Физика металлов и металловедение, 2022, T. 123, № 5, стр. 491-498
О влиянии окислительного размола матричного порошка на структуру и свойства пеноалюминия на основе сплава Al–12Si
А. С. Просвиряков a, *, А. Н. Солонин a, А. Ю. Чурюмов a, Н. Ю. Табачкова a, b, Н. М. Манцевич c, Л. В. Колеров d
a Национальный исследовательский технологический университет “МИСиС”
119049 Москва, Ленинский просп., 4, Россия
b Институт общей физики им. А.М. Прохорова Российской академии наук
119991 Москва, ул. Вавилова, 38, Россия
c АО “Прорыв”
107140 Москва, ул. Малая Красносельская, 2/8, к. 4, Россия
d ООО “КОЛТЕК-ЭкоХим”
215505 Смоленская обл., Сафоново, ул. Октябрьская, 78, к. 132, Россия
* E-mail: pro.alex@mail.ru
Поступила в редакцию 09.10.2020
После доработки 16.11.2021
Принята к публикации 18.11.2021
- EDN: EXUVDE
- DOI: 10.31857/S001532302205014X
Аннотация
Исследовали влияние продолжительности обработки порошка алюминиевого сплава Al–12Si в шаровой мельнице в воздушной атмосфере на макроструктурные характеристики пеноалюминия. Продолжительность размола составляла от 5 до 20 мин при скорости 300 об./мин и соотношении массы мелющих шаров к массе материала 8 : 1. Обработанный порошок матричного сплава смешивали с 1 мас. % TiH2, после чего получали компактные цилиндрические образцы методом горячего прессования при температуре 400°С. Вспенивание образцов проводили в стальной оснастке при температуре 800°С. Результаты показали, что увеличение продолжительности размола порошка матричного алюминиевого сплава до 15 мин оказывает положительное влияние на процесс вспенивания в результате увеличения степени окисления, что выражается в уменьшении размера образующихся пор и плотности образцов пеноалюминия. Однако последующее повышение времени размола, при котором происходит укрупнение порошковых частиц в результате холодной сварки, приводит к деградации макроструктурных характеристик вспененного образца.
ВВЕДЕНИЕ
На протяжении последних лет наблюдается значительный интерес к разработке новых составов и технологий получения пеноалюминия, что объясняется наличием у изделий из этого материала необычного комплекса свойств: способность эффективно поглощать энергию удара, высокий коэффициент звукопоглощения, пониженная теплопроводность и плотность [1–6]. Одним из способов получения пеноалюминия является метод порошковой металлургии, включающий в себя следующие основные стадии: приготовление порошковых смесей из матричного сплава и порофора (в основном, гидрида титана (TiH2)), получение консолидированного прекурсора и последующее его вспенивание [4, 5, 7–10]. Вспенивание происходит в результате разложения порофора в металлическом расплаве, сопровождающееся выделением газа, что приводит к формированию пористой структуры после кристаллизации.
Основной проблемой при получении пеноалюминия, отрицательным образом сказывающейся на качестве пеноалюминия, является нестабильность пены, что связано с большой площадью ее поверхности. Для того чтобы предотвратить всплытие и слияние пузырьков газа, которые формируют поры, необходимо использование специальных добавок, стабилизирующих металлическую пену. Такими добавками могут служить керамические частицы микронного размера, например, SiC и SiO2 [6, 11, 12]. Присутствие твердых частиц в расплаве увеличивают его объемную вязкость, что приводит к замедлению вертикального движения жидкого металла и способствует кинетической стабильности пены [4]. Когда значительная часть частиц находится на границе раздела газ/расплав, то они стабилизируют стенки пор за счет снижения проницаемости для расплава. Положительное влияние на стабильность пены и конечную структуру пеноалюминия оказывает также увеличение содержания оксида в алюминиевом порошке [13–16]. В этой связи, целью данной работы является изучение влияния предварительного окисления порошка матричного сплава АК12, обладающего хорошей пенообразующей способностью благодаря низкой температуре плавления [2], на качественные характеристики пеноалюминия на его основе.
