Физика металлов и металловедение, 2022, T. 123, № 5, стр. 569-576
Структура и ударная вязкость сварных соединений, выполненных из трубной стали с применением гибридной лазерно-дуговой сварки
Н. А. Терещенко a, *, И. Л. Яковлева a, М. А. Федоров b, А. Б. Гизатуллин b, Т. С. Есиев c
a Институт физики металлов УрО РАН
620108 Екатеринбург, ул. С. Ковалевской, 18, Россия
b ПАО “ЧТПЗ”
454129 Челябинск, ул. Машиностроителей, 21, Россия
c ООО “Газпром ВНИИГАЗ”
142717 Московская обл., п. Развилка, г.о. Ленинский, здание 15, строение 1, Россия
* E-mail: tereshchenko@imp.uran.ru
Поступила в редакцию 11.11.2021
После доработки 23.12.2021
Принята к публикации 03.01.2022
- EDN: GTRNCF
- DOI: 10.31857/S0015323022050163
Аннотация
Исследованы сварные соединения труб диаметром 1420 мм с толщиной стенки 30 мм, изготовленные по двум различным технологиям: комбинирование дуговой и лазерной сварки при выполнении корневого шва с последующей дуговой сваркой под слоем флюса при наложении облицовочных швов и методом двусторонней дуговой сварки под слоем флюса. Показано, что при использовании первой технологии в сварных соединениях формируется дисперсная структура на основе бейнита, что обеспечивает вязкий характер разрушения и повышенный уровень ударной вязкости при различном положении надреза относительно центра сварного шва.
ВВЕДЕНИЕ
В настоящее время магистральные трубопроводы для транспортировки нефти и газа выполняются из низкоуглеродистых низколегированных сталей. Передовые технологии производства листового проката, включающие контролируемую прокатку и ускоренное охлаждение (Thermo-Mechanical Controlled Processing), позволяют получать трубные стали различного уровня прочности; среди которых наиболее востребованы трубной промышленностью стали класса прочности К60. Практика их производства показывает, что применение современного оборудования надежно гарантирует комплекс стандартных показателей, регламентированных требованиями к химическому составу, свариваемости и механическим свойствам трубных сталей [1–3].
При больших объемах транспортируемых энергоресурсов увеличение пропускной способности трубопровода достигается за счет повышения давления транспортируемого реагента и увеличения диаметра трубы. Технологический цикл изготовления труб большого диаметра включает операцию сварки. Широко применяемый для таких изделий способ дуговой сварки плавящимися электродами под слоем флюса (ДСФ) предполагает выполнение многопроходных швов и сопровождается большим тепловложением в сварочную ванну, при этом вблизи сварного шва формируется протяженная зона термического влияния (ЗТВ) с неоднородной микроструктурой и повышенным уровнем микроискажений [1, 4, 5].
Перспективный метод гибридной лазерно-дуговой сварки (ГЛДС) позволяет сваривать листовой прокат больших толщин с малым тепловложением [6, 7]. В процессе ГЛДС одновременно используется два источника энергии: лазерный луч и электрическая дуга, лазерный луч испаряет металл, возникший из металлической плазмы, факел стабилизирует дуговой разряд, в итоге образуется сварной шов с глубоким проплавлением металла [8–10]. Применение технологии ГЛДС для производства труб большого диаметра целесообразно с экономических позиций, так как ГЛДС отличается от традиционной сварки ДСФ повышенной производительностью [7, 9].
