Известия РАН. Энергетика, 2019, № 6, стр. 78-109
Демпферные системы защиты корпусов высоковольтного электрооборудования пористыми металлами
1 Объединенный институт высоких температур
Москва, Россия
2 Московский физико-технический институт
Москва, Россия
* E-mail: son.eduard@gmail.com
Поступила в редакцию 26.11.2019
После доработки 27.11.2019
Принята к публикации 28.11.2019
Аннотация
Статья посвящена применению пористых материалов для защиты корпусов оборудования, подверженных нагрузкам, приводящим к их разрушению. Рассматриваются различные варианты использования демпферных систем на базе пенометаллов и других пористых материалов для снижения нагрузки на корпуса высоковольтного оборудования, силовых маслонаполненных трансформаторов, мощных коммутаторов. Корпуса оборудования могут содержать газы, жидкости или смешанные газожидкостные системы при нормальном или высоком давлениях. Сверхкритические нагрузки могут создаваться при взрывах химических реакторов, а также вследствие коротких замыканий в высоковольтном оборудовании. Методы защиты корпусов пористыми материалами применяются в самых различных системах, таких как металлические корпуса в резервуарах высокого давления, подводных объектах и других устройствах. В ряде объектов создаются ударные волны, которые распространяются в газовой и конденсированных средах до ограничивающих их твердых деформируемых и/или разрушающихся стенках.
1. ВВЕДЕНИЕ
Начиная с 1990-х годов, пористые металлы (пенометаллы) находят все более широкое применение в различных отраслях промышленности в связи с тем, что они обладают комплексом эффективных свойств, таких как низкая масса, высокие удельные свойства, способность значительно поглощать шум, теплоту, энергию удара и др. Пенометаллы не засоряют фильтруемую жидкость продуктами фильтра, легко подвергаются механической обработке и сварке, допускают многократную регенерацию, обладают хорошей электропроводностью [1].
Методы защиты корпусов оборудования, содержащего энергоемкие газожидкостные среды при высоких давлениях, имеют важное значение в различных отраслях энергетики, а в частности, при защите высоковольтных трансформаторов от взрывов и пожаров [2]. Поэтому настоящей статьей мы хотели бы привлечь внимание специалистов других областей к возможным методам защиты энергоемкого оборудования. В данной работе представлены не только экспериментальные результаты и испытания опытных образцов трансформаторов, но и методы моделирования и тестирования устройств на основе расчетных программ и кодов как коммерческих специализированных, так и разработанных самостоятельно программ расчета возникновения и развития возмущений, конечных деформаций и разрушения систем. Методы моделирования пористых деформируемых систем до сих пор специально не рассматривались, поэтому в статье приведены теоретические обоснования и методы расчета динамических процессов в газо- и гидродинамических процессах, в различных системах, включая пористые материалы.
Среди пенометаллов особое место занимает пеноалюминий, обладающий многими замечательными технологическими и эксплуатационными свойствами. Пеноалюминий (пористый алюминий) – металл с закрытыми (открытыми) порами, получаемый методами литейной и порошковой технологии. Пеноалюминий обладает малой плотностью – от 0.4 до 1.0 г/см3, хорошими теплоизоляционными и звукопоглощающими свойствами и высокой прочностью. Кроме того, он имеет низкую электрическую и термическую проводимость по сравнению с алюминиевыми сплавами, может применяться в широком интервале температур и является негорючим материалом до температуры около 800°С. Пенометалл – металл или сплав ячеистого строения, состоит из тонких металлических оболочек, заполненных газом [4]. Пористый алюминий нашел применение в следующих областях: подготовка сжатого воздуха, фильтрация природного газа, масел и топлива, очистка горячих сред, аэрация жидкостей, системы пневмотранспорта, снижение шума пневматических устройств и т.д.
Пенометаллы производятся из расплавленных металлов путем впрыска (вдувания) газов (воздуха, инертных газов) либо путем стимулирования их местного образования введением газовыделяющего реактива (порофора), в качестве которого в основном используется гидрид титана (TiH2) и карбонат кальция (СаCO3). Существует технология получения пенометаллов из смеси порошкообразных сплавов и газвыделяющего реактива [1]. Свойства пенометаллов зависят от количества пузырьков газа и свойств исходного металла. Известны пенометаллы на основе алюминия, меди, нихрома, магния, стали и др. Пенометаллы используются в качестве наполнителей (для обеспечения жесткости конструкции), а также как теплоизолирующие материалы и т.п. [3]. Пенометалл обычно сохраняет часть физических характеристик исходного металла: например, пенометалл, изготовленный из негорючего металла, будет негорючим. Степень термического расширения при этом сохраняется, а теплопроводность уменьшается [1].
Пенометалл подходит для создания крупногабаритных прочных конструкций. Он способен обеспечить рациональные соотношения прочности и массы деталей машин. Пенометалл будет активно применяться в космических технологиях, где снижение массы имеет большое значение. Пенометаллы из алюминия, магния, стали, титана или цинка выдерживают высокое давление, приглушают звук, ослабляют вибрации, хорошо изолируют. Они легко поддаются механической обработке: сверлению, распиливанию и фрезерованию, поэтому они хорошо подходят для защиты от ударов в автомобилях, в качестве катализаторов в химии, в изготовлении топливных элементов, а также как биологически совместимый протез костной ткани в медицине [1]. В авиакосмической промышленности замена пенометаллическими панелями дорогостоящих сотовых конструкций может сократить издержки производства.
Широкое применение открывается в строительстве и для вспененных заготовок, возможно также создание конструктивных элементов с основой из пенометалла, покрытого слоями алюминия, стали, пластмассы или углеродных волокон. Эти технологии пригодны для производства крупных серий и полностью автоматизированы, что, например, разработано в Институте производственных технологий и прикладного материаловедения им. Фраунгофера в Бремене (Германия) [2].
2. ЭКСПЕРИМЕНТАЛЬНЫЕ ИССЛЕДОВАНИЯ СТАТИЧЕСКИХ И ДИНАМИЧЕСКИХ ХАРАКТЕРИСТИК ДЕФОРМИРОВАНИЯ И РАЗРУШЕНИЯ ДЕМПФИРУЮЩИХ МАТЕРИАЛОВ
При изучении прочности пористых металлических материалов, используемых в демпфирующих элементах, важной особенностью по сравнению с обычными металлами является необходимость исследования их поведения при значительных уровнях сжимающих деформаций. Из-за большого объема пор и более хаотичного характера их распределения в материале наблюдаются расширенные диапазоны отклонения механических свойств от их среднестатистических значений по сравнению с обычными металлами. Вследствие этого при проведении испытаний образцов из пористых материалов на сжатие при сравнительно небольших напряжениях (по сравнению с реальными элементами демпфирующих конструкций) с большой вероятностью может наступать потеря устойчивости деформирования, что затрудняет получение достоверных данных о механических свойствах. Такие особенности деформирования пористых материалов требуют их учета при проведении испытаний на сжатие образцов и при разработке оборудования для проведения прочностных испытаний.
Для получения достоверных и стабильных данных о прочностных свойствах пористых металлических материалов в условиях сжатия необходимо, чтобы испытываемые образцы имели достаточно большую площадь поперечного сечения, обеспечивающую малую величину рассеяния прочностных и деформационных свойств, по сравнению с обычными металлами. При этом системы нагружения и измерения нагрузки и деформации должны обеспечивать возможность нагружения и измерения нагрузки, продольных и поперечных деформаций, которые могут достигать больших величин (десятки процентов). Кроме того, необходимо иметь в виду, что система нагружения используемого оборудования в процессе испытании пористых материалов для предотвращения преждевременной потери устойчивости образцов должна содержать элементы, препятствующие возможности взаимного смещения их торцевых поверхностей в поперечном направлении даже в минимальной степени. Для проведения статических и динамических испытаний демпфирующих материалов использовалась универсальная испытательная машина TIRATEST 2300 и вертикальный копер ВК-7, которые вместе составляют экспериментальный стенд (Московский политехнический университет). В испытаниях на сжатие использовались образцы из пеноалюминия с закрытой пористостью, прямоугольной формы (h × а × b) на сжатие. Образец состоит из трех частей, которые склеены между собой эпоксидным клеем. Целью испытаний являлось определение физико-механических характеристик пеноалюминия различной плотности при статическом и динамическом сжатии при нормальной (Т = 23 ± 2°С) и повышенной (60 ± 2°С) температурах. Нагрузка на образце измерялась с помощью преобразователя сил, входящего в комплект испытательной машины. Погрешность измерения нагрузки составляла ±1% от измеряемой величины. В осевом направлении перемещения на образце измерялись по перемещению траверсы специальным датчиком, отслеживающим перемещения траверса. Погрешность измерения составляла ±2% от измеряемой величины. Перемещения на образце в поперечном направлении измерялись с помощью специального экстензометра, представляющего собой упругий элемент с наклеенными тензодатчиками. Температура на образце измерялась с помощью цифрового четырехканального измерителя температур АТТ-2004. В качестве датчика температуры использовалась ХА термопара. Перед испытаниями на образце закреплялся упругий элемент для измерения поперечной деформации, а затем вместе с ним помещался в специальное приспособление (рис. 1), которое устроено таким образом, что при сжатии верхняя и нижняя плоскости перемещаются параллельно и не сдвигаются друг относительно друга. Приспособление в сборе с образцом устанавливалось в испытательную машину, где и проводились испытания. Эксперименты проводились по программе сжатия со скоростью деформации 2–6 × 10–3. В качестве регистрирующей аппаратуры на машине TIRATEST-2300 использовалась модульная система сбора и обработки результатов Compact DAQ, (National Instruments). Параметры нагружения образцов и результаты испытаний записывались в памяти аппаратуры, частота измерения для каждого из датчиков составляла 10 измерений в секунду.
