Известия РАН. Серия физическая, 2022, T. 86, № 10, стр. 1479-1485
Исследование влияния типа инертного газа на процесс плазмодинамического синтеза оксидов железа
А. И. Циммерман 1, 2, И. И. Шаненков 1, 2, *, А. А. Сивков 2, А. С. Ивашутенко 2, А. Р. Насырбаев 2, В. А. Власов 2
1 Федеральное государственное автономное образовательное учреждение высшего образования
“Тюменский государственный университет”
Тюмень, Россия
2 Федеральное государственное автономное образовательное учреждение высшего образования
“Национальный исследовательский Томский политехнический университет”
Томск, Россия
* E-mail: i.i.shanenkov@utmn.ru
Поступила в редакцию 01.06.2022
После доработки 15.06.2022
Принята к публикации 22.06.2022
- EDN: DUFLUW
- DOI: 10.31857/S0367676522100222
Аннотация
Приведены результаты экспериментальных исследований по оценке влияния типа инертного газа (гелия, азота или аргона), использующегося в смеси с кислородом в качестве газообразной среды камеры-реактора, на продукт плазмодинамического синтеза системы “железо–кислород”. Методами рентгеновской дифрактометрии и сканирующей электронной микроскопии установлено, что синтезированные материалы представляют собой ультрадисперсные порошки, преимущественно состоящие из магнетита Fe3O4 с небольшими включениями гематита α-Fe2O3, вюстита FeO и железа Fe. Экспериментально обнаружено, что при реализации плазмодинамического синтеза в смеси газов N2/O2 и He/O2 содержание магнетита может достигать 85 мас. % в составе продукта, что приводит к достижению наибольшей удельной намагниченности насыщения 78.3 Гс ⋅ см3/г.
ВВЕДЕНИЕ
В последнее время большое внимание уделяется исследованиям магнитных материалов, в частности, оксидов железа различных структурных модификаций и фазового состава. Известно, что существует семь негидратированных фаз оксида железа, которые обычно разделяются по его валентности в химическом соединении [1]. Оксид железа (IV), известный как минерал магнетит (Fe3O4), является одним из наиболее известных магнитных материалов. Благодаря расширению областей возможного применения магнетита, интерес к его получению в различных формах (нано- и микропорошки, объемные керамические материалы, покрытия) постоянно повышается. Среди магнитомягких ферритов Fe3O4 наиболее подходит для медицинских применений из-за того, что он является нетоксичным (при низких дозах), биосовместимым и биоразлагаемым [2, 3]. Ферромагнитные свойства могут быть использованы в процессах магнитной сепарации для удаления вредных клеток крови, антител и различных биологических субстанций из организма человека. Кроме того, магнетит может применяться в устройствах спинтроники, оптических устройствах, биосенсорах и др. [4–6].
На сегодняшний день разработано множество различных методов получения магнетита в ультрадисперсном виде, например, твердотельные реакции, высокоэнергетический механосинтез, золь–гель метод, химическое осаждение, микроволновое спекание и др. [7–9]. Все эти методы имеют как преимущества, так и недостатки, основными из которых являются время протекания химических реакций (от суток до нескольких недель), использование токсичных химикатов и дороговизна процесса. Одним из возможных путей преодоления указанных недостатков является синтез Fe3O4 с использованием плазмы дугового разряда, например, плазмодинамическим методом, который характеризуется высоким быстродействием (время синтеза составляет менее 1 мс), низкими удельными энергозатратами (10 кВт ⋅ ч на 1 кг материала) и использованием относительно дешевых прекурсоров. В ранее опубликованных работах [10, 11] была показана возможность получения магнетита и его использования в качестве радиопоглощающего материала для абсорбции электромагнитного излучения в широком диапазоне частот. Тем не менее, чистота выхода Fe3O4, согласно представленным данным, не превышала 75 мас. %, что, по всей видимости, обусловлено особенностями протекающих процессов в смеси газов Ar/O2, которая использовалась в качестве рабочей среды для плазмохимических реакций.
В представленной работе показаны результаты исследований по оценке возможности повышения содержания магнетита в продукте, полученном плазмодинамическим методом, за счет реализации синтеза с использованием другого инертного газа (гелия) и условно инертного газа по отношению к компонентам системы “железо–кислород” (азота). Установлено, что при реализации плазмодинамического синтеза в смеси газов N2/O2 и He/O2 содержание магнетита может достигать 85 мас. % в составе продукта, что приводит к достижению наибольшей удельной намагниченности насыщения 78.3 Гс ⋅ см3/г.
