Физика металлов и металловедение, 2022, T. 123, № 9, стр. 1002-1008
Улучшение прочностных характеристик сплава Zr–2.5% Nb ротационной ковкой
С. О. Рогачев a, b, *, В. А. Андреев b, c, М. В. Горшенков a, Д. В. Тен a, А. С. Кузнецова a, А. Б. Щербаков d
a Национальный исследовательский технологический университет “МИСиС”
119049 Москва, Ленинский пр., 4, Россия
b Институт металлургии и материаловедения им. А.А. Байкова РАН
119334 Москва, Ленинский пр., 49, Россия
c ООО “Промышленный центр МАТЭК-СПФ”
117449 Москва, ул. Карьер, 2А/1, Россия
d ООО “3Д-КОМПОНЕНТ”
347360 Ростовская обл., Волгодонск, 7-я Заводская ул., 36, Россия
* E-mail: csaap@mail.ru
Поступила в редакцию 30.05.2022
После доработки 07.07.2022
Принята к публикации 11.07.2022
- EDN: KTMGXE
- DOI: 10.31857/S001532302209011X
Аннотация
Для улучшения прочности биосовместимого циркониевого сплава Zr–2.5% Nb (Э125) использован один из методов большой пластической деформации – ротационная ковка. В результате обжатия исходно рекристаллизованного прутка сплава с диаметра 12 мм на диаметр 6.5 мм в нем сформировалась зеренно-субзеренная ориентированная микроструктура с преобладанием малоугловых разориентировок структурных элементов и высокой плотностью дислокаций. Такое изменение структуры привело к увеличению условного предела текучести и предела прочности сплава в 2.1 и 1.6 раза, соответственно. После ротационной ковки сплав обладает хорошим запасом пластичности – относительное удлинение составило 14%. Достигнутый на сплаве Zr–2.5% Nb комплекс механических свойств соответствует требованиям, предъявляемым к материалу стоматологических имплантатов.
ВВЕДЕНИЕ
В развитии стоматологической имплантологии актуальна проблема выбора оптимального материала для изготовления имплантатов [1]. Сегодня основным материалом для этой цели служит титан [2]. Для достижения требуемой прочности титан легируют, в том числе относительно токсичными элементами (ванадий, алюминий), что ограничивает срок эксплуатации имплантата [3]. Хорошей альтернативой титану является его близкий аналог – цирконий, благодаря высокой коррозионной стойкости и совместимости с биологическими тканями человека [4–6]. Как и титан, цирконий для повышения прочности легируют [7]. Однако в отличие от сплавов титана, важнейшие сплавы циркония, а именно сплавы системы Zr–Nb, являются биоинертными [4]. Ввиду этого перспективным для медицинского применения материалом является биоинертный низколегированный промышленный сплав Zr–2.5% Nb (Э125) [8]. Тем не менее производимые промышленностью циркониевые сплавы не обладают достаточной для применения в медицине прочностью и требуют дополнительного упрочнения.
Хорошо известно, что за счет некоторых методов больших пластических деформаций циркониевым сплавам можно придать необходимый для изготовления имплантатов комплекс высоких механических и функциональных свойств [9–12]. Ранее было показано, что за счет обработки равноканальным угловым прессованием (РКУП) в сплаве Zr–2.5% Nb формируется ультрамелкозернистая структура, в результате чего достигается комплекс свойств (высокая статическая и усталостная прочность, улучшенная коррозионная стойкость), удовлетворяющий требованиям к конструкционному материалу со стороны медицины [13]. Хотя сплав Zr–2.5% Nb после обработки РКУП уже может быть применим для изготовления имплантатов, небольшие размеры РКУП-заготовки ограничивают объем производства и усложняют его. Поэтому поиск альтернативного метода, позволяющего достичь сопоставимый комплекс свойств в крупногабаритных заготовках, является актуальной задачей. Таким методом может быть ротационная ковка (РК), которая наиболее эффективна при производстве длинномерных прутков или проволок [14–18]. РК относят к методам больших пластических деформаций, ввиду возможности достигать очень высокие степени сдвиговой деформации в обрабатываемой заготовке при низких температурах. Поэтому целью работы является изучение влияния РК на структуру и механические свойства циркониевого сплава Zr–2.5% Nb.
