Известия РАН. Энергетика, 2021, № 4, стр. 103-126
Кинетика термохимического превращения твердого органического топлива при высокоскоростном нагреве
Е. А. Бойко 1, *, А. В. Страшников 1, **
1 ФГАОУ ВО “Сибирский федеральный университет”
Красноярск, Россия
* E-mail: EBoiko@sfu-kras.ru
** E-mail: savtr@mail.ru
Поступила в редакцию 24.05.2021
После доработки 03.08.2021
Принята к публикации 11.08.2021
Аннотация
Представлены результаты экспериментальных исследований процесса термохимического превращения твердого органического топлива при его термической обработке и сжигании в лабораторных условиях с сопоставлением полученных данных по определению видимых констант скоростей горения угля. Экспериментальные исследования проведены на экспериментальной установке с вертикальной реакционной камерой при высокоскоростном нагреве (104–106 град./с), соответствующему условиям реальных теплотехнологических процессов и устройств. Установка обеспечивает термообработку пылеугольных частиц в различных газовых средах в диапазоне от 200 до 1500°С при времени пребывания в реакционном пространстве от 0.5 до 4.5 с. Полученные экспериментальные данные в виде зависимостей lg k = f(1/T) используются для оценки кинетических характеристик различных стадий термохимического превращения топлива (сушки, термической деструкции и горения нелетучего остатка). Установлено, что при соблюдении определенных условий можно рекомендовать комплексный метод термического анализа твердого органического топлива в неизотермических условиях при низких скоростях нагрева (β = 5–20 град./мин) для объективной и адекватной оценки реакционной способности энергетических углей.
ВВЕДЕНИЕ
Согласно “Энергетической стратегии России на период до 2035 года”, утвержденной распоряжением Правительства РФ № 1523-р от 09.06.2020 г., твердое органическое топливо рассматривается в качестве основного сырьевого источника для производства энергии на длительную перспективу. Совершенствованию технологии производства и потребления энергии, вырабатываемой на твердом органическом топливе, уделяется значительное внимание в энергетической, углехимической, металлургической и других отраслях промышленности [1]. Создание новых и повышение эффективности существующих технологических приемов термохимической обработки, сжигания и газификации твердых горючих ископаемых основано на всесторонней оценке их состава и свойств. Технологии производств, так или иначе связанных с использованием процессов испарения влаги, термического разложения и взаимодействия топлива с окислителем, предусматривают, в качестве непременного условия, оценку его реакционной способности [2]. При этом необходимо учитывать специфические, для каждой марки угля, сложные кинетические механизмы большого класса недостаточно исследованных явлений термохимического превращения органической и минеральной части пылевидного твердого топлива. Значительный разброс и неполнота экспериментальных значений кинетических параметров, определяющих реакционную способность, а также отсутствие обобщающих методических работ по определению этих параметров применительно к основным этапам термохимического превращения твердого органического топлива в условиях реальных теплотехнологических процессов и установок, предопределили основные положения исследований в рамках самостоятельного научного направления “Реакционная способность углей” [3].
Достаточно эффективным средством исследования механизма и кинетики процессов термохимического превращения твердого органического топлива является использование методов комплексного термического анализа и математического моделирования [4]. Перечисленные методы нашли широкое применение в практике научных исследований, однако, сложность исследуемых процессов требует их дальнейшего совершенствования. Следует отметить, что имеет место необъективность при оценке и интерпретации получаемых результатов, а иногда и явно ошибочные гипотезы. Феноменологическое описание нуждается в дополнительной информации, главным образом структурного характера, что особенно важно при исследовании динамики процессов.
Разработка комплексного метода оценки реакционной способности энергетических углей, математических моделей и методик расчета степени термохимического превращения твердого органического топлива и обоснование на их основе технических и технологических решений по повышению эффективности энергетического использования углей имеет существенное значение для ускорения научно-технического прогресса в топливно-энергетическом комплексе страны и являются важными народно-хозяйственными задачами [5].
ПОСТАНОВКА ЗАДАЧ ИССЛЕДОВАНИЯ
В этой связи значительный практический интерес представляет сопоставление результатов, полученных при низких скоростях нагрева (β = 5–20 град./мин), присущих условиям комплексного термического анализа с экспериментом по термохимическому превращению твердого топлива при высокоскоростном нагреве (β = 104–106 град./с). Если полагать, что кинетические параметры индивидуальных реакций, составляющих процесс горения угля, не изменяются в широком диапазоне скоростей нагрева, то увеличение скорости нагрева топлива должно привести лишь к смещению максимума скорости реакции в область более высоких температур в соответствии с уравнением неизотермической кинетики [6]:
(1)
$\frac{{{{k}_{0}}}}{\beta } = \frac{E}{{RT_{{\max }}^{2}}}\exp \left( {\frac{E}{{R{{T}_{{\max }}}}}} \right).$Пересчет значений Tmax термического анализа реакций с кинетическими параметрами, приведенными в работе [2] на высокоскоростной нагрев, соответствующий условиям реальных топливоиспользующих процессов и установок (β = 104–106 град./с) по уравнению (1), показал, что в этом случае величины Tmax возрастут до значений, приведенных в табл. 1 и 2. В табл. 1 и 2 приведены также значение полуширины дифференциальной кривой скорости реакции и длительность выделения газообразных компонентов, рассчитанных по методике [6] при высокоскоростном нагреве. Полученные результаты подтверждают существенную зависимость характера исследуемых кинетических процессов от скорости изменения температуры газовой среды. Как видно из табл. 1 и 2 увеличение скорости нагрева парогазовой среды приводит к значительному сокращению длительности протекания индивидуальных стадий по мере повышения скорости нагрева, что как следствие приводит к их смещению относительно друг друга.
Таблица 1.
Расчетные значения индивидуальных реакций газовыделения при термическом разложении канско-ачинских углей со скоростью нагрева (104–106) град./с
Газовая компонента |
Марка угля | № стадии |
Температура максимума реакции, Tmax, °С | Полуширина дифференциальной кривой, ΔT, °С | Длительность выделения, τ, с |
---|---|---|---|---|---|
Н2 | Бородинский | 1 | 1205–1680 | 321–535 | 0.0642–0.001 |
2 | 1530–1950 | 255–530 | 0.05–0.00170 | ||
3 | 1150–1490 | 220–455 | 0.044–0.0009 | ||
Березовский | 1 | 1040–1400 | 240–625 | 0.047–0.0012 | |
2 | 910–1100 | 120–165 | 0.024–0.0030 | ||
Назаровский | 1 | 1320–1720 | 255–590 | 0.051–0.0011 | |
2 | 755–1290 | 140–325 | 0.027–0.0007 | ||
3 | 915–1345 | 120–205 | 0.023–0.0004 | ||
СО | Бородинский | 1 | 1225–2200 | 260–640 | 0.052–0.0012 |
2 | 1425–1730 | 190–255 | 0.038–0.0050 | ||
3 | 960–1395 | 285–875 | 0.057–0.0017 | ||
4 | 960–1600 | 430–845 | 0.086–0.0038 | ||
Березовский | 1 | 945–1760 | 210–560 | 0.041–0.0012 | |
2 | 895–1085 | 120–165 | 0.024–0.0032 | ||
3 | 1090–1590 | 310–935 | 0.062–0.0018 | ||
4 | 610–1595 | 230–780 | 0.046–0.0015 | ||
Назаровский | 1 | 860–1620 | 195–515 | 0.039–0.0010 | |
2 | 1105–1490 | 205–450 | 0.041–0.0009 | ||
3 | 1010–1565 | 340–860 | 0.068–0.0023 | ||
СО2 | Бородинский | 1 | 850–1495 | 165–360 | 0.033–0.0007 |
2 | 380–630 | 65–135 | 0.013–0.0003 | ||
Березовский | 1 | 700–1350 | 165–410 | 0.033–0.0008 | |
Назаровский | 1 | 1110–1415 | 265–440 | 0.053–0.0008 | |
2 | 890–1120 | 145–205 | 0.029–0.0004 | ||
3 | 1110–1495 | 240–570 | 0.047–0.0011 | ||
СН4 | Бородинский | 1 | 795–1175 | 260–860 | 0.051–0.0017 |
2 | 920–1315 | 255–715 | 0.050–0.0014 | ||
Березовский | 1 | 860–1430 | 150–320 | 0.030–0.00063 | |
2 | 625–1030 | 110–225 | 0.021–0.00050 | ||
Назаровский | 1 | 1180–1665 | 140–230 | 0.027–0.00050 | |
2 | 840–1675 | 210–585 | 0.042–0.00110 | ||
3 | 1055–1390 | 210–465 | 0.041–0.00090 | ||
Смола | Бородинский | 1 | 650–1150 | 130–295 | 0.026–0.00060 |
Березовский | 1 | 905–1845 | 225–590 | 0.045–0.00110 | |
Назаровский | 1 | 415–690 | 70–150 | 0.014–0.00030 |
Таблица 2.
