных причин, вызванных действием сложно взаимосвязанных факторов, традиционный “прогноз по возмущению” – действию одного из параметров технологии – обычно не эффективен. Для прогноза, а в последствии и управления необходимо описание K-мерной нелинейной (действующая технология находится вблизи оптимума) зависимости yi (ξk). Для каждой из N партий продукта (плавки, садки, рулона) есть результаты измерения значений “режимов” {ξk} и свойств yi – “траектории процесса в пространстве параметров”. Ретроспективный анализ массивов данных заводского контроля должен дать вид и параметры зависимости yi (ξk).
Из объема N вытекают математические ограничения на выбор метода выявления значимых связей “входной–выходной параметры”. Если “партией” является плавка (данной марки и сортамента), то обычно N < 1000 [1]. Уравнение регрессии yi (ξk) в окрестностях оптимума при K ~ 100 параметрах ξk должно содержать ~K2/2 “перекрестных” членов cksξkξs, описывающих взаимодействие факторов. Отсюда поиск неизвестных cks ограничен в принципе, поскольку K2/2 $ \gg $ N – их количество существенно больше, чем число уравнений.
Однако можно ограничить саму задачу. Поскольку, как правило, грубо дискретны как аргументы ξk, так и функции – меры качества yi, регрессию можно заменить дискриминантным анализом. Искать в пространстве {ξk} только границу между областью риска, где находят y < d0, и областью “благополучных” исходов “приемлемого качества”, где y > d0, например, ниже и выше среднего значения по выборке результатов измерения параметра качества yi. Минимум суммы двух ошибок дискриминации дает точка x, где разность соответствующих эмпирических распределений Φ1(x) и Φ2(x) наибольшая [9]. Такая непараметрическая дискриминация инвариантна к виду распределений, а для учета возможных корреляций обобщаема и на многомерные распределения [29].
Для поиска областей с доминирующим типом зависимости эффективными оказались сложные эвристические приемы когнитивной графики (выявление неочевидных зависимостей графическим путем). Например, полезным стало двумерное отображение областей существования объектов зависимостей yi (ξk) в виде “плотных облаков точек” на разных плоскостях ξi – ξm. В случае разделения облака на два, есть все основания предполагать соответствие этому объективных причин – наличие областей изменения параметров технологии, приводящего к качественной смене поведения системы. В целом, такой подход позволил оценить риски появления аномального вязкого разрушения (камневидного излома) в крупных поковках из улучшаемой стали 38ХН3ФМА-Ш еще в рамках технологического процесса. Он также дает возможность получить рекомендации по его предотвращению нелокальной корректировкой последствий отрицательных возмущений на последующих этапах технологического процесса в пределах его поля допуска [27].
ЗАКЛЮЧЕНИЕ
Показано, что определение закономерностей разрушения среды с неоднородной структурой на основе применения цифровых технологий способно обеспечить прогноз разрушения материалов, провести оценку их остаточного ресурса, а также позволяет сформулировать рекомендации по совершенствованию технологии производства, обеспечивающей повышение качества конечного продукта.
Для прогноза риска разрушения материалов с неоднородной структурой необходимы метрологически обеспеченные цифровые измерения морфологии разнородных структур, изломов в макро-, мезо- и микромасштабах наблюдения и акустической эмиссии, проводимые с учетом статистической природы исследуемых объектов.
Сопоставление морфологии структур, изломов и свойств у для данной группы сплавов или их состояний позволяет решить обратную задачу: выявить критические элементы структуры (или их группы и сочетания), величина которых х определяет данное свойство, и найти зависимость Y(x), прогнозирующую это свойство для структур данного типа, отличающихся геометрией строения.
Ранний прогноз разрушения материалов возможен еще на стадии их получения, на основе рассмотрения взаимосвязей между вариацией значений управляющих параметров технологии и характеристик материала, отвечающих за сопротивление разрушению. Прогноз может быть осуществлен средствами непараметрической статистики и с использованием сложных эвристических приемов когнитивной графики, предполагающих понимание закономерностей технологической наследственности и разрушения металла, как среды с неоднородной структурой.
Список литературы
Сталь на рубеже столетий / Под ред. Ю.С. Карабасова. М.: МИСиС, 2001. С. 445–543.
Разрушение. В 2 кн. Кн. 1. Разрушение материала: моногр. / М.А. Штремель. М.: Изд. Дом МИСиС, 2014. 670 с.
Разрушение. В 2 кн. Кн. 2. Разрушение структур: моногр. / М.А. Штремель. М.: Изд. Дом МИСиС, 2015. 976 с.
Дюк В., Самойленко А. Data Mining. Учебный курс. СПб.: Питер, 2001. 368 с.
