Физика металлов и металловедение, 2022, T. 123, № 6, стр. 621-629
Влияние скорости нагрева до температуры старения на структуру и упрочнение титанового сплава Ti–10V–2Fe–3Al с разным содержанием углерода
М. С. Калиенко a, b, **, А. В. Желнина a, А. Г. Илларионов b, c, *
a ПАО “Корпорация ВСМПО-АВИСМА”
624760 Верхняя Салда, ул. Парковая, 1, Россия
b Уральский федеральный университет им. первого Президента России Б.Н. Ельцина
620002 Екатеринбург, ул. Мира, 19, Россия
c Институт физики металлов им. М.Н. Михеева УрО РАН
620108 Екатеринбург, ул. С. Ковалевской, 18, Россия
** E-mail: kamak@yandex.ru
* E-mail: a.g.illarionov@urfu.ru
Поступила в редакцию 20.02.2022
После доработки 15.03.2022
Принята к публикации 21.03.2022
- EDN: EQZPNW
- DOI: 10.31857/S0015323022060080
Аннотация
Методами дифференциальной сканирующей калориметрии, растровой электронной микроскопии, рентгеноструктурного фазового анализа и дюрометрии изучено влияние скорости нагрева до температуры старения 500°С на протекание фазовых превращений, формирование структурно-фазового состояния и изменение твердости в закаленном титановом сплаве Ti–10V–2Fe–3Al с различным содержанием углерода. Показано, что изменение скорости нагрева и содержания углерода в сплаве влияет на температуры экзотермических пиков фазовых превращений, связанных с распадом в процессе нагрева метастабильного β-твердого раствора, полученного закалкой. Установлено, что уменьшение скорости нагрева до температуры старения с 40 до 10°С/мин и повышение содержания углерода с 0.008 до 0.034 мас. % в закаленном сплаве Ti–10V–2Fe–3Al увеличивают дисперсность образующихся при старении вторичных фаз, способствуя повышению твердости сплава. Рассмотрено влияние скорости нагрева и содержания углерода на изменение параметров фиксируемых после обработки фаз, рассчитанных с использованием метода полнопрофильного анализа линий на дифрактограммах.
ВВЕДЕНИЕ
(α + β)-Сплавы титана переходного класса, в частности Ti–10V–2Fe–3Al, благодаря высокому уровню механических свойств в термоупрочненном состоянии (удельной прочности, вязкости разрушения, характеристик усталости) широко используются в авиастроении при изготовлении высокопрочных конструкционных элементов, например, узлов шасси самолетов [1–3].
Сплав Ti–10V–2Fe–3Al преимущественно применяют после упрочняющей термической обработки, включающей закалку и старение. Диффузионно-контролируемое превращение закаленной β-матрицы с образованием пластин вторых фаз и последующий их рост — это процессы, которые определяют упрочнение сплава при старении [4, 5]. Хорошо известно, что кинетика выделения и размеры вторичной αВ-фазы в термически упрочняемых сплавах титана сильно зависят от параметров термической обработки. А именно, температура старения и скорость нагрева существенно влияют на морфологию αВ-фазы и, как следствие, на комплекс механических свойств сплавов [6–8]. В одной из первых опубликованных работ по сплаву Ti–10V–2Fe–3Al [4], раскрывающей взаимосвязи между структурой и механическими свойствами, было отмечено существенное влияние скорости нагрева на прочность сплава после старения. Показано, что предел прочности сплава после медленного нагрева выше на 200 МПа в сравнении с этой характеристикой после быстрого нагрева при аналогичной длительности старения (500°С, 1–8 ч), но значения скорости нагрева в работе не приведены. В других работах также не удалось найти данных о влиянии определенной скорости нагрева до температуры старения на структуру и свойства сплава Ti–10V–2Fe–3Al. В работе [9], используя синхротронное излучение in-situ, было показано, что при увеличении скорости нагрева с 20 до 50°С/мин до температуры старения β-закаленного сплава Ti–10V–2Fe–3Al пики экзотермических и эндотермических превращений на кривых ДСК (дифференциальная сканирующая калориметрия) смещаются в область больших температур, также наблюдается изменение последовательности фазовых превращений. Однако в работе не рассмотрено влияние наблюдаемых явлений на механические свойства сплава. Ранее показано [10], что образование метастабильных фаз при нагреве до температуры старения оказывает существенное влияние на последующее выделение αВ-фазы и упрочение сплава. Помимо скорости нагрева на дисперсность αВ-фазы, образующейся при старении, оказывает влияние содержание в сплаве углерода [11–13], но природа этого влияния остается дискуссионной. В частности, в работах [11, 14, 15] указывается, что повышение содержания углерода способствует образованию более дисперсной вторичной αВ-фазы, подавлению образования зернограничной α-фазы в сплавах титана на основе β-фазы при старении. Причины этого указываются разные, включая как образование C-кластеров [14] или комплексов “углерод–кислород–вакансия” [11], выступающих местами зарождения для αВ-фазы, так и рассмотрение карбида титана в сплавах с повышенным содержанием углерода как геттера, который снижает уровень кислорода в матрице, что подавляет образование зернограничной α-фазы [15]. В связи с этим, цель настоящей работы состоит в установлении влияния скорости нагрева и содержания углерода на дисперсность вторичных фаз, образующихся в ходе нагрева, и дюрометрические свойства сплава Ti–10V–2Fe–3Al.