МАТЕРИАЛЫ И МЕТОДИКИ ИССЛЕДОВАНИЯ
В качестве исходного материала использовали прутки сплава Zr–2.5% Nb (Э125) диаметром 12 мм в состоянии поставки, которые перед РК подвергали рекристаллизационному отжигу (Т = 580°С, 6 ч, вакуум 6.5 × 10-3 Па, медленное охлаждение). Химический состав сплава: 97.34% Zr; 2.55% Nb; 0.01% Fe; 0.03% Hf %; 0.002% N; 0.03% O.
РК заготовок с начального диаметра 12 мм до конечного диаметра 6.5 мм осуществляли при температуре 200°С на модернизированной двухбойковой ротационно-ковочной машине В2129.01 производства ОАО “Прессмаш” за 9 проходов: обжатие за проход составляло 7–19%. Для исследования были взяты образцы в состоянии поставки, после рекристаллизационного отжига, после РК на диаметр 8.5 мм и после РК на диаметр 6.5 мм.
Электронно-микроскопические исследования структуры заготовки в продольном сечении до и после РК проводили на тонких фольгах с помощью электронного микроскопа JEM-1400 (JEOL) в светлых и темных полях.
Рентгеновский анализ продольных образцов проводили на дифрактометре ДРОН 3М в монохроматическом CuKα-излучении.
Для оценки степени упрочнения/разупрочнения измеряли микротвердость по Виккерсу (нагрузка 0.5 Н, время выдержки 10 с) образцов, используя микротвердомер Micromet 5101 Buehler. Измерения проводили на полированном шлифе заготовки (по 30 измерений случайным образом с последующим расчетом среднего арифметического значения и cреднеквадратического отклонения).
Миниатюрные плоские разрывные образцы длиной и шириной рабочей части 5 и 1.45 мм, соответственно, и толщиной 0.5 мм вырезали в продольном направлении электроэрозионным методом с последующей механической шлифовкой и полировкой поверхности. Испытание на растяжение проводили при комнатной температуре с помощью машины INSTRON 5966 и специальных переходников. Скорость деформации составила 1.5 × 10–3 с–1. Испытывали по 3 образца на точку.
РЕЗУЛЬТАТЫ И ОБСУЖДЕНИЕ
В состоянии поставки сплав имел частично рекристаллизованную структуру (рис. 1а, 1б). Наблюдали области, занятые рекристаллизованными зернами размером 0.5–2 мкм с малой плотностью дислокаций, и области, занятые сильно вытянутыми слаборазориентированными субзернами толщиной 0.05–0.3 мкм. Такие вытянутые субзерна сформировались при холодной деформации прутка в процессе его изготовления. Кроме этого в структуре наблюдаются строчки наноразмерных частиц β-Nb, ориентированные вдоль направления холодной деформации.
Рис. 1.
Микроструктура сплава Zr–2.5% Nb в состоянии поставки (а, б) и после рекристаллизационного отжига (в, г): а, в – светлопольные изображения при увеличении ×15 000; б, г – светлопольные изображения при увеличении ×30 000.
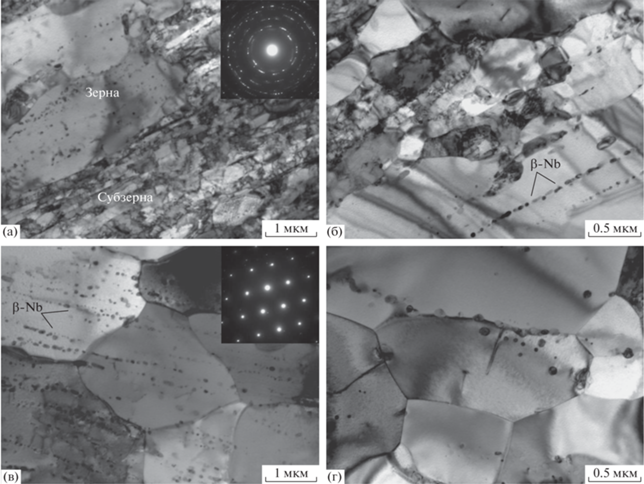
Такая частично рекристаллизованная структура с высокой плотностью дислокаций обеспечивает комбинацию относительно высокой прочности и пластичности сплава при растяжении: условный предел текучести и предел прочности составили 507 и 679 МПа соответственно при относительном удлинении 24% (табл. 1).