Голиков И.Н., Масленков С.Б. Дендритная ликвация в сталях и сплавах. М.: Металлургия, 1997. 224 с.
Кудря А.В., Соколовская Э.А., Нго Х.Н.Х, Кайкибаева А.С. Связь неоднородности свойств крупных поковок со структурой // Электрометаллургия. 2018. № 5. С. 30–35.
Методы анализа данных в физическом эксперименте / Ред. М. Реглер. М.: Мир, 1993. 478 с.
Кудря А.В., Соколовская Э.А., Ле Х.Н., Нго Н.Х. Связь морфологии вязких изломов различной природы и свойств конструкционных сталей // МиТОМ. 2018. № 4. С. 36–41.
Никитин Я.Ю. Асимптотическая эффективность непараметрических критериев. М.: Физматлит, 1995. 240 с.
Большев Л.Н., Смирнов Н.В. Таблицы математической статистики. М.: Наука, 1965. 464 с.
Броек Д. Основы механики разрушения. Пер. с англ. М.: Высшая школа, 1980. 368 с.
Scruby C.B. An introduction to acoustic emission // J. Physics E: Scientific Instruments. 1987. V. 20. P. 946–953.
Кудря А.В., Соколовская Э.А. Неоднородность разномасштабных структур и сопротивление разрушению конструкционных сталей// Известия РАН. Сер. Физическая. 2004. Т. 68. № 10. С. 1495–1502.
Новые методы оценки сопротивления металлов хрупкому разрушению / Пер. с англ. под ред. Ю.Н. Работнова. М.: Мир, 1972. 439 с.
Кудря А.В., Соколовская Э.А., Нго Н. Х., Кузько Е.И., Котишевский Г.В. Прогноз разрушения крупных поковок с неоднородной структурой // Электрометаллургия. 2019. № 6. С. 33–39.
Штремель М.А., Карабасова Л.В., Чижиков В.И., Водениктов С.И. Об оптимальном легировании высокованадиевой быстрорежущей стали // МиТОМ. 1999. № 4. С. 16–20.
Штремель М.Л., Беломытцев М.Ю., Медведев В.В., Мочалов Б.В., Чернуха Л.Г. Структура и свойства композиционных материалов на основе интерметаллида NiAl // Изв. вузов. Черная металлургия. 2006. № 1. С. 40–44.
Восстановление деталей машин напылением и наплавкой. М.: Колос, 1993. 195 с.
Mel’nichenko A.S., Kudrya A.V., Akhmedova T.S., Sokolovskaya E.A. Predicting the risk of destruction of hard-facing alloys based on the morphology of their structure // Metallurgist. 2018. V. 61. № 11–12. P. 1130–1134.
Крупин Ю.А., Сухова В.Г. Компьютерная металлография. М.: МИСиС, 2009. 87 с.
Metallography Principles and Practice George F. Vander Voort, ASM International, 1999. 752 p.
Мандельброт Б. Фрактальная геометрия природы. Пер. с англ. М.: ИКИ, 2002. 656 с.
Соколовская Э.А. О воспроизводимости результатов измерений структур и изломов с использованием компьютеризированных процедур // Вопр. материаловедения. 2013. № 4(76). С. 143–153.
Иванова В.С., Баланкин А.С., Бунин И.Ж., Оксогоев А.А. Синергетика и фракталы в материаловедении. М.: Наука, 1994. 383 с.
Кудря А.В., Соколовская Э.А., Арсенкин А.М. Морфология вязкого излома по измерениям средствами наблюдения различной размерности // Деформация и разрушение материалов. 2010. № 1. С. 38–44.
Хлусова Е.И., Сыч О.В., Орлов В.В. Хладостойкие стали. Структура, свойства, технологии // ФММ. 2021. № 7. С. 621–657.
Лепихин А.М., Махутов Н.А., Шокин Ю.И. Вероятностное многомасштабное моделирование разрушений структурно-неоднородных материалов и конструкций // Заводская лаборатория. Диагностика материалов. 2020. Т. 86. № 7. С. 45–54.
Kudrya A.V., Sokolovskaya E.A., Kodirov D.F., Bosov E.V., Kotishevskiy G.V. On necessity of taking into account statistical nature of the objects using Big Data in metallurgy // CIS Iron and Steel Review. 2022. V. 23. P. 105–112.
Штремель М.А., Кудря А.В., Иващенко А.В. Непараметрический дискриминантный анализ в задачах управления качеством // Заводская лаборатория. Диагностика материалов. 2006. № 5. С. 53.
Дополнительные материалы отсутствуют.
Инструменты
Физика металлов и металловедение