Физика металлов и металловедение, 2022, T. 123, № 9, стр. 986-995
Нейтрон-дифракционное исследование влияния закреплений и термообработки на остаточные напряжения в стальном сварном шве
И. Д. Карпов a, *, В. Т. Эм a, И. Г. Карпов b, А. В. Ильин b
a НИЦ “Курчатовский институт”
123182 Москва, пл. Академика Курчатова, 1, Россия
b НИЦ “Курчатовский институт” – ЦНИИКМ “Прометей”
191015 Санкт-Петербург, Шпалерная, 49, Россия
* E-mail: Karpov_ID@nrcki.ru
Поступила в редакцию 19.04.2022
После доработки 28.06.2022
Принята к публикации 29.06.2022
- EDN: MPNZMB
- DOI: 10.31857/S0015323022090054
Аннотация
Методом дифракции нейтронов исследованы остаточные напряжения в Х-образном сварном шве стальных пластин толщиной 32 мм. Изучено влияние предварительного закрепления свариваемых деталей и послесварочной термообработки на распределение остаточных напряжений. Распределение напряжений близко к симметричному относительно центральной линии сечения шва и явно ассиметрично относительно середины толщины шва. Максимальные растягивающие (продольные) напряжения находятся в той половине шва по толщине, которая сваривалась первой. Пиковое значение продольных напряжений в пластине с закреплениями 800 МПа (98% предела текучести металла шва) значительно выше, чем в пластине без закреплений 530 МПа. Область максимальных сжимающих (поперечных) напряжений (–400 МПа) в пластине с закреплениями находится в первой половине толщины шва, а в пластине без закреплений во второй половине. После термообработки растягивающие и сжимающие напряжения, в целом, остались, соответственно, растягивающими и сжимающими. Максимальные растягивающие (продольные) напряжения уменьшились до 270 МПа в пластине с закреплениями и 220 МПа в пластине без закреплений. Максимальные сжимающие (поперечные) напряжения в обеих пластинах уменьшились до –170 МПа.
ВВЕДЕНИЕ
При сварке расплавленный металл шва после затвердевания охлаждается с гораздо более высокой температуры, чем основной металл. Большая разница в степени сжатия металла шва и основного металла при охлаждении приводит к появлению больших растягивающих напряжений в сварном шве [1, 2]. В случае использования в качестве металла шва ферритной стали, еще одним фактором, влияющим на распределение остаточных напряжений, является объемное расширение металла шва, связанное с γ – α-фазовым переходом, которое приводит к образованию сжимающих напряжений в зоне, где произошел переход.
Остаточные напряжения могут значительно ухудшить усталостную прочность и коррозионную стойкость сварного соединения [3–8]. Поэтому количественная информация об остаточных напряжениях, в особенности, величина и местонахождение максимальных растягивающих напряжений, важна для надежной оценки прочности и срока эксплуатации сварного соединения. Она также необходима для верификации различных расчетных моделей. В случае швов большой толщины необходима информация о напряжениях внутри сварного шва, поскольку большое количество проходов и сильные ограничивающие условия приводят к сложной картине распределения напряжений по толщине соединения.
С целью снижения деформаций конструкций свариваемые детали часто закрепляются различными способами, кроме того многие сварные швы располагаются на уже скрепленных деталях. Наиболее частым видом закрепления являются ребра жесткости. Для уменьшения остаточных напряжений обычно используется термообработка. Поэтому нужна надежная количественная информация о влиянии закреплений и термообработки на остаточные напряжения.
Благодаря большой проникающей способности нейтронов в большинстве металлов, метод дифракции нейтронов (ДН) в настоящее время является единственным методом, который позволяет неразрушающим способом измерить все три компоненты тензора напряжения внутри массивных деталей (в стали толщиной до 50 мм) [2, 9]. Рентгеновским методом можно измерить напряжения только на поверхности или приповерхностных слоях (в стали ~20 мкм). Поэтому в настоящее время нейтронный метод широко используется для измерения остаточных напряжений в массивных сварных соединениях.
В последние годы нейтронным методом интенсивно исследовали напряжения в сварных соединениях пластин большой толщины (≥20 мм) с V-образной разделкой кромок [9–15]. Эти исследования показали, что в V-образных сварных швах максимальные растягивающие продольные напряжения образуются в верхней половине шва вблизи поверхности или на глубине, которая может достигать 40% толщины пластины. В зависимости от технологических параметров сварки (ширина шва, тепловложение, последовательность нанесения валиков и др.) образуется один максимум на центральной линии шва вблизи верхней поверхности или два максимума, расположенные симметрично относительно центральной линии шва. В последнем случае максимумы могут находиться в зоне металла шва или вне этой зоны. Пиковые значения продольных растягивающих напряжений близки к пределу текучести металла шва и, в некоторых случаях, превышают его.
