Известия РАН. Серия физическая, 2022, T. 86, № 6, стр. 873-878
Нанотехнологические методы в задачах создания современных пьезоэлектрических корректоров волнового фронта
В. В. Топоровский 1, *, А. В. Кудряшов 1, 2, А. А. Скворцов 2, В. В. Самаркин 1, Ю. В. Шелдакова 1, А. Л. Рукосуев 1
1 Федеральное государственное бюджетное учреждение науки
“Институт динамики геосфер имени академика М.А. Садовского Российской академии наук”
Москва, Россия
2 Федеральное государственное автономное образовательное учреждение высшего образования
“Московский политехнический университет”
Москва, Россия
* E-mail: topor@activeoptics.ru
Поступила в редакцию 17.01.2022
После доработки 07.02.2022
Принята к публикации 21.02.2022
- EDN: FSOCIW
- DOI: 10.31857/S0367676522060308
Аннотация
Рассмотрены возможности использования нанотехнологических методов производства корректоров волнового фронта биморфного типа. Показаны результаты удаления электропроводящего слоя с поверхности пьезокерамического диска импульсным Nd:YAG лазером. Создание электрического контакта осуществлялось методом расщепленного электрода для медной проволоки и пленки серебра.
ВВЕДЕНИЕ
Корректор волнового фронта – основополагающий элемент адаптивных оптических систем [1–3]. Его основной функцией, как исполнительного устройства, является непосредственная компенсация искажения светового излучения путем изменения своей формы под действием определенных механизмов: электростатических [4, 5], электромагнитных [6] или пьезоэлектрических [7, 8].
При изготовлении деформируемых зеркал широко используются современные материалы и технологий производства. Так, например, при создании подложек для корректоров применяется метод химического осаждения из газовой фазы для получения желаемой геометрии c возможностью реализации каналов охлаждения непосредственно внутри подложки [9], а также вакуумное напыление для снижения общей поверхностной плотности зеркала в задачах построения космических телескопов [10]. При создании управляющих элементов используются аддитивные технологии, например, лазерная стереолитография [11, 12]. Помимо этого, значительно распространены нанотехнологические методы магнетронного распыления и термического осаждения в области создания отражающих и проводящих покрытий для адаптивных зеркал [13, 14].
Тем не менее, развитие элементной базы адаптивной оптики сопряжено с проблемой создания надежных и миниатюрных устройств компенсации искажений лазерного излучения [15–17]. Поэтому, при разработке устройств для коррекции фазовых флуктуаций светового пучка необходимо применять инновационные методы, например, такие как ультразвуковая сварка [18], контактная сварка расщепленным электродом [19] и лазерная абляция [20].
В первом разделе данной работы представлен общий принцип работы биморфного деформируемого зеркала и основные этапы его изготовления. Во втором – описаны технологии производства, позволяющие уменьшить размер корректора и обеспечивающие устойчивую работу как гибкого зеркала, так и всей адаптивной оптической системы. Также рассмотрены основные параметры использованных технологий и продемонстрировано нанесение сетки электродов на пьезокерамическую пластину и создание надежного электрического контакта между проводом и проводящим покрытием на поверхности пьезодиска. В третьем разделе приводятся результаты изготовления биморфного деформируемого зеркала с малой апертурой и высокой плотностью управляющих элементов. Проведен анализ эффективности применения данных методик при использовании различных технологий присоединения контактных проволок с целью выявления дальнейших перспектив развития технологии производства корректоров волнового фронта биморфного типа.
БИМОРФНЫЕ КОРРЕКТОРЫ ВОЛНОВОГО ФРОНТА
Датой выделения адаптивной оптики как отдельной отрасли науки принято считать 1953 г. [21], когда Х. Бэбкок предложил использовать зеркало с нанесенным на его поверхность слоем электропроводящего масла, при подаче электрического заряда на который, локально изменяется его толщина (по принципу работы эйдофора [22]). Это приводило к изменению оптической длины пути оптического луча и позволяло компенсировать искажения волнового фронта светового пучка.
