Физика металлов и металловедение, 2022, T. 123, № 6, стр. 643-648
Влияние примесей на фазовый состав и свойства сплава Al–Cu–Gd
М. В. Барков a, О. И. Мамзурина a, М. В. Главатских a, Р. Ю. Барков a, *, А. В. Поздняков a
a НИТУ “МИСиС”
119049 Москва, Ленинский просп., 4, Россия
* E-mail: barkov@misis.ru
Поступила в редакцию 13.12.2021
После доработки 25.01.2022
Принята к публикации 04.02.2022
- EDN: OYTOFB
- DOI: 10.31857/S0015323022060031
Аннотация
Проведено исследование влияния примесей железа и кремния на фазовый состав и свойства нового квазибинарного сплава системы Al–Cu–Gd. Микроструктура литого сплава представлена алюминиевым твердым раствором, дисперсной эвтектикой с фазой Al8Cu4Gd, в которой растворяется около 1% примеси железа, и фазой (AlGdCuSi), примерного состава Al80Gd5Cu8Si5. Высокотемпературная гомогенизация при 600°С приводит к фрагментации и сфероидизации фаз кристаллизационного происхождения, в том числе и фазы образованной примесью кремния. При отжиге деформированных листов при температурах до 250°С разупрочнение, связанное с прохождением процессов возврата и полигонизации, в сплавах с примесями и без протекает примерно одинаково. Полностью структура рекристаллизуется после часового отжига при 300°, при этом средний размер зерна составляет 7.5 мкм и незначительно больше после отжига при 550°С – 11 мкм. После отжига прокатанных сплавов при 100–150°С предел текучести составляет 227–276 МПа при удлинении более 5%. Примеси железа и кремния не оказывают негативного влияния на микроструктуру и механические свойства нового сплава.
ВВЕДЕНИЕ
Наличие неизбежных для алюминия примесей железа и кремния может существенно влиять на фазовый состав и, соответственно, структуру алюминиевых сплавов. Морфология фаз с примесями меняется от пластинчато-игольчатой до разветвленной компактной, что может существенно сказаться на пластичности [1, 2]. При разработке новых сплавов необходимо обязательно учитывать влияние примесей. Исследования последних лет показали перспективность систем Al–Ce–Cu [3, 4], Al–Cu–Y [5–10], Al–Cu–Er [6, 9–14], Al–Cu–Yb [15] и Al–Cu–Gd [15] для разработки на их основе новых высокотехнологичных и жаропрочных литейных и деформируемых сплавов. Тройные квазибинарные сплавы этих систем имеют узкий интервал кристаллизации, а эвтектические фазы высокую термическую стабильность [5, 6, 11, 15]. Дополнительное легирование позволяет существенно повысить их прочностные характеристики [7–10, 12–14]. Авторы работ [16, 17], изучая влияние примесей на фазовый состав и свойства тройных сплавов Al–Cu–Y и Al–Cu–Er, выявили образование в процессе кристаллизации достаточно компактных фаз Al11Cu2Y2Si2 и Al3Er2Si2. Железо при этом растворялось в другой фазе кристаллизационного происхождения, не образуя грубых пластинчатых частиц. В дополнение кремний в сплавах алюминия с редкоземельными металлами [18–20] приводит к ускорению процессов упрочнения при отжиге. В работе [21] установлено, что добавка иттрия в сплав со скандием и цирконием приводит к образованию фазы (Al,Y,Fe,Si)/Al10Fe2Y, при этом скандий полностью растворяется в матрице. Наличие примесей в сплаве Al–Y–Er–Zr–Sc несколько снижает эффект упрочнения из-за частичного связывания циркония, эрбия и иттрия в фазы кристаллизационного происхождения с иттрием и эрбием [22]. Малые добавки гадолиния в алюминиевых сплавах, легированных так же цирконием и/или скандием, позволяют повысить эффект от дисперсионного упрочнения [23–26].
Настоящее исследование посвящено изучению влияния примесей железа и кремния на фазовый состав и механические свойства деформируемого сплава Al–4.5Cu–2.5Gd.