Расчетные значения индивидуальных реакций газовыделения при термическом разложении кузнецких углей со скоростью нагрева (104–106) град./с
Газовая компонента |
Марка угля | № стадии |
Температура максимума реакции, Tmax, °С | Полуширина дифференциальной кривой, ΔT, °С | Длительность выделения, τ, с |
---|---|---|---|---|---|
Н2 | Кузнецкий Г | 1 | 1215–1800 | 160–300 | 0.032–0.00060 |
2 | 970–1450 | 135–250 | 0.026–0.00050 | ||
3 | 820–1230 | 115–210 | 0.023–0.00040 | ||
Кузнецкий СС | 1 | 820–1180 | 100–180 | 0.020–0.00035 | |
2 | 675–985 | 85–155 | 0.016–0.00030 | ||
Кузнецкий Т | 1 | 1275–1820 | 170–315 | 0.034–0.00060 | |
2 | 855–1250 | 110–200 | 0.021–0.00040 | ||
3 | 630–925 | 80–145 | 0.016–0.00030 | ||
СО | Кузнецкий Г | 1 | 915–1150 | 65–95 | 0.013–0.00020 |
2 | 840–1420 | 155–335 | 0.035–0.00070 | ||
3 | 595–915 | 90–165 | 0.018–0.00030 | ||
Кузнецкий СС | 1 | 960–1175 | 65–90 | 0.013–0.00020 | |
2 | 890–1325 | 120–225 | 0.023–0.00040 | ||
3 | 1070–1540 | 125–205 | 0.025–0.00040 | ||
4 | 1250–1610 | 255–595 | 0.050–0.00120 | ||
Кузнецкий Т | 1 | 890–1100 | 60–90 | 0.012–0.00020 | |
2 | 890–1440 | 145–310 | 0.029–0.00060 | ||
3 | 590–945 | 95–190 | 0.019–0.00040 | ||
СН4 | Кузнецкий Г | 1 | 810–910 | 25–35 | 0.005–0.00010 |
2 | 760–860 | 25–35 | 0.005–0.00010 | ||
3 | 720–835 | 30–40 | 0.006–0.00010 | ||
4 | 690–835 | 40–55 | 0.008–0.00010 | ||
5 | 660–885 | 60–100 | 0.012–0.00020 | ||
6 | 590–780 | 55–85 | 0.011–0.00020 | ||
Кузнецкий СС | 1 | 775–880 | 25–35 | 0.005–0.00010 | |
2 | 750–895 | 40–55 | 0.007–0.00010 | ||
3 | 665–870 | 55–90 | 0.011–0.00020 | ||
4 | 755–1045 | 80–140 | 0.016–0.00030 | ||
Кузнецкий Т | 1 | 760–860 | 25–35 | 0.005–0.00010 | |
2 | 690–830 | 35–50 | 0.007–0.00010 | ||
3 | 550–685 | 30–50 | 0.006–0.00010 | ||
4 | 595–775 | 50–80 | 0.010–0.00015 | ||
5 | 590–770 | 50–80 | 0.010–0.00016 | ||
Смола | Кузнецкий Г | 1 | 590–865 | 75–135 | 0.015–0.00030 |
Кузнецкий СС | 1 | 680–910 | 70–105 | 0.013–0.00020 | |
Кузнецкий Т | 1 | 885–1470 | 150–310 | 0.030–0.00060 |
Результаты расчетной оценки Tmax послужили основанием для выбора конечной температуры нагрева (Tk = 900°С) в эксперименте с высокоскоростным нагревом. При этом строго должно обеспечиваться условие Tk ≤ Tmax [7].
Экспериментальные работы выполнялись на бурых канско-ачинских и каменных кузнецких углях. Быстротекущий процесс газовыделения расчленялся во времени (отбор газов осуществлялся в газовые пипетки, предварительно вакуумированные и заполняющиеся газообразными продуктами поочередно) и хроматографически оценивалось содержание в суммарном газе отдельных газовых компонентов – CO, CO2, H2 и CH4. Скорость нагрева угольной пыли (δ < 100 мкм) в реакционной камере обеспечивалась порядка 104–106 град./с.
Оценка скорости нагрева (град./с) пылеугольных частиц в реакционном пространстве выполнялась по уравнению [8]
(2)
$\beta = \frac{{{{a}_{{\text{т}}}}{{\lambda }_{{\text{г}}}}}}{{{{\lambda }_{{\text{т}}}}}}\frac{{\Delta {{T}_{{{\text{г - ч}}}}}}}{{20{{r}^{2}}}},$ЭКСПЕРИМЕНТАЛЬНАЯ УСТАНОВКА И МЕТОДИКА ПРОВЕДЕНИЯ ИССЛЕДОВАНИЙ
Экспериментальная установка для исследования процессов термохимического превращения пылевидного твердого топлива в условиях высокоскоростного нагрева с вертикальной реакционной камерой представлена на рис. 1. Несмотря на значительное многообразие существующих лабораторных установок и методических подходов по исследованию процесса горения угля [9, 10] отсутствуют экспериментальные установки, обеспечивающие весь комплекс условий и режимных факторов термохимической обработки топлива, присущих реальным топливоиспользующим и теплотехнологическим устройствам (со скоростью нагрева более 103 град./с). Также особенностью разработанной экспериментальной установки является то, что она позволяет в рамках единого методического подхода выполнять раздельные исследования как процессов термического разложения, так и горения пылеугольных частиц в широком диапазоне изменения температур от 20 до 1500°С, коэффициентов избытка воздуха от 0.2 до 2.0 концентрации пылегазовоздушной смеси от 0.3 до 0.6 кг/кг и времени пребывания пылеугольных частиц в реакционной зоне от 0.5 до 5 с.
Рис. 1.
Принципиальная схема экспериментальной установки для высокотемпературной обработки твердого пылевидного топлива: 1 – баллон с инертным газом; 2 – регулятор расхода инертного газа; 3 – реактор для удаления кислорода на линии подачи инертного газа; 4 – вентилятор для подачи воздуха; 5 – ротаметр; 6 – теплообменник; 7 – распределительный тройник; 8 – аэромеханический пылепитатель; 9 – пылеугольная горелка; 10 – реакционная камера; 11 – хвостовая часть; 12 – приемный бункер; 13 – газоход; 14 – золоуловитель; 15 – дымосос; 16 – тягонапоромер; 17 – самописец (КСП-4); 18 – самописец (КСП-3); 19 – регулятор напряжения (РНО); 20 – устройство для отбора газообразных продуктов; 21 – обогреваемый пылеулавливающий циклон; 22 – водоохлаждаемый циклон для конденсации жидких продуктов деструкции; 23 – многоходовой кран; 24 – штатив газовых пипеток; 25 – газоанализатор; 26 – кран дозатор; 27 – перистальтический насос; 28 – газометр.
