Физика металлов и металловедение, 2022, T. 123, № 6, стр. 658-664
Влияние иттрия и эрбия на фазовый состав и старение сплава Al–Zn–Mg–Cu–Zr c повышенным содержанием меди
М. В. Главатских a, *, Р. Ю. Барков a, М. Г. Хомутов a, А. В. Поздняков a
a НИТУ “МИСиС”
119049 Москва, Ленинский просп., 4, Россия
* E-mail: glavatskikh@edu.misis.ru
Поступила в редакцию 24.01.2022
После доработки 17.03.2022
Принята к публикации 22.03.2022
- EDN: JRPUCJ
- DOI: 10.31857/S0015323022060067
Аннотация
С использованием термодинамических расчетов, сканирующей электронной микроскопии, рентгенофазового анализа, дифференциальной сканирующей калориметрии исследован фазовый состав сплава Al–Zn–Mg–Cu–Zr с избытком меди и дополнительно легированного иттрием или эрбием. В сплаве AlZnMgCuZrY отмечено наличие фаз (Al), T, Al8Cu4Y и AlMgY кристаллизационного происхождения. В сплаве с эрбием AlZnMgCuZrEr выявлено наличие трех дополнительных интерметаллидов кроме T-фазы: два интерметаллида состава близкого к фазе Al8Cu4Er и один состава Al3Er. В одной из частиц фазы Al8Cu4Er обнаружено примерно 2 мас. % Fe. Старение при температуре 150°С показывает больший прирост твердости в сплаве с эрбием при одинаковом достигнутом уровне твердости во всех сплавах. Перестаривание при 210 и 250°С протекает существенно быстрее в сплаве без добавок иттрия и эрбия при одинаковом уровне упрочнения. С учетом, что кинетику старения определяет в основном состав (Al), то различия можно объяснить более бедным по основным элементам цинку, магнию и меди твердым раствором и дисперсоидами, образованными при гомогенизации перед закалкой в сплавах с добавками. Сплавы с добавками иттрия и эрбия незначительно уступают по пределу текучести при повышенных температурах, что, вероятно, связано с меньшей легированностью алюминиевой матрицы, но отличаются лучшей технологичностью при литье.
ВВЕДЕНИЕ
При содержании цинка на уровне 3–7 мас. % и магния 1–4.5 мас. % в сплавах на основе системы Al–Zn–Mg–Cu обычно достигается макcимальное упрочнение после закалки и старения [1–3]. Однако сплавы с таким соотношением Zn/Mg (более 1) обладают низким сопротивлением коррозии [2, 3] и высокой склонностью к образованию горячих трещин [4]. Сочетать достаточно высокие механические, коррозионные и технологические свойства можно при соотношении Zn/Mg примерно равном 1 [2–6]. Повышения технологичности при литье сплавов на основе системы Al–Zn–Mg возможно достичь за счет легирования эвтектикообразующими элементами [5–9]. Легирование редкоземельными и переходными металлами, в частности, цирконием способствует модифицированию зеренной структуры и упрочнению за счет образования дисперсоидов [10–16]. При этом в сплавах формируется структура, обеспечивающая хорошие удлинения при сверхпластической деформации и высокий уровень свойств после деформации [17–22].
Квазибинарные сплавы тройных систем Al–Cu–Y [23, 24] и Al–Cu–Er [24, 25], представляют большой интерес благодаря узкому интервалу кристаллизации и высокой термической стабильности фаз кристаллизационного происхождения. Дополнительное легирование цирконием позволяет существенно повысить характеристики механических свойств за счет выделения дисперсоидов Al3(Zr,Y) [26] и Al3(Zr,Er) [27, 28]. В результате литейные и деформируемые сплавы на основе систем Al–Cu–Y и Al–Cu–Er отличаются достаточно высокой прочностью, как при комнатной, так и при повышенных температурах [28–32]. Данная работа посвящена изучению влияния легирования иттрием и эрбием на фазовый состав и упрочнение при старении сплава системы Al–Zn–Mg–Cu–Zr с повышенным содержанием меди.