МЕТОДИКА ЭКСПЕРИМЕНТОВ
Сплав состава Al–4.5Cu–2.5Gd–0.15Fe–0.15Si (AlCuGdFeSi) выплавлен в печи сопротивления из Al (99.7%), меди (99.9%) и лигатуры Al–10Gd (все составы указаны в мас. %). Расплав заливали в медную водоохлаждаемую изложницу с внутренней полостью 20 × 40 × 100 мм при скорости охлаждения около 15 K/с. Термическую обработку проводили в печах “Nabertherm” и “Snol” с вентилятором и точностью поддержания температуры 1°С. Подготовку шлифов для микроструктурных исследований производили на шлифовально – полировальной установке Struers Labopol-5. Микроструктурные исследования и идентификацию фаз проводили на световом микроскопе (СМ) Zeiss и сканирующем электронном микроскопе (СЭМ) TESCAN VEGA 3LMH с использованием энерго-дисперсионного детектора X-Max 80. Калориметрический анализ проводили на дифференциальном сканирующем калориметре (ДСК) Labsys Setaram. Рентгенофазовый анализ проведен с использованием дифрактометра Brucker D8 Advanced. Слиток после термической обработки (гомогенизации при 600°С в течение 3 ч с последующей закалкой в воде) был прокатан до толщины 10 мм при температуре 440°С и до 1 мм при комнатной температуре. Отжиг после прокатки проводили при температурах 100–550°С в течение различного времени. Твердость измеряли стандартным методом Виккерса при нагрузке 49 H и выдержке 15 с. Испытания на растяжение проводили на машине Zwick/Roell Z250 серии Allround с автоматическим датчиком продольной деформации.
РЕЗУЛЬТАТЫ ЭКСПЕРИМЕНТОВ И ОБСУЖДЕНИЕ
Рисунок 1 иллюстрирует микроструктуру и фазовый состав исследуемого сплава AlCuGdFeSi в литом состоянии. Микроструктура представлена алюминиевым твердым раствором (Al), дисперсной эвтектикой и отдельными более светлыми включениями фазы кристаллизационного происхождения (рис. 1а). Средняя концентрация меди в (Al) составляет 1.4%, гадолиния – 0.2% и кремния – 0.1%. Дисперсная эвтектика состоит из (Al) и фазы, обогащенной медью и гадолинием, в которой также определено около 1% Fe. Основной эвтектической фазой является фаза Al8Cu4Gd, как и в сплаве без примесей [15]. На рентгенограмме определены пики этой фазы в интервале углов 40°–41° (серая кривая для сплава AlCuGdFeSi). Для сравнения на рис. 1б (черная кривая) также приведена рентгенограмма сплава того же состава без примесей. Более светлые включения в микроструктуре обогащены медью, гадолинием и кремнием. На рентгенограмме сплава с примесями выявлены пики, которых не было в сплаве AlCuGd на углах 31°, 33.5° и 36.8°. Данные пики соответствуют фазе образованной примесью кремния (AlGdCuSi). Согласно точечному анализу в СЭМ эта фаза содержит около 60.5Al, 23Gd, 13Cu и 3.5Si (в массовых %), что в атомных процентах составит 82.5Al, 5.4Gd, 7.5Cu и 4.6Si. С учетом, что фаза достаточно дисперсная, содержание в ней легирующих элементов занижено на фоне алюминиевой матрицы. Однако соотношение элементов в фазе в разных частицах примерно постоянно. И в первом приближении фазу можно записать как Al80Gd5Cu8Si5.
Рис. 1.
Литая микроструктура и распределение легирующих элементов между фазами (а) (СЭМ) и рентгенограмма (б) сплава AlCuGdFeSi (черная линия – сплав AlCuGd, серая – исследуемый сплав AlCuGdFeSi).
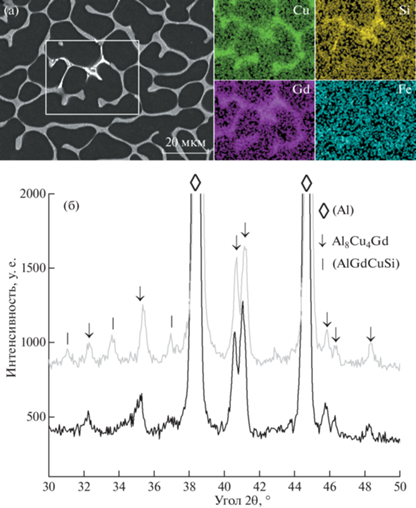
Температура солидуса сплава AlCuGdFeSi составляет 612°С, а ликвидуса – 633°С (рис. 2).