МАТЕРИАЛ И МЕТОДИКИ
Материалом для исследования служили горячедеформированные в (α + β)-области прутки диаметром 22 мм из сплава Ti–10V–2Fe–3Al (мас. %) производства ПАО “Корпорация ВСМПО-АВИСМА”. В работе исследовали сплавы двух плавок с различным содержанием углерода 0.008 и 0.034 мас. %, которое было определено атомно-эмиссионным методом. Образцы, отобранные от прутков, были термообработаны путем закалки в воду с температуры на 45°С ниже температуры полиморфного (α + β) → β-превращения (Тпп). Состояние после закалки в воду соответствовало начальному для дальнейших исследований.
Изучение процессов распада при непрерывном нагреве метастабильного β-твердого раствора, полученного при закалке сплавов, проводили методом ДСК на приборе Netzsch STA449F3 c использованием цилиндрических образцов диаметром 5 мм и высотой 1.5 мм. В качестве образца эталона для калибровки прибора использовали сапфир. Образцы помещали в платиновые тигли, их нагрев и охлаждение осуществляли в проточной атмосфере аргона. Кривые ДСК строились с учетом базовой линии, полученной при нагреве пустых тиглей. Нагрев образцов до температуры 500°С осуществляли со скоростями 10, 20, 40°С/мин, по достижении 500°С следовало охлаждение со скоростью 40°С/мин.
Изучение структуры и измерение твердости проводили на шлифованных и полированных образцах в продольном сечении прутка. Микроструктуру исследовали с помощью растрового электронного микроскопа (РЭМ) Quanta 3D FEG c использованием детектора обратно-отраженных электронов (BSED). Твердость по Виккерсу определяли на микрошлифах после исследования методом РЭМ. Измерения проводили на твердомере DuraScan50 при нагрузке 9.8 Н (10 отпечатков на образец).
Рентгеноструктурный фазовый анализ (РСФА) образцов осуществляли с использованием дифрактометра Bruker D8 Advance с детектором LynxEye (CuKα-излучение, напряжение на трубке 40 кВ, ток 40 мА). Дифрактограммы были записаны в диапазоне углов 2θ = 34°–120°, шаг 0.01°, экспозиция 1 секунда в точке. Полнопрофильный анализ полученных дифрактограмм проводили в программе TOPAS 3. Для подгонки профильной функции уточняли параметры модели, состоящей из следующих фаз (в скобках указана их пространственная группа симметрии): первичной и вторичной α-фазы (P63/mmc), α" (Cmсm) и β-фазы (Im-3m). Качество подгонки профиля дифрактограммы оценивали по весовому фактору недостоверности Rwp, а также визуально по разностной кривой. Юстировку дифрактометра проводили, используя эталон корунда (NIST SRM 1976b).