Рис. 1.
Общий вид приспособления для испытаний образцов на статическое (а) и динамическое (б) сжатия.
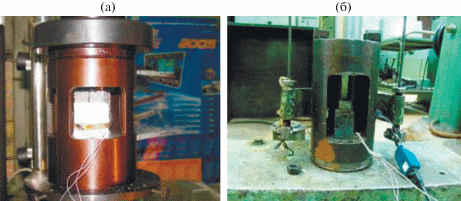
После статических испытаний с помощью штангенциркуля измерялись конечная высота и конечная ширина образца с целью сравнения и контроля конечных деформаций, которые были получены при испытаниях с помощью датчиков.
2.1. Динамические испытания
Динамические испытания образцов из пеноалюминия проводились на вертикальном копре ВК-10 при нормальной (Т = 23 ± 2°С) и повышенной (60 ± 2°С) температурах. Динамометр для динамических испытаний был предварительно тарирован на статической испытательной машине TIRATEST-2300. Температура на образце измерялась с помощью цифрового четырехканального измерителя температур АТТ-2004 и ХА термопарой. Перед испытанием на образце закреплялись упругие элементы для измерения поперечной, продольной деформаций, и вместе с ними он помещался в специальное приспособление, которое устроено таким образом, что при динамическом сжатии пуансон и динамометр перемещаются параллельно и не сдвигаются друг относительно друга. Приспособление в сборе с образцом устанавливалось на копер, и проводились испытания. С заданной высоты (2.5 м) сбрасывался груз. Эксперименты проводились по программе сжатия со скоростью деформации порядка 0.5–1.0 × 102 с–1. Нагрузка, осевая и поперечная деформации на образце измерялись с помощью регистрирующей аппаратуры, которая тарировалась совместно с динамометром и датчиками перемещений. Параметры нагружения образцов и результаты испытаний зафиксированы в памяти аппаратуры системы сбора данных. Частота измерения для каждого из датчиков и упругих элементов (скобочки продольные, поперечные и динамометра) составляла 200 измерений в секунду. После динамических испытаний измерялись конечная высота и конечная ширина образцов с целью сравнения и контроля конечных деформаций, которые были получены при испытаниях с использованием датчиков. Скорость падения груза во всех случаях в начальный момент нагружения составляла 7 м/с.
2.2. Влияние температуры и скорости деформирования на механические свойства пеноалюминия
Статические испытания пеноалюминиевых образцов серии А с вытянутыми порами и плотностью 0.615–0.628 г/см3 при нормальной (T = 20°С) и повышенной (T = = 60°С) (рис. 2) температурах показали, что диаграммы сжатия и характеристики разрушения слабо зависят от температуры. Испытания образцов серии Б с круглыми порами и плотностью 0.529–0.576 г/см3 также показали незначительное влияние температуры на диаграммах сжатия.
Рис. 2.
Диаграммы динамического и статического сжатия пеноалюминиевого образца № А8 при температуре 60 ± 2°С.
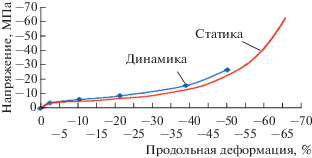
Рис. 3.
Диаграммы динамического и статического сжатия пеноалюминиевого образца № В4 при температуре 60 ± 2°С.
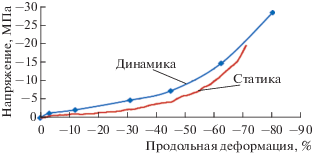
Рис. 4.
Установка для взрыва проволочки импульсом электрического тока: 1 – разрядник РГУ-1, 2 – высоковольтный конденсатор 54 мкФ 15 кВ, 3 – высоковольтный источник питания ИВН-3.
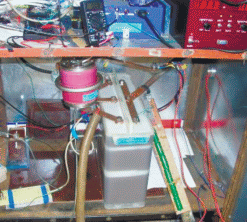
Рис. 5.
Внутренний вид взрывной камеры. 1 – датчик давления PCB 109C11, установленный на дне камеры, 2 – демпфирующий пористый материал, закрывает второй датчик давления PCB 109C11, расположенный центрально - симметрично первому на внутреннем диаметре дна камеры.
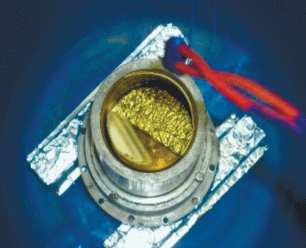
Рис. 6.
1 – осветитель, 2 – цифровая скоростная видеокамера Motion Pro X-3 (Red Lake US), 3 – ноутбук, 4 – зарядовый усилитель PCB, 5 – 4-канальный цифровой осциллограф GDS-2104, 6 – генератор прямоугольных импульсов Г5-54, 7 – защитное оргстекло.
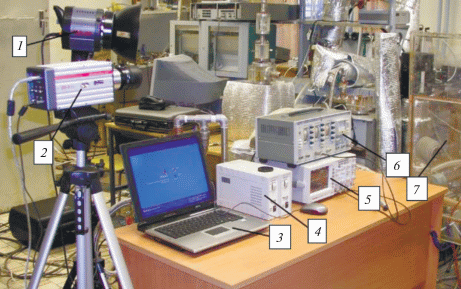
Рис. 7.
Осциллограмма со скоростью развертки 1 мс/дел, нижняя кривая соответствует закрытому датчику, верхняя – открытому. Использовался образец № 1.
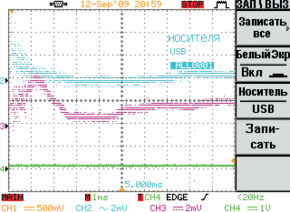
Рис. 8.
Осциллограмма с переставленными местами каналами датчиков, нижняя кривая соответствует закрытому датчику, верхняя – открытому, образец №1 (1 мс/дел).
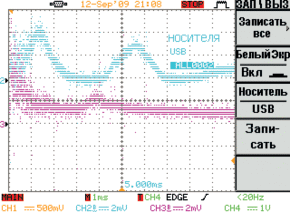
Рис. 9.
Ударные адиабаты алюминия с плотностью 0.1 (1), 0.21 (2), 0.37 (3), 0.54 (4) и 2.71 г/см3 (5). V – удельный объем вещества за фронтом ударной волны.
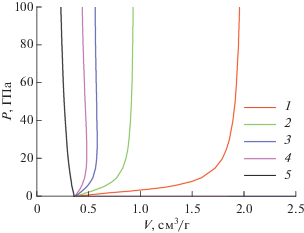
Рис. 12.
Фотография образца испытуемого материала с плотностью 0.38 г/cм3, подвергнутого воздействию ударной волны. Максимальное действующее на образец давление составляло 120 атм. Толщина образца после воздействия уменьшилась почти вдвое.
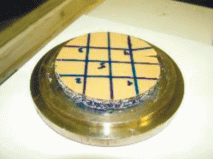
Рис. 13.
Фотографии эксперимента по ударно-волновому нагружению образца пористого алюминия. Сверху показано исходное расположение заряда относительно образца. Снизу приведены четыре кадра с экспозицией 40 нс, сделанные через 40, 50, 70 и 80 мкс после момента подрыва заряда.
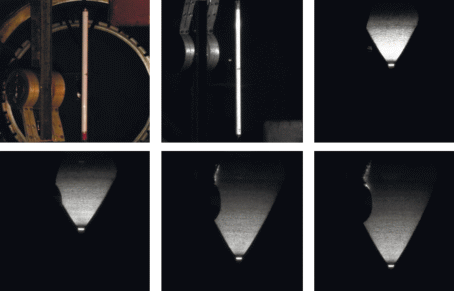
Рис. 14.
Совмещение двух фотографий потока продуктов детонации, снятых с интервалом 10 мкс. Скорость потока составляет 3.1 км/с. Угол набегания потока на образец составляет 36°.
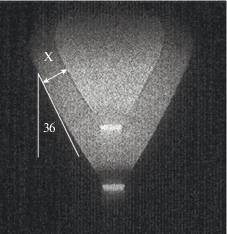
Рис. 15.
Фотографии образцов пеноалюминия после взрывного нагружения: R2 (а), R3 (б), R12 (в) и Sq1 (г).

Рис. 16.
Результаты динамических испытаний образцов пористого алюминия, выполненных на экспериментальных стендах “Яшма” (1) и ВБК-2 (2). По оси абсцисс отложена относительная деформация образца. По оси ординат – ударно-волновое давление, действующее на образец. Около экспериментальных точек указаны плотности соответствующих образцов. Для сравнения приведены результаты [5], полученные на ударной трубе для образцов пористого алюминия с плотностью 0.1 г/см3 (3).