ЭКСПЕРИМЕНТАЛЬНАЯ ЧАСТЬ
Система плазмодинамического синтеза для получения порошкообразных продуктов системы “железо–кислород” была подробно описана ранее [10]. Основным элементом является коаксиальный магнитоплазменный ускоритель (КМПУ), который представляет собой классический Z-пинч ускоритель, размещенный внутри мощной индукционной системы (рис. 1а). Основными элементами ускорителя являются: хвостовик центрального электрода (1), проходной изолятор (2), опорный изолятор (3), металлическая обойма (4), изолятор наконечника (5), стальная вставка центрального электрода (6), стальной электрод-ствол (7), внешняя индуктивная система (8), разрушаемая перемычка (9) – слой графитового спрея. КМПУ герметично монтируется в рабочую камеру-реактор (рис. 1б), в которой протекают основные плазмохимические реакции. Камера-реактор представляет собой цилиндр с фланцами из нержавеющей стали объемом 0.034 м3. Перед проведением эксперимента камеру вакуумируют при помощи форвакуумного насоса (ФН), после чего заполняют газообразной смесью из инертного газа (азота, гелия или аргона) с добавлением кислорода суммарным давлением 1 атм, регулируемым с помощью манометра (М). Емкостной накопитель энергии (C) заряжается до необходимой величины Uзар. При замыкании силовых ключей (K) батарея конденсаторов начинает разряжаться, что выражается появлением напряжения на электродах КМПУ и протеканием разрядного тока по цепи. При достижении током некоторого значения происходит разрушение перемычки с возникновением дуговой стадии разряда в межэлектродном пространстве канала формирования плазменной структуры [12, 13]. Сформированная плазменная структура ускоряется в коаксиальной системе за счет индукционных и кондукционных электродинамических сил. В ходе ускорения вследствие термического взаимодействия плазмы дугового разряда со стенками ускорительного канала (электрода-ствола) происходит вовлечение в движение плазменной струи эродированного материала (железа). Это железо и является основным прекурсором плазмодинамического синтеза.
Рис. 1.
Принципиальная схема экспериментальной установки по синтезу оксидов железа: коаксиальный магнитоплазменный ускоритель (а); камера-реактор (б).
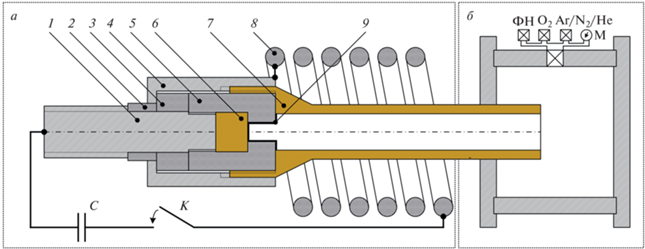
Для серии экспериментов были выбраны газы с разными физическими свойствами (плотность, теплопроводность и теплоемкость при постоянном объеме). Соотношение парциальных давлений инертного газа и кислорода ω(O2) во всех экспериментах составляло 90%/10%, соответственно, для наибольшей наработки магнетита [10]. В качестве марки электродов ускорителя была выбрана сталь “Ст20” из-за низкого содержания примесных элементов, которые согласно оценке методом рентгенофлюоресцентной волнодисперсионной спектроскопии (Shimadzu XRF-1800) составили: Fe – 98.87 мас. %; Mn – 0.45 мас. %, Si – 0.35 мас. %, прочие элементы – менее 0.10 мас. %.
Исходные энергетические параметры накопителя (зарядное напряжение Uзар, емкость Сзар и накапливаемая энергия WC конденсаторных батарей) в рамках данной серии экспериментов оставались неизменными и были выбраны такими же, как и в ранее проведенных исследованиях [10]. Результаты регистрации энергетических параметров процесса синтеза (табл. 1) получены путем осциллографирования напряжения на электродах КМПУ и импульсного тока электропитания с последующей аналитической обработкой для определения максимальной мощности Pмакс и подведенной энергии W. Эти данные свидетельствуют об отсутствии влияния типа газовой среды на энергетические характеристики процесса, что позволяет исключить их влияние.
Таблица 1.
Энергетические параметры серии экспериментов
№ | Состав газовой среды | ω(O2), % |
Uзар, кВ |
Cзар, мФ |
WC, кДж |
Uд, кВ |
Iмакс, кА |
Pмакс, МВт |
W, кДж |
---|---|---|---|---|---|---|---|---|---|
1 | He/O2 | 10 | 2.5 | 14.4 | 45 | 1.02 | 139 | 141 | 33.1 |
2 | N2/O2 | 1.00 | 142 | 142 | 32.5 | ||||
3 | Ar/O2 | 1.02 | 142 | 143 | 33.2 |
Напряжение на электродах КМПУ u(t) и импульсный ток электропитания i(t) в процессе проведения эксперимента регистрировались с помощью омического делителя напряжения и трансформатора Роговского соответственно. Запись массива данных происходила с помощью цифрового осциллографа Tektronix 2012. Используя эти данные, были построены кривые мощности дугового разряда в ускорительном канале p(t) и подведенной энергии w(t), как показано на рис. 2.
