Известия РАН. Серия физическая, 2021, T. 85, № 7, стр. 1031-1035
Карбидные покрытия на металлических лентах
В. П. Коржов *
Федеральное государственное бюджетное учреждение науки
“Институт физики твердого тела Рoссийской академии наук”
Черноголовка, Россия
* E-mail: korzhov@issp.ac.ru
Поступила в редакцию 25.01.2021
После доработки 25.02.2021
Принята к публикации 29.03.2021
Аннотация
Представлен твердофазный метод получения карбидных покрытий на металлических поверхностях с использованием терморасширенного графита. В качестве объектов нанесения выбраны фольги ниобия, Ti-сплава c Cr, Mo и Al и сплава Nb–2% Zr. Формирование покрытий происходило при нагреве и выдержке под давлением многослойных пакетов, составленных из металлических фольг, чередовавшихся с лентами терморасширенного графита. Образование покрытий происходило в результате твердофазной диффузии углерода в металлические фольги. Исследованы микроструктуры поперечных сечений лент с карбидными покрытиями, и представлены результаты температурных испытаний на прочность при изгибе слоистых композитов, изготовленных из Nb-фольг и фольг Ti‑сплава с карбидными покрытиями.
ВВЕДЕНИЕ
Карбиды титана, ниобия и циркония характеризуются тем, что химически инертны при комнатной температуре и не окисляются вплоть до 1200°С. Они стойки в расплавах алюминия, меди, латуни, чугуна и сталей. Кроме того, карбиды имеют высокую термическую стойкость. Такие свойства уже в 60-е годы прошлого века сделали их востребованными для нанесения и изготовления покрытий, надежно защищающих поверхности материалов, не противостоящие коррозии при высоких температурах, а также покрытий на рабочую поверхность режущих стальных инструментов для увеличения их твердости [1–4]. Благодаря таким свойствам, детали конструкций из материалов с карбидными покрытиями используются в турбинах и ракетостроении.
В отношении карбида NbC нужно добавить, что он защищает даже поверхность графита, который не защищается другими термостойкими покрытиями, и оказывается достаточно пластичным, что его научились ковать.
В представляемой работе покрытия из карбида металлов планировались использоваться не как самостоятельные функциональные покрытия, а как промежуточный продукт для получения жаропрочных слоистых композитов, предназначенных для работы при высоких, вплоть до 1500°С, температурах. Однако мы не исключаем, что карбидные покрытия, полученные с помощью терморасширенного графита (ТРГ), смогут найти применение и как собственно покрытия.
Слоистые композиты, о которых идет речь, это материалы, похожие на сплавы с направленными структурами, характеризующиеся лучшими прочностными свойствами по сравнению со сплавами, имеющими литую структуру и, поэтому, технологии направленной кристаллизации постоянно совершенствуются [5–10]. Для жаропрочных сплавов стремятся сформировать направленно-ячеистую структуру [11] с ячейками из жаропрочных интерметаллических или карбидных фаз, чередующихся со структурными элементами твердого раствора на основе сплав-образующего металла, способного придать сплаву должную трещиностойкость при комнатной температуре.
Подобная структура жаропрочного материала может быть заложена искусственным путем на начальной стадии процесса его получения. Это относится к слоистым композитам с карбидным упрочнением, получаемых в представленной работе.
ПОЛУЧЕНИЕ КАРБИДНЫХ ПОКРЫТИЙ НА МЕТАЛЛИЧЕСКИХ ЛЕНТАХ
Суть метода состоит в термообработке под давлением многослойных пакетов, сформированных из фольг металлов или сплавов, проложенных отрезками гладкой ТРГ-ленты (ленты из терморасширенного графита). Металлическими элементами для пакетов были фольги ниобия, титанового сплава Ti–10.0% Cr–7.3% Mo–2.6 мас. % Al и сплава Nb–2 мас. % Zr.