С этого момента было разработано большое количество различных типов корректирующих устройств [23–27]. При этом в данной области намечена тенденция увеличения количества управляющих элементов на меньшей площади [28] и повышения надежности таких приборов [29] с последующим снижением стоимости конечного продукта. Самым подходящим с точки зрения относительно низкой стоимости и высокой ремонтопригодности конструкции являются биморфные деформируемые зеркала [30, 31]. Более того, наша группа широко известна разработкой подобных гибких зеркал [32–36]. Но тем не менее существует задача создания таких корректоров с высоким пространственным разрешением электродов. Именно поэтому наше внимание было сосредоточено на совершенствовании конструкции этих устройств.
Биморфное гибкое зеркало представляет собой полированную пассивную подложку, сделанную из стекла, кремния или меди, к которой приклеивается активная пьезокерамическая пластина с проводящим покрытием из серебра или никеля (рис. 1а). На внешней поверхности пьезодиска размещена сетка электродов (рис. 1б и 1в). При подаче напряжений на управляющие электроды под действием обратного пьезоэлектрического эффекта пьезопластина расширяется (или сжимается) и происходит деформация (изгиб) поверхности зеркала. Благодаря приложению необходимых управляющих сигналов можно формировать требуемую форму отражающей поверхности.
Рис. 1.
Традиционное биморфное зеркало: конструкционная схема зеркала и принцип действия: 1 – пассивная подложка, 2 – пьезокерамический диск, 3 – заземленный электрод, 4 – управляющие электроды, 5 – изолирующие дорожки, U – прикладываемое напряжение (а); радиально-кольцевая геометрия электродов (б); гексагональная геометрия электродов (в).
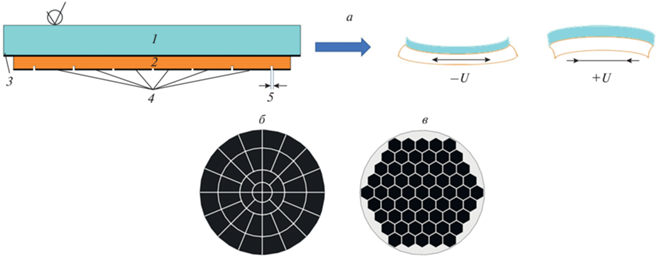
Основные этапы изготовления традиционного биморфного зеркала представляют следующую последовательность: 1) пьезокерамическая пластина приклеивается к пассивной подложке; 2) после этого методом фотолитографии наносится сетка электродов; 3) затем, подложка полируется для достижения высокого качества отражающей поверхности; 4) на следующем этапе наносится покрытие с высоким коэффициентом отражения (>99.9%); 5) далее при помощи токопроводящего клея производится соединение контактов с поверхностью пьезодиска; 6) и, наконец, выполняется электрический монтаж контактов зеркала и сборка в оправе.
Данный процесс производства корректора биморфного типа характерен для зеркал со средней (30–100 мм) и большой (>100 мм) апертурой. Причем при сборке больших зеркал обеспечивается предварительная механическая коррекция путем изменения натяжения винтов, расположенных в оправе. Такое решение позволяет снизить влияние начальных аберраций (астигматизм, кома), возникающих после сборки и напыления отражающего покрытия.
Однако, в задачах дистанционного зондирования атмосферы лидарными средствами [37] или при лазерной обработке материалов [38] важным становится задача создания малоапертурных зеркал (<30 мм). Причем количество управляющих элементов должно позволять компенсировать аберрации волнового фронта до 5 порядка, наличие которых характерно для искажений, вызванных атмосферной турбулентностью [39].
Как известно, пьезокерамика является пористым материалом, что вызывает некоторые сложности при нанесении сетки электродов. Традиционная методика химического травления не вполне применима в данном случае, так как ее использование не всегда может обеспечить полное вымывание проводящего покрытия из пор керамики. Но в то же время создание изолирующих дорожек на поверхности диска способом лазерной абляции может привести к излишнему удалению пьезоматериала.
