Химия твердого топлива, 2021, № 3, стр. 24-28
НОВЫЙ СПОСОБ ПОЛУЧЕНИЯ ТОПЛИВНЫХ БРИКЕТОВ ИЗ УГЛЕРОДСОДЕРЖАЩИХ ОТХОДОВ
М. С. Фуфаева 1, *, Л. К. Алтунина 1, **, В. Н. Манжай 1, ***, А. С. Буяков 2, ****
1 Институт химии нефти СО РАН
634055 Томск, Россия
2 Институт физики прочности и материаловедения СО РАН
634055 Томск, Россия
* E-mail: maria81@ipc.tsc.ru
** E-mail: alk@ipc.tsc.ru
*** E-mail: mang@ipc.tsc.ru
**** E-mail: alesbuyakov@gmail.com
Поступила в редакцию 11.12.2020
После доработки 11.12.2020
Принята к публикации 03.02.2021
Аннотация
Разработан новый способ получения топливных брикетов под давлением из углеродсодержащих мелкодисперсных отходов и водного раствора поливинилового спирта. Установлено, что проведение цикла замораживания–размораживания способствует формированию топливных брикетов с минимальным количеством полимерного связующего. Получены образцы полноценного топлива с высокими физико-механическими и энергетическими характеристиками для его использования в бытовых и производственных условиях.
Экологическая обстановка в угледобывающих регионах России осложняется наличием мелкодисперсных некондиционных отходов при добыче и переработке угля. На угледобывающих предприятиях накапливается угольная мелочь, энергетический потенциал которой сложно использовать. Разработка новых способов получения углеродсодержащих материалов и использования их в качестве полноценного топлива в бытовых и производственных целях может решить проблему утилизации отходов.
Цель работы – получение прочных топливных брикетов на основе углеродсодержащих отходов.
Брикетирование мелкодисперсных частиц угля с целью получения топливных брикетов осуществляют при помощи различных связующих, например [1–3], используя мелассу – побочный продукт сахарно-свекловичного производства, а также другие растительные остатки. В работах [4, 5] описано использование лигносульфоната в качестве связующего, но он повышает в брикетах содержание серы, что недопустимо для большинства промышленных и бытовых потребителей.
Известно также применение поливинилового спирта (ПВС) для формирования прочных образцов из мелкодисперсных углеродных материалов [6]. Водные растворы поливинилового спирта обладают хорошими клеящими свойствами [7]. Адгезия макромолекул ПВС увеличивается по мере снижения его степени гидролиза, следовательно, при склеивании рекомендуется применять полимер со значительным содержанием остаточных ацетатных групп и с повышенной вязкостью [8].
В исследованиях использовали образец ПВС со степенью гидролиза 88% и молекулярной массой ~ 25 000. Мелкодисперсные частицы угля с размерами менее 1 мм пропитывали 20%-ным водным раствором поливинилового спирта. Полученную композицию прессовали под давлением 200 кПа и удаляли из образцов излишки полимерного раствора. Затем брикеты сушили при температуре 50°С до постоянной массы (полного испарения воды). Измеряли предел прочности топливных брикетов при осевом сжатии на универсальной испытательной машине Devotrans GP при постоянной скорости движения сжимающей пластины 0.1 мм/с. Погрешность определения максимальной нагрузки, выдерживаемой материалом, составляет 1%. Полученные результаты представлены в табл. 1.
Таблица 1.
Составы и свойства топливных брикетов
Состав высушенных брикетов, мас. % | Предел прочности на сжатие R, МПа | |
---|---|---|
ПВС | 1.3 | 4.5 |
Уголь | 98.7 | |
ПВС | 2.2 | 5.0 |
Уголь | 97.8 | |
ПВС | 2.6 | 5.0 |
Уголь | 97.4 |
Таблица 2.
