Химическая физика, 2022, T. 41, № 1, стр. 52-59
Формирование мах-фазы Ti2AlC в гидридном цикле из смеси порошков карбогидридов титана и алюминия
С. К. Долуханян 1, *, А. Г. Алексанян 1, О. П. Тер-Галстян 1, Г. Н. Мурадян 1, Н. Л. Мнацаканян 1, К. В. Асатрян 1, А. С. Мнацаканян 1
1 Институт химической физики Национальной Академии наук Армении им. А.Б. Налбандяна
Ереван, Армения
* E-mail: seda@ichph.sci.am
Поступила в редакцию 16.12.2020
После доработки 12.01.2021
Принята к публикации 20.01.2021
- EDN: IDAAPC
- DOI: 10.31857/S0207401X22010046
Аннотация
Создание и разработка новых методов и технологий получения MAX-фаз – преспективных материалов на основе бескислородной керамики, востребованных в современном материаловедении в качестве конструкционных материалов, является актуальной задачей. Существующие методы их получения довольно сложны, энергоемки и многостадийны. Разработка жизнеспособных коммерческих предложений, обеспечивающих меньшую стоимость и создающих возможность изготовления MAX-фаз в большем количестве, представляет научный и практический интерес. В настоящей работе представлены результаты исследований процессов формирования МАХ-фазы Ti2AlC в гидридном цикле (ГЦ) при использовании в качестве исходных компонентов карбогидридов титана TiC0.45H1.07–1.17 (содержание H2 – 1.97–2.17 вес.%) с ГПУ-структурой и TiC0.5H0.22–0.73 (содержание Н2 – 0.44–1.48 вес.%) с ГЦК-структурой. Изучалась реакция TiC0.45–0.5H0.22–1.17 + 0.5Al → Ti2AlC + Н2↑. В задачу работы входило установление влияние температур и времени нагрева на фазовый состав и структуру МАХ-фазы Ti2AlC. Для аттестации образцов использовался следующий набор методов анализа: химический, дифференциально-термический, рентгенофазовый. Mикроструктуру образцов исследовали на сканирующем электронном микроскопе SEM Prisma E. В результате исследований в ГЦ была синтезирована однофазная MAX-фаза Ti2AlC (а = 3.0553 Å, с = 13.6459 Å, с/а = 4.466; группа симметрии P63/mmc). Формирование MAX-фазы Ti2AlC в ГЦ происходит по твердофазному механизму, в одну технологическую стадию при температуре нагрева до 1000 °С в течение 0.5–1 ч. Показаны преимущества метода гидридного цикла при синтезе MAX-фазы Ti2AlC относительно традиционных методов, которые позволяют упростить технологический процесс, снизить энергозатраты и повысить качество.
ВВЕДЕНИЕ
Растущий интерес к МАХ-фазам связан с уникальным набором свойств, которые обусловлены природой их особого кристаллического строения. Это многослойные химические соединения с общей формулой Мn+ 1АХn, где М – переходный металл, А – элемент подгруппы “А” таблицы Менделеева, X – углерод или азот. Слоистая гексагональная элементарная ячейка МАХ-фаз относится к пространственной группе P63/mmc, в которой шестиугольные (hexagonal) слои Mn+ 1Xn расположены между слоями A (Si, Al, Ga и т.д.) [1–3]. Они (MAX-фазы) были исследованы в Дрексельском университете (США) в лаборатории профессора М. Барсоума на протяжении более десяти лет, где и были синтезированы десятки слоистых карбидов, нитридов и карбонитридов. Эти карбиды и нитриды сочетают в себе достоинства как керамических, так и металлических материалов, и в некоторых публикациях их называют “металлическая керамика”. Подобно металлам, МАХ-фазы обладают высокой прочностью, превосходной коррозионной стойкостью в агрессивных жидких средах, стойкостью к высокотемпературному окислению и термическим ударам, имеют высокую температуру плавления и являются достаточно стабильными при температурах до 1000 °С и выше, высокой электрической и тепловой проводимостью, превосходной жаростойкостью, а также легко подвергаются механической обработке. С другой стороны, как керамические материалы, они стойки к окислению, к усталостным нагрузкам, жаростойкие, сохраняют прочность при высоких температурах, имеют небольшой удельный вес (низкую плотность), обладают высоким модулем упругости, характеризуются низким коэффициентом трения и низким тепловым коэффициентом расширения [1–4].