МЕТОДИКА ЭКСПЕРИМЕНТА
В качестве исходного матричного материала для получения пеноалюминия использовали порошок промышленного сплава АК12 с размером частиц от 1 до 40 мкм. С целью увеличения содержания оксида алюминия исходный порошок подвергали окислению путем обработки его в планетарной шаровой мельнице Retsch PM400 в воздушной атмосфере со скоростью 300 об./мин. Соотношение массы стальных мелющих шаров к массе обрабатываемого материала составляло 8 : 1. Для обеспечения доступа кислорода воздуха к поверхности обрабатываемого алюминиевого порошка размольные контейнеры открывали каждые 2 мин. Обработку материала проводили в течение 5–20 мин. После обработки порошок сплава смешивали с порошком порофора (TiH2) в количестве 1 мас. % в течение 5 мин. Средний размер частиц гидрида титана составлял не более 40 мкм.
Приготовленные порошковые смеси компактировали в стальной матрице в прекурсоры диаметром 25 мм и высотой 10 мм при давлении 180 МПа. Компактирование осуществляли в две стадии: при комнатной температуре и при 400°С. Время прогрева при данной температуре во время горячего прессования составляло 10 мин. Плотность образцов после прессования составила 2.61–2.64 г/см3. Для проведения процесса вспенивания прекурсоры загружали в стальной цилиндрический контейнер диаметром 27 мм и высотой 30 мм, который затем помещали в лабораторную печь, нагретую до температуры 800°С. Время выдержки в печи составляло 7–8 мин. После вспенивания образец вместе с контейнером извлекали из печи и охлаждали на воздухе.
Содержание кислорода в компактированных образцах (до вспенивания) оценивали с помощью энергодисперсионного спектрометра INCA ENERGY Dry Cool фирмы Oxford Instruments. Анализ проводили при ускоряющем напряжении 20 кВ. Средняя площадь отбора информации составляла 500 × 500 мкм2. Исследуемые образцы предварительно подвергали шлифованию и последующей механической полировке. Для повышения точности измерения предварительно была проведена калибровка прибора с использованием специально приготовленных образцов на основе исходного порошка АК12 с известным содержанием частиц Al2O3: 1 и 5 мас. % (0.47 и 2.35 мас. % О соответственно). Средний размер частиц оксида алюминия, используемого для этих образцов, составлял 10 мкм.
Микроструктуру исследовали с помощью просвечивающего электронного микроскопа JEM-2100 фирмы JEOL. Приготовление образца для ПЭМ осуществляли с помощью установки ионного утонения PIPS фирмы Gatan. Определение плотности проводили методом гидростатического взвешивания. Микротвердость измеряли с помощью твердомера 402 MVD при нагрузке 50 г и времени выдержки 10 с. Механические испытания на сжатие вспененных образцов диаметром 25 мм и высотой 10–15 мм проводили на универсальной испытательной машине Zwick Z250 при скорости 4 мм/мин.
РЕЗУЛЬТАТЫ И ИХ ОБСУЖДЕНИЕ
На рис. 1 представлены изображения порошковых частиц матричного сплава АК12 после различного времени обработки в шаровой мельнице. Из рисунка видно, что после 5–10 мин обработки размер и форма частиц примерно одинаковые. Форма частиц близка к округлой, а их средний размер составляет около 11 мкм. Однако, после 20 мин частицы матричного сплава становятся значительно крупнее, а их форма приобретает угловатый характер. Средний размер порошковых частиц становится равным почти 60 мкм, при этом отдельные частицы достигают размера более 200 мкм, что в несколько раз выше размера частиц в исходном состоянии. Значительное увеличение размера порошковых частиц после 20 мин обработки вызвано достижением стадии холодной сварки, характерной для механического легирования пластичных алюминиевых сплавов [17, 18]. Холодная сварка частиц обусловлена интенсивной пластической деформацией в результате ударного воздействия мелющих шаров.
Рис. 1.
Морфология порошковых частиц сплава АК12 после различного времени обработки в мельнице: (а) 5, (б) 10 и (в) 20 мин.