МЕТОДИКА ЭКСПЕРИМЕНТОВ
Сплавы для исследования выплавлены в печи сопротивления из Al (99.99%), цинка (99.9%), магния (99.9%) меди (99.9%), лигатур Al–5Zr, Al–10Y и Al–10Er. Сплавы заливали в графитовую изложницу с внутренней полостью 15 × 60 × 150 мм при скорости охлаждения около 15 K/с. Термическую обработку проводили в печах “Nabertherm” и “Snol” с вентилятором и точностью поддержания температуры 1°С. Подготовку шлифов для микроструктурных исследований осуществляли на шлифовально-полировальной установке Struers Labopol-5. Микроструктурные исследования и идентификацию фаз выполняли на сканирующем электронном микроскопе (СЭМ) TESCAN VEGA 3LMH с использованием энерго-дисперсионного детектора X-Max 80. Калориметрический анализ выполнен на дифференциальном сканирующем калориметре (ДСК) Labsys Setaram. Рентгенофазовый анализ проведен с использованием дифрактометра Brucker D8 Advanced. Термодинамические расчеты проводили с использованием программы Thermo-Calc в базе данных TCAL4.
Показатель горячеломкости (ПГ) определяли по “карандашной” пробе путем трех заливок в стальной кокиль стрежней разного диаметра с переходными сечениями [4, 7]. Твердость измеряли стандартным методом Виккерса. Комплекс Gleeble-3800 использован для испытаний на сжатие при комнатной и повышенных температурах 150, 200 и 250°С со скоростью 4 мм/мин.
РЕЗУЛЬТАТЫ ЭКСПЕРИМЕНТОВ И ОБСУЖДЕНИЕ
Основываясь на ранее проведенных исследованиях [7, 8], содержание основных добавок цинка и магния выбрано по 4.5 мас. %. Медь в высокопрочных сплавах обычно вводят на уровне 1.5 мас. %, чтобы при гомогенизации она полностью переходила в алюминиевый твердый раствор (Al). В данной работе в базовый сплав введено 2.5 мас. % меди. Избыток меди необходим для сплавов с иттрием и эрбием для образования высокотемпературных эвтектических фаз Al8Cu4Y и Al8Cu4Er [17–22]. В соответствии с этим концентрации иттрия и эрбия выбраны 0.4 и 1 мас. % соответственно, для соблюдения атомного соотношения Cu/Y и Cu/Er равного 4. Цирконий, как известно существенно повышает ликвидус алюминиевых сплавов. Для определения содержания циркония проведен расчет политермического разреза Al–4.5Zn–4.5Mg–2.5Cu–(0–0.25)Zr (рис. 1а). Согласно разрезу, при увеличении содержания циркония с 0.05 до 0.25 мас.% ликвидус возрастает примерно с 680 до 800°С. Во избежание потерь легкоплавких элементов при выплавке сплавов, концентрация циркония выбрана равной 0.2 мас. %, когда температура ликвидуса составляет 770°С. Согласно кривой неравновесной кристаллизации по модели Шайля (расчет в программе Thermo-Calc) в сплаве при кристаллизации образуются фазы Al3Zr, (Al), S (Al2CuMg) и Т (AlZnMgCu).
Рис. 1.
Политермический разрез Al–4.5Zn–4.5Mg–2.5Cu–(0–0.25)Zr (а) и кривая неравновесной кристаллизации сплава Al–4.5Zn–4.5Mg–2.5Cu–0.2Zr (б) (штриховая линия на (б) – равновесная кривая).
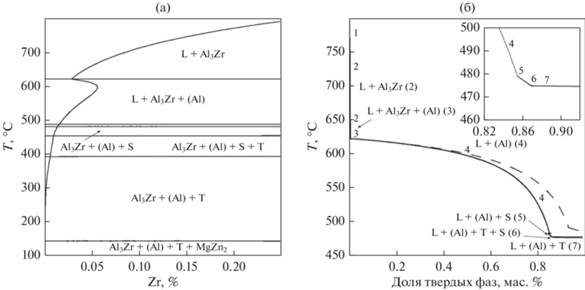
При этом доля эвтектики (Al) + S очень мала – около 2% (вставка на рис. 1б).
