Физика металлов и металловедение, 2022, T. 123, № 8, стр. 864-871
Влияние термической обработки и условий нагружения на структуру оболочки из Аl–Zn–Mg–Сu сплава
И. Г. Ширинкина a, *, Д. Ю. Распосиенко a, И. Г. Бродова a, А. Б. Смирнов b, А. В. Коваль b
a Институт физики металлов УрО РАН
620990 Екатеринбург, ул. С. Ковалевской, 18, Россия
b РФЯЦ-ВНИИТФ
45677 Снежинск, ул. Васильева, 13, а.я. 245, Россия
* E-mail: shirinkina@imp.uran.ru
Поступила в редакцию 17.03.2021
После доработки 06.05.2022
Принята к публикации 12.05.2022
- EDN: TNKQEZ
- DOI: 10.31857/S0015323022080101
Аннотация
Приведены результаты сравнения деформационного поведения и характера схлопывания полых цилиндрических оболочек из сплава системы Аl–Zn–Mg–Сu после различной преддеформационной термической обработки, нагруженных методом скользящей детонации по двум режимам, которые отличались длительностью импульса ударной волны. Показано, что при одинаковой мощности взрывчатых веществ сценарий схождения оболочек из исследованного сплава слабо зависит от длительности импульса ударной волны, задаваемого конструктивными особенностями экспериментальной установки. Установлено, что на реологию схождения существенно влияет фазовый состав сплава, задаваемый термической обработкой. Показано, что в отожженной оболочке образуются множественные отколы, а в закаленной оболочке наблюдается полное и устойчивое схлопывание до образования сплошного цилиндра. Методами световой оптики, сканирующей и просвечивающей электронной микроскопии изучена эволюция структуры цилиндрических оболочек. Разный сценарий схождения связан с наличием или отсутствием источников хрупкого разрушения, которыми являются интерметаллидные фазы, число, размер и природа которых регулируется исходной термической обработкой сплава.
ВВЕДЕНИЕ
Изучая структурные превращения при динамических нагрузках, можно получить данные о взаимосвязи между характеристиками ударно-волнового воздействия и особенностями высокоскоростного деформирования металлов и сплавов [1–5]. Несмотря на достаточное число работ в этой области, они не теряют своей актуальности и активно развиваются в настоящее время, так как применение конструкционных сплавов в условиях экстремальных воздействий неуклонно расширяется [6–9]. Так, в [10–12] подробно изучен процесс высокоскоростного схождения медных и стальных цилиндрических оболочек разного диаметра при различной толщине стенки и интенсивности взрывного нагружения, и описано несколько структурных механизмов потери устойчивости фронта радиальной деформации. Подробно разобраны последовательные стадии процесса схождения оболочек и эволюция структурных зон при нагружении скользящей детонационной волной.
Известно, что ударная сжимаемость материалов и их реологические свойства зависят от прочностных свойств. Учитывая широкую палитру Al сплавов, среди них легко выбрать материалы, отличающиеся по своим физико-механическим характеристикам, что позволяет использовать их в качестве удобных моделей для изучения особенностей деформирования материалов под действием сжимающих ударно-волновых нагрузок. Так, в работе [13] описаны особенности динамического деформирования цилиндрических оболочек из сплава АМг6 в зависимости от интенсивности нагружения. На основании результатов исследования эволюции макро- и микроструктуры оболочек в процессе схождения, показано влияние интенсивности детонационной волны на деформационное поведение сплава АМг6. В [14] установлено влияние структуры и статических механических свойств оболочек из алюминиевых сплавов Д16 и АМц на характер их схлопывания при одинаковых условиях нагружения. Показано, что наличие интерметаллидных фаз в упрочненном сплаве Д16 препятствует устойчивому схождению оболочек и приводит к множественным отколам и разрушению.
