Известия РАН. Серия физическая, 2020, T. 84, № 9, стр. 1350-1354
Влияние структурно-фазового состояния поверхности подложки переменного состава на растекание расплава и их связь с диаграммой состояния
А. А. Ахкубеков 1, *, С. Н. Ахкубекова 2, Ю. М. Гуфан 3, М. З. Лайпанов 4
1 Федеральное государственное бюджетное образовательное учреждение высшего образования
“Кабардино-Балкарский государственный университет имени Х.М. Бербекова”
Нальчик, Россия
2 Федеральное государственное бюджетное образовательное учреждение высшего образования
“Кабардино-Балкарский государственный аграрный университет имени В.Н. Кокова”
Нальчик, Россия
3 Федеральное государственное автономное образовательное учреждение высшего образования
“Южный федеральный университет”, Научно-исследовательский институт физики
Краснодар, Россия
4 Федеральное государственное бюджетное образовательное учреждение высшего образования
“Карачаево-Черкесский государственный университет имени У.Д. Алиева”
Карачаевск, Россия
* E-mail: dis1@kbsu.ru
Поступила в редакцию 19.03.2020
После доработки 10.04.2020
Принята к публикации 27.05.2020
Аннотация
Предложен метод формирования и нанесения дозированных капель на поверхность твердой подложки, в том числе переменного состава. С целью получения таких подложек и капель различных концентраций использован метод контактного плавления, тесно связанный с диаграммой состояния. Указанная связь позволяет изучать концентрационную и температурную зависимости поверхностных характеристик в одинаковых условиях, что повышает точность их определения. Показано, что микроструктура подложки переменного состава влияет на процесс растекания капли по ее поверхности.
ВВЕДЕНИЕ
Исследования кинетики растекания жидких металлов по твердой поверхности в определенных концентрационных и температурных интервалах показывают, что образование различных фаз, например интерметаллидов, ухудшают физико-химические свойства зон соединений при сварке оплавлением. Этот вопрос становится еще более актуальным, когда объектами практического использования являются материалы с поверхностью переменного состава – композиционные материалы, многофазные сплавы, пористые тела и т.д.
Решение данной задачи так же тесно связано с формированием и нанесением капель одинакового размера на соответствующие точки поверхности подложки переменного состава.
На наш взгляд, удачной моделью исследования указанной проблемы являются переходные зоны, полученные методом контактного плавления (КП), осуществленного в нестационарно-диффузинном режиме (НДР) [1].
В научной литературе практически отсутствует обсуждение данной проблематики, хотя решение подобных задач имеет научную и практическую ценность.
Цель исследования – разработка способа получения и нанесения на соответствующие точки поверхности подложки капель металлических жидкостей одинакового размера, в одинаковых условиях, в нужном количестве, в одном эксперименте, как из чистых металлов, так и сплавов различных концентраций, а также установление взаимосвязи между фазовой диаграммой состояния и поверхностными характеристиками, а именно: формой и диаметром пятна растекания. Данная работа является продолжением исследований [2], где экспериментально показана зависимость конфигурации и размера пятна растекания от местоположения жидкой капли металла на поверхности подложки переменного состава.
МЕТОД ПОЛУЧЕНИЯ КАПЕЛЬ ОДИНАКОВОГО РАЗМЕРА
Решение проблемы формирования и нанесения дозированных капель на поверхность твердых тел началось с работ М. Симона и является весьма актуальной.
Дальнейшее развитие методов и приборов для исследования в области физики межфазных явлений продолжены в [3–7], в т.ч. при высоких температурах, а также в ряде других работ.
Воспользовавшись идеями, изложенными в [8], нами предлагается метод получения дозированных капель, как из чистых металлов, так и сплавов на их основе, а также изготовление подложек переменного состава. Для применения этого метода на прослойках, полученных контактным плавлением, используется специальный держатель, собранный на основе микрометра.
Основным узлом держателя является набор пластин одинаковой толщины и одинаковых отверстий, обеспечивающих разделение жидкой диффузионной зоны на отдельные части (диски, таблетки, навески). Набор пластин (ячейка), собранных в определенном порядке, образуют полый цилиндр, в котором проводится контактное плавление, либо заполняется чистым металлом. Ячейка помещается в соответствующую среду с температурой достаточной для проведения КП или плавления чистого металла в полом цилиндре. После чего производят “срез” жидкой консистенции, ведущий к образованию дисков (таблеток) (рис. 1).