Таблица 1.
Механические свойства сплава Zr–2.5% Nb
Состояние | σ0.2, МПа | σВ, МПа | δ, % | δравн, % |
---|---|---|---|---|
Поставка | 507 | 679 | 24.0 | 7.0 |
Отжиг при 580°C, 6 ч | 313 | 491 | 32.0 | 14.0 |
РК на диаметр 8.5 мм | 644 | 748 | 16.0 | 6.0 |
РК на диаметр 6.5 мм | 659 | 805 | 14.0 | 3.5 |
Отжиг при температуре 580°С привел к полной рекристаллизации сплава с формированием равноосных зерен размером 1–4 мкм с малой плотностью дислокаций (рис. 1в, 1г). При этом в структуре сплава сохранились строчки частиц β-Nb. Эти результаты отличаются от [19], где даже после 12 ч отжига при температуре 580°С в структуре сплава сохранялись вытянутые субзерна. Это может быть связано с большей степенью рекристаллизации исходного прутка (до отжига) в работе [19] и, следовательно, с меньшей плотностью дислокаций в его структуре, что потребовало бы более высокой температуры или времени выдержки для завершения процесса рекристаллизации.
Рекристаллизационный отжиг привел к снижению прочности и увеличению пластичности сплава: условный предел текучести и предел прочности составили 313 и 491 МПа, соответственно, при относительном удлинении 32% (табл. 1).
В результате РК-обжатия рекристаллизованной заготовки с диаметра 12 мм на диаметр 8.5 мм в ней сформировалась сильно неоднородная ультрамелкозернистая структура с высокой плотностью дислокаций и преобладанием малоугловых разориентировок структурных элементов с преимущественной шириной 0.76–2.31 мкм (рис. 2а, 2б). В структуре наблюдаются немногочисленные кристаллиты с большеугловой разориентировкой нано- и субмикронных размеров 0.1–0.4 мкм. Дальнейшее обжатие на диаметр 6.5 мм привело к увеличению доли кристаллитов (причем диапазон их размеров не изменился) с большеугловой разориентировкой (рис. 2в, 2г). В структуре сохраняются слаборазорентированные структурные элементы, причем их ширина уменьшается до 0.07–0.48 мкм, а длина увеличивается, и структура приобретает ярко выраженную ориентацию.
Рис. 2.
Микроструктура сплава Zr–2.5% Nb после РК на диаметр 8.5 (а, б) и 6.5 мм (в, г): а, в – светлопольные изображения при увеличении ×50 000; б, г – темнопольные изображения в рефлексе (Zr) при увеличении ×20 000.
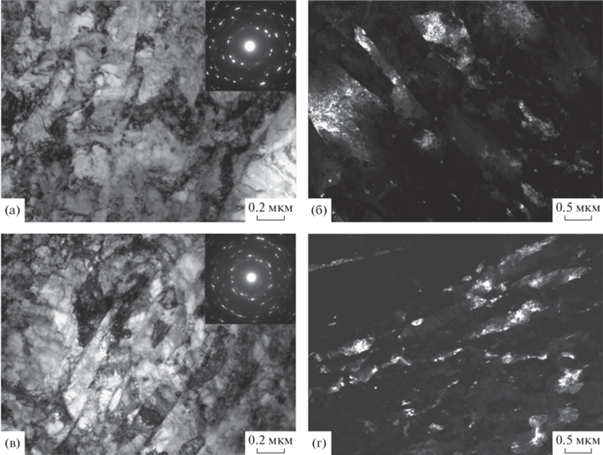
После РК в структуре сплава строчки частиц β-Nb не наблюдаются, однако отдельные малочисленные частицы присутствуют. Этот факт может свидетельствовать о частичном растворении ниобия в твердом растворе (Zr), что обсуждалось в работах [12, 13]. В этом случае следует ожидать вклада твердорастворного упрочнения в общее упрочнение сплава. В то же время нельзя исключать и трансформацию частиц в сегрегации ниобия. Например, при обработке сплава Al–Ca методом кручения под давлением наблюдалось образование сегрегаций кальция [20]. Вклад сегрегаций в общее упрочнение неоднозначен и требует дальнейших исследований.
