Известия РАН. Серия физическая, 2019, T. 83, № 11, стр. 1558-1562
Влияние параметров ионного потока на структуру и свойства покрытий из α-оксида алюминия, получаемых в дуговом разряде реактивным анодным испарением c ионным сопровождением
Н. В. Гаврилов 1, А. С. Каменецких 1, *, П. В. Третников 1, А. В. Чукин 2
1 Федеральное государственное бюджетное учреждение науки Институт электрофизики
Уральского отделения Российской академии наук
Екатеринбург, России
2 Федеральное государственное автономное образовательное учреждение высшего образования
“Уральский федеральный университет имени первого Президента России Б.Н. Ельцина”
Екатеринбург, Россия
* E-mail: alx@iep.uran.ru
Поступила в редакцию 20.05.2019
После доработки 20.06.2019
Принята к публикации 27.07.2019
Аннотация
Покрытия из оксида алюминия получены в дуговом разряде методом реактивного термического анодного испарения алюминия с интенсивным ионным сопровождением. Изучено влияние величины напряжения смещения и плотности ионного тока на структуру и свойства α-фазы Al2O3, формирующейся на подложке из нержавеющей стали с изоструктурным Cr2O3 подслоем при 600°С.
ВВЕДЕНИЕ
Существует несколько кристаллических модификаций Al2O3, среди которых единственной термодинамически стабильной является α-фаза, твердость которой достигает 25 ГПа, а температура плавления – 2044°С [1]. Благодаря сочетанию электрофизических и оптических свойств, высокой твердости, термостойкости, химической инертности, а также теплозащитных характеристик тонкие пленки Al2O3 являются перспективным материалом для широкого спектра применений. Покрытия из α-Al2O3 получают химическим осаждением из паровой фазы при температуре ~1000°С [2]. Плазменная активация рабочей среды позволяет снизить температуру кристаллизации покрытия до 700°С [3]. Более низкие температуры формирования α‑Al2O3 покрытий достигнуты методами физического осаждения с ионным сопровождением и использованием изоструктурного подслоя из Cr2O3 [4].
Получение однофазных α-Al2O3 покрытий затруднено тем, что γ-фаза имеет более низкую поверхностную энергию, поэтому стабильна при малом размере кристаллитов (до 12 нм) [5] и доминирует при интенсивном ионном воздействии, способствующем росту числа центров кристаллизации и уменьшению размера кристаллитов. Наиболее детально исследовано влияние параметров ионного потока на свойства γ-Al2O3 покрытий, получаемых методом реактивного магнетронного распыления (РМР) [6]. В работе [7] для анализа результатов экспериментов по получению покрытий РМР при различной энергии ионов и отношении потока ионов к полному потоку частиц, формирующих покрытие, ji/ja использовали обобщенный параметр dpa, который определяется произведением числа смещенных атомов на ион на ji/ja. При амплитуде напряжения смещения 50–300 В и температуре 500°С покрытия были рентгеноаморфными вплоть до достижения значений dpa > 0.8. C увеличением температуры до 550°С γ‑Al2O3 покрытия формировались при dpa > 0.6, а при 600°С все покрытия были кристаллическими. Минимальное значение потенциала смещения, при которых формировались кристаллические покрытия, составляло около 100 В.
Условия низкотемпературного формирования α-Al2O3 исследованы менее детально. Метод, основанный на создании моноэнергетического потока ионов из фильтрованной плазмы дуги в Ar–O2 газовой смеси с катодным пятном на алюминии, применялся в [8]. В диапазоне энергий ионов 40–200 эВ при температуре 720°С было получено однофазное α-Al2O3 покрытие. В работе [9] также был использован дуговой разряд, но поток ионов Al+ из плазмы имел значительную ширину энергетического спектра (>100 эВ). При температуре образцов 700°С и потенциале смещения –100 В наблюдалась смесь α- и γ-фаз, а в диапазоне 200–700°С в покрытиях доминировала γ-фаза.