Впервые распределение напряжений в сварных швах с Х-образной разделкой кромок было изучено экспериментально в работе [16] методом удаления и расслоения блоков (УРБ). Перед сваркой пластины были закреплены приваренными ребрами жесткости, которые сохранялись при исследовании. Было показано, что в Х-образном сварном шве ферритной стали толщиной 50 мм продольные напряжения являются растягивающими в металле шва и основном металле с пиковым значением 740 МПа (~150% предела текучести металла шва), расположенном на центральной линии сечения шва (ЦЛ) в середине толщины (корне) шва. Поперечные напряжения были растягивающими в той половине шва по толщине, которая сваривалась первой, и сжимающими во второй. В распределении по толщине как продольных, так и поперечных напряжений при удалении от ЦЛ сохранялся локальный максимум в середине толщины. После термообработки (600°C, 2 ч) так же как, и до термообработки, в корне шва наблюдался максимум продольных напряжений, который уменьшился с 740 до 140 МПа.
В работе [17] было исследовано распределение напряжений по толщине (50 мм) вдоль ЦЛ стального сварного шва с Х-образной разделкой кромок методом конечных элементов (КЭ). В отличие от работы [16] исследовали пластину со сварным швом без закреплений. Распределения продольной и поперечной компонент были весьма схожи. Максимальные напряжения находились примерно на глубине 10 мм от обеих поверхностей. В отличие от результатов, полученных методом УРБ [16], в корне шва находился минимум, а не максимум продольных и поперечных напряжений. Продольные напряжения были растягивающими по всей толщине, однако поперечные изменялись от растягивающих вблизи поверхностей к сжимающим вблизи середины толщины.
Можно было предположить, что расхождение результатов, полученных в работах [16] и [17], связано с тем, что в первой исследовали пластины с закреплениями, а во второй без них. Целью настоящей работы было исследовать остаточные напряжения в Х-образном стальном сварном шве неразрушающим методом ДН, изучить влияние закреплений и термообработки на распределение остаточных напряжений.
ОБРАЗЦЫ И МЕТОДИКА ИЗМЕРЕНИЙ
Приготовление образцов. В качестве основного металла использовали листовой прокат толщиной 32 мм из ферритной низкоуглеродистой легированной конструкционной стали российского производства, изготовленной методом контролируемой термодеформационной прокатки. По химическому составу (табл. 1) и механическим свойствам используемая сталь является аналогом таким сталям как Amstrong® Ultra 960, Optim 960 QC, XABO 960 и соответствует категории S960QL по EN ISO 10025-6. Сварку производили ручным дуговым способом штучными покрытыми плавящимися электродами (MMA/111). В качестве сварочного материала использовали ферритные электроды российского производства номинальным диаметром 4.0 мм с покрытием основного типа. Химический состав электродов приведен в табл. 1. По механическим свойствам наплавленного металла данные электроды являются аналогами электродов ESAB OK 75.75 и соответствуют по ГОСТ 9467 категории Э85, согласно EN ISO 18275-A категории E 79 A-B.
Таблица 1.
Химический состав стали и электродов (в мас. %)
Материал | C | Si | Mn | Cr | Ni | Al | V | Cu | Mo | S | P |
---|---|---|---|---|---|---|---|---|---|---|---|
Сталь | 0.10 | 0.17 | 0.42 | 0.75 | 2.80 | 0.02 | 0.08 | 1.15 | 0.54 | 0.005 | 0.012 |
Электрод | 0.07 | 0.25 | 0.70 | 0.89 | 2.50 | 0.92 | 0.51 | 0.015 | 0.012 |
Механические свойства материалов, определенные экспериментально по методике аналогичной EN 10002-1:2001 на образцах круглого сечения диаметром 6 мм и рабочей частью длиной равной 5 диаметрам образца, представлены в табл. 2.
Таблица 2.
Механические свойства основного металла и металла шва
Зона сварного соединения | Предел текучести, МПа | Предел прочности, МПа | Удлинение, % |
---|---|---|---|
Основной металл | 1040 | 1140 | 17 |
Металл шва | 820 | 910 | 16 |
Подготовку кромок под сварку выполняли газопламенным способом с последующей механической абразивной зачисткой. Ручную сварку выполняли по направлению проката в стык, по двухсторонней симметричной Х-образной разделке в раскладку валиков. Количество слоев было 7 на одну сторону, а общее количество проходов 20 на одну сторону. С обеих сторон сварки было массивное усиление высотой ~6.5 мм над поверхностью пластины так, что толщина сварного шва в центре была ~45 мм. Эскиз разделки кромок и фотография макрошлифа поперечного сечения шва представлены на рис. 1.
Рис. 1.
