Физика металлов и металловедение, 2022, T. 123, № 8, стр. 859-863
Покрытия системы гафний–кадмий: получение и фазовый состав
Ю. Ж. Тулеушев a, *, В. Н. Володин a, Б. К. Каракозов a, Е. А. Жаканбаев a, А. К. Мамырбаев a, А. К. Калиева a
a Институт ядерной физики Министерства энергетики РК
050032 Алматы, Казахстан
* E-mail: yuriy.tuleushev@mail.ru
Поступила в редакцию 20.12.2021
После доработки 19.04.2022
Принята к публикации 05.05.2022
- EDN: RMDAHQ
- DOI: 10.31857/S0015323022080150
Аннотация
Ионно-плазменным напылением ультрадисперсных частиц гафния и кадмия получены покрытия на подложках из поликристаллического оксида алюминия, монокристаллического кремния, стекла и нержавеющей стали при температуре не выше 100°С. Исследованием структуры полученных покрытий установлено существование твердых растворов в интервале концентраций 5.8–64.1 ат. % Cd. В области концентрации 0–50 ат. % Cd покрытие представлено фазой твердого раствора кадмия в α-Hf, а при концентрации Cd более 64 ат. % кадмий начинает выделяться в отдельную фазу. Отмечено влияние материала подложки на границу существования твердого раствора кадмия в гафнии, и высказано предположение о влиянии эпитаксии на границу существования твердых растворов кадмия в гафнии.
ВВЕДЕНИЕ
Современное развитие техники требует от материаловедов создания новых материалов с новыми свойствами [1]. При этом в одном и том же материале совмещаются часто трудно сочетаемые высокие механические, физические и химические характеристики. Традиционные материаловедческие принципы формирования структуры и свойств, основанные на термических и деформационных воздействиях на твердое тело, не всегда применимы для создания материалов с необходимыми свойствами. Одним из способов придания новых свойств материалам являются экстремальные воздействия на твердое тело, при которых формируются ранее неизвестные структурные состояния. Одним из вариантов таких воздействий является механосплавление [2–4], позволяющее существенно расширить зону взаимной растворимости металлов. Другим способом, позволяющим получать новые фазы, является технология ионно-плазменного осаждения чередующихся слоев металлов нанометровой толщины [5–8]. Одним из вариантов выбора несочетаемых металлов являются гафний и кадмий как сочетание тугоплавкого металла (Hf) с одним из самых легколетучих металлов (Cd). С помощью плавления такую комбинацию металлов получить невозможно, для механосплавления необходимо оба компонента иметь в виде порошков, а порошковый кадмий не существует.
К настоящему времени диаграмма состояния системы гафний–кадмий не построена [9]. Согласно этому изданию, диаграмма состояния Cd–Hf в литературе отсутствует. В системе образуются два соединения: CdHf и CdHf2 [10, 11]. Соединение CdHf имеет тетрагональную структуру типа TiCu с параметрами решетки а = 0.311 нм, с = = 0.867 нм, соединение CdHf2 – тетрагональную объемно-центрированную структуру типа Zr2Cu с параметрами решетки а = 0.327 нм, с = 1.188 нм. Однако в современных базах рентгеновских данных ICPDS, данные об этих двух соединениях отсутствуют.
Авторами настоящей работы исследовались комбинации кадмия с тугоплавкими металлами Ta, W, Nb и Mo. Было показано, что в системах Cd–Ta и Cd–W новые интерметаллиды не образуются [6, 12], а в системах Cd–Nb и Cd–Mo при формировании покрытий ультратонкими слоями с использованием размерного эффекта возникают новые фазы NbCd2 и МоCd2 [13, 14], которые являются термически неустойчивыми и распадаются при температуре выше 200°С. Возникает вопрос – как поведет себя гафний при соединении с кадмием, учитывая то, что для Hf основной тип решетки не ОЦК, как для Ta, W, Nb и Mo, а гексагональная, как и у кадмия.
В связи с этим целью настоящей работы явилось определение возможности формирования сплавов системы гафний–кадмий при послойном ионно-плазменном нанесении субслоев и концентрационных пределов существования твердых растворов, а также установление фазового состава напыленных покрытий и получение предварительных данных для идентификации интерметаллического соединения.