В соответствие с этим, гомогенизацию слитка проводили при температуре 600°С. В процессе гомогенизации перед закалкой происходит растворение неравновесного избытка фаз кристаллизационного происхождения, фрагментация и сфероидизация равновесных интреметаллидов. После 1 ч гомогенизации (рис. 3а) размер частиц избыточных фаз составляет около 1 мкм, увеличение времени до 3 ч приводит к их незначительному росту до 1.5 мкм. При этом частицы фазы (AlGdCuSi) также приобретают компактную сферическую форму (рис. 3б). Шестичасовая гомогенизация при 600°С приводит к еще большему росту частиц, но при этом состав алюминиевого твердого раствора уже не изменяется. После 1 ч содержание меди составляет 1.5%, а после 3 ч выдержки достигает максимума в 1.7%.
Рис. 3.
Микроструктуры сплава AlCuGdFeSi после закалки с 600°С с выдержками 1 (а), 3 (б) и 6 (в) часов; для (б) представлено распределение легирующих элементов между фазами в выделенном прямоугольнике.

Зависимости твердости холоднодеформированного сплава от времени отжига при 100, 180 и 210°С и от температуры отжига в течение 1 ч представлены на рис. 4. Для сравнения результаты сопоставлены с характеристиками сплава AlCuGd близкого состава без примесей [15]. После прокатки твердость листа сплава AlCuGd составляет 103 HV, а сплава с примесями примерна та же – 101 HV. Разупрочнение при низких температурах до 250°С в обоих сплавах протекает примерно одинаково. Твердость резко снижается после 0.5 ч с постепенным замедлением после 2 ч и практически не изменяется до 6 ч отжига (рис. 4а). Разупрочнение при температурах до 250°С связано с прохождением процессов возврата и полигонизации. Зеренная структура после часа отжига при 250°С представлена вытянутыми в направлении прокатки волокнами (вставка микроструктуры на рис. 4б). Полностью рекристаллизованная структура со средним размером зерна 7.5 мкм выявлена после отжига при 300°С (вставка микроструктуры на рис. 4б). При увеличении температуры отжига до 550°С размер зерна несущественно увеличивается до 11 мкм. При этом сплав с примесями имеет несколько более высокую твердость в сравнение со сплавом близкого состава без примесей. Похожие результаты получены при исследовании влияния примесей на свойства сплавов AlCuY [16] и AlCuEr [17].
Рис. 4.
Зависимости твердости холоднодеформированных сплавов от времени отжига при 100, 180 и 250°С (а) и от температуры отжига в течение 1 ч (б) (пунктирные линии для сплава AlCuGd, сплошные линии для сплава AlCuGdFeSi).
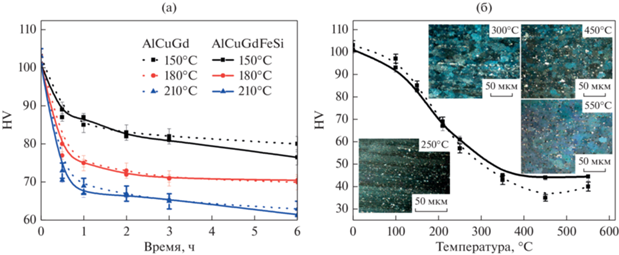
Таблица 1.
Характеристики механических свойств после испытаний на одноосное растяжение в деформированном и отожженном состояниях в сплавах AlCuGdFeSi/AlCuGd [15]
Состояние | σ0.2, МПа | σв, МПа | δ, % |
---|---|---|---|
Деформированное | 287 ± 5/290 ± 1 | 315 ± 5/315 ± 2 | 4.8 ± 0.1/2.1 ± 0.1 |
Отжиг 100°С, 1 час | 276 ± 1/266 ± 2 | 302 ± 2/285 ± 3 | 5.2 ± 0.2/3 ± 1 |
Отжиг 100°С, 3 часа | 261 ± 3/254 ± 3 | 294 ± 1/278 ± 4 | 5.8 ± 0.4/4.2 ± 0.6 |
Отжиг 150°С, 1 час | 236 ± 2/237 ± 2 | 261 ± 2/253 ± 1 | 5.4 ± 0.2/5.5 ± 0.5 |
Отжиг 150°С, 3 часа | 233 ± 2/227 ± 1 | 253 ± 2/244 ± 2 | 5.4 ± 0.2/4 ± 1 |
Отжиг 250°С, 0,5 часа | 198 ± 1/175 ± 4 | 200 ± 1/182 ± 3 | 13.0 ± 0.5/16.0 ± 1.2 |
Результаты испытаний на одноосное растяжение сплава AlCuGdFeSi в холоднодеформированном состоянии и после последующего отжига представлены в таблице в сравнение со сплавом AlCuGd без примесей. Исследуемый сплав демонстрирует достаточно высокий уровень характеристик механических свойств. Результаты по пределу текучести достаточно хорошо коррелируют с результатами измерения твердости. После низких температур отжига 100–150°С сплавы с примесями и без имеют примерно одинаковый предел текучести 227–276 МПа при удлинении более 5% для сплава AlCuGdFeSi. После отжига при 250°С различие в величине предела текучести более заметно – 198 МПа для сплава с примесями против 175 МПа в сплаве без примесей.