Сварное Х-образное соединение, a – схема разделки кромок, б – поперечное сечение шва (ЦЛ – центральная линия сечения шва), в – расположение областей исследования структуры. Размеры даны в миллиметрах.
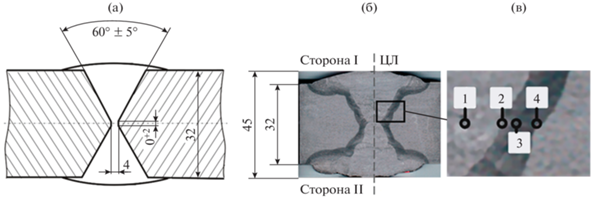
Сварку производили прямым током обратной полярности по режиму: сила тока = 180 А, напряжение на дуге 25 В, скорость сварки 3.5 мм/с. Расчетная погонная энергия 1.4 кДж/мм. Перед сваркой производили предварительный подогрев листов до 100°С. Межпроходную температуру выдерживали в диапазоне 100–200°С. По окончании сварки обеспечивали замедленное охлаждение с помощью термоизоляционных матов.
На рис. 2 представлены микрофотографии, полученные с областей металла шва и зоны термического воздействия (ЗТВ), указанных на рис. 1в. Микроструктура метала шва преимущественно бейнитная со слабо выраженными ферритными областями. Ширина ферритных полос равна 21.5 мкм. Крупнозернистая ЗТВ преимущественно имеет структуру мартенсита. Мелкозернистая ЗТВ определяется как бейнит с размером зерна 40.7 мкм. Мартенсит в этой зоне отсутствует.
Рис. 2.
Микроструктура металла шва и зоны термического влияния (ЗТВ), указанных на рис. 1в. ЛС – линия сплавления.
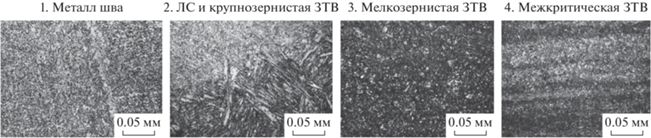
В межкритической ЗТВ по границам бейнитых зерен произошло повышенное карбидообразование (размер зерна бейнита 32.3 мкм). В мелкозернистой и межкритической ЗТВ наблюдается полосчатая структура, что характерно для структуры листа, прошедшего термомеханическую обработку (а именно прокатку). Протяженность (толщина) ЗТВ равна 3.61 мм.
Были подготовлены 4 сварных соединения в виде пластин размерами 280 × 400 со сварным швом, расположенным по стороне 400 (здесь и далее размеры даны в миллиметрах). Два образца перед сваркой были закреплены путем установки приварных ребер жесткости (рис. 3а), обозначим их как ПЗ. Два образцы сваривали в свободном состоянии, обозначим их как ПС. Пластины сваривали с одной стороны (Сторона I) затем переворачивали и сваривали с другой стороны (Сторона II). Пластины ПЗ сначала сваривали со стороны ребер жесткости. По окончании сварки две пластины (ПЗ и ПС) подвергали термообработке при температуре 550°С в течение 3 ч и охлаждали в воде. Обозначим пластины после термообработки, соответственно, ПЗТ и ПСТ. Далее с торца каждого сварного соединения методом гидроабразивной резки были отсечены части длиной 100 (рис. 3а) для изготовления макрошлифа и d0‑образца.
Рис. 3.
(a) Схема пластины со сварным швом с закреплениями (ПЗ); (б) схема точек измерения методом ДН (сверху) и схема d0-образца (снизу). Размеры даны в миллиметрах. ЦЛ – центральная линия сечения шва.
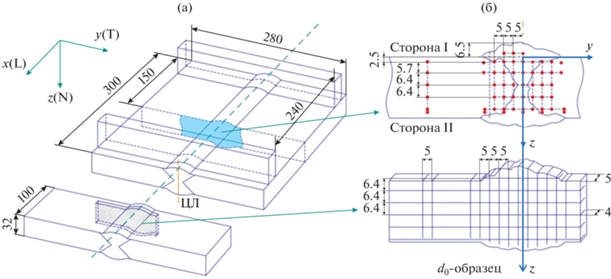
Таким образом, для исследований методом ДН были приготовлены 4 образца в виде пластин размерами 280 × 300 × 32 со сварным швом в середине (рис. 3а): два с закреплениями (ПЗ, ПЗТ) и два без закреплений (ПС, ПСТ).