Метод относится к категории диффузионных твердофазных методов для получения двухсторонних (или односторонних) карбидных покрытий на металлических лентах. На начальном этапе составлялся пакет из 20–30 шт. металлических лент, например, ниобия, толщиной 60 или 70 мкм, и ленточных пар терморасширенного графита, количество которых нужно на одну больше.
Такую пакетную сборку помещали между неподвижным и подвижным пуансонами и подвергали термической обработке (ТО) под давлением до 15 МПа при 1500°С в течение 15–60 мин. ТО проводилась в вакуумной камере установки для диффузионной сварки (рис. 1).
Рис. 1.
Схематическое изображение пакета и твердофазного диффузионного способа получения карбидных покрытий на металлических фольгах.
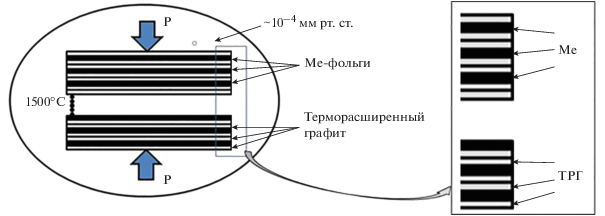
После термообработки пакет, в местах соприкосновения двух слоев ТРГ, легко разбирался на исходное количество фольг с 2-сторонними покрытиями. Поверхности фольг зачищались от оставшегося на них графита.
Как следует из сказанного, насыщению поверхности металла углеродом служила графитовая лента марки ТРГ – thermally expanded graphite, но в специальной литературе он значится еще и как exfoliated graphite (отслаивающийся графит).
Способу характерна простота, доступность и эффективность. Используя ленты терморасширенного графита, диффузией в твердой фазе можно получать карбидные покрытия на фольгах, лентах и плоских изделиях любых металлов, способных образовывать с углеродом карбидные соединения. Несмотря на температурные ограничения, а ТРГ стандартно применим лишь при температурах от –200 до +400°С, в случаях, если он “закрыт” в конструкции уплотнением от окисления, то его можно применять при температурах до 2000–2500°С. В связи с этим, для получения карбидных слоев здесь используются ленты ТР-графита в качестве прокладок между металлическими лентами как раз в “закрытой” для графитовых лент конструкции.
МИКРОСТРУКТУРА МЕТАЛЛИЧЕСКИХ ФОЛЬГ С КАРБИДНЫМИ ПОКРЫТИЯМИ
Исследование структуры металлических фольг с покрытиями проводилось с помощью растровой электронной микроскопии и рентгеновского спектрального анализа (РСА). Микроструктурные исследования, включающие получение изображений объектов во вторичных и отраженных (обратно-рассеянных) электронах и РСА, выполнялись на цифровых электронных сканирующих микроскопах Tescan VEGA-II XMU и CamScan MV230. Микроскопы имеют W-катоды, оснащены YAG-детекторами вторичных и отраженных электронов и рентгеновским микроанализатором. Глубина области характеристического рентгеновского излучения достигала 5–6 мкм. На горизонтальном разрезе это есть круг, а в объеме – зона грушевидной формы с максимальным диаметром ~10 мкм.
Nb-ленты с карбидными покрытиями
На рис. 2 представлены микроструктуры поперечных сечений ниобиевых лент двух толщин после термообработки их в составе пакетов, проложенных двумя лентами ТРГ толщиной ∼0.5 мм, и результаты локального РС-анализа.
Рис. 2.
Микроструктура поперечного сечения Nb-лент толщиной 60 (а) и 70 мкм (б) после твердофазного взаимодействия с лентами ТРГ при 1500°С и 15 МПа в течение 1 ч и их концентрационные профили ниобия и углерода: 1–5 (а) и 1–12 (б) – точки спектров.
