Физика металлов и металловедение, 2023, T. 124, № 2, стр. 248-254
Сравнительная характеристика структуры и функциональных свойств покрытий, формируемых на алюминиевых сплавах 2ххх и 7ххх серии методом плазменного электролитического оксидирования
Н. В. Летягин a, b, *, А. А. Сокорев c, В. Н. Кокарев c, А. С. Шатров c, А. Г. Цыденов c, А. С. Финогеев a, c, А. Ф. Мусин a, М. И. Петржик a
a Национальный исследовательский технологический университет “МИСиС”
119049 Москва, ул. Ленинский просп., 4, Россия
b Московский политехнический университет
107023 Москва, ул. Большая Семёновская, 38, Россия
c АО “Завод алюминиевых сплавов”
142155 Московская область, Подольск, просп. Металлургов, 3к, Россия
* E-mail: n.v.letyagin@gmail.com
Поступила в редакцию 17.04.2022
После доработки 30.11.2022
Принята к публикации 09.12.2022
- EDN: HJMCIK
- DOI: 10.31857/S0015323022100345
Аннотация
Исследованы структура и свойства покрытий, сформированных при одинаковых режимах процесса плазменного электролитического оксидирования (ПЭО) на образцах алюминиевых сплавов 2ххх и 7ххх серии. Показано, что материал подложки оказывает значительное влияние на качество, структуру и свойства формируемого покрытия. Подложка из сплава В95 Т1 (6.2Zn, 2.4Mg, 1.7Cu), в сравнении со сплавом Д16 Т (4Cu, 1.4Mg мас. %), способствует образованию более однородного по составу и толщине покрытия с превосходящими показателями когезионной и адгезионной прочности, механических и трибологических свойств. Адгезионное разрушение ПЭО покрытий на сплаве В95 Т1 происходит при нагрузке 63 Н, что значительно выше значения критической нагрузки (49 Н) покрытий, сформированных на сплаве Д16 Т. Максимальное значение твердости сформированных покрытий на сплаве В95 Т1 составляет 25 ГПа, что превосходит твердость покрытий на сплаве Д16 Т, которая составляет 20 ГПа. Износостойкость в водной среде покрытия, образованного на подложке из сплава В95 Т1, в 4,4 раза выше по сравнению с износостойкостью покрытия на сплаве Д16 Т.
ВВЕДЕНИЕ
Функциональные защитные покрытия, формируемые на изделиях из алюминиевых сплавов методом плазменного электролитического оксидирования (ПЭО), в значительной мере способствуют расширению области применения алюминиевой продукции, существенно повышая твердость, износостойкость, коррозионную стойкость изделий [1–5]. Ярким примером этого является возможность серийного производства алюминиевых изделий с ПЭО-покрытием для нефтегазовой отрасли, таких как ступени центробежных насосов [6], шаровых затворов [7], бурильных труб [8], которые в условиях интенсивной химической и электрохимической коррозии, механического изнашивания и кавитации, имеют больший ресурс, чем стальные, чугунные или латунные детали. Такие кардинальные изменения в области применения конструкционных материалов на основе алюминия обусловлены как возможностью достижения требуемых прочностных свойств при использовании высокоресурсных дюралюминов 2ххх серии или высокопрочных сплавов 7ххх серии (предел прочности более 450 МПа, предел текучести более 300 МПа, при относительном удлинении не менее 8% [9–11]), так и резкому улучшению функциональных характеристик поверхностных слоев благодаря формируемому ПЭО-покрытию.
Характеристики формируемых покрытий зависят от режимов плазменного электролитического оксидирования, состава электролита и материала подложки [12–14]. Существенное влияние на структуру, морфологию и свойства покрытий оказывает как химический, так и фазовый состав подложки, что было отмечено при исследовании оксидированных поверхностей алюминиевых сплавов различных систем легирования [15–26].
В процессе ПЭО под действием высоких температур плазменных микроразрядов происходит плавление алюминия и других компонентов сплава подложки с их переходом в покрытие. Причем в образующийся канал микроразряда втягиваются анионные компоненты электролита, которые способствуют окислению расплавленных компонентов подложки. А развитая система пор и прогрев близлежащих участков покрытия способствуют его росту на свободной от разрядов поверхности за счет дополнительной миграции и диффузии катионов и анионов. Таким образом происходит как локальный рост покрытия, так и проникновение покрытия вглубь подложки [12].