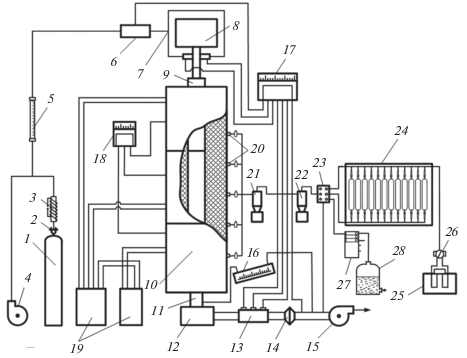
Основной частью экспериментальной установки является вертикальная цилиндрическая реакционная камера (10) длиной 2100 мм и диаметром 50 мм с электрическим компенсационным обогревом, что позволяет проводить исследования в стационарном режиме.
Угольная пыль поступает в реакционное пространство через тангенциальную горелку (9) из аэромеханического питателя пыли (8). Транспорт пыли к горелке осуществляется в зависимости от целей эксперимента либо инертным газом (аргон), либо воздухом предварительно нагретыми в теплообменнике (6). Расход газа определяется по ротаметру (5) марки РМ 0.04Ж.
Инертный газ для исследования процесса термической деструкции пылевидного топлива подается из газового баллона (1) через регулятор расхода (2) и реактор для удаления кислорода (3) из линии подачи инертного газа. Для исследования процессов горения угля в качестве первичного и вторичного воздуха используются воздух, нагнетаемый вентилятором (4). Расход воздуха и соответственно коэффициент избытка воздуха (α) в реакционной камере регулируются изменением положения шибера, расположенного на всасе вентилятора.
Температурный режим работы реакционной камеры определяется величиной подаваемого напряжения, регулирование значения которого осуществляется РНО (19). Уголь, прошедший термическую обработку, поступает в хвостовую часть (11) реакционной камеры, охлаждается и накапливается в приемном бункере (12) инерционного типа, из которого при необходимости осуществляется отбор нелетучих остатков и золовых частиц на анализ.
Газообразные продукты далее поступают в газоход (13), в котором остаточная дисперсная фаза улавливается в золоуловителе (14) с тканевым фильтром, после чего удаляются в атмосферу дымососом (15). Разряжение, создаваемое дымососом, измеряется тягонапоромером марки ТНЖ-Н (16) с классом точности 1.5 и поддерживается порядка 0.1–0.2 мм рт. ст.
Для исследования процессов термического разложения топлива по длине реакционной камеры на равном расстоянии (через 350 мм) организовано пять газозаборных точек (20). Выделяющие из угля парогазовые продукты обеспыливаются в обогреваемом фильтре-циклоне (21) и поступают на водоохлаждаемый циклон (22), в котором происходит конденсация жидких продуктов (смол) и быстрое охлаждение газа-пиролиза. Для отвода и сброса в атмосферу газообразных продуктов из реакционного пространства и организации рециркуляции солевого раствора из газометра (28) предусмотрен многоходовой кран (23).
С целью количественной оценки газообразных продуктов реакции многоходовой кран может быть переведен в позицию, при которой происходит переключение линии отвода газа от перистальтического насоса (27) на линию подачи газа на штатив газовых пипеток (24), заполненных солевым раствором. При этом рециркуляция солевого раствора переводится на отсос раствора из газовых пипеток. Газ из циклона (22) за счет разряжения создаваемого дымососом и уменьшения уровня солевого раствора в газовых пипетках заполняет освободившееся пространство. Выбор пипетки для заполнения газом осуществляется открытием кранов пипетки. Далее газ из газовых пипеток с помощью крана дозатора подается на хроматографический газоанализатор (26) марки 3700 (ЛХМ-80).
Регистрация температурного режима работы реакционной камеры осуществляется с помощью платино-платиновых термопар (ПП68), соединенных с регистрирующим прибором КСП-4 (18). Слежение за температурой вторичного воздуха и температурой газов в газоходе выполняется с помощью хромель-алюмелевых термопар (ХА) соединенных с регистрирующим прибором КСП-3 (17).
Пылеугольная горелка установлена в верхней части реакционной камеры (5) экспериментальной установки. Корпус горелки (3) изготовлен из нержавеющей стали. Нижняя часть корпуса выполнена в виде расширяющегося конуса, что обеспечивает равномерное распределение пылегазовоздушной смеси по сечению реакционной камеры. Угольная пыль в смеси с первичным транспортирующим газообразным агентом из аэромеханического питателя поступает в горелку по пылепроводу (1). Подогретый инертный газ (для организации процесса термического разложения) или вторичный воздух (для организации процесса термооокислительной деструкции (горения)) подводятся тангенциально, что обеспечивает хорошее перемешивание топлива с газом и, как следствие, приводит к увеличению времени пребывания пылегазовоздушной смеси в зоне горелке. В конусной части горелки вращательное движение пылеугольного потока интенсивно изменяется на прямолинейное, что существенно упрощает расчет времени пребывания угольной частицы в реакционной зоне установки. Расход топлива через горелку определялся с помощью предварительной тарировки пылепитателя и контролировался объемно-весовым методом [9]. Расчетное значение расхода топлива составляло в среднем 0.2–0.3 г/с.
При оценке времени пребывания угольных частиц в камере термообработки при заданной температуре и плотности среды учитывалась скорость витания частиц, которая определялась по формуле
где d – размер пылеугольных частиц, м; ρт – действительная плотность топлива, кг/м3; g – ускорение свободного падения, м/с2; μ – динамическая вязкость среды, кг/(м ⋅ с).Общая скорость частицы определялась как сумма скорости витания wв и скорости потока wп
Расчет скорости потока производился при подаче газов в камеру термообработки в количестве 1 × 10–4 м3/с.
Расчетные значения скорости витания и времени пребывания пылеугольных частиц в камере термообработки приведены в табл. 3.
Таблица 3.
Расчетные значения скорости витания и времени пребывания частиц угля
Размер частиц, мкм |
Температура обработки, °С |
Скорость витания, м/с |
Общая скорость, м/с |
Время пребывания, с |
---|---|---|---|---|
63 | 100 | 0.102 | 0.171 | 12.28 |
140 | 0.093 | 0.170 | 12.35 | |
170 | 0.086 | 0.169 | 12.43 | |
200 | 0.081 | 0.171 | 12.28 | |
300 | 0.067 | 0.177 | 11.86 | |
400 | 0.057 | 0.187 | 11.23 | |
500 | 0.050 | 0.210 | 10.40 | |
600 | 0.044 | 0.235 | 9.45 | |
700 | 0.038 | 0.266 | 8.34 | |
800 | 0.034 | 0.304 | 7.07 | |
900 | 0.031 | 0.346 | 5.64 | |
100 | 100 | 0.256 | 0.325 | 6.46 |
140 | 0.231 | 0.308 | 6.82 | |
170 | 0.216 | 0.299 | 7.02 | |
200 | 0.202 | 0.292 | 7.19 | |
300 | 0.167 | 0.277 | 7.58 | |
400 | 0.140 | 0.270 | 7.78 | |
500 | 0.123 | 0.258 | 8.04 | |
600 | 0.108 | 0.250 | 8.21 | |
700 | 0.095 | 0.244 | 8.36 | |
800 | 0.083 | 0.239 | 8.49 | |
900 | 0.073 | 0.234 | 8.61 | |
160 | 100 | 0.641 | 0.710 | 2.96 |
140 | 0.579 | 0.656 | 3.20 | |
170 | 0.540 | 0.623 | 3.37 | |
200 | 0.506 | 0.596 | 3.52 | |
300 | 0.417 | 0.527 | 3.98 | |
400 | 0.355 | 0.485 | 4.33 | |
500 | 0.312 | 0.446 | 4.49 | |
600 | 0.273 | 0.416 | 4.68 | |
700 | 0.241 | 0.391 | 4.83 | |
800 | 0.213 | 0.369 | 4.96 | |
900 | 0.189 | 0.350 | 5.08 |
Исследования проводились на полифракции и на монофракциях узких диапазонов размера частиц d = 0–63 мкм; d = 63–100 мкм; d = 100–160 мкм угля.