Потенциальные области применения МАХ-фаз: термоустойчивые огнеупоры, высокотемпературные нагревательные элементы, покрытия для электрических контактов, а также МАХ-фазы, устойчивые к радиационному (особенно нейтронному) облучению [4] и поэтому пригодные для ядерных применений. Кроме того, МАХ-фазы являются исходным материалом для получения MXenes-семейства двумерных карбидов, нитридов и карбонитридов переходных металлов. Удаление слоя А из MAX-фаз приводит к образованию двумерных слоев, которые маркируются как MXenes. Известно, что двумерные (2D) материалы, такие как графен, обладают уникальными свойствами, что может потенциально привести к некоторым перспективным их применениям [5–7].
Известны около пятидесяти МАХ-фаз, соответствующих стехиометрической формуле М2АХ (Mn+ 1AXn, т.е. n = 1). Их принято обозначать как 211. В кристаллической решетке М2АХ параметр с должен быть примерно в 4 раза больше параметра а. Композиты алюминий–MAX-фаза обладают способностью улучшать пластичность и ударную вязкость. Среди них фаза Ti2AlC является одной наиболее интересной с типичной структурой 211. Она обладает самой низкой плотностью среди всех соединений этого класса, отличной электропроводностью, небольшим коэффициентом трения [8], имеет высокую температуру плавления (1625 °С) и стабильна при высоких температурах [5].
Наиболее известными способами получения МАХ-фаз являются: индукционная, электродуговая или электронно-лучевая плавки; порошковая металлургия – горячее изостатическое прессование (ГИП), реактивное спекание, такое как горячее прессование, искровое плазменное спекание, спекание с импульсным разрядом; химическое осаждение из паровой фазы при различных температурах; самораспространяющийся высокотемпературный синтез (СВС) и др.
Процесс синтеза МАХ-фаз Ti2AlC, Ti2AlN, Ti3AlC2, Ti3SiC2 и других методом ГИП из смеси тонкодисперсных порошков (размер частиц – 2–10 мкм) титана, углерода, алюминия и карбида кремния хорошо отработан в Дрексельском университете (США) М. Барсоу с сотр. [1, 3, 4]. Горячее изостатическое прессование требует больших затрат энергии, времени и большого числа технологических операций, характерных для порошковой металлургии: прессование, вакуумное спекание или горячее прессование, отжиг пластификатора и др.
Фазы Ti2AlC и Ti3AlC2 были получены методом искрового плазменного спекания с использованием порошков Ti, Al и графита [9]. Был также использован метод СВС в сочетании с ГИП [10–14]. Авторами работы [14] было показано, что МАХ-фазы Ti2AlC и Ti3AlC2 возможно синтезировать, используя СВС с восстановительной стадией при горении системы TiO2–Mg–Al–C в среде аргона под давлением 3 МПа. Синтез проводили при нагревании порошков до температуры 1500 °C в течение 2 ч. В синтезированных таким образом МАХ-фазах кроме основных фаз Ti2AlC и Ti3AlC2 содержались фазы MgAl2O4 и TiC.
Почти при всех перечисленных выше методах наряду с МАХ-фазами, например Ti2AlC, всегда наблюдались второстепенные фазы, такие как TiCx, TiAlx и Ti3AlC2 [1–15]. Существующие методы их получения довольно сложны, энергоемки и многостадийны и не являются практическими методами для массового промышленного производства изделий из MAX-фаз. Недавние исследования и разработки выявили потенциал для практического применения MAX-фаз. Задачи на ближайшее будущее состоят в том, чтобы продолжить изучение известных на сегодняшний день MAX-фаз и добиться дальнейшего прогресса в облегчении их промышленного применения [16]. Таким образом, создание и разработка новых методов и технологий получения MAX-фаз, материалов, востребованных в современном материаловедении в качестве конструкционных материалов для авиакосмической, оборонной, химической, пищевой промышленности, медицины (имплантанты) и других областей является актуальной задачей.
В этой связи наиболее актуальной проблемой в исследовании MAX-фаз является разработка жизнеспособных коммерческих предложений, обеспечивающих меньшую стоимость, создающих возможность изготовления MAX-фаз сложной геометрии в большем количестве.
