Физика металлов и металловедение, 2023, T. 124, № 3, стр. 330-336
Моделирование прокатки в магнитострикционном сплаве Fe–Ga
В. А. Милютин a, *, С. О. Непряхин b, И. В. Гервасьева a
a Институт физики металлов УрО РАН
620990 Екатеринбург, ул. С. Ковалевской, 18, Россия
b Уральский Федеральный Университет им. Б.Н. Ельцина
620002 Екатеринбург, ул. Мира, 19, Россия
* E-mail: v.a.milutin@gmail.com
Поступила в редакцию 03.11.2022
После доработки 21.12.2022
Принята к публикации 30.12.2022
- EDN: CMGUXI
- DOI: 10.31857/S0015323022601635
Аннотация
На основе измеренных физических свойств сплава Fe–Ga установлено, что уменьшение толщины материала до 0.3 мм приводит к приемлемому уровню потерь на вихревые токи при высокочастотном перемагничивании (20 кГц). Разработаны рекомендации по выбору режимов прокатки для достижения требуемой толщины. Реализовано моделирование прокатки по предложенному режиму, получены распределения деформации, напряжений и температуры для каждого прохода. Полученные результаты проанализированы в контексте связи особенностей деформации с процессами образования кристаллографической текстуры.
1. ВВЕДЕНИЕ
Деформация прокаткой является одним из основных технологических процессов при изготовлении листов из магнитомягких сплавов. Наиболее ярким примером является электротехническая сталь (сплав железа с кремнием в количестве до 6.5 мас. %). Данный материал производят в форме тонких листов, получаемых путем прокатки и серии отжигов различного назначения. Готовое изделие представляет собой конструкцию, набранную из большого количества вырубленных листов заданного размера и формы. Друг от друга листы отделяют электроизоляционным слоем. Такая конструкция позволяет существенно снизить магнитные потери при перемагничивании в ходе эксплуатации изделия.
Аналогичный подход используется и для магнитомягких сплавов другого назначения, в частности, магнитострикционных. Материалы с повышенной магнитострикцией находят применение в широком спектре электротехнических приложений, таких как прецизионные приводящие устройства, датчики различного назначения, преобразователи звука и ультразвука. Многие из этих устройств работают в условиях высокочастотного перемагничивания, например, для генерации ультразвука необходимы частоты в районе 20 кГц и выше. Снижение потерь через контроль толщины листа в этом случае становится особенно актуальным, поскольку при повышении частот, вихретоковая составляющая магнитных потерь начинает доминировать над гистерезисной [1]. Традиционными магнитострикционными материалами являются чистый никель, а также сплавы на основе железа: Fe–Co, Fe–Al, Fe–Dy–Tb. Однако в последние годы в качестве их перспективной замены рассматривается сплав Fe–Ga (наиболее распространенным составом является Fe81Ga19), который, с одной стороны, обладает более высокой магнитострикцией чем традиционные Ni, Fe–Al и Fe–Co, а, с другой, гораздо более низкой стоимостью и лучшими механическими свойствами по сравнению с Fe–Dy–Tb [2]. Необходимо отметить, что задача прокатки состоит не только в уменьшении толщины листа. В сочетании с термообработкой она призвана создать определенную кристаллографическую текстуру, благоприятную с точки зрения функциональных свойств. В случае Fe–Ga такой текстурой является $\left\langle {100} \right\rangle $ // НП (направление прокатки), при которой достигается максимальная величина магнитострикции. Однако создание текстуры такого типа в сплаве с ОЦК-решеткой (каким является состав Fe81Ga19) – достаточно сложная задача. Работа в этом направлении активно ведется последние годы [3, 4]. Кристаллографическая текстура в первую очередь зависит от особенностей самого материала, таких как тип кристаллографической решетки, действующие системы скольжения, энергия дефектов упаковки и др. Важную роль играют также условия прокатки, такие как степень и скорость деформации, температура и т.д. Более того, из-за неравномерного распределения деформации и температуры (в случае горячей или теплой прокатки) в объеме листа конечная текстура в различных слоях может существенно отличаться.
В данном контексте серьезной проблемой является склонность сплава к хрупкому разрушению при холодной прокатке [5], что существенно осложняет деформацию и сужает возможности варьирования режимов прокатки. Таким образом, при прокатке сплава Fe–Ga необходимо одновременно решать две задачи: избегать разрушения листа в ходе деформации и создавать необходимую преимущественную ориентировку зерен.
