Химия твердого топлива, 2021, № 3, стр. 18-23
БРИКЕТИРОВАНИЕ МЕЛКОЗЕРНИСТОГО УГОЛЬНОГО СЫРЬЯ СО СВЯЗУЮЩИМИ
Н. И. Буравчук 1, *, О. В. Гурьянова 1, **
1 ФГАОУ ВО “Южный федеральный университет”
344006 Ростов-на-Дону, Россия
* E-mail: nburavchuk@sfedu.ru
** E-mail: oguryanova@sfedu.ru
Поступила в редакцию 29.10.2020
После доработки 03.02.2021
Принята к публикации 03.02.2021
Аннотация
Представлены результаты экспериментальных исследований по подбору связующих для брикетирования антрацитовых штыбов и угольных шламов, имеющихся в Ростовской области. Исследовано влияние гранулометрического состава угольных компонентов, содержания связующего, влажности шихты, удельного давления прессования на технические свойства топливных брикетов. Приведен технический анализ экспериментальной партии топливных брикетов. Рассмотрен механизм упрочнения и формирования структуры и свойств топливных брикетов.
Одним из крупных потребителей твердого топлива являются слоевые топочные устройства промышленной энергетики и коммунально-бытового хозяйства. При сложившейся тенденции сокращения выпуска сортовых углей для коммунально-бытовых нужд возникает потребность в дополнительных видах твердого топлива. В угольно-промышленных регионах накоплены значительные количества угольных отходов: антрацитовый штыб, коксовая и каменноугольная мелочь, угольные шламы. Запасы угольных мелкозернистых материалов огромны, но использование их в тонкодисперсном состоянии не эффективно. Однако исследование технических характеристик этих отходов (зольность, содержание серы, выход летучих веществ, теплота сгорания) позволяют установить их перспективность для использования в качестве полноценного топлива. Для этого нужны технологии переработки технологической мелочи и низкосортных углей и других энергонесущих отходов в кондиционное топливо. Получить продукт с необходимыми свойствами из некондиционного, но имеющего определенный энергетический потенциал сырья, можно применив технологию брикетирования. Проблема использования отсевов каменных углей и антрацитов все активнее привлекает внимание многих исследователей [1–3] в связи с возможностью утилизировать угольную мелочь и получить дополнительное кондиционное топливо. Наиболее обоснованным технологическим направлением, которое может обеспечить получение топлива с удовлетворительными потребительскими характеристиками, является брикетирование некондиционных углеродсодержащих отходов со связующими.
ЭКСПЕРИМЕНТАЛЬНАЯ ЧАСТЬ
В данной работе приведены результаты исследований брикетирования мелкозернистого угольного сырья с экологически чистыми связующими. В качестве объектов исследования использовали угольные продукты: антрацитовый штыб и угольный шлам углеобогатительных фабрик Ростовской области. Характеристика угольного сырья приведена в табл. 1.
Таблица 1.
Характеристика углеродсодержащих продуктов
Компонент | Элементный состав,% | Технический анализ | ||||||
---|---|---|---|---|---|---|---|---|
Cdaf | Hdaf | Odaf + Ndaf | Sdaf | Ad,% | $W_{t}^{r}$,% | V daf,% | $Q_{s}^{{daf}}$, МДж/кг | |
АШ ОФ “Октябрьская Южная” | 95.6 | 1.22 | 0.77 | 0.9 | 6.7 | 11.0 | 3.0 | 31.44 |
АШ ЦОФ “Гуковская” | 93.3 | 1.66 | 0.68 | 2.2 | 29.0 | 9.8 | 6.3 | 20.64 |
Шлам ЦОФ “Гуковская” | 82.7 | 1.46 | 0.77 | 1.3 | 28.0 | 23.8 | 8.9 | 16.70 |
Шлам ОФ “Замчаловская” | 70.6 | 1.49 | 0.92 | 1.2 | 29.9 | 22.6 | 8.7 | 16.72 |
Наибольшую сложность для брикетирования антрацитовых штыбов представляет подбор связующего вещества. Связующее должно обеспечивать необходимую механическую прочность брикетов при их изготовлении, хранении и использовании. В отечественной и зарубежной практике наибольшее распространение получили каменноугольный пек и нефтебитумы. Однако такие связующие не обеспечивают экологической чистоты топливных брикетов. Неорганические связующие повышают зольность и ухудшают горение брикетов. Отсутствие недефицитных и безвредных связующих веществ является основной причиной, сдерживающей развитие производства брикетного топлива из антрацитовых штыбов и каменноугольной мелочи.