Исследования микроструктуры и функциональных свойств ПЭО-покрытий в контексте влияния химического состава подложки на примере промышленных алюминиевых сплавов 2ххх и 7ххх серии показывает, что наличие определенных легирующих элементов подложки (Cu, Mg, Zn) в покрытии оказывает существенное влияние на его структуру, морфологию, твердость и износостойкость.
Такой легирующий элемент как Mg способствует росту толщины ПЭО покрытия, а Cu, Zn замедляют процесс его формирования. Наличие катионов Cu, Mg, Zn способно в значительной мере изменять объемное соотношение формируемых в процессе ПЭО оксидов γ-Al2O3 и α-Al2O3 [21–24], влияющих на твердость и износостойкость. Кроме того, пористость покрытия имеет тенденцию увеличиваться с увеличением концентрации легирующих элементов. В том числе медьсодержащие структурные составляющие подложки, имея существенную растворимость в покрытии в процессе его формирования, способны повышать пористость покрытия вблизи подложки [17, 25, 26].
Прямой сравнительный анализ данных публикаций невозможно провести в связи с вариативностью состава электролита и параметров обработки, используемых в каждом конкретном случае. Таким образом, целью настоящего исследования является сравнительная оценка структуры и свойств функциональных ПЭО-покрытий, формируемых в процессе идентичной обработки сплавов Д16 Т и В95 Т1.
МЕТОДИКА ИССЛЕДОВАНИЙ
Объектом исследования были плоскопараллельные образцы-диски (диаметром 62 мм, толщиной 6.5 мм) из промышленных алюминиевых сплавов В95 Т1 и Д16 Т (табл. 1) с покрытием, сформированном методом плазменно-электролитического оксидирования. Процесс формирования покрытия осуществляли на установке ПЭО с высокочастотным высоковольтным импульсным источником питания мощностью 250 кВт. Процесс ПЭО-проводили в силикатно-щелочном электролите, подготовленном путем растворения в дистиллированной воде KOH – 2 г/л, Na2SiO3 – 6 г/л, Н3ВО3 – 1 г/л. В процессе формирования ПЭО-покрытия электролит непрерывно перемешивали для поддержания его однородности и температуры на уровне 15–20°С вокруг электролитической ячейки. В процессе формирования покрытия поддерживали следующие режимы процесса: напряжение (анодное Ua = 1000 В, катодное Uk = 300 В); плотность тока 25 А/дм2; частота следования импульсов f = 3 кГц; время оксидирования – 40 мин.
Таблица 1.
Химический состав сплавов (подложек)
Сплав | Состояние | Содержание легирующих элементов, мас. % | |||||
---|---|---|---|---|---|---|---|
Cu | Mg | Zn | Mn | Si | Fe | ||
Д16 | Т | 4.0 | 1.4 | 0.1 | 0.6 | 0.3 | 0.3 |
В95 | Т1 | 1.7 | 2.4 | 6.2 | 0.4 | 0.1 | 0.2 |
Исследование микроструктуры и химического состава сплава и покрытия проводили с использованием сканирующего электронного микроскопа (СЭМ) TESCAN VEGA 3 (Чехия) с энергодисперсионной приставкой-микроанализатором производства Oxford Instruments и программным обеспечением Aztec. Химический состав покрытия был определен методом микрорентгеноспектрального анализа (МРСА) в поперечном сечении покрытия с интервалом кратным 1/16 толщины покрытия.
С помощью оптического профилометра WYKO NT 1100 (VEECO, США) был проведен анализ размеров пор и их распределения. Измерения геометрических размеров пор проводили на поверхности образцов-дисков на радиусах 5 и 24 мм в трех полях.
Испытание ПЭО-покрытий с целью определения когезионной/адгезионной прочности и механизма разрушения проводили на скретч-тестере “REVETEST” (CSM Instruments, Швейцария) [27]. Царапание поверхности ПЭО-покрытий проводили алмазным конусным индентором (радиус закругления 200 мкм), двигающемся с заданной линейной скоростью (70 мм/мин) под нарастающей нормальной нагрузкой (1.0–71.0 Н). Критические нагрузки, вызвавшие когезионное/адгезионное разрушение, определяли при сопоставлении зависимости от приложенной нагрузки сигнала датчиков (силы трения, акустической эмиссии, глубины вдавливания) и изображений участков царапины.