Наиболее вероятной причиной различия полученных в [8, 9] результатов является влияние высокоэнергетических ионов, которые увеличивают число центров кристаллизации, что способствует формированию γ-фазы. Поэтому уменьшение разброса энергий ионов в потоке является необходимым условием при изучении влияния ионной обработки на кристаллизацию α-фазы. Поскольку использованный в [7] параметр dpa нелинейно зависит от энергии ионов, но прямо пропорционален ji/ja, представляет интерес раздельное исследование роли энергии и плотности тока ионов.
В настоящей работе для получения α-Al2O3 покрытий использован метод реактивного анодного термического испарения Al в дуге низкого давления с интенсивным ионным сопровождением [10]. Ток разряда распределялся между неохлаждаемым анодом-тиглем и полым анодом системы ионизации, через который в реакционный объем подавали O2. Такой подход позволил управлять скоростью испарения Al и регулировать степень ионизации плазмы и диссоциации O2. Поскольку испаренные атомы Al поступают в объем с тепловой энергией, ионизация газов происходит в разрядном промежутке, а слой пространственного заряда у подложки является бесстолкновительным, то энергия ионов на поверхности покрытия определялась, в основном, величиной потенциала смещения. Возможность независимой регулировки основных параметров процесса нанесения покрытия позволяет использовать этот метод для изучения условий кристаллизации Al2O3 при пониженных температурах.
Целью данной работы было систематическое исследование влияния энергии ионов и плотности ионного тока на фазовый состав, структуру и свойства покрытий, осаждаемых на поверхность подложек из нержавеющей стали c изоструктурным Cr2O3 подслоем при постоянной скорости испарения Al, температуре подложек 600°С и неизменных газовых условиях в реакционном объеме.
МЕТОДИКА ЭКСПЕРИМЕНТА
Устройство для нанесения покрытий детально описано в [10]. Ток разряда с самонакаливаемым полым катодом регулировали в пределах 2–32 А и распределяли между тиглем и полым анодом системы ионизации. В малой входной апертуре анода (1 см2) оказываются совмещенными поток О2 и большая доля анодного тока разряда, следствием чего является увеличение плотности плазмы и доли атомарных частиц кислорода.
Тигель с характерным размером полости 8 мм был изготовлен из графита. Анод имел принудительное водяное охлаждение и помещался в керамический экран. Держатель образцов был установлен на расстоянии 60 мм от тигля. Токи в цепях тигля Ic и анода Ia регулировали раздельно. К держателю образцов прикладывали импульсное напряжение смещения U (50 кГц, 10 мкс). С тыльной стороны держателя образцов был установлен нагреватель, обеспечивающий нагрев образцов до 600°С. На образцах из нержавеющей стали AISI430 с размерами 15 × 15 × 1 мм предварительно методом РМР наносился подслой Cr2O3 толщиной 200 нм.
Камеру откачивали турбомолекулярным насосом до давления 1 ⋅ 10–3 Па, нагревали образцы и тигель до рабочих температур, затем в камеру подавали O2 и задавали требуемые значения Ia (2–32 А) и U (25–400 В). Затем открывали заслонку и проводили осаждение покрытия. Соотношение потоков Ar/O2 составляло 40/30, давление газов в камере было равно 0.3 Па.
Твердость и модуль упругости покрытий измеряли при нагрузке 10 мН на твердомере DUH-211/211S (Shimadzu). Рентгенофазовый анализ покрытий проводился на рентгеновском дифрактометре XRD-7000 (Shimadzu) в излучении Cu-Kα с графитовым монохроматором на вторичном пучке.
РЕЗУЛЬТАТЫ ЭКСПЕРИМЕНТА
На образцах без Cr2O3 подслоя, поверхность которых подвергали предварительной очистке ионным распылением, в диапазоне температур 400–600°С формировались аморфно-кристаллические (γ-фаза) покрытия, степень кристаллизации которых возрастала с ростом интенсивности ионного сопровождения и температуры.
Было проведено несколько серий экспериментов по нанесению покрытий на образцы с Cr2O3 подслоем при температуре образцов 600°С, в каждой из которых варьировали один из двух параметров: U и среднюю плотность ионного тока j. При описании условий эксперимента приводятся значения измерявшегося Ia непосредственно в эксперименте. Величина j линейно зависит от Ia в диапазоне токов 8–32 А (j = 3 мА/см2 при Ia = 10 А).