В проведенных исследованиях основным связующим веществом являются побочные продукты сахарно-свекловичной и крахмально-паточной промышленности Краснодарского края: меласса и гидрол. Проведены результаты сравнения использования этих связующих в технологии брикетирования мелкозернистого угольного сырья.
Меласса – отход свеклосахарного производства. По внешнему виду это сиропообразная высоковязкая жидкость от коричневого до темно-бурого цвета. Интенсивность окраски зависит от количества коллоидов. Плотность мелассы находится в пределах 1.30–1.52 г/см3. Основным веществом в мелассе является сахароза: 45–50%, органические вещества: 20–25%, минеральные несахарные вещества: до 10% и вода: до 20%. В холодное время года для снижения вязкости мелассы в емкостях-резервуарах предусмотрен подогрев до 25–40°С.
Гидрол представляет собой сиропообразную легкоподвижную жидкость темно-коричневого цвета с плотностью 1.30–1.34 г/см3. В его состав входят глюкоза, продукты разложения глюкозы и хлористый натрий. В числе минеральных веществ гидрола содержатся: калий, натрий, фосфор, кальций. Реализуется гидрол с содержанием 65–77% сухих веществ, в том числе около 50% глюкозы, 11–14% поваренной соли, 6–8% золы, а также органические кислоты. Выход гидрола составляет 56% выработки кристаллической глюкозы. Гидрол проявляет связующие и клеящие свойства, сохраняет подвижность при низкой температуре (до –10°С), что позволяет исключить подогрев при его использовании. Вязкость гидрола меньше, чем мелассы. Меласса и гидрол хорошо смешиваются с водой в любых соотношениях. Эти продукты не горючи, не взрывоопасны и не токсичны. Хранятся эти вещества в закрытых емкостях специальных цистерн. Срок хранения 1–2 года.
Отверждающим продуктом к связующим использовался фильтрационный осадок – отход свеклосахарного производства. Осадок содержит гашеную известь и карбонат кальция – 75–85% и 19–25% органического вещества, состоящего из кальциевых солей щавелевой, лимонной, яблочной кислот, сахарозы, пектиновых веществ. Количество фильтрационного осадка составляет 9–11% массы перерабатываемой сахарной свеклы. Он накапливается в отвалах, занимает значительные земельные площади, загрязняет окружающую среду. Утилизация фильтрационного осадка важна для повышения эффективности свеклосахарного производства и улучшения состояния окружающей среды.
Подготовка угольного компонента заключается в дроблении и измельчении крупных фракций и шихтовании антрацитовых штыбов с угольными шламами. В процессе дробления и измельчения у угольных частиц появляются трещины, шероховатости и неровности. На твердой поверхности возрастает число активных центров, усиливается адсорбционная активность угольного компонента по отношению к связующему. Кроме того, на шероховатой поверхности дополнительно происходит механическое закрепление связующего.
Главным критерием оценки брикетируемости углеотходов и качества получаемого продукта являлась прочность брикетов на сбрасывание и сжатие. Брикеты изготавливали на гидравлическом прессе в цилиндрической матрице с линзообразной формой верхних и нижних рабочих поверхностей пуансонов. Испытание брикетов на прочность на сжатие проводилось на образцах-цилиндрах высотой и диаметром 50 мм.