Изменение механической прочности при сжатии брикетов, полученных из угля и водного раствора ПВС при разных условиях
№ | Содержание, мас. % | Характеристика процесса | Теплота сгора- ния, МДж/кг | |||
---|---|---|---|---|---|---|
Уголь | ПВС | температура, °С | механическая прочность, МПа, при давлении брикетирования, МПа | |||
100 | 150 | |||||
1 | 99.5 | 0.5 | +20 | 4.5 | 6.5 | 29,0 |
2 | 99.5 | 0.5 | –20 | 5.8 | 7.5 | 29.0 |
3 | 99.0 | 1.0 | +20 | 6.0 | 9.5 | 29.0 |
4 | 99.0 | 1.0 | –20 | 8.5 | 12.0 | 29.0 |
Из табл. 1 следует, что полученные брикеты достаточно прочные [3]. Влагостойкость полученных брикетов исследовали при комнатной температуре. Образец помещали в дистиллированную воду (рис. 1) и перемешивали на магнитной мешалке при скорости вращения якоря 60 об/мин.
Рис. 1.
Топливный брикет, сформированный под давлением из угля: высушенный брикет (а); брикет погружен в воду (б); брикет разрушился (в).
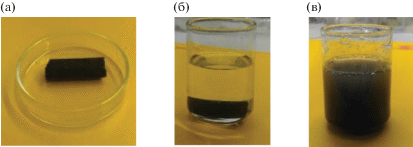
Установили, что брикеты не влагостойкие и при контакте с водой разрушаются (рис. 1). При содержании в цепи ПВС более 10% ацетатных групп полимер растворяется в воде при температуре 30–50°С [8], поэтому в качестве связующего вещества для брикетов не подходит.
Известно, что водные растворы ПВС после замораживания при отрицательной температуре (ниже 0°С) и последующего оттаивания при положительной температуре образуют упругие полимерные тела, так называемые криогели [9]. Температура плавления сформированных криогелей превышает 70°С, т.е. существенно выше температуры плавления льда. Следует отметить, что механические свойства упругих криогелей принципиально отличаются от свойств исходных вязкотекучих композиций, что позволяет использовать криогели в качестве связующего материала [10]. Особенностью ПВС, используемого для получения криогелей, является минимальное количество в полимере остаточных ацетатных групп (не более 2%). В образующихся криогелях связи между полимерными цепями имеют нековалентную природу. Межмолекулярные контакты в зонах микрокристалличности обеспечиваются множественными водородными связями между вторичными спиртовыми группами различных цепей. У недостаточно дезацетилированных образцов ПВС объемные ацетатные группы создают стерические препятствия, которые мешают образованию комплементарных контактов [11]. Криогели – нетоксичный и экологически чистый материал, широко применяются в биотехнологиях, медицине и пищевой промышленности [12–14]. При сгорании ПВС образуются углекислый газ и вода.
Опытным путем установили, что образовывать криогели способны водные растворы ПВС при концентрации не ниже 5% [15]. Для получения наполненных криогелей в водный раствор ПВС вносили мелкодисперсные частицы кокса в количестве от 30 до 80 мас. %, размер которых не более 1 мм, и проводили цикл замораживания–размораживания, а затем на установке, функционирующей на основе реологической модели Максвелла [16], определяли модуль упругости (рис. 2).
Рис. 2.
Зависимость модуля упругости (G, кПа) криогеля на основе водного раствора поливинилового спирта (СПВС = 5 мас. %) от содержания кокса (Cк, мас. %).
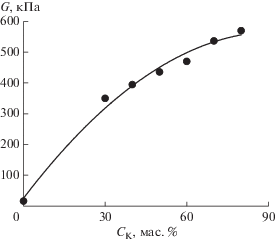
Из рис. 2 видно, что увеличение содержания твердых частиц кокса приводит к значительному росту модуля упругости наполненных криогелей, которая обусловлена главным образом наличием механического каркаса, построенного из частичек кокса. Экспериментально также установлен температурный предел (Тпл), до которого криогели, наполненные коксом, сохраняют свою структуру Тпл ~ 70°С [17]. Криогели, наполненные коксом, сушили при комнатной температуре до полного испарения воды. В результате получали жесткие брикеты с пределом прочности 2.8 МПа и теплотворной способностью 28.5 МДж/кг. Влагостойкость полученных брикетов исследовали по методике, описанной выше.