Целью настоящей работы является разработка режима прокатки, который мог бы привести к требуемому уровню функциональных характеристик сплава Fe–Ga и при этом исключить разрушение листа в ходе деформации. Для этого планируется подобрать подходящие параметры прокатки и реализовать анализ распределения напряжений, деформации и температуры в ходе прокатки по выбранному режиму.
С точки зрения формирования текстуры наиболее важным является финальный этап прокатки листа, осуществляемый либо при температуре окружающей среды (холодная прокатка), либо с небольшим подогревом (теплая прокатка). В случае Fe–Ga это также технологически наиболее проблематичная стадия из-за низкой пластичности сплава. По этой причине в работе исследуется именно заключительная стадия прокатки. Исходные параметры, используемые для моделирования, соответствуют реальному составу и образцам, которые в дальнейшем планируется подвергнуть экспериментальным исследованиям для проверки и оптимизации модели. Эти результаты необходимы не только для разработки оптимальных режимов прокатки, но и для более детального анализа особенностей формирования кристаллографической текстуры в прокатанных листах из сплава Fe–Ga.
2. МЕТОДИКА И МАТЕРИАЛЫ
Объектом исследования выступает классический сплав Fe81Ga19. Для экспериментального измерения основных свойств был выплавлен слиток указанного состава методом электродуговой плавки в защитной атмосфере аргона. Для этого были использованы высокочистые элементы Fe (99.95%), Ga (99.9999%). Слиток, представляющий собой стержень диаметром 10 мм и длиной около 50 мм, был отлит в медную изложницу. Плотность определяли с помощью метода гелиевой пикнометрии (AccuPyc II 1340). Измерения электросопротивления проводили на вырезанных из слитков дисках, толщиной 1 мм с использованием четырехконтактного метода (Mitsubishi Loresta AX). Затем слиток был разрезан на несколько частей для последующей деформации.
Оценку вихретоковой составляющей магнитных потерь осуществляли с помощью формулы [6]:
где B – максимальное значение магнитного поля, d – толщина листа, f – частота перемагничивания, ρ – электрическое сопротивление материала, D – плотность.Расчет температурных полей и напряженно-деформированного состояния прокатываемого металла был реализован с использованием программного комплекса “Deform-3D”. Материал валков приняли абсолютно жестким. Условия контактного взаимодействия трения принимали по Зибелю с показателем трения ψ = 1. Коэффициент теплопередачи между объектами во время деформации k = 5, во время перехода от одного прохода к другому k = 1. Окружающую температуру принимали равной t = 20°C. Методом решения температурной задачи является прямой метод разряжения. Критерием остановки решения является количество заданных шагов. Чаще всего для одного прохода использовали 1000–2000 шагов с затратой времени 0.01–0.001 с/шаг. Через каждые 10 шагов осуществляли сохранение результатов расчета: температуры и напряженно-деформированного состояния. На последнем подготовительном этапе выполняли проверку составленной базы. В случае полноты и правильности подготовленных данных генерировали базу и приступали к решению задачи в основном модуле программы. При моделировании процесса прокатки в первом проходе использовали созданную ранее твердотельную модель заготовки с конечно-элементной сеткой и температурой 350°C, одинаковой по длине и всему объему.
3. РЕЗУЛЬТАТЫ
3.1. Исходные данные и параметры моделирования
Прежде всего необходимо установить минимальную толщину листов Fe–Ga, которая требуется для существенного снижения магнитных потерь. Это можно сделать по формуле (1), для чего требуются информация об электросопротивлении и плотности сплава. По результатам измерений установлено, что сплав Fe81Ga19, используемый в данной работе, имеет достаточно высокое электросопротивление: 110.7 ± 11.3 мкОм см. Для сравнения, электросопротивление чистого железа – примерно 10 мкОм см, сплава Fe–6.5 мас. % Si – около 80 мкОм см. На микроуровне, при содержании галлия примерно до 20 ат. % сплав Fe–Ga сохраняет решетку α-Fe и является неупорядоченным твердым раствором замещения, в котором часть атомов железа замещена атомами галлия [2]. Именно это и является причиной значительного роста электросопротивления. Дело в том, что атомы галлия имеют заметно больший металлический радиус (139.2 пм), чем атомы железа (124.1 пм). Замещение такого большого количества атомов приводит к существенным искажениям кристаллографической решетки и, как следствие, уменьшению длины свободного пробега электронов. Это, в свою очередь, повышает электросопротивление [7]. Следует отметить, что на наноуровне в данном сплаве могут присутствовать упорядоченные нанокластеры, тип упорядочения и количество которых зависят от состава сплава и термообработки [8]. Однако из-за их малого количества и размера, можно считать, что их влияние на электросопротивление минимально.