Рис. 1.
Схема расположения пластин после “среза” (а); капли галлия дозированного размера полученные методом “среза” (б).
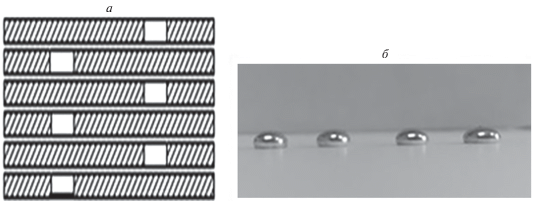
Полученные таким образом жидкие диски кристаллизируются (иногда в жидком азоте). С целью подтверждения одинаковой дозированности капель каждая навеска взвешивалась на аналитических весах.
Концентрация каждой отдельной навески определялась контактированием с одним из чистых компонентов (А или В) (рис. 2) и помещалась в термостат.
Рис. 2.
К определению С(х) методом снятия жидких проб (нахождение концентрации навесок): (а) твердофазное контактирование; (б) термодинамическое равновесие – твердое–жидкое, при Т = const.
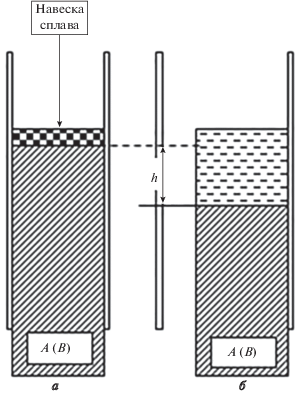
Термостат должен иметь температуру ниже температуры плавления чистого компонента, но выше ликвидусной температуры анализируемого сплава А + В. Таким образом, в начальный момент времени чистый компонент находится в твердом состоянии, а анализируемая навеска – в жидком.
Так как температура термостата превышает ликвидусную температуру навески, то чистый компонент будет растворяться в жидкой навеске и граница жидкость–твердая фаза начинает двигаться. Движение границы продолжается до тех пор, пока концентрация жидкости не достигнет значения, соответствующего ликвидусной по диаграмме плавкости при температуре термостата. По достижении термодинамического равновесия смещение границы жидкость–твердая фаза прекращается.
Для уменьшения времени достижения равновесия в качестве подложки выбирается менее плотное вещество (развивается конвекция).
Зная массу m анализируемой навески, концентрацию жидкости, соответствующую ликвидусной по диаграмме состояния при заданной температуре термостата, высоту h расплавившейся части чистого компонента, можно определить искомую концентрацию по формуле:
где СA – искомая концентрация в весовых долях, СL – весовая доля А, соответствующая ликвидусу на диаграмме плавкости при температуре опыта, ρ, d, h – соответственно плотность, диаметр и высота выплавившейся части чистого образца.Согласно строению диаграмм состояния, изменение концентрации данного компонента лежит между двумя ликвидусами. Поэтому концентрацию таблеток можно найти и другим способом. Помещают таблетку в тигель с раскисляющей жидкостью (глицерин), поднимают температуру и фиксируют момент плавления таблетки (диска), что позволяет из диаграммы плавкости определить концентрацию С.
Соответствие концентрации дисков (капель), описанными выше методами, избирательно контролируется современными ренгенофазными, рентгеноструктурными методами.
Возможны два варианта контакта таблеток с подложками переменного состава, а именно: полученные таблетки контактируют с подложкой в различных точках и поднимают температуру системы до перехода таблеток в жидкую фазу – каплю; или закристаллизованные капли на инертной поверхности (стекле) переносят на исследуемую подложку.
Затем следят за их смачиванием и растеканием, что позволяет изучать временную и концентрационную зависимости формы и диаметра пятна растекания.
РЕЗУЛЬТАТЫ ИССЛЕДОВАНИЯ
В работах [1, 8] представлены основы связи диаграммы состояния с концентрационным распределением компонентов C(xi) в контактных прослойках, которые затем используются нами для изучения зависимости смачивания и растекания от концентрации (структурно-фазового состояния поверхности).