На рис. 2 приведены микроструктуры слитков исследованных сплавов. Согласно результатам анализа химического состава с помощью СЭМ, содержание цинка в сплавах составило 4.8–5.1 мас. %, магния – 4.1–4.2 мас. %, меди 2.4–2.6 мас. %, циркония – 0.2 мас. %, иттрия и эрбия по 0.4 мас. % и 1 мас. % соответственно. В базовом сплаве AlZnMgCuZr помимо (Al) присутствует дисперсная эвтектика с фазой T (рис. 2а). Цирконий полностью растворен в (Al). Фазы S в структуре не выявлено. Фазовый состав подтверждается рентгенофазовым анализом (рис. 3) – на рентгенограмме отмечены пики от (Al) и T-фазы. После введения иттрия в сплаве AlZnMgCuZrY отмечено наличие двух интерметаллидов, обогащенных медью и иттрием (частицы фаз выделены кругами на рис. 2б) и магнием и иттрием (частица фазы выделена овалом на рис. 2б). Фаза богатая медью и иттрием соответствует соединению Al8Cu4Y, что подтверждается наличием пиков на рентгенограмме (рис. 3). Данных о тройной фазе AlMgY нет в базе данных, однако ранее было выявлено наличие подобной фазы в сплаве Al–Mg–Mn–Zr–Sc–Y [33]. В сплаве с эрбием AlZnMgCuZrEr отмечено наличие трех дополнительных интерметаллидов: два состава близкого к фазе Al8Cu4Er (выделения овалом и прямоугольником на рис. 2в) и один состава Al3Er. Соответствующие пики выявлены на рентгенограмме (рис. 3). В одной из частиц фазы Al8Cu4Er отмечено наличие примерно 2 мас. % Fe (частица выделена овалом на рис. 2в). Железо является неотъемлемой примесью алюминия и попадает в сплав, в том числе из лигатур. Железо предположительно замещает часть атомов меди в фазе, в таком случае ее можно записать как Al8(Cu,Fe)4Er. При этом отдельных пиков от этой фазы не отмечено на рентгенограмме (рис. 3). Растворение примеси железа в фазах Al8Cu4Y и Al8Cu4Er было отмечено ранее в работах [34, 35]. Концентрация иттрия и эрбия в (Al) составляет 0.1–0.2 мас. %, а цирконий также как и в базовом сплаве не образовал интерметаллидов и полностью растворился в матрице.
Рис. 2.
Литая микроструктура (СЭМ) сплавов AlZnMgCuZr (а), AlZnMgCuZrY (б) и AlZnMgCuZrEr (в) и распределение легирующих элементов между фазами в выделенной области (белые прямоугольники).
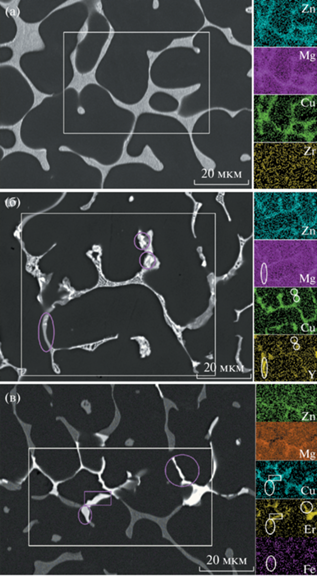
Таблица 1.
Предел текучести на сжатие (МПа) при комнатной и повышенных температурах
Сплав | 20°С | 150°С | 200°С | 250°С |
---|---|---|---|---|
AlZnMgCuZr | 435 ± 10 | 390 ± 5 | 360 ± 5 | 295 ± 5 |
AlZnMgCuZrY | 420 ± 15 | 350 ± 10 | 335 ± 15 | 265 ± 5 |
AlZnMgCuZrEr | 460 ± 15 | 380 ± 5 | 335 ± 15 | 285 ± 5 |
Температура солидуса сплава AlZnMgCuZr составляет 477°С (рис. 4), что хорошо согласуется с результатами расчетов. Два пика на ДСК-кривой при нагреве соответствуют реакциям плавления T- и S-фаз соответственно, что также подтверждают расчеты. В сплавах AlZnMgCuZrY и AlZnMgCuZrEr при нагреве выделен один основной первый пик при температуре солидуса и высокотемпературные пики в интервале 540–580°С, соответствующие реакциям с интерметаллидами, обогащенными иттрием и эрбием.