На рис. 1 приведены зависимости твердости (H), модуля упругости (Е), среднего размера областей когерентного рассеяния (ОКР) и внутренних напряжений в покрытиях (σ) от U для покрытий, полученных при Ia = 10 А. При U менее 50 В величина H составляет ~10 ГПа, E ~ 220 ГПа, а ОКР – 60 нм. С ростом U до 100 В величина H быстро увеличивается с 12 до 24 ГПа, а ОКР уменьшается до 20 нм. С ростом U от 200 до 250 В величина Н снижается до 23 ГПа, ОКР уменьшается до 10 нм. σ достигает 3.7 ГПа при U = 200 В и снижается на порядок величины при увеличении U до 250 В.
Рис. 1.
Зависимости твердости, модуля упругости, среднего размера ОКР и внутренних напряжений покрытий от напряжения смещения. Ток на анод – 10 А.
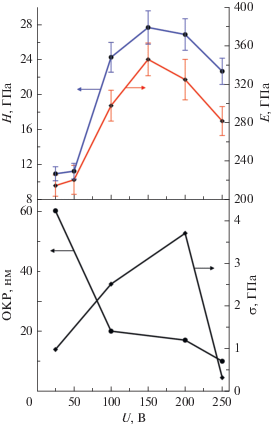
На рис. 2 приведены дифрактограммы покрытий, которые содержат полный набор основных пиков, соответствующих α-Al2O3. С ростом U меняется текстура покрытия: вначале доминирующим в спектре является рефлекс (012) при 2θ ~ ~ 25.6°, затем пик (104) при 2θ ~ 35.15°. В покрытии, полученном при U = 250 В, пики α-фазы исчезают, появляется рефлекс (440) γ-фазы.
Рис. 2.
Дифрактограммы Al2O3 покрытий, полученных при различных напряжениях смещения, токе на анод – 10 А и температуре 600°С.
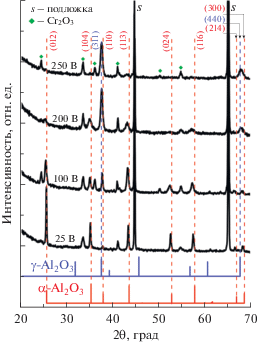
На рис. 3 приведены зависимости H, E, ОКР и σ от Ia для покрытий, полученных при U = 100 В и 600°С. Резкие изменения Н и E наблюдаются при малых (<4 А) и больших (>24 А) токах. σ резко увеличивается до ~3 ГПа при росте Ia до 4 А, достигает 4.5 ГПа при 24 А и снижается на порядок величины при дальнейшем увеличении тока. Рост j вследствие увеличения Ia при неизменной энергии ионов приводит к немонотонному изменению ОКР, который достигает минимального значения 15 нм при Ia = 16 А.
Рис. 3.
Зависимости твердости, модуля упругости, среднего размера ОКР и внутренних напряжений покрытий от тока на анод. Напряжение смещения –100 В.
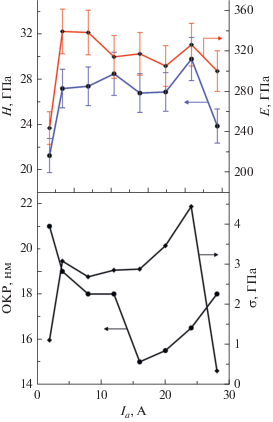
На рис. 4 приведены дифрактограммы этих покрытий, из которых видно, что фаза α-Al2O3 присутствует во всех образцах. Интенсивности рефлексов фазы растут по мере увеличения Ia. При этом наблюдаются изменения в текстуре кристаллитов. Покрытие, полученное при максимальном токе 28 А, имеет очень сильную текстуру (110).
Рис. 4.
Дифрактограммы Al2O3 покрытий, полученных при различных токах на анод, напряжении смещения 100 В и температуре 600°С.