Также, при изготовлении малоапертурных зеркал определенной задачей является присоединение электрических проводов, потому что размер контактной площадки значительно уменьшается (~5–20 мм2), а для такого размера электрода крайне затруднительно применить традиционную технологию приклеивания проводов. Использование обычных методов пайки также невозможно, так как нагрев пьезодиска ведет к деполяризации пьезокерамики, что влечет за собой выход из строя зеркала.
По этой причине предлагается использовать методы лазерной абляции и контактной сварки при изготовлении биморфных корректоров волнового фронта.
НАНОТЕХНОЛОГИЧЕСКИЕ МЕТОДЫ ДЛЯ ИЗГОТОВЛЕНИЯ БИМОРФНЫХ ДЕФОРМИРУЕМЫХ ЗЕРКАЛ
Технология лазерной абляции используется для получения наночастиц в коллоидных растворах [40] и для создания наноструктурированных покрытий [41]. Также данная методика применяется для удаления части вещества с поверхностей разного рода материалов [42]. Традиционная установка лазерной абляции представлена на рис. 2а. Принцип работы устройства заключается в следующем: свет от излучателя передается через систему зеркал на объектив и фокусируется на поверхности объекта. В процессе лазерной абляции испаряется верхний или несколько верхних слоев, после чего в материале возникают небольшие углубления. Для обработки металлов применяются лазеры с длиной волны порядка 1 мкм [43], например, твердотельные Nd:YAG лазеры. Также, нередко используется излучение с вдвое меньшей длиной волны, равной 532 нм. В состав установки лазерной абляции входит одномодовый Nd:YAG лазер с модуляцией добротности, с энергией импульсов 0.67 мДж, длительностью 100 нс и частотой повторения от 20 до 200 кГц, средняя выходная мощность достигает 20 Вт. Рабочее поле обработки образцов – 110 × 110 мм, фокусное расстояние объектива – 160 мм, скорость обработки образцов равна 5000 мм/с. Минимальный размер фокального пятна на поверхности обрабатываемого материала составляет порядка 50 мкм. Преимуществами данной технологии являются: быстрота процесса; высокая точность; полная автоматизация, что позволяет исключить брак при обработке изделий. Тем не менее ее применение имеет значительный недостаток – неравномерность удаления вещества по площади объекта, что вызвано неоднородностью обрабатываемого материала.
Рис. 2.
Биморфное деформируемое зеркало с высокой плотностью управляющих элементов: схема лазерной абляции: 1 – сканатор, 2 – поворотное зеркало, 3 – лазерный источник, 4 – линза объектива, 5 – обрабатываемый объект (а); геометрия электродов зеркала (б); схема контактной сварки расщепленным электродом: 1 – рабочий инструмент, 2 – микропроволока, 3 – подложка, 4 – металлизированная контактная площадка (в); стрелками указано направление действия силы F, приложенной к рабочему инструменту, пунктир – схематичное изображение протекания тока I; биморфное деформируемое зеркало в сборе (г).
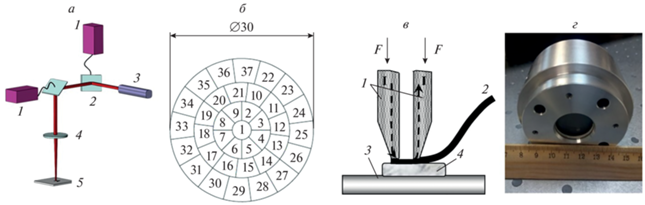
Как было отмечено ранее, излишний нагрев биморфной пластины может привести к дополнительным начальным аберрациям отражающей поверхности зеркала, а также снижению эффективности коррекции аберраций волнового фронта. В связи с этим характеристики технологии лазерной абляции должны быть подобраны исходя из максимально допустимой температуры нагрева пьезодиска. Очевидно, что в зависимости от свойств пьезопластины (толщина покрытия, материал покрытия) должны быть изменены параметры лазерного излучения, необходимые для удаления проводящего слоя.