Максимальная прочность топливного композита достигается лишь при оптимальном сочетании условий для проявления физико-химических процессов упрочнения. Структурно-механические свойства топливного брикета начинают формироваться на всех стадиях брикетирования – при подготовке сырья в процессе перемешивания, уплотнения шихты при приложении усилия прессования и закрепляются при упрочнении. Выбор оптимальных параметров брикетирования будет способствовать активизации проявления всех видов связи, структурообразованию и максимальному упрочнению брикетов. Одним из важных условий формирования плотной и прочной структуры брикета является увеличение площади контакта частиц композита. Это достигается при оптимальном гранулометрическом составе, когда обеспечивается наиболее плотная упаковка частиц и достигается наибольшая прочность контактов. Антрацитовые штыбы и угольные шламы представляют собой сложные дисперсные системы, состоящие из мелко- и крупнодисперсных частиц органической массы угля, минеральной составляющей и воды, находящейся в свободном и связанном состояниях. Тонкодисперсные угольные шламы можно рассматривать как составную часть связующего вещества. Использование угольных шламов приводит к улучшению технологических свойств шихты и повышению плотности упаковки частиц в брикетной композиции. Крупность антрацитового штыба 0–6 мм, угольного шлама – 0–3 мм. Зерновой состав антрацитового штыба: содержание частиц (%) > 6 мм: 3–5; 3–6 мм: – 28–36; 1–3 мм – 28–33; 0–1 мм –35–40. В зерновом составе угольного шлама преобладают частицы размером до 1.0 мм. На рис. 1 кривая 1 отражает планируемый гранулометрический состав угольного компонента, кривая 2 – фактически полученный при шихтовании зернового состава антрацитового штыба угольным шламом.
Модель шихты может быть представлена как многокомпонентная композиция, состоящая из твердых частиц различной крупности, сформированных в единый конгломерат под действием адсорбционных, физико-химических и химических связей. В полидисперсной системе в большей степени проявляются физические и химические силы взаимодействия частиц. Такие системы характеризуются избытком поверхностной энергии, что обуславливает сближение частиц, т.е. переход системы в устойчивое термодинамическое состояние. Наличие частиц различного размера в составе угольного компонента влияет на плотность упаковки композиции. Формирование структуры топливного композита происходит по принципу оптимальных смесей и дисперсного армирования. Зерна самой крупной фракции образуют скелет композиции, пустоты которого заполняет следующая фракция, включая угольный шлам. Последний облегчает перемещение зерен и их контактирование. Лещадные и игольчатые зерна дробленого антрацитового штыба в определенном смысле являются элементами короткой арматуры, влияют на прочность сцепления между частицами, способствуя их взаимному физическому переплетению, создавая эффект дисперсного армирования. При уплотнении структуры путем приложения удельного давления прессования увеличивается контактная поверхность между зернами композиции. Связующее выжимается на поверхность контактирующих частиц (эффект обмазки), цементируя их. Таким образом, формируется физическая структура шихты (матрица).
Управление структурообразованием в топливной композиции можно осуществить путем регулирования влажностного режима формовочной смеси, которое существенным образом оказывает влияние на баланс внутренних сил в процессе формирования структуры сырца брикетной композиции, изготавливаемых методом прессования. От исходной влажности углеотходов, предназначенных для брикетирования, значительно зависит как прочность брикета-сырца, так и конечные технические характеристики топливной композиции. Изменение содержания влаги в углеотходах влияет на силы сцепления между частицами [4]. Наличие водной пленки позволяет связывать частицы на расстояниях больших, чем ван-дер-ваальсов радиус взаимодействия двух частиц в отсутствие жидкой фазы, и благоприятствует подвижности частиц относительно друг друга при наложении удельного давления прессования. Повышенное содержание влаги в угле сопровождается утолщением водных пленок, сопровождающееся отдалением друг от друга твердых частиц и снижением действия молекулярных сил. Из отечественного и зарубежного опыта следует, что оптимальным содержанием влаги угля мелких классов, предназначенного для брикетирования, считается 2–3% [5]. При такой влажности штыба возможно получение прочного брикета-сырца при минимальном расходе связующего. Удовлетворительные результаты также могут быть получены при исходной влажности штыба 5–6% [6]. На прочностные свойства брикета-сырца оказывает влияние влагосодержание шихты. При недостатке влаги не обеспечивается сплошная гидратная пленка на поверхности частиц, влияющая на адгезионную прочность связующего с угольным компонентом. Нет условий для максимального проявления сил сцепления. При избытке влаги увеличивается толщина гидратной пленки, препятствующая адсорбционному контакту частиц, смачивающая способность связующего уменьшается и прочность брикетной композиции снижается. На рис. 2 показано влияние влажности шихты для брикетирования с разными связующими на прочность топливных брикетов. Наибольшие значения прочности отмечаются в диапазоне влажности 4–8%. Из полученных экспериментальных данных следует, что рабочая влажность шихты, при которой достигается достаточная для брикета-сырца прочность, может составлять 6–11%. С увеличением влажности шихты (свыше 11%) прочность брикетов заметно падает, причем в наибольшей степени для брикетов со связующим гидролом.