Металловедческий аспект применения ГЛДС связан с риском появления закалочных структур и локального охрупчивания металла в зоне термического влияния сварного шва из-за высоких скоростей охлаждения, реализуемых при этом способе сварки [8, 11, 12]. Использование ГЛДС в сочетании с последующим выполнением облицовочных швов методом ДСФ способствует получению преимущественно бейнитной структуры в металле околошовной зоны и обеспечивает более высокое сопротивление хрупкому разрушению [13]. Сварка облицовочных швов после сварки корневого шва выполняется на минимальных погонных энергиях, что позволяет минимизировать ЗТВ в отличие от классической многодуговой двусторонней сварки под слоем флюса. Однако для промышленного внедрения комбинированной (ГЛДС + ДСФ) технологии необходимо обеспечить стабильность и воспроизводство значений ударной вязкости, как наиболее важной характеристики для конструктивной прочности сварного соединения и изделия в целом. Настоящая работа призвана способствовать решению этой проблемы, для этого необходимо изучить траекторию движения трещины при ударном нагружении сварного соединения, изготовленного с применением метода ГЛДС, выявить механизмы разрушения металла в отдельных его зонах.
МАТЕРИАЛ И МЕТОДИКИ ИССЛЕДОВАНИЙ
Материалом для исследования служили сварные соединения труб диаметром 1420 мм с толщиной стенки 30 мм. Сварку осуществляли в заводских условиях по двум различным технологиям. Для первой группы сварных соединений применяли комбинированную технологию: корневой шов выполняли ГЛДС в среде защитных газов с применением плавящегося электрода, внутренний и наружный швы выполняли автоматической ДСФ. Вторую группу сварных соединений изготавливали по стандартной технологии методом двусторонней автоматической ДСФ.
Сварные соединения, изготовленные с применением различных технологий сварки, были выполнены из отдельных листов низкоуглеродистой низколегированной стали одной плавки, подвергнутых контролируемой термо-механической обработке. Химический состав стали в листах (табл. 1) практически одинаков и соответствует требованиям ГОСТ ISO 3183–2015 [14].
Таблица 1.
Химический состав стали, мас. %
№ п/п | С | Mn | Si | Cr | Ni | Cu | V | Mo | Ti | Nb |
---|---|---|---|---|---|---|---|---|---|---|
1 | 0.096 | 1.68 | 0.26 | 0.033 | 0.065 | 0.043 | 0.003 | 0.148 | 0.015 | 0.053 |
2 | 0.092 | 1.68 | 0.26 | 0.034 | 0.065 | 0.043 | 0.003 | 0.147 | 0.014 | 0.052 |
Идентичность химического состава стали обеспечивает одинаковые показатели свариваемости Сэ = 0.42 и Рcm = 0.20 и близкие значения механических характеристик (табл. 2), удовлетворяющие условиям нормативной документации СТО Газпром 2-4.1-713-2013 [15].
Таблица 2.
Механические свойства сталей после контролируемой термомеханической обработки
№ п/п | σв, МПа | σ0.2, МПа | δ, % | δравн, % | ψ, % | σ0.2/σв | KCU –60, Дж/см2 | KCV –20, Дж/см2 | HV10 |
---|---|---|---|---|---|---|---|---|---|
1 | 610 | 530 | 23 | 11.4 | 35 | 0.87 | 333 | 339 | 211 |
2 | 620 | 540 | 24 | 10.5 | 35 | 0.87 | 378 | 338 | 211 |
Ударную вязкость сварных соединений определяли на образцах Шарпи с V-образным надрезом типа IX. Отдельные образцы различались ориентацией механического надреза относительно центра сварного соединения: он располагался по центру сварного шва, вдоль линии сплавления. Испытания проводили на маятниковом копре серии PSW и RKP-450.Т при температуре –40°С. Охлаждение образцов осуществляли в термостатирующем лабораторном устройстве LOIP FT-311-80. Условия испытаний соответствовали ГОСТ 6996-66 [16].
Макроструктуру сварных соединений изучали на шлифах после травления в 4%-ном растворе азотной кислоты в этиловом спирте с использованием оптического микроскопа NEOРHOT-30. Микроструктуру и изломы образцов сварных соединений после испытаний изучали с применением сканирующего электронного микроскопа “ThermoFisher Scientific”. Сведения, полученные в ходе фрактографического исследования, сопоставляли с данными металлографии, полученными с торцевой поверхности фрагмента ударного образца после ударного нагружения.
Твердость измеряли по методу Виккерса при нагрузке 10 кгс.