Как известно, концентрация на границе кристалл–жидкость (К–Ж) в контактной прослойке практически совпадает с ликвидусными концентрациями, как со стороны компонента А, так и со стороны компонента В, указанными на диаграмме состояния исследуемых двухкомпонентных систем [9–12].
Кроме того, как теоретически, так и экспериментально показано, что в плоскости первоначального контакта концентрация расплава всегда совпадает с эвтектической, указанной на диаграмме состояния. Для контактных прослоек, полученных в нестационарно-диффузионном режиме (НДР) также характерно образование в них новых фаз, например, интерметаллидов (рис. 3) [13, 14], концентрации которых указываются на диаграмме состояния и проявляются в структуре контактных прослоек с химическим взаимодействием компонентов.
Рис. 3.
Микрофотография интерметаллидов в контактной прослойке системы медь–алюминий (увеличение 480×) [13].
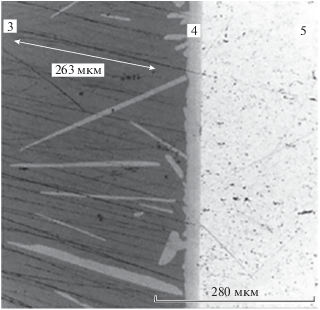
На рис. 4 показана связь между диаграммой состояния и концентрационным распределением компонентов А(В) вдоль переходной зоны.
Рис. 4.
Связь распределения концентрации вдоль контактной прослойки с диаграммой состояния (а) диаграмма состояния двухкомпонентной системы; (б) концентрационное распределение в контактной прослойке; (в) контактная прослойка в двухкомпонентной системе
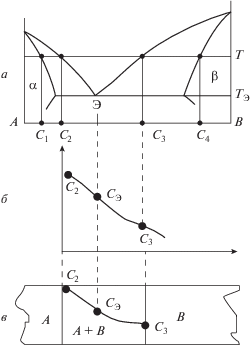
Указанная корреляция между изменением концентрации C(xi) вдоль жидкой контактной прослойки протяженностью δ и диаграммой состояния (С, Т) дает возможность расширить круг исследований зависимости δ = f(C, T), в частности, при изучении смачивания и растекания расплавов по поверхности твердых подложек переменного состава.
Суть предлагаемого подхода заключается в том, что смачивание и растекание дозированных капель будет зависеть от их местоположения вдоль подложки, т.е. от концентрации (структурно-фазового состояния) площадки соприкосновения (контакта) капель и поверхности подложки. Так как C(xi) в переходной зоне связана с диаграммой состояния, то опосредовано с ней будут связаны и параметры растекания.
Таким образом, можно заключить, что существует связь между поверхностными характеристиками, диаграммой состояния и распределением компонентов в подложках переменного состава.
На рис. 5 приведены форма и размер пятен на подложке в процессе смачивания и растекания. Видно, что на различных участках, как форма, так и размер пятен существенно отличаются друг от друга: 1 – 83, 2 – 85, 3 – 80, 4 – 90, 5 – 70 в относительных единицах, т.е. наблюдается тенденция к увеличению общего диаметра пятна по мере приближения к чистому висмуту. Ширина “белой” части пятна также увеличивается в направлении висмута, в то время как размер “черной” части пятна в сторону висмута уменьшается. Анализ микроструктуры зоны взаимодействия капель галлия одинакового размера показывает, что глубина растворения подложек зависит от их местоположения. Установлено, что увеличение концентрации висмута в подложке ведет к перестройке дендритного роста за счет изменения характера диффузии на межфазной границе – структура измельчается.
Рис. 5.
Изменение диаметра пятна растекания вдоль переходной зоны: 1 – на поверхности чистого свинца, 2 – на границе Pb – переходная зона, 3 – внутри переходной зоны, 4 – на границе переходная зона – Bi, 5 – на висмуте [2].