СОПОСТАВЛЕНИЕ РЕЗУЛЬТАТОВ КОМПЛЕКСНОГО ТЕРМИЧЕСКОГО АНАЛИЗА И ЛАБОРАТОРНОГО ЭКСПЕРИМЕНТА ВЫСОКОСКОРОСТНОГО НАГРЕВА ПЫЛЕВИДНОГО ТОПЛИВА
Для обоснования методики определения кинетических параметров различных процессов термохимической обработки по результатам комплексного термического анализа твердого органического топлива, изложенной в работе [2], были выполнены исследования процессов сушки, термического разложения и горения нелетучего коксового остатка пылевидного угля в условиях высокоскоростного нагрева (104–106 град./с). Решение данной задачи позволит обосновать применимость комплексного термического анализа для получения данных о реакционной способности различных стадий термохимического превращения угля в пылевидном состоянии, а также скорректировать и оптимизировать условия его проведения при низких скоростях нагрева (5–20 град./мин) и температур (до 1500°С).
Исследование процесса испарения влаги осуществлялось при следующих условиях: варьировались размер пылеугольных частиц: 0–63 мкм, 63–160 мкм и полифракция, а также температура термообработки: 200, 250, 300 и 400°С и время пребывания в реакционном пространстве экспериментальной установки от 1 до 4.5 с. Так как на настоящий момент отсутствует стандартная методика определения химически связанной влаги в топливе, то при высокоскоростном нагреве у нелетучих продуктов термообработки производили оценку содержания только гигроскопической влаги. Остаточная влажность пылеугольных частиц определялась в сушильном шкафу по ГОСТ 8719-90.
Полученные экспериментальные данные по изменению содержания влаги в топливе при постоянных температурах и различном времени пребывания угольных частиц в камере термообработки позволяют выполнить количественную оценку кинетических характеристик процесса испарения влаги из топлива.
С этой целью результаты обработки экспериментальных данных представлялись в форме следующей зависимости: $\ln \left( {\frac{W}{{W - \Delta W}}} \right) = k\tau $ или Wi = W exp(–kτ), где W – начальная влажность исходного топлива, %; ΔW – изменение влажности при термообработке, %; Wi – текущее значение влажности угля, %; k – константа скорости процесса сушки топлива, 1/с; τ – время термической обработки, с.
Из данной зависимости видно, что в координатах $\ln \left( {\frac{W}{{W - \Delta W}}} \right) = f\left( \tau \right)$ экспериментальные точки должны подчиняться линейному закону. На рис. 2 на примере термообработки полифракции бородинского угля приведены зависимости $\ln \left( {\frac{W}{{W - \Delta W}}} \right)$ от времени пребывания в камере термообработки при различных значениях температуры. Как видно из рисунка, экспериментальные точки удовлетворительно описываются прямыми линиями в рассматриваемых координатах.
Рис. 2.
Зависимость изменения $\ln \left( {\frac{W}{{W - \Delta W}}} \right)$ от времени термообработки для полифракции бородинского угля; температура обработки, °С: ⚪ – 200; Δ – 250; ◇ – 300; ◻ – 400.
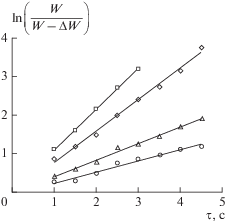
Для определения энергии связи (E) влаги с топливом и предэкспоненциального множителя (k0) по опытным данным выполнялось построение графических зависимостей ln k от обратной абсолютной температуры процесса термообработки (1/T), при различных фиксированных значениях времени пребывания частиц в камере термообработки τ.
На рис. 3 приведена зависимость ln k = f(1/T) для полифракции бородинского угля со средним размером частиц d = 100 мкм. Из рисунка видно, что для рассматриваемых моментов времени τ экспериментальные точки удовлетворительно описываются уравнением прямой линии, а энергия связи процесса испарения влаги может быть найдена как тангенс угла наклона этой линии к оси абсцисс, E = tg α.
Рис. 3.
Зависимость изменения ln k процесса испарения влаги бородинского угля от обратной температуры процесса; размер пылеугольных частиц, мкм: Δ – 63–160; ◇ – полифракция; ⚪ – 0–63.
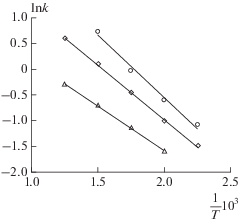
Определяемая по рис. 3 энергия связи имеет значение E = 18.083 кДж/моль. Предэкспоненциальный множитель k0 измеряется в единицах обратного времени 1/с и находится из закона Аррениуса. Применительно к данным рис. 3 значение k0 составляет 22.5 1/с.
Для детального анализа протекания процесса испарения влаги из пылеугольных частиц в условиях высокоскоростного нагрева были проведены исследования монофракций на примере бородинского угля. Конечной целью данного исследования являлось определение кинетических параметров процесса испарения влаги из пылеугольных частиц разного размера.
На рис. 4 и 5 представлены зависимости в координатах $\ln \left( {\frac{W}{{W - \Delta W}}} \right) = f\left( \tau \right)$ для фракций с размером частиц d = 0–63 мкм и d = 63–160 мкм. Данные зависимости используются для оценки кинетических характеристик процесса испарения влаги. Анализ полученных зависимостей (см. рис. 4 и 5) показывает, что значения энергии связи влаги с топливом (E) фактически не зависят от размера пылеугольных частиц, так как графики, построенные в координатах ln k = f(1/T) для различных фракций, проходят параллельно друг другу, т.е. с одинаковыми углами наклона (tg α = const).
Рис. 4.
Изменение $\ln \left( {\frac{W}{{W - \Delta W}}} \right)$ от времени термообработки для монофракций ирша-бородинского угля с размером частиц от 0 до 63 мкм: температура обработки, °С: ⚪ – 200; Δ – 250; ◇ – 300.
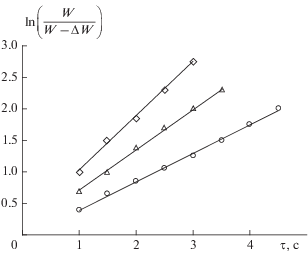
Рис. 5.
Изменение $\ln \left( {\frac{W}{{W - \Delta W}}} \right)$ от времени термообработки для монофракций ирша-бородинского угля с размером частиц от 63 до 160 мкм: температура обработки, °С: ⚪ – 200; Δ – 250; ◇ – 300.