Рис. 2.
Влияние влажности шихты на прочность топливных брикетов: 1 – связующее меласса + фильтрационный осадок; 2 – связующее гидрол + фильтрационный осадок.
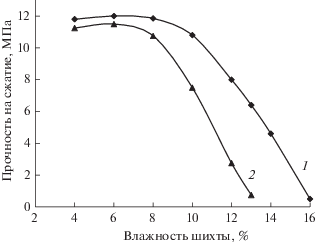
На брикетируемость антрацитовых штыбов и угольной мелочи и на технические свойства брикетов оказывают существенное влияние качество и количество связующего вещества. Результаты исследования зависимости прочности брикетов от содержания связующих веществ представлены на рис. 3, из которого следует, что характер кривых для обоих связующих идентичен. Увеличение содержания связующего сопровождается ростом прочности брикетов, изготовленных при одинаковых технологических режимах. Установлено, что при расходе мелассы и гидрола в диапазоне от 4 до 10% отформованные брикеты имеют прочность, достаточную для того, чтобы брикет не разрушился при транспортировке к месту упрочнения и складирования. По абсолютной величине для мелассы отмечены большие показатели прочности топливных брикетов: 19. 0 и 18.2 МПа соответственно.
Рис. 3.
Зависимость прочности топливных брикетов от содержания связующего: 1 – связующее гидрол + + фильтрационный осадок; 2 – связующее меласса + + фильтрационный осадок.
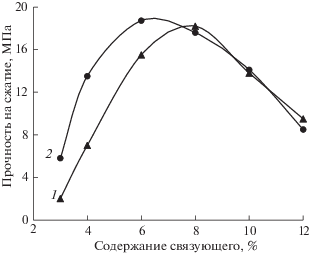
Увеличение количества и площади контактов между частицами и интенсивность их сцепления усиливаются при приложении усилия прессования. В местах контакта частиц при приложении усилия прессования начинают действовать физические силы аутогезии и химические связи. Дополнительный прирост прочности достигается за счет сил поверхностного натяжения. Влияние удельного давления прессования на прочность топливных брикетов проиллюстрировано на рис. 4. Удельное давление прессования варьировалось в пределах 5–45 МПа при оптимальной влажности шихты. С ростом усилия прессования прочность брикетов сначала растет, затем постепенно снижается. При приложении усилия прессования увеличивается контактная поверхность частиц. Одновременно происходит выжимание связующего на контактную поверхность. Оба эти фактора обуславливают возрастание сцепления между частицами и рост прочности брикетов. Максимум прочности приходится на диапазон удельного давления 25–35 МПа в зависимости от вида связующего. В этом диапазоне удельного давления прессования прочность топливных брикетов на связующем гидроле превышает прочность брикетов со связующим мелассой на 6.9–19.7%. Увеличение усилия прессования влечет за собой частичное разрушение наиболее крупных частиц угольного компонента, появление мелких частиц и трещин, не заполненных связующим. Прессование при повышенном давлении сопровождается выжиманием части связующего к стенкам пресс-формы и ослаблением сцепления между частицами. Кроме того, из-за интенсивного упругого расширения, имеющего место при высоком усилии прессования, возникают трещины на образцах при выталкивании их из пресс-формы. Все эти факторы отрицательно сказываются на прочности брикетов.
Рис. 4.