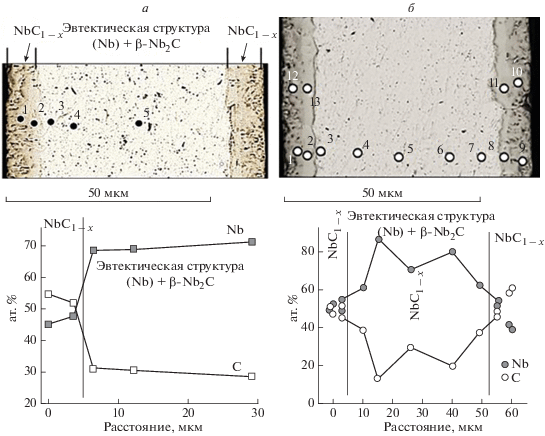
При используемых нами режимах термообработки многослойных пакетов ТРГ/ТРГ/Nb/ТРГ/ ТРГ/Nb… объем Nb-лент насыщался углеродом до состава эвтектической области (Nb) + β-Nb2C бинарной диаграммы Nb–C, и на обеих поверхностях каждой ленты формировались покрытия из монокарбида NbC1 –х.
По данным локального рентгеновского спектрального анализ (РСА) покрытия состояли из монокарбидов NbC1 – х практически одинаковых составов Nb0.93C1.07 и Nb0.98C1.02 на лентах толщиной соответственно 60 и 70 мкм после термообработки пакета при 1500°С и давлении 15 МПа в течение 1 ч.
Монокарбидные покрытия имели одинаковую толщину, равную ~8.2 мкм, по всей длине лент независимо от их толщины. В покрытиях присутствуют два типа структуры: плотный беспористый слой NbC1 –х, граничащий с эвтектической областью (Nb) + β-Nb2C, толщиной 3.5–4.0 мкм и наружный слой толщиной 4.7–4.2 мкм с зернами, растущими перпендикулярно поверхности ленты-подложки.
В эвтектической структуре Nb-лент наблюдались дискретные выделения вторичного карбида β-Nb2C размером меньше 1 мкм (рис. 3). В ленте толщиной 60 мкм, как в более тонкой подложке, выделения карбида Nb2C были несколько больше по размеру и заметно в большем количестве, чем в ленте толщиной 70 мкм.
Рис. 3.
Микроструктура эвтектической области Nb-ленты толщиной 60 (а) и 70 мкм (б) с выделениями карбида β-Nb2C (показаны стрелками).
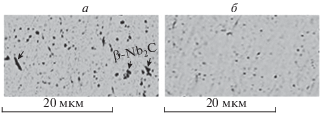
Концентрация углерода в эвтектической области фольг 60-микронной толщины оставалась постоянной на уровне 30 ат. %, а в ленте толщиной 70 мкм она немонотонно изменялась от ~40 вблизи от слоя NbC1 – х до 15–30 ат. % в остальной области эвтектики (см. рис. 2б).
Ленты из Ti-сплава с карбидными покрытиями
Состав фольг Ti-сплава: Ti–10.0% Cr–7.3% Mo–2.6 мас. % Al. После ТО под давлением пакетов ТРГ/ТРГ/Ti-сплав/ТРГ/ТРГ/Ti-сплав… поверхности лент с покрытиями на микронном уровне были негладкими, а покрытия на лентах – неоднородными по толщине – от ~3.5 до 6–7 мкм, но имели беспористые структуры. Различавшиеся почти в 2 раза давления – 8 и 15 МПа – не влияли на морфологию и структуру покрытий.
Рис. 4.
Микроструктура поперечного сечения отрезков ленты из Ti-сплава после ТО под давлением при 1500°С в течение 15 мин под давлением 8 (а) и 15 МПа (б): 1–5 –точки анализа.
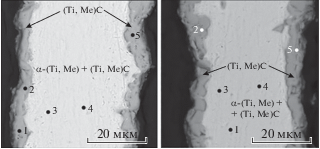
По данным локального РС-анализа покрытия состояли из монокарбида титана: (Ti, Me)C ≡ ≡ (Ti1.18Me0.01)1.19C0.81, где Ме – Cr, Al, Mo. Согласно двойной диаграмме Ti–C состав самих лент с 6.0 ат. % С соответствовал заэвтектической области α-(Ti,Me) + (Ti,Me)C, где α-(Ti,Me) – твердый раствор углерода в матрице на основе титана.