РЕЗУЛЬТАТЫ ИССЛЕДОВАНИЙ И ИХ ОБСУЖДЕНИЕ
Структура металла сварных соединений. Макроструктура сварных соединений представлена на рис. 1. После травления поверхность шлифа включает отдельные области, различающиеся по характеру контраста. Основной металл имеет слабовыраженную полосчатую структуру, характерную для трубных сталей после контролируемой термомеханической обработки. Основу структуры составляет феррито-бейнитная смесь с небольшим количеством вырожденного перлита, средний размер ферритного зерна равен 2–4 мкм. Твердость такой структуры составляет 211 HV. Сварное соединение, изготовленное по комбинированной технологии, содержит корневой шов ГЛДС и облицовочные швы ДСФ, каждый шов окаймляет зона его термического влияния, за которой располагается основной металл (рис. 1а).
Рис. 1.
Макроструктура сварных соединений, выполненных с применением комбинированной технологии (а) и стандартной технологии (б): 1 – шов ГЛДС; 2 – внутренний облицовочный шов ДСФ; 3 – наружный облицовочный шов ДСФ.
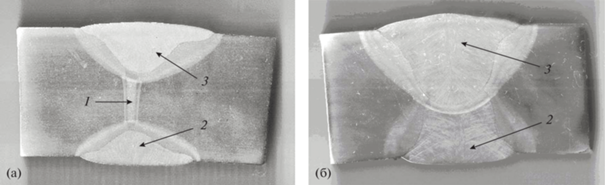
При осуществлении ГЛДС тепловложение реализуется на малой площади; ширина шва ГЛДС изменяется от 1.8 мм вблизи внутреннего облицовочного шва до 2.0 мм у наружного шва ДСФ (рис. 1а, область 1). В процессе кристаллизации расплавленного металла сформировалась зона столбчатых зерен шириной 40–60 мкм, ориентированных от линии сплавления к центру шва. Границы зерен окаймлены ферритной сеткой, в теле зерен образовались чрезвычайно дисперсные кристаллы бейнитной α-фазы, рис. 2а. Переплавленный металл шва ограничен линией сплавления, за которой располагается зона термического влияния шва ГЛДС с градиентной структурой протяженностью от 0.5 до 1.0 мм. Вдоль линии сплавления при температурах, близких к температуре плавления, образовался участок перегрева с крупнозернистой структурой, рис. 2б. Размер бывшего аустенитного зерна на участке перегрева сопоставим с шириной столбчатых зерен в металле шва и достигает 40–60 мкм, внутри зерен преобладает структура бейнита реечной морфологии. Средняя твердость металла шва и зоны термического влияния составляет 257 HV и 274 HV соответственно. Такой уровень твердости сформировался в результате фазовой перекристаллизации при охлаждении после сварочного нагрева ГЛДС, а также под влиянием процессов отпуска при наложении облицовочных швов ДСФ.
Рис. 2.
СЭМ-изображение структуры локальных зон сварного соединения, изготовленного по комбинированной технологии: а – корневой шов ГЛДС, б – зона термического влияния шва ГЛДС на участке перегрева; в – наружный облицовочный шов ДСФ; г – зона термического влияния наружного облицовочного шва ДСФ на участке перегрева.