РЕЗУЛЬТАТЫ И ИХ ОБСУЖДЕНИЕ
Микроструктура сплава после закалки с (Тпп – 45)°С характеризуется наличием в β-матрице частиц первичной α-фазы (αП) глобулярной морфологии размером 2–3 мкм (рис. 1а, αП-фаза имеет наиболее темный контраст на снимках), объемная доля которой составляет 13–15%, что согласуется с результатами работы [4].
Рис. 1.
Микроструктура сплава Ti–10V–2Fe–3Al с разным содержанием углерода после закалки (а) и нагрева с различной скоростью до 500°С (б–д). а–в – сплав с 0.008 мас. % С, г, д – сплав с 0.034 мас. % С; скорость нагрева: б, г – 20°С/мин, в, д – 40°С/мин.
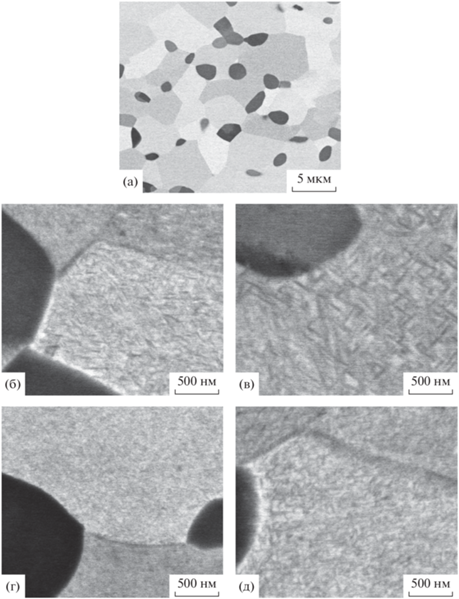
Согласно данным РСФА после закалки сплавы имеют фазы со следующими параметрами кристаллических решеток: – в сплаве с 0.008 мас. % С aβ = 0.3240 нм, aα = 0.2932 нм, сα = 0.4676 нм, с/a = 1.595; в сплаве с 0.034 мас. % С aβ = 0.3239 нм, aα = 0.2932 нм, сα = 0.4683 нм, с/a = 1.597. Сравнительный анализ этих параметров показывает, что увеличение содержания углерода в сплаве с 0.008 до 0.034 мас. % способствует преимущественно росту периодов решетки и параметра с/a первичной α-фазы. Это подтверждают данные предыдущих исследований [16] о влиянии углерода на параметры ГПУ-решетки α-фазы.
Микроструктура предварительно закаленного сплава Ti–10V–2Fe–3Al после непрерывного нагрева до 500°С и последующего охлаждения представлена на рис. 1.
Сравнительный анализ структуры до и после непрерывного нагрева показал, что в процессе нагрева образцов до температуры старения со всеми исследуемыми скоростями происходит распад закаленной β-матрицы (светлый контраст на снимках) с образованием однородно распределенных мелкодисперсных вторичных частиц пластинчатой морфологии (рис. 1б–1д). При скорости нагрева 20°С/мин вторичные частицы намного дисперснее, чем после нагрева со скоростью 40°С/мин. Повышение содержания углерода в сплаве так же приводит к увеличению дисперсности вторичных частиц (рис. 1). Эти результаты, полученные в сплаве Ti–10V–2Fe–3Al, согласуются с данными предыдущих исследований титановых сплавов на основе β-фазы [4, 11, 12], в соответствии с которыми размер вторичных пластин, образующихся при одинаковой температуре старения, уменьшается при снижении скорости нагрева и повышении содержания углерода в сплаве титана.
На рис. 2 представлены ДСК кривые, полученные при нагреве с разной скоростью до 500°С образцов сплава с различным содержанием углерода. Анализ профиля ДСК кривых показал, что все шесть кривых имеют по два характерных ярко выраженных экзотермических эффекта, очевидно, связанных с разными стадиями распада метастабильного β-твердого раствора. Экзоэффекты смещаются в область больших температур с увеличением скорости нагрева.
Рис. 2.
ДСК кривые нагрева до температуры 500°С со скоростями 10, 20, 40°С/мин закаленного сплава Ti–10V–2Fe–3Al с разным содержанием углерода.