“Покрытия” на лентах из сплава Nb–2% Zr (рис. 5)
Рис. 5.
Микроструктура поперечного сечения ленты (Nb–Zr)-сплава после ТО под давлением при 1500°С в течение 45 мин.

Материал, полученный после термообработки под давлением пакета ТРГ/ТРГ/NbZr/ТРГ/ТРГ/ NbZr… с фольгами из сплава Nb–2% Zr, отличался от всех предыдущих металлических фольг с покрытиями тем, что не имел пограничного карбидного слоя, подобного тем, которые наблюдались на фольгах титанового сплава и ниобия. Взаимодействие фольг (Nb–Zr)-сплава с лентами ТР-графита происходило без образования сплошного поверхностного карбидного слоя как такового. Вблизи поверхности и на глубине до 5–7 мкм наблюдались мелкодисперсные выделения карбида на основе Zr в (Nb)-матрице: (Zr,Nb)C = (Zr0.91Nb0.20)1.11C0.89. По мере продвижения к середине ленты выделения Zr-карбида увеличивались в линейном размере, вытягиваясь в иглы.
По данным РС-анализа матричная фаза представляла собой карбид на основе ниобия: (Nb,Zr)C1 – х = (Nb0.97Zr0.15)1.12C0.88. Если быть точным, то нужно отметить, что в (Nb,Zr)C1 – х-матрице, кроме игольчатых карбидных выделений (Zr,Nb)C, наблюдались и глобулярные выделения (Zr,Nb)C размером меньше 1 мкм. И, по-видимому, их количество по мере продвижения к середине ленты не изменялось.
В итоге можно констатировать, что образовался композит, состоящий из 2 не трещиностойких, но прочных структурных составляющих – матрицы карбида на основе Nb и выделений карбида на основе Zr. Полученный результат был неожиданным и нетривиальным еще и потому, что сами фольги “хрупко” не разрушались, выдерживая изгиб с радиусом ∼10 мм!
Нужно отметить, что возникающая проблема трещиностойкости, в связи с наличием в структуре материала хрупких соединений, давно не считается непреодолимой. Впервые одна из возможностей ее решения была показано еще в 1964 г. в работе [12] путем торможения трещин на слабой границе раздела хрупких фаз. Эта идея впоследствии использовалась при разработке различных слоистых и волокнистых композитов [13, 14]. Поэтому, можно ожидать, что оптимальное совмещение уже полученной структуры через чередование ее, например, со слоями твердых металлических растворов углерода способно будет обеспечить приемлемый уровень трещиностойкости полученного таким образом композита.
ПРОЧНОСТЬ МНОГОСЛОЙНЫХ КОМПОЗИТОВ ИЗ Nb-ФОЛЬГ И ФОЛЬГ Ti-СПЛАВА С КАРБИДНЫМИ ПОКРЫТИЯМИ
Из лент титанового сплава и лент ниобия с карбидными покрытиями были составлены многослойные пакеты для получения из них слоистых композитов с карбидным упрочнением. Режим диффузионной сварки (ДС): 1250°С в течение 2 ч при ~10 МПа.
Из полученных после ДС композитов вырезались образцы для прочностных испытаний на 3-точечный изгиб. Длина образцов совпадала с направлением прокатки фольг. Нагрузка прикладывалась перпендикулярно плоскости слоев в композите.
Был проведен большой комплекс испытаний при комнатной температуре и в интервале температур от 650 до 900°С (рис. 6). Общий итог таков, что и при комнатной температуре σВ = 950–1400 МПа, в температурном интервале 650–900°С – от 400 до 1100 МПа.
Рис. 6.
Значения предела прочности σВ многослойных композитов из металлических лент Ti-сплава (⚫, △, ▲) и ниобия (◼, ◻, ⚪) с карбидными покрытиями после диффузионной сварки при 1250°С, 2 ч, 10 МПа.