Измеренная величина плотности сплава составила 7.86 г/см3. Известно, что для достижения технического насыщения магнитострикции в сплаве требуются относительно невысокие магнитные поля (около 16 000 А/м). Если подставить все указанные значения в формулу (1) то для работы при частоте 20 кГц приемлемая величина потерь на вихревые токи (<20 Вт/кг) может быть достигнута при толщине листов не больше 0.3 мм. Разумеется, дальнейшее снижение толщины будет позитивно сказываться на вихретоковой составляющей магнитных потерь, однако, во-первых, это будет приводить к росту гистерезисных потерь [9], а, во-вторых, получение сверхтонких листов – сложная техническая задача, особенно в случае материала с ограниченной пластичностью. Поэтому в качестве конечной толщины листов при моделировании прокатки мы выбрали значение 0.3 мм. Известно, что средние степени обжатия (60–70%) при прокатке Fe–Ga оказывают благоприятное воздействие на формирование $\left\langle {100} \right\rangle $ // НП текстуры [3], поэтому в качестве исходных объектов выбраны листы толщиной 1 мм, чтобы обеспечить необходимую степень деформации. Такие заготовки могут быть успешно получены путем ковки и горячей прокатки при 1000°С, что и было сделано в настоящей работе.
Таким образом, для моделирования выбраны образцы прямоугольной формы размерами 50 × × 20 × 1 мм, которые могут быть вырезаны из полученных заготовок. Разумеется, для прокатки в заводских условиях такие заготовки слишком маленькие, но на данном этапе целью является моделирование прокатки именно в лабораторных условиях для того, чтобы в дальнейшем реализовать экспериментальную валидацию модели. Еще одним ключевым параметром прокатки является степень деформации за один проход и, как следствие, суммарное количество проходов. Этот параметр был подобран с учетом механических свойств сплава Fe–Ga [10], а также предыдущего опыта его прокатки. В данном случае необходимо соблюдать определенный баланс. Слишком большая деформация за проход с высокой долей вероятности приведет к разрушению. Например, в случае абсолютной деформации за проход 0.07 мм, к концу прокатки относительное обжатие возрастает практически до 20% что, судя по диаграмме сжатия [10], уже может привести к разрушению. С другой стороны, технически достаточно сложно реализовать равномерное уменьшение зазора между валками на очень маленькую величину в случае малого обжатия за проход. Поэтому мы остановились на 14 проходах с обжатием за проход 0.05 мм. В табл. 1 приведены условия процесса прокатки, которые использовались при моделировании.
Таблица 1.
Параметры прокатки при моделировании
Параметр | Значение |
---|---|
Размер образцов, мм | 50 × 20 × 1 |
Суммарная степень деформации, % | 70 |
Температура прокатки, °C | 350 |
Диаметр валков, мм | 58 |
Количество проходов деформации | 14 |
Абсолютная деформация за проход, мм | 0.05 |
Частота вращения валков, об./мин | 15 |
В связи с тем, что в стандартной библиотеке материалов программного комплекса “Deform-3D” отсутствует сплав Fe–Ga, необходимо создать новую базу материала на основе имеющихся опытных данных. За основу для построения кривых упрочнения были взяты диаграммы, полученные ранее в результате проведения испытаний на сжатие при повышенных температурах [10]. Для моделирования распределения температуры при теплой прокатке использован коэффициент теплопроводности 17.5 Вт/(м К).
3.2. Результаты моделирования
Результаты расчетов представлены в виде цветовых эпюр: температуры в плоскости листа и в поперечном сечении полосы; изменения σхх – компоненты тензора напряжений, показывающей распределение напряжений в очаге деформации при прокатке вдоль направления прокатки (напряженное состояние). Деформированное состояние характеризовали через εхх – компоненту тензора деформации, показывающую распределение деформаций вдоль направления прокатки. Схема расположения листа и главные направления обозначены на рис. 1.