На рис. 3 приведены рентгеновские дифрактограммы сплава Zr–2.5% Nb в состоянии поставки, после отжига и после РК на диаметр 6.5 мм. Видно, что структура сплава всех состояний однофазная и представлена твердым раствором α-Zr. Наблюдаемые методом ПЭМ частицы β-Nb в структуре сплава в состоянии поставки и после отжига рентгеновским методом не выявлены, по-видимому, из-за их небольшой доли (около 2%) и неравномерного (строчечного) распределения в структуре. Можно отметить, что в состоянии поставки рентгеновские линии уширены (ширина на полувысоте линии (114)Zr составила 0.91°). После отжига уширение линий уменьшается (ширина на полувысоте линии (114)Zr составила 0.73°. Наибольшее уширение линий наблюдается после РК на диаметр 6.5 мм (ширина на полувысоте линии (114)Zr составила 1.16°), что можно связать с увеличением плотности дислокаций и измельчением структуры.
Формирование подобной структуры в сплаве Zr–2.5% Nb в результате РК привело к существенному повышению его прочностных характеристик при растяжении по сравнению с рекристаллизованным состоянием (табл. 1). Так условный предел текучести и предел прочности сплава после РК на диаметр 8.5 мм составили 644 и 748 МПа, соответственно (в 2 и 1.5 раза выше, соответственно, по сравнению с рекристаллизованным сплавом). При этом относительное удлинение сохраняется на относительно высоком уровне 16% (которое, тем не менее, в 2 раза ниже по сравнению с рекристаллизованным сплавом). Полученные значения пределов текучести и прочности оказались выше и по сравнению со сплавом в состоянии поставки – в 1.3 и 1.1 раз соответственно.
Дальнейшая РК на диаметр 6.5 мм приводит к еще большему повышению прочности: условный предел текучести и предел прочности сплава составили 659 и 805 МПа, соответственно (в 2.1 и 1.6 раза выше, соответственно, по сравнению с рекристаллизованным сплавом), при относительном удлинении 14%. Полученные значения пределов текучести и прочности выше в 1.3 и 1.2 раз, соответственно, по сравнению со сплавом в состоянии поставки. Кривые деформации сплава для всех состояний характеризуются протяженной областью локализованной деформации (рис. 4).
Рис. 4.
Кривые растяжения сплава Zr–2.5% Nb в состоянии поставки (1), после рекристаллизационного отжига (2), после РК на диаметр 8.5 мм (3) и после РК на диаметр 6.5 мм (4).
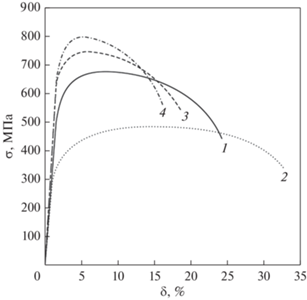
Не обнаружено прямой корреляции между измеренными на образцах значениями микротвердости со статической прочностью. Так наименьшие значения микротвердости наблюдаются для образцов сплава с рекристаллизованной структурой, полученной после отжига при 580°С; они составили 144.1 ± 3.3 HV. В то же время значения микротвердости для образцов сплава в состоянии поставки и после РК на диаметр 6.5 мм близки и составили 190.6 ± 5.2 HV и 187.4 ± 4.7 HV, соответственно, что в 1.3 раза выше по сравнению с рекристаллизованным сплавом.
Полученный за счет РК комплекс механических свойств сплава Zr–2.5% Nb близок к достигнутому ранее за счет РКУП через 6 проходов с температурой последнего прохода 350°С [13]. Так условный предел текучести сплава после РКУП всего на 6% выше условного предела текучести сплава после РК, а предел прочности сплава после РКУП сопоставим с пределом прочности сплава после РК, несмотря на более высокую температуру РКУП по сравнению с РК. Относительное удлинение сплава после РК выше, чем после РКУП. При этом можно отметить отличия в структуре сплава после РКУП и после РК. Сплав после РКУП характеризовался наличием большой доли равноосных кристаллитов с большеугловой разорентировкой [13]. По-видимому, значительный вклад в упрочнение вносят дислокации, плотность которых может быть сопоставима как после РКУП, так и после РК.