МАТЕРИАЛ И МЕТОДИКА ЭКСПЕРИМЕНТА
Объекты для исследования – пленочные покрытия системы гафний–кадмий, изготовленные соосаждением ультрадисперсных частиц металлов, полученных ионно-плазменным распылением, на подложки из поликристаллического оксида алюминия (поликора), монокристаллического кремния, стекла и нержавеющей стали при температуре не выше 100°С. Нержавеющая сталь имела сопоставимую с вышеперечисленными материалами степень чистоты поверхности, поскольку нержавеющую фольгу подвергали электрохимической полировке до 13–14 класса.
В экспериментах использованы гафний йодидный ГФИ-1 чистотой 99.95 мас. % основного элемента и кадмий (99.99 мас. %) в виде мишеней для распыления диаметром 40 мм и толщиной 4 мм. При магнетронном распылении в качестве плазмообразующего газа использован особо чистый аргон, прошедший очистку на геттере – распыленном титане.
Методика формирования покрытий заключалась в ионно-плазменном распылении гафния и кадмия и их совместном осаждении в виде субслоев толщиной около 1 нм, до суммарной толщины пленки 1.5 мкм на перемещающиеся относительно потоков плазмы подложки. Скорость перемещения подложек – 5 × 10–2 м с–1. Напыление осуществляли одновременно с двух расположенных на стенках камеры друг против друга магнетронов, разделенных между собой устройством для перемещения подложек.
Составом покрытия управляли изменением соотношения электрических мощностей, подаваемых на распыляющие гафний и кадмий магнетроны. Мощность, подаваемая на мишени из гафния изменяли в пределах 21 од 100 Вт, а на мишени из кадмия мощность составляла от 0.15 до 4.6 Вт. Соотношение осажденных металлов контролировали весовым методом по количеству распыленных металлов во время формирования покрытия. Толщину пленки определяли методом резерфордовского обратного рассеяния протонов на тандемном ускорителе УКП-2–1 и расчетным путем на основании количества осажденных металлов и взятых из таблиц [15] значений плотности.
Рентгеноструктурные исследования выполнены на дифрактометре D8 Advance фирмы Bruker с медным излучением λKα = 0.154051 нм с графитовым монохроматором. Значение параметров решетки вычислено как среднее при использовании всех дифракционных линий от идентифицируемой фазы [16].
Нагрев образца контролировали на неподвижной карусели с помощью термопары, и он не превышал 110°С. Учитывая то, что при вращении карусели образец только раз в 6 с попадает на 1 с под нагрев магнетрона, считали, что нагрев образца не превышает 100°С.
РЕЗУЛЬТАТЫ И ИХ ОБСУЖДЕНИЕ
С целью определения концентрационных границ существования твердых растворов в системе Hf–Cd ионно-плазменным напылением сформированы образцы покрытий с концентрацией кадмия от 5.8 до 73.6 ат. %. Толщина единичных слоев гафния (dHf) и кадмия (dCd) при напылении покрытий, состав покрытия и образующиеся при напылении фазы представлены в табл. 1.
Таблица 1.
Состав покрытий на поликоре, толщина субслоев гафния и кадмия и обнаруженные фазы
Состав покрытия, ат. %: | dHf,нм | dCd, нм | Общая толщина, мкм | Фазовый состав | |
---|---|---|---|---|---|
Hf | Cd | ||||
94.2 | 5.8 | 1.84 | 0.09 | 1.15 | α-Hf; a = 0.3174 нм, c = 0.5072 нм |
89.4 | 10.6 | 1.79 | 0.17 | 1.18 | α-Hf; a = 0.3187 нм c = 0.5074 нм |
80.9 | 19.1 | 1.76 | 0.34 | 1.40 | α-Hf; a = 0.3174 нм, c = 0.5072 нм |
67.1 | 32.9 | 1.6 | 0.64 | 1.34 | α-Hf; a = 0.3177 нм, c = 0.5097 нм |
62.4 | 37.6 | 1.25 | 0.62 | 1.12 | α-Hf; a = 0.3167 нм, c = 0.5108 нм |
50.3 | 49.7 | 0.70 | 0.86 | 0.69 | α-Hf; a = 0.3143 нм, c = 0.5121 нм |
35.9 | 64.1 | 0.39 | 0.57 | 0.76 | α-Hf c = 0.5134 нм + Cd |
26.4 | 73.6 | 0.38 | 0.87 | 1.00 | Aморфный Hf + Cd |
На рис. 1 представлены дифрактограммы покрытий системы Hf–Cd, подтверждающие представленные в табл. 1 сведения о фазовом составе полученных покрытий.
Рис. 1.