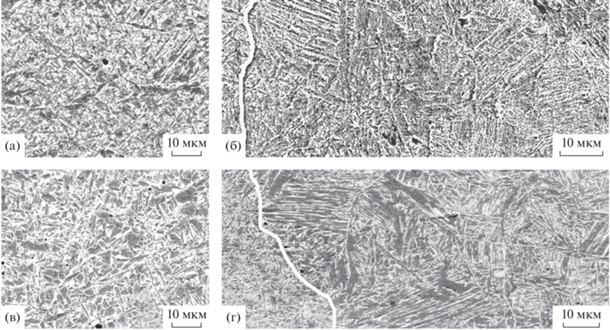
В силу специфики термических циклов ДСФ [5] облицовочные швы значительно превосходят по площади шов ГЛДС (рис. 1а, области 2, 3). Ширина наружного облицовочного шва увеличивается от 4–5 мм у вершины до 30 мм у поверхности. Средняя твердость металла шва ДСФ составляет 232 HV, что на 10% ниже, чем твердость металла шва ГЛДС. Структура металла шва представлена на рис. 2в. Столбчатое строение металла швов ДСФ и ГЛДС подобны, однако, масштаб структуры отличается. Ширина столбчатых кристаллов в шве ДСФ достигает 80–100 мкм, что в 2 раза больше, чем в шве ГЛДС. Кристаллы бейнитной α-фазы в теле зерна заметно крупнее. Зона термического влияния повторяет форму шва ДСФ, из-за большого тепловложения и малых скоростей охлаждения после сварочного нагрева ее ширина на отдельных участках изменяется от 2 до 8 мм. Средний размер бывшего аустенитного зерна на участке перегрева составляет 100–120 мкм, морфология продуктов распада аустенита отличается большим разнообразием и в равной пропорции включает кристаллы реечного и глобулярного бейнита (рис. 2г). Твердость металла в ЗТВ шва ДСФ находится в интервале 231–247 HV.
В сварном соединении, выполненном по стандартной технологии, переплавленный металл присутствует во внутреннем и наружном швах ДСФ (рис. 1б). Состояния металла в швах ДСФ и зоне их термического влияния качественно подобны, при этом размер “бывшего” аустенитного зерна вблизи линии сплавления наружного облицовочного шва достигает 150–200 мкм, а твердость составляет 224 HV.
Ударная вязкость и фрактография. Результаты ударных испытаний образцов сварных соединений, изготовленных с применением комбинированной и классической технологий сварки (табл. 3), указывают на то, что все они отвечают установленным требованиям KCV–40 ≥ 50 Дж/см2 [15]. В связи с тем, что структура сварных соединений крайне неоднородна, при всех способах сварки значения ударной вязкости в существенной степени зависят от взаимного расположения сварного шва и надреза в образце. Однако в целом, данные таблицы свидетельствуют о том, что металл в шве ГЛДС и вблизи него демонстрирует значительно более высокий уровень этой характеристики относительно металла шва ДСФ. Такое различие в величине ударной вязкости обусловлено особенностями развития разрушения в отдельных областях сварных соединений.
Таблица 3.
Ударная вязкость образцов сварных соединений
Технология сварки | Ориентация надреза | KCV –40, Дж/см2 |
---|---|---|
Комбинированная технология с применением ГЛДС и ДСФ | По шву ГЛДС | 315 |
По линии сплавления шва ГЛДС | 311 | |
Стандартная технология ДСФ | По центру наружного шва ДСФ | 144 |
По линии сплавления наружного шва ДСФ | 56 |
Образцы, содержащие шов ГЛДС, отличаются самыми высокими значениями ударной вязкости KCV–40 = 315–311 Дж/см2. Процесс их разрушения энергоемок по всей траектории движения магистральной трещины.
В образце с надрезом по металлу шва ГЛДС поверхность разрушения, возникшая под надрезом при зарождении магистральной трещины, составляет не менее 20% от площади излома, она выходит за пределы металла шва, пересекает линию сплавления и зону термического влияния шва (рис. 3а).
Рис. 3.
Макроструктура фрагментов образцов сварных соединений после ударных испытаний: а, б – комбинированная технология сварки с надрезом по металлу шва ГЛДС (а), по линии сплавления шва ГЛДС (б),); в, г – стандартная технология сварки с надрезом по металлу шва ДСФ (в), по линии сплавления шва ДСФ (г). Цифрами обозначены: 1 – надрез; 2 – металл шва; 3 – зона термического влияния сварного шва.