На рис. 2 показана зависимость микротвердости горячепрессованных образцов от продолжительности обработки порошка в мельнице. Здесь видно, что с увеличением времени микротвердость непрерывно возрастает, достигая после 20 мин значения 90 HV0.05. Упрочнение алюминиевого сплава в процессе шарового размола, как правило, связано с увеличением микродеформации кристаллической решетки алюминия и уменьшением размера кристаллитов [18, 19]. В нашем случае, ввиду малого времени обработки и прохождения процессов возврата при горячем прессовании, основной причиной роста микротвердости компактированных образцов может служить дисперсионное упрочнение оксидными частицами вследствие увеличения степени окисления алюминия [20–22]. При шаровом размоле алюминиевого порошка образуются новые поверхности, которые в условиях доступа кислорода воздуха подвергаются окислению [23]. Так, из рис. 3 видно, что с увеличением продолжительности обработки алюминиевого порошка в планетарной мельнице содержание кислорода в образцах возрастает. Как следствие, возрастает и количество упрочняющего оксида алюминия. Так, например, после 10 мин обработки содержание кислорода в образце достигает 0.85 мас. %, что соответствует ~1.7 мас. % Al2O3, а после 20 мин ~2.1 мас. % Al2O3.
Известно, что аморфная оксидная пленка на поверхности алюминия в нормальных условиях имеет толщину несколько нанометров [24]. При этом оксидная пленка на поверхности порошковых алюминиевых частиц может разрушаться (фрагментироваться) в результате их пластической деформации в процессе обработки в мельнице. Чередующиеся процессы сварки и разрушения алюминиевых частиц приводят к тому, что фрагменты оксидной пленки внедряются внутрь алюминиевой матрицы [20, 25, 26]. В результате последующего компактирования формируется структура, состоящая из вытянутых алюминиевых зерен (бывших порошковых частиц), разделенных сплошной или фрагментированной оксидной пленкой [27, 28]. На рис. 4а приведено светлопольное изображение тонкой структуры горячепрессованного образца, полученного с использованием порошка после 10 мин размола. Очевидно, что тонкие аморфные оксидные пленки (показаны стрелками) присутствуют на границах зерен алюминиевой матрицы, при этом сами зерна имеют размер нескольких сотен микрометров. Трансформация аморфной фазы в кристаллическую γ-Al2O3 при температуре 400°С происходит только после длительного (2 ч) отжига [26]. На рис. 4б представлено темнопольное изображение, полученное в рефлексах Si. Из анализа светлопольного и темнопольного изображений следует, что эвтектический кремний в состоянии после размола и последующего горячего прессования присутствует в материале в виде ограненных частиц размером 10–50 нм, расположенных преимущественно по границам зерен алюминия. Таким образом, структура исследуемого компактного образца состоит из субмикронных зерен алюминия с прослойками оксидных пленок и наночастиц кремния.
Рис. 4.
Светлопольное (а) и темнопольное (б) изображение микроструктуры горячепрессованного образца (10 мин обработки порошка).