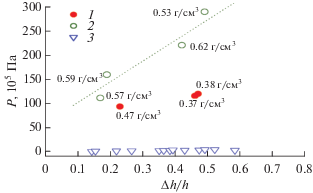
Рис. 17.
Напряжения в стенках пеноалюминия при его деформировании (кинематическое нагружение, изолированная ячейка).
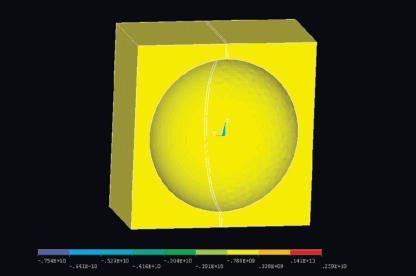
Статические испытания образцов серии В с круглыми порами и плотностью 0.334–0.343 г/см3 показали некоторое влияние температуры на диаграммы сжатия (рис. 3) и незначительное влияние на характеристики разрушения. Диаграммы сжатия при температуре 60°С ниже на 2–4 МПа соответствующих диаграмм при нормальной температуре. При динамических испытаниях образцов серии А и Б влияние температуры незначительно, а при испытаниях образцов серии В наблюдается небольшое снижение диаграммы сжатия (2–4 МПа). Весь процесс динамического деформирования имел длительность порядка 10 мс, что обеспечило скорость деформирования порядка 0.5–1.0 × 102 с–1. Наблюдается повышение диаграмм сжатия при динамическом нагружении по сравнению со статическим (до 5 мПа), а также снижение характеристик разрушения образцов серии А и Б и повышение характеристик разрушения образца серии Б при температуре 60°С.
Рис. 21.
Зависимость накопленной пластической деформации в зависимости от массы заряда: 1 – пластины без защиты, 2 – пластины с защитой.
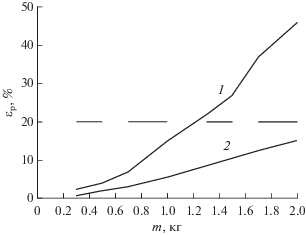
3. ИСПОЛЬЗОВАНИЕ ПЕНОАЛЮМИНИЯ ДЛЯ ЗАЩИТЫ ВЫСОКОВОЛЬТНОГО МАСЛОНАПОЛНЕННОГО ЭЛЕКТРООБОРУДОВАНИЯ (ВМЭО)
При электровзрыве масляного трансформатора происходит разрушение стенок с выбросом масла, а при сильном взрыве осколки могут повредить близлежащие трансформаторы. Для зашиты от подобных чрезвычайных ситуаций нами впервые предложена демпферная система защиты трансформаторов, основанная не на увеличении объема полости трансформатора, а на защитных свойствах пеноалюминия, который при взрыве сминается, и энергия взрыва затрачивается на смятие пеноалюминия, сохраняя невредимыми стенки трансформатора.
3.1. Эффективность пористых демпферов при малых интенсивностях ударных волн
Нарушение электрической прочности изоляционного материала приводит к интенсивному локальному разложению масла (деградации). Это разложение – одна из главных причин, по которой в начале короткого замыкания в условиях высокого давления образуется кратковременный газовый пузырь. Затем, в течение миллисекунд после появления электрической дуги, происходит образование газа, заканчивающееся резким подъемом давления.
Принципиальная схема установки (Московский физико-технический институт) и принцип ее работы (рис. 4, 5) состоят в следующем. На установке в масле генерируется дуга миллисекундной длительности при токе ~1 кА. В трансформаторном масле зажигание дуги производится подрывом тонкой проволочки диаметром 0.06 мм и длиной 5 мм. Зажигание дуги происходит за счет термоэлектронной эмиссии, возникающей при высокой температуре испарения проволочки ~6000 К, а также высоковольтного импульса, образующегося при обрыве тока. В качестве материала проволочки был выбран вольфрам, обладающий необходимой температурой испарения, при которой идет значительная термоэлектронная эмиссия. На проволочку подается напряжение 5–15 кВ от взрывного высокоиндуктивного комплекса. Полная электрическая энергия комплекса регулируется в пределах 1–6 кДж. Время горения дуги задается декрементом затухания контура, который определяется параметрами контура L, С, и R в каждый момент времени, а также напряжением повторного зажигания дуги. Через каждые полпериода затухающих колебаний ток проходит через ноль. Происходит гашение дуги, и через время t = L/Rп, где Rп – сопротивление газа после погасания дуги (очень велико), происходит восстановление полного напряжения на промежутке и повторное зажигание. Это видно по высокочастотным помехам на осциллограммах тока вблизи нуля. Время составляет величину порядка 1 мкс, что много меньше времени горения дуги в течение полупериода колебаний, и им можно пренебречь. Дуга перестает повторно возникать, как только напряжение на промежутке станет меньше напряжения ее зажигания. Этим определяется полное время ее горения. Сопротивление дуги и напряжение повторного зажигания в свою очередь определяется ее длиной. При длине проволочки 5 мм время горения дуги составляет 4–8 мс.
В эксперименте с чистым маслом время горения дуги составляет 4 мс. Однако в эксперименте масло загрязняется углеродом и металлической взвесью, которые образуются при разложении масла и эрозии электродов, тем самым снижая электрическую прочность масла, а значит и напряжение повторного зажигания и сопротивления дуги. В этом случае время горения составляет 6–8 мс.
Кабели от катушки индуктивности идут во взрывную камеру, в которой на днище расположены датчики динамической составляющей давления (с максимальным измеряемым давлением в импульсе до 5000 атм). Взрывная камера помещается в защитный кожух, представляющий собой бочку из пластика, обклеенную металлической фольгой для снижения электрических наводок на приборы во время взрыва проволочки. Для предотвращения возгорания масла во время взрыва бочка каждый раз наполнялась углекислым газом и закрывалась полиэтиленом и экранированной крышкой. На рис. 5 показана взрывная камера из нержавеющей стали внутренним диаметром 110 мм, глубиной 120 мм, толщиной стенок 10 мм, помещенная в защитный кожух. В камеру залито трансформаторное масло ТКП. Справа видны подводящие силовые провода с проволочкой. Из взрывной камеры от датчиков сигнал поступает на запоминающий осциллограф GDS 2104, где обрабатывается и расшифровывается (рис. 6).
Для визуализации быстропротекающих процессов используется высокоскоростная цифровая кинокамера (рис. 6). Для разработки методов защиты трансформаторов на лабораторных стендах в МФТИ проводились исследования воздействия взрыва на стенки взрывной камеры, наполненной маслом, без защиты и с защитой с использованием различных пористых материалов. Нами было найдено оригинальное техническое решение: дуга, инициированная взрывом проволочки. Время взрыва составило порядка нескольких миллисекунд, мощность взрыва при этом существенно снижается, и процесс моделирования можно производить в лабораторных условиях без дополнительных мер предосторожности. На рис. 7 показана характерная осциллограмма электрического тока, проходящего через электрическую дугу, при взрыве проволочки в трансформаторном масле.
Далее представлены результаты исследований процесса взрыва проволочки в трансформаторном масле во взрывной камере без защиты и с защитой приемных датчиков. Подрываемая проволочка располагалась на расстоянии 60 мм от дна взрывной камеры. Для защиты использовались образцы из пористых полимеров с различающимися размерами пор – крупнопористый материал – образец № 1 и мелкопористый – образец № 2. Характерные размеры пор для первого образца составляют менее 0.5 мм. В экспериментах использовались испытательные образцы (пенополиуретан, плотность 35 кг/м3, пористость около 95%; пенофол, предельная нагрузка при сжатии не менее 0.035 МПа, плотность 44 кг/м3, пористость 0.95). Результаты испытаний приведены в виде осциллограмм, показывающих изменение давления в условных единицах от времени воздействия взрыва (рис. 7, 8).
В данном разделе описана созданная на базе силового разрядного комплекса установка для моделирования ударно волнового воздействия на стенки трансформатора. Исследованы процессы объемной детонации при распылении щелочных металлов с целью моделирования взрыва трансформатора. Исследованы процессы пробоя, образования пузыря при наличии пузырьков в трансформаторном масле и без них. На основе проведенных исследований на малогабаритных лабораторных стендах разработана методика проведения испытаний в натурных условиях с использованием образцов заряда объемного взрыва на основе щелочных металлов с целью разработки методов защиты стенок трансформаторов. Показано, что эффективность защиты в сильной степени зависит от структуры пористого материала и его основы. Результаты измерений показывают существенное демпфирование импульса на торец стенки взрывной камеры и сглаживание импульсов давления при использовании различных демпферных материалов.