Создание изолирующих дорожек на поверхности пьезодиска является отдельной задачей, которую предлагается решить путем применения установки лазерной абляции, где имеется возможность оптимизации частоты повторения импульсов, мощности излучения, скорости обработки изделия. В нашем случае были использованы пьезокерамические диски толщиной 0.2 мм. На их поверхности находится проводящий серебряный слой толщиной приблизительно 20 мкм. При создании изолирующих дорожек в слое серебра использовалось излучение со средней мощностью 4 Вт при частоте повторения импульсов 20 кГц. Скорость обработки составила 150 мм/с. На диск были нанесены изолирующие дорожки шириной 300 мкм. Данная величина была выбрана во избежание возникновения поверхностного электрического пробоя.
Была получена радиально-кольцевая геометрия управляющих элементов с 37 актюаторами на апертуре 30 мм (рис. 2б). В данном случае площадь одного электрода составляла в среднем 10 мм2. С нашей точки зрения лучшим решением для соединения контактного провода с пьезодиском является применение технологии ультразвуковой и контактной сварки, широко используемые в микроэлектронике.
При монтаже изделий электронной техники одним из наиболее распространенных способов электрического соединения между контактными площадками кристалла является соединение при помощи проволочных выводов [44]. Традиционные методы сварки при выполнении таких монтажных соединений практически не применяют, что обусловлено малыми размерами соединений. Микросоединения выполняют, как правило, золотой, алюминиевой или медной проволокой диаметром от 30 до 150 мкм. Для создания микросварных соединений используют различные методы сварки, основными из которых являются: термокомпрессионная, ультразвуковая, расщепленным электродом.
Термокомпрессионная сварка применяется для присоединения выводов к полупроводниковым кристаллам, сварки микропроводов и проволок между собой, приварки жил плоского кабеля к выводам соединителя и др. (Т = 250—450°С) [45]. Однако локальные температуры в процессе сварки могут достигать 650°С. Столь высокие температурные нагрузки не позволяют использовать термокомпрессионную сварку для задач изготовления пьезоэлектрических адаптивных зеркал.
Свободным от указанного недостатка является метод ультразвуковой сварки (УЗС) микропроводников. Этот метод характеризует ввод энергии ультразвука в область контакта [46]. Такой подход приводит к растрескиванию и выгоранию твердых жировых пленок в области контакта, пластическое деформирование материала, а также интенсивную диффузию. Одновременно с этим происходит активация контактных поверхностей, приводящая к образованию очагов взаимодействия в условиях пластической деформации свариваемых материалов и наложения ультразвукового поля. Таким образом, УЗ-колебания создают условия для разрушения оксидных пленок и формирования надежного омического контакта свариваемых поверхностей. Как правило, УЗС применяется для алюминиевой (иногда медной и серебряной) проволок диаметром 20–200 мкм. Нами экспериментально отработаны процессы УЗ приварки алюминиевых и медных проволок диаметром 50–100 мкм к различным поверхностям (Al, Cu, Ag).
Однако следует отметить, что наряду с минимальными тепловыми нагрузками на область формируемого контакта, нам не удалось добиться нужной величины усилия отрыва Р. Для контактной пары “алюминиевая проволока (диаметр d = = 80 мкм) – пленка серебра (толщина h = 20 мкм)” величина силы на отрыв для алюминиевого провода при ультразвуковой сварке составляет PAl(US) = = 0.15–0.20 Н в зависимости от различных режимов, а для пары “медная проволока (d = 75 мкм) – пленка серебра (h = 20 мкм)” величина усилия на отрыв медного провода PCu(US) = 0.2…0.25 Н.
Большие значения величины PCu были получены методом сварки расщепленным электродом. Данная технология является разновидностью контактной сварки [19], приспособленной к особенностям конструкции адаптивного зеркала (рис. 2б). Свариваемыми материалами являлись медь, алюминий и серебро. Толщина пленок серебра составляла 0.01–0.03 мм, диаметр проводников меди и алюминия – 100 мкм. Материалом электродов выступал вольфрам.
Подготовка свариваемых поверхностей заключалось в предварительном отжиге материалов для снятия внутренних напряжений и увеличения пластичности, в обезжиривании поверхностей химическими растворителями. Сварку осуществляли инструментом-электродом, изготовленным из вольфрама в виде токопроводящих частей, разделенных зазором 0.02–0.25 мм в зависимости от толщины или диаметра привариваемых выводов.