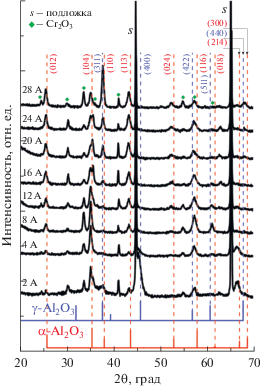
Фаза γ-Al2O3 обнаружена в образцах, полученных при токах 2 и 4 А (основные линии дифракции на 37.5°; 45.5° и 66°), причем содержание этой фазы в образце 2 А существенно выше, чем в образце 4 А, что говорит о подавлении формирования γ-фазы при увеличении тока.
ОБСУЖДЕНИЕ РЕЗУЛЬТАТОВ
Особенностью использованного метода термического испарения является невысокая тепловая энергия испаряемых атомов (менее 0.1 эВ), тогда как при катодном распылении средние энергии распыляемых частиц составляют (1–10 эВ), а энергия однозарядных ионов, образуемых в катодном пятне дугового разряда, составляет несколько десятков эВ [12]. Столь значительное различие в энергии конденсирующихся частиц способно оказать влияние на структуру, фазовый состав и плотность покрытий, формируемых различными методами. Важную роль в формировании покрытий может также играть массовый состав ионной компоненты плазмы. Так, высокое содержание ионов металла в плазме дуги обеспечивает преимущественное внедрение (субплантацию) ионов металла в кристаллическую решетку [8], тогда как при ускорении потенциалом смещения ионов инертного газа передача энергии атомам кристаллической решетки происходит опосредованно.
Из полученных в работе результатов следует, что влияние энергии ионов на формирование α‑фазы заключается в уменьшении ОКР и росте σ с увеличением U (рис. 2), что приводит к увеличению плотности и повышению твердости покрытия. Существует некоторое максимальное значение энергии ионов, при достижении которого происходит переход от α-Al2O3 к γ-фазе с меньшими значениями твердости, размера ОКР и на порядок меньшим уровнем σ. При j = 3 мА/см2 этот переход наблюдался при U = 250 В. Низкая интенсивность ионного воздействия (U < 100 В) приводит к формированию α-Al2O3 покрытий с низкой твердостью (до 8 ГПа) и плотностью.
При изучении γ-Al2O3 покрытий измерение твердости поверхности используется для оценки степени кристалличности покрытий [11]. Как известно, твердость аморфного Al2O3 составляет порядка 5 ГПа, тогда как твердость объемных образцов γ-Al2O3 – 15–20 ГПа [1]. В аморфно-кристаллическом состоянии значения твердости γ-Al2O3 покрытий находятся в интервале между приведенными значениями. При росте α-фазы на подложке с изоструктурным подслоем в условиях слабого ионного воздействия также формируются покрытия с низкой твердостью, которая растет по мере увеличения интенсивности ионной обработки. Однако если для γ-Al2O3 рост твердости обусловлен увеличением числа кристаллитов, то для α-Al2O3 рост твердости связан с увеличением плотности покрытия вследствие изменение его кристаллической структуры.
Влияние j при постоянном U проявляется в существовании некоторой минимального значения, выше которого в покрытии формируется только α-Al2O3 (рис. 4). При U = 100 В пороговый уровень j составил 2.4 мА/см2. С ростом j возрастает уровень σ, меняется текстура покрытия, но ОКР сохраняется примерно постоянным. При j ~ ~ 8 мА/см2 наблюдается резкое снижение σ и формирование текстуры, однако структура α-фазы при этом сохраняется. В таком режиме получены покрытия толщиной до 10 мкм с хорошей адгезией к подложке.
Оценочная величина отношения флюенса ионов к числу атомов в покрытии единичной площади, полученном при плотности ионного тока 3 мА/см2 и энергии ионов 100 эВ, составила 1.4. Минимальная интенсивность ионной бомбардировки, при которой обеспечивается формирование α-фазы, оцененная по числу dpa с использованием полученной в [12] расчетной зависимости, оказывается примерно на порядок выше, чем при формировании γ-фазы при 600°С методом РМР [11]. Если исходить из примерно четырехкратного снижения величины dpa при уменьшении энергии ионов со 100 до 50 эВ, то для достижения сопоставимого уровня dpa рабочий диапазон значений токов должен начинаться не с 8 А, а с 32 А, что качественно объясняет низкую твердость покрытий, полученных при токах 8–28 А.