Рис. 2.
Осциллограммы напряжения на электродах u(t), импульсного тока электропитания i(t), электрической мощности разряда в ускорительном канале p(t) и подведенной энергии w(t): эксперимент № 1 (а), № 2 (б) и № 3 (в) (номера экспериментов соответствуют номерам в табл. 1).
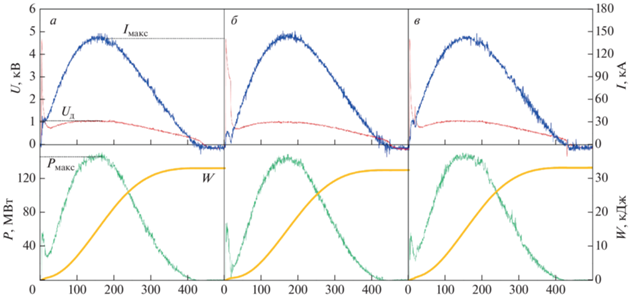
В результате проведения экспериментов были получены порошкообразные материалы, которые после полного осаждения из взвешенного состояния без дополнительной обработки исследовались методами рентгеновской дифрактометрии (дифрактометр Shimadzu XRD 7000S, CuKα излучение) и сканирующей электронной микроскопии (СЭМ) (микроскоп Hitachi TM3000). Обработка и анализ рентгеновских дифрактограмм для оценки фазового состава синтезированных материалов производились в программной среде Powder Cell 2.4 с использованием базы данных PDF4. Значения удельной намагниченности насыщения синтезированных материалов определены с помощью автоматизированного комплекса для исследования магнитных характеристик в импульсных полях (магнитометр Н-04).
РЕЗУЛЬТАТЫ АНАЛИТИЧЕСКИХ ИССЛЕДОВАНИЙ
Процесс плазмодинамического синтеза материалов осуществляется при распылении электроэрозионной плазмы в газообразную среду камеры-реактора. Как известно [14], скорость плазменного потока в указанной системе зависит от параметров среды, а именно от давления, плотности, вида и концентрации активных и инертных газов. Условия ускорения плазменного потока и, соответственно, внешнего сопротивления газовой среды влияют на скорость распыления и дисперсность получаемых материалов. Кроме того, в работе [15] было показано, что соотношение парциальных давлений аргона и кислорода в газовой смеси непосредственно влияет на фазовый состав синтезируемых оксидов железа, а получение продукта с преимущественным содержанием магнетита наиболее предпочтительно в условиях низкой концентрации O2. Получаемые в таких условиях частицы магнетита отличаются полой сферической формой, что обусловлено особенностями их формирования при попадании в кислородсодержащую среду. Подробно механизм формирования таких частиц был изучен в работе [11], где сделан вывод о том, что формирование полостей внутри частиц происходит по модели “пузыря” при наличии жидкой фазы и быстро расширяющегося газа. По всей видимости, нарушение условий отвода тепла способствует увеличению размеров таких полых частиц, но в тоже время приводит к общему снижению содержания магнетита за счет фазовых превращений из магнетита в гематит, вызванных локальным нагревом. Это послужило основанием для проведения серии экспериментов в газовой смеси, содержащей другие инертные и условно инертные газы (гелий и азот).
Полученные в результате проведения таких экспериментов материалы были исследованы методом рентгеновской дифрактометрии (рис. 3). Как видно из приведенных данных, дифрактограммы представляют собой совокупность когерентных отражений трех основных фаз оксидов железа (магнетит Fe3O4, гематит α-Fe2O3 и вюстит FeO). Также для образцов, полученных в экспериментах с гелием (рис. 3а) и азотом (рис. 3б), на дифрактограммах идентифицируется наличие максимумов высокой интенсивности, характерных для чистого металлического железа (Fe). Стоит отметить, что в случае плазмодинамического синтеза в среде гелия интенсивность рентгеновских пиков, соответствующих фазе гематита α‑Fe2O3, является минимальной, а для аргона максимальной.
Рис. 3.
Дифрактограммы продуктов плазмодинамического синтеза, полученных в условиях газовой смеси: He/O2 (а), N2/O2 (б) и Ar/O2 (в).