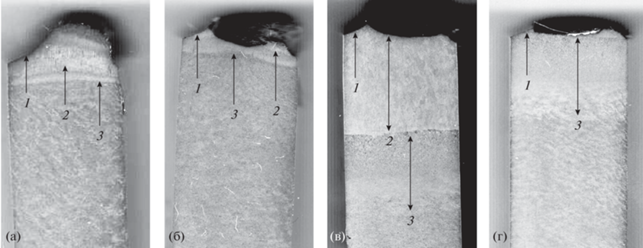
На фрактограммах, снятых в этой области излома, обнаруживаются крупные ямки, возникшие по механизму вязкого разрушения путем образования и слияния микропор (рис. 4а). Центральная область излома, образованная на этапе распространения магистральной трещины, проходит по основному металлу сварного соединения (рис. 3а). Рельеф поверхности разрушения включает несколько “трещин расслоения” с прямолинейными гребнями отрыва (рис. 4б). Поверхности, ориентированные вдоль направления удара, содержат ямки, сгруппированные в строчки, параллельные гребням отрыва (рис. 4в). Они чередуются с участками квазихрупкого разрушения, вытянутыми перпендикулярно направлению удара (рис. 4г). Процесс разрушения чрезвычайно энергоемок за счет образования протяженной зоны вязкого зарождения трещины и поглощения энергии на боковых гранях трещин расслоения [17].
Рис. 4.
Фрактограммы образца сварного соединения с надрезом по шву ГЛДС: а – область зарождения трещины; б, в, г – область развития трещины.
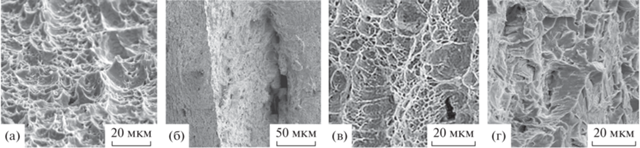
В образце с надрезом по линии сплавления шва ГЛДС область зарождения магистральной трещины по ширине не превышает 0.5 мм, ее поверхность образована плоскими мелкими чашечками с редкими фасетками квазискола (рис. 5а). На этапе развития трещина неоднократно меняет вектор своего движения: в начальный момент разрушения смещается в зону термического влияния, проходит по металлу шва вблизи линии сплавления, вновь переходит в зону термического влияния и далее – в основной металл (рис. 3б). Область развития трещины представлена бугристой поверхностью ямочного разрушения с обилием вторичных трещин (рис. 5б). Высокая величина ударной вязкости данного образца обусловлена сочетанием двух факторов. Наряду с вязким механизмом разрушением стали по телу зерна на энергоемкость разрушения оказывает влияние “эффект составного образца”, когда отдельные зоны сварного соединения разделяют поперечное сечение образца на “слои” переменной толщины с различной структурой, изменяют напряженное состояние в вершине движущейся трещины и инициируют появление вторичных трещин [18, 19].
Рис. 5.
Фрактограммыв образца сварного соединения с надрезом по линии сплавления шва ГЛДС: а – область зарождения трещины; б – область развития трещины.
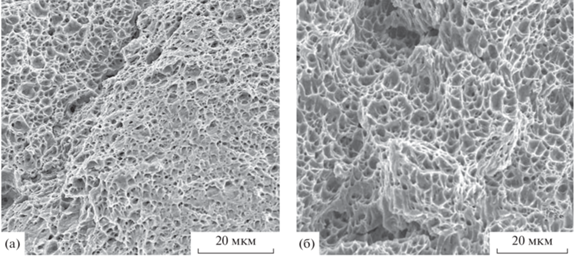
Самые низкие значения ударной вязкости KCV–40 = 144–56 Дж/см2 демонстрируют образцы сварных соединений, выполненных по традиционной технологии. В образце с надрезом по центру шва ДСФ трещина движется прямолинейно (рис. 3в). Область зарождения трещины ограничена шириной 0.5 мм, имеет ямочный рельеф (рис. 6а). Центральная часть излома представляет собой развитую поверхность с многочисленными вторичными трещинами. Развитие магистральной трещины происходит по механизму квазискола, разрушение протекает как по телу зерна, так и по границам зерен (рис. 6б). Группы фасеток объединены преимущественной плоскостью залегания, близкой к кристаллографической плоскости скола в ОЦК-металлах типа (100). Размер фасеток ≈100 мкм сопоставим с шириной столбчатых зерен, сформированных в процессе кристаллизации сварного шва, а овальная форма таких областей воспроизводит поперечное сечение литых зерен. Вторичные трещины зарождаются на границах зерен и перемещаются до пересечения с другой группой плоскостей типа (100) с неблагоприятной ориентировкой, так образуются конгломераты фасеток в смежных зернах.