Из рис. 3 следует, что при контакте с водой топливные брикеты, сформированные с помощью криогелей, не разрушаются и сохраняют свою первоначальную форму.
Рис. 3.
Топливный брикет, сформированный из кокса и раствора ПВС после цикла замораживания–размораживания: высушенный брикет (а); брикет погружен в воду (б); сгорание сухого брикета (в).
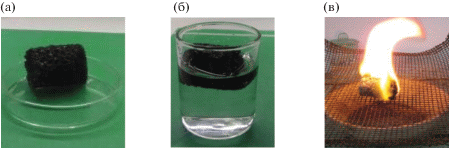
Предложенный способ формирования брикетов через стадию криогелеобразования предполагает высокий расход связующего, что не экономично, поэтому для снижения расходов связующего (ПВС) более оптимальной технологией является формирование брикетов под давлением с последующим циклом замораживания–оттаивания.
Мелкодисперсные частицы угля, размер которых не более 5 мм, пропитывали водными растворами ПВС с концентрацией 5 и 10%. В ячейках под давлением 100 и 150 МПа формировали брикеты с площадью торцевой поверхности 8.5 · 10–5 м2. Часть образцов замораживали при температуре –20°С и размораживали при комнатной температуре 20°С. Затем сушили брикеты при температуре 50°С до полного испарения воды, убыль которой контролировали гравиметрическим методом. Определяли предел прочности топливных брикетов, сформированных в виде цилиндрических образцов, при осевом сжатии с помощью универсальной испытательной машины Devotrans GP, при постоянной скорости движения сжимающей пластины 0.1 мм/с.
На рис. 4 и 5 представлены кривые нагружения высушенных образцов в координатах деформация–напряжение.
Рис. 4.
Зависимость напряжения (σ, МПа) от деформации (ε, %) топливных брикетов, сформированных под давлением 100 МПа, при условиях: 1 – уголь 99.5%, ПВС 0.5% при Т = +20°С; 2 – уголь 99.5%, ПВС 0.5% при Т = –20°С; 3 – уголь 99.0%, ПВС 1.0% при Т = +20°С; 4 – уголь 99.0%, ПВС 1.0% при Т = = –20°С.
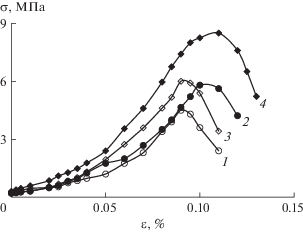
Рис. 5.
Зависимость напряжения (σ, МПа) от деформации (ε, %) топливных брикетов, сформированных под давлением 150 МПа, при условиях: 1 – уголь 99.5%, ПВС 0.5% при Т = +20°С; 2 – уголь 99.5%, ПВС 0.5% при Т = –20°С; 3 – уголь 99.0%, ПВС 1.0% при Т = +20°С; 4 – уголь 99.0%, ПВС 1.0% при Т = = –20°С.
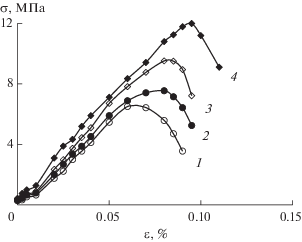
Из рис. 4 и 5 видно, что с увеличением концентрации ПВС в использованных растворах связующего прочность брикетов увеличивается, т.е. чем больше в образце структурообразующего компонента (поливинилового спирта), тем лучше смачиваются углеродные частички, следовательно, адгезионные свойства выражены сильнее. У брикетов, полученных после проведения цикла замораживания–размораживания, прочность выше (кривые 2 и 4), чем без криогенной обработки (кривые 1 и 3). Также установлено, что при увеличении давления пресса в процессе формирования прочность брикетов увеличивается.
Теплоту сгорания топливных брикетов исследовали на термоанализаторе STA 449C Jupiter фирмы NETZSCH (Германия). В табл. 1 приведены состав и свойства полученных брикетов.
Из табл. 1 следует, что концентрация ПВС и условия формирования брикетов не влияют на теплотворную способность получаемых брикетов.