Сплав В95 относится к классу многокомпонентных термически упрочняемых Al-сплавов. Фазовый состав, структуру и свойства таких материалов можно регулировать в широких пределах, применяя различную термическую обработку. Смена режима термической обработки задает разный уровень прочности и пластичности материала, что, безусловно, должно сказаться на деформационном поведении материала в процессе высокоинтенсивного нагружения. Так, для сплава В95 известны свойства, полученные после таких режимов термической обработки как Т1 – закалка и искусственное старение (σв = 490–510 МПа, σт = = 375–400 МПа, δ = 5–7%), и Т – отжиг (σв = = 275 МПа, σт = 100 МПа, δ = 10%) [15–18].
Цель исследований – изучение структурных особенностей при схлопывании полых цилиндрических оболочек из сплава В95 в зависимости от термической обработки материала до нагружения и длительности импульса ударной волны.
МЕТОДИКА ЭКСПЕРИМЕНТА
В качестве материала для цилиндрических оболочек был выбран пруток из многокомпонентного алюминиевого сплава В95 состава (мас. %): Al основа, Сu–1.6; Mg–2.4; Zn–5.3; Cr–0.12, Mn–0.2, Ti < 0.05; Si < 0.5; Fe < 0,5. В состоянии поставки (ГОСТ 21488–97 и ГОСТ 8617–81) отожженный пруток имел твердость 61HB и гетерофазную структуру, состоящую из Al-твердого раствора, легированного Cu, Zn, Mg, интерметаллидов, включая фазы эвтектического происхождения и упрочняющие фазы [16–18]. Для установления зависимости деформационного поведения и характера схождения оболочек от их предыстории был приготовлен образец 2 путем термической обработки исходного прутка (образец 1). Термическая обработка (т/о) состояла из закалки на твердый раствор по стандартному режиму: нагрев до температуры 470°С, выдержка 30 мин, охлаждение в воде [18]. Проведенные металлографические исследования показали, что в свежезакаленном состоянии (образец 2) количество интерметаллидов резко сократилось, остались единичные включения фаз с тугоплавкими элементами (Fe, Mn, Cr), декорирующие зерна пересыщенного Al-твердого раствора. Растворение интерметаллидов и увеличение содержания меди, цинка и магния в Al-твердом растворе привели к твердорастворному упрочнению сплава и росту его твердости от 61 до 71 HB. Микротвердость Al-матрицы образца 2 составила HV = 850 МПа, против HV = 600 МПа матрицы образца 1.
Из этих двух исходных заготовок с разной структурой были выточены цилиндрические полые оболочки с внутренним диаметром 20 мм и толщиной стенки 2 мм. Для взрывного нагружения оболочек использовали оригинальную экспериментальную сборку [14], которая позволяла в одном опыте комбинировать условия нагружения: часть оболочки (приблизительно 1/2 ее длины) нагружали без наружного стального корпуса, а оставшуюся часть оболочки помещали в корпус толщиной 50 мм, который обеспечивал более длительный импульс ударной волны (табл. 1). Схождение оболочек к оси симметрии осуществлялось под действием скользящей детонационной волны. Учитывая крайне нестабильное состояние после закалки и способность сплава В95 к естественному старению в процессе вылеживания материала, образец 2 был приготовлен непосредственно перед проведением испытаний.
Таблица 1.