4. ТЕОРЕТИЧЕСКИЙ РАСЧЕТ УДАРНЫХ АДИАБАТ ПОРИСТОГО АЛЮМИНИЯ
Для описания поведения пористого вещества при ударно-волновом нагружении существует целый ряд различных теоретических моделей. Например, в соответствии с [7] ударная адиабата пористого вещества может быть рассчитана по формуле:
(1)
$D\left( {U,k} \right) = \frac{{{{A}_{1}}}}{{{{k}^{a}}}} + \left[ {1 + \frac{b}{k} - \frac{{1 + b - {{B}_{1}}}}{{{{k}^{a}}}}} \right]U,$Необходимо заметить, что данная формула справедлива для алюминия со значениями пористости, лежащими в диапазоне 1 ≤ k ≤ 2.5. Для вещества с такой плотностью реализуется так называемый “нормальный” ход ударной адиабаты, когда рост давления за фронтом ударной волны сопровождается увеличением плотности вещества за ней. Однако в настоящей работе исследовались образцы пористого алюминия с плотностями 0.37–0.6 г/cм3, что соответствует значениям пористости k = 4.5–3; в работе [5] исследовались образцы с плотностями 0.1, 0.21 и 0.37 г/cм3, что соответствует значениям пористости k = 21, 12.9 и 3. При таких плотностях рассмотренный выше подход неприменим, так как реализуется так называемый “аномальный” ход ударной адиабаты, когда рост давления за фронтом ударной волны сопровождается уменьшением плотности вещества за фронтом ударной волны. Расширение вещества за фронтом ударной волны, распространяющейся по сильно пористому веществу, связано с его нагревом до очень высокой температуры [6].
Построить имеющие “аномальный” ход ударные адиабаты сильно пористого вещества можно, используя широкодиапазонные уравнения состояния и используя какие-либо дополнительные модельные предположения о механизме схлопывания пор. Простейшей моделью для описания поведения пористого вещества при ударно-волновом нагружении является модель Я.Б. Зельдовича [6]. Ударная адиабата, согласно этой модели, строится в предположении, что схлопывание пор при сжатии происходит при пренебрежимо малых давлениях. Основанные на данной модели теоретические расчеты ударных адиабат для алюминия с различной плотностью представлены на рис. 9. При расчетах использовались уравнения состояния из базы данных ОИВТ РАН (http://ihed.ras.ru/rusbank).
Изложенный выше подход успешно используется для описания ударных волн достаточно большой интенсивности, когда давление за фронтом ударной волны существенно превышает предел текучести материала. Однако в данной работе нас интересует область относительно малых давлений, ограниченных пределом прочности корпуса трансформатора до разрушения – речь идет о сотнях атмосфер. Для описания поведения пористых сред в этой области также существует ряд моделей [8–12], однако все они достаточно сложны и требуют знания многочисленных постоянных среды, для нахождения которых требуется проведение специальных экспериментов.
Таким образом, для определения кривой ударной сжимаемости конкретного пористого материала в области низких давлений целесообразно проведение прямых ударно-волновых экспериментов.
5. ДИНАМИЧЕСКИЕ УДАРНО-ВОЛНОВЫЕ ИСПЫТАНИЯ ПОРИСТОГО АЛЮМИНИЯ
Описанные в данном разделе эксперименты были проведены на экспериментальном стенде “Яшма”, ударной трубе (УТ) из нержавеющей стали, изготовленной в размерах, позволяющих получить однородный ламинарный поток газа за фронтом падающей ударной волны и сохранить стационарные условия (температуру и давление газа) за отраженной от торца ударной волной не менее 30 мс [13]. Диаметр ударной трубы – 1000 мм. Длина камеры низкого давления – 5 м, камеры высокого давления – 3 м. Камеры разделены мембраной из листовой меди, которая рвалась на крестообразных ножах под действием толкающего газа из камеры высокого давления. Вблизи торца ударной трубы, в измерительной ее части, установлены четыре пьезоэлектрических датчика давления на равных расстояниях друг от друга 150 мм.
Сигналы с датчиков давления записывались на цифровой четырехканальный осциллограф LeCroy 64 Xi с полосой пропускания 600 МГц. Это позволяет измерить скорость ударной волны с точностью до 0.3% [13].
Установка оснащена системой подачи газа в камеру низкого давления, системой подачи газа в камеру высокого давления, позволяющей работать при давлениях вплоть до 150 атм, и системой измерения с точностью не хуже 2%.
5.1. Проведение динамических ударно-волновых испытаний
Методика проведения эксперимента была максимально приближена к методике, описанной в работе [5]. Первоначально в экспериментах использовались цилиндрические образцы с диаметром 80 мм и толщиной 20 мм, имеющие плотность 0.54 г/см3. Образец плотно крепился термоклеем к стальному торцу ударной трубы, после чего сам торец крепился к ударной трубе.
Осушенный специальным образом газообразный азот заполнял камеру низкого давления под давлением до 10 атм. Толкающим газом во всех экспериментах был водород – он находился в камере высокого давления. Интенсивность генерируемой ударной волны зависела от толщины медной мембраны, установленной между камерами низкого и высокого давления, и от начального давления и температуры газа в камера низкого давления. Давление водорода в камере высокого давления поднималось до тех пор, пока мембрана не разрезалась крестообразными ножами, острые кромки которых находились вблизи плоскости мембраны.
После раскрытия мембраны на границе раздела камер высокого и низкого давлений происходит распад контактного разрыва, в результате которого порождаются ударная волна и волна разрежения, которые распространяются в противоположные стороны от плоскости мембраны к обоим торцам ударной трубы. В момент прихода ударной волны, распространяющейся в сторону образца, в сечении, где установлен пьезодатчик, на осциллограмме появлялся сигнал. На осциллограммах хорошо виден момент прихода падающей, а затем и отраженной от испытуемого образца ударной волны.
Равновесные параметры за отраженной ударной волной рассчитывались по скорости ударной волны, измеренной на трех независимых базах. Поскольку режимы экспериментов были таковы, что диссоциация, ионизация и другие подобные эффекты, меняющие значительно показатель адиабаты, не наблюдаются (равновесная температура за ОУВ не превышала 900 К), для расчетов давления и температуры были применены законы сохранения энергии, импульса, массы и уравнение состояния идеального газа [6, 13].
5.2. Механизм разрушения образцов
Первые же эксперименты на стенде “Яшма” показали, что механизм разрушения испытуемого материала при воздействии на него ударной волны, падающей на образец из среды, способной неограниченно менять форму под действием касательных механических напряжений (жидкой или газообразной), принципиально отличается от механизма разрушения при воздействии прочного ударника (например, молота копровой установки). На рис. 11 показаны состояния образца испытуемого материала с плотностью 0.54 г/cм3, последовательно подвергнутого воздействию ударной волны с нарастающей амплитудой, падающей на него из газовой среды (азот). Максимальное действующее на образец давление в этих экспериментах, получаемое за фронтом отраженной ударной волны, составляло 15, 62 и 92 атм. Какой-либо макроскопической деформации (изменения толщины) образца в опытах зафиксировано не было. На рисунке видно, что вместо этого разрушение образца происходит путем разрыва стенок отдельных пор на его поверхности с последующим затеканием туда гидродинамического потока. Очевидно, что для поглощения энергии падающей ударной волны такой режим разрушения малоэффективен – необходимо, чтобы имела место макроскопическая деформация образца. Необходимо отметить, что в работе [5] есть упоминание о том, что поверхностный слой образца в экспериментах на ударной трубе прикрывали поливинилхлоридом, но не указано, по какой причине. С целью предотвратить разрушение образца путем разрыва стенок отдельных пор было принято решение в дальнейших экспериментах защитить поверхность образца слоем листового винипласта ВНЭ толщиной 2 мм.
Винипласт представляет собой жесткий поливинилхлорид, содержащий смазывающие добавки и стабилизаторы. Обладает отличными физическими свойствами, что позволяет использовать его в качестве конструкционного материала. Материал имеет отличную светостойкость, хорошо склеивается и сваривается. Листовой винипласт листовой изготавливают из непластифицированной поливинилхлоридной композиции методом экструзии или прессованием. Материал не токсичен, нерастворим в этиловом и метиловом спирте, высших алифатических спиртах, алифатических углеводородах, глицерине, смазочных и растительных маслах, не взрывоопасен. Его относят к группе горючих материалов, к подгруппе – трудновоспламеняемых. С успехом применяется в промышленности, где используются щелочи, кислоты и прочие агрессивные соединения и вещества. Основные свойства винипласта ВНЭ приведены в табл. 1.
Таблица 1.
Теплофизические свойства винипласта ВНЭ
Наименование показателя | Ед. измерения | Значение |
---|---|---|
Рабочая температура (длительно доп.) | °С | –15 +60 |
Предел текучести при растяжении | МПа (кгс/см2) | 50–59 |
Относительное удлинение при разрыве | % | 10 |
Температура размягчения по Вика | °С | 86 |
Твердость по Бринеллю | Мн/м кв. (кгс/мм2) | 150 (15) |
Удельная теплоемкость | кДж | 1.13–2.14 |
Коэффициент теплопроводности | Вт | 0.15–0.16 |
Изменение размеров при подогреве, не более | % | 5 |
Электрическая прочность (при 20°С) | МВ/м | 15 |
Диэлектрическая проницаемость | при 50 Гц | 4.1 |
Учитывая все вышеизложенное, винипласт можно рассматривать в качестве возможного материала для облицовки поверхности демпфируемого слоя из алюминия внутри трансформатора.
