Физика металлов и металловедение, 2022, T. 123, № 6, стр. 665-672
Нейтрон-дифракционное исследование влияния направления выращивания на распределение остаточных напряжений в призмах из аустенитной стали, полученных методом селективного лазерного плавления
И. Д. Карпов a, *, В. Т. Эм a, С. А. Рылов a, Е. А. Сульянова b, Д. И. Сухов c, Н. А. Ходырев c
a НИЦ “Курчатовский институт”
123182 Москва, пл. Академика Курчатова, 1, Россия
b ФНИЦ “Кристаллография и фотоника” РАН
119333 Москва, Ленинский проспект, 59, Россия
c НИЦ “Курчатовский институт” – ВИАМ
105005 Москва, ул. Радио, 17, Россия
* E-mail: Karpov_ID@nrcki.ru
Поступила в редакцию 26.02.2022
После доработки 21.03.2022
Принята к публикации 22.03.2022
- EDN: OLCUMU
- DOI: 10.31857/S0015323022060092
Аннотация
На примере призмы из стали марки 316L размерами 20 × 20 × 70 мм, изучено влияние направления выращивания методом селективного лазерного плавления на распределение остаточных напряжений. Исследовали призмы с разным направлением выращивания (вдоль длинного и короткого ребра). Использовали метод нейтронной стресс-дифрактометрии, который позволяет неразрушающим методом измерить все три компоненты тензора напряжений в массивных материалах и изделиях. В обоих случаях в центральной части призмы формируются сжимающие напряжения, которые при приближении к поверхности близки к нулю или переходят в растягивающие напряжения. В призме, выращенной вертикально вдоль длинного ребра, растягивающие напряжения больше по величине и занимают больший объем, чем в такой же призме, выращенной вдоль короткого ребра. Максимальные растягивающие напряжения (~500 МПа) вблизи ребер вертикальной призмы близки к пределу текучести (~540 МПа) материала. Максимальные сжимающие напряжения (~–400 МПа) образуются в центральной части вертикальной призмы.
ВВЕДЕНИЕ
Аддитивные технологии (АТ) сегодня – одно из наиболее динамично развивающихся направлений в современной промышленности. По сравнению с традиционными технологиями, они позволяют значительно уменьшить материалоемкость, трудоемкость и время изготовления деталей. С помощью аддитивных технологий можно получить принципиально новые материалы и изделия, которые невозможно получить традиционными технологиями. Металлические изделия с помощью аддитивных технологий получают путем послойного наплавления металла до нужной толщины. Технологии различаются способами формирования слоя (селективное плавление слоя порошка, прямое выращивание), источником энергии (лазерный или электронный луч, электрическая дуга) и видом используемого материала (порошок, проволока). Наибольшее распространение получили методы, основанные на использовании лазерного излучения: селективное лазерное плавление (СЛП) и прямое лазерное выращивание (ПЛВ). В методе СЛП сначала формируется однородный слой порошка толщиной в несколько десятков микрон на подложке, затем с помощью лазерного луча происходит его сплавление для получения горизонтального слоя детали. Затем наносится следующий слой порошка и процесс повторяется. Суть метода ПЛВ заключается в том, что металлический порошок через специальное сопло подается в ту же область, куда подводится лазерный луч, образуя локальную ванну жидкого расплава. Соответствующий горизонтальный слой детали получают перемещением луча.
Создание АТ материала происходит при высоких градиентах температур и высоких скоростях охлаждения. Поэтому в нем возникают значительные остаточные напряжения, которые могут сильно ухудшить его усталостную прочность, приводят к короблению, образованию трещин и деформации детали [1–3]. Большие остаточные напряжения являются одним из основных факторов, препятствующих широкому распространению аддитивных производств металлических изделий. Для понимания природы остаточных напряжений в материалах, полученных АТ, и поиска путей их уменьшения исследуется влияние вида технологии и параметров технологических процессов (материал, рисунок сканирования, скорость сканирования, угол поворота между соседними слоями, мощность лазера, геометрия образца и т. д) на распределение остаточных напряжений [4–9]. Остаточные напряжения трудно рассчитать теоретически, поэтому экспериментальные исследования важны для верификации различных расчетных моделей. Отметим, что направление выращивания также является одним из технологических параметров. Однако работ, посвященных этой проблеме, сравнительно мало [9–13].