Сплавы гомогенизировали при 465°С в течение 1, 3 и 6 ч. В процессе гомогенизации происходит растворение неравновесного избытка фазы Т и сопутствующее насыщение цинком, магнием и медью (Al). После трех часов выдержки структура практически не изменяется и содержание элементов в твердом растворе стабилизируется. При этом содержание основных твердорастворных упрочнителей в сплавах с иттрием и эрбием несколько меньше из-за образования при кристаллизации нерастворимых интерметаллидов. Микроструктура после трехчасовой гомогенизации перед закалкой представлена на рис. 5. Параллельно в сплавах должна проходить гетерогенизация с выделением L12 дисперсоидов фаз Al3(Zr), Al3(Zr,Y) и Al3(Zr,Er).
Рис. 5.
Микроструктура (СЭМ) сплавов AlZnMgCuZr (а), AlZnMgCuZrY (б) и AlZnMgCuZrEr (в) после гомогенизации при 465°С c выдержкой 3 ч и закалки, и распределение легирующих элементов между фазами в выделенной области (белые прямоугольники).
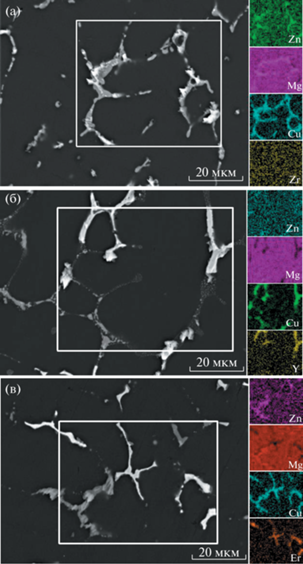
После трехчасовой гомогенизации при 465°С и закалки твердость сплавов AlZnMgCuZr, AlZnMgCuZrY и AlZnMgCuZrEr составила 98, 91 и 88 HV соответственно (рис. 6). Последующее старение при температуре 150°С показывает больший прирост твердости в сплаве с эрбием при примерно одинаковом достигнутом уровне твердости во всех сплавах. Достижение пика твердости после старения при 180°С сокращается до 1–3 ч, при этом сплав с эрбием начинает уступать в величине упрочнения. Перестаривание при температурах 210 и 250°С протекает существенно быстрее в сплаве без добавок иттрия и эрбия, при примерно одинаковом уровне упрочнения. С учетом, что кинетику старения определяет в основном состав (Al), а во всех сплавах по основным элементам цинку, магнию и меди он близок, то различия в кинетике определяют дисперсоиды, образованные при гомогенизации перед закалкой.
Рис. 6.
Зависимости твердости от времени старения при температурах 150 (а), 180 (б), 210 (в)
и 250°С (г) после гомогенизации при 465°С c выдержкой 3 часа и закалки, – сплав AlZnMgCuZr,
– сплав AlZnMgCuZrY,
– сплав AlZnMgCuZrEr.
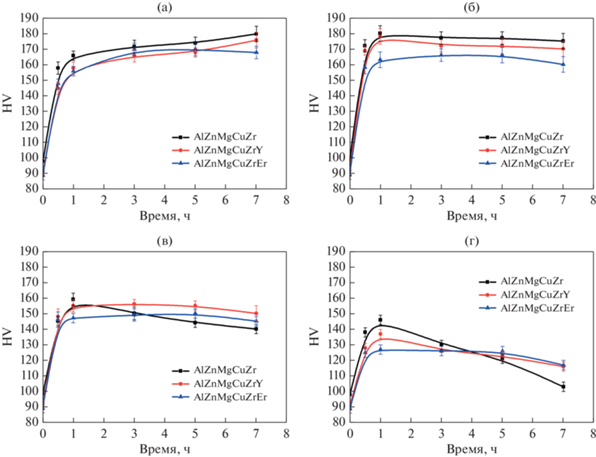
В табл. 1 представлены результаты испытаний на сжатие при комнатной и повышенных температурах. Предел текучести сплавов при комнатной температуре находится на уровне 420–460 МПа. С повышением температуры испытания предел текучести снижается до 265–295 МПа при 250°С. При этом сплавы с добавками иттрия и эрбия незначительно уступают по пределу текучести, что, вероятно связано с меньшей легированностью алюминиевой матрицы. Однако сплавы с добавками отличаются лучшей технологичностью при литье – их показатель горячеломкости по карандашной пробе составил 14 мм против 16 мм у сплава без добавок. Для сравнения новые жаропрочные сплавы систем Al–Cu–Y и Al–Cu–Er при 250°С имеют меньший предел текучести на сжатие 197–223 МПа при лучших литейных свойствах [31]. Композиционные материалы на основе жаропрочной матрицы Al–Cu–Mn c карбидом бора [36] и жаропрочные аддитивные сплавы Al–Ce–Cu [37] также отличаются более низким пределом текучести в 160 МПа при 250°С.