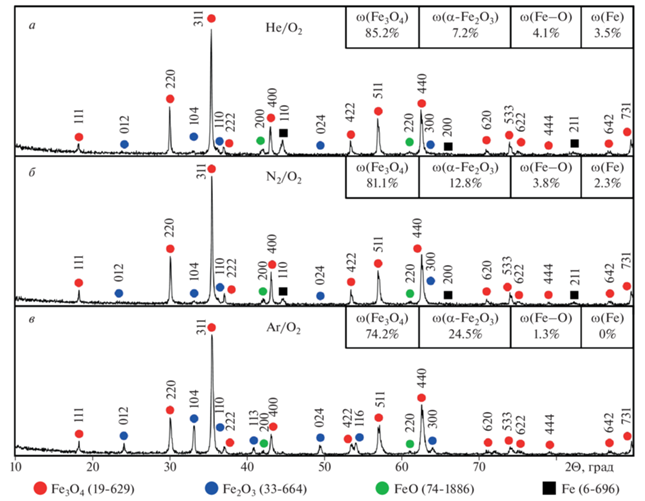
Содержание кристаллических фаз в продуктах плазмодинамического синтеза, определенное по результатам количественного рентгеноструктурного анализа, представлено на рис. 3. Наибольшее содержание Fe3O4 (до 85 мас. %) наблюдается в условиях использования газовой смеси азота и кислорода, а наименьшее – при использовании аргона в смеси с кислородом. Соответственно, обратные эффекты наблюдаются для фазы гематита (α-Fe2O3).
Этот момент является весьма показательным, если учесть тот факт, что гематит – наиболее термодинамически стабильная фаза в рассматриваемой системе “железо–кислород”, и ее формирование в указанных условиях возможно вследствие высокотемпературного воздействия, оказываемого плазменным потоком на газовую среду, особенно обладающую низкой теплоотводящей способностью. Таким образом, чрезмерный нагрев жидкофазного материала может приводить не только к формированию полых частиц, но и служить причиной фазовых превращений Fe3O4 → → α-Fe2O3. В этой связи для подтверждения высказанных предположений были проведены исследования структуры синтезируемых частиц магнетита, полученных в каждом из экспериментов.
На рис. 4 приведены характерные микроснимки частиц магнетита, полученных в условиях газовой среды He/O2 (рис. 4а и 4г), N2/O2 (рис. 4б и 4д) и Ar/O2 (рис. 4в и 4е). Во всех случаях основу синтезированных продуктов преимущественно составляют частицы сферической формы с достаточно широким распределением по размерам от единиц до сотен микрометров (а–в), мало отличающиеся внешне. Для изучения внутренней структуры этих сферических частиц был осуществлен помол в агатовой ступке, что позволило обнаружить ряд характерных особенностей. В случае использования аргона, отличающегося наименьшей теплопроводностью, также, как и в ранних работах [11], были получены полые сферические частицы (рис. 4е), что согласуется с данными рентгенофазового анализа, на которых видно увеличение содержания фазы гематита. Размол частиц, синтезированных в азоте и гелии, позволил обнаружить, что они преимущественно представляют собой агрегаты, состоящие из большого количества более мелких частиц. Несмотря на наличие локальных участков, где, по всей видимости, происходило расширение газа, можно утверждать, что вследствие высокой теплопроводности этих газов, отвод тепла осуществлялся более эффективно, что не приводило к росту “пузыря”. Таким образом, это позволило избежать чрезмерного нагрева жидкофазного материала и предотвратить фазовые превращения Fe3O4 → → α-Fe2O3. Следовательно, удалось сохранить исходную структуру магнетита, что и отразилось положительным образом на увеличении его содержания в составе конечных продуктов, согласно данным рентгенофазового анализа.
Рис. 4.
СЭМ-снимки продуктов плазмодинамического синтеза, полученных в условиях газовой смеси: He/O2 (а), N2/O2 (б) и Ar/O2 (в). СЭМ-снимки продуктов плазмодинамического синтеза, полученных в условиях газовой смеси (после размола): He/O2 (г), N2/O2 (д) и Ar/O2 (е).