Рис. 6.
Фрактограммы изломов образцов сварных соединений с надрезом по металлу шва (а, б) и линии сплавления шва ДСФ (в, г): а, в – область зарождения трещины; б, г – область развития трещины.
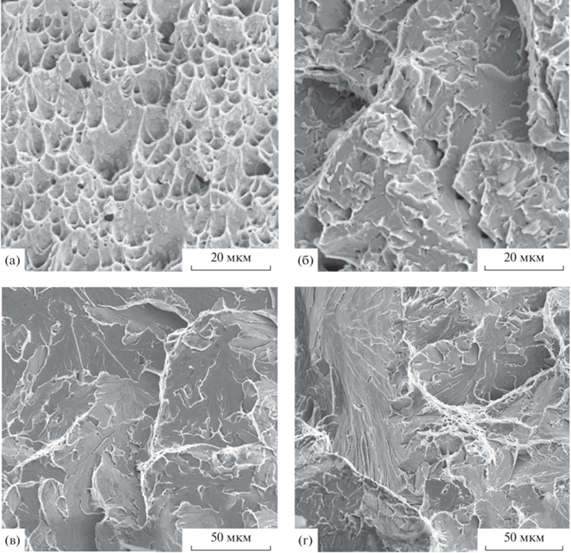
На разрушение образца с надрезом, нанесенном по линии сплавления шва ДСФ, затрачивается минимальное количество работы. Вектор движения трещины соответствует направлению удара (рис. 3г). Область зарождения магистральной трещины практически отсутствует. Вся поверхность разрушения, включая область в непосредственной близости от надреза, образована по механизму хрупкого интеркристаллитного разрушения (рис. 6в, 6г).
ЗАКЛЮЧЕНИЕ
Проведен сравнительный анализ структуры, ударной вязкости и характера разрушения сварных соединений труб диаметром 1420 мм с толщиной стенки 30 мм, изготовленных по комбинированной технологии при сочетании ГЛДС и ДСФ, а также по классической технологии методом двусторонней ДСФ.
Выявлено, что при применении ГЛДС и ДСФ фазовый состав переплавленного металла и зоны термического влияния в сварном соединении идентичен, а масштаб структуры существенно различается. Столбчатые зерна металла шва ГЛДС заполнены кристаллами бейнитной α-фазы и окантованы сеткой феррита, в зоне термического влияния сформировалась полностью бейнитная структура. Ширина столбчатых кристаллов, как и размер “бывшего” аустенитного зерна на участке перегрева составляет 40–60 и 150–200 мкм в швах ГЛДС и ДСФ соответственно.
Установлено, что образцы сварных соединений, содержащих шов ГЛДС, демонстрируют повышенный уровень ударной вязкости, в значениях которой заметную долю составляет удельная работа зарождения трещины. Дисперсность структуры, свойственная металлу шва ГЛДС и зоне его термического влияния, способствует реализации вязкого механизма разрушения по всей траектории движения магистральной трещины. Малая энергоемкость разрушения, присущая образцам сварных соединений, выполненных по стандартной технологии ДСФ, определяется ограниченностью этапа зарождения трещины и квазихрупким характером излома, рельеф которого воспроизводит грубозернистую структуру металла шва ДСФ и зоны его термического влияния.
Работа выполнена в рамках государственного задания МИНОБРНАУКИ России (тема “Структура”, № АААА-А18-118020190116-6).
Список литературы
Эфрон Л.И. Металловедение в “большой” металлургии. Трубные стали. М.: Металлургиздат, 2012. 696 с.