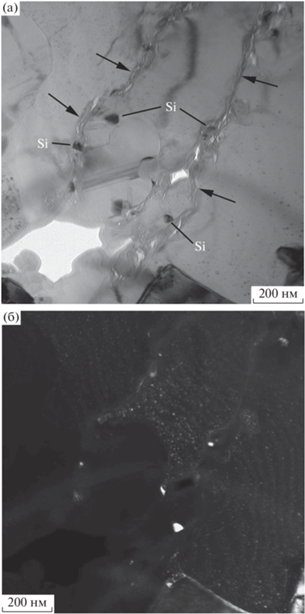
На рис. 5 представлены изображения продольных срезов вспененных образцов пеноалюминия, полученных с использованием порошков после различного времени обработки в мельнице. Из рисунка видно, что при использовании порошка в исходном состоянии до обработки в образце присутствуют довольно крупные поры (ячейки) неправильной формы (рис. 5а). C увеличением времени размола порошка до 15 мин размер пор в образце снижается одновременно с уменьшением дисперсии среднего значения (рис. 6), что говорит о том, что поры становятся более однородными по размеру. Кроме того, из рис. 5 видно, что увеличение продолжительности размола порошка приводит к росту количества пор и уменьшению толщины перемычек (стенок) между порами образца. Вместе с тем, возрастает высота образца. Так, при использовании порошка, обработанного в течение 10–15 мин, увеличение объема (высота) образца по сравнению с горячепрессованным прекурсором достигает максимального уровня около 300%. Увеличение расширения образца свидетельствует об эффективности вспенивания. Однако после 20 мин обработки порошка расширение вспененного образца резко уменьшается. Рисунок 5д показывает, что структура становится резко неоднородной как по размеру пор, так и по их форме. Так, в средней части образца обнаруживаются грубые крупноразмерные поры, а в верхней части поры имеют сплющенную форму. В целом же, средний размер пор и его дисперсия возрастают (рис. 6).
Рис. 5.
Структура продольного сечения образцов, полученных с использованием порошков после различного времени обработки (мин): а – 0; б – 5; в – 10; г – 15; д – 20.

Рис. 6.
Зависимость среднего размера пор и его дисперсии от времени окислительного размола в мельнице.
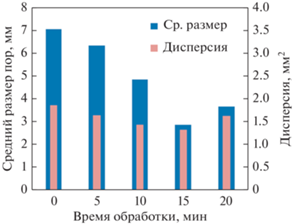
На основе проведенного анализа результатов можно сделать вывод о том, что структура образца, полученная при спекании порошка после 15 мин обработки и характеризующаяся относительно однородным распределением пор, демонстрирует наилучший эффект вспенивания. Основной причиной изменения характера структуры пеноалюминия при различной продолжительности размола порошка является разное содержание оксида в образцах. Согласно работам [14–16], улучшение качества структуры пеноалюминия при увеличении содержания кислорода обусловлено стабилизацией пены в результате формирования сети оксидных кластеров. Так, оксидные пленки, которыми покрыты внешние поверхности порошковых частиц, при вспенивании разрываются и фрагментируются в результате зарождения и роста пузырей в алюминиевом расплаве. Вместе с фрагментами, образовавшимися в процессе размола, они агломерируются и образуют оксидные кластеры, формирующие в расплаве тонкую сеть. Кластеры, расположенные на границе соседних пузырьков (ячеистой стенке), увеличивают объемную вязкость расплава и тем самым затрудняют капиллярный дренаж [29] жидкости через нее, что способствует стабилизации пены [14]. Кроме того, положительное влияние на стабильность пены также может оказывать способность оксидных кластеров увеличивать расклинивающее давление в этой ячеистой стенке, что препятствует слиянию соседних пузырьков под давлением газа в них [15]. Расклинивающее давление, противодействующее давлению роста пор, позволяет ячеистым стенкам значительно истончаться, обеспечивая дальнейший рост пор перед разрывом ячеистой стенки. Уменьшение критической толщины ячеистой стенки перед разрывом означает, что клеточные стенки будут иметь более длительное время истончения, что позволяет достичь большого расширения. Из всего вышесказанного следует, что чем больше оксидов содержится в прекурсоре, тем больший стабилизирующий эффект на пену они оказывают и тем выше качество пеноалюминия.
Однако при значительной степени окисления вспенивание и, соответственно, качество пеноалюминия, наоборот, ухудшаются. Так, после 20 мин обработки порошка наблюдается значительное уменьшение расширения образца (рис. 5д). Это указывает на то, что содержание оксида в прекурсоре, достигнутое в результате длительного размола, является чрезмерным. В этом случае давления газообразного водорода недостаточно для раздувания пор в процессе вспенивания, что может быть связано с образованием сплошной и плотной оксидной сети, которая обеспечивает механическое ограничение расширения пены и предотвращает истончение ячеистой стенки [14]. Кроме того, присутствие чрезмерно большого количества оксида на поверхности бывших порошковых частиц, сохранивших свою индивидуальность после компактирования, значительно увеличивает поверхностную вязкость и, следовательно, препятствует росту пор, что приводит к малому расширению. При этом водород может выходить по окисленным границам в атмосферу, о чем может свидетельствовать наличие плоских пор в верхней части образца, перпендикулярных направлению уплотнения при прессовании (см. рис. 5д). Другой причиной ухудшения вспенивания пеноалюминия, полученного с использованием порошка после 20 мин окислительной обработки, является увеличение среднего размера порошковых частиц, вызванное холодной сваркой. Укрупнение алюминивых частиц способствует возрастанию агломерации частиц TiH2 при смешивании и их неравномерному распределению, что негативно сказывается на характеристиках вспененного образца [30].