В ходе моделирования были получены распределения напряжений для каждого прохода деформации. Наиболее важной проекцией в данном случае является плоскость листа. В первую очередь это связано с тем, что из-за знакопеременных деформаций именно на поверхности листа образуются мезоструктурные неоднородности (так называемые полосы деформации и сдвига), которые часто оказывают ключевое влияние на образование кристаллографической текстуры. Построение распределения напряжений и их анализ позволяют продвинуться в понимании закономерностей формирования мезоструктурных неоднородностей и, как следствие, текстуры в сплаве Fe–Ga. Кроме того, на поверхности листа при достижении критического напряжения, превышающего предел прочности материала, могут зарождаться трещины, приводящие к его разрушению. Анализ таких распределений позволяет оценить риск разрушения листа при прокатке. В качестве примера на рис. 2 приведено подобное распределение для пятого прохода (уменьшение толщины с 0.8 до 0.75 мм) прокатки.
Рис. 2.
Распределение напряжений на поверхности листа при прокатке с 0.8 до 0.75 мм с указанием очага деформации (области, которая в данный момент времени находится между валками).
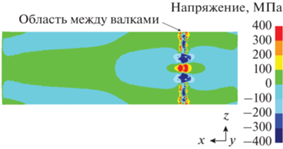
Контроль распределения деформации по толщине листа (рис. 3) также важен для анализа особенностей формирования текстуры. Во-первых, в случае существенных различий по степени деформации в разных участках листа будет иметь место неоднородность текстуры деформации. Во-вторых, процесс рекристаллизации при следующим за деформацией отжиге начинается неравномерно в объеме листа, в зависимости, в том числе, от степени деформации в конкретном участке. Все это оказывает влияние на конечную текстуру. Величина деформации, указанная на рисунке, это одна из составляющих тензора деформации, которая, по сути, является удлинением вдоль оси x (оси прокатки) отрезка бесконечно малой длины при заданной высотной деформации (0.05 мм в каждом проходе). Из рис. 3 видно, что деформация после первого прохода прокатки практически равномерна, тогда как к четырнадцатому проходу накапливаются заметные (около 5%) неоднородности.
4. ОБСУЖДЕНИЕ РЕЗУЛЬТАТОВ
Полученные результаты моделирования проанализированы, главным образом, в контексте связи с процессами формирования текстуры, а кроме того, с точки зрения особенностей деформации.
4.1. Распределение температур
Обычно при деформации листовых магнитомягких материалов заключительным этапом является холодная прокатка. Однако в случае сплава Fe–Ga, который склонен к хрупкому разрушению, это часто приводит к растрескиванию заготовок при деформации. По этой причине предлагается использовать теплую прокатку при 350°С (нагрев перед первым проходом), поскольку, как известно, при данной температуре происходит существенное повышение пластичности сплава Fe–Ga [5]. Такой подход уже показал свою эффективность ранее [11]. По результатам моделирования уствновлено, что разница температур в разных частях листа при теплой прокатке составляет около 15°C. Такое различие не является значительным и, в данном случае, не может оказать существенного влияния на течение деформации и процессы формирования текстуры.
4.2. Распределение деформаций
Основной движущей силой первичной рекристаллизации является энергия, запасенная в ходе деформации. По объему материала ее накопление происходит неравномерно и зависит как от кристаллографической ориентировки конкретного участка структуры [12], так и степени деформации. После деформации сплава Fe–Ga по выбранному режиму существуют участки, степень деформации в которых отличается в пределах 5%. В свою очередь, различие по степени деформации в разных участках листа приводит к неоднородности распределения запасенной энергии деформации. Существуют различные теории относительно того, как именно количество запасенной энергии деформации коррелирует с процессом зародышеобразования при рекристаллизации [13]. В рамках одной из них считается, что рекристаллизация преимущественно начинается в участках, в которых уровень запасенной энергии выше, чем в соседних. Таким образом, владея информацией о распределении деформации, можно предсказать, в каких участках листа будет преимущественно происходить зарождение и рост новых зерен. Возможность более раннего начала рекристаллизации в одних участках с определенной кристаллографической ориентировкой может внести существенные изменения в процесс образования текстуры. Дело в том, что при отжиге рост зародышей рекристаллизации происходит за счет поглощения соседних областей, в которых рекристаллизация по определенным причинам еще не началась. Это оказывает определяющее влияние на конечную текстуру по всему объему листа. Возможный сценарий приоритетного роста зерен в листе Fe–Ga, подвергнутом прокатке по выбранному режиму, схематически показан на рис. 4.