В настоящее время исследования по MAX-фазам финансируется агентствами, научными фондами и оборонной промышленностью в России, США, Китае, Европе, Австралии и др. В Лаборатории высокотемпературного синтеза и технологии неорганических соединений ИХФ НАН РА был разработан новый высокоэффективный метод получения сплавов и интерметаллидов тугоплавких металлов – метод гидридного цикла [17–23]. Сущность метода заключается в использовании в качестве исходных материалов гидридов переходных металлов. В процессе нагрева компактированной смеси двух и более гидридов и удалении водорода при температурах чуть выше температур диссоциации гидридов происходит формирование прочных, беспористых сплавов. В настоящей работе метод ГЦ использован для синтеза MAX-фазы состава Ti2AlC.
ЭКСПЕРИМЕНТАЛЬНАЯ ЧАСТЬ
В качестве исходных материалов использовали титан марки ПТМ-1, алюминий чистотой 99.7% и ламповую сажу. Для проведения настоящих исследований предварительно методом СВС были синтезированы карбогидриды титана TiC0.45H1.07–1.17 с ГПУ-структурой (содержание Н2 – 1.97–2.17 вес.%) и TiC0.5H0.22–0.73 с ГЦК+ (5–10%) ГПУ-структурой (содержание Н2 – 0.4–1.48 вес.%); см. табл. 1 [24, 25]. Карбогидриды измельчались до фракции <7.5 мкм. Тщательно перемешанная смесь карбогидридов с порошком алюминия прессовалась в цанговых прессформах в цилиндрические таблетки диаметром 22 мм и высотой 20 мм на гидравлическом прессе (усилие прессования – до 20 000–45 000 кГс).
Таблица 1.
Параметры процесса ГЦ и характеристики MAX-фаз
Карбогидриды титана; кристаллическая структура; параметры в Å | Условия ГЦ | MAX-фаза; кристаллическая структура; параметры в Å |
---|---|---|
Ti; ГПУ (P63/mmc); a = 2.95, с = 4.686 |
– | – |
TiC0.45H1.07–1.17 (содержание Н2 – 1.97–2.15 вес.%); основная фаза – ГПУ (P63/mmc), а = 3.0442, с = 5.0930; + 1–5% ГЦК-фазы, а = 4.3101 |
Рпр = 20 000 кГс Тн = 1000 °С t = 1 ч |
Ti2AlC; гексагональная (P63/mmc): a = 3.0553, с = 13.6459, с/а = 4.466 |
TiC0.5H0.22–0.73 (содержание Н2 – 0.4–1.48 вес.%); основная фаза – ГЦК, а = 4.3165; + до 5% ГПУ-фазы |
Рпр = 20000 кГс Тн = 1000 °С t = 0.5–1 ч |
Ti2AlC; гексагональная (P63/mmc); а = 3.0614, с = 13.663, с/а = 4.466 |
Исследования проводили в герметичной установке, состоящей из кварцевого реактора, печи, приборов для контроля вакуума и температур в реакторе. Таблетки устанавливали в реактор, вакуумировали до 10–3 Торр и включали нагрев. Процесс ГЦ проводили при температурах 600–1000 °C.
Для аттестации образцов использовали следующие анализы: химический, дифференциально-термический (ДТА, дериватограф Q-1500) и рентгенофазовый (РФА, дифрактометр ДРОН-0.5). Дифференциально-термический анализ проводили при нагреве образца до 1000 °С со скоростью нагрева 20 °С/мин. Дифракционные картины идентифицировали с помощью Международной картотеки ASTM. Параметры кристаллических решеток рассчитывались по известным формулам. Количественный фазовый анализ проводили путем расчета нормированной интенсивности самого высокого дифракционного пика каждой фазы. Ошибки в количественном анализе были определены при повторении расчетов 3 раза для параллельных образцов. Mикроструктуру образцов исследовали на сканирующем электронном микроскопе SEM Prisma E. Плотность образцов измеряли гидростатическим методом, рентгеновскую плотность рассчитывали по параметрам кристаллической решетки.