Подтверждением снижения эффективности вспенивания после превышения порогового значения содержания оксида алюминия служат также результаты измерения плотности пеноалюминия. На рис. 7 показана зависимость плотности образцов после вспенивания от времени обработки порошка алюминиевого сплава на воздухе. Из этого рисунка видно, с увеличением продолжительности обработки вплоть до 15 мин плотность пеноалюминия плавно снижается до 0.93 г/см3. При последующем же увеличении времени до 20 мин плотность резко возрастает до 1.44 г/см3, превышая значение для образца, полученного из порошка без обработки.
Таким образом, анализ структуры образцов пеноалюминия и их плотности показал, что продолжительность обработки порошка алюминиевого сплава на воздухе оказывает влияние на процесс вспенивания путем увеличения степени окисления, уменьшая при этом размер образующихся пор и плотность образцов. Однако существует некоторое максимальное количество кислорода, которое в соответствии с рис. 3 после 15 мин обработки порошка составляет около 1 мас. %, при превышении которого макроструктура пеноалюминия, отражающая его качество, начинает деградировать.
Следует также отметить, что увеличение содержания кислорода и образование оксида алюминия приводит к уменьшению доли чистого алюминия в матричном сплаве. Так, на рис. 8 представлено изображение микроструктуры вспененного образца, полученного с использованием порошка после 15 мин размола в воздушной атмосфере. В структуре видны первичные кристаллы кремния (указаны стрелками), которые отсутствовали в образцах из порошков без предварительного окисления и после 10 мин обработки, что может свидетельствовать о переходе сплава от эвтектического состояния к заэвтектическому.
Рис. 8.
Микроструктура образца пеноалюминия, полученного с использованием порошка после 15 мин обработки.
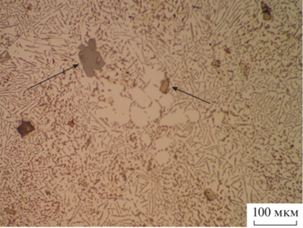
Время размола порошка через структуру вспененного образца влияет также и на прочность пеноалюминия. На рис. 9 приведены участки кривых сжатия образцов пеноалюминия при деформации до 15%. Каждая диаграмма характеризуется начальным прямолинейным участком, после которого напряжение достигает максимального значения. На прямолинейном участке, соответствующем упругой деформации, происходит упругое изгибание стенок ячеек [31]. Как видно из диаграмм, угол наклона прямолинейного участка, который условно соответствует модулю упругости, для образцов из порошка в исходном состоянии и порошка после 5 мин обработки практически равен. С дальнейшим увеличением времени обработки порошка до 15 мин сопротивляемость образцов упругой деформации сжатия снижается и, соответственно, уменьшается модуль упругости. Вместе с тем, как видно из этого рисунка, с увеличением времени обработки, начиная с 5 мин, снижается максимальное напряжение, именуемое верхним пределом текучести [32]. Это напряжение характеризует начало пластической деформации, при которой происходит последовательное разрушение перемычек и последующее схлопывание пор [31]. В результате напряжение плавно уменьшается на фоне уплотнения материала. Снижение показателей жесткости и прочности при увеличении времени обработки порошка до 15 мин обусловлено уменьшением плотности образцов (см. рис. 7), что характерно для поведения пеноалюминия [32, 33]. Чем меньше плотность, тем меньше толщина перемычек между порами и тем выше концентрация напряжений в стенках ячеек.