Цель настоящей работы – изучение методом нейтронной стресс-дифрактометрии влияния направления выращивания на распределение остаточных напряжений на примере двух одинаковых прямоугольных призм, выращенных методом СЛП из стали марки 316L, и сравнение полученного результата с распределением напряжений в призме, выращенной из той же стали методом ПЛВ [14]. В настоящее время метод нейтронной стресс-дифрактометрии является единственным методом, который, благодаря высокой проникающей способности нейтронов, позволяет неразрушающим методом измерить все три компоненты тензора напряжения в массивных металлических деталях (в стали толщиной до 50 мм) [15–17]. Проникающая способность рентгеновских лучей значительно меньше (~10 мкм в сталях), поэтому рентгеновский метод дает информацию о напряжениях на поверхности или в приповерхностных слоях материала [15].
ОБРАЗЦЫ И МЕТОДИКА ЭКСПЕРИМЕНТА
Приготовление образцов. Для приготовления образцов использовали металлопорошковую композицию (фракция 10–63 мкм, средний размер частиц 36 мкм) стали марки 316L. Химический состав стали представлен в табл. 1. Процесс СЛП выполняли на установке “Concept Laser M2 Cusing”. Образцы размерами 20 × 20 × 70 (здесь и далее размеры даны в миллиметрах) выращены на общей базовой плите из стали 316L путем послойного наплавления горизонтальных слоев порошка металла. Направление выращивания первой призмы совпадало с ее длинным ребром 70 (рис. 1а), второй призмы – с ее коротким ребром 20 (рис. 1б).
Таблица 1.
Химический состав стали марки 316 L
Элемент | C | Si | Mn | Ni | S | P | Cr | Mo | Fe |
---|---|---|---|---|---|---|---|---|---|
Вес. % | ≤0.03 | ≤0.75 | ≤2.0 | 10–14 | ≤0.03 | ≤0.045 | 16–18 | 2.00–3.00 | ~65 |
Рис. 1.
Прямые четырехугольные призмы из стали марки 316L, выращенные методом селективного лазерного плавления: а – вертикальная призма, б – горизонтальная призма. L1, L2, L3, L4, L5, L6 – линии, параллельные оси Z (продольное направление), вдоль которых измеряли напряжения. Показаны также сечения XY, перпендикулярные оси Z (Z = 1.5, 17, 35), в которых проводили измерение напряжений. Размеры даны в миллиметрах.
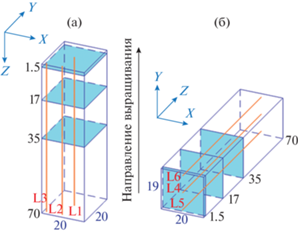
После изготовления образцы с помощью отрезного круга были отделены от базовой плиты и поддерживающих конструкций. Для придания правильной формы у горизонтальной призмы со стороны основания методом электроэрозионной резки был дополнительно удален слой толщиной ~1 так, что окончательный размер горизонтальной призмы составил 20 × 19 × 70 (19 – вертикальное ребро вдоль направления роста). На рис. 1 даны системы координат для обеих призм. В обеих призмах ось Z соответствует продольному направлению, ось X – поперечному и ось Y – нормальному.