Механические свойства (твердость и модуль упругости) ПЭО-покрытий определяли методом измерительного индентирования на нанотвердомере “Nano-HardnessTester” (CSM Instruments, Швейцария) [27] на поперечных косых шлифах. Использовали трехгранную алмазную пирамидку Берковича при максимальной нагрузке 10 мН. Трибологические испытания покрытий по схеме “стержень–диск” проводили методом измерительного скольжения с целью определения коэффициента трения и расчета износа на машине трения “Tribometer” (CSM Instruments, Швейцария) [27]. Контртелом служил неподвижно закрепленный на конце стержня шарик диаметром 3 мм из карбида кремния. При испытаниях пятно контакта находилось под слоем водопроводной воды. Приложенная к контртелу нагрузка составляла 5 Н. При вращении образца линейная скорость составляла 0.16 м/с. Длина пробега – 5000 м на радиусе дорожки износа – 24.7 мм. Количественно износостойкость оценивали после испытания по результатам измерений геометрии бороздки износа на образце и пятна износа на сферическом контртеле, как описано в [27]. Диаметр пятна износа на контртеле измеряли на оптическом микроскопе “Axiovert 25” (Zeiss), площадь сечения бороздок износа для последующего расчета приведенного износа определяли на оптическом профилометре.
РЕЗУЛЬТАТЫ И ИХ ОБСУЖДЕНИЕ
В поперечном сечении ПЭО-покрытия (рис. 1а–1г) состоят из пористой приповерхностной области (~10 мкм) с характерными расслойными трещинами и относительно плотной внутренней области (~30 мкм). Такая неоднородная (композитная) структура согласно результатам МРСА коррелирует с изменением химического состава по толщине покрытия (рис. 1д, 1е).
Рис. 1.
Микроструктура поперечного сечения ПЭО покрытия (а, б, в, г) и изменение содержания элементов по толщине ПЭО покрытия (д, е) сплава Д16 Т (а, в, д) и В95 Т1 (б, г, е).
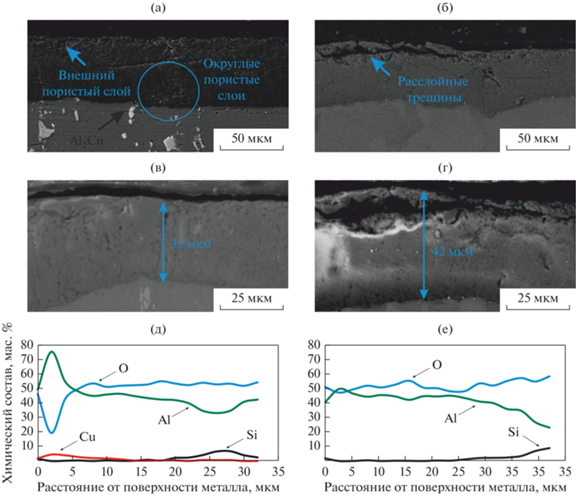
В толще ПЭО-покрытия сохраняется практически равномерное распределение алюминия и кислорода, однако вблизи поверхности покрытия содержание алюминия снижается, и значительно возрастает содержание кремния, который входит в состав электролита. Увеличенное содержание кремния способствует образованию более хрупкого оксида кремния, что приводит к появлению трещин между слоями оксида алюминия и оксида кремния (скорее всего, в процессе механического воздействия при приготовлении шлифа).
В тоже время результаты микроструктурных исследований покрытий, сформированных на различных алюминиевых подложках, показывают существенные отличия. Так, общая толщина сформированного оксидного слоя на сплаве Д16 Т отличается разноразмерностью и находится в диапазоне 32–50 мкм, а на сплаве В95 Т1 толщина ПЭО покрытия составляет около 42 мкм.