При исследовании брикетов, полученных при использовании в качестве связующего компонента ПВС и содержащих в полимерных цепях менее 2% остаточных ацетатных групп, установлена их высокая влагостойкость. Из рис. 6 видно, что образцы, помещенные в воду, сохранили первоначальную форму.
Таким образом, разработанный способ позволяет формировать прочные брикеты из мелкодисперсных углеродсодержащих отходов с минимальным количеством связующего компонента и получать высокоэнергетическое топливо для бытовых и производственных целей.
Список литературы
Буравчук Н.И., Гурьянова О.В. Состав для получения топливного брикета. Пат. 2629365 РФ // Опубл. 29.08.2017. Бюл. № 25. С. 8.
Буравчук Н.И., Гурьянова О.В. // ХТТ. 2016. № 6. С. 19. [Solid Fuel Chemistry, 2016. V. 50. № 6. P. 352. https://doi.org/10.3103/S0361521916060021]https://doi.org/10.7868/S0023117716060025
Елишевич А.Т. Брикетирование угля со связующим. М.: Недра, 1972. 180 с.
Попов С.Н., Буренина О.Н., Николаева Л.А., Соловьев Т.М. // ХТТ. 2018. № 4. С. 69. [Solid Fuel Chemistry, 2018. V. 52. № 4. P. 275. https://doi.org/10.3103/S0361521918040092]https://doi.org/10.1134/S0023117718040096
Головичев А.И., Никишанин М.С., Мегера В.С., Жарков С.В. Способ получения топливных брикетов. Пат. 2298028 РФ // Опубл. 27.04.2007. Бюл. № 12. С. 7.
Станкевич С.И., Дружинина Т.В., Харченко И.М., Кряжев Ю.Г. // ХТТ. 2007. № 1. С. 51. [Solid Fuel Chemistry, 2007. V. 41. № 1. P. 45. https://doi.org/10.3103/S0361521907010107]
Николаев А.Ф., Орхименко Г.И. Водорастворимые полимеры. Л.: Химия, 1979. 144 с.
Ушаков С.Н. Поливиниловый спирт и его производные. М.: АН СССР, 1960. Т. 2. 868 с.
Lozinsky V.I. // Advances in Polymer Science. 2014. V. 263. P. 48. https://doi.org/10.1007/978-3-319-05846-7_1
Алтунина Л.К., Манжай В.Н., Фуфаева М.С., Егорова Л.А. Топливный брикет и способ его формирования. Пат. 2467058 РФ // Опубл. 20.11.2012. Бюл. № 32. С. 6.
Лозинский В.И. // Успехи химии. 1998. Т. 67. № 7. С. 641. [Russian Chemical Reviews, 1998. V. 67. № 7. P. 651. https://doi.org/10.1070/RC1998v067n07ABEH000399].
Suzuki A., Sasaki S. // Journal of Engineering in Medicine. 2015. V. 229. №. 12. P. 828.
Van Rie J., Declercq H., Van Hoorick J., Dierick M., Van Hoorebeke L., Cornelissen R., Thienpont H., Dubruel P., Van Vlierberghe S. // Journal of Materials Science: Materials in Medicine. 2015. V. 26. № 3. P. 7. https://doi.org/10.26577/2218-7979-2015-8-1-52-60
Mattiasson B. // Advances in Polymer Science. 2014. V. 263. P. 245.
Алтунина Л.К., Манжай В.Н., Фуфаева М.С. // ЖПХ. 2006. Т. 79. № 10. С. 1689. [Russian Journal of Applied Chemistry, 2006. V. 79. № 10. P. 1669. https://doi.org/10.3103/S0361521913010060]
Фуфаева М.С., Кашлач Е.С., Манжай В.Н., Алтунина Л.К. // Химия в интересах устойчивого развития. 2020. Т. 28. № 3. С. 315. https://doi.org/10.15372/KhUR2020235
Манжай В.Н., Фуфаева М.С., Егорова Л.А. // ХТТ. 2013. № 1. С. 44. [Solid Fuel Chemistry, 2013. V. 43. № 1. P. 43. https://doi.org/10.3103/S0361521913010060]https://doi.org/10.7868/S0023117713010076
Дополнительные материалы отсутствуют.
Инструменты
Химия твердого топлива