5.3. Результаты динамических ударно-волновых испытаний
В основной серии экспериментов использовались образцы диаметром ~100 мм, поверхность которых была защищена листовым винипластом ВНЭ толщиной 2 мм. Для обеспечения плоскопараллельности торцевых поверхностей образцов перед экспериментом они обрабатывались на токарном станке.
Время действия максимального давления на образец составляло около 30 мс. Характерный вид образца после нагружения приведен на рис. 12. После эксперимента образец отделялся от съемного торца ударной трубы путем нагревания вместе с торцом до размягчения термоклея и проводились замеры его геометрических размеров.
Условия испытаний и результаты замера образцов приведены в табл. 2. Указана исходная плотность образцов ρ, толщина образцов перед экспериментом h, исходное давление азота в камере низкого давления P1, температура Т и давление P за фронтом отраженной от образца ударной волны, среднее уменьшение толщины образца в результате воздействия ударной волны ∆h, относительная деформация ∆h/h.
5.4. Проведение динамических взрывных испытаний на стенде ВБК-2
Для проведения динамических взрывных испытаний использовалась цилиндрическая взрывная барокамера ВБК-2 (ОИВТ РАН), рассчитанная на подрыв заряда взрывчатого вещества массой до 20 кг в тротиловом эквиваленте.
Образцы пеноалюминия, поверхность которых была защищена листовым винипластом ВНЭ толщиной 2 мм, размещали на плоском торце массивного недеформируемого цилиндра массой 25 кг перпендикулярно цилиндрическому заряду ВВ. Экспериментальные заряды для взрывного нагружения образцов формировали при заполнении порошком гексогена тонкостенных (0.75–1.0 мм) стеклянных трубок с внутренним диаметром d ~ 24, 30 и 36 мм и длиной до 500 мм. Плотность заряда составляла 1.0–1.3 г/см3. Линейное энергосодержание зарядов составляло 2.6–5.8 МДж/м. Заряд инициировался в его верхней части. Расстояние от образца до цилиндрического заряда ВВ устанавливали в интервале 15–30 см. Расширяющиеся продукты детонации набегали на образцы с начальным давлением 100–250 атм. В экспериментах использовались образцы с плотностью свыше 0.5 г/cм3, для исследования которых интенсивности ударных волн, реализуемых на экспериментальном стенде “Яшма”, оказалось недостаточно. Для высокоскоростной регистрации параметров нагружения в экспериментах использовалась высокоскоростная видеосъемка камерой “Cordin 222–16”, позволяющая записать 16 кадров с экспозицией от 5 нс.
Определение скорости детонации D и скорости потока продуктов детонации, падающего на испытуемый образец UПД осуществляли на основе сопоставления 16-ти фотографий детонации цилиндрических зарядов, полученных при экспозиции 30–50 нс. Моменты открытия затвора камеры регистрировали и определяли с помощью импульсного цифрового осциллографа LeCroy WP 7100A с точностью не хуже ±1 нс.
На рис. 13 приведена иллюстрация методики получения количественных данных из экспериментальных фотографий. При наложении фотографий извлекается информация о скорости и угле падающего на образец потока продуктов детонации и скорости детонации заряда взрывчатого вещества.
На рис. 13 и 14 приведены иллюстрации изменения давления ударной волны при детонации цилиндрического заряда. Эти данные послужили основой для выбора схемы и параметров экспериментальных испытаний образцов пеноалюминия в диапазоне давлений 100–250 атм.
5.5. Результаты динамических взрывных испытаний
В экспериментах на стенде ВБК-2 использовались образцы диаметром ~80 мм, а также образцы в виде прямоугольного параллелепипеда ~100 × 100 × 20 мм, поверхность которых была защищена листовым винипластом ВНЭ толщиной 2 мм. Время действия максимального давления на образец составляло ~50 мкс.
После эксперимента проводились замеры геометрических размеров образца. Фотографии образцов после нагружения приведены на рис. 15. Видны их частичная деформация и локальные разрушения. Условия взрывных испытаний и результаты замера образцов приведены в табл. 3. Указана исходная плотность образцов ρ, толщина образцов перед экспериментом h, среднее уменьшение толщины образца в результате воздействия ударной волны ∆h, относительная деформация ∆h/h, диаметр заряда взрывчатого вещества d, его плотность ρВВ, линейное энергосодержание заряда El, расстояние от оси заряда до поверхности образца R, относительное удаление образца от заряда 2R/d, динамическое давление, действующее на образец.
Таблица 3.
Условия и результаты динамических взрывных испытаний
Образец | ρ, г/cм3 | h, мм | ∆h, мм | ∆h/h | d, м | ρВВ, кг/м3 | El, МДж/м | R, м | 2R/d | P, атм |
---|---|---|---|---|---|---|---|---|---|---|
Sq1 | 0.62 | 27.53 | 11.5 | 0.42 | 0.0355 | 1000 | 5.840 | 0.255 | 14.37 | 221 |
R3 | 0.53 | 22.8 | 11.6 | 0.49 | 0.0245 | 1153 | 3.207 | 0.165 | 13.47 | 290 |
R2 | 0.59 | 24.0 | 4.7 | 0.19 | 0.024 | 1283 | 3.424 | 0.230 | 19.17 | 160 |
R12 | 0.57 | 21.7 | 3.8 | 0.17 | 0.030 | 1000 | 4.170 | 0.305 | 20.33 | 112 |
Результаты динамических испытаний образцов пористого алюминия, выполненных на экспериментальных стендах “Яшма” и ВБК-2, суммированы на рис. 16 в сравнении с данными [5]. Экспериментальные данные, полученные на стенде ВБК-2, относятся к образцам с примерно одинаковой плотностью и могут быть аппроксимированы пунктирной линией. Экспериментальных данных, полученных на стенде “Яшма” для образцов с низкими плотностями, недостаточно для выполнения такой аппроксимации ввиду малого количества образцов с низкой плотностью, предоставленных для исследований. Тем не менее, можно предположить, что на поле: относительная деформация образца – ударно-волновое давление, действующее на образец, экспериментальные данные для образцов пористого алюминия с плотностями в диапазоне 0.1–0.6 г/см3 могут быть аппроксимированы веером прямых линий, расположенных в секторе, ограниченном на рис. 16 пунктиром (0.6 г/см3) и экспериментами (0.1 г/см3).
Анализ проведенных экспериментов и рис. 16 позволяют сделать следующие выводы:
1. Для эффективного использования плит из пористого алюминия в качестве материала, поглощающего энергию ударной волны, падающей на него из жидкой или газообразной среды, необходимо дополнительно защищать поверхность этого материала (например, слоем диэлектрика). Винипласт, примененный для этой цели в данной работе, хорошо справляется с ролью защитного слоя в случае однократного воздействия, однако желательно было бы использовать материал, обладающий большей пластичностью. Для выбора и определения эффективной толщины и особенностей использования материала защитного слоя необходимо проведение дополнительных экспериментов.
2. Использование плит из пористого алюминия с плотностью 0.54 г/cм3 в качестве материала, поглощающего энергию ударной волны, с точки зрения защиты корпуса трансформатора не эффективно, так как при давлениях, являющихся критическими для корпуса (около 120 атм), деформация этого материала явно недостаточна. Такой материал может быть рекомендован для защиты от более интенсивных ударно-волновых воздействий (например, в оборонной технике). Для защиты корпусов трансформаторов необходимо использовать алюминиевую пену с плотностью 0.38 г/cм3 и менее. Для определения оптимальной плотности алюминиевой пены необходимо проведение дополнительных экспериментов. Вероятно, она должна составлять около 0.2–0.3 г/cм3. На основе опыта и результатов, полученных ранее, созданы установки для моделирования и исследования импульсного воздействия на стенки трансформатора при энерговыделении в трансформаторном масле.
6. МАТЕМАТИЧЕСКОЕ МОДЕЛИРОВАНИЕ ВОЗДЕЙСТВИЯ УДАРНОЙ ВОЛНЫ НА МЕТАЛЛИЧЕСКУЮ КОНСТРУКЦИЮ С ЗАЩИТНЫМ СЛОЕМ ИЗ ПЕНОАЛЮМИНИЯ
Математическое моделирование систем с демпферной защитой является важным с точки зрения создания конструкций. Эксперименты ставятся, как правило, для простых геометрий (рис. 17) с целью определения конструктивных соотношений для различных напряжений, деформации и скоростей деформаций. Расчеты же конкретных конструкций должны производиться численно с помощью коммерческих или самостоятельно разработанных (inhouse) кодов, программ и пакетов. До применения пакетов для конкретных конструкций необходимо провести численное моделирование для простых трехмерных объектов. По этой причине в данном разделе было проведено изучение воздействия ударной волны на стенки металлического куба с внутренним защитным слоем из пеноалюминия. Воздействие ударной волны на стенки куба изучалось для случая, когда источник волны расположен внутри куба, что соответствует внутреннему взрыву. Для оценки эффективности защиты трансформатора слоем пеноалюминия проведено сравнительное исследование влияния взрывных волн различной интенсивности на стальную пластину с защитой и без защиты. Исследовалась стальная квадратная пластина длиной 1300 мм и шириной 1000 мм, толщина защитного слоя составляла 50 мм (рис. 18).