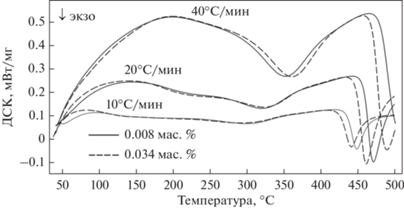
Первый экзотермический эффект, имеющий пики в области температур 290–360°С, характеризует β → ω-превращение. Это следует из данных работы [9] и подтверждено нами рентгенографически (рис. 3) при съемке образцов, подвергнутых длительному старению в течение 98 ч при температуре 320°С, сопоставимой с температурой экстремума низкотемпературного экзоэффекта (табл. 1).
Рис. 3.
Дифрактограммы сплава Ti–10V–2Fe–3Al с разным содержанием углерода после старения при 320°С в течение 98 ч. а – 0.008 мас. % С, б – 0.034 мас. % С.
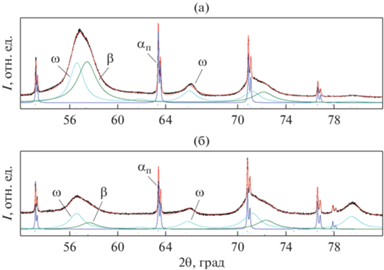
Таблица 1.
Температуры пиков экзотермических эффектов на ДСК кривых, связанных с образованием ω- и αВ (α")-фаз в сплаве Ti–10V–2Fe–3Al с содержанием 0.008 и 0.034 мас. % углерода при нагреве до температуры старения 500°С
Скорость нагрева, °С/мин | Температура, °С | |||
---|---|---|---|---|
0.008 мас. % С | 0.034 мас. % С | |||
ω-фаза | αВ (α'')-фазы | ω-фаза | αВ (α'')-фазы | |
10 | 300 | 449 | 291 | 442 |
20 | 320 | 471 | 323 | 462 |
40 | 352 | выше 500 | 361 | 490 |
На полученных дифрактограммах с образцов, состаренных при 320°С, кроме дифракционных линий матричного β-твердого раствора и первичной αП-фазы обнаружены линии ω-фазы, которая имеет следующие параметры – в сплаве с 0.008 мас. % С aω = 0.4583 нм, сω = 0.2833 нм, с/a = = 0.618; в сплаве с 0.034 мас. % С aω = 0.4585 нм, сω = 0.2838 нм, с/a = 0.619.
Сравнительный анализ фиксируемых параметров кристаллической решетки ω-фазы в сплавах с разным содержанием углерода показал, что с повышением содержания углерода в сплаве наблюдается рост периодов решетки а и с ω-фазы, а вместе с ними и параметра с/a. Как отмечено выше, аналогичным образом углерод влияет на параметры решетки первичной αП-фазы, которые после старения при 320°С сохраняются на уровне, характерном для закаленного состояния.
Второй экзотермический эффект с пиками в области температур 440–500°С, согласно данным РСФА (рис. 4), связан с протеканием при распаде β → αВ (α'') превращения, где αВ – вторичная α‑фаза с ГПУ-решеткой, а α" – промежуточная фаза с ромбической решеткой.
Рис. 4.
Дифрактограммы сплава Ti–10V–2Fe–3Al с разным содержанием углерода после нагрева с различными скоростями до 500°С (а, б) и с выделенными профилями линий фаз, полученных после нагрева со скоростью 10°С/мин (в, г).
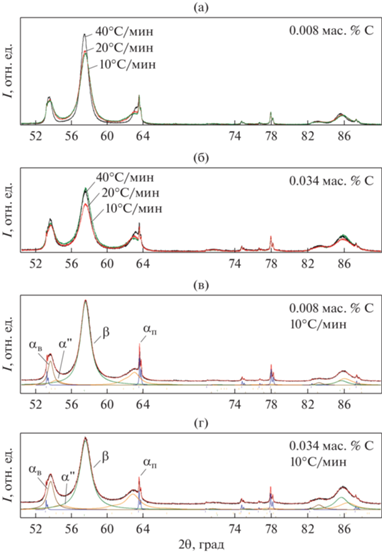
В табл. 1 представлены данные ДСК по температуре экстремумов экзоэффектов, вызванных выделением ω- и αВ (α")-фаз в исследованных сплавах при разных скоростях нагрева. Сравнительный анализ полученных температур показал, что увеличение скорости нагрева сплавов с 10 до 40°С/мин приводит к повышению температур пиков экзоэффектов выделения ω- и αВ (α")-фаз на 70 и 50 град, соответственно (табл. 1). При содержании в сплаве меньшего количества углерода (0,008 мас. %) соответствующие пики выделения αВ (α")-фаз выше на 7–10°С, чем при 0.034 мас. % С (табл. 1).