Измерение напряжений методом дифракции нейтронов. Нейтрон-дифракционный метод измерения напряжений основан на точном измерении межплоскостного расстояния d в кристаллической решетке материала. Согласно закону Вульфа–Брэгга 2d sin θ = nλ (n – целое число) на нейтронном дифрактометре с постоянной длиной волны нейтронов λ межплоскостное расстояние d может быть определено путем точного измерения углового положения дифракционного пика 2θ. Изменение межплоскостного расстояния Δd приводит к сдвигу углового положения дифракционного пика Δ2θ. Решеточная деформация ε определяется по сдвигу дифракционного пика [2]:
Измеряются деформации в трех взаимно-перпендикулярных направлениях (x, y, z) и, пользуясь обобщенным законом Гука, определяются напряжения в этих направлениях [2]:
Исследование остаточных напряжений проводили на стресс-дифрактометре СТРЕСС на реакторе ИР-8 (максимальная мощность 8 МВт) НИЦ “Курчатовский институт” при мощности реактора 6 МВт. Благодаря использованию оригинальной схемы монохроматизации, возможности прибора для измерения напряжений на глубине (50 в стали при пробном объеме 80 мм3 и времени измерении 1 ч) сравнимы с возможностями других современных приборов на более мощных реакторах [18, 19]. Двойной монохроматор PG(002)/Si(220) из пиролитического графита и фокусирующего идеального монокристалла кремния выводит монохроматические нейтроны с фиксированной длиной волны λ = 0.156 нм, которая оптимальна для измерения напряжений на глубине в ферритной стали [20]. Использовали дифракционный пик (112) ОЦК-решетки ферритной стали (2θ ≈ 82°), который наименее чувствителен к микронапряжениям [2]. ПО задавали щелями шириной 3 в кадмиевых экранах, установленных в падающем и отраженном нейтронных пучках. Высота щели в падающем пучке была 20 (ПО = 3 × 3 × 20) при измерении нормальной (z) и поперечной (y) компонент и 5 (ПО = 3 × 3 × 5) при измерении продольной (x) компоненты. В обоих случаях пространственное разрешение вдоль толщины шва было 4. Распределение напряжений по толщине измеряли в середине пластины, в поперечном сечении шва, в точках, указанных на рис. 3б. Заметим, что y = 0 соответствует ЦЛ, а z = 0 соответствует поверхности пластины (Сторона I) на глубине 6.5 от поверхности шва при y = 0.
Свободный от напряжений образец для измерения d0 (d0-образец) был приготовлен с помощью электроэрозионной резки проволокой диаметром 0.25 (рис. 3). Из каждой отрезанной от сварных соединений части длиной 100 была вырезана пластина толщиной 5 и была приготовлена обычная “гребенка” [2] с зубьями (~40(z) × 5(x) × 5(y)) вдоль нормального (z) направления. Затем в этой гребенке для уменьшения напряжений в зубьях длиной ~40 [21] было сделано несколько надрезов (шириной 0.25 и глубиной 4) вдоль поперечного (y) направления перпендикулярно зубьям. Такая двумерная гребенка использовалась как d0-образец.
Для расчетов напряжений использовали значения модуля Юнга E112 = 225 ГПа и коэффициента Пуассона ν112 = 0.28, соответствующие отражающим плоскостям (112) ферритной стали [2].
ЭКСПЕРИМЕНТАЛЬНЫЕ РЕЗУЛЬТАТЫ
Остаточные напряжения в образцах с закреплениями. На рис. 4 представлены распределения продольных (L) и поперечных (Т) напряжений по толщине в пластинах ПЗ и ПЗТ на расстояниях y = 0, ±5, ±10, ±15 от ЦЛ. На рис. 5 представлены двумерные картограммы распределения напряжений в этих пластинах, построенные по всем измеренным точкам.
Рис. 4.
Распределение продольных (L) и поперечных (T) напряжений по толщине в пластине ПЗ (a) и ПЗТ (б) на расстояниях y = 0, ±5, ±10, ±15 от ЦЛ.
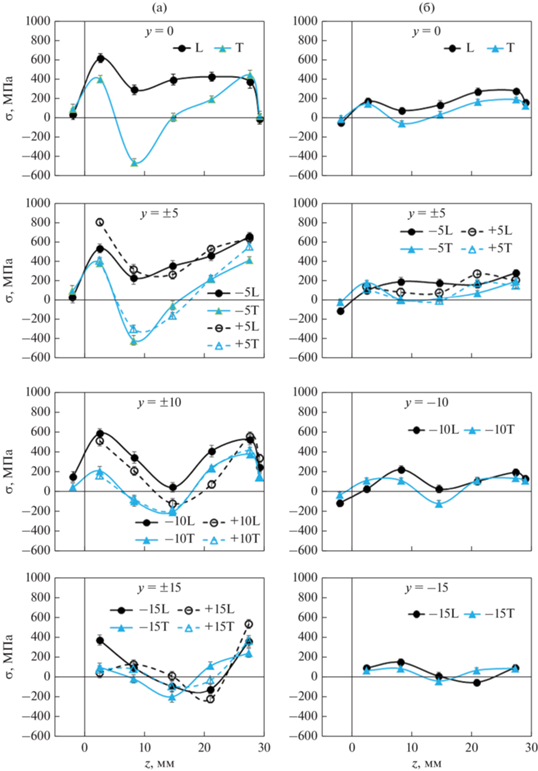
Рис. 5.