Измерение напряжений нейтронным методом. Нейтрон-дифракционный метод измерения напряжений основан на измерении изменения углового положения дифракционного пика, вызванного изменением межплоскостного расстояния кристаллической решетки при растягивающих или сжимающих напряжениях [18]. Согласно закону Вульфа–Брэгга:
где ${{d}_{{hkl}}}$ – расстояние между атомными плоскостями кристаллической решетки с миллеровскими индексами $hkl,$ ${{\theta }_{{hkl}}}$ – брэгговский угол рассеяния от плоскостей $\left( {hkl} \right)$, $\lambda $ – длина волны нейтронов. Усредненная по измеряемому пробному объему относительная деформация в направлении нормали к отражающим плоскостям $\left( {hkl} \right)$ определяется соотношением:Исследование распределения напряжений проводили на нейтронном дифрактометре СТРЕСС на реакторе ИР-8 в НИЦ “Курчатовский институт” [19–21]. Для уменьшения времени измерения на нейтронном пучке и получения информации о распределении напряжений в объеме призмы измерения проводили по следующей схеме. В вертикальной призме (рис. 1а) – в точках, расположенных на трех линиях L1, L2, L3, параллельных вертикальной оси Z. Указанные линии проходят: в центре призмы L1 (X = 10, Y = 10), вблизи боковой грани призмы L2 (X = 10, Y = 1.5) и вблизи ребра призмы L3 (X = 1.5, Y = 1.5). Измерения проводились в точках от Z = 2 до Z = 68 с шагом 3. Также измерения проводили в сечениях призмы XY на расстояниях 1.5, 17 и 35 вдоль Z от ее верхней грани (рис. 1а). Ближайшие к боковым граням точки в сечениях находились на глубине 1.5. В сечениях дополнительно измеряли несколько точек на глубине 1 мм от поверхности боковых граней. В горизонтальной призме (рис. 1б) измерения проводили в точках, расположенных на трех линиях L4, L5, L6, параллельных горизонтальной оси Z и проходящих: в центре призмы L4 (X = 10, Y = 9.5), вблизи нижней грани призмы L5 (X = 10, $Y$ = 1.5) и вблизи ее верхней грани L4 (X = 10, Y = 17.5). Измерения проводили в точках от Z = 2 до Z = 68 с шагом 3. Аналогично измерениям в вертикальной призме, напряжения измеряли в сечениях призмы XY на расстояниях 1.5, 17 и 35 вдоль Z от боковой грани. Для уменьшения времени измерения в сечении Z = 1.5 измерения проводили в 1/4 сечения. Измеряли дифракционный пик (311) гранецентрированной кубической (ГЦК) решетки аустенитной стали 316L на угле $2\theta \approx 91^\circ .$ Отражающая плоскость (311) рекомендована для измерения напряжений в материалах с ГЦК-решеткой, поскольку она малочувствительна к микронапряжениям [18]. Измерения проводили с пробным объемом ∼1.5 × 1.5 × 2. Точки на глубине 1 мм от поверхности граней измеряли с пробным объемом ~1 × 1 × 3. При всех измерениях пробный объем был полностью погружен в металл, чтобы избежать погрешности измерений при его неполном погружении [18]. Компоненты деформаций измеряли со статистической погрешностью ~50 × 10–6, что соответствует погрешности в измерении напряжений ~20 МПа. Референсное значение межплоскостного расстояния ${{d}_{0}},$ соответствующее материалу в ненапряженном состоянии, определяли из условия баланса сил вдоль направления Z в сечениях XY с Z = 17.5, 35 [9, 15]. Разброс значений ${{d}_{0}},$ полученных для разных сечений, соответствовал изменению напряжений в измеряемой точке менее 40 МПа.
В расчетах принимали значения модуля Юнга ${{E}_{{311}}} = 184\,{\text{ГПа}}$ и коэффициента Пуассона ν311 = = 0.294 для стали марки 316L [15].
РЕЗУЛЬТАТЫ ЭКСПЕРИМЕНТОВ И ОБСУЖДЕНИЕ
Результаты измерений вдоль линий, параллельных оси Z, в вертикальной (L1, L2, L3) и горизонтальной (L4, L5, L6) призмах представлены на рис. 2. В средней части вертикальной призмы (15 < Z < 55) все компоненты напряжения вдоль всех линий изменяются в пределах ±50 МПа (рис. 2а).
Рис. 2.
Распределение компонент напряжений вдоль линий, параллельных оси Z, в (а) вертикальной (L1, L2, L3) и (б) горизонтальной (L4, L5, L6) призмах.
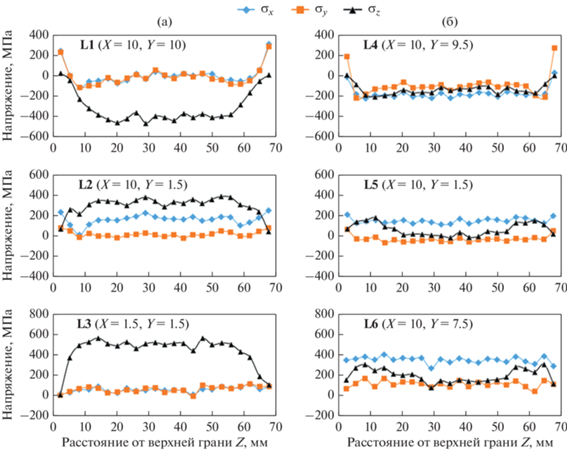
Максимальное сжимающее напряжение (${{\sigma }_{z}}$ ~ ~ –400 МПа) наблюдается в средней части участка измерений линии L1 (X = 10, Y = 10), проходящей через центр призмы. Сжимающие напряжения резко уменьшаются при приближении к верхней и нижней граням призмы до близких к нулю величин, поскольку нормальная к свободной поверхности компонента напряжения должна быть равна нулю на поверхности. Напротив, компоненты ${{\sigma }_{x}}$ и ${{\sigma }_{y}},$ близкие к нулю в средней части, резко увеличиваются до ~220/270 МПа при приближении к верхней/нижней граням призмы. Отметим, что распределение напряжений вдоль центральной линии L1 хорошо согласуется с распределением вдоль центральной линии в призме из стали 316L, полученной методом ПЛВ [14].