ЗАКЛЮЧЕНИЕ
На примере сплава АК12 показано успешное использование предварительной обработки матричного порошка в шаровой мельнице на воздухе для улучшения качества пеноалюминия. Увеличение продолжительности размола порошка алюминиевого сплава до 15 мин оказывает положительное влияние на процесс вспенивания в результате увеличения степени окисления, что отражается на уменьшении размера образующихся пор и плотности образцов пеноалюминия. Однако последующее повышение времени размола, при котором происходит укрупнение порошковых частиц в результате холодной сварки, приводит к деградации макроструктурных характеристик вспененного образца.
Работа выполнена при поддержке Минобрнауки России в рамках государственного задания (код проекта 0718-2020-0030).
Список литературы
García-Moreno F. Commercial Applications of Metal Foams: Their Properties and Production // Materials. 2016. V. 9. № 2. P. 85.
Banhart J. Manufacture, characterisation and application of cellular metals and metal foams // Prog. Mater. Sci. 2001. V. 46. № 6. P. 559–632.
Patel P., Bhingole P.P., Makwana D. Manufacturing, characterization and applications of lightweight metallic foams for structural applications: Review // Mater. Today Proc. 2018. V. 5. P. 20391–20402.
Banhart J. Manufacturing routes for metallic foams // JOM. 2000. V. 52. P. 22–27.
Rajak D.K., Kumaraswamidhas L.A., Das S. Technical overview of aluminum alloy foam // Rev. Adv. Mater. Sci. 2017. V. 48. P. 68–86.
Daoud A., Abou El-Khair M.T., Fairouz F., Mohamed E., Lotfy A. Effect of Processing Parameters on 7075 Al–Silica Particle Waste Composite Foams Produced with Recycled Aluminum Cans. // Phys. Metals Metallogr. 2021 (in press).
Surace R., De Filippis L.A.C. Investigation and Comparison of Aluminium Foams Manufactured by Different Techniques / in Advanced Knowledge Application in Practice, ed.: I. Fuerstner, Rijeka, Sciyo, 2010. P. 95–118.
Paulin I., Šuštaršič B., Kevorkijan V., Škapin S.D., Jenko M. Synthesis of aluminium foams by the powder-metallurgy process: compacting of precursors // Mater. Technol. 2011. V. 45. № 1. P. 13–19.
Duarte I., Oliveira M., Garcia-Moreno F., Mukherjee M., Banhart J. Foaming of AA 6061 using multiple pieces of foamable precursor // Colloid Surface A. 2013. V. 438. P. 47–55.
Aksenov A.A., Mansurov Yu.N., Ivanov D.O., Reva V.P., Kadyrova D.S., Shuvatkin R.K., Kim E.D. Mechanical alloying of secondary raw material for foam aluminum production // Metallurgist. 2017. V. 61. № 5–6. P. 475–484.
Li A.-B., Xu H.-Y., Geng L., Li B.-L., Tan Z.-B., Ren W. Preparation and characterization of SiCp/2024Al composite foams powder metallurgy // Trans. Nonferrous Met. Soc. China. 2012. V. 22. P. 33–38.
Guden M., Yüksel S. SiC-particulate aluminum composite foams produced from powder compacts: foaming and compression behavior // J. Mater. Sci. 2006. V. 41. P. 4075–4084.
Asavavisithchai S., Kennedy A.R. The effect of oxides in various aluminium powders on foamability // Procedia Eng. 2012. V. 32. P. 714–721.
Asavavisithchai S., Kennedy A.R. Effect of powder oxide content on the expansion and stability of PM-route Al foams // J. Colloid Interface Sci. 2006. V. 297. № 2. P. 715–723.
Körner C., Arnold M., Singer R.F. Metal foam stabilization by oxide network particles // Mater. Sci. Eng. A. 2005. V. 396. № 1–2. P. 28–40.