Влияние удельного давления прессования на прочность топливных брикетов: 1 – связующее гидрол + + фильтрационный осадок; 2 – связующее меласса + + фильтрационный осадок.

Проведено испытание технических свойств экспериментальных брикетов и опытной партии топливных брикетов, изготовленных на вальцовом прессе, по техническим условиям и гостовским методам оценки качества углей и топливных брикетов [7]. Результаты испытаний топливных брикетов, используемых как топливо на внутреннем рынке, в качестве альтернативы рядовому углю, приведены в табл. 2. В табл. 3 приведены сравнительные результаты сжигания экспериментальных партий топливных брикетов с разными связующими, изготовленных на вальцовом прессе.
Таблица 2.
Показатели качества топливных брикетов
Наименование показателя | Значение показателя | |
---|---|---|
cвязующее | ||
меласса | гидрол | |
Массовая доля общей влаги в рабочем состоянии топлива ($W_{t}^{r}$), % | 4.3–4.8 | 3.9–5.2 |
Зольность (Аd), % | 9.0 –19.7 | 7.8–16.4 |
Выход летучих веществ (V daf), % | 4.4–7.0 | 4.1–6.3 |
Механическая прочность при испытании сбрасыванием, % | 98.3–100.0 | 98.7–100 |
Массовая доля общей серы (${\text{S}}_{t}^{d}$), % | 0.82–1.07 | 0.64–0.98 |
Низшая теплота сгорания рабочего топлива ($Q_{i}^{r}$), МДж/кг | 24.84–28.67 | 23.94–26.12 |
Высшая теплота сгорания рабочего топлива ($Q_{i}^{r}$), МДж/кг | 30.80–34.98 | 29.45–34.86 |
Массовая доля хлора (Cld), % | 0.029 | 0.018 |
Массовая доля мышьяка (Asd), % | 0.0014–0.0017 | 0.0009–0.0011 |
Таблица 3.
Результаты сжигания топливных брикетов опытных партий
Вес пробы, кг | $A_{t}^{d}$, % | $W_{t}^{r}$, % | ${\text{S}}_{t}^{d}$, % | V daf, % | Количество несгоревшего топлива | Время горения брикетов, мин | |
---|---|---|---|---|---|---|---|
кг | % | ||||||
Связующее: меласса + фильтрационный осадок | |||||||
7.7 | 16.8 | 4.1 | 1.13 | 6.8 | 1.25 | 16.2 | 390 |
Связующее: гидрол + фильтрационный осадок | |||||||
7.8 | 14.7 | 4.7 | 1.10 | 5.5 | 1.17 | 15.0 | 410 |
Горение брикетов хорошее, без разрушения. Линзообразная с двух сторон форма брикетов способствует циркуляции воздуха в слое топливных брикетов. В начале горения ощущался легкий запах дыма и жженого сахара. При подсыпке нет пыли. При горении брикеты сохраняют форму и выдерживают механическую нагрузку, коржи не образуются. Принципиальных различий в горении брикетов с различным составом связующего не отмечено. Термоустойчивость брикетов при горении характеризуется как “очень хорошая”. Количество несгоревшего топлива не превышает 17.0%.
ОБСУЖДЕНИЕ РЕЗУЛЬТАТОВ
Прочностные свойства топливного дисперсно-зернистого композита во многом определяются структурой контакта между углеродистым материалом и связующим. По результатам исследований [8] антрациты инертны, так как их структурная основа состоит из ароматических соединений высокой степени конденсированности. Взаимодействие антрацитов со связующими осуществляется путем прочных ван-дер-ваальсовых связей. Изменение поверхности угольных частиц влияет на характер взаимодействия со связующим. По данным [9, 10] для улучшения адсорбционных свойств неактивной поверхности проводится ее модифицирование, способствующее гидрофилизации поверхности. Для этого используются поверхностно-активные вещества (ПАВ). Растворы, подобные мелассе, гидролу, проявляют свойства анионактивного ПАВ [11]. Адсорбция этих веществ на активных центрах малополярной [12] поверхности угля изменяет ее свойства, способствуя гидрофилизации поверхности. Под влиянием процессов, протекающих на границе контакта связующего с поверхностью адсорбента, происходит формирование структурирующих слоев вокруг зернистого углесодержащего компонента, определяющих прочностные и другие технические характеристики топливных брикетов. Вводимые кальцийсодержащие добавки в виде фильтрационного осадка интенсифицируют процесс упрочнения, блокируют сахара и образуют с мелассой и гидролом комплексы по донорно-акцепторному типу [13], способствующие уплотнению и упрочнению структуры, созданию наиболее прочных связей конденсационно-кристаллизационного и кристаллизационного типа [14], устойчивых к колебаниям влажностного и температурного режима окружающей среды. Наличие глюкозы в составе гидрола облегчает протекание реакции с осаждающим реагентом двухзарядного катиона кальция.