4.3. Распределение напряжений
На примере ОЦК сплава Fe–Si давно известно, что в листовых монокристаллах, представляющих из себя однородный материал, вследствие неоднородности распределения напряжений при холодной прокатке возникают некие регулярно расположенные элементы мезоструктуры [14]. С точки зрения типа решетки и особенностей деформации данный материал практически полностью совпадает с Fe–Ga [15], поэтому накопленную информацию целесообразно использовать в данном случае. При прокатке плоского монокристалла Fe–Si (110) со степенью деформации 65–70% в направлении [001] в смежных полосах происходит поворот решетки в двух противоположных направлениях, в результате чего образуются полосы деформации (ПД). Они представляют собой веретенообразные области материала, вытянутые в направлении прокатки, которые отличаются друг от друга кристаллографической ориентировкой (рис. 5). Кроме полос деформации, можно выделить другие элементы мезоструктуры: переходные полосы (ПП) между двумя полосами деформации и полосы сдвига (ПС) внутри полосы деформации.
Из схемы на рис. 5 видно, что при малом перемещении по образцу прокатных валков (1 → 2) без изменения зазора между ними, в очаге деформации, в соответствии с его геометрией, существует вертикальный слой материала S, который испытывает по сравнению с соседними слоями наибольшее мгновенное приращение абсолютного обжатия Δh = h1 – h2. Слой, испытывающий большее обжатие, сильнее других течет в различных направлениях. Губернаторов назвал это гофрированием [16] металла в очаге деформации, вызванном стесненными условиями течения металла, что вызывает знакопеременные напряжения и заставляет соседние объемы поворачиваться в противоположные стороны [17]. Таким образом, образование мезоструктурных элементов зависит от распределения напряжений в листе. За годы исследований было показано, что мезоструктурные неоднородности играют ключевую роль при формировании текстуры в листах из различных сплавов. Стоит отметить, что помимо режима деформации и распределения напряжений, процессы формирования неоднородностей зависят от исходной ориентировки. Четко выраженные полосы деформации формируются не при всех исходных ориентировках монокристаллов. При прокатке плоских монокристаллов так называемых стабильных ориентировок ({100}$\left\langle {011} \right\rangle $, {111}$\left\langle {011} \right\rangle $ и {111}$\left\langle {112} \right\rangle $) исходная ориентировка не изменяется, а только рассеивается. Однако в [14] было показано, что и в этом случае на полированной поверхности металла возникает рельеф в поперечном и продольном направлении, и появляются регулярные знакопеременные колебания ориентировки. Разумеется, анализ образования мезоструктурных неоднородностей и их связь с образующейся текстурой в поликристаллических материалах гораздо более сложная задача. Проанализированное в настоящей работе знакопеременное распределение напряжений в плоскости листа Fe–Ga позволит в дальнейшем более детально исследовать данное явление и его связь с образованием текстуры в сплаве. Полученные распределения напряжений в каждом проходе прокатки в сочетании с экспериментальными исследованиями дадут возможность отследить всю историю образования мезостурктурных неоднородностей. В свою очередь, эта информация позволяет контролировать их формирование и, как следствие, итоговую кристаллографическую текстуру путем варьирования режимов прокатки.
Кроме того, несмотря на то что абсолютные величины напряжений, получаемые при моделировании, могут несколько отличаться от реальных, результаты позволяют сделать вывод о том, что при деформации по предложенному режиму в листах Fe–Ga не возникает участков, уровень напряжения в которых существенно превышает предел прочности материала. Таким образом, можно ожидать, что прокатка по предложенному режиму не будет приводить к растрескиванию образцов.
ЗАКЛЮЧЕНИЕ
В работе реализовано моделирование теплой прокатки сплава Fe–Ga при задании физически обоснованных параметров деформации. Показано, что листы толщиной 0.3 мм могут быть получены 70% деформацией за 14 последовательных проходов с абсолютной деформацией за проход 0.05 мм при температуре 350°C. Такой режим позволяет минимизировать риск растрескивания при прокатке, что в случае FeGa является критической проблемой. Полученные распределения напряжений и деформации позволят продвинуться в понимании процессов текстуробразования в данном материале. Результаты моделирования могут быть использованы для разработки технологи производства листов сплава Fe–Ga.
