Химия твердого топлива, 2021, № 6, стр. 28-40
СИНТЕЗ ГРАФЕНОСОДЕРЖАЩИХ НАНОМАТЕРИАЛОВ НА ОСНОВЕ КОКСА МЕТОДОМ ЭЛЕКТРОДУГОВОГО РАЗРЯДА
Б. Т. Ермагамбет 1, *, М. К. Казанкапова 1, **, Б. К. Касенов 1, ***, А. Ж. Айтмагамбетова 1, ****, Е. Е. Куанышбеков 1, *****
1 ТОО “Институт химии угля и технологии”
010000 Нур-Султан, Казахстан
* E-mail: bake.yer@mail.ru
** E-mail: maira_1986@mail.ru
*** E-mail: kasenov1946@mail.ru
**** E-mail: assemaitmagambetova04@gmail.com
***** E-mail: mr.ero1986@mail.ru
Поступила в редакцию 23.02.2021
После доработки 10.03.2021
Принята к публикации 21.07.2021
Аннотация
Проведен синтез графеносодержащих наноматериалов из угля месторождения “Шубарколь” марки “Д” (Казахстан). Графеносодержащие наноматериалы были получены методом электродугового разряда на основе кокса из угля месторождения “Шубарколь” при 1173 К в среде азота. Несколько слоистых хлопьев графена синтезированы с использованием дугового разряда при постоянном напряжении 75 В и силе тока 150, 300 А в кварцовом реакторе. Изучены физико-химические характеристики и морфология поверхности исследуемых образцов. Определены электросопротивление (R), электроемкость (C) и диэлектрическая проницаемость (ε) графеносодержащего материала в интервале температур 293–483 К.
В современном мире передовые научные и технологические исследования в области энергетики, а также окружающей среды сталкиваются с проблемами, связанными с производительностью, функциональностью и долговечностью основных материалов. Широко признано, что современные материалы, включая наноматериалы на основе углерода, такие как углеродные нанотрубки, нановолокна, графен, оксид графена, углеродные квантовые точки, привлекли внимание благодаря своим исключительным физическим, химическим, оптическим, механическим и термическим свойствам. Высокий спрос на рынке и высокая цена на разработку углеродных наноматериалов с помощью экологически чистых и недорогих ресурсов, а также конкурентное исследование привели к усилению финансирования со стороны правительственных органов и предпринимателей во всем мире.
На рынке стоимость 1 кг графена в зависимости от чистоты продукта составляет от 100 до 1000 долларов США. Высокая цена формируется из-за использования дорогостоящих углеводородов (ацетилен, ксилол, метан и т.д.) и графита, что приводит к высокой стоимости производства и, следовательно, ограничивает их коммерциализацию. Прекурсоры для синтеза углеродных наноматериалов играют особую роль в развитии технологий наноиндустрии. В этом аспекте уголь является недорогим альтернативным ресурсом для производства углеродных нанотрубок, нановолокна, графена, фуллерена, оксида графена и углеродных квантовых точек.
Графеносодержащие материалы с большой площадью поверхности, хорошими электрическими характеристиками, проводимостью и стабильностью можно использовать для быстрого накопления и высвобождения энергии. Благодаря превосходным свойствам графен и его производные широко применяются в различных областях, таких как высокопроизводительные суперконденсаторы, аккумуляторы, наноэлектроника, композиты и датчики [1–5]. С момента его открытия были предложены десятки потенциальных применений графена: от более быстрых компьютерных микросхем и гибких сенсорных экранов до сверхэффективных солнечных батарей и опреснительных мембран. Одно из свойств, представляющее интерес, – это способность накапливать электрический заряд. Огромная площадь поверхности графена может быть сжата внутри батареи, что позволяет создавать новые устройства хранения энергии, способные хранить огромное количество заряда [6–9]. Многие эксперты предсказывают в недалеком будущем возможную замену кремниевых транзисторов на более экономичные и быстродействующие – графеновые. Известно, что графен обладает прекрасными механическими свойствами. Этот материал прочный и жесткий, благодаря своей гибкости может равномерно покрыть практически любую поверхность. Многие исследователи и технологические лидеры рассматривают графен как полезный материал, который может значительно ускорить появление гибких устройств и дисплеев толщиной с бумагу [10–13].
Графен можно получить с помощью двух разных методов – “сверху вниз” и “снизу вверх”. К ним относятся микромеханическое расщепление, электрохимическое расслоение, расслоение соединений интеркаляции графита, расслоение на основе растворителя, расслоение оксида графита, лазерное испарение и дуговый разряд, эпитаксиальный рост на карбиде кремния, деградация SiC при высокой температуре, химическое осаждение из газовой