В средней части линии L2 (X = 10 мм, Y = 1.5 мм) (рис. 2а), проходящей вблизи центральной линии боковой грани призмы, присутствуют растягивающие напряжения (${{\sigma }_{z}}$ ~350 МПа), которые резко уменьшаются при приближении к верхней и нижней граням призмы. Компонента ${{\sigma }_{x}}$ в средней части призмы имеет значение ~160 МПа. При приближении к верхней и нижней граням она сначала несколько уменьшается, а затем увеличивается до ~230 МПа. Компонента ${{\sigma }_{y}}$ близка к нулю, поскольку она перпендикулярна к поверхности.
Максимальные значения растягивающих напряжений (~500 МПа) имеет продольная компонента ${{\sigma }_{z}}$ в средней части призмы вблизи боковых ребер вдоль линии L3 (X = 1.5, Y = 1.5) (рис. 2а). Она резко уменьшается при приближении к верхней и нижней граням призмы, поскольку перпендикулярна к ним. По этой же причине компоненты напряжения σx и σy в точках вдоль линии L3 вблизи боковых граней близки к нулю, и максимальное напряжение ${{\sigma }_{z}}~$ ≈ 500 МПа близко к эквивалентному напряжению по Мизесу. Отметим, что вблизи нижней вершины призмы напряжения несколько выше, чем вблизи верхней вершины.
В горизонтальной призме (рис. 2б) так же, как и в вертикальной, в средней части призмы на участке 5 ≤ Z ≤ 65 все компоненты напряжения, за исключением компоненты ${{\sigma }_{z}}$ вблизи верхней и нижней граней (L5, L6), изменяются слабо в пределах ±50 МПа.
Все компоненты напряжения вдоль линии L4, проходящей через центр горизонтальной призмы, сжимающие. При приближении к торцам призмы (Z = 0, Z = 70) сжимающие напряжения$~{{\sigma }_{z}}$ и ${{\sigma }_{x}}~$уменьшаются до величин близким к нулю, а компонента ${{\sigma }_{y}}$, параллельная направлению выращивания, меняет знак и увеличивается до ~200 МПа.
Вблизи верхней и нижней грани горизонтальной призмы (L5, L6) напряжения близки к нулю или являются растягивающими. Отметим, что напряжения вблизи верхней грани (L6) выше, чем вблизи нижней грани (L5).
На рис. 3 представлены распределения напряжений в сечениях XY (Z = 1.5, 17, 35) вдоль центральных линий этих сечений Y (X = 10) и X (Y = = 10/9.5) в вертикальной и горизонтальной призмах. На рис. 4 показаны картограммы двумерного распределения напряжений в сечениях XY (Z = = 1.5, 17, 35).
Рис. 3.
Распределение напряжений в сечениях XY (Z = 1.5, 17, 35) вдоль центральных линий сечений Y (X = 10) и X (Y = 10/9.5) в вертикальной (а) и горизонтальной (б) призмах.
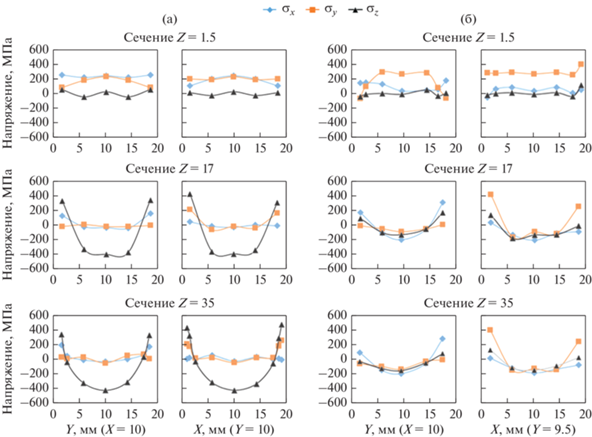
Рис. 4.