Дифрактограммы покрытий системы Hf–Cd с различным содержанием Cd на подложках из стекла: 1 – 73.6 ат. % Cd, 2 – 64.1 ат. % Cd, 3 – 37.6 ат. % Cd, 4 – 19.1 ат. % Cd, 5 – 5.8 ат. % Cd (* – Cd, ⚫ твердый раствор Cd в Hf).
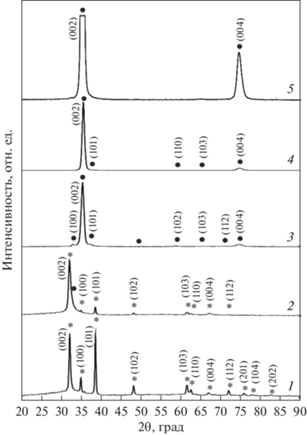
Из рис. 1 видно, что при высоком содержании кадмия (73.6 ат. % Cd) покрытие представлено фазой кадмия, а присутствующий в нем гафний аморфизован, о чем свидетельствует гало в районе пика (002) кадмия. При понижении содержания кадмия в покрытии до 64.1 ат. % появляются признаки появления твердого раствора Cd в Hf – пик (002) твердого раствора. При содержании кадмия в покрытии 37.6 ат. % наблюдается четко выраженная фаза α-Hf с параметрами a = 0.3167 нм, c = 0.5108 нм, имеющая признаки текстурированности в направлении [002].
При концентрации кадмия в покрытии менее 19.1 ат. % текстурированность в направлении [002] становится доминирующей, но есть очень слабый рефлекс (103) на рентгенограммах от покрытий этого состава, а также при концентрациях кадмия 10.6 и 5.8 ат. %. Существование твердого раствора на основе гафния до концентрации кадмия 64.1 ат. % подтверждено дифрактометрически (рис. 2) – присутствует четкий пик (002) α‑гафния на дифрактограмме от покрытия на подложке из нержавеющей стали. На подложках из поликора, монокристаллического кремния и стекла твердые растворы кадмия в гафнии существуют только до концентрации кадмия 49.7 ат. %, а при указанной концентрации 64.1 ат. % Cd на подложках из поликора, стекла и кремния твердый раствор Cd в гафнии аморфизируется. Мы предполагаем, что причиной влияния материала подложки на порог аморфизации твердого раствора кадмия в гафнии является эпитаксия. Дело в том, что межплоскостное расстояние у плоскостей (004) гафния d004 = 0.1264 нм очень близко к межплоскостному расстоянию d220 = 0.1269 нм нержавеющей стали 12Х18Н10Т.
Рис. 2.
Дифрактограмма покрытия с содержанием кадмия 64,1 ат. % на подложке из легированной стали Х18Н10Т (* – Cd, ⚫ твердый раствор Cd в Hf, ▼ – сталь).
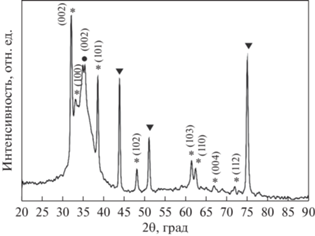
На рис. 3 представлены графики зависимости параметров a и c гексагональной решетки твердого раствора кадмия в α-Hf от концентрации кадмия. Из величины параметра a можно сделать вывод о том, что в данном случае речь идет о растворе кадмия в гафнии типа замещения, поскольку параметр решетки a твердых растворов заметно меньше такового для гафния (aHf = 0.3196 нм, cHf = 0.5058 нм), так как при внедрении кадмия с меньшим атомным номером в решетку гафния должно быть уменьшение параметра решетки. Зависимость параметра c решетки гафния от концентрации кадмия описывается формулой c [нм] = 0.0001СCd + 0.505, а зависимость параметра а решетки гафния от концентрации кадмия описывается формулой а [нм] = –4 × × 10–0.6$C_{{{\text{Cd}}}}^{2}$ + 0.0001СCd + 0.317, где СCd – концентрация кадмия в ат. %. Изменение параметров гексагональной решетки твердого раствора кадмия в гафнии в концентрационном интервале от 5.8 до 64.1 ат. % Cd свидетельствует о их малой зависимости от концентрации кадмия. Увеличение параметра с при одновременном уменьшении параметра а говорит о преимущественном размещении атомов кадмия в базовой плоскости гексагональной решетки гафния.