Качество сварки сдвоенным электродом обеспечивало для контактной пары “медная проволока (d = 80 мкм) – пленка серебра (h = 20 мкм)” значение усилия на отрыв PCu(R) = 0.45–0.50 Н в зависимости от режимов сварки.
На рис. 3 представлены результаты приваривания медной проволоки диаметром 80 мкм к серебряной пленке толщиной 20 мкм на поверхности пьезокерамического диска в составе биморфного деформируемого зеркала.
ОБСУЖДЕНИЕ РЕЗУЛЬТАТОВ И ДАЛЬНЕЙШИЕ ПЕРСПЕКТИВЫ
Оптимизация классических технологий лазерной абляции и контактной сварки методом расщепленного электрода для задач адаптивной оптики позволила изготовить биморфный корректор волнового фронта с высокой плотностью управляющих элементов (рис. 2г). Было показано, что при использовании метода ультразвуковой сварки для соединения медных проволочных выводов с серебряной площадкой пьезодиска значение величины усилия на отрыв PCu(US) составило 0.2–0.25 Н, в то время как применение метода расщепленного электрода позволило получить вдвое большее значение – PCu(R) = 0.45–0.5 Н. Был отработан способ соединения медных проволочных выводов с серебряной площадкой пьезодиска при помощи метода расщепленного электрода. Нанотехнологические методы показывают свою эффективность при изготовлении устройств адаптивной оптики. В дальнейшем предполагается использование стереолитографических методов для создания деформируемых зеркал на основе микроэлектромеханических систем (МЭМС), где плотность управляющих элементов составляет в среднем 9 актюаторов на мм2.
ЗАКЛЮЧЕНИЕ
Показаны результаты применения лазерной абляции для нанесения сетки электродов на серебряном покрытии пьезодиска биморфного корректора волнового фронта диаметром 30 мм. Использование лазера Nd:YAG лазер с модуляцией добротности со средней мощностью 4 Вт при частоте повторения импульсов 20 кГц и скоростью обработки 150 мм/с позволило получить изолирующие дорожки шириной 300 мкм. Показана эффективность применения технологии контактной сварки расщепленным электродом в сравнении с методом ультразвуковой сварки в задаче создания надежного электрического контакта между медным проводом диаметром 80 мкм и серебряной контактной площадкой толщиной 20 мкм.
Список литературы
Sato T., Ishida H., Ikeda O. // Appl. Opt. 1980. V. 19. P. 1430.
Wei K., Zhang X., Xian H. et al. // Chin. Opt. Lett. 2010. V. 8. P. 1019.
Kudryashov A., Rukosuev A., Nikitin A. et al. // Opt. Expr. 2020. V. 28. Art. No. 37546.
Bifano T. // Nature Photon. 2011. V. 5. P. 21.
Moghimi M., Wilson C., Dickensheets D. // Proc. SPIE. 2013. V. 8617. Art. No. 861707.
Biasi R., Gallieni D., Salinari et al. // Proc. SPIE. 2010. V. 7736. Art. No. 77362B.
Toporovsky V.V., Kudryashov A.V., Samarkin V.V. et al. // Atmos. Ocean. Opt. 2020. V. 33. P. 584.
Самаркин В.В., Александров А.Г., Джитсуно Т. и др. // Квант. электрон. 2015. Т. 45. № 12. С. 1086.
Ahn K., Rhee H.-G., Yang H.-S., Kihm H. // Opt. Expr. 2018. V. 26. P. 9724.
Patterson K., Pellegrino S. // Appl. Opt. 2013. V. 52. P. 5327.
Cholleti E.R. // IOP Conf. Ser. Mater. Sci. Engin. 2018. V. 455. Art. No. 012046.
Hall S., Regis J., Renteria A. et al. // Ceram. Int. 2021. V. 47. No. 15. Art. No. 22042.
Hickey G., Barbee T., Ealey M., Redding D. // Proc. SPIE. 2010. V. 7731. Art. No. 773120.
Rausch P., Verpoort S., Wittrock U. // Opt. Expr. 2015. V. 23. Art. No. 19469.