Условия нагружения оболочек из сплава В95
№№ оболочек | т/о | схема |
---|---|---|
1/1 | Отжиг (состояние поставки), образец 1 | Без корпуса |
1/2 | » | С корпусом |
2/1 | Закалка, образец 2 | Без корпуса |
2/2 | » | С корпусом |
При данной схеме нагружения деформация осуществляется преимущественно в радиальном направлении, поэтому структурные исследования выполнены на поперечных сечениях оболочки с помощью светового микроскопа “Neophot-32”. Исследования тонкой структуры и локальный микроанализ проводили с помощью сканирующего электронного микроскопа (СЭМ) QUANTA-200 с приставкой для энергодисперсионного анализа (EDS) и просвечивающих электронных микроскопов JEM 200CX при напряжении 160 кВ и Tecnai G 30 Twin при ускоряющем напряжении 300 кВ. Рентгеноструктурные исследования (РСА) проведены с помощью лабораторного дифрактометра “Bruker Advance-D8” в медном Kα-излучении (Kαср = 0.15418 нм) в интервале углов 18°–140° с шагом съемки 0.02° и временем экспозицией 2 с. Анализ полученных дифрактограмм проводили с помощью программ DIFFRAC.EVA 4.0 и DIFFRAC.TOPAS 5.0. Аттестацию свойств нагруженных оболочек и исходных образцов проводили путем измерения твердости по Бринеллю и микротвердости основы сплава – Al-твердого раствора. Микротвердость Hv измеряли на приборе “ПМТ-3” при нагрузке 0.2–0.5 H (погрешность не превышала 5%). Твердость НВ измеряли при нагрузке 250 кг шариком ∅10 мм (ГОСТ 9012–59).
РЕЗУЛЬТАТЫ И ИХ ОБСУЖДЕНИЕ
С целью определения влияния фазового состава сплава на сценарий схождения оболочек были проведены сравнительные структурные исследования оболочек, нагруженных по одинаковой схеме, т.е. оболочек 1/1 и 2/1 и 1/2 и 2/2. Внешний вид поперечных сечений оболочек 1/1 и 2/1, нагруженных без корпуса, показан на рис. 1а, 1б. Видно, что при одинаковых условиях нагружения наблюдается разный характер схождения оболочек. Очевидно, что отклик материала на ударно-волновое воздействие связан с разной структурой исходных образцов. Так, в отожженной оболочке 1/1 образовались множественные отколы, и она распалась на 15 фрагментов, собранных и впоследствии склеенных для визуализации, как показано на рис. 1а. В результате схлопывания закаленной оболочки 2/1 сформировался сплошной цилиндр диаметром 6 мм с центральной полостью, от которой радиально отходят трещины (рис. 1б).
Рис. 1.
Поперечные сечения оболочек из сплава В95 после ударно-волнового нагружения без наружного корпуса: а – оболочка № 1/1, б – оболочка № 2/1; в – поры и участки плавления вокруг центральной полости в оболочке 2/1 (СЭМ).
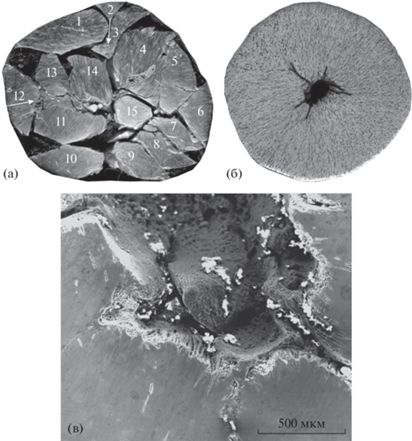
Форма полости в оболочке 2/1 эллипсообразная, отходящие от нее радиальные трещины распространяются на расстоянии 1–1.5 мм от края полости. Часть откольных трещин залечивается в процессе инерционного схождения, вокруг них формируются участки литой структуры, доказывающие существование зон локализованной деформации с повышенной температурой, превышающей температуру плавления сплава В95 (рис. 1в). Осесимметричный характер радиальной деформации в оболочке 2/1 наглядно виден по кольцевой форме зон деформированной и литой структуры. Было установлено, что независимо от разного характера схождения, преимущественной структурой обеих оболочек является деформированная полосовая макроструктура, характеристики которой изменяются по радиусу оболочки в зависимости от степени высокоскоростного сжатия и температуры. Например, ширина волокон уменьшается с 35 до 15 мкм от наружной поверхности к центру. Границы зерен декорированы интерметаллидами, которые дробятся под действием деформации, а в центральной зоне “слипаются” в конгломераты размером 8–10 мкм.