Особенностью покрытия, формируемого на сплаве Д16 Т, является образование внутренних округлых пористых зон (рис. 1а) вблизи структурных составляющих подложки – частиц фазы Al2Cu, которые, согласно источникам [25, 26], являются наиболее активными местами для возникновения плазменных разрядов и претерпевают дальнейшее растворение в покрытии под их действием. Это наглядно подтверждается результатами МРСА, на рис. 1д прослеживается значительное растворение меди в слое покрытия, прилегающего к подложке.
При этом в случае выбранных для исследования сплавов, можно полагать, что различие по содержанию меди оказывает существенное влияние на процесс формирования, структуру и морфологию покрытия, за счет значительного растворения Cu в покрытии. Что касается различий по содержанию Zn и Mg, то они оказывают дополнительный эффект [21], для выявления которого необходимы более тонкие методы исследования. Содержание легирующих компонентов сплава в ПЭО-покрытии приведено в табл. 2.
Таблица 2.
Содержание легирующих компонентов сплава в ПЭО покрытии
Сплав | Концентрация, ат. % | ||
---|---|---|---|
Cu | Mg | Zn | |
Д16 Т | 1.65 | 0.85 | 0.1 |
В95 Т1 | 0.34 | 0.95 | 1.73 |
Также, помимо различимых внутренних дефектов покрытия, сформированного на сплаве Д16 Т, следует отметить повышенную глубину и диаметр открытых пор, выявляемых в процессе анализа поверхности покрытия (табл. 3), по сравнению с покрытием на сплаве В95 Т1. Это может быть связано с различной толщиной покрытия и кинетическими особенностями его формирования. Причем, на периферийных участках глубина и диаметр пор повышаются по сравнению с центральной областью.
Таблица 3.
Средние размеры поверхностных пор по радиусу образцов-дисков по данным оптической профилометрии
Образец (радиус) | Глубина, мкм | Диаметр, мкм |
---|---|---|
Д16 Т (5 мм) | 17.4 ± 2.3 | 81.7 ± 7.3 |
Д16 Т (24 мм) | 37.2 ± 4.3 | 164 ± 21 |
В95 Т1 (5 мм) | 4.2 ± 1.8 | 73.2 ± 8.8 |
В95 Т1 (24 мм) | 11.2 ± 2.2 | 78 ± 11 |
Таким образом, общий вид структуры, морфология и сплошность покрытия в значительной мере зависят от химического и фазового состава подложки.
Выявленные различия отражаются как на прочностных свойствах, так и на износостойкости покрытий. При рассмотрении результатов измерительного царапания видна заметная разница (табл. 4) между нагрузкой для когезионного и адгезионного разрушения, которые наступают последовательно при увеличении нормальной нагрузки. Первые следы когезионного разрушения в виде единичных сколов на дне или по берегам царапины свидетельствуют о неоднородности структуры или контактах индентора со случайным дефектом. Такой характер разрушения иллюстрирует рис. 2, на котором видны сколы, а также признаки неоднородной деформации (ступеньки) на дне царапины. В данном случае критическая нагрузка когезионного разрушения (когезионная прочность) соответствует стойкости покрытия к тангенциальному скалыванию.
Таблица 4.
Критическая нагрузка стадий разрушения ПЭО-покрытий на разных подложках
Подложка | Когезионная прочность, Н | Адгезионная прочность, Н |
---|---|---|
Д16 Т | 14.5 ± 0.9 | 49 ± 3.4 |
В95 Т1 | 16 ± 1 | 63 ± 4.4 |
При дальнейшем увеличении нагрузки происходит адгезионное разрушение ПЭО-покрытия, которое сопровождается резким проломом покрытия вплоть до основы в диапазоне нагрузок 49–63 Н, о чем свидетельствует резкое изменение глубины погружения индентора. Адгезионное разрушение покрытия образцов с основой из сплава В95 Т1 происходит при нагрузке 63.0 ± 4.4 Н, что значительно выше прочности ПЭО-покрытий на образцах сплава Д16 Т, которые разрушаются при нагрузке 49.0 ± 3.4 Н.
Как видно на рис. 3, по данным измерительного избирательного индентирования зависимость значений твердости и модуля Юнга от расстояния от поверхности носит волнообразный характер, что скорее всего связано с локальной неоднородностью структуры покрытия или его дефектами. Вблизи границы раздела практически для всех образцов наблюдается скачкообразное понижение механических свойств.