Примеси железа и кремния не оказывают негативного влияния на механические свойства нового сплава после прокатки и последующего отжига.
ВЫВОДЫ
Исследовано влияние примесей на фазовый состав и свойства квазибинарного сплава системы Al–Cu–Gd. Примеси железа и кремния не оказывают негативного влияния на микроструктуру и механические свойства нового сплава.
1. В литой структуре выявлено наличие алюминиевого твердого раствора, дисперсной эвтектики с фазой Al8Cu4Gd, в которой растворено около 1% примеси железа, и фазы (AlGdCuSi), примерного состава Al80Gd5Cu8Si5.
2. Гомогенизация при 600°С приводит к фрагментации и сфероидизации фаз кристаллизационного происхождения, в том числе и фазы, образованной с примесью кремния.
3. Разупрочнение, связанное с прохождением процессов возврата и полигонизации, при температурах отжига до 250°С после прокатки в сплавах с примесями и без протекает примерно одинаково. Твердость резко снижается после 0.5 ч с постепенным замедлением после 2 ч и практически не изменяется до 6 ч отжига.
4. Структура полностью рекристаллизуется после часового отжига при 300°С, при этом средний размер зерна составляет 7.5 мкм и незначительно больше после отжига при 550°С – 11 мкм.
5. После отжига прокатанного сплава при 100–150°С предел текучести составляет 227–276 МПа при удлинении более 5%.
Работа выполнена при финансовой поддержке Российского Научного Фонда (проект № 21-79-00193).
Список литературы
Zolotorevsky V.S., Belov N.A., Glazoff M.V. Casting Aluminum Alloys, Alcoa Technical Center, Alcoa Center, PA, United States, 2007. 530 p.
ASM HANDBOOK. Properties and Selection: Nonferrous Alloys and Special-Purpose Materials. V. 2. The Materials Information Company, 2010.
Belov N.A., Khvan A.V., Alabin A.N. Microstructure and phase composition of Al–Ce–Cu alloys in the Al-rich corner // Mater. Sci. Forum 2006. V. 519–521 (PART 1). P. 395–400.
Belov N.A., Khvan A.V. The ternary Al–Ce–Cu phase diagram in the aluminum-rich corner // Acta Mater. 2007. V. 55. P. 5473–5482.
Pozdniakov A.V., Barkov R.Y. Microstructure and materials characterisation of the novel Al–Cu–Y alloy // Mater. Sci. and Tech. 2018. V. 34. № 12. P. 1489–1496.
Amer S.M., Barkov R.Yu., Yakovtseva O.A., Pozdniakov A.V. Comparative analysis of structure and properties of quasi-binary Al–6.5Cu–2.3Y and Al–6Cu–4.05Er alloys // Phys. of Met. and Metall. 2020. V. 121. № 5. P. 528–534.
Pozdniakov A.V., Barkov R.Yu., Amer S.M., Levchenko V.S., Kotov A.D., Mikhaylovskaya A.V. Microstructure, mechanical properties and superplasticity of the Al–Cu–Y–Zr alloy // Mat. Sci. Eng. A. 2019. V. 758. P. 28–35.
Amer S.M., Barkov R.Yu., Pozdniakov A.V. Effect of Mn on the Phase Composition and Properties of Al–Cu–Y–Zr Alloy // Phys. Met. Metall. 2020. V. 121. № 12. P. 1227–1232.
Amer S.M., Barkov R.Y., Prosviryakov A.S., Pozdniakov A.V. Structure and properties of new heat-resistant cast alloys based on the Al–Cu–Y and Al–Cu–Er systems // Phys. Met. Metall. 2021. V. 122. P. 908–914.
Amer S.M., Barkov R.Y., Prosviryakov A.S., Pozdniakov A.V. Structure and properties of new wrought Al–Cu–Y and Al–Cu–Er based alloys // Phys. Met. Metall. 2021. V. 122. P. 915–922.