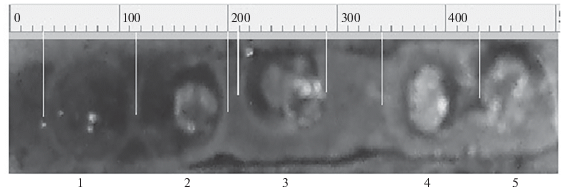
Таким образом, знание концентрационного распределения изменения структуры в контактных прослойках (подложках переменного состава), разработанные нами подходы формирования и нанесения дозированных капель позволяют установить связь между диаграммой состояния, т.е. изучать температурную и концентрационную зависимости поверхностных характеристик расплавов при смачивании и растекании. Диаграмма состояния позволяет конкретизировать концентрации компонентов минимум в 4 точках контактной прослойки: у двух границ жидкое–твердое (2 ликвидусные концентрации данного компонента); концентрацию в месте первоначального контакта, которая совпадает с эвтектической, а так же в зависимости от количества интерметаллидов в данной системе их местоположения и концентрации.
ВЫВОДЫ
1. Предложен подход получения дозированных капель методом “среза”, как чистых металлов, так и сплавов на их основе.
2. В основу получения подложек переменного состава и капель различных концентраций положено явление контактного плавления, тесно связанного с диаграммой состояния, что в свою очередь позволяет изучить концентрационные (структурные) зависимости поверхностных характеристик взаимодействующих металлов, т.е. предложена связь между диаграммой состояния и поверхностными характеристиками, например, конфигурацией и размером диаметра пятна растекания.
3. Характер диффузии подложка–капля меняется в зависимости от местоположения капли (концентрации подложки) – по мере увеличения концентрации висмута структура на межфазной границе измельчается.
Список литературы
Ахкубеков А.А.,Орквасов Т.А., Созаев В.В. Контактное плавление металлов и наноструктур на их основе. М.: ФИЗМАТЛИТ, 2008. 152 с.
Ахкубеков А.А., Ахкубекова С.Н., Багов А.М. и др. // Изв. РАН. Сер. физ. 2016. Т. 80. № 6. С. 701; Akhku-bekov A.A., Akhkubekova S.N., Bagov A.M. et al. // Bull. Rus. Acad. Sci. Phys. 2016. V. 80. № 6. P. 634.
Алчагиров Б.Б., Хоконов Х.Б. Методы и приборы для исследования в области физики межфазных явлений (Специальный физический практикум). Нальчик: КБГУ, 2017. 152 с.
Алчагиров Б.Б., Хоконов Х.Б. // ТВТ. 1994. Т. 32. № 4. С. 590.
Еременко В.Н., Лесник Н.Д., Пестун Т.С. и др. // В сб.: Смачиваемость и поверхностные свойства расплавов и твердых тел. Киев: Наукова Думка, 1972. С. 39.
Еременко В.Н., Лесник Н.Д., Пестун Т.С. и др. Смачиваемость и поверхностные свойства расплавов и твердых тел. Киев: Наукова Думка, 1972. С. 38.
Витюнин М.А. Растекание расплавов на основе алюминия по поверхности твердых тел и особенности микроструктуры закристаллизованных материалов. Челябинск, 2009. 124 с.
Ахкубеков А.А. Диффузия и электроперенос в низкоплавких металлических системах при контактном плавлении. Нальчик: Изд. КБГУ, 2001. 312 с.
Рогов В.И. Исследование контактного плавления металлических систем в диффузионном режиме. Автореферат дис. … канд. физ.-мат. наук. Нальчик: КБГУ, 1969. С. 13.
Багов А.М. Влияние электропереноса на взаимную диффузию и макроскопическое течение расплава, образующегося при контактном плавлении. Дис. … канд. физ.-мат. наук. Нальчик: КБГУ, 2016. 156 с.
Нилова Н.Н., Бартенов Г.М., Борисов В.Т., Матвеев Ю.Е. // Сб. мат. конф. по физике. Нальчик: КБГУ, 1972. С. 13.
Нилова Н.Н., Бартенев Г.М., Борисов В.Т., Матвеев Ю.Е. // ДАН СССР. 1968. Т. 180. № 2. С. 394.
Ахкубеков А.А., Ахкубекова С.Н., Багов А.М. и др. // Изв. РАН. Сер. физ. 2015. Т. 79. № 11. С. 1548.
Шморгун В.Г., Кулевич В.П., Савченко В.В. // Изв. ВолГТУ. 2016. № 2. С. 21.
Дополнительные материалы отсутствуют.
Инструменты
Известия РАН. Серия физическая