Картограммы двумерного распределения напряжений в сечениях XY (Z = 1.5, 17, 35) вертикальной (а) и горизонтальной (б) призм.
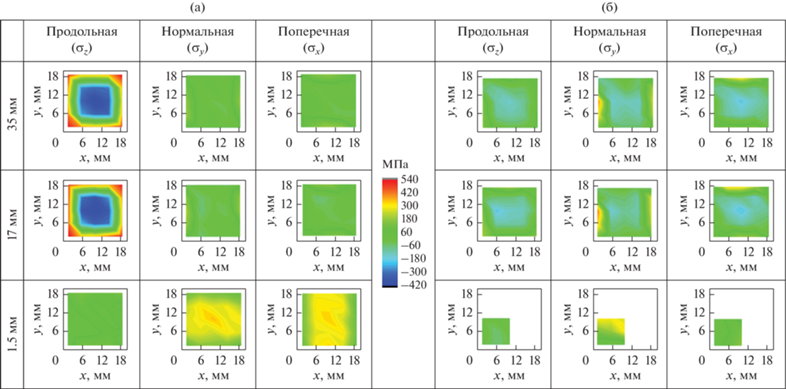
По результатам измерений вдоль линий L1, L2, L3 (рис. 2а) и в сечениях (рис. 3а, 4а) можно сделать следующее заключение о распределении напряжений в вертикальной призме. В большей части объема призмы (на глубине больше 3 мм от боковых граней) нормальная и поперечная компоненты напряжения малы, и реализуется одноосное (вдоль вертикальной оси Z) напряженное состояние. Большие (~–400 МПа) сжимающие продольные напряжения в центральной части призмы при приближении к боковым граням уменьшаются и на расстоянии ~3 от грани переходят в растягивающие. При дальнейшем приближении к грани напряжения быстро растут и на расстоянии 1.5 от грани достигают величины ~350 МПа. Максимальные растягивающие продольные напряжения (~500 МПа) наблюдаются вблизи боковых ребер призмы.
Сжимающие напряжения в центральной части призмы уравновешиваются растягивающими напряжениями вблизи ее боковых граней. На глубине 1.5 от боковых граней наблюдаются параллельные граням небольшие (~150 МПа) растягивающие нормальные и поперечные напряжения, а также близкие к нулю напряжения, перпендикулярные к боковым граням. Вблизи верхней грани в сечении Z = 1.5 мм вертикальная компонента ${{\sigma }_{z}},$ перпендикулярная к этой грани, близка к нулю. Близкие к нулю в средней части призмы поперечная ${{\sigma }_{x}}$ и нормальная $~{{\sigma }_{y}}$ компоненты увеличиваются до ~200 МПа.
Предел текучести стали марки 316L, полученной методом СЛП, зависит от направления выращивания и параметров технологического процесса [22–24]. Максимальные растягивающие напряжения (~500 МПа) вблизи ребер в центральной части призмы близки к пределу текучести стали 316L в направлении выращивания (540 МПа) [25].
По результатам измерений вдоль линий L4, L5, L6 (рис. 2б) и в сечениях (рис. 3б, 4б) можно сделать следующее заключение о распределении напряжений в горизонтальной призме. В центральной части объема призмы на глубине ≥5 мм от ее граней наблюдается трехосное напряженное состояние: все три компоненты напряжения сжимающие, с максимальным значением ~–200 МПа. Сжимающие напряжения в центральной части компенсируются соответствующими растягивающими напряжениями вокруг этой части. Растягивающие компоненты напряжения увеличиваются с приближением к граням. Максимальные значения компонент напряжений наблюдаются вблизи поверхностей граней, параллельных соответствующей компоненте: σZ ~ 100 МПа, σX = = 300 МПа, σY = 350 МПа.