Таким образом, проведенное исследование показало, что технология обработки сплава Zr–2.5% Nb методом РК с точки зрения достигнутого комплекса механических свойств не уступает технологии РКУП. Напротив, метод РК является более технологичным, т.к. позволяет осуществлять процесс при более низких температурах, а также получать длинномерные заготовки. С учетом приобретенного комплекса механических свойств, сплав Zr–2.5% Nb после РК применим в качестве конструкционного материала для изготовления медицинских имплантатов. По результатам работы получена пробная партия конструкционных элементов стоматологических имплантатов с использованием токарного оборудования. В качестве заготовки использовали РК-пруток сплава диаметром 6.5 мм (наиболее упрочненный), который перед токарной обработкой подвергали правке и шлифовке на диаметр 6.1 мм. Внешний вид полученных изделий показан на рис. 5.
ВЫВОДЫ
В результате обжатия ротационной ковкой (РК) при 200°С исходно рекристаллизованного прутка циркониевого сплава Zr–2.5% Nb с диаметра 12 мм на диаметр 6.5 мм в нем сформировалась ориентированная ультрамелкозернистая микроструктура с высокой плотностью дислокаций. В структуре присутствуют вытянутые субзерна шириной 0.07–0.48 мкм и кристаллиты преимущественно равноосной формы размером 0.1–0.4 мкм.
Изменение структуры в ходе РК привело к увеличению условного предела текучести и предела прочности сплава в 2.1 и 1.6 раза, соответственно. После РК сплав обладает хорошим запасом пластичности – относительное удлинение составило 14%.
Прочностные свойства сплава после ротационной ковки и после равноканального углового прессования с температурой последнего прохода 350°С близки, при этом относительное удлинение сплава после РК выше, чем после РКУП.
Технология обработки сплава Zr–2.5% Nb методом РК является более технологичной по сравнению с РКУП, т.к. позволяет осуществлять процесс при более низких температурах, а также получать длинномерные заготовки. С учетом приобретенного комплекса механических свойств сплав Zr–2.5% Nb после РК применим в качестве конструкционного материала для изготовления медицинских имплантатов.
Работа выполнена в рамках государственного задания ИМЕТ РАН № 075-00715-22-00 на 2022 г. Исследование структуры выполнено на оборудовании ЦКП “Материаловедение и металлургия” при финансовой поддержке РФ в лице Минобрнауки (№ 075-15-2021-696).
Список литературы
Steinemann S.G. Corrosion of surgical implants – in vivo and in vitro tests, evaluation of biomaterials. N.Y.: Wiley, 1980. P. 1–34.
Balazic M., Kopac J., Jackson M.J., Ahmed W. Review: Titanium and titanium alloy applications in medicine // Intern. J. Nano and Biomater. 2007. V. 1. № 1. P. 3–34.
Leyens C., Peters M. Titanium and Titanium Alloys. Fundamentalsand Applications, by Wiley-VCH, Köln, Germany, 2003. 532 p.
Фадеев А.Ю. Цирконий в ортопедической стоматологии // Медтехника и медизделия. 2002. № 4(10). С. 26–30.
Шапошников Ю.Г., Шерепо К.М., Горохов В.Ю., Берченко Г.Н. Цирконий для эксплантатов в травматологии и ортопедии // Ортопедия, травматология и протезирование. 1993. № 1. С. 31–33.
Byeli A.V., Kukareko V.A., Kononov A.G. Titanium and zirconium based alloys modified by intensive plastic deformation and nitrogen ion implantation for biocompatible implants // J. the Mech. Behavior of Biomedical Mater. 2012. V. 6. P. 89–94.
Займовский А.С., Никулина А.В., Решетников Ф.Г. Циркониевые сплавы в атомной промышленности. М.: Энергоатомиздат, 1994. 253 с.