Работа выполнена при поддержке Гранта Президента Российской Федерации для молодых ученых – кандидатов наук (номер МК-344.2022.4) и в рамках государственного задания Министерства Науки и Высшего Образования Российской Федерации (Шифр “Магнит”, номер 122021000034-9).
Список литературы
Плотников С.М. Определение потерь на вихревые токи и на гистерезис в магнитопроводах электрических машин // Электромагнитные Измерения. 2020. № 11. С. 54–58.
Головин И.С., Палачева В.В., Мохамед А.К., Балагуров А.М. Структура и свойства Fe–Ga-сплавов – перспективных материалов для электроники // ФММ. 2020. Т. 121. С. 937–980.
Fu Q., Sha Y.H., Zhang F., Esling C., Zuo L. Correlative effect of critical parameters for η recrystallization texture development in rolled Fe81Ga19 sheet: Modeling and experiment // Acta Mater. 2019. V. 167. P. 167–180.
Гервасьева И.В., Милютин В.А. Образование текстуры при прокатке и первичной рекристаллизации в сплаве Fe86Ga14 // Письма о материалах. 2018. Т. 8. С. 341–345.
Li J.H., Gao X.X., Zhu J., Bao X.Q., Xia T., Zhang M.C. Ductility, texture and large magnetostriction of Fe–Ga-based sheets // Scr. Mater. 2010. V. 63. P. 246–249.
Fiorillo F. Soft Magnetic Materials. Elsevier Ser. Electromagn., Academic Press, San Diego, 2004. P. 25–88.
Sondheimer E.H. The mean free path of electrons in metals // Adv. Phys. 2001. V. 50. P. 499–537.
Черненков Ю.П., Ершов Н.В., Горностырев Ю.Н., Лукшина В.А., Смирнов О.П., Шишкин Д.А. Рентгеноструктурный анализ ближнего порядка в твердых растворах железо–галлий // ФММ. 2022. Т. 123. № 10. С. 1054–2022.
Плотников С.М. Определение потерь в стали и оптимизация толщины листов магнитопровода трансформатора // Энергетика. Изв. Высш. Учеб. Заведений и Энерг. Объединений СНГ. 2022. Т. 2. С. 115–126.
Cheng L.M., Nolting A.E., Voyzelle B., Galvani C. Deformation behavior of polycrystalline Galfenol at elevated temperatures // Behav. Mech. Multifunct. Compos. Mater. 2007. P. 65262N.
Мансури Я., Чеверикин В.В., Палачева В.В., Кошмин А.Н., Алещенко А.С., Астахов В.А., Дементьева О.Ю., Милютин В.А., Головин И.С. Текстура и магнитострикция сплава Fe–Ga после теплой прокатки и рекристаллизации // ФММ. 2021. Т. 122. С. 416–423.
Every R.L., Hatherly M. Oriented Nucleation in Low-Carbon Steels // Texture. 1974. V. 1. P. 183–194.
Kestens L.A.I., Pirgazi H. Texture formation in metal alloys with cubic crystal structures // Mater. Sci. Technol. 2016. V. 32. P. 1303–1315.
Taoka T., Furubayashi E., Takeuchi S. Formation of Cold-Rolled Texture and Recrystallized Texture in Single Crystals of 3% Silicon Iron // Trans. Nat. Research Inst. For Metals. 1967. V. 9. P. 155–207.
Na S.M., Smith M., Flatau A.B. Deformation Mechanism and Recrystallization Relationships in Galfenol Single Crystals: On the Origin of Goss and Cube Orientations // Metall. Mater. Trans. A Phys. Metall. Mater. Sci. 2018. V. 49. P. 2499–2512.
Gubernatorov V.V., Sokolov B.K., Gervasyeva I.V., Vladimirov L.R. About band structures formation in structure homogeneous materials under deformation // Phys. Mesomech. 1999. V. 2. P. 157–162.
Gubernatorov V.V., Sokolov B.K., Gervasyeva I.V., Vladimirov L.R. Corrugation of Metal at the Deformation Zone as a Cause of the Local Texture Inhomogeneity // Proc. Of the 12th Int. Conf. on Textures of Materials. Montreal. 1999. P. 742–747.
Дополнительные материалы отсутствуют.
Инструменты
Физика металлов и металловедение