Из полученных результатов следует, что связующие меласса и гидрол могут быть использованы в равной степени для брикетирования угольной мелочи. С гидролом, имеющим меньшую вязкость в сравнении с мелассой, легче получить однородную смесь для брикетирования. Выбор того или иного связующего будет определяться его доступностью и стоимостью для конкретного производителя брикетов.
ЗАКЛЮЧЕНИЕ
Технология брикетирования со связующими веществами позволяет получить качественный топливный продукт, транспортабельный и удобный к употреблению в коммунально-бытовом секторе и промышленных тепловых установках, использовать и одновременно утилизировать мелкодисперсное угольное сырье, применение которого технологически затруднено и малоэффективно. С экономической точки зрения привлекательно создавать брикетное производство при обогатительных фабриках или шахте, где имеются соответствующие инженерные сооружения и коммуникации и сосредоточены многотоннажные скопления угольной мелочи и шламов, имеющих достаточный энергетический потенциал.
Используя угольные отходы, можно значительно экономить энергетические и сырьевые ресурсы, повышать комплексность использования добытых углей, снижать загрязнение окружающей среды. Помимо внутреннего потребления, возможен экспорт брикетов с высокими потребительскими свойствами за рубеж.
Список литературы
Александрова Т.Н., Рассказова А.В. // Зап. Горного ин-та. 2016. Т. 220. С. 573.
Солодов В.С., Папин А.В., Косинцев В.И., Оссовская Н.С. // Вестн. Кузбасск. гос. техн. ун-та. 2013. № 3 (97). С. 110.
Петрова Л.А., Латышев В.Г. // Нефтегазовое дело. 2007. № 1. С. 49.
Воларович М.П., Гамаюнов Н.И., Цеплаков О.А. Сб. “Физико-химическая механика дисперсных структур”. М.: Наука, 1966. С. 265.
Елишевич А.Т. Брикетирование полезных ископаемых. Одесса: Лидыбь, 1990. 296 с.
Буравчук Н.И., Гурьянова О.В. // ХТТ. 2014. № 4. С. 49. [Solid Fuel Chemistry, 2014. V. 48. № 4. P. 260. https://doi.org/10.3103/S036152191404003X].https://doi.org/10.7868/S0023117714040033
Тайц Е.М., Андреева И.А. Методы анализа и испытания углей. М.: Недра, 1983. 301 с.
Елишевич А.Т., Рыбаченко В.И., Перекрестов Б.И. // ХТТ. 1974. № 4. С. 94.
Колбановская А.С. // Докл. АН СССР. 1962. Т. 143. № 5. С. 1159.
Суринова С.И., Полушкин А.Н. // ХТТ. 1987. № 4. С. 123.
Воробьев В.Н., Лещенко П.С. Климова Л.К. // ХТТ. 1997. № 2. С. 81.
Петрова Г.И., Москаленко Т.В., Леонов А.М., Бы-чев М.И. // ГИАБ (научн.-техн. журн.). 2010. № 7. С. 366.
Бобровник Л.Д., Логвин В.М., Выговский В.Ю. // Сахар. 2009. № 10. С. 56.
Ребиндер П.А. Поверхностные явления в дисперсных системах. Физико-химическая механика. Избр. тр. М.: Наука, 1979. 384 с.
Дополнительные материалы отсутствуют.
Инструменты
Химия твердого топлива