Внутри зерен в отдельных фрагментах оболочки 1/1 четко видны следы интенсивной деформации, о чем свидетельствуют изогнутые границы, пересекающиеся следы скольжения, деление зерен на субзерна размером 2–5 мкм (рис. 2а).
Рис. 2.
Структура оболочек: а – участки деформированной структуры (оболочка 1/1); б – “вихревая” субструктура (оболочка 2/1); в – трещины (СЭМ).
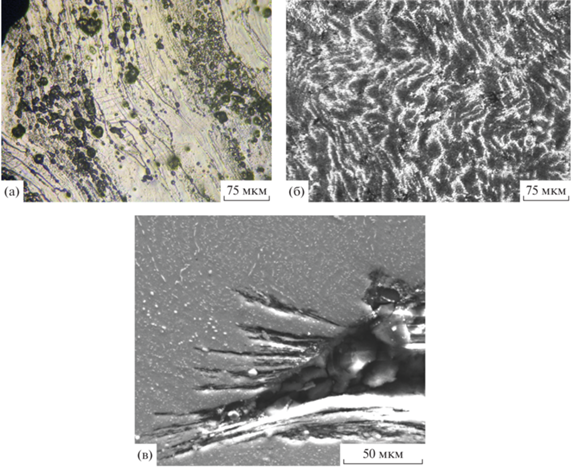
В оболочке 2/1 выявлены участки с “вихревой” субструктурой, которые появляются около трещин (рис. 2б, 2в) или начинаются от наружной поверхности оболочки, нарушая тем самым радиальное течение материала. Формирование радиальных участков оболочки с “вихревой” субструктурой (рис. 2б), возможно, связано с несимметричностью высокоскоростной деформации в тангенциальном направлении.
На рис. 3а, 3б показан внешний вид поперечных сечений оболочек 1/2 и 2/2, нагруженных с корпусом, сценарии схождения которых повторяют те же закономерности, что наблюдались при схождении оболочек, нагруженных без корпуса. Неровные края центральной полости в оболочке 2/2 свидетельствуют в пользу того, что полость образовалась вследствие разлета схлопнувшейся оболочки под действием отраженных от центра волн напряжений, а не на стадии ее схождения.
Рис. 3.
Поперечные сечения оболочек из сплава В95 после ударно-волнового нагружения с наружным корпусом: (а) оболочка № 1/2, (б) оболочка № 2/2 (СЭМ).
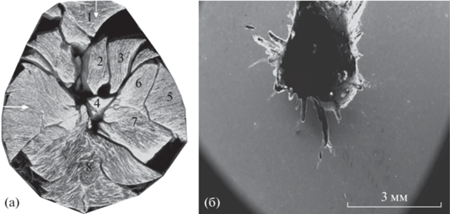
Сравнивая рис. 1 и 3, можно заключить, что наличие наружного корпуса мало сказывается на реологии схождения оболочек. Более важным фактором, влияющим на характер схождения, является фазовый состав сплава, задаваемый режимом термической обработки. Видимой причиной недостаточного сопротивления хрупкому разрушению отожженной оболочки является ее гетерофазная структура с наличием большого количества интерметаллидов, которые присутствовали в образце 1 до нагружения оболочки (рис. 4а), и наблюдаются в структуре оболочки сохраненной после схлопывания (рис. 4б).
По данным EDS-спектров и РСА эти алюминиды имеют разную природу. Более мелкие (1–3 мкм) принадлежат к стабильным T (Mg4Zn3Al3) и η (MgZn2) фазам. Более крупные (десятки мкм) относятся к фазам кристаллизационного происхождения и представляют собой нерастворимые железистые и марганцовистые фазы, входящие в состав неравновесных эвтектик сложного состава типа Al(MnFeCr).
