Известия РАН. Серия физическая, 2019, T. 83, № 6, стр. 830-833
Эволюция с деформацией кривизны-кручения кристаллической решетки в различных субструктурах сплавов на основе меди
Н. А. Конева 1, *, Л. И. Тришкина 1, Т. В. Черкасова 1, 2
1 Федеральное государственное бюджетное образовательное учреждение высшего образования
“Томский государственный архитектурно-строительный университет”
Томск, Россия
2 Федеральное государственное бюджетное образовательное учреждение высшего образования
“Национальный исследовательский Томский политехнический университет”
Томск, Россия
* E-mail: koneva@tsuab.ru
Поступила в редакцию 20.11.2018
После доработки 16.12.2018
Принята к публикации 25.02.2019
Аннотация
В работе представлены результаты электронно-микроскопического исследования кривизны-кручения (χ) кристаллической решетки, возникающей при деформации поликристаллических твердых ГЦК-растворов. Исследовались сплавы Cu + 0.4 ат. % Mn и Cu + 19 ат. % Mn со средними размерами зерен 〈d〉 = 10–240 мкм. Образцы деформировались растяжением при комнатной температуре. Установлены источники кривизны-кручения. Выявлено, что наиболее высокие значения χ характерны для стыков зерен и границ зерен.
ВВЕДЕНИЕ
Важным дефектом металлических материалов, возникающим при пластической деформации, является локальная кривизна кристаллической решетки (χ) [1–4]. Как следует из работ [4, 5], этот дефект развивается с деформацией материала на всей иерархии масштабных уровней, определяет зарождение дислокаций и дает основной вклад в деформационное упрочнение, способствует образованию микротрещин, а затем и разрушению. Представления о кривизне кристаллической решетки используются для объяснения фрагментации и измельчения зерен при интенсивной пластической деформации [6]. В общем случае χ представляет собой тензор [1, 7–10], который содержит компоненты кривизны и кручения кристаллической решетки. Поэтому будем определять χ как кривизну-кручение кристаллической решетки.
Изучение вопроса о кривизне–кручении кристаллической решетки показывает, что экспериментальных работ пока недостаточно для создания полной картины эволюции χ с деформацией и определения источников ее происхождения. Для поликристаллических материалов в этом плане важно понять роль размера зерен.
Цель настоящего исследования заключалась в экспериментальном изучении кривизны-кручения кристаллической решетки методом просвечивающей дифракционной электронной микроскопии (ПЭМ) в деформированных поликристаллических твердых ГЦК-растворах с разным размером зерен, установлении источников ее происхождения, эволюции χ с деформацией.
МАТЕРИАЛЫ И МЕТОДЫ ИССЛЕДОВАНИЯ
Для исследования были выбраны поликристаллические ГЦК сплавы Cu + 0.4 ат. % Mn и Cu + 19 ат. % Mn со средними размерами зерен: 10–240 мкм. Плоские образцы с размером рабочей части 100 × 12 × 2 мм подвергались растяжению на машине Instron со скоростью 2 ⋅ 10–2 с–1 при температуре 293 К до разрушения. Дефектная структура образцов изучалась методом ПЭМ на фольгах, приготовленных из образцов, деформированных до различных степеней деформации εист. Величина χ измерялась электронно-микроскопически с использованием изгибных экстинкционных деформационных контуров, изображение которых на микрофотографиях свидетельствует о наличии кривизны-кручения кристаллической решетки [1]. Величина χ определяется из градиента непрерывной разориентировки:
где φ – угол наклона кристаллографических плоскостей с одинаковой ориентировкой по отношению к электронному пучку, $\ell $ – расстояние в кристалле. Изгибный экстинкционный контур локализован на участке с одинаковой ориентировкой отражающих плоскостей. Интенсивность в контуре спадает от центра к краям по мере удаления от точного брэгговского отражения. Ширина контура Δ𝓵 в величинах разориентировок Δφ для ГЦК металлов Ni, Cu и Fe и сплавов на их основе составляет 1° [11, 12]. Таким образом, величину χ можно определить из измерений ширины экстинкционного контура Δ$\ell $ в локальных участках. Такой метод использовался в настоящей работе. Отметим, что в настоящее время для измерения χ и связанной с ней плотностью геометрически необходимых дислокаций используется также метод дифракции обратно рассеянных электронов (ЕВSD) [10, 13].РЕЗУЛЬТАТЫ И ИХ ОБСУЖДЕНИЕ
Пластическая деформация в сплавах вызывает образование и развитие различного типа дислокационных субструктур (ДСС) [14]. При развитой пластической деформации (εист > 0.20) в исследуемых сплавах наблюдаются разориентированные ДСС, например, такие как разориентированная ячеистая, разориентированная ячеисто-сетчатая, микрополосовая и оборванные субграницы. Оборванные субграницы представляют собой частичные дисклинации [15]. Уже при небольших степенях пластической деформации возникают экстинкционные деформационные контуры. Их источником являются границы зерен и их стыки. Образование разориентированных субструктур также сопровождается возникновением экстинкционных деформационных контуров. На рис. 1 представлены электронно-микроскопические изображения формирования экстинкционных деформационных контуров от разных источников.