Рис. 3.
Распределение твердости () и модуля упругости (■) по толщине ПЭО-покрытия на сплавах Д16 Т (а) и В95 Т1 (б).
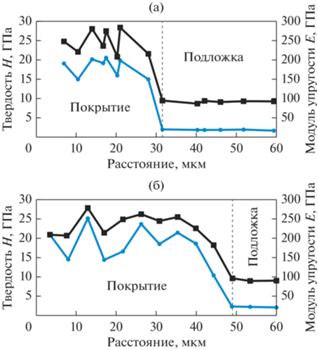
Наибольшее значение твердости 25 ГПа найдено у ПЭО-покрытия на сплаве В95 Т1, для покрытий на сплаве Д16 Т наибольшее значение твердости составляет около 20 ГПа. Для алюминиевой основы все образцы показали значения твердости в диапазоне 1.7–2.3 ГПа. Усредненные по всей толщине ПЭО-покрытий значения механических свойств приведены в табл. 5. Видно, что разница в средних значениях твердости (Нср) и модуля упругости (Еср) меньше, чем погрешность измерений (ΔН, ΔЕ).
Таблица 5.
Механические свойства, усредненные по толщине ПЭО покрытий
Подложка | Твердость, ГПа | Модуль Юнга, ГПа | ||
---|---|---|---|---|
Нср | Δ Н | Еср | ΔЕ | |
Д16 Т | 18.1 | 3.5 | 247 | 31 |
В95 Т1 | 19.5 | 5.5 | 239 | 40 |
При трибологических испытаниях для покрытий на обеих подложках наблюдается приработка контактирующих поверхностей на первых десятках метров пробега (рис. 4). На этой стадии наблюдается максимальное значения коэффициента трения (к.т.) за все испытание, после чего к.т. опускается до значений ниже 0.1. Наименьшим установившимся к.т. (0.036) и наименьшим приведенным износом (1.09 × 10–7 мм3/Н/м) обладает образец покрытия на сплаве В95 Т1. Наибольший износ (4.81 × 10–7 мм3/Н/м) у образца покрытия на сплаве Д16 Т (табл. 6).
Рис. 4.
Экспериментальные зависимости коэффициента трения от пробега для ПЭО покрытий на подложках Д16 Т и В95 Т1.
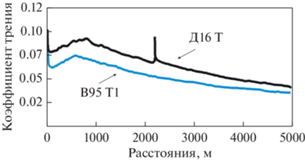
Таблица 6.
Трибологические характеристики исследованных ПЭО-покрытий на разных подложках
Подложка | Приведенный износ, 10–7 мм3/Н/м | Коэффициент трения | ||||
---|---|---|---|---|---|---|
образца | контртела | начальный | максимальный | средний | конечный | |
Д16 Т | 4.807 | 0.708 | 0.169 | 0.169 | 0.062 | 0.038 |
В95 Т1 | 1.086 | 0.540 | 0.099 | 0.102 | 0.050 | 0.036 |
Эти результаты согласуются с данными по микроструктуре ПЭО-покрытий (рис. 1): покрытия на В95 Т1 имеют гладкую трибологическую кривую, а на кривой для покрытий на Д16 Т заметны колебания значений коэффициента трения, в том числе резкий всплеск. Вероятно, эти отличия связаны с локальным когезионным разрушением при испытаниях.
ЗАКЛЮЧЕНИЕ
С применением прецизионных методов исследований проведен сравнительный анализ структуры и свойств функциональных покрытий, сформированных на поверхности алюминиевых сплавов В95 Т1 и Д16 Т методом плазменно-электролитического оксидирования (ПЭО), и сделаны следующие выводы:
1. Формируемые покрытия имеют дефекты двух типов: округлые пористые зоны вблизи металлической основы и расслойные трещины вблизи поверхности. Образование округлых пористых зон в покрытии увеличивается с повышением содержания меди в сплаве, что выражено на образцах из сплава Д16 Т.
2. Формируемое при одинаковых режимах ПЭО покрытие на подложке сплава В95 Т1 отличается большей однородностью по структуре и толщине оксидного слоя, содержит меньше дефектов.