Двумерная картограмма распределения продольных (σx) и поперечных (σy) напряжений в пластинах ПЗ (a) и ПЗТ (б).
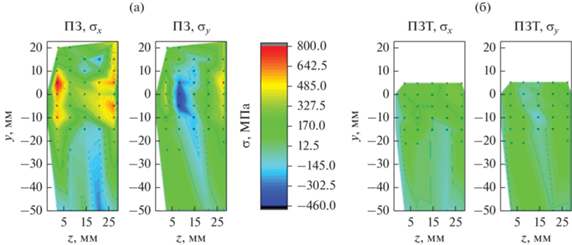
В пластине ПЗ (рис. 4а, 5a) распределение продольных и поперечных напряжений близко к симметричному относительно ЦЛ, хотя различие в величине напряжений в некоторых симметричных точках значительно. Максимумы растягивающих продольных и поперечных напряжений расположены в металле шва на глубине z = 2.5 и z = 27.5 (~10 от поверхностей шва) по обе стороны (y = ±5) от ЦЛ.
Ближе к поверхностям (z = –0.25; z = 29) и середине толщины шва они уменьшаются. Наибольшее значение растягивающих продольных напряжений 800 МПа наблюдалось в первой половине толщины шва на Стороне I (z = 2.5, y = 5). На глубине 7.5 вдоль ЦЛ наблюдается локальный минимум продольных растягивающих напряжений ~ 270 МПа. С удалением от ЦЛ локальный минимум смещается из первой половины толщины во вторую: от z = 7.5 при y = 0 до z = 20 при y = = ±15. При этом значение минимума уменьшается от 270 МПа при y = 0 до нуля при y = ±10, и далее напряжения переходят в сжимающие до –200 МПа при y = ±15. Растягивающие поперечные напряжения с максимумами 400 МПа заметно ниже, чем продольные. Сжимающие поперечные напряжения значительно выше, чем продольные, с максимумом –400 МПа в широкой области (–10 ≤ ≤ y ≤ 10) в первой половине толщины шва (z = 7.5).
После термообработки напряжения значительно уменьшились (рис. 4б, 5б). При этом, в целом, растягивающие и сжимающие напряжения остались, соответственно, растягивающими и сжимающими. Максимальные растягивающие продольные напряжения уменьшились до 270 МПа, а максимальные сжимающие поперечные напряжения до –170 МПа.
Остаточные напряжения в образцах без закреплений. На рис. 6 представлены двумерные картограммы распределения напряжений в пластинах ПС и ПСТ, построенные по результатам нейтронных измерений. В пластине ПС (рис. 6a) так же, как и в пластине ПЗ (рис. 5a) распределение продольных и поперечных напряжений близко к симметричному относительно ЦЛ и явно асимметрично относительно середины толщины шва.
Рис. 6.
Двумерная картограмма распределения продольных (σx) и поперечных (σy) напряжений в пластинах ПС (a) и ПСТ (б).
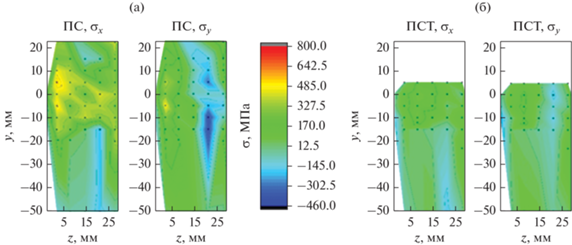
В целом, распределение продольных напряжений имеет сходство с распределением напряжений в пластине ПЗ, однако по величине они значительно ниже. Пиковое значение (530 МПа) наблюдается вблизи поверхности в первой половине толщины шва на Стороне I (z = 2.5, y = 5). Так же, как и в пластинах ПЗ растягивающие поперечные напряжения ниже, чем продольные.
В отличие от пластины ПЗ (рис. 5a), в пластине ПС (рис. 6a) сравнительно большая область сжимающих поперечных напряжений с пиковым значением –400 МПа расположена во второй половине толщины шва, а не в первой.
После термообработки в пластине ПСТ (рис. 6б) напряжения значительно уменьшились. Максимальные растягивающие (продольные) напряжения уменьшились до 220 МПа, а максимальные сжимающие (поперечные) напряжения до –170 МПа.