Рис. 1.
Электронно-микроскопические изображения экстинкционных деформационных контуров (К) от границы зерна (а), в разориентированной ячеисто-сетчатой ДСС (б), от оборванной субграницы (в) в сплаве Cu + 19 ат. % Mn, εист = 0.80.
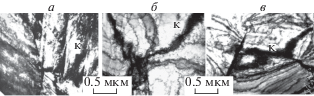
На рис. 2а представлены зависимости напряжения течения (σ) и коэффициента деформационного упрочнения (θ) от степени деформации в сплаве Cu + 19 ат. % Mn с размерами зерен 〈d〉 = = 10 мкм и 〈d〉 = 240 мкм. Наблюдаются четыре стадии деформационного упрочнения, связанные с различным поведением θ [14]. Максимальное значение θ наблюдается на стадии II, на стадии III происходит его уменьшение, а на стадии IV он практически остается неизменным. Коэффициент деформационного упрочнения выше в сплаве с размером зерна 10 мкм.
Рис. 2.
а – Зависимости напряжения течения (σ) и коэффициента деформационного упрочнения (θ) для сплава Cu + 19 ат. % Mn с размерами зерен (〈d〉): 1, 3 – 10 мкм, 2, 4 – 240 мкм; б, в – зависимости кривизны-кручения кристаллической решетки (χ) для разных источников (1 – от стыков зерен, 2 – от границ зерен, 3 – в разориентированной ячеисто-сетчатой субструктуре) от степени деформации (εист) сплава с разными размерами зерен (б – 10 мкм, в – 240 мкм). Пунктирными линиями и римскими цифрами указаны стадии пластической деформации.
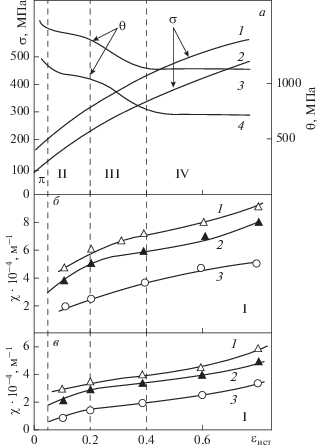
С использованием параметров изгибных экстинкционных контуров были измерены значения χ, связанные с различными источниками ее происхождения на разных стадиях деформации. На рис. 2б, 2в представлены результаты этих измерений для сплава Cu + 19 ат. % Mn. Из рисунка следует, что величина χ, обусловленная границами зерен и их стыками, в разориентированной ячеисто-сетчатой субструктуре, характерной для этого сплава в значительном интервале деформации, растет с увеличением степени деформации. Значения χ при всех степенях пластической деформации оказываются наиболее высокими вблизи стыков зерен и границ зерен. Сравнение рис. 2а и 2б, 2в позволяет проследить изменения χ на различных стадиях пластической деформации.
Уменьшение размера зерна увеличивает значения χ. Это следует из сравнения рис. 2б и 2в и особенно четко из результатов, представленных на рис. 3. На этом рисунке даны зависимости χ = = f(〈d〉) для широкого интервала размеров зерен для сплава Сu + 0.4 ат. % Mn для степени деформации εист = 0.60. Измерения χ проводились на расстоянии 1–2 мкм от различных источников. Видно, что уменьшение размера зерен сопровождается увеличением χ. Этот эффект наиболее заметен при 〈d〉 менее 100–120 мкм. Наибольшие значения χ наблюдаются для стыков зерен и границ зерен. В субструктурах – микрополосовой и разориентированной ячеистой ДСС – значения χ меньше.
Рис. 3.
Взаимосвязь кривизны-кручения кристаллической решетки χ с размером зерна 〈d〉 от разных источников: 1 – от стыков границ зерен, 2 – от границ зерен, 3 – от микрополос, 4 – в разориентированной ячеистой ДСС в сплаве Cu–0.4 ат. % Mn; εист = 0.60. Измерения проводились в интервале 1–2 мкм от источников.
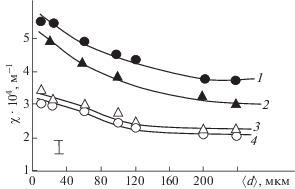
На рис. 4 представлена зависимость средней величины кривизны-кручения кристаллической решетки χ от размера зерна 〈d〉 с учетом разных источников (границ зерен, их стыков, оборванных субграниц, микрополос, других разориентированных субструктур, микротрещин) в сплавах Сu + 0.4 ат. % Mn и Cu + 19 ат. % Mn, при εист = 0.60. Видно, что и средние значения χ с уменьшением размера зерен увеличиваются.
Рис. 4.