Электронно-микроскопические исследования показали, что деформированная микроструктура обеих оболочек практически одинакова. На рис. 5а видно, что она состоит из тонких волокон с мелкими субзернами шириной 150–200 нм. Наличие субзеренной структуры с большим количеством дислокаций и малоугловых границ отчетливо проявляется на светлопольном и темнопольном в рефлексах Al-изображениях (рис. 5б, 5в). По данным РСА после нагружения плотность дислокаций возрастает относительно плотности дислокаций в соответствующих исходных образцах (ρ1 = = 0.5 × 1010 см–2; ρ2 = 0.8 × 1010 см–2) и составляет в оболочке 1 ρ = 0.9 × 1011 см–2, а в оболочке 2 ρ = = 0.4 × 1011 см–2, т.е. в закаленной оболочке прирост плотности дислокаций ~в два раза меньше (точность измерения плотности дислокаций ~0.1 × 1011 см–2).
Рис. 5.
Тонкая структура матрицы и интерметаллиды в оболочке 2/1: а, б – светлое поле; в – темнопольное изображение в рефлексах Al; г, д – темнопольные изображение в рефлексах типа (100) стабильной фазы ɳ и метастабильной фазы ɳ'; ж – электроннограмма (рефлекс стабильной фазы ɳ отмечен стрелкой).
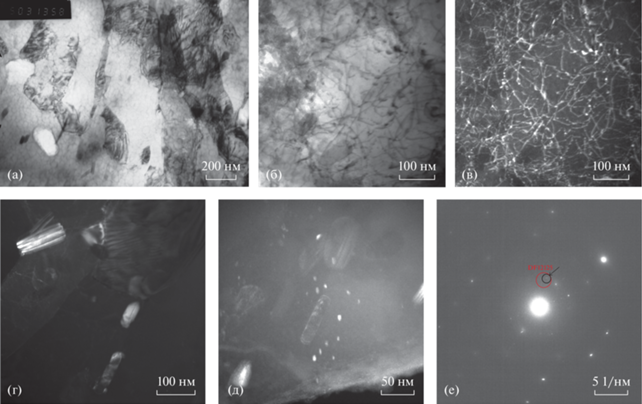
В деформированной структуре обеих оболочек на темнопольных снимках обнаруживается стабильная пластинчатая ɳ-фаза (MgZn2) размером 50–100 нм (рис. 5г), имеющая межплоскостные расстояния, сравнимые с табличными данными d100 = 0.456 нм и d103 = 0.243 нм, и метастабильная тонкопластинчатая η'-фаза с межплоскостными расстояниями d100 = 0.431 нм, размером ~10 нм (рис. 5д). Учитывая, что в сплаве В95 активно протекают процессы естественного и искусственного старения, наличие упрочняющих фаз, обнаруженных в сохраненной закаленной оболочке, может быть следствием распада пересыщенного твердого раствора как во время нагружения при тепловом и деформационном воздействиях, так и при последующем вылеживании оболочки до проведения структурных исследований. О протекании процессов распада Al-твердого раствора в схлопнувшейся закаленной оболочке качественно можно судить по изменению параметра решетки матрицы от 0.40558 до 0.40533 (±0.00005) нм, определенного методом РСА.
Качественную оценку механических свойств и упрочнения материала оболочек в зависимости от режима их нагружения и разного фазового состава можно сделать на основании измерений твердости. Графики изменения усредненных значений HV, измеренных по двум взаимно – перпендикулярным направлениям, показаны на рис. 6а, 6б. По оси абсцисс отложено расстояние от наружного края оболочек. Из представленных на рис. 6а, 6б данных следует, что значения твердости по сечению обеих оболочек с ростом длительности импульса их нагрузки изменяется незначительно. Более “ровный” характер изменения HV по сечению оболочки 2 подтверждает сделанный из анализа структуры вывод о ее равномерном схождении в радиальном направлении. Из рис. 6а следует, что все значения HV оболочек 1/1 и 1/2 укладываются в узкий интервал 1025–1100 МПа, что на 400–450 МПа выше значения HV образца 1. Рост твердости оболочки 1 свидетельствует о деформационном упрочнении, обусловленном повышением плотности дислокаций и наличием интерметаллидов, создающих барьеры для движения дислокаций. Такая же тенденция изменения HV отмечалась ранее на сохраненных полых оболочках из сплава АМг6 после аналогичного ударно-волнового нагружения [13].