Pozdnyakov A.V., Barkov R.Yu., Sarsenbaev Zh., Amer S.M. and Prosviryakov A.S. Evolution of Microstructure and Mechanical Properties of a New Al–Cu–Er Wrought Alloy // Phys. Met. Metall. 2019. V. 120(6). P. 614–619.
Amer S.M., Barkov R.Yu., Yakovtseva O.A., Loginova I.S., Pozdniakov A.V. Effect of Zr on microstructure and mechanical properties of the Al–Cu–Er alloy //Mater. Sci. Tech. 2020. V. 36. № 4. P. 453–459.
Amer S.M., Mikhaylovskaya A.V., Barkov R.Yu., Kotov A.D., Mochugovskiy A.G., Yakovtseva O.A., Glavatskikh M.V., Loginova I.S., Medvedeva S.V., Pozdniakov A.V. Effect of Homogenization Treatment Regime on Microstructure, Recrystallization Behavior, Mechanical Properties, and Superplasticity of Al–Cu–Er–Zr Alloy // JOM. 2021. V. 73. № 10. P. 3092–3101.
Amer S., Yakovtseva O., Loginova I., Medvedeva S., Prosviryakov Al., Bazlov A, Barkov R. Pozdniakov A.The Phase Composition and Mechanical Properties of the Novel Precipitation-Strengthening Al–Cu–Er–Mn–Zr Alloy // Appl. Sci. 2020. V. 10. P. 5345.
Amer S., Barkov R., Pozdniakov A. Microstructure and Mechanical Properties of Novel Quasibinary Al–Cu–Yb and Al–Cu–Gd Alloys // Metals. 2021. V. 11. P. 476.
Amer S.M., Barkov R.Yu., Pozdniakov A.V. Effect of Iron and Silicon Impurities on Phase Composition and Mechanical Properties of Al–6.3Cu–3.2Y Alloy // Phys. Met. Metall. 2020. V. 121. № 10. P. 1002–1007.
Amer S.M., Barkov R.Yu., Pozdniakov A.V. Effect of Impurities on the Phase Composition and Properties of a Wrought Al–6% Cu–4.05% Er Alloy // Phys. Met. Metall. 2020. V. 121. № 5. P. 495–499.
Vo N.Q., Dunand D.C., Seidman D.N. Improving aging and creep resistance in a dilute Al–Sc alloy by microalloying with Si, Zr and Er // Acta Mater. 2014. V. 63. P. 73–85.
De Luca A., Dunand D. C., Seidman D. N. Mechanical properties and optimization of the aging of a dilute Al–Sc–Er–Zr–Si alloy with a high Zr/Sc ratio // Acta Mater. 2016. V. 119. P. 35–42.
Booth-Morrison C., Seidman D.N., Dunand D. C. Effect of Er additions on ambient and high-temperature strength of precipitation-strengthened Al–Zr–Sc–Si alloys // Acta Mater. 2012. V. 60. P. 3643–3654.
Pozdniakov A.V., Aytmagambetov A.A., Makhov S.V., Napalkov V.I. Effect of impurities of Fe and Si on the structure and strengthening upon annealing of the Al–0.2% Zr–0.1% Sc alloys with and without Y additive // Phys. Met. Metall. 2017. V. 118. № 5. P. 479–484.
Pozdnyakov A.V., Barkov R.Yu. Effect of impurities on the phase composition and properties of a new alloy of the Al–Y–Er–Zr–Sc system // Metallurgist. 2019. V. 63. № 1–2. P. 79–86.
Karnesky R.A., van Dalen M.E., Dunand D.C., Seidman D.N. Effects of substituting rare-earth elements for scandium in a precipitation-strengthened Al–0.08 at. % Sc alloy // Scripta Mater. 2006. V. 55. № 5. P. 437–440.
Van Dalen M.E., Dunand D.C., Seidman D.N. Nanoscale precipitation and mechanical properties of Al–0.06 at. % Sc alloys microalloyed with Yb or Gd // J. Mat. Sci. 2006. V. 41. P. 7814–7823.
Van Dalen M.E., Dunand D.C., Seidman D.N. Microstructural evolution and creep properties of precipitation-strengthened Al–0.06Sc–0.02Gd and Al–0.06Sc–0.02Yb (at %) alloys // Acta Mater. 2011. V. 59. № 13. P. 5224–5237.
Cacciamani G., De Negri S., Saccone A., Ferro R. The Al–R–Mg (R = Gd, Dy, Ho) systems. Part I: experimental investigation // Intermetallics. 2003. V. 11. P. 1125–113.
Дополнительные материалы отсутствуют.
Инструменты
Физика металлов и металловедение