Качественная оценка размера вторичных частиц αВ (α")-фаз, образующихся при непрерывном нагреве, может быть получена методом полнопрофильного анализа дифрактограмм, если размеры частиц менее 60 нм [17]. На рис. 4 приведены данные полнопрофильного анализа дифрактограмм образцов, подвергнутых непрерывному нагреву. По этим данным после нагрева до 500°С и последующего охлаждения в структуре сплавов присутствуют четыре фазы – αП, αВ, α", β.
В результате расчета дифрактограмм были определены параметры решеток фиксируемых фаз и размеры областей когерентного рассеяния (ОКР), определяющих характерные размеры αВ-, α"-, β-фаз, рис. 5. Анализ этих результатов позволил выявить следующие закономерности.
Рис. 5.
Изменение параметров фаз от скорости нагрева сплава Ti–10V–2Fe–3Al с разным содержанием углерода: а – ОКР β-фазы; б – ОКР αВ-, α"-фаз; в – объема элементарной ячейки β-фазы, αП-, αВ-фаз; г – параметра с/а αП-, αВ‑фаз; д – периода а α"-фазы и параметра bα"/√3.
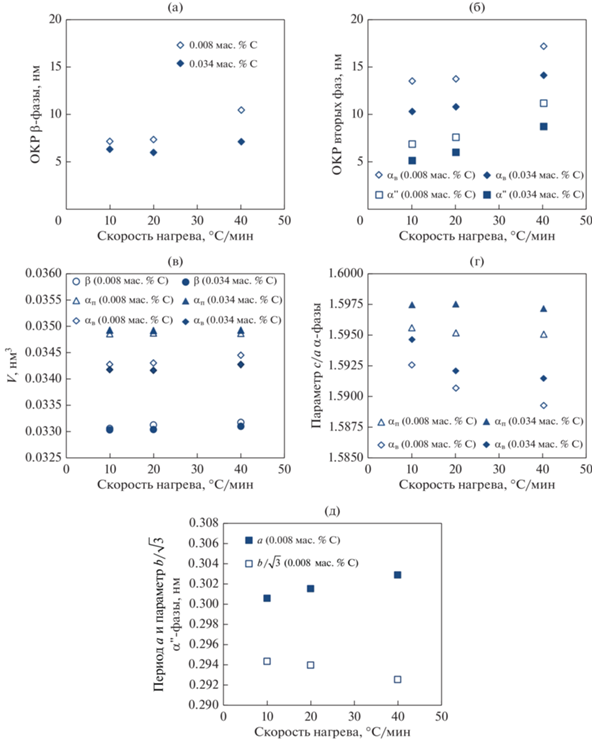
В сплаве одного состава, подвергнутом нагреву с различными скоростями, с повышением скорости нагрева имеют тенденцию к увеличению – период решетки матричного β-твердого раствора, ОКР β-матрицы, вторых фаз (αВ, α"), ромбичность α"-фазы, характеризуемая уровнем различия периода a и параметра b/√3 в кристаллической решетке α"-фазы, а к снижению – параметр с/а для ГПУ решетки первичной и вторичной α‑фазы (рис. 5).
Характерное влияние скорости нагрева на параметры фаз мы связываем с отмеченным выше при исследовании методом ДСК (рис. 2, табл. 1) более поздним по температуре развитием процессов распада β-твердого раствора с выделением вторых фаз (αВ, α") и менее полным протеканием процессов установления термодинамического равновесного химического состава во вторичной α-фазе при увеличении скорости непрерывного нагрева. В результате этого, в матричном β-твердом растворе менее полно реализуется процесс его распада при увеличении скорости нагрева, и, соответственно, он менее обогащается в ходе распада β-стабилизаторами (ванадием, железом), способствующими снижению периода его решетки [16]. В первичной и вторичной α (α")-фазах, наоборот, сохраняется повышенное содержание β-стабилизаторов, в первую очередь, ванадия, который, как известно, способствует снижению параметра c/a [18] и увеличению ромбичности α"‑фазы [19].