Принято, что плотность материала ρ = 7800 кг/м3, модуль упругости E = 200 ГПа, коэффициент Пуассона ν = 0.3, предел текучести σT = 300 МПа, касательный модуль Eτ = 10 ГПа. В расчетах при знакопеременном упругопластическом деформировании отклик стали моделировался моделью кинематического упругопластического деформирования.
Для описания упругопластического поведения защитного слоя из пеноалюминия применялась нелинейная модель сотового материала $\rho = 300\,\,{\text{кг}}{\kern 1pt} /{{{\text{м}}}^{{\text{3}}}},$ модуль упругости алюминия $E = 72\,{\text{ГПа}},$ коэффициент Пуассона $\nu = 0.33,$ предел текучести ${{\sigma }_{T}} = 145\,{\text{МПа}};$ предельное относительное изменение объема ${{V}_{f}} = 0.15.$
Сотовый материал рассматривался как анизотропный с модулями по направлениям
Вначале давление скачком возрастает до пикового избыточного давления ${{p}_{s}}.$ Затем давление постепенно убывает, и образуется область низкого давления (рис. 19) сравнительно небольшой амплитуды, после чего давление, в конечном счете, возвращается к атмосферному ${{p}_{0}}$ за время ${{t}_{s}}.$ Часть кривой, находящаяся ниже нуля называется фазой разрежения, а часть, находящаяся выше нуля – положительной фазой. В любой момент времени избыточное давление ${{p}_{s}}$ описывается в безразмерной форме: для параметра $\alpha ,$ отвечающего за форму волны и времени продолжительности положительной фазы ${{t}_{0}},$ как
(2)
$p\left( t \right) = \left( {1 - \frac{t}{{{{t}_{0}}}}} \right){{p}_{s}},\,\,\,\,0 \leqslant t \leqslant {{t}_{0}},\,\,\,\,p\left( t \right) = {{p}_{s}}\left( {1 - \frac{t}{{{{t}_{0}}}}} \right){{e}^{{ - \alpha \frac{t}{{{{t}_{0}}}}}}},\,\,\,\,t \geqslant {{t}_{0}}.$Для моделирования такого поведения в системе LS DYNA в качестве нагрузки использовалась модель BLAST_LOAD. Модель BLAST_LOAD основана на представлениях Randers-Pehrson и Bannister (1997). Это удобная модель для прикладывания ударных нагрузок к различным структурам. Эта модель аппроксимирует экспериментальные данные полученные Kingery (1984). В модели учитывается угол падения волны $\theta ,$ отраженное давление${{P}_{{{\text{ref}}}}}$ и падающее давление ${{P}_{{{\text{in}}}}}.$
(3)
$p\left( t \right) = {{p}_{{{\text{ref}}}}}{{\cos }^{2}}\theta + {{p}_{{{\text{in}}}}}\left( {1 + {{{\cos }}^{2}}\theta - 2\cos \theta } \right),$(4)
${{p}_{{{\text{ref}}}}} = {{p}_{{r0}}}\left( {1 - \frac{t}{{{{t}_{0}}}}} \right){{e}^{{ - a\frac{t}{{{{t}_{0}}}}}}},\,\,\,\,{{p}_{{{\text{in}}}}} = {{p}_{{s0}}}\left( {1 - \frac{t}{{{{t}_{0}}}}} \right){{e}^{{ - b\frac{t}{{{{t}_{0}}}}}}}.$Модель BLAST_LOAD требует следующих входных параметров: масса-эквивалент массы тринитротолуола (m); координаты точки взрыва; время задержки между началом расчета и моментом взрыва $\left( \tau \right).$ В нашем случае рассматривалась ударная волна, приходящая по нормали к поверхности, то есть $\theta = 0^\circ $ и уравнение (2) преобразуется к виду:
В дальнейшем исследовалась зависимость накопленных пластических деформаций в зависимости от массы заряда (прикладываемого давления) с учетом того, что эпицентр взрыва находился на расстоянии 1 м от образца и время запаздывания равнялось τ = 0.0001 с. Сравнение результатов проводилось по двум моделям:
1) стальная пластинка покрытая слоем пеноалюминия;
2) стальная пластинка без защиты.
Результаты моделирования в виде зависимостей накопленной пластической деформации от массы заряда приведены в табл. 4.
Таблица 4.
Накопленные пластические деформации, полученные из расчетов двух моделей при разных массах заряда М
M, кг | ${{\varepsilon }_{p}},\% $ (пластинка с защитой) | ${{\varepsilon }_{p}},\% $ (пластинка без защиты) |
---|---|---|
0.3 | 0.8 | 2.3 |
0.5 | 2 | 4 |
0.7 | 3 | 7 |
1.0 | 5.5 | 15 |
1.3 | 8.5 | 22 |
1.5 | 5 | 27 |
1.7 | 12.5 | 37 |
2.0 | 15 | 46 |
Если принять за критерий разрушения стальной пластинки уровень предельных пластических деформаций $\delta = 20\% ,$ то из полученных результатов видно, что при массе заряда равной $m \approx 1.2$ кг пластинка без защиты разрушается, в то время как пластинка, покрытая слоем пеноалюминия, достигает уровня пластических деформаций ниже предельного значения в 2.5 раза.
Динамические нагрузки на пластину приведены на рис. 20. На рис. 21 приведены графики, показывающие процесс накопления пластических деформаций в зависимости от массы заряда. Как видно из рис. 21–23, пластинка, защищенная слоем пеноалюминия, может выдержать массу взрывчатки, равную m ≈ 2.7 кг, что в 2.25 раза больше, чем для незащищенной пластинки. Значения поглощенной пеной энергии в зависимости от массы заряда приведены на рис. 23.
Величины максимального действующего давления в зависимости от массы заряда представлены на рис. 24.
7. ЭКСПЕРИМЕНТАЛЬНОЕ ТЕСТИРОВАНИЕ ДЕМПФЕРНОЙ СИСТЕМЫ ЗАЩИТЫ
7.1. Описание трансформаторного стенда и диагностики
Макетный образец взрывобезопасного маслонаполненного автотрансформатора напряжением 220/110 кВ IV габарита с методами защиты на основе демпфирующих материалов изготовлен совместно с ОАО “ПК ХК Электрозавод”. Модель трансформатора, на базе которого разработана конструкция трансформатора с демпферной защитой – ТМП-4000/10-ХЛ1 (рис. 25). Материалом защитных панелей является пеноалюминий толщиной 20 мм, плотностью 0.2–0.3 г/см3. Демпферными панелями закрыта большая часть боковой поверхности бака трансформатора и крышки с внутренней стороны. Пористость пеноалюминия – закрытая. Демпфирующие панели расположены в зазоре между активной частью трансформатора и корпусом (боковая поверхность, крышка). Крепление панелей к корпусу является простым и удобным для последующей их замены в случае повреждения. Смена панелей должна производиться при снятой крышке трансформатора, без вынимания активной части из бака трансформатора.
Трансформатор оснащен сменной крышкой для испытаний на взрывобезопасность. Сменная крышка имеет ту же конструкцию, что и штатная, за исключением следующих требований: отсутствие штатных трансформаторных вводов высокого и низкого напряжений и отверстий для них в крышке, наличие съемной панели для доступа к электродам, наличие датчиков импульсного давления, наличие крановых петель на расширительном бачке, а также высоковольтные разрядники, установленные в проходных изоляторах.
Трансформатор на период испытаний оснащался четырьмя быстродействующими манометрами для регистрации изменений импульсного давления, три из которых расположены в сменной крышке на разном расстоянии от эпицентра ударной волны и один – в стенке бака за демпферной панелью, а также датчиками температуры масла. Пределы измерения давления составляли 0.01–1000 МПа, время между измерениями давления – 20 мкс. Температура в трансформаторе измеряется в нескольких точках с установленной штатной крышкой. Всего в трансформаторе установлено 16 термодатчиков.
Система электроснабжения. Электрооборудование стенда включает в себя низковольтную и высоковольтную части. Высоковольтная часть стенда состоит из высоковольтного трансформатора, высоковольтного диодного моста, зарядных резисторов, конденсаторной батареи, высоковольтных делителей напряжения, игнитронного разрядника сильноточного фидера. Разряд заряженной батареи на испытываемый образец осуществляется с помощью игнитронов. Для обеспечения механической прочности токопроводящих элементов при воздействии электродинамических сил между проводниками в режиме разряда конденсаторной батареи при подводе высокого напряжения к испытываемому объекту применяется усиленная конструкция электрических шин и фидеров.
Конденсаторная батарея. С целью формирования мощного импульса тока, протекающего через нагрузку, энергия импульса предварительно запасается в накопителе, в качестве которого используется конденсаторная батарея. Батарея собрана из конденсаторов типа К41И-7 емкостью 100 мкФ каждый. Вся батарея состоит из четырех секций, каждая из которых имеет три группы по 92 конденсатора. Всего батарея содержит 1104 конденсатора. Емкость секции Cс = 0.0276 Ф, а общая емкость батареи Cб = 0.11 Ф. Максимальное рабочее напряжение на конденсаторах U = 5 кВ, при этом запасенная энергия составляет 1.38 МДж. При заряде батареи до напряжения 4.5 кВ энергия, накопленная в конденсаторах, превышает 1 МДж.