ЗАКЛЮЧЕНИЕ
Методом реакционного термического испарения с ионным сопровождением получены покрытия из α-Al2O3 на металлической подложке с изоструктурным Cr2O3 подслоем при 600°С и изучено влияние параметров ионного потока на структуру и свойства покрытий. Установлено, что в условиях эксперимента α-фаза формируется в диапазоне энергий ионов 25–200 эВ, при этом увеличение энергии ионов приводит к снижению размера кристаллитов до 10 мкм, росту микроискажений кристаллической решетки до 0.6% и в конечном итоге формированию γ-фазы.
Твердость α-Al2O3 покрытий возрастает при увеличении энергии ионов от 25 до 100 эВ от ~10 ГПа до значений, характерных для объемного корунда (25 ГПа). В отличие от γ-фазы рост твердости обусловлен изменением структуры покрытий, а не степени кристаллизации покрытия.
Плотность ионного тока, при которой в покрытиях формируется только α-фаза, ограничен снизу значением ~2 мА/см2 при энергии ионов 100 эВ. При меньшей плотности тока в покрытии формируется смесь фаз. С увеличением плотности тока возрастает уровень микроискажений и меняется текстура покрытий. При плотности тока ~8 мА/см2 происходит резкий сброс внутренних напряжений и формируется α-фаза с преимущественной текстурой (110).
Значения нормализованного ионного потока, оцениваемого как отношение флюенса ионов к числу атомов в покрытии единичной площади, при которых обеспечивается формирование твердого α-Al2O3 покрытия с приемлемым уровнем внутренних напряжений, в экспериментах находились в диапазоне 1–3. Минимальная интенсивность ионной бомбардировки, при которой обеспечивается формирование α-фазы, оцененная по числу смещений атомов кристаллической решетки, примерно на порядок выше, чем при формировании γ-фазы при 600°С реактивным магнетронным распылением.
Работа выполнена при поддержке РФФИ (проект № 17-08-00942-а).
Список литературы
Gitzen W.N. Alumina as a ceramic material. Columbus: Am. Ceram. Soc. 1970, 262 p.
Lux B., Colombier C., Altena H., Stjernberg K. // Thin Sol. Films. 1986. V. 138. P. 49.
Taschner C., Ljungberg B., Alfredsson V. et al. // Surf. Coat. Technol. 1998. V. 108–109. P. 257.
Jin P., Xu G., Tazawa M. et al. // J. Vac. Sci. Technol. A. 2002. V. 20. P. 2134.
McHale J.M., Auroux A., Perrotta A.J., Navrotsky A. // Science. 1997. V. 277. P. 788.
Sridharan M., Sillassen M., Bottiger J. et al. // Surf. Coat. Technol. 2007. V. 202. P. 920.
Prenzel M., Kortmann A., Stein A. et al. // J. Appl. Phys. 2013. V. 114. Art. № 113301.
Sarakinos K., Music D., Nahif F. et al. // Phys. Stat. Sol. (RRL). 2010. V. 4. P. 154.
Rosen J., Mra’z S., Kreissig U. et al. // Plasma Chem. Plasma Proces. 2005. V. 25. P. 303.
Гаврилов Н.В., Каменецких А.С., Третников П.В., Чукин А.В. // ПЖТФ. 2017. № 20. C. 86.
Noyan C.I., Cohen B.J. Residual stress measurement by diffraction and interpolation, N.Y.: Springer, 1987. 276 p.
Raizer Yu.P. Gas discharge physics. N.Y.: Springer, 1997. 449 p.
Davis C.A. // Thin Sol. Films. 1993. V. 226. P. 30.
Thornton J.A. // J. Vac. Sci. Technol. A. 1993. V. 4. P. 3059.
Kelly P.J., Arnell R.D. // J. Vac. Sci. Technol. A. 1998. V. 16. P. 2858.
Дополнительные материалы отсутствуют.
Инструменты
Известия РАН. Серия физическая