Повышение температуры начала превращения при непрерывном нагреве с более высокой скоростью способствует образованию вторых фаз большего размера, приводя к увеличению получаемых из расчета дифрактограмм значений ОКР для этих фаз после обработки (рис. 5а, 5б). В исследуемых сплавах величина ОКР αВ-фазы примерно в 1.5–2 раза больше, чем значения ОКР для α"-фазы, и разница между ними уменьшается при повышении скорости непрерывного нагрева (рис. 5б). По-нашему мнению, это связано с тем, что образование α"-фазы при распаде β-твердого раствора, как известно [9], начинается раньше, чем αВ-фазы, и поэтому размер выделений α"-фазы меньше. При повышении скорости нагрева сокращается еще и время на рост этих фаз, особенно αВ-фазы, что способствует уменьшению разницы в размерах ОКР αВ- и α"-фаз.
Необходимо отметить, что для фиксируемых после обработки фаз (β, αВ, αП), имеющих по 2 атома на элементарную ячейку кристаллической решетки, объем, приходящийся на элементарную ячейку, увеличивается в последовательности β–αВ–αП (рис. 5в). Это вполне закономерно, так как именно в этой последовательности наблюдается снижение содержания в фазах β-стабилизаторов (ванадия, железа), вносящих основной вклад в уменьшение объема элементарной ячейки.
С повышением содержания углерода от сплава к сплаву, при одинаковой скорости непрерывного нагрева, имеется тенденция, с одной стороны, фиксации более высокого значения параметра с/а первичной и вторичной α-фаз и, с другой стороны, получения меньших значений ОКР, характерных для вторых фаз (αВ, α") и β-матрицы (рис. 5а, 5б, 5г). Первый эффект объясняется характерным влиянием углерода на параметр c/a в ГПУ решетке α-фазы [16], отмеченным выше. Второй эффект, подтверждает данные работы [11], согласно которых, увеличение содержания углерода в твердом растворе в титановых сплавах на основе β-фазы способствует измельчению вторых фаз при старении.
В работе [11] выдвинута гипотеза, что при старении сплава Ti–15V–3Cr–3Sn–3Al уменьшение размера выделяющейся вторичной αВ-фазы при увеличении содержания растворенного углерода в матричной β-фазе связано с увеличением количества образующихся в β-твердом растворе комплексов “углерод–кислород–вакансия”, на которых облегчено выделение αВ-фазы. В нашем случае определенным подтверждением данной гипотезы служат результаты по изменению параметра c/a αВ-фазы в зависимости от содержания углерода в сплаве при одинаковой скорости непрерывного нагрева (рис. 5г). Как отмечено выше, с увеличением содержания углерода в сплаве параметр c/a αВ-фазы имеет тенденцию к росту, и одной из наиболее вероятных причин этого является возрастание количества в αВ-фазе растворенного углерода и кислорода, повышающих данный параметр [16]. А это как раз возможно в результате образования выше указанных комплексов “углерод–кислород–вакансия”. На это дополнительно указывают и данные по химическому составу исследуемых сплавов. В сплаве с повышенным содержанием углерода 0.034 мас. % концентрация других элементов, повышающих параметр с/а – Al (3.13 мас. %), O (0.1 мас. %), находится либо на более низком уровне, чем в сплаве с 0.008 мас. % углерода (Al – 3.15 мас. %, О – 0.11 мас. %), либо на сопоставимом – для азота – это около 0.003 мас. %.
На рис. 6 представлены результаты измерения твердости исследуемых сплавов, подвергнутых непрерывному нагреву до 500°С и последующему охлаждению. Твердость сплава после закалки составляет около 300 HV. После нагрева до температуры старения 500°С со скоростями 40, 20, 10°С/мин образцов сплава с 0.008 мас. % С твердость увеличивается до 400, 430, 435 HV, соответственно. При содержании углерода в сплаве 0.034 мас. % после аналогичных скоростей нагрева наблюдается большее увеличение твердости до 440–460 HV (рис. 6).