На рис. 26 представлена фотография фрагмента стеллажа, демонстрирующая особенности конструкции конденсаторной батареи. Конденсаторы размещены на двух одинаковых стеллажах. На каждой из двух сторон стеллажей собрана одна секция батареи, которая состоит из двенадцати рядов по 23 конденсатора, расположенных друг над другом. Конденсаторы уложены в специальные ячейки под небольшим углом к горизонтальной плоскости таким образом, что при нарушении герметичности их корпуса масло, заполняющее конденсатор, стекает внутрь стеллажа в специальный поддон, не загрязняя элементы ошиновки. Шины батареи изготовлены из медных стержней длиной 5 м. Каждый конденсатор соединен с парой коллекторных шин гибкими предохранительными проводниками, изготовленными из кабеля РК-75-4-12 со снятой оплеткой. В случае пробоя внутри какого-либо конденсатора гибкий предохранитель выгорает, и взрыва конденсатора, вызываемого разрядом на него энергии всей батареи, не происходит. Пары шин составляют три группы, которые через электродинамические предохранители соединены между собой. Конструкция стеллажа, крепление шин, их диаметр обеспечивают достаточную механическую прочность, так что в случае короткого замыкания разрушение ошиновки батареи исключено. С целью обеспечения электробезопасности при пробое на “землю” изоляторов шин, подводящих напряжение к объекту испытания, дополнительно в качестве шины заземления используется металлический пол из стальных листов толщиной 3 мм. Такая низкоомная и малоиндуктивная шина наряду с ограничивающими ток сопротивлениями из нержавеющей стали является средством электрозащиты и позволяет не устанавливать конденсаторную батарею на изоляторах.
Зарядное устройство. Батарея заряжается до напряжения U = 0–5 кВ от высоковольтного источника, в составе которого трехфазный согласующий трансформатор 380/220 В, трехфазный повышающий трансформатор 220/6000 В и выпрямитель, собранный по схеме Ларионова. Ток заряда ограничивается общим балластным резистором R1 и развязывающими резисторами R2, установленными в каждой секции. Зарядные сопротивления собраны из резисторов ПЭВ-100. Величина сопротивления определяется схемой соединения резисторов.
Рис. 27.
Распределение температуры масла в баке с теплопроводящими стенками в режиме короткого замыкания эквивалентным током (а) сечение № 1; (б) сечение № 3.
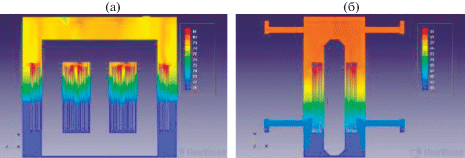
Рис. 28.
Распределение температуры масла в баке с теплопроводящими стенками в рабочем режиме (а) сечение № 1; (б) сечение № 3.
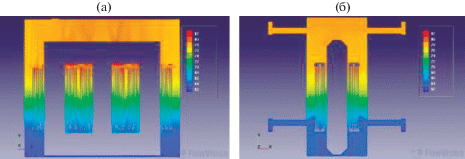
Рис. 29.
Распределение температуры масла в баке с адиабатическими стенками в рабочем режиме (а) сечение № 1; (б) сечение № 3.
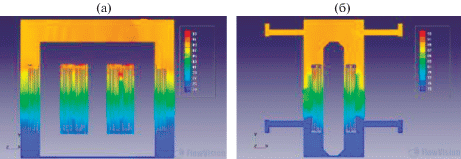
Рис. 30.
Распределение температуры масла в баке с установленной демпферной защитой на теплоизолирующей основе (а) сечение № 1; (б) сечение № 3.
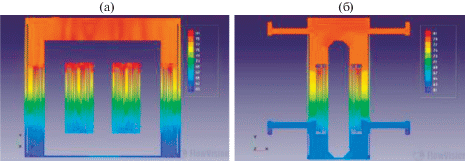
Рис. 31.
Распределение температуры масла в баке с установленной демпферной защитой на теплопроводящей основе (а) сечение № 1; (б) сечение № 3.
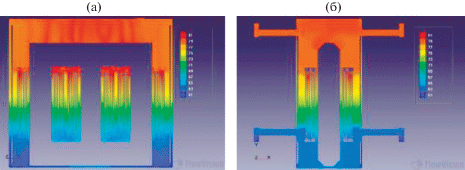
Рис. 32.
Распределение температуры масла в баке в режиме 10% перегрузки (а) сечение № 1 (б) сечение № 3.
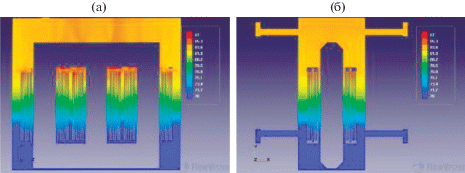
Рис. 33.
Распределение температуры масла в баке с установленной демпферной защитой в режиме 10% перегрузки (а) сечение № 1 (б) сечение № 3.
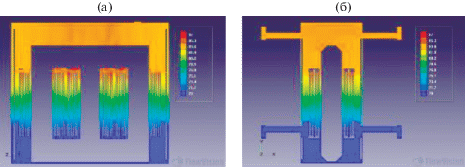
Разряд конденсаторной батареи. Четыре секции подсоединяются на одну общую нагрузку. Так как запас энергии батареи достаточно велик, каждая секция разряжается через свой игнитронный разрядник И1–И4 на общую нагрузку, где Rн – омическое сопротивление, а Lн – индуктивность нагрузки. Параметры игнитронов “Богатырь” следующие: анодное напряжение – 20 кВ; максимальный коммутируемый ток – 100 кА; количество заряда за импульс – не более 200 Кл; амплитуда тока поджигающего импульса – 300 А; длительность поджигающего импульса – 10 мкс; частота повторения импульсов – не более 10 имп/мин.
С целью обеспечения надежной параллельной работы нескольких игнитронов в цепях разряда устанавливаются дроссели развязки Lр. При отсутствии этих дросселей пробой одного из разрядников приведет к повышению потенциала катодов других игнитронов практически до потенциала батареи, и в результате разность потенциалов анод-катод будет близка к нулю, т.е. пробой остальных разрядников станет невозможен. Установка дросселей развязки позволяет поделить напряжение батареи между нагрузкой и индуктивным сопротивлением дросселя. Таким образом, в случае неодновременного пробоя игнитронов потенциал катодов игнитронов оказывается ниже потенциала батареи на величину падения напряжения на индуктивном сопротивлении дросселя в цепи первого пробившегося игнитрона. Импульсы запуска игнитронов формируется блоками поджига, собранными на базе тиратрона с холодным катодом ТХИ-1200/2.5. Для всех игнитронов используются одинаковые схема поджига, что позволяет заменять вышедшие из строя блоки. Четыре секции конденсаторной батареи подсоединяются на одну общую нагрузку с помощью коаксиального фидера. Центральный провод фидера изготовлен из медного стержня диаметром 25 мм, а внешний проводник – из медной трубы диаметром 60 мм. Такая конструкция обеспечивает необходимую механическую прочность при малых величинах омического и индуктивного сопротивлений фидера.
Система измерений. Система измерений позволит регистрировать следующие параметры процесса: напряжение на разрядном промежутке, ток разряда, импульсное давление в газовой подушке и на стенке корпуса, механическое напряжение на поверхности бака трансформатора, температуру масла. Для выполнения измерений на стенде предлагается следующая схема, состоящая из 3-х независимых систем сбора данных: Модульная система сбора данных “LTR-EU-8-1”, собирающая данные с 16-ти термопар (ТТ41ХК), 10-ти тензорезисторов (UFLA-5-11), 2-х датчиков давления (PCB109C11) и сигнала напряжения (термопары измеряют температуру внутри бака трансформатора, тензорезисторы измеряют механическое напряжение на поверхности бака трансформатора, напряжение на разрядном промежутке измеряется с помощью делителя напряжения, расположенного непосредственно на высоковольтных разрядниках, датчики давления измеряют импульсное давление в режиме реального времени); анализатор спектра AS, принимающий сигналы с 2-х датчиков давления PS-02-01 (измеряет импульсное давление в режиме реального времени). Измерение силы тока разряда осуществляется с помощью пояса Роговского.
7.2. Расчет оптимизированной конструкции в разных режимах работы трансформатора
В данном разделе получены данные по тепловым заводским испытаниям трансформатора. Это позволило провести сравнение построенной модели с реальными данными. Тепловые испытания трансформатора состоят из нескольких этапов:
1) испытание холостого хода, когда вторичные обмотки разомкнуты, а к первичной подано номинальной напряжение;
2) испытание короткого замыкания, когда вторичные обмотки соединены накоротко и на первичную обмотку подается номинальный ток;
3) испытание коротким замыканием эквивалентным током (ток, потери при котором на омическом сопротивлении равны сумме тепловых потерь в режиме холостого хода и в режиме короткого замыкания).