3. С точки зрения адгезионной прочности лучшими являются ПЭО-покрытия на сплаве В95 Т1 (63.0 ± 4.4 Н), покрытия на сплаве Д16 Т разрушаются при значительно меньшей нагрузке (49.0 ± 3.4 Н).
4. Изменение твердости по сечению ПЭО-покрытия носит волнообразный характер. Наибольшее значение твердости 25 ГПа показало покрытие на сплаве В95 Т1, а наименьшее 20 ГПа на сплаве Д16 Т, однако разница в средних значениях твердости и модуля упругости меньше, чем погрешность их измерений.
5. Все образцы выдержали трибологические испытания под водой с сохранением ПЭО слоев до окончания испытания. Наименьшим установившимся коэффициентом трения (0.036) и наименьшим приведенным износом (1.09 × 10–7 мм3/Н/м) обладает покрытие на образце из сплава В95 Т1. Приведенный износ покрытия на образце сплава Д16 Т составил 4.81 × 10–7 мм3/Н/м, что в 4.4 раза выше, чем для ПЭО покрытия на сплаве В95 Т1.
Исследование выполнено при финансовой поддержке Московского Политехнического Университета в рамках программы грантов им. П.Л. Капицы (подготовка сплавов с ПЭО покрытием, микроструктурный анализ (СЭМ, МРСА)), а также Министерства науки и высшего образования Российской Федерации (проект № 0718‑2020‑0034) (in-situ изучение механизмов деформации и разрушения покрытий).
Список литературы
Sabitini G., Leschini L., Martini C., William J.A., Hutchings I.M. Improving sliding and abrasive wear behavior of cast A356 and wrought AA7075 aluminum alloys by plasma electrolytic oxidation // Mater. Des. 2010. V. 31. P. 816–828.
Liu C., Wang Q., Cao X., Cha L., Ye R., Ramachandran C.S. Significance of plasma electrolytic oxidation treatment on corrosion and sliding wear performances of selective laser melted AlSi10Mg alloy // Mater. Characteriz. 2021. V. 181. P. 111479.
Krishna L.R., Purnima A.S., Wasekar N.P., Sundararajan G. Kinetics and properties of micro arc oxidation coatings deposited on commercial Al alloys // Metall. Mater. Trans. 2007. V. 38. P. 370–378.
Muhaffel F., Baydogan M., Cimenoglu H. A study to enhance the mechanical durability of the MAO coating fabricated on the 7075 Al alloy for wear-related high temperature applications // Surface & Coatings Techn. 2021. V. 409. P. 126843.
Agureev L., Savushkina S., Ashmarin A., Borisov A., Apelfeld A., Anikin K., Tkachenko N., Gerasimov M., Shcherbakov A., Ignatenko V., Bogdashkina N. Study of Plasma Electrolytic Oxidation Coatings on Aluminum Composites // Metals. 2018. V. 8. P. 459.
Шатров А.С., Кокарев В.Н. Высокоэффективные легкие погружные многоступенчатые электроцентробежные насосы для добычи нефти в осложненных условиях // Нефтегазовые технологии и аналитика. 2018. № 2. С. 14–22.
Шатров А.С., Кокарев В.Н. Новая технология промышленного производства износостойких деталей трубопроводной арматуры из алюминиевых сплавов с защитным керамическим наноструктурным покрытием // Вестник арматурщика. 2014. № 6(19). С. 48–50.
Wang P., Wu T., Xiao Y.T., Zhang L., Pu J., Cao W.J., Zhong X.M. Characterization of micro-arc oxidation coatings on aluminum drill pipes at different current density // Vacuum. 2017. V. 142. P. 21–28.
Akopyan T.K., Gamin Y.V., Galkin S.P., Prosviryakov A.S., Aleshchenko A.S., Noshin M.A., Koshmin A.N., Fomin A.V. Radial-shear rolling of high-strength aluminum alloys: Finite element simulation and analysis of microstructure and mechanical properties // Mater. Sci. Eng. A. 2020. V. 786. P. 139 424.
Akopyan T.K., Belov N.A. Approaches to the design of the new high-strength casting aluminum alloys of 7xxx series with high iron content // Non-ferrous Metals. 2016. № 1. P. 20–27.