Liu C., Bhole S.D. Challenges and developments in pipeline weldability and mechanical properties // Sci. Techn. of Welding and Joining. 2013. V. 18. № 2. P. 169–181.
Shigeru E., Naoki N. Development of thermo-mechanical control process (TMCP) and high performance steel in JFE // JFE technical Report. 2015. № 20. P. 1–7.
Борцов А.Н., Шабалов И.П., Величко А.А., Ментюков К.Ю., Уткин И.Ю. Особенности многоэлектродной сварки под слоем флюса при производстве высокопрочных толстостенных труб // Металлург. 2013. № 4. С. 69–76.
Ефименко Л.А., Есиев Т.С., Пономаренко Д.В., Севастьянов С.П., Уткин И.Ю. Влияние термической обработки на ударную вязкость металла сварных соединений труб, выполненных многодуговой сваркой под слоем флюса // Металлург. 2018. № 3. С. 59–63.
Cristina Churiaque, Mariane Chludzinski, Manuel Porrua-Lara, Antonio Dominguez-Abecia, Francisco Abad-Fraga, Jose Maria Sánchez-Amaya. Laser Hybrid Butt Welding of Large Thickness Naval Steel // Metals. 2019. V. 9. № 1. P. 100. https://doi.org/10.3390/met9010100
Bappa Acherjee. Hybrid laser arc welding: State-of-art review // Optics and Laser Technology. 2018. V. 99. P. 60–71.
The Theory of Laser Materials Processing. Heat and Mass Transfer in Modern Technology. / By ed. John Dowden. Springer, 2009. 396 p.
Романцов А.П., Федоров М.А., Черняев А.А., Котлов А.О. Способ гибридной лазерно-дуговой сварки. Патент РФ № 2640105. Гос. Регистрация от 26.12.2017.
Гоок С.Э., Гуменюк А.В., Ретмайер М. Гибридная лазерно-дуговая сварка высокопрочных трубных сталей прочности API X80 и X120 // Глобальная ядерная безопасность. 2017. № 1. С. 21–35.
Górka J. Structure and Properties of Hybrid Laser arc Welded t-joints (laser beam – mag) in Thermo-mechanical Control Processed Steel S700mc of 10 mm Thickness // Arch. Metall. Mater. 2018. V. 63. № 3. P. 1125–1131.
Уткин И.Ю., Ефименко Л.А., Бобринская В.Ю., Капустин О.Е. Оценка роли ванадия и молибдена в изменении кинетики распада аустенита и механических свойств смоделированной зоны перегрева малоуглеродистых ниобийсодержащих сталей // ФММ. 2021. Т. 122. № 7. С. 769–775.
Ефименко Л.А., Капустин О.Е., Пономаренко Д.А., Уткин И.Ю., Федоров М.А., Романцев А.И. Особенности формирования структуры и свойств сварных соединений при лазерно-гибридной сварке продольных стыков труб // Металлург. 2020. № 11. С. 63–68.
ГОСТ ISO 3183-2015. Трубы стальные для трубопроводов нефтяной и газовой промышленности.
СТО Газпром 2-4.1-713-2013. Технические требования к трубам и соединительным деталям.
ГОСТ 6996-66. Методы определения механических свойств.
Kimura Y., Inoue T., Yin F., Tsuzaki K. Inverse temperature dependence of toughness in an ultrafine grain-structure steel // Science. 2008. V. 320. № 5879. P. 1057–1060.
Долженко А.С., Долженко П.Д., Беляков А.Н., Кайбышев Р.О. Микроструктура и ударная вязкость высокопрочной низколегированной стали после темпформинг // ФММ. 2021. Т. 122. № 10. С. 1091–1100.
Яковлева И.Л., Терещенко Н.А., Мирзаев Д.А., Панов А.В., Шабуров Д.В. Ударная вязкость и пластические свойства составных слоистых образцов по сравнению с монолитными // ФММ. 2007. Т. 104. № 2. С. 212–221.
Дополнительные материалы отсутствуют.
Инструменты
Физика металлов и металловедение