ОБСУЖДЕНИЕ РЕЗУЛЬТАТОВ
Сварной шов с Х-образной разделкой кромок геометрически симметричен относительно центральной линии сечения шва и середины толщины и может рассматриваться как два V-образных шва с корнем в середине толщины. Поэтому можно было ожидать некоторое сходство и различие в распределении напряжений в Х- и V-образных сварных швах. Распределение продольных и поперечных напряжений близко к симметричному относительно ЦЛ (рис. 5a, 6a), что согласуется с результатами работы [16] и характерно для V-образных сварных швов [9–15]. Распределение напряжений явно асимметрично относительно середины толщины шва, поскольку первая и вторая половина толщины свариваются при различных ограничивающих условиях.
В пластине ПЗ (рис. 5a) максимальные растягивающие продольные напряжения наблюдаются в металле шва вблизи поверхностей пластин по обе стороны от ЦЛ. Они постепенно уменьшаются с приближением к середине толщины шва. Во всей области металла шва продольные напряжения являются растягивающими. Они уменьшаются с удалением от ЦЛ и переходят в сжимающие напряжения на расстоянии ±15 от ЦЛ в основном металле во второй половине толщины шва. Пиковое значение продольных напряжений (800 МПа) в первой половине толщины, близко к пределу текучести металла шва (820 МПа). Однако эффективное напряжение по Мизесу (560 МПа), рассчитанное с использованием измеренных значений продольной, поперечной и нормальной компонент напряжений, составляет около 68% от предела текучести. В целом, распределения продольных напряжений в пластинах ПЗ и ПС схожи (рис. 5a, 6a). Однако в пластине ПС продольные напряжения меньше (пиковое значение 530 МПа), и нет четких максимумов на Стороне II.
Распределение поперечных напряжений имеет четкую асимметрию относительно середины толщины шва (рис. 5a, 6a) и зависит от наличия или отсутствия ребер жесткости. В пластинах ПЗ область максимальных сжимающих напряжений (–400 МПа) находится в первой половине толщины шва, а в пластинах ПС – во второй половине. В целом, в обеих пластинах растягивающие продольные напряжения больше, чем поперечные, что согласуется с результатами работы [16]. Более высокие продольные напряжения по сравнению с поперечными характерны для V- образных сварных швов [13, 22, 23]. Эксперименты [22] показали, что продольные напряжения увеличиваются с увеличением длины шва. Поперечные и нормальные напряжения значительно меньше и слабо зависят от длины шва. Возможно, это объясняется тем, что жесткость пластины в продольном направлении выше, чем в поперечном.
В отличие от работы [16], выполненной методом УРБ, в данной работе не обнаружены максимумы продольных и поперечных напряжений в середине толщины шва. Напротив, вблизи середины толщины шва напряжения уменьшаются. В результате отжига предыдущих валиков при нанесении последующих можно ожидать уменьшение напряжений в корне шва [13].
Неожиданно низкие напряжения (∼10% предела текучести металла шва) наблюдались в усилении вблизи поверхностей швов (рис. 4, 5a, 6a). В отличие от этого в работах [13, 16] на поверхности и вблизи поверхности металла шва наблюдались большие напряжения близкие к пределу текучести. Сравнительно небольшие напряжения (~30% предела текучести основного металла) под точками примыкания усиления шва к основному металлу плохо согласуются с большими напряжениями, измеренными в этих точках методом УРБ (~140% предела текучести основного металла) в X-образном сварном шве [16] и методом ДН (~100% предела текучести основного металла) в V-образном сварном шве [13]. Возможно, низкие напряжения в этих точках связаны с относительно большими размерами усиления.
На рис. 7 представлены распределения остаточных напряжений по толщине шва вдоль ЦЛ, полученные в данной работе методом ДН и в работе [16] методом УРБ. Для сравнения распределения напряжений в швах разной толщины и из разных материалов на графиках указаны глубины, приведенные к толщине сварного шва, а напряжения, приведенные к пределу текучести соответствующего металла шва. Имеется большое различие в распределении продольных напряжений, полученных разными методами (рис. 7а). Оба метода дают растягивающие продольные напряжения вдоль ЦЛ, однако напряжения, полученные методом УРБ значительно выше и в некоторых точках на 50% превышают предел текучести. Следует указать, что помимо различий в толщине и материале шва имеются другие различия между образцами, изученными в данной работе и работе [16], которые могут быть причиной различий продольных напряжений. В образцах работы [16] предел текучести основного металла был ниже, чем предел текучести металла шва (360 и 500 МПа, соответственно). В наших образцах было обратное: соответственно 1040 и 820 МПа. Тепловложение при сварке в наших образцах и образцах работы [16] было также различным: ~1.4 и ~3 кДж мм–1, соответственно. Учитывая большое расхождение в распределении продольных напряжений, было неожиданным большое сходство в распределении поперечных напряжений (рис. 7б), если не учитывать локальный максимум в корне шва в работе [16]. Видимо, поперечные напряжения менее чувствительны к параметрам сварки и более чувствительны к наличию или отсутствию ребер жесткости.
Рис. 7.