Asavavisithchai S., Kennedy A.R. In-Situ Oxide Stabilization Development of Aluminum Foams in Powder Metallurgical Route // High Temp. Mater. Proc. 2011. V. 30. № 1–2. P. 113–120.
Prosviryakov A.S., Shcherbachev K.D. Strengthening of mechanically alloyed Al-based alloy with high Zr contents // Mater. Sci. Eng. A. 2018. V. 713. P. 174–179.
Prosviryakov A.S., Shcherbachev K.D., Tabachkova N.Yu. Microstructural characterization of mechanically alloyed Al–Cu–Mn alloy with zirconium // Mater. Sci. Eng. A. 2015. V. 623. P. 109–113.
Rofman O.V., Prosviryakov A.S., Mikhaylovskaya A.V., Kotov A.D., Bazlov A.I., Cheverikin V.V. Processing and Microstructural Characterization of Metallic Powders Produced from Chips of AA2024 Alloy // JOM. 2019. V. 71. P. 2986–2995.
Benjamin J.S., Bomford M.J. Dispersion strengthened aluminum made by mechanical alloying // Metall. Trans. A. 1977. V. 8. P. 1301–1305.
Аксенов А.А., Солонин А.Н., Истомин-Кастровский В.В. Структура и свойства композиционных материалов на основе алюминия, получаемых методом механического легирования в воздушной атмосфере // Изв. вузов. Цвет. Металлургия. 2004. № 4. С. 58–66.
Chikova O.A., Finkel’shtein A.B., Shefer A.A. Structure and Nanomechanical Properties of the Al–Si–Fe Alloy Produced by Blowing the Melt with Oxygen // Phys. Met. Metall. 2018. V. 119. P. 685–690.
Coulet M.-V., Esposito P.H., Rufino B., Denoyel R. High-energy ball milling to enhance the reactivity of aluminum nanopowders // Mater. Lett. 2013. V. 110. P. 108–110.
Olefjord I., Nylund A. Surface analysis of oxidized aluminium – Part II: Oxidation of Aluminium in Dry and Humid Atmosphere Studied by ESCA, SEM, SAM and EDX // Surf. Interface Anal. 1994. V. 21. № 5. P. 290–297.
Benjamin J.S., Schelleng R.D. Dispersion strengthened aluminum-4 pct magnesium alloy made by mechanical alloying // Metall. Trans. A. 1981. V. 12. P. 1827–1832.
Singer R.F., Oliver W.C., Nix W.D. Identification of dispersoid phases created in aluminum during mechanical alloying // Metall. Trans. A. 1980. V. 11 P. 1895–1901.
Jiang L., Li Z., Fan G., Zhang D. A flake powder metallurgy approach to Al2O3/Al biomimetic nanolaminated composites with enhanced ductility // Scr. Mater. 2011. V. 65. № 5. P. 412–415.
Vogel T., Ma S., Liu Y., Guo Q., Zhang D. Impact of alumina content and morphology on the mechanical properties of bulk nanolaminated Al2O3–Al composites // Compos. Commun. 2020. V. 22. P. 100462.
Gergely V., Clyne T.W. Drainage in standing liquid metal foams: modelling and experimental observations // Acta Mater. 2004. V. 52. № 10. P. 3047–3058.
Guo Z.-Q., Yao G.-C., Yu H.-J., Li H.-B. Influences of powder particle size on preparation of foamed aluminum by powder compact foaming method // J. Northeastern University. 2007. V. 28. № 8. P. 1163–1166.
Yu H., Guo Z., Li B., Yao G., Luo H., Liu Y. Research into the effect of cell diameter of aluminum foam on its compressive and energy absorption properties // Mater. Sci. Eng. A. 2007. V. 454–455. P. 542–546.
Banhart J., Baumeister J. Deformation characteristics of metal foams // J. Mater. Sci. 1998. V. 33. P. 1431–1440.
Malekjafarian M., Sadrnezhaad S.K. Closed-cell Al alloy composite foams: Production and characterization // Mater. Des. 2012. V. 42. P. 8–12.
Дополнительные материалы отсутствуют.
Инструменты
Физика металлов и металловедение