В задачу входило экспериментальное исследование влияния химического и фазового состава шихты (соотношения карбогидрида титана и порошков алюминия в реакционной смеси), размеров зерен карбогидрида титана (микро- и наноразмеры), давления прессования при компактировании шихты, а также режимов дегидрирования/спекания (температуры и скорости нагрева в ГЦ) на характеристики полученных фаз.
Надо отметить, что синтезированные порошки карбогидрида титана благодаря высокому содержанию водорода легко диспергируются до размеров частиц <10 мкм и ниже (до субмикронных размеров, включая нано размеры кристаллитов: 20–80 нм [26]). Кроме того, при приготовлении реакционной шихты тщательное перемешивание смеси в течение 30–60 мин приводит к дальнейшему интенсивному измельчению исходного карбогидрида титана.
Исследовалась реакция TiC0.45–5H0.22–1.17 + + 0.5Al → Ti2AlC + Н2↑. На рис. 1 представлена термограмма процесса ГЦ при нагреве реакционной смеси TiC0.45H1.17 + 0.5Al до Tн = 1000 °С в течение времени t = 60 мин.
Рис. 1.
Термограмма процесса ГЦ при нагреве реакционной смеси TiC0.45H1.17 + 0.5Al до 1000 °С в течение 60 мин.
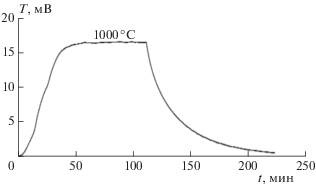
По данным РФА в результате проведения серии экспериментов в ГЦ была синтезирована однофазная MAX-фаза состава Ti2AlC с гексагональной элементарной ячейкой и параметрами а = 3.055 Å, с = 13.6459 Å, с/а = 4.47 со следами ГЦК-фазы TiC. На рис. 2 представлены дифракционные картины: а – исходного карбогидрида TiC0.45H1.17 (ГПУ + 5% ГЦК); б – реакционной шихты TiC0.45H1.17 + 0.5Al; в – MAX-фазы состава Ti2AlC, полученного в ГЦ при нагреве до Tн = 1000 °С и t = 60 мин.
Рис. 2.
Дифракционные картины: а – карбогидрида TiC0.45H1.17 (ГПУ + 5% ГЦК); б – реакционной шихты TiC0.45H1.17 + + 0.5Al; в – MAX-фазы состава Ti2AlC, полученного в ГЦ при нагреве до Tн = 1000 °С и выдержке в течение 60 мин.
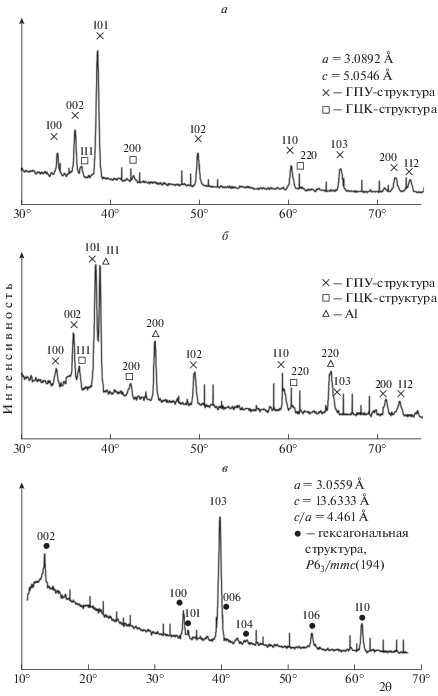
На рис. 3 представлена микроструктура карбогидрида TiC0.45H1.17, исследованная с помощью растровой электронной микроскопии. Как видно, размер зерен составляет <7.2 мкм.
На рис. 4 представлена микроструктура MAX-фазы состава Ti2AlC0.9. Максимальный размер зерен MAX-фазы не превышает 7.9 мкм.
В другой серии экспериментов для синтеза MAX-фазы был использован карбогидрид TiC0.5H0.22–0.73, содержащий в основном ГЦК-фазу с примесью 5% ГПУ (табл. 1). Первоначально предполагали, что использование карбогидрида с ГПУ структурой должно способствовать формированию MAX-фазы состава Ti2AlC в ГЦ. Дальнейшие исследования показали, что формирование MAX-фазы состава Ti2AlC происходит также при использовании ГЦК-карбогидрида TiC0.5H0.22–0.73, даже при небольшом содержании водорода.