Рис. 6.
Зависимость твердости закаленного сплава Ti–10V–2Fe–3Al с разным содержанием углерода от скорости нагрева до 500°С.
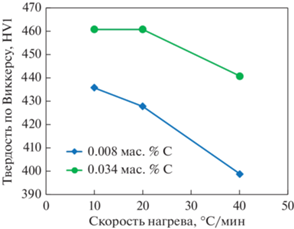
Полученные данные хорошо согласуются с результатами оценки размеров (ОКР) упрочняющих фаз, выделяющихся при старении сплавов с разным содержанием углерода (рис. 5б). Уменьшение при медленной скорости нагрева и более высоком содержании углерода размера образующихся частиц αВ-, α"-фаз, а, соответственно, и расстояния между ними, как известно, приводит к увеличению сопротивления движению дислокаций при деформации и повышению прочности (твердости) сплава [20], что и отражено на рис. 6.
Таким образом, в работе установлено как скорость нагрева до температуры старения и содержание углерода в сплаве Ti–10V–2Fe–3A влияют на дисперсность образующихся при нагреве αВ (α")-фаз. Полученные в настоящем исследовании результаты весьма важны для учета факторов, оказывающих влияние на механические свойства сплава, и оптимизации технологического процесса производства полуфабрикатов из сплава Ti–10V–2Fe–3Al.
ЗАКЛЮЧЕНИЕ
В работе исследованы структура, фазовый состав закаленного из (α + β)-области высокопрочного титанового сплава Ti–10V–2Fe–3Al с разным содержанием углерода после различных скоростей нагрева (10, 20, 40°С/мин) до температуры старения 500°С. Методом ДСК определены температурные интервалы образования вторичных фаз при нагреве. Проведен расчет параметров решеток фиксируемых фаз и размера ОКР αВ-, α"- и β-фазы методом полнопрофильного анализа дифрактограмм, измерена твердость сплава. На основании анализа полученных в ходе исследования результатов сделаны следующие выводы:
1. Показано, что уменьшение скорости непрерывного нагрева с 40 до 10°С/мин до температуры старения 500°С закаленного сплава Ti–10V–2Fe–3Al способствует получению более дисперсных выделений вторичных αВ (α")-фаз, обеспечивая более высокий уровень твердости сплава после охлаждения с температуры нагрева. Такое влияние скорости нагрева на структуру и свойства связано с зафиксированным методом ДСК эффектом смещения в область более низких температур интервала β–αВ (α") –превращения при снижении скорости нагрева, что, как известно, способствует образованию более дисперсных зародышей вторичных выделений.
2. Установлено, что увеличение содержания углерода в сплаве с 0.008 до 0.034 мас. % обеспечивает дополнительное измельчение образующихся при непрерывном нагреве с одной скоростью вторичных αВ (α")-частиц и, соответственно, повышение характеристик твердости. В ходе полнопрофильного фазового анализа исследуемых сплавов подтверждена версия о том, что при повышении содержания углерода измельчение вторичных αВ (α")-выделений обусловлено образованием в β-твердом растворе комплексов “углерод-кислород-вакансия”, способствующих ускорению образования вторичных фаз и закономерным образом влияющих на параметр c/a αВ-фазы.
Работа выполнена в рамках Госзадания Минобрнауки РФ УрФУ № 0836-2020-0020.
Список литературы
Boyer R.R., Briggs R.D. The Use of β Titanium Alloys in the Aerospace Industry // J. Mater. Eng. Perform. 2005. V. 14. P. 681–685.
Cotton J.D., Briggs R.D., Boyer R.R., Tamirisakandala S., Russo P., Shchetnikov N., Fanning J.C. State of the Art in Beta Titanium Alloys for Airframe Applications // JOM. 2015. V. 67. P. 1281–1303.
Williams J.C., Boyer R.R. Opportunities and issues in the application of titanium alloys for aerospace components // Metals. 2020. V. 10. № 6. P. 705.
Duerig T.W., Terlinde G.T., Williams J.C. Phase transformations and tensile properties of Ti–10V–2Fe–3AI // Metal. Trans. A. 1980. V. 11. № 12. P. 1987–1998.