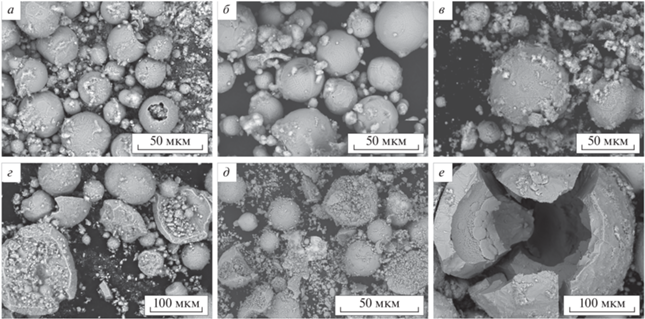
Увеличение процентного содержания магнетита в составе синтезируемых продуктов ожидаемо должно приводить к росту их магнитных свойств. В этой связи была проведена оценка величины удельной намагниченности насыщения σs для всех синтезируемых материалов. Данные результаты были получены с использованием автоматизированного комплекса для исследования магнитных характеристик в импульсных полях при заряде конденсаторов магнитометра до 200 В, что соответствует намагничивающему полю величиной 18.6 кЭ. При больших значениях заряда конденсаторов и, соответственно, величине поля удельная намагниченность не изменялась. В табл. 2 приведены удельные намагниченности насыщения для синтезированных порошкообразных материалов, значения которых, как оказалось, достаточно близки к известным литературным данным (~80 Гс ⋅ см3/г) [16].
ЗАКЛЮЧЕНИЕ
Показана возможность получения ультрадисперсных частиц в системе “железо–кислород” плазмодинамическим методом и изменения фазового состава продуктов за счет варьирования типа инертного газа (азот, аргон, гелий) в смеси с кислородом. Установлено, что использование гелия и азота вместо аргона позволяет увеличить содержание магнетита с 75 до 85 мас. % и, следовательно, увеличить удельную намагниченность насыщения продукта с 70.9 до 78.3 Гс ⋅ см3/г. Методом сканирующей электронной микроскопии установлено, что условия газовой среды оказывают непосредственное влияние на структуру получаемых частиц магнетита. Таким образом, в условиях плазмодинамического синтеза возможно не только управлять фазовым составом конечных продуктов за счет изменения газообразной среды, но и изменять структуру частиц магнетита, что положительным образом сказывается на конечных магнитных свойствах.
Работа выполнена при финансовой поддержке в рамках темы государственного задания № FEWZ-2021-0014 (Научно-технические основы и прикладные решения комплексной энерготеплотехнологической переработки биомассы для обеспечения экологически чистых технологий в энергетике и металлургии).
Список литературы
Tuček J., Machala L., Ono S. et al. // Sci. Rep. 2015. V. 5. Art. No. 15091.
Marinca T., Chicinaş H., Neamţu B. et al. // Mater. Chem. Phys. 2016. V. 171. P. 336.
Li J., Ji H., Xu Y. et al. // J. Mater. Res. Technol. 2020. V. 9. No. 1. P. 762.
Venugopal R., Dhanyaprabha K., Thomas H., Sini R. // Mater. Today. Proc. 2020. V. 25. P. 1.
Pekdur Ö., Yıdırım S., Büyükmumcu Z. // J. Mol. Struct. 2020. V. 1222. Art. No. 128895.
Goikhman A., Shvets P., Koneva U. et al. // Thin Solid Films. 2018. V. 652. P. 28.
Saeed M., Seyed-Yazdi J., Hekmatara H. // J. Alloys Compounds. 2020. V. 843. Art. No. 156052.
Dehkordi R., Toghraie D., Hashemian M. et al. // Int. Commun. Heat Mass Transfer. 2020. V. 116. Art. No. 104653.
Chen T., Wang Q., Lyu J. et al. // Sep. Purif. Meth. 2020. V. 231. Art. No. 115930.
Shanenkov I., Sivkov A., Ivashutenko A. et al. // J. Alloys Compounds. 2019. V. 774. P. 637.
Shanenkov I., Sivkov A., Ivashutenko A. et al. // Phys. Chem. Chem. Phys. 2017. V. 19. No. 30. Art. No. 19975.
Kuzenov V.V., Ryzhkov S.V., Frolko P.A. // J. Phys. Conf. Ser. 2017. V. 830. No. 1. Art. No. 012049.
Kuzenov V.V., Ryzhkov S.V., Varaksin A.Y. // Appl. Sci. 2022. V. 12. No. 7. P. 3610.
Sivkov A., Shanenkova Y., Vympina Y. et al. // Surf. Coat. Technol. 2022. V. 440. Art. No. 128484.
Сивков А., Шаненков И., Ивашутенко А. и др. // Росс. нанотехнол. 2017. Т. 12. № 7–8. С. 25; Sivkov A., Shanenkov I., Ivashutenko A. et al. // Nanotechnol. Russ. 2017. V. 12. No. 7. P. 352.
Del Bianco L., Spizzo F., Barucca G. et al. // Nanoscale. 2019. V. 11. No. 22. Art. No. 10896.
Дополнительные материалы отсутствуют.
Инструменты
Известия РАН. Серия физическая