ЗАКЛЮЧЕНИЕ
При соосаждении ультрадисперсных частиц гафния и кадмия на перемещающиеся относительно потоков металлсодержащей плазмы подложки методом магнетронного распыления впервые получены твердые растворы – сплавы металлов, несмешивающихся при традиционных методах получения, до концентрации 50.3 ат. % Cd. При осаждении покрытий на подложки из нержавеющей стали 12Х18Н10Т порог существования твердых растворов кадмия в гафнии сдвигается до концентрации кадмия 64.1 ат. % предположительно за счет влияния эпитаксии.
Подобный способ изготовления покрытий и синтеза в них соединений может быть распространен на другие металлические системы, составляющие которых не смешиваются традиционным способом.
Работа выполнена при финансовой поддержке Министерства энергетики Республики Казахстан (BR09158958).
Список литературы
Счастливцев В.М., Зельдович В.И. Влияние экстремальных воздействий на структуру и свойства сплавов // ФММ. 2018. Т. 119. № 9. С. 909.
Волкова Е.Г., Волков А.Ю., Антонов Б.Д. Структура интерметаллида Al2Au, полученного методом механосинтеза // ФММ. 2018. Т. 119. № 7. С. 693.
Григорьева Т.Ф., Петрова С.А., Ковалева С.А., Дудина Д.В., Батраев И.С., Киселева Т.Ю., Жолудев С.И., Восмериков С.В., Девяткина Е.Т., Удалова Т.А., Поляков С.Н., Ляхов Н.З. Механохимический синтез порошков сплавов системы Сu–Аl и их консолидация методом электроискрового спекания // ФММ. 2021. Т. 122. № 7. С. 729.
Григорьева Т.Ф., Петрова С.А., Ковалева С.А., Киселева Т.Ю., Жолудев С.И., Восмериков С.В., Удалова Т.А., Девяткина Е.Т., Поляков С.Н., Ляхов Н.З. Механохимическое формирование твердого раствора алюминия в меди // ФММ. 2021. Т. 122. № 4. С. 396.
Володин В.Н., Тулеушев Ю.Ж., Цай К.В., Жаканбаев Е.А. Новая фаза Мo3Рb со структурой А15 в твердых растворах пленочной системы молибден–свинец // ФММ. 2014. Т. 115. № 5. С. 532–538.
Тулеушев Ю.Ж., Володин В.Н., Жаканбаев Е.А. Пленочные покрытия системы тантал-кадмий: получение, фазовый состав и структура // ФММ. 2015. Т. 116. № 1. С. 59–66.
Володин В.Н., Тулеушев Ю.Ж., Жаканбаев Е.А. Структура и фазовый состав напыленных пленок системы ниобий–медь // Поверхность. 2015. № 2. С. 75–80.
Володин В.Н., Тулеушев Ю.Ж., Жаканбаев Е.А., Цай К.В., Рофман О.В. Новая фаза NbCd2 в пленочных покрытиях системы ниобий–кадмий // ФММ. 2018. Т. 119. № 2. С. 180–184.
Диаграммы состояния двойных металлических систем/ под ред. Н.П. Лякишева, М.: Машиностроение, 2001. Т. 3. Кн. 1. С. 429.
Schubert K., Meissner H.G., Rossteutscher W. // Naturwissenschaften. 1964. Bd. 51. № 21. S. 507.
Schubert K., Meissner H.G., Raman A., Rossteutscher W // Naturwissenschaften. 1964. Bd. 51. S. 287.
Тулеушев Ю.Ж., Володин В.Н, Жаканбаев Е.А., Сукуров Б.М., Козловский А.Л. Получение пористого вольфрама из пленочных покрытий системы вольфрам-кадмий // Письма в ЖТФ. 2018. Т. 44. Вып. 11. С. 63–70.
Володин В.Н., Тулеушев Ю.Ж., Жаканбаев Е.А., Цай К.В., Рофман О.В. Новая фаза NbCd2 в пленочных покрытиях системы ниобий–кадмий // ФММ. 2018. Т. 119. № 2. С. 180–184.
Tuleushev Yu.Zh., Volodin V.N., Zhakanbaev Y.A. New MoCd2-phase in film coatings of molybdenum-cadmium system // Eurasian J. Phys. Funct. Mater. 2018. V. 2. № 4. P. 341–353.
Физические величины: Справочник / А.П. Бабичев, Н.А. Бабушкина, А.М. Братковский и др.; Под ред. И.С. Григорьева, Е.З. Мейлихова. М.: Энергоатомиздат, 1991. 1232 с.
Tabular processor for X-ray diffractometry RTP / rtp32.cab, RTP 4.2 для Win32, английская версия от 1.02.2014.
Дополнительные материалы отсутствуют.
Инструменты
Физика металлов и металловедение