Рис. 6.
Графики изменения микротвердости по сечению оболочки: а – оболочка 1; б – оболочка 2 ( средние значения HV до нагружения).
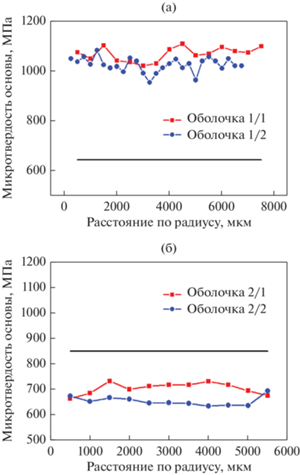
Все измеренные значения HV по радиусу оболочек 2/1 и 2/2 ниже значений микротвердости закаленного образца 2 и близки твердости сплава в отожженном состоянии HV = 640 МПа (рис. 6б). Наиболее вероятной причиной снижения твердости закаленной оболочки, сохраненной после высокоскоростного сжатия, является динамический возврат, наступающий после стадии деформационного упрочнения и приводящий к уменьшению плотности дислокаций в результате их переползания и поперечного скольжения. Данное объяснение можно считать корректным, т.к. в условиях горячей деформации Al-сплавов динамический возврат развивается очень быстро вследствие высокой энергии дефекта упаковки алюминия.
Таким образом, анализируя эти данные и учитывая высокую теплопроводность алюминиевого сплава, можно констатировать, что под действием высокоскоростной деформации и разогрева оболочек при инерционном схождении наблюдается конкуренция процессов упрочнения и разупрочнения материала, которые формируют разные конечные структуры и твердость оболочек.
ВЫВОДЫ
1. Длительность импульса ударной волны, которая регулируется конструктивными особенностями экспериментальной установки, а именно наличием металлического корпуса толщиной 50 мм, не оказывает влияния на сценарий схождения оболочек из сплава В95.
2. Характер схлопывания сохраненных цилиндрических оболочек определяется фазовым составом и твердостью сплава, задаваемых преддеформационной термической обработкой.
3. При одних и тех же режимах нагружения в оболочке из отожженного сплава (состояние поставки) формируются множественные отколы, и она распадается на отдельные фрагменты, а полая оболочка из закаленного сплава схлопывается полностью до сплошного цилиндра.
Авторы выражают благодарность В.В. Астафьеву и Т.И. Яблонских за помощь в проведении металлографических исследований.
Работа выполнена в рамках государственного задания Минобрнауки России (тема “Структура”, № АААА-А18-118020190116-6). Электронно-микроскопические исследования проведены в ЦКП “Испытательный центр нанотехнологий и перспективных материалов” ИФМ УрО РАН.
Список литературы
Матюшкин Н.И., Тришин Ю.А. О некоторых эффектах, возникающих при взрывном обжатии вязкой цилиндрической оболочки // Прикладная механика и технич. физика. 1978. № 3. С. 99–112.
Глазков В.С., Игнатова О.Н., Малышев А.Н. Надежин С.С., Подурец А.М., Раевский В.А., Тюпанова О.А. Метод исследования особенностей высокоскоростного деформирования металлов на микро- и мезомасштабных уровнях // Физич. мезомеханика. 2010. Т. 13. Вып. 3. С. 61–68.
Козлов Е.А., Коваленко Г.В., Литвинов Б.В., Уваров А.И., Теплов В.А. Особенности деформации и разрушения аустенитной стали 60ХЗГ8Н8Ф в сферических волнах напряжений // ДАН. 1998. Т. 358. № 2. С. 189–192.