Распределения продольных (a) и поперечных (б) напряжений по толщине шва вдоль ЦЛ в пластинах ПЗ и ПС, полученные методами ДН и УРБ [16].
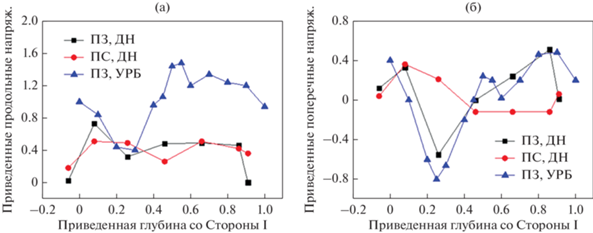
Сравнение пластин до и после термообработки показывает, что после термообработки напряжения значительно уменьшились, но растягивающие и сжимающие напряжения остались, соответственно, растягивающими и сжимающими.
Так же, как и в не отожженных образцах локальные максимумы напряжений в середине толщины сварного шва, в отличие от работы [16], обнаружены не были. Продольные напряжения остались более высокими, чем поперечные. В пластине с ребрами жесткости максимальные растягивающие продольные напряжения 270 МПа (33% предела текучести металла шва) выше, чем в пластине без ребер жесткости 220 МПа и согласуется с результатами (28% предела текучести металла шва), полученными в работе [16].
ВЫВОДЫ
Впервые неразрушающим методом дифракции нейтронов проведено исследование влияния закреплений и термообработки на распределение остаточных напряжений в стальном X-образном сварном шве. Результаты проведенных исследований позволяют сделать следующие выводы:
1. Распределение напряжений в X-образном сварном шве близко к симметричному относительно центральной линии сечения шва и явно асимметрично относительно середины толщины шва.
2. Имеется сходство в распределении продольных растягивающих напряжений в пластинах с закреплениями и без закреплений. В обеих пластинах имеются два максимума вблизи поверхности на Стороне I в металле шва по обе стороны от центральной линии сечения шва. В пластине с закреплениями пиковое значение продольных напряжений 800 МПа (98% предела текучести металла шва) выше, чем в пластине без закреплений 530 МПа (65% предела текучести металла шва).
3. Распределение поперечных напряжений сильно зависит от наличия или отсутствия закреплений. В пластине с закреплениями область максимальных сжимающих (поперечных) напряжений (–400 МПа) находится в первой половине толщины шва, а в пластине без закреплений – во второй.
4. Остаточные напряжения в усилении (10% предела текучести металла шва) и под точками примыкания усиления к основному металлу (30% предела текучести основного металла) значительно ниже, чем пределы текучести соответствующих металлов.
5. После термообработки максимальные растягивающие (продольные) и сжимающие (поперечные) напряжения значительно уменьшились, однако они остались, соответственно, растягивающими и сжимающими. В пластине с закреплениями максимальное растягивающее продольное напряжение 270 МПа (33% предела текучести металла шва) несколько ниже, чем в пластине без закреплений 220 МПа (27% предела текучести металла шва). Максимальные сжимающие поперечные напряжения (–170 МПа) одинаковы в обеих пластинах.
Работа выполнена на оборудовании уникальной научной установки “Нейтронный исследовательский комплекс на базе реактора ИР-8”.
Список литературы
Withers P.J., Bhadeshia H.K. Residual Stress – II: Nature and Origins // Mater. Sci. Technol. 2001. V. 17. P. 366–375.
Hutchings M.T., Withers P.J., Holden T.M., Lorentzen T. Introduction to the Characterization of Residual Stress by Neutron Diffraction. 1st ed. Taylor and Francis. London, 2005. 434 p.
Mochizuki M. Control of welding residual stress for ensuring integrity against fatigue and stress–corrosion cracking // Nucl. Eng. Des. 2007. V. 237. P. 107–123.
Winzer N., Atrens A., Dietzel W., Raja V.S., Song G., Kainer K.U. Characterisation of Stress Corrosion Cracking (SCC) of Mg–Al Alloys // Mater. Sci. Eng. A. 2008. V. 488. № 1–2. P. 339–351.
Barsoum Z., Barsoum I. Residual stress effects on fatigue life of welded structures using LEFM // Eng. Fail. Anal. 2009. V. 16. P. 449–467.
Doremus L., Cormier J., Villechaise P., Henaff G., Nadot Y., Pierret S. Influence of Residual Stresses on the Fatigue Crack Growth From Surface Anomalies in a Nickel-Based Superalloy // Mater. Sci. Eng. A. 2015. V. 644. P. 234–246.
Cheng X., Fisher J.W., Prask H.J., Gnäupel-Herold T., Yen B.T., Roy S. Residual stress modification by post-weld treatment and its beneficial effect on fatigue strength of welded structures // Int. J. Fatigue. 2003. V. 25. P. 1259–1269.