На рис. 5 представлены дифракционные картины: а – карбогидрида TiC0.5H0.67 (ГЦК + 5% ГПУ); б – реакционной шихты TiC0.5H0.67 + 0.5Al; MAX-фаз состава Ti2AlC, полученных в ГЦ при нагреве до Tн = 1000 °С и выдержках в течение 60 (в) и 30 мин (г). Было показано, что для формирования MAX-фазы Ti2AlC в ГЦ достаточно нагревать исходную шихту при 1000 °С в течение 30 мин.
Рис. 5.
Дифракционные картины: а – карбогидрида TiC0.5H0.67 (ГЦК + 5% ГПУ); б – реакционной шихты TiC0.5H0.67 + + 0.5Al; MAX-фаз состава Ti2AlC, полученных в ГЦ при нагреве до Tн = 1000 °С и выдержках в течение 60 (в) и 30 мин (г).
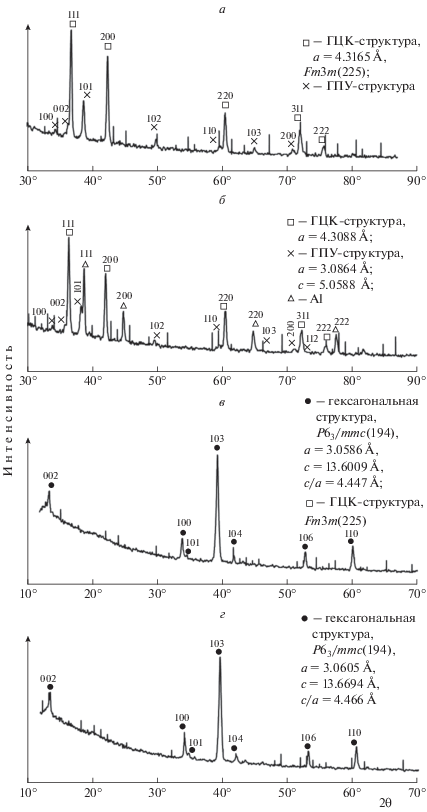
Для выявления термических эффектов, протекающих в ГЦ, и установления механизма формирования MAX-фазы состава Ti2AlC был проведен ДТА исходного карбогидрида состава TiC0.45H1.17 и реакционной шихты TiC0.45H1.17 + 0.5Al в условиях, близких к ГЦ. На рис. 6 представлены ДТА-кривые: а – карбогидрида TiC0.45H1.17, б – реакционной шихты TiC0.45H1.17 + 0.5Al. При нагреве до 1000 °С карбогидрида титана на ДТА-кривой 2 (рис. 6а) наблюдаются три эндопика, обусловленные диссоциацией водорода из карбогидрида титана при 460, 580 и 800 °С соответственно. При нагреве реакционной шихты TiC0.45H1.17 + 0.5Al (рис. 6б) на ДТА-кривой наблюдаются: один эндопик при 580 °С, обусловленный выходом водорода из карбогидрида титана, один экзопик при 640 °С и второй эндопик при 790 °С.
Рис. 6.
Кривые ДТА: а – карбогидрида состава TiC0.45H1.17, б – реакционной шихты TiC0.45H1.17 + 0.5Al.
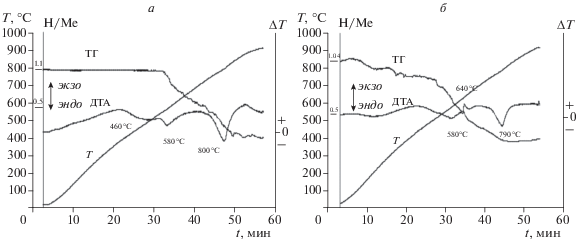
Данные РФА промежуточных и конечных продуктов, полученные в процессе ГЦ и ДТА при закалке при разных температурах, позволили установить маршрут формирования MAX-фазы в ГЦ. При нагреве реакционной шихты TiC0.45H1.17 + 0.5Al начинается частичная диссоциация водорода из карбогидрида. Разрыв связи TiC0.45H1.17 – х–Hх приводит к активации карбогидрида и экзотермическому взаимодействию его с алюминием при 640 °С. Появление экзопика вероятнее всего связано с взаимодействием алюминия с частично разложенным карбогидридом титана и, фактически, началом формирования MAX-фазы Ti2AlC. При этом образуется промежуточная фаза (алюмокарбогидрид), которая с повышением температуры теряет последнюю порцию водорода (второй эндопик при 790 °С), что практически приводит к структурированию MAX-фазы.