В первом случае выделение энергии на омической нагрузке в катушке минимальны, тогда как потери на вихревых токах и гистерезисе в магнитопроводе максимальны и соответствуют тепловыделению в рабочем режиме. Во втором случае наблюдается обратная ситуация, магнитное поле невелико, так как нагрузкой служит только сопротивление катушек, а ток, равный рабочему, приводит к тепловыделениям на омических сопротивлениях катушек соответствующим потерям в рабочем режиме. Таким образом, первые два испытания дают представление о потерях в трансформаторе в работающем режиме. Для моделирования тепловеделения работающего трансформатора, в режиме короткого замыкания, на первичную обмотку подают такое напряжение, чтобы ток соответствовал суммарным потерям в трансформаторе. В результате суммарное тепловыделение соответствует тепловыделению в обмотках трансформатора и магнитопроводе в рабочем режиме. При этом в режиме короткого замыкания эквивалентным током измеряют температуру верхних слоев масла. То есть, если в модели задать тепловыделение в обмотках, соответствующее тепловыделению при коротком замыкании, то расчетная температура масла в верхней области бака трансформатора должна соответствовать результату испытаний.
Режим короткого замыкания. По результатам испытаний коротким замыканием с током эквивалентным суммарным потерям трансформатора 30.939 кВт (этот ток составил 239.74 А), температура верхних слоев масла составила 58.7°С. относительно температуры окружающей среды (рис. 27). Результаты моделирования данного эксперимента приведены ниже.
Из приведенных рисунков видно, что температура верхних слоев масла в результате расчета составляет примерно 78.5°С. Данное значение с хорошей точностью совпадает с реально измеренным. Средняя температура масла по всему объему бака составила 72.6°С. И хотя для полной верификации необходимо провести более подробные измерения, данные результаты говорят о хорошем совпадении расчетной величины с реально измеренной.
Рабочий режим. Распределение температуры в работающем трансформаторе определяется заданием в магнитопроводе тепловыделения, соответствующего потерям холостого хода (4.9 кВт из данных по тепловым испытаниям), а в катушках – снижением тепловыделения до потерь в режиме короткого замыкания номинальным током.
Как видно из рис. 28, температура верхних слоев масла изменилась не сильно и находится в диапазоне от 78 до 80°С. Однако в рабочем режиме распределение температуры стало более неоднородным из-за тепловыделения в магнитопроводе. Средняя температура в баке составила 72.7°С, что крайне незначительно отличается от данной величины в режиме короткого замыкания эквивалентным током.
Для того чтобы определить максимально возможный уровень влияния установки демпферной защиты в автотрансформатор, проведем расчет в тех же условиях, но при адиабатической боковой стенке трансформатора (рис. 29).
Температура в верхних слоях бака теперь находится в диапазоне от 89 до 91°С. Таким образом, температура в верхних слоях увеличилась примерно на 10°С в случае исключения боковой стенки трансформатора из теплообмена. Средняя температура в баке составила 83.3°С, т.е. на 10.5°С больше, чем в случае с теплопроводящими стенками. Эти результаты говорят о значительной роли боковой стенки в процессах теплообмена трансформатора. Теперь необходимо установить, насколько влияет установка демпферной защиты в бак трансформатора в рабочем режиме. Также оценим, какое влияние оказывает теплопроводность листов, на которых закреплены демпферные пластины, на результирующее распределение температур. Для этого в одном случае в качестве материала для листов зададим теплоизолятор (рис. 30) с коэффициентом теплопроводности на два порядка ниже, чем теплопроводность демпферных пластин, а в другом случае материал с сопоставимой теплопроводностью (рис. 31). Результаты расчета приведены ниже.
Из рисунков видно, что отличия температур, при использовании разных материалов подложки для демпферных пластин, практически незаметны. Средняя температура в баке составила 72.9 и 73°С для случаев с изолирующей и проводящей основами соответственно. Таким образом, можно заключить, что изменение температуры при установке демпферной защиты в первую очередь определяется тем, как изменяются процессы конвекции, нежели процессы теплопередачи. Отметим, что установка демпферной защиты увеличивает среднюю температуру лишь на 0.1°С, в то время как полной исключение боковых стенок бака из процессов теплообмена повышает среднюю температуру более чем на 10°С. Значит, установка демпферной защиты практически не уменьшает мощность теплоотдачи через боковую стенку бака трансформатора.
Режим перегрузки на 10% по мощности. Рассмотрим, каким образом поведет себя распределение температуры в обычном трансформаторе и трансформаторе с установленной демпферной защитой, в режиме превышения мощностей тепловыделения на 10% в обмотках и магнитопроводе (рис. 32, 33).
Средние температуры в баке масла в случае с демпферной защитой и без составили 78 и 77.8°С. Отметим, что увеличение температуры масла происходит синхронно в обоих случаях.
ВЫВОДЫ
Моделирование тепловых испытаний трансформатора на заводе дало результаты, практически совпадающие с экспериментальными значениями. Измеренная величина превышения температуры верхних слоев масла над температурой окружающей среды составила 58.7°С, а рассчитанная примерно 58.5°С. Влияние различных конфигураций на теплообмен в различных режимах представлено в сводной табл. 5.
Таблица 5.
Превышение средней температуры масла в баке над температурой окружающей среды в различных режимах и при различной конфигурации трансформатора
Режим | Без демпферной защиты | С демпферной защитой (теплоизолирующая подложка) | С демпферной защитой (теплопроводящая подложка) | С адиабатическими стенками |
---|---|---|---|---|
Режим короткого замыкания эквивалентным током | 52.6°С | 63.5°С | ||
Рабочий режим | 52.7°С | 52.9°С | 52.8°С | 63.3°С |
Режим перегрузки на 10% | 57.8°С | 58°С |
Видим, что внесение демпферной защиты увеличивает среднюю температуру масла всего на 0.2°С. Тогда как полное исключение боковой стенки бака трансформатора из процессов теплообмена повышает температуру масла более чем на 10°С. То есть, установка демпферной защиты практически не исключает боковые стенки трансформатора из процесса теплообмена с окружающей средой. При этом не важно, теплоизолирующая ли основа, на которой закреплены демпфирующие пластины, или теплопроводящая. В режиме перегрузки разница между средней температурой при установленной демпферной защите и не установленной не изменяется по сравнению с рабочим режимом. Можно заключить, что добавление данной конфигурации демпферной защиты практически не нарушает процесс теплообмена боковой стенки бака автотрансформатора с внешней средой, и поэтому повышение средней температуры в баке для текущей конфигурации трансформатора незначительно.
Список литературы
Иванов Д.О. Исследование и разработка пеноалюминия, получаемого методом механического легирования из вторичного сырья. Дисс на соиск. уч. ст. канд. техн. н. МГТУ им. Баумана, М., 2008.
Сон Э.Е., Фортов В.Е., Азмеев Х.Х., Аксенов А.А., Бондарь В.С., Бабаева Н.Ю., Гаджиев М.Х., Зицерман В., Киверин А.Д., Коробейников С.М., Куликов Ю.М., Минцев В.Б., Панов В.А., Смирнов Б.М., Темис Ю.М., Тюфтяев А.С. “Электрофизика и взрывобезопасность высоковольтного маслонаполненного электрооборудования”, М.: Издательство “Наука РАН”, 2019.
Сарафанов М.А. Новая технология и оборудование для получения конструкционных материалов на основе пеноалюминия / М.А. Сарафанов // Тяжелое машиностроение. 2011. № 2. С. 34–38.
Пенометаллы (пеноалюминий) [Электронный ресурс], [2019]. https://mydocx.ru/7-38282.html
Schenker A., Anteby I., Nizri E., Ostraich B., Kivity Y., Sadot O., Haham1 O., Michaelis R., Gal O.E., Ben-Dor G. Foam-Protected RC Structures under Impact: Experimental and Numerical Studies // ASCE J. Structural Engineering. 2005. V. 131(8). P. 1233–1242.
Зельдович Я.Б., Райзер Ю.П. Физика ударных волн и высокотемпературных гидродинамических явлений. М.: Физматгиз, 1963.
Милявский В.В. Эмпирическая формула для оценки параметров ударного сжатия пористого вещества // Теплофизика высоких температур. 2000. Т .38. № 2. С. 232–241.
Golub V., Mirova O. Shock Waves in Granular Media // Shock Wave Science and Technology Reference Library, 2007, Part III. P. 325–351.
Herrmann W. Constitutive Equation for the Dynamic Compaction of Ductile Porous Materials // J. Appl. Phys. 1969. V. 40. № 6. P. 2490.
Dijken D.K., De Hosson J.Th.M. Shock wave equation of state of powder material // J. Appl. Phys. 1994. V. 75. № 2. P. 809.
Dijken D.K., De Hosson J.Th.M. Thermodynamic model of the compaction of powder materials by shock waves // J. Appl. Phys. 1994. V. 75. № 1. P. 203.
Trunin R.F., Zhernokletov M.V., Simakov G.V., Gudarenko L.F., Gushchina O.N. Shock compression of highly porous samples of Copper, Iron, Nickel and their equation of state // Shock Compression of Condensed Matter – 1997. AIP Conference Proceedings 429. Woodbury, N.Y. P. 83.
Гейдон А., Герл И. Ударная труба в химической физике высоких температур. М.: “Мир”, 1966.
Седов Л.И. Методы подобия и размерности в механике. М., 1981.
Дополнительные материалы отсутствуют.
Инструменты
Известия РАН. Энергетика