Максимальные растягивающие напряжения вблизи поверхности в вертикальной призме значительно выше, чем в горизонтальной призме, и занимают значительно больший объем (рис. 4а и 4б). В вертикальной призме они направлены вдоль длинного ребра $({{\sigma }_{z}}),$ а в горизонтальной вдоль короткого ребра $({{\sigma }_{y}}).$ Качественно такое сильное различие можно объяснить следующим образом. В вертикальной призме вблизи вертикальных граней образуются растягивающие напряжения, направленные вертикально вдоль направления выращивания (длинного ребра). Они растут с удалением от свободных горизонтальных поверхностей (торцов призмы) достигая максимума на расстоянии ~15 от торцов (рис. 2а). В горизонтальной призме также вблизи вертикальных граней образуются растягивающие напряжения вдоль направления выращивания (короткого ребра), но максимальное напряжение на расстоянии ~10 будет меньше, чем на расстоянии ~15 от свободных горизонтальных поверхностей (нижней и верхней граней). Как в вертикальной, так и в горизонтальной призме, в центральной части присутствуют сжимающие напряжения, а вблизи поверхности – растягивающие, что хорошо согласуется с результатами [14, 15]. Отметим, что для понимания причин образования растягивающих напряжений вблизи поверхности и компенсирующих их сжимающих напряжений в средней части обеих призм необходимы расчеты методом конечных элементов.
Растягивающие напряжения на поверхности детали ухудшают коррозионную стойкость, прочностные характеристики и стойкость к образованию трещин. Поэтому при выращивании массивной детали методом СЛП для уменьшения остаточных напряжений направление выращивания по возможности следует выбирать параллельным ее наименьшему размеру.
ВЫВОДЫ
Методом нейтронной стресс-дифрактометрии изучено влияние направления выращивания на остаточные напряжения в образцах из стали марки 316L, полученных методом СЛП. На примере образца в форме призмы показано, что величина и распределение остаточных напряжений сильно зависят от направления выращивания. В призме, выращенной вдоль длинного ребра, растягивающие напряжения больше по величине и занимают больший объем, чем в такой же призме, выращенной вдоль короткого ребра. Максимальные растягивающие напряжения (~500 МПа), близкие к пределу текучести материала (~540 МПа), формируются вблизи длинных ребер вертикальной призмы. Общим для деталей, полученных методом СЛП, является формирование сжимающих напряжений внутри детали и растягивающих вблизи ее поверхности.
Работа выполнена на оборудовании УНУ НИК ИР-8 при частичной финансовой поддержке Министерства науки и высшего образования РФ в рамках выполнения работ по Государственному заданию ФНИЦ “Кристаллография и фотоника” РАН (проект RFMEFI62119X0035).
Список литературы
Köhler H., Partes K., Kornmeier J.R., Vollertsen F. Residual stresses in steel specimens induced by laser cladding and their effect on fatigue strength // Phys. Procedia. 2012. V. 39. P. 354–361.
Spierings A.B., Starr T.L., Wegener K. Fatigue performance of additive manufactured metallic parts // Rapid Prototyping J. 2013. V. 19. P. 88–94.
Riemer A., Leuders S., Thone M., Richard H.A., Troster T., Niendorf T. On the fatigue crack growth behavior in 316L stainless steel manufactured by selective laser melting // Eng. Fructure Mechanics. 2014. V. 120. P. 15–25.
Rangaswamy P., Griffth M.L., Prime M.B., Holden T.M., Rogge R.B., Edwards J.M., Sebring R.J. Residual stresses in LENS components using neutron diffraction and contour method // Mater. Sci. Eng. A. 2005. V. 399. P. 72–83.
Wang L., Felicelli S.D., P.Pratt P. Residual stresses in LENS-deposited AISI 410 stainless steel plates // Mater. Sci. Eng. A. 2008. V. 496. P. 234–241.
Liu Y., Yang Y., Wang D. A study on the residual stress during selective laser melting (SLM) of metallic powder // Int. J. Adv. Manuf. Technol. 2016. V. 87. P. 647–656.
Cheng B., Shrestha S., Chou K. Stress and deformation evaluations of scanning strategy effect in selective laser melting // Addit. Manuf. 2016. V. 12. P. 240–251.
Robinson J., Ashton I., Fox P., Jones E., Sutcliffe C. Determination of the effect of scan strategy on residual stress in laser powder bed fusion additive manufacturing // Addit. Manuf. 2018. V. 23. P. 13–24.