Взаимосвязь средней величины кривизны-кручения кристаллической решетки χ с размером зерна 〈d〉 с учетом разных источников в сплавах: Сu + + 0.4 ат. % Mn (1) и Cu + 19 ат. % Mn (2), εист = 0.60. Измерения χ проводились в интервале 1–2 мкм от источников (от стыков, ГЗ, оборванных границ, микрополос, микротрещин, в субструктурах) и затем суммировались.
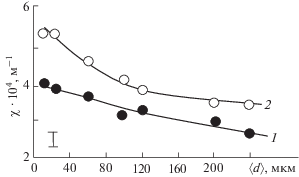
Для сравнения поведения кривизны-кручения кристаллической решетки в зависимости от деформации сплавов с разным содержанием Mn на рис. 5 представлены зависимости средней величины χ от εист для этих сплавов с размером зерен 〈d〉 = 10 мкм. Средняя величина χ, как и на рис. 4, определялась с учетом всех источников ее происхождения. Из рисунка видно, что средняя величина χ оказывается больше в сплаве Cu + 19 ат. % Mn. Увеличение содержания Mn и, следовательно, увеличение твердорастворного упрочнения сопровождается ростом χ. Этот эффект проявляется во всем исследованном интервале деформаций.
ЗАКЛЮЧЕНИЕ
Методом ПЭМ выполнено исследование кривизны-кручения кристаллической решетки, возникающей при деформации поликристаллических ГЦК-сплавов Cu–Mn с разным размером зерен. Установлено, что источниками возникновения кривизны-кручения являются границы зерен, стыки зерен и деформационные границы разориентации дислокационного и дисклинационного происхождения. Границы зерен и их стыки являются главными источниками возникновения кривизны-кручения вплоть до разрушения сплавов. Размер зерен оказывает существенное влияние на величину χ. Уменьшение размера зерен увеличивает кривизну-кручение. Это влияние оказывается наиболее существенным при 〈d〉 менее 100–120 мкм. Влияние размера зерен на величину χ связано с возрастающей ролью границ зерен и их стыков в формировании кривизны-кручения при уменьшении 〈d〉, и, следовательно, увеличении доли границ зерен и стыков зерен в объеме материала.
Исследования выполнены при поддержке государственного задания на проведение научных исследований по проекту № 3.8320.2017/БЧ.
Список литературы
Конева Н.А., Тришкина Л.И., Лычагин Д.В., Козлов Э.В. // в кн.: Новые методы в физике и механике деформируемого твердого тела. Ч. 1. Под ред. В.Е. Панина. Томск: ТГУ, 1990. С. 83.
Тюменцев А.Н., Коротаев А.Д., Пинжин Ю.П. // Физ. мезомех. 2004. Т. 7. № 4. С. 35.
Тюменцев А.Н., Дитенберг И.А., Коротаев А.Д., Денисов К.И. // Физ. мезомех. 2013. Т. 16. № 3. С. 63.
Панин В.Е., Панин А.В., Елсукова Т.Ф., Попко-ва Ю.Ф. // Физ. мезомех. 2014. Т. 17. № 6. С. 7.
Панин В.Е., Егорушкин В.Е. // Физ. мезомех. 2015. Т. 18. № 3. С. 100.
Vinogradov A., Estrin Y. // Progr. Mat. Sci. 2018. V. 95. P. 172.
Вайнштейн Б.К., Фридкин В.М., Инденбом В.Л. Совр. кристаллография, Т. 2. Структура кристаллов. М.: Наука, 1979. 359 с.
Штремель М.А. Прочность сплавов. Дефекты решетки. М.: Металлургия, 1982. 280 с.
Конева Н.А., Киселева С.Ф., Попова Н.А., Козлов Э.В. // Фунд. проб. совр. материаловед. 2011. Т. 8. № 3. С. 35.
Kundu A., Field D.P. // Mat. Sci. Eng. A. 2016. V. A667. P. 435.
Козлов Э.В., Конева Н.А., Попова Н.А. // Изв. РАН. Сер. физ. 2009. Т. 73. № 9. С. 1295; Kozlov E.V., Kone-va N.A., Popova N.A. // Bull. Russi. Acad. Sci. Phys. 2009. V. 73. № 9. P. 1227.
Козлов Э.В., Лычагин Д.В., Конева Н.А., Тришкина Л.И. // в кн.: Физика прочности гетерогенных материалов. Под ред. А.Е. Романова, Л.: ФТИ им. А.Ф. Иоффе, 1988. С. 3.
Calcagnotto M., Ponge E., Raabe D. // Mat. Sci. Eng. A. 2010. V. A 527. P. 2738.
Конева Н.А., Тришкина Л.И., Потекаев А.И., Козлов Э.В. Структурно-фазовые превращения в слабоустойчивых состояниях металлических систем при термосиловом воздействии, Томск: Изд-во НТЛ, 2015. 344 с.
Рыбин В.В. Большие пластические деформации и разрушение металлов, М.: Металлургия, 1986. 224 с.
Дополнительные материалы отсутствуют.
Инструменты
Известия РАН. Серия физическая