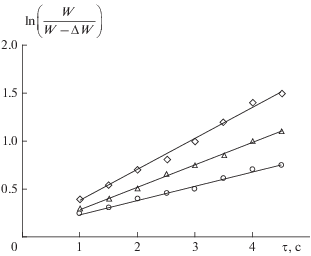
Несовпадение экспериментальных данных и их параллельное расположение указывает на различные значения предэкспоненциального множителя k0. Более низкое значение k0 характерно для крупных частиц и объясняется наличием у угольных частиц этих фракций капиллярного испарения, которое протекает с более медленными скоростями, чем поверхностное испарение [10]. Наличие капиллярного испарения в мелких фракциях d < 100 мкм имеет незначительное влияние на общую картину процесса испарения влаги и поэтому k0 для этих частиц принимает максимальное значение.
Сопоставление констант скоростей процесса испарения влаги из канско-ачинских углей в условиях комплексного термического анализа [2] и высокоскоростного нагрева представлено в табл. 4. Анализ полученных данных по исследованию кинетики сушки в различных условиях термообработки топлива позволяет констатировать, что реакционный механизм и профиль кривых процесса сушки пылевидного топлива остаются неизменными при варьировании соответственно скорости нагрева.
Таблица 4.
Константы скоростей процесса испарения влаги при термической обработке полифракции канско-ачинских углей (tк = 900°С)
Марка топлива |
Константа скорости сушки, K900, 1/мин | |
---|---|---|
5 град./мин [2] | 104–106 град./с | |
Березовский сажистый | 0.39 | 0.51 |
Березовский окисленный | 0.31 | 0.60 |
Березовский рядовой | 0.92 | 1.10 |
Бородинский | 0.79 | 0.92 |
Назаровский | 0.88 | 1.04 |
Для проверки адекватности принятой в работе кинетической модели исследуемого процесса испарения влаги проведено статистическое сопоставление результатов комплексного термического анализа и высокоскоростного нагрева топлива. Установлено, что их относительная погрешность при 95%-ном доверительном интервале (по Стьюденту) составляет не более 2–3%.
При высокоскоростном нагреве пылеугольной частицы скорость выхода, W, отдельных газовых компонентов для произвольного порядка реакции, n, определяется выражением [2]:
(5)
$W = \frac{{dC}}{{d\tau }} = k{{\left[ {\frac{{C_{0}^{{n - 1}}}}{{1 + \left( {n - 1} \right)C_{0}^{{n - 1}}k\tau }}} \right]}^{{\frac{n}{{n - 1}}}}},$(6)
$\frac{1}{{{{W}^{{\frac{n}{{n - 1}}}}}}} = \left( {n - 1} \right){{k}^{{\frac{1}{n}}}}\tau + \frac{1}{{C_{0}^{{n - 1}}{{k}^{{\frac{{n - 1}}{n}}}}}}.$В уравнениях (5) и (6): C0 – суммарное количество выделяющегося при Tк рассчитываемого газового компонента за весь период изотермической выдержки; С – текущая концентрация газового компонента к расчетному моменту времени τ; k – константа скорости процесса, 1/мин. В общем случае, зависимость $\frac{1}{{{{W}^{{\frac{n}{{n - 1}}}}}}} = f\left( \tau \right)$ – прямая линия, тангенс угла наклона которой определяется величиной k.
Применимость выражений (5) и (6) для оценки скорости реакций газовыделения обеспечена достижением условий проведения эксперимента в строго кинетической области при отсутствии диффузионных осложнений, когда количества прореагировавшего вещества на единице поверхности в единицу времени (“поток реакции”) существенно превышает диффузионной поток через слой продукта [6].
Кривые динамики выделения индивидуальных компонентов суммарного газа при термическом разложении бородинского угля приведены на рис. 6 и 7. Здесь и во всех последующих графиках представлены экспериментальные зависимости, полученные при температуре процесса от 500 до 1000°С с интервалом через 100°С.
Рис. 6.
Динамика выделения индивидуальных газовых компонентов при термическом разложении бородинского угля в условиях высокоскоростного нагрева: (а) СO2; (б) CO; (в) CH4; температура обработки: ◇ – 500°С; ◻ – 600°С; Δ – 700°С; × – 800°С; * – 900°С; ⚪ – 1000°С.
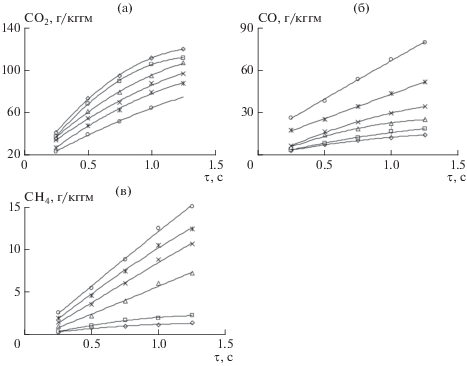
Рис. 7.
Динамика выделения индивидуальных газовых компонентов при термическом разложении бородинского угля в условиях высокоскоростного нагрева: (а) H2; (б) суммарный выход газовых компонентов ($\sum {{{C}_{i}}} $); температура обработки: ◇ – 500°С; ◻ – 600°С; Δ – 700°С; × – 800°С; * – 900°С; ⚪ – 1000°С.
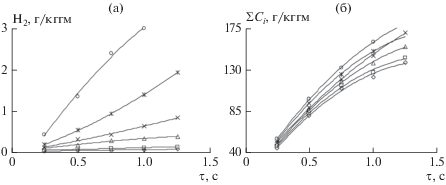
Полученные экспериментальные данные по динамике термического разложения бородинского угля в условиях высокоскоростного нагрева отражают сложный характер зависимостей выхода индивидуальных компонентов суммарного газа как от времени, так и от температуры протекания процесса. При этом характер соответствующих закономерностей различен для каждого из компонентов. Например, в первые 1.5–2 с массовый выход CO2 (рис. 6а) снижается с повышением температуры, а у CO, CH4 и H2 (рис. 6б, 6в и рис. 7а) возрастает.
Конечные выходы CO, CO2, CH4 и H2, как иллюстрируют рис. 8 и 9 возрастают с повышением температуры процесса термообработки.
Рис. 8.
Конечный выход индивидуальных газовых компонентов при термическом разложении бородинского угля в условиях высокоскоростного нагрева: ◇ – CO2; ◻ – CO; Δ – CH4; × – H2.
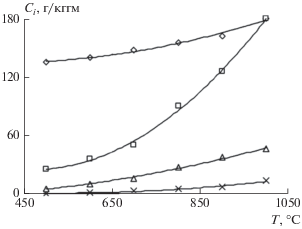
Рис. 9.
Конечный выход летучих веществ при термическом разложении бородинского угля в условиях высокоскоростного нагрева: ◻ – выход летучих веществ; ◇ – сумма индивидуальных газообразных компонентов; Δ – смоловыделение.
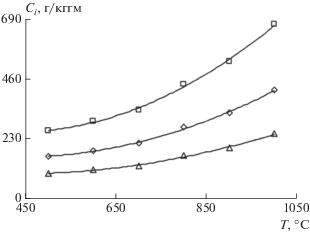
На рисунках 10 и 11 представлена расчетная динамика (по уравнению 5) суммарного выхода индивидуальных газообразных компонентов (CO, H2 и CH4) на примере термического разложения бородинского и кузнецкого Г углей в эксперименте с высокоскоростным нагревом (tк = 900°С). Здесь же приведены результаты выделения из суммарных кривых индивидуальных реакций 1-го порядка. В табл. 5 представлено сопоставление кинетических констант, определенных в условиях комплексного термического анализа (β = 5 град./мин) и в опытах с высокоскоростным нагревом (β = = 104–106 град./с).
Рис. 10.
Динамика газовыделения при термическом разложении бородинского угля в условиях высокоскоростного нагрева (β = 104–105 град./с) до tк = 900°С: (а) СО; (б) H2; (в) CH4.