Sun L., Guo Y., Chen L., Zhao G. Effects of solution and aging treatments on the microstructure and mechanical properties of cold rolled 2024 Al alloy sheet // JMR&T. 2021. V. 21. P. 1126–1142.
Ракоч А.Г., Гладкова А.А., Дуб А.В. Плазменно-электролитическая обработка алюминиевых и титановых сплавов. М.: Издательский Дом “МИСиС”, 2017. 160 с.
Markov M.A., Bykova A.D., Krasikov A.V., Farmakovskii B.V., Gerashchenkov D.A. Formation of Wear- and Corrosion-Resistant Coatings by the Microarc Oxidation of Aluminum // Refract. Ind. Ceram. 2018. V. 59. P. 207–214.
Rakoch A.G., Khabibullina Z.V., Volkova O.V., Borko A.V, Van Tuan T., Suminov I.V., Zhukov S.V. Influence of current density and duration of PET of AA2024 alloy on the rate and growth mechanisms of a coating’s wear-resistant anticorrosive inner layer // Int. J. Corros. Scale Inhib. 2021. V. 10. P. 1621–1637.
Gulec A.E., Gencer Y., Tarakci M. The characterization of oxide based ceramic coating synthesized on Al–Si binary alloys by microarc oxidation // Surf. Coating. Technol. 2015. V. 269. P. 100–107.
Gencer Y., Gulec A.E. The effect of Zn on the microarc oxidation coating behavior of synthetic Al–Zn binary alloys // J. Alloys Compd. 2012. V. 525. P. 159–165.
Cengiz S., Tarakci M., Gencer Y., Devecili A.O., Azakli Y. Oxide based ceramic coating on Al–4Cu alloy by microarc oxidation // Acta Phys. Pol. A. 2013. V. 123. P. 445–448.
Tarakci M. Plasma electrolytic oxidation coating of synthetic Al–Mg binary alloys // Mater. Char. 2011. V. 62. P. 1214–1221.
Gencer Y., Tarakci M., Gulec A.E., Oter Z.C. Plasma electrolytic oxidation of binary Al-Sn alloys // Acta Phys. Pol. A. 2014. V. 125. P. 659–663.
Cengiz S. Synthesis of eutectic Al–18Ce alloy and effect of cerium on the PEO coating growth // Materials Chemistry and Physics. 2020. V. 247. P. 122897.
Oh Y.-J., Mun J.-I., Kim J.-H. Effects of alloying elements on microstructure and protective properties of Al2O3 coatings formed on aluminum alloy substrates by plasma electrolysis // Surface & Coatings Technology. 2009. V. 204. P. 141–148.
Tillous K., Toll-Duchanoy T., Bauer-Grosse E., Hericher L., Geandier G. Microstructure and phase composition of microarc oxidation surface layers formed on aluminium and its alloys 2214-T6 and 7050-T4 // Surface & Coatings Technology. 2009. V. 203. P. 2969–2973.
Venugopal A., Srinath J., Rama Krishna L., Ramesh Narayanan P., Sharma S.C., Venkitakrishnan P.V. Corrosion and nanomechanical behaviors of plasma electrolytic oxidation coated AA7020-T6 aluminum alloy // Mater. Sci. Eng., A. 2016. V. 660. P. 39-46.
Arunnellaiappan T., Kishore babu N., Rama Krishna L., Ramesh Babu N. Influence of frequency and duty cycle on microstrure of plasma electrolytic oxidized AA7075 and the correlation to its corrosion behavior // Surf. Coat. Technol. 2015. V. 280. P. 136–147.
Wu T., Blawerta C., Zheludkevich M.L. Influence of secondary phases of AlSi9Cu3 alloy on the plasma electrolytic oxidation coating formation process // J. Mater. Sci. & Techn. 2020. V. 50. P. 75–85.
Veys-Renaux D., Rocca E. Initial stages of multi-phased aluminium alloys anodizing by MAO: micro-arc conditions and electrochemical behavior // J. Solid State Electrochem. 2015. V. 19. P. 3121–3129.
Петржик М.И., Левашов Е.А. Современные методы изучения функциональных поверхностей перспективных материалов в условиях механического контакта // Кристаллография. 2007. Т. 52. № 6. С. 1002–1010.
Дополнительные материалы отсутствуют.
Инструменты
Физика металлов и металловедение