ВЫВОДЫ
1. В сплаве AlZnMgCuZrY, помимо алюминиевого твердого раствора и фазы T, отмечено наличие двух интерметаллидов фаз Al8Cu4Y и AlMgY кристаллизационного происхождения.
2. В сплаве с эрбием AlZnMgCuZrEr отмечено наличие трех дополнительных интерметаллидов фаз Al8Cu4Er, Al8(Cu,Fe)4Er и Al3Er. В некоторых частицах фазы Al8Cu4Er растворяется до 2 мас. % Fe.
3. Старение при температуре 150°С показывает больший прирост твердости в сплаве с эрбием при примерно одинаковом достигнутом уровне твердости во всех сплавах. Перестаривание при 210 и 250°С протекает существенно быстрее в сплаве без добавок иттрия и эрбия, при примерно одинаковом уровне упрочнения. С учетом, что кинетику старения определяет в основном состав (Al), то различия можно объяснить более бедным по основным элементам цинку, магнию и меди твердым раствором и дисперсоидами, образованными при гомогенизации перед закалкой в сплавах с добавками.
4. Сплавы с добавками иттрия и эрбия незначительно уступают по пределу текучести при повышенных температурах, что вероятно связано с меньшей легированностью алюминиевой матрицы, но отличаются лучшей технологичностью при литье.
Исследование выполнено за счет гранта Российского научного фонда (проект № 20-79-00305).
Список литературы
Zou Y., Wu X., Tang S., Zhu Q., Song H., Guo M., Cao L. Investigation on microstructure and mechanical properties of Al–Zn–Mg–Cu alloys with various Zn/Mg ratios // J. Mater. Sci. & Tech. 2021. V. 85. P. 106–117.
Золоторевский В.С. Микростроение и механические свойства литых алюминиевых сплавов: Дис. докт. техн. наук, М.: МИСиС, 1978. 444 с.
Gerchikova N.S., Fridlyander I.N., Zaitseva N.I., Kirkina N.N. Change in the structure and properties of Al–Zn–Mg alloys // Met. Sci. & Heat Treat. 1972. V. 14. № 3. P. 233–236.
Новиков И.И. Горячеломкость цветных металлов и сплавов. М.: Наука, 1966. 299 с.
Чеверикин В.В. Влияние эвтектикообразующих элементов на структуру и свойства высокопрочных сплавов системы Al–Zn–Mg. Дис. … канд. техн. наук, М.: МИСиС, 2007. 179 с.
Pan Y., Zhang D., Liu H., Zhuang L., Zhang J. Precipitation hardening and intergranular corrosion behavior of novel Al–Mg–Zn(–Cu) alloys // J. All. & Comp. 2021. V. 853. P. 157199.
Zolotorevskiy V.S., Pozdniakov A.V., Churyumov A.Yu. Search for Promising Compositions for Developing New Multiphase Casting Alloys Based on Al–Zn–Mg Matrix Using Thermodynamic Calculations and Mathematic Modeling // Phys. Met. Metall. 2014. V. 115. № 3. P. 286–294.
Pozdniakov A.V., Zolotorevskiy V.S., Mamzurina O.I. Determining the hot cracking index of Al-Mg-Zn casting alloys calculated using the effective solidification range // Int. J. Cast Met. Res. 2015. V. 28. № 5. P. 318–321.