Szost B.A., Terzi S., Martina T., Boisselier D., Prytuliak A., Pirling T., Hofmann M., Jarvis D.J. A comparative study of additive manufacturing techniques: Residual stress and microstructural analysis of CLAD and WAAM printed Ti–6Al–4V components // Mater. Design. 2016. V. 89. P. 559–567.
Wu A.S., Brown D.W., Kumar M., Gallegos G.F., King W.E. An experimental investigation into additive manufacturing-induced residual stresses in 316L stainless steel // Metall. Mater. Trans. A. 2014. V. 45. P. 6260–6270.
Vrancken B., Cain V., Knutsen R., Van Humbeeck J. Residual stress via the contour method in compact tension specimens produced via selective laser melting // Scr. Mater. 2014. V. 87. P. 29–32.
Mugwagwa L., Dimitrov D., Matope S., Becker T. A methodology to evaluate the influence of part geometry on residual stresses in selective laser melting // International Conference on Competitive Manufacturing (COMA’16). 2016. P. 133–139.
Salmi A., Piscopo G., Atzeni E., Minetola P., Iuliano L. On the effect of part orientation on stress distribution in AlSi10Mg specimens fabricated by laser powder bed fusion (L-PBF) // Procedia CIRP. 2018. V. 67. P. 191–196.
Pant P., Proper S., Luzin V., Sjöström S., Simonsson K., Moverare J., Hosseini S., Pacheco V., Peng R.L. Mapping of residual stresses in as-built Inconel 718 fabricated by laser powder bed fusion: A neutron diffraction study of build orientation influence on residual stresses // Addit. Manuf. 2020. V. 36, 101501.
Rangaswamy P., Holden T.M., Rogge R., Griffith M.L. Residual stresses in components formed by the laser-engineered net shaping (LENS®) process // J. Strain Anal. Eng. Des. 2003. V. 38. № 6. P. 519–527.
Withers P.J. Depth capabilities of neutron and synchrotron diffraction strain measurement instruments. II. Practical implications // J. Appl. Cryst. 2004. V. 37. P. 607–612.
Woo W., Em V.T., Seong B., Shin E., Mikula P., Joo J., Kang M. Effect of wavelength-dependent attenuation on neutron diffraction stress measurements at depth in steels // J. Appl. Cryst. 2011. V. 44. P. 747–754.
Woo W., Em V.T., Mikula P., An G.B., Seong B. Neutron diffraction measurements of residual stresses in a 50mm thick weld // Mater. Sci. Eng. A. 2011. V. 528. P. 4120–4124.
Hutchings M.T., Withers P.J., Holden T.M., Lorentzen T. Introduction to the characterization of residual stress by neutron diffraction. 1st ed. CRC Press, 2005. 420 p.
Эм В.Т., Балагуров А.М., Глазков В.П., Карпов И.Д., Микула П., Мирон Н.Ф., Соменков В.А., Сумин В.В., Шароун Я., Шушунов М.Н. Двойной монохроматор для нейтронной стресс-дифрактометрии // ПТЭ. 2017. № 4. С. 75–81.
Em V.T., Karpov I.D., Somenkov V.A., Glazkov V.P., Balagurov A.M., Sumin V.V., Mikula P., Šaroun J. Residual stress instrument with double-crystal monochromator at research reactor IR-8 // Physica B: Condensed Matter. 2018. V. 551. P. 413–416.
Mertens A.I., Reginster S., Contrepois Q., Dormal T., Lemaire O. Microstructures and Mechanical Properties of Stainless Steel AISI 316L Processed by Selective Laser Melting // Mater. Sci. Forum. 2014. V. 783–786. P. 898–903.
Buchanan G., Matilinen V.-P., Salminen A., Gardnera L. Structural performance of additive manufactured metallic material and cross-sections // J. Construct. Steel Res. 2017. V. 136. P. 35–48.
Suryawanshi J., Prashanth K.G., Ramamurty U. Mechanical behavior of selective laser melted 316L stainless steel // Mater. Sci. Eng. A. 2017. V. 696. P. 113–121.
Erikson P. Evaluation of mechanical and microstructural properties for laser powder-bed fusion 316L. Master degree thesis, Uppsala University, Department of Engineering Sciences, Appl. Mater. Sci. 2018. http://www.diva-portal.org/smash/record.jsf?pid= diva2%3A1231504&dswid=-6174.
Дополнительные материалы отсутствуют.
Инструменты
Физика металлов и металловедение