Желнина А.В., Калиенко М.С., Илларионов А.Г., Щетников Н.В. Трансформация структуры, параметров фаз при старении сплава титана Ti–10V–2Fe–3Al и их связь упрочнением // ФММ. 2020. Т. 121. № 12. С. 1324–1330.
Wang B., Liu Z., Gao Y., Zhang S., Wang X. Microstructural evolution during aging of Ti–10V–2Fe–3Al titanium alloy // J. University Sci. Technol. Beijing, Mineral, Metallurgy, Material. 2007. V. 14. № 4. P. 335–340.
Ivasishin O.M., Markovsky P.E., Matviychuk Y.V., Semiatin S.L., Ward C.H., Fox S.A comparative study of the mechanical properties of high-strength β-titanium alloys // J. Alloys Compounds. 2008. V. 457. № 1–2. P. 296–309.
Kent D., Wang G., Wang W., Dargusch M.S. Influence of ageing temperature and heating rate on the properties and microstructure of β Ti alloy, Ti–6Cr–5Mo–5V–4Al // Mater. Sci. Eng.: A. 2012. V. 531. P. 98–106.
Barriobero-Vila P., Requena G., Warchomicka F., Stark A., Schell N., Buslaps T. Phase transformation kinetics during continuous heating of a β-quenched Ti–10V–2Fe–3Al alloy // J. Mater. Sci. 2015. V. 50. № 3. P. 1412–1426.
Ohmori Y., Ogo T., Nakai K., Kobayashi S. Effects of ω‑phase precipitation on β → α, α"′ transformations in a metastable β titanium alloy // Mater. Sci. Eng.: A. 2001. V. 312. № 1–2. P. 182–188.
Wu X., del Prado J., Li Q., Huang A., Hu D., Loretto M.H. Analytical electron microscopy of C-free and C-containing Ti–15–3 // Acta Mater. 2006. V. 54. № 20. P. 5433–5448.
Желнина А.В., Калиенко М.С., Щетников Н.В. Исследование влияния углерода на деформационное поведение и микроструктуру сплава Ti–10V–2Fe–3Al // ФММ. 2021. Т. 122. № 2. С. 166–172.
Cao S., Zhou X., Lim C.V.S., Boyer R.R., Williams J.C., Wu X. A strong and ductile Ti–3Al–8V–6Cr–4Mo–4Zr (Beta-C) alloy achieved by introducing trace carbon addition and cold work // Scripta Mater. 2020. V. 178. P. 124–128.
Alam T., Kami P., Cao L., Nag S., Bettles C.J., Wu X., Banerjee R. On the role of C addition on alpha precipitation in a beta titanium alloy // Met. Mater. Trans. A. 2014. V. 45. № 3. P. 1089–1095.
Chen Z.Q., Hu D., Loretto M.H., Wu X. Influence of 0.2 wt % C on the aging response of Ti–15–3 // J. Mater. Sci. Techn. 2004. V. 20. № 6. P. 756–764.
Цвиккер У. Титан и его сплавы. М.: Мир.1979. 512 с.
Калиенко М.С., Волков А.В., Желнина А.В. Использование полнопрофильного анализа дифрактограмм для оценки дисперсности вторичной альфа-фазы титана в высокопрочных титановых сплавах // Кристаллография. 2020. Т. 65. № 3. С. 428–433.
Aurelio G., Guillermet A.F., Cuello G.J., Campo J. Metastable Phases in the Ti–V System: Part I. Neutron Diffraction Study and Assessment of Structural Properties // Metal. Mater. Trans. A. 2002. V. 33A. № 5. P. 1307–1317.
Dobromyslov A.V., Elkin V.A. The orthorhombic α''‑phase in binary titanium-base alloys with d-metals of V–VIII groups //Mater. Sci. Eng. A. 2006. V. 438–440. P. 324–326.
Nie J.F. Effects of precipitate shape and orientation on dispersion strengthening in magnesium alloys // Scripta Mater. 2003. V. 48. № 8. P. 1009–1015.
Дополнительные материалы отсутствуют.
Инструменты
Физика металлов и металловедение