Shurkin P.K., Akopyan T.K., Galkin S.P., Aleshchenko A.S. Effect of Radial Shear Rolling on the Structure and Mechanical Properties of a New-Generation High-Strength Aluminum Alloy Based on the Al–Zn–Mg–Ni–Fe System // Met. Sci. & Heat Treat. 2019. V. 60. P. 764–769.
Ryum N. Precipitation and recrystallization in an Al–0.5 wt % Zr-alloy // Acta Metall. 1969. V. 17. P. 269–278.
Nes E., Billdal H. The mechanism of discontinuous precipitation of the metastable Al3Zr phase from an Al-Zr solid solution // Acta Metall. 1977. V. 25. P. 1039–1046.
Knipling K.E., Dunand D.C., Seidman D.N. Nucleation and Precipitation Strengthening in Dilute Al–Ti and Al–Zr Alloys // Metall. Mater. Trans. A. 2007. V. 38. P. 2552–2563.
Белов Н.А., Алабин А.Н, Прохоров А.Ю. Влияние добавки циркония на прочность и электросопротивление холоднокатаных алюминиевых листов // Изв. вузов. Цвет. Металл. 2009. № 4. С. 42–47.
Белов Н.А., Алабин А.Н., Прохоров А.Ю. Влияние отжига на электросопротивление и механические свойства холоднодеформированного сплава Al–0.6% (мас.) Zr // Цвет. Мет. 2009. № 10. С. 65–68.
Souza P.H.L., de Oliveira C.A.S., do Vale Quaresma J.M. Precipitation hardening in dilute Al–Zr alloys // J. Mater. Res. Tech. 2018. V. 7. P. 66–72.
Zakharov V.V., Fisenko I.A. Effect of Homogenization on the Structure and Properties of Alloy of the Al–Zn–Mg–Sc–Zr System // Met. Sci. & Heat Treat. 2018. V. 60. P. 354–359.
Mikhaylovskaya A.V., Kotov A.D., Pozdniakov A.V., Portnoy V.K. A high-strength aluminium-based alloy with advanced superplasticity // J. All. Comp. 2014. V. 599. P. 139–144.
Kotov A.D., Mikhaylovskaya A.V., Borisov A.A., Yakovtseva O.A., Portnoy V.K. High-strain-rate superplasticity of the Al–Zn–Mg–Cu alloys with Fe and Ni additions // Phys. Met. Metall. 2017. V. 118. P. 913–921.
Kotov A.D., Mikhaylovskaya A.V., Portnoy V.K. Effect of the solid-solution composition on the superplasticity characteristics of Al–Zn–Mg–Cu–Ni–Zr Alloys // Phys. Met. Metall. 2014. V. 115. P. 730–735.
Petrova A.N., Brodova I.G., Razorenov S.V., Shorokhov E.V., Akopyan T.K. Mechanical Properties of the Al–Zn–Mg–Fe–Ni Alloy of Eutectic Type at Different Strain Rates // Phys. Met. Metall. 2019. V. 120. P. 1221–1227.
Brodova I.G., Shirinkina I.G., Rasposienko D.Yu., Akopyan T.K. Structural Evolution in the Quenched Al–Zn–Mg–Fe–Ni Alloy during Severe Plastic Deformation and Annealing // Phys. Met. Metall. 2020. V. 121. P. 899–905.
Shirinkina I.G., Brodova I.G. Annealing-Induced Structural–Phase Transformations in an Al–Zn–Mg–Fe–Ni Alloy after High Pressure Torsion // Phys. Met. Metall. 2020. V. 121. P. 344–351.
Pozdniakov A.V., Barkov R.Y. Microstructure and materials characterisation of the novel Al–Cu–Y alloy // Mater. Sci. Tech. 2018. V. 34. № 12. P. 1489–1496.
Amer S.M., Barkov R.Y., Yakovtseva O.A., Pozdniakov A.V. Comparative Analysis of Structure and Properties of Quasibinary Al–6.5Cu–2.3Y and Al–6Cu–4.05Er Alloys // Phys. Met. Metall. 2020. V. 121. № 5. P. 476–482.