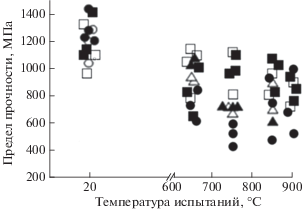
Однако анализы результатов испытаний для каждого из композитов в интервале температур 650–900°С заметно отличаются. Для композита из Nb-фольг σВ в интервале от 650 до 850°С находился в пределах 650–1100 МПа и только при 900°С его верхний предел падал до 950 МПа. В отличие от Nb-композита предел прочности композита из Ti-сплава сначала падал до 400–700 МПа, но при 850–900°С его верхнее значение повышалось до ∼1000 МПа.
ЗАКЛЮЧЕНИЕ
В процессе термообработки под давлением многослойных пакетов из тонких фольг ниобия или Ti-сплава, чередовавшихся с лентами термически расширенного графита, на поверхностях фольг формировались непрерывные плотные покрытия соответственно монокарбидов NbC1 – х и (Ti,Me)C, где Ме – Cr, Al и Mo, толщиной до 6–8 мкм. Внутренний объем фольг имел эвтектические структуры из твердых растворов основного металла и тех же монокарбидов.
Из металлических фольг с карбидными покрытиями формировались многослойные пакеты, подвергавшиеся диффузионной сварке под давлением для получения слоистых композитов с упрочнением карбидными слоями. Испытания композитов на прочность при изгибе показали высокие значения. Предел прочности при комнатной температуре для обоих композитов составлял 1000–1400 МПа, а при температурах в интервале 650–900°С изменялся от 600 до 1100 МПа.
Результаты, представленные по фольгам ниобия с 2% циркония, интересны тем, что после диффузионной сварки пакета, составленного из этих фольг, композит может представлять научный интерес как объект, в котором торможение трещин будет происходить на слабой границе раздела хрупких фаз. По теоретическим оценкам такой эффект способен обеспечить приемлемый для слоистого материала уровень трещиностойкости.
Список литературы
Косолапова Т.Я. Карбиды. М.: Металлургия, 1968. 300 с.
Стормс Э.К. Тугоплавкие карбиды. М.: Атомиздат, 1970. 304 с.
Тот Л. Карбиды и нитриды переходных металлов. М.: Мир, 1974. 294 с.
Кипарисов C.C., Левинский Ю.В., Петров А.П. Карбид титана. Получение, свойства, применение. М.: Металлургия, 1987. 216 с.
Jackson M.R., Bewley B.P., Rowe R.G. et al. // J. Metals. 1996. V. 48. No. 1. P. 39.
Bewley B.P., Jackson M.R., Subramanian P.R. // J. Metals. 1999. V. 51. No. 4. P. 32.
Bewley B.P., Jackson M.R., Zhao J.C., Subramanian P.R. // Met. Mater. Trans. 2003. V. A34. No. 10. P. 2043.
Светлов И.Л., Абузин Ю.А., Бабич Б.Н. и др. // Журн. функц. мат. 2007. Т. 1. № 2. С. 48.
Колобов Ю.Р., Каблов Е.Н., Козлов Э.В. и др. Структура и свойства интерметаллидных материалов с нанофазным упрочнением. М.: ИД МИСиС, 2008. 328 с.
Коржов В.П., Карпов М.И. // Материаловедение. 2009. № 11. С. 39.
Карпов М.И., Внуков В.И., Коржов В.П. и др. // Деф. разруш. мат. 2012. № 12. С. 2.
Cook J., Gordon J.E. // Proc. Royal Soc. 1964. V. 282. No. 8. P. 508.
Анищенков В.М., Милейко С.Т. // ДАН СССР. 1978. Т. 241. № 5. С. 1068.
Kolchin A.A., Kiiko V.M., Sarkissyan N.S., Mileiko S.T. // Compos. Sci. Technol. 2001. V. 61. No. 7. P. 1079.
Дополнительные материалы отсутствуют.
Инструменты
Известия РАН. Серия физическая