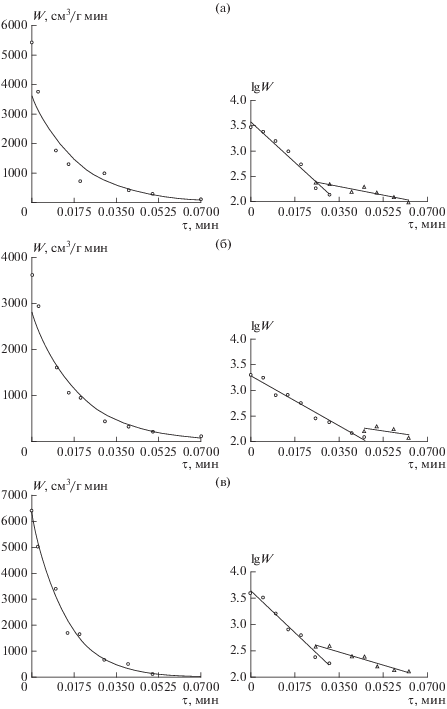
Рис. 11.
Динамика газовыделения при термическом разложении кузнецкого угля марки Г в условиях высокоскоростного нагрева (β = 104–105 град./с) до tк = 900°С: (а) СО; (б) H2; (в) CH4.
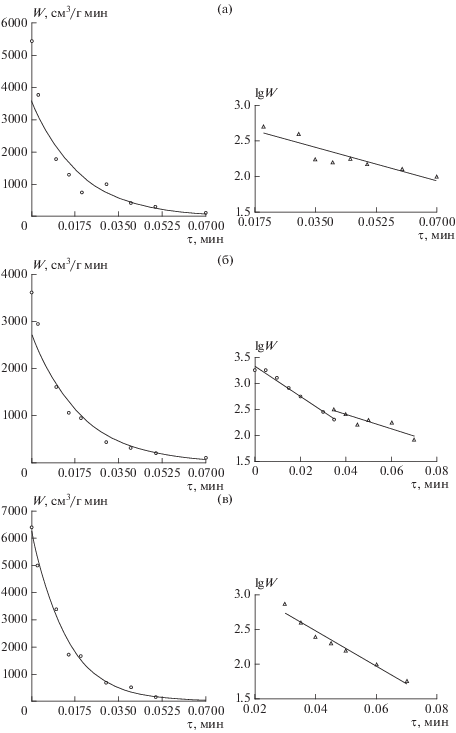
Таблица 5.
Константы скоростей индивидуальных реакций, ответственных за выделение индивидуальных летучих компонентов при термическом разложении канско-ачинских углей и кузнецких углей (tк = 900°С)
Марка топлива |
№ стадии |
Константа скорости, К900, 1/мин | |||||
---|---|---|---|---|---|---|---|
СО | H2 | CH4 | |||||
5 град./мин | 104–106 град./с | 5 град/мин | 104–106 град./с | 5 град./мин | 104–106 град./с | ||
Бородинский | 1 | 3.63 | 4.55 | 1.49 × 10–1 | 3.3 × 10–1 | 8.8 × 10–1 | – |
2 | – | – | – | – | 1.87 | 2.12 | |
3 | – | – | 1.27 × 10–1 | 2.7 × 10–1 | – | – | |
4 | – | – | – | – | – | – | |
Березовский | 1 | 4.18 | 3.97 | 2.28 | 2.81 | 4.06 × 101 | 5.3 × 101 |
2 | – | – | 3.48 × 10–1 | – | 2.45 | 2.15 | |
3 | 2.42 | 2.66 | – | – | – | – | |
4 | – | – | – | – | – | – | |
Назаровский | 1 | 4.15 × 10–1 | 4.01 × 10–1 | 1.79 | 1.65 | 3.45 × 10–1 | 5.07 × 10–1 |
2 | 1.72 × 10–1 | – | 7.07 | 6.89 | 1.9 | 2.1 | |
3 | 1.78 | 2.44 | – | – | – | – | |
4 | – | – | – | – | – | – | |
Кузнецкий Г | 1 | 1.31 × 102 | 1.22 × 102 | – | – | 2.3 × 103 | – |
2 | – | – | 5.89 × 101 | 7.15 × 101 | 0.3 × 103 | 0.5 × 102 | |
3 | 2.92 | 4.6 | – | – | 2.3 × 103 | 0.11 × 103 | |
4 | – | – | 8.47 | 8.00 | 5.0 × 103 | – | |
5 | – | – | – | – | 3.6 × 103 | – | |
6 | – | – | – | – | 4.7 × 102 | – | |
Кузнецкий СС | 1 | – | – | – | – | 1.6 × 103 | 8.9 × 102 |
2 | 2.05 × 10–1 | 1.61 × 10–1 | 6.73 × 101 | 5.59 × 101 | 5.1 × 102 | – | |
3 | 2.42 | 2.38 | – | – | 4.9 × 102 | 5.0 × 102 | |
4 | – | – | 7.38 | 7.15 | 0.3 × 102 | – | |
Кузнецкий Т | 1 | 9.0 × 101 | 8.8 × 101 | 1.37 × 102 | 1.11 × 102 | 2.7 × 103 | |
2 | 1.91 | – | 4.21 | 3.99 | 2.9 × 103 | 9.5 × 102 | |
3 | 5.1 | 6.4 | – | – | 5.3 × 104 | 4.2 × 104 | |
4 | – | – | – | – | 2.8 × 103 | – | |
5 | – | – | – | – | 2.6 × 103 | – |
Так, при высокоскоростном нагреве в большинстве случаев отмечены две индивидуальные реакции, ответственные за выделение CH4, да и то с несовпадающими с медленным нагревом численными значениями их констант скоростей.
Выделение H2 и СО характеризуется, в отличие от CH4, практически постоянным реакционным механизмом при изменении скорости нагрева на 5–6 порядков. Основной причиной аномалии по CH4 с большой долей вероятности следует считать вторичные процессы, сопутствующие смоловыделению, с которым связан выход углеводородных газов и CH4 в первую очередь [11].
ОБСУЖДЕНИЕ РЕЗУЛЬТАТОВ ИССЛЕДОВАНИЯ
Из приведенного выше сопоставления результатов комплексного термического анализа при медленном нагреве (∼5 град./мин) [2] с экспериментальными данными высокоскоростного (∼104–106 град./с) нагрева, следует важный вывод неизменности механизма термической деструкции угольного вещества при экстремальных значениях скоростей нагрева. Обнаруженное в эксперименте отклонение по значению констант скорости выделения метана (CH4), на наш взгляд, не может являться основанием для пересмотра этой концепции при термическом разложении органической массы угля.
Для определения кинетических констант процесса выгорания нелетучих остатков термического разложения канско-ачинских и кузнецких углей пробы коксовых частиц различного фракционного состава: полифракция; 63–100 мкм; 100–1000 мкм; 1000–3000 мкм сжигались при четырех значениях температуры: 1040, 1180, 1315 и 1455°С. Время пребывания коксовых частиц в реакционном пространстве экспериментальной установки составляло 0.85 с. Температурно-временной режим обработки коксовых частиц, а также коэффициент избытка воздуха в реакционном пространстве выбирались исходя из условий проведения экспериментальных исследований максимально близких к условиям реальных топливоиспользующих устройств, в частности топочных камер современных котельных агрегатов.
Типичные результаты интенсивности выгорания коксовых частиц на примере бородинского и кузнецкого газового углей представлены на рис. 12.
Рис. 12.
Интенсивность выгорания коксовых частиц (размер 63–100 мкм) бородинского (а) и кузнецкого Г (б) углей при различной температуре обработки, °С: ⚪ – 1040; ◻ – 1180; Δ – 1315; ◇ – 1455.