Xu M., Chen J., Lu H., Xu J., Yu C., Wei X. Effects of Residual Stress and Grain Boundary Character on Creep Cracking in 2.25Cr–1.6W Steel // Mater. Sci. Eng. A. 2016. V. 659. P. 188–197.
Woo W., Em V.T., Mikula P., An G.B., Seong B. Neutron diffraction measurements of residual stresses in a 50mm thick weld // Mater. Sci. Eng. A. 2011. V. 528. P. 4120–4124. https://doi.org/10.1016/j.msea.2011.02.009
Paradowska A.M., Price J.W.H., Finlauson T.R., Rogge R.B., Donaberger R.L., Ibrahim R. Comparison of neutron diffraction measurements of residual stress of steel butt welds with current fitness-for-purpose assessments // J. Pres. Ves. Technol. Trans. ASME. 2010. V. 132. P. 051503-7.
Woo W., An G., Kingston E., Dewald A., Smith D., Hill M.R. Through-thickness distributions of residual stresses in two extreme heat-input thick welds: a neutron diffraction, contour method and deep hole drilling study // Acta Mater. 2013. V. 61. P. 3564–3574.
Smith D.J., Zheng G., Hurrell P.R., Gill C.M., Pellereau B.M.E., Ayres K., Goudar D., Kingston E. Measured and Predicted Residual Stresses in Thick Section Electron Beam Welded Steels // Int. J. Pres. Ves. Pip. 2014. V. 120–121. P. 66–79.
Alipooramirabad H., Paradowska A., Ghomashchi R., Kotousov A., Reid M. Quantification of Residual Stresses in Multi-Pass Welds Using Neutron Diffraction, // J. Mater. Process. Technol. 2015. V. 226. P. 40–49.
Jiang W., Woo W., Wan Y., Luo Y., Xie X., Tu S.T. Evaluation of through-thickness residual stresses by neutron diffraction and finite-element method in thick weld plates // J. Pressure Vessel Technol. 2017. V. 139. №3. P. 031401-11.
Wan Y., Jiang W., Lu J., Sun G., Kim D.K., Woo W., Tu S.T. Weld residual stresses in a thick plate considering back chipping: neutron diffraction, contour method and finite element simulation study // Mater. Sci. Eng. A. 2017. V. 699. P. 62–70.
Smith D.J., Garwood S.J. Influence of postweld heat treatment on the variation of residual stresses in 50 mm thick welded ferritic steel plates // Int. J. Pres. Ves. Pip. 1992. V. 51. P. 241–256.
Shim Y., Feng Z., Lee S., Kim D., Jaeger J., Parritan J.C., Tsai C.L. Determination of residual stresses in thick-section weldments // Welding Research Supplement I. 1992. V. 71. P. 305–312.
Эм В.Т., Балагуров А.М., Глазков В.П., Карпов И.Д., Mikula P., Мирон Н.Ф., Соменков В.А., Сумин В.В., Saroun J., Шушунов М.Н. Двойной монохроматор для нейтронной стресс-дифрактометрии // ПТЭ. 2017. № 4. С. 75–81. [Em V.T., Balagurov A.M., Glazkov V.P., Karpov I.D., Mikula P., Miron N.F., Somenkov V.A., Sumin V.V., Šaroun J., Shushunov M.N. A double-crystal monochromator for neutron stress diffractometry // Instr. exper. techn. 2017. 60(4). P. 526–532.]https://doi.org/10.7868/S003281621704004
Em V.T., Karpov I.D., Somenkov V.A., Glazkov V.P., Balagurov A.M., Sumin V.V., Mikula P., Šaroun J. Residual stress instrument with double-crystal monochromator at research reactor IR-8 // Physica B: Condensed Matter. 2018. V. 551. P. 413–416. https://doi.org/10.1016/j.physb.2018.02.042
Woo W., Em V.T., Seong B., Shin E., Mikula P., Joo J., Kang M. Effect of wavelength-dependent attenuation on neutron diffraction stress measurements at depth in steels // J. Appl. Cryst. 2011. V. 44. P. 747–754. https://doi.org/10.1107/S0021889811018899
Ganguly S., Edwards L., Fitzpatrick M.E. Problems in using a comb sample as a stress-free reference for the determination of welding residual stress by diffraction // Mater. Sci. Eng. A. 2011. V. 528. P. 1226–1232.
Ohms C., Hornak P., Wimpory R., Youtsos A.G. Residual stress analyses based on neutron diffraction in double-V butt welded steel plates // J. Neutron Res. 2003. V. 11. P. 273–276.
Suzuki H., Holden T.M. Neutron diffraction measurements of stress in an austenitic butt weld // J. Strain Analysis. 2006. V. 41. № 8. P. 575–581.
Дополнительные материалы отсутствуют.
Инструменты
Физика металлов и металловедение