Pozdnyakov A.V., Barkov R.Yu., Sarsenbaev Zh., Amer S.M. and Prosviryakov A.S. Evolution of Microstructure and Mechanical Properties of a New Al–Cu–Er Wrought Alloy // Phys. Met. Metall. 2019. V. 120. № 6. P. 614–619.
Pozdniakov A.V., Barkov R.Yu, Amer S.M., Levchenko V.S., Kotov A.D., Mikhaylovskaya A.V. Microstructure, mechanical properties and superplasticity of the Al–Cu–Y–Zr alloy // Mater. Sci. Eng. A. 2019. V. 758. P. 28–35.
Amer S.M., Barkov R.Yu., Yakovtseva O.A., Loginova I.S., Pozdniakov A.V. Effect of Zr on microstructure and mechanical properties of the Al–Cu–Er alloy //Mater. Sci. Tech. 2020. V. 36. № 4. P. 453–459.
Amer S.M., Mikhaylovskaya A.V., Barkov R.Yu., Kotov A.D., Mochugovskiy A.G., Yakovtseva O.A., Glavatskikh M.V., Loginova I.S., Medvedeva S.V., Pozdniakov A.V. Effect of Homogenization Treatment Regime on Microstructure, Recrystallization Behavior, Mechanical Properties, and Superplasticity of Al–Cu–Er–Zr Alloy // JOM. 2021. V. 73. № 10. P. 3092–3101.
Amer S., Yakovtseva O., Loginova I., Medvedeva S., Prosviryakov Al., Bazlov A, Barkov R. Pozdniakov A. The Phase Composition and Mechanical Properties of the Novel Precipitation-Strengthening Al–Cu–Er–Mn–Zr Alloy // Appl. Sci. 2020. V. 10. P. 5345.
Amer S.M., Barkov R.Yu., Pozdniakov A.V. Effect of Mn on the Phase Composition and Properties of Al–Cu–Y–Zr Alloy // Phys. Met. Metall. 2020. V. 121. № 2. P. 1227–1232.
Amer S.M., Barkov R.Y., Prosviryakov A.S., Pozdniakov A.V. Structure and properties of new heat-resistant cast alloys based on the Al–Cu–Y and Al–Cu–Er systems // Phys. Met. Metall. 2021. V. 122. P. 908–914.
Amer S.M., Barkov R.Y., Prosviryakov A.S., Pozdniakov A.V. Structure and properties of new wrought Al–Cu–Y and Al–Cu–Er based alloys // Phys. Met. Metall. 2021. V. 122. P. 915–922.
Barkov R.Yu., Pozdniakov A.V., Tkachuk E., Zolotorevskiy V.S. Effect of Y on microstructure and mechanical properties of Al–Mg–Mn–Zr–Sc alloy with low Sc content // Mat. Let. 2018. V. 217. P. 135-138.
Amer S.M., Barkov R.Yu., Pozdniakov A.V. Effect of Iron and Silicon Impurities on Phase Composition and Mechanical Properties of Al–6.3Cu–3.2Y Alloy // Phys. Met. Metall. 2020. V. 121. № 10. P. 1002–1007.
Amer S.M., Barkov R.Yu., Pozdniakov A.V. Effect of Impurities on the Phase Composition and Properties of a Wrought Al–6% Cu–4.05% Er Alloy // Phys. of Met. and Metall. 2020. V. 121. № 5. P. 495–499.
Lotfy A., Pozdniakov A.V., Zolotorevskiy V.S., Mohamed E., Abou El-Khair M.T., Daoud A., Fairouz F. Microstructure, compression and creep properties of Al–5% Cu–0.8Mn/5% B4C composites // Mater. Res. Exp. 2019. V. 6. P. 095530.
Manca D.R., Churyumov A.Yu., Pozdniakov A.V., Prosviryakov A.S., Ryabov D.K., Krokhin A.Yu., Korolev V.A., Daubarayte D.K. Microstructure and properties of novel heat resistant Al–Ce–Cu alloy for additive manufacturing // Met. Mater. Intern. 2019. V. 25. № 3. P. 633–640.
Дополнительные материалы отсутствуют.
Инструменты
Физика металлов и металловедение