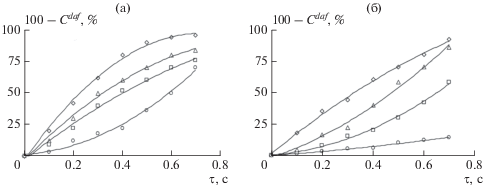
Результаты обработки экспериментального материала по интенсивности выгорания коксовых частиц различного фракционного состава представлены в координатах $\lg k = f\left( {\frac{1}{T}{{{10}}^{3}}} \right)$, которые затем использовались для нахождения видимых кинетических констант. Данные зависимости на примере выгорания коксовых остатков бородинского угля и кузнецкого газового угля представлены на рис. 13.
Рис. 13.
Видимая константа скорости горения различных фракций коксовых частиц бородинского (а) и кузнецкого Г (б) углей: ⚪ – полифракция; ◻ – 63–100 мкм; Δ – 100–1000 мкм; ◇ – 1000–3000 мкм.
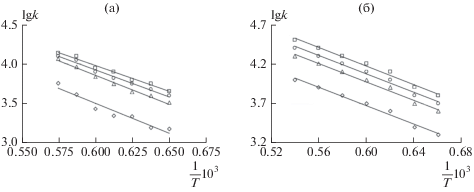
Сопоставление констант скоростей процесса выгорания коксовой основы из канско-ачинских и кузнецких углей в условиях комплексного термического анализа и высокоскоростного нагрева представлено на рис. 14 и 15, в табл. 6 .
Рис. 14.
Видимая константа скорости горения коксовых частиц (полифракция) канско-ачинских углей в условиях высокоскоростного нагрева: ⚪ – Бородинский; ◻ – Березовский; Δ – Назаровский.
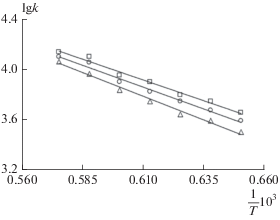
Рис. 15.
Видимая константа скорости горения коксовых частиц (полифракция) кузнецких углей в условиях высокоскоростного нагрева: ⚪ – Кузнецкий Г; ◻ – Кузнецкий СС; Δ – Кузнецкий Т.
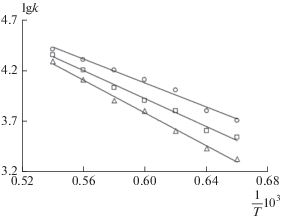
Таблица 6.
Константы скоростей процесса выгорания коксовой (нелетучей) основы полифракции канско-ачинских и кузнецких углей (tк = 900°С)
Марка топлива | Константа скорости выгорания коксовой основы, К900, м/мин | |
---|---|---|
5 град./мин [2] | 104–106 град./с | |
Березовский рядовой | 2.44 × 102 | 2.74 × 102 |
Березовский окисленный | 7.86 × 102 | 8.22 × 102 |
Березовский сажистый | 3.74 × 102 | 3.51 × 102 |
Бородинский | 9.95 × 101 | 1.92 × 102 |
Назаровский | 3.68 × 102 | 4.03 × 102 |
Кузнецкий Г | 2.42 × 102 | 2.32 × 102 |
Кузнецкий СС | 5.36 × 102 | 5.84 × 102 |
Кузнецкий Т | 5.97 × 102 | 6.45 × 102 |
Анализ полученных данных по исследованию кинетики выгорания нелетучих остатков в различных условиях термообработки топлива позволяет констатировать, что реакционный механизм и профиль кривых процесса выгорания коксового остатка пылевидного топлива остаются неизменными при варьировании соответственно скорости нагрева в широком диапазоне.
Относительная погрешность при 95%-ном доверительном интервале (по Стьюденту) составляет не более 5–7%, что свидетельствует об адекватности принятой в работе кинетической модели исследуемого процесса выгорания нелетучих (коксовых) остатков в условиях комплексного термического анализа и высокоскоростного нагрева топлива.
К совокупности качественных и количественных характеристик продуктов термообработки можно отнести теплотехнические и реакционные характеристики полукокса, физико-химические свойства его минеральной части, состав газообразных продуктов термического разложения [14].
Обобщение полученных реакционных характеристик от содержания углерода на горючую массу Cdaf представлено на рис. 16 и 17.
Рис. 16.
Кинетические параметры основного периода выхода летучих веществ (смоловыделения) энергетических углей: ⚪ – энергия активации (E); Δ – вероятностный фактор (k0).
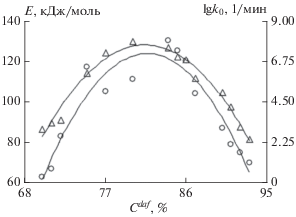
Рис. 17.
Кинетические параметры горения коксового остатка энергетических углей: ⚪ – Е; Δ – k0 канско-ачинских углей; ⚫ и ▲ – кузнецких углей.
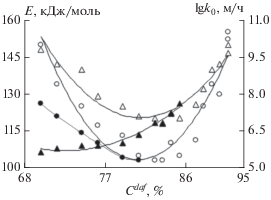
Обращает на себя внимание существенные изменения значений энергии активации (Е) и вероятностного фактора (k0) как основного периода выхода летучих веществ (периода смоловыделения), так и горения коксовых остатков от качества исходного угля, в частности, главным образом от содержания углерода в топливе Cdaf.
Из приведенных на рис. 16 и 17 данных следует, что влияние степени метаморфизма на кинетические параметры в случае выхода летучих веществ и горения коксовых остатков канско-ачинских углей носит экстремальный характер с точкой экстремума Cdaf = 82%. Характер изменения реакционной способности (E и k0) энергетических углей различной стадии метаморфизма подтверждает предположение о том, что реакционный механизм и профиль кинетических кривых остаются неизменными при экстремальных скоростях нагрева (в пределах 10–2–106 град./с).
При определении кинетических параметров основного периода выделения летучих веществ и горения кокосового остатка энергетических углей выявлена связь энергии активации этих процессов с размерами элементарных структурных единиц (Rлок, А°). Этой зависимостью подтверждается влияние молекулярного строения исходного угольного вещества на характер образования и выделения летучих веществ, а также горения кокосовых остатков твердых органических топлив. Отмечается тенденция возрастания величины энергии активации (Е) исследуемых процессов с увеличением размеров элементарных структурных единиц.
Несмотря на значительное многообразие вычислительных программ для обработки результатов термоаналитического эксперимента, каждая из них является носителем тех методических подходов, которые положены в основу расчетного алгоритма. При этом мощный математический аппарат таких вычислительных комплексов, их возможности ограничены необходимостью учета наличия специфических особенностей выполнения термоаналитического эксперимента в силу существенного различия технических, теплофизических и реакционных свойств испытуемого топлива. Данная связь находит свое отражение как в изменении измерительной схемы и конструкции экспериментальной установки, так и в методиках проведения анализа и обработки получаемых результатов. В связи с тем, что в реальном эксперименте всегда присутствует случайная составляющая погрешности измерения, целесообразно при проведении экспериментальных работ выполнить проверку устойчивости экспериментально-расчетного алгоритма к воздействию случайного шума с целью получения предельных оценок погрешностей расчета кинетических параметров. Случайный шум моделировался программно с помощью генератора случайных чисел. Результаты обработки более чем 450 вычислений с различным уровнем шума приведены на рис. 18 и 19.
Рис. 18.
Зависимость погрешности определения энергии активации от уровня случайного шума (β = = 5 град./мин): ⚪ – kд = 13.2 град./с; ◻ – kд = 9.8 град./с; Δ – kд = 3.2 град./с; × – kд = 6.5 град./с.