Хомская И.В., Зельдович В.И., Литвинов Б.В., Пурыгин Н.П. Эффекты локализации деформации в сплавах на основе меди, тинана и железа при нагружении сходящимися ударными волнами // ФММ. 2004. Т. 98. № 4. С. 88–95.
Тришин Ю.А. Влияние процесса диссипации энергии на характер кумулятивного течения // Прикладная механика и технич. физика. 2000. Т. 41. № 4. С. 3–11.
Канель Г.И., Разоренов С.В., Уткин А.В., Фортов В.Е. Ударно-волновые явления в конденсированных средах. М.: Янус-К, 1996. 407 с.
Razorenov S.V. Influence of structural factors on the strength properties of aluminum alloys under shock wave loading // Matter and Radiation at Extremes. 2018. V. 3. № 4. P. 145–158.
Бондарь М.П., Мержиевский Л.А. Эволюция микроструктуры металла и условия локализации деформаций при высокоскоростном нагружении // Физика горения и взрыва. 2006. Т. 42. № 3. С. 121–131.
Беликова А.Ф., Буравова С.Н., Гордополов Ю.А. Локализация деформации и связь ее с деформированным состоянием материала // Журн. технич. физики. 2013. Т. 83. Вып. 2. С. 153–155.
Зельдович В.И., Фролова Н.Ю., Хейфец А.Э., Долгих С.М., Гаан К.В., Шорохов Е.В. Деформационно-температурные процессы, происходящие при схлопывании толстой цилиндрической оболочки из стали 20 // ФММ. 2015. Т. 116. № 3. С. 300–308.
Зельдович В.И., Фролова Н.Ю., Хейфец А.Э., Хомская И.В., Дегтярев А.А., Шорохов Е.В., Смирнов Е.Б., Долгих С.М., Коваль А.В. Деформационные явления при схождении металлических цилиндрических оболочек. Потеря устойчивости // Физика горения и взрыва. 2019. № 4. С. 92–102.
Zel’dovich V.I., Kheifets A.E., Frolova N.Yu., Deg-tyarev A.A., Smirnov E.B., Shorokhov E.V. Metallographic Study of the Convergence of Cylindrical Copper Shells at Different Intensities of Explosive Loading // Phys. Met. Metal. 2021. V. 122. P. 566–571.
Бродова И.Г., Смирнов Е.Б., Ширинкина И.Г., Астафьев В.В., Яблонских Т.И., Коваль А.В., Дегтярев А.А., Шорохов Е.В. Изменение структуры и свойств цилиндрических оболочек из сплава АМг6 при нагружении скользящими детонационными волнами // Деформация и разрушение материалов. 2018. № 1. С. 17–22.
Коваль А.В., Ширинкина И.Г., Петрова А.Н., Бродова И.Г., Смирнов Е.Б., Шорохов Е.В. Cтруктурные превращения в алюминиевых цилиндрических оболочках при динамическом нагружении // Физика горения и взрыва. 2019. V. 55. P. 82–91.
Мондельфо Л.Ф. Алюминий. Свойства и физическое металловедение. Справочник / Под редакцией Дж.Е. Хетча. М.: Металлургия, 1989. 422 с.
Алюминиевые сплавы. Справочник. Структура и свойства полуфабрикатов из алюминиевых сплавов / Ответственные редакторы В.И. Елагин, В.А. Ливанов. М.: Металлургия, 1984. 408 с.
Мальцев М.В., Барсукова Т.А., Борин Ф.А. Металлография цветных металлов и сплавов. Москва. Государственное научно-техническое издательство литературы по черной и цветной металлургии, 1960. 372 с.
Алюминий. Металловедение, обработка и применение алюминиевых сплавов. / Перевод с английского под редакцией А.Т. Туманова, Ф.И. Квасова, И.Н. Фридляндера. М.: Металлургия, 1972. 663 с.
Дополнительные материалы отсутствуют.
Инструменты
Физика металлов и металловедение