Bendek E., Lynch D., Pluzhnik E. et al. // Proc. SPIE. 2016. V. 9909. Art. No. 990984.
Divoux C., Cugat O., Basrour S. et al. // Proc. SPIE. 1998. V. 3353. P. 850.
Toporovsky V., Kudryashov A., Samarkin V. et al. // Proc. SPIE. 2021. V. 11672. Art. No. 1167215.
Neppiras E.A. // Ultrasonics. 1965. V. 3. No. 3. P. 128.
Biele L., Schaaf P., Schmid F. // Phys. Stat. Sol. A. 2021. V. 218. No. 19. Art. No. 2100224.
Chichkov B., Momma C., Nolte S. et al. // Appl. Phys. A. 1996. V. 63. No. 2. P. 109.
Babcock H.W. // Publ. Astron. Soc. Pac. 1953. V. 65. P. 89.
Labin E. // J. SMPTE Soc. 1950. V. 54. No. 4. P. 393.
Lefaudeux N., Levecq X., Dovillaire G. et al. // Nucl. Instrum. Meth. Phys. Res. A. 2011. V. 653. No. 1. P. 164.
Salinari P., Del Vecchio C. Biliotti V. // Proc. ICO-16. 1994. V. 48. P. 261.
Lück H., Müller K., Aufmuth P., Danzmann K. // Opt. Commun. 2000. V. 175. P. 275.
Ivanova N., Onokhov A., Chaika A. et al. // Proc. SPIE. 1996. V. 2754. P. 180.
Samarkin V., Alexandrov A., Toporovsky V. et al. // Proc. SPIE. 2021. V. 11849. Art. No. 1184917.
Riaud P. // A&A. 2012. V. 545. Art. No. A25.
Cornelissen S., Bifano T., Bierden P. // Proc. SPIE. 2012. V. 8253. Art. No. 825306.
Oya S., Bouvier A., Guyon O. et al. // Proc. SPIE. 2006. V. 6272. Art. No. 62724S.
Alaluf D., Bastaits R., Wang K. et al. // Appl. Opt. 2018. V. 57. P. 3629.
Kudryashov A., Kulakov V., Kotsuba Ye. et al. // Proc. SPIE. 1999. V. 3688. P. 469.
Galaktionov I., Sheldakova J., Nikitin A. et al. // Opt. Expr. 2020. V. 28. No. 25. Art. No. 38061.
Kudryashov A., Alexandrov A., Rukosuev A. et al. // Appl. Opt. 2015. V. 54. P. 4352.
Wattellier B., Fuchs J., Zou J.-P. et al. // J. Opt. Soc. Amer. B. 2003. V. 20. P. 1632.
Samarkin V., Aleksandrov A., Dubikovsky V., Kudrya-shov A. // Proc. SPIE. 2005. V. 6018. Art. No. 60180Z.
Tan X., Wu Z., Liang Z. // Proc. SPIE. 2009. V. 7284. Art. No. 72840G.
Spalding I. // High Power Laser Sci. Engin. 1996. V. 7. P. 27.
Noll R. // J. Opt. Soc. Amer. 1976. V. 66. P. 207.
Arakelyan S., Veiko V., Kutrovskaya S. et al. // J. Nanopart. Res. 2016. V. 18. P. 155.
Takaku R., Wen Q., Cray S. et al. // Opt. Expr. 2021. V. 29. Art. No. 41745.
Chryssolouris G. Laser machining – theory and practice. N.Y.: Springer-Verlag, 1991. 274 p.
Patel R., Chaudhary P.S., Soni D.K. // IJSRD. 2015. V. 2. No. 11. P. 1.
Babu S., Santella M., Feng Z. et al. // Sci. Technol. Weld. Join. 2001. V. 6. P. 126.
Reinert W., Kulkarni A., Vuorinen V., Merz P. Handbook of silicon based MEMS materials and technologies. William Andrew Publishing, 2015. P. 626.
Sprigode T., Gester A., Wagner G. et al. // Metals. 2021. V. 11. No. 12. Art. No. 1936.
Дополнительные материалы отсутствуют.
Инструменты
Известия РАН. Серия физическая