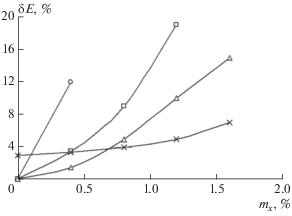
На рис. 18 показаны зависимости математического ожидания относительной погрешности определения энергии активации (δЕ) от математического ожидания уровня шума в процентах (mx) к максимальной степени превращения. Параметром оценки кривых выступает коэффициент дискретности (kд) численно равный отношению величины температурного интервала протекания процесса к периоду регистрации информации при проведении комплексного термического анализа (темп нагрева фиксированный – β = 5 град./мин).
Из представленных результатов следует, что для выбранного темпа нагрева (исходя из принципа идентичности экспериментальным условиям проведения комплексного термического анализа) существует область коэффициентов дискретности, соответствующая устойчивому решению задачи с минимальными погрешностями расчета кинетических параметров. Обобщение этих результатов на произвольные темпы нагрева показано на рис. 19, где заштрихованная область соответствует области устойчивого решения обратной кинетической задачи. Все приведенные результаты получены с использованием предварительного интерполяционного сглаживания исходных данных.
ЗАКЛЮЧЕНИЕ
1. Сопоставлением значений видимых констант скорости термохимического превращения угля, полученных при низких скоростях нагрева (β = 5–20 град./мин), присущих условиям комплексного термического анализа, с экспериментом при высокоскоростном нагреве топлива (β = 104–106 град./с) в лабораторных условиях, присущих условиям реальных топливоиспользующих установок, показана неизменность механизмов отдельных стадий процесса горения угольного вещества (сушки, термической деструкции и горения нелетучего остатка) при экстремальных изменениях значений скорости нагрева, что позволяет рекомендовать комплексный метод термического анализа твердого органического топлива в неизотермических условиях для объективной и адекватной оценки реакционной способности энергетических углей. Относительная погрешность реакционных характеристик, полученных методом комплексного термического анализа угля и на установках его высокоскоростного нагрева при 95%-ном доверительном интервале (по Стьюденту), составляет не более 5–7%.
2. Установлено, что основная масса летучих веществ канско-ачинских углей представлена смолами (соотношение “смола–газ” составляет 0.6–2.4). Значение кажущихся констант горения коксовой основы E и k0 сопоставимы с таковыми для микрокомпонентов группы витринита каменных углей с содержанием углерода на горючую массу ∼72% и составляют соответственно: Eсм = 50.3–83.8 кДж/моль; k0 см = 4 × 102–3 × 105 1/мин и E = = 104.8–217.9 кДж/моль; k0 = 3 × 104–5 × 1014 м/ч. Влияние размера угольных частиц на значения E и k0 ощутимо сказывается при увеличении размера более 250–300 мкм (смоловыделение) и при размерах частиц более 2000 мкм (горение нелетучего остатка) и определяется диффузионным осложнением. Предельный размер буроугольных частиц, вокруг которых образуется фронт горючих летучих, составляет ∼250 мкм. Длительность выделения летучих веществ сопоставима с временем пребывания газов в зоне активного горения топочных камер паровых котлов, что указывает на необходимость уточнения теплового расчета топочных камер при сжигании бурых углей с раздельной оценкой длительности выделения летучих веществ и горения коксового остатка.
3. Соответствие значений E и k0, полученных методом комплексного термического анализа результатам обработки испытаний лабораторной установки по высокоскоростному нагреву пылевидного топлива, позволяет использовать кинетические характеристики, отражающие реакционную способность твердого органического топлива в расчетах выгорания пылеугольного факела. При расчете длительности выделения и выгорания горючих компонентов летучих веществ (метана, оксида углерода), а также при определении длительности выгорания коксовой основы угля, данные лабораторных исследований по кинетике высокоскоростного нагрева совместно с кинетическими характеристиками (результаты комплексного термического анализа) могут быть использованы для объяснения и обоснования природы тепловых потерь с химическим и механическим недожогом.
4. Исследование кривых выгорания коксовых остатков показывает, что при скоростях нагрева менее 103 град./с выгорание кокса завершается в период прогрева частицы. При больших скоростях нагрева время выгорания коксовых частиц складывается из неизотермической и изотермической составляющих. Анализ экспериментальных данных по исследованию кинетики различных этапов термохимического превращения пылевидного топлива позволяет констатировать, что реакционный механизм и профиль кривых остаются неизменными при экстремальных скоростях нагрева (в пределах 10–2–106 град./с), что позволяет рекомендовать комплексный термический анализ для оценки реакционной способности энергетических углей.
Список литературы
Глинина О.И. Второй международный форум “Российская энергетическая неделя” // Уголь. 2019. № 2. С. 4–10.
Бойко Е.А. Реакционная способность энергетических углей // Красноярск: ИПЦ СФУ, 2011. С. 606.
Федорова Н.И., Хицова Л.М., Исмагилов З.Р. Термогравиметрическое исследование инертинитовых фракций каменных углей // Химия в интересах устойчивого развития. 2019. Т. 27. № 4. С. 421–429.
Моисеева К.М., Крайнов А.Ю. Моделирование распространения пламени аэровзвеси угольной пыли с учетом выхода летучих компонентов // Горение и взрыв. 2018. Т. 11. № 4. С. 29–35.
Козлов А.Н., Свищев Д.А., Худякова Г.И., Рыжков А.Ф. Кинетический анализ термохимической конверсии твердых топлив (обзор) // Химия твердого топлива. 2017. № 4. С. 12–21.
Бойко Е.А., Страшников А.В. Теоретическое обобщение и развитие математического аппарата неизотермической кинетики // Известия РАН. Энергетика. 2021. № 2. С. 97–118.
Ponomareva A.A., Tcoi K.A., Mokrin S.N., Shtym K.A. A laboratory setup based on porous burner for coal particles combustion investigation // Journal of Physics: Conference Series. 5th International Workshop on Heat/Mass Transfer Advances for Energy Conservation and Pollution Control, IWHT 2019. 2019. P. 12–41.
Liu Y., Qi H., Huo P., Li X. Numerical study of coal gasification dual-CFB plant based on the generalized drag model // Fuel Processing Technology. 2020. V. 203. P. 10–63.
Silva R.C., Krautz H.J. Experimental studies on heat transfer of oxy-coal combustion in a large-scale laboratory furnace // Applied Thermal Engineering. 2015. V. 82. P. 82–97.
Pang L., Shao Y., Zhong W., Liu H., Jiang P. Experimental Investigation of Oxy-coal Combustion in a 15 kWth Pressurized Fluidized Bed Combustor // Energy Fuels. 2018. V. 33. P. 1694–1703.
Кузнецов П.Н., Федорчак М.А., Тарасова Л.С., Колесникова С.М., Каменский Е.С. Реакционная способность бурых углей в условиях термоокислительной деструкции // Химия твердого топлива. 2012. № 1. С. 1–12.
Glushkov D.O., Kuznetsov G.V., Strizhak P.A., Syrodov S.V. A mathematical model for processes in coal water slurries containing petrochemicals under heating // Energy and Fuels. 2018. V. 32. № 8. P. 8789–8802.
Бойко Е.А., Пачковский С.В. Диффузионно-кинетическая модель горения и тепломассообмена пылеугольных частиц в газовом потоке // Химия твердого топлива. 2008. № 6. С. 3–13.
Михайлов А.С., Пиралишвили Ш.А., Степанов Е.Г., Спесивцева Н.С. Экспериментальное исследование теплофизических свойств торфяного топлива // Инженерно-физический журн. 2017. Т. 90. № 2. С. 521–527.
Дополнительные материалы отсутствуют.
Инструменты
Известия РАН. Энергетика