Асташина Н.Б., Оголь Р.Ю., Рогожников А.Г., Шулятникова О.А., Неменатов И.Г. Обоснование применения сплава циркония Э-125 для реставрации твердых тканей зубов // Российский стоматологический журн. 2009. № 6. С. 13–14.
Lee B.S., Kim M.H., Hwang S.K., Kwun S.I., Chae S.W. Grain refinement of commercially pure zirconium by ECAP and subsequent intermediate heat treatment // Mater. Sci. Eng. A. 2007. V. 449–451. P. 1087–1089.
Sklenicka V., Dvorak J., Kral P., Svoboda M., Kvapilova M., Kopylov V.I., Nikulin S.A. and Dobatkin S.V. Creep Behavior of a Zirconium Alloy Processed by Equal-Channel Angular Pressing // Acta Physica Polonica A. 2012. V. 122. P. 485–489.
Шаркеев Ю.П., Ерошенко А.Ю., Данилов В.И., Толмачев А.И., Уваркин П.В., Абзаев Ю.А. Микроструктура и механические свойства наноструктурированных и ультрамелкозернистых титана и циркония, сформированных методом интенсивной пластической деформации // Известия вузов. Физика. 2013. Т. 56. № 10. С. 47–53.
Рогачев С.О., Рожнов А.Б., Никулин С.А., Рыбальченко О.В., Горшенков М.В., Чжен В.Г., Добаткин С.В. Влияние режимов кручения под высоким давлением на структуру и упрочнение сплава Zr–1% Nb // ФММ. 2016. Т. 117. № 4. С. 385–391.
Nikulin S.A., Rozhnov A.B., Rogachev S.O., Khatkevich V.M., Turchenko V.A., Khotulev E.S. Investigation of structure, phase composition, and mechanical properties of Zr–2.5% Nb alloy after ECAP // Mater. Letters. 2016. V. 169. P. 223–226.
Rogachev S.O., Andreev V.A., Yusupov V.S., Bondareva S.A., Hatkevich V.M., Nikolaev E.V. Effect of rotary forging on microstructure evolution and mechanical properties of aluminum alloy/copper bimetallic material // Metals Mater. Intern. 2022. V. 28. P. 1038–1046.
Стёпин П.С., Рааб Г.И. Исследование потенциала ротационной ковки для получения материалов с ультрамелкозернистой структурой // Кузнечно-штамповочное производство. Обработка материалов давлением. 2012. № 4. С. 34–37.
Никулин С.А., Котрехов В.А., Рожнов А.Б., Хаткевич В.М., Рогачев С.О., Заводчиков А.С. Механические свойства и характер разрушения трубной заготовки из циркониевого сплава Э110 после радиальной ковки с различной степенью деформации // Деформация и разрушение материалов. 2012. № 2. С. 36–42.
Kocich R., Macháčková A., Kunčická L., Fojtík F. Fabrication and characterization of cold-swaged multilayered Al–Cu clad composites // Mater. Design. 2015. V. 71. P. 36–47.
Чувильдеев В.Н., Копылов В.И., Нохрин А.В., Бахметьев А.М., Тряев П.В., Табачкова Н.Ю., Чегуров М.К., Козлова Н.А., Михайлов А.С., Ершова А.В., Грязнов М.Ю., Шадрина Я.С., Лихницкий К.В., Степанов С.П., Мышляев М.М. Повышение прочности и коррозионной стойкости титанового сплава ПТ-7М с использованием технологии ротационной ковки // Металлы. 2021. № 3. С. 37–48.
Белов В.А., Никулин С.А., Рожнов А.Б., Рогачев С.О. Влияние РКУ-прессования на трещиностойкость и сопротивление равномерной коррозии циркониевого сплава Zr–2.5% Nb // Сборник трудов XIII Российско-Китайского Симпозиума Новые материалы и технологии. Под общей редакцией академика РАН К.А. Солнцева. В 2-х томах. М.: Интерконтакт Наука, 2015. С. 69–71.
Sauvage X., Cuvilly F., Russell A., Edalati K. Understanding the role of Ca segregation on thermal stability, electrical resistivity and mechanical strength of nanostructured aluminum // Mater. Sci. Eng.: A. 2020. V. 798. P. 140108.
Дополнительные материалы отсутствуют.
Инструменты
Физика металлов и металловедение