Таким образом, при внедрении алюминия в нестехиометрический карбогидрид титана происходит фазовый переход ГПУ-структуры карбогидрида с параметрами a = 2.95 Å; с = 4.686 Å; с/а = 1.59 в гексагональную MAX-фазу Ti2AlC с параметрами элементарной ячейки а = 3.0568 Å, с = 13.658 Å, с/а = 4.468. В табл. 1 представлены условия проведения процесса ГЦ и характеристики MAX-фаз, полученных в ГЦ.
Несколько иначе можно описать формирование MAX-фазы Ti2AlC при использовании карбогидрида TiC0.5H0.22–0.73 с ГЦК-структурой, содержащего 1–5% ГПУ-фазы. При нагреве, в зависимости от содержания водорода в ГЦК карбогидриде титана, диссоциация последнего происходит при Т = 780 °С. Разрушаются связи TiC0.5–H, и активированный таким образом нестехиометрический карбид титана экзотермически взаимодействует с алюминием аналогично ГПУ-карбогидриду состава TiC0.45H1.17. При этом происходит фазовый переход уже ГЦК-структуры (а = 4.3165) в гексагональную MAX-фазу Ti2AlC с параметрами гексагональной элементарной решетки а = 3.0614 Å, с = 13.663 Å, с/а = 4.466.
Плотность синтезированной MAX-фазы состава Ti2AlC, измеренная гидростатическим методом, равна 3.78–3.88 г/см3; рентгеновская плотность, рассчитанная по параметрам гексагональной кристаллической решетки (а = 3.0553–3.568 Å, с = 13.6459–3.658 Å), равна 4.034 г/см3. Измеренная рентгеновская плотность MAX-фазы Ti2AlC и параметры гексагональной кристаллической решетки хорошо совпадают с известными литературными данными [16, 27].
Мишель Борсоум в работе [27] пишет “На данный момент лучшая и первая MAX-фаза, которая будет принята для высокотемпературных приложений, вероятно, будет Ti2AlC по двум причинам: во-первых, присутствие алюминия, обладающего превосходной стойкостью к окислению; во-вторых, Ti2AlC, скорее всего, самый дешевый из MAX-фаз”.
ВЫВОДЫ
1. Синтезирована MAX-фаза состава Ti2AlC методом гидридного цикла при использовании в качестве исходных реагентов карбогидридов титана: TiC0.45H1.07–1.17 с ГПУ-структурой; TiC0.5H0.22–0.73 с ГЦК-структурой, и порошка алюминия.
2. Показано, что однофазная MAX-фаза Ti2AlC формируется при использовании карбогидридов с ГПУ- и ГЦК-структурами.
3. Установлено, что на формирование MAX-фазы Ti2AlC в ГЦ существенное влияние оказывают:
– природа химической связи TiC0.45–0.5–H и фазовые переходы;
– физические свойства карбогидридов – пластичность, высокая диспергируемость до микронных, субмикронных и наноразмеров в зерне порошка;
– химические свойства (содержание водорода, относительно низкие температуры диссоциации).
4. Показан одностадийный твердофазный механизм формирования MAX-фазы Ti2AlC в ГЦ.
5. Установлены оптимальные параметры процесса ГЦ, приводящие к формированию однофазной MAX-фазы Ti2AlC.
6. Показаны преимущества метода гидридного цикла при синтезе MAX-фазы Ti2AlC относительно традиционных методов: снижение температур и длительности процесса; понижение энергозатрат; одностадийность; высокопроизводительность и экологическая чистота; доступность высокоэффективного, неэнергоемкого технологического СВС-процесса получения карбогидридов титана.
Список литературы
Barsoum M.W. // Amer. Sci. 2000. V. 89. P. 336.
Naguib M., Mashtalir O., Carle J., Presser V., Jun Lu et al. // ACS Nano. 2012. V. 6. № 2. P. 1322.
Barsoum M.W. // Prog. Solid State Chem. 2000. V. 28. Issues 1–4. P. 201.
Barsoum M.W., Ali M., El-Raghy T. // J. Metallurg. Mate. Trans. 2000. № 31. P. 1857.
Rao C.N., Subrahmanyam K.S., Matte H.S. et al. // Sci. Technol. Adv. Mater. 2010. V. 11. P .054502.
Gogotsi Y. // ACS Nano. 2019. V. 13. P. 8491; www. acsnano.org
Шабалин И.Л. // Изв. вузов. Порошк. металлургия и функц. покрытия. 2018. № 4. С. 73; dx.doi.org/https://doi.org/10.17073/1997-308X-2018-4-73-81
Lu Chengjie, Sun Liangbo, Zhang Jie et al. // Ceram. Intern. 2017. V. 43. № 12. P. 8579.
Zhou W.B., Mei B.C., Zhu J.Q., Hong X.L. // J. Article Mater. Lett. 2005. V. 59. № 1. P. 131; https://doi.org/10.1016/j.matlet.2004.07.052
Bai Yuelei, He Xiaodong, Li Yibin, Chuncheng Zhu et al. // J. Mater. Res. 2009. V. 24. № 8. P. 2528; https://doi.org/10.1557/JMR.2009.0327
Łopacin’ski Michał, Puszynski Jan, Lis Jerzy // J. Amer. Ceram. Soc. 2004. V. 84. № 12. P. 3051; https://doi.org/10.1111/j.1151- 2916.2001.tb01138.x
Bazhin P.M., Kovalev D.Yu., Luginina M.A., Averichev O.A. // Intern. J. Self-Propag. High-Temp. Synth. 2016. V. 25. № 1. P. 30.
Bagliuk G.A., Suprun O.V., Mamonova A.A. // Phys. Chem. Solid State. 2017. V. 18. № 4. P. 438; https://doi.org/10.15330/pcss.18.4.438-443
Martirosyan V.A., Sasuntsyan M.E. // Intern. J. Pharma Sci. Sci. Res. 2019. V. 5. Issue 1.
Вершинников В.И., Ковалёв Д.Ю. // Сб. матер. Междунар. конф. “СВС-50”. 2017. С. 89; ISBN 978-5-91845-080-2
Sun M. // Intern. Mater. Rev. 2011. V. 56. № 3. P. 143; https://doi.org/10.1179/1743280410Y.0000000001
Долуханян С.К., Тер-Галстян О.П., Алексанян А.Г., Мнацаканян Н.Л. // Хим. физика. 2017. Т. 36. № 4. С. 1.
Dolukhanyan, S.K., Aleksanyan A.G., Ter-Galstyan O.P. et al. // Intern. J. Self-Propag. High-Temp. Synth. 2010. V. 19. № 2. P. 85.
Aleksanyan A.G., Dolukhanyan S.K., Ter-Galstyan O.P. et al. // J. Alloys Compd. 2011. V. 509. P. 786.
Aleksanyan A.G., Dolukhanyan S.K., Ter-Galstyan O.P. et al. // Intern. J. Hydrogen Energy. 2012. V. 37. P. 14234.
Dolukhanyan S.K., Aleksanyan A.G., Shekhtman V.Sh. et al. // Intern. J. Self-Propag. High-Temp. Synth. 2014. V. 23. № 2. P. 78.
Мурадян Г.Н., Долуханян С.К., Алексанян А.Г. и др. // Хим. физика. 2019. Т. 38. № 1. С. 38.
Долуханян С.К., Тер-Галстян О.П., Алексанян А.Г. и др. // Хим. физика. 2015. Т. 34. № 9. С. 1.
Долуханян С.К., Мартиросян Н.А., Мержанов А.Г., Налбандян А.Б. Способ получения карбогидрида титана: А.с. № 683191.СССР // Б. И. 1978. № 32. С. 13.
Мартиросян Н.А., Долуханян С.К., Мержанов А.Г. // Физика горения и взрыва. 1981. № 4. С. 24.
Shekhtman V.Sh., Dolukhanyan S.K., Abrosimova G.E. et al. // Intern. J. Hydrogen Energy. 2001. V. 26. P. 435.
Barsoum M. // Annu. Rev. Mater. Res. 2011; https://doi.org/10.1146/annurev-matsci-062910-100448
Дополнительные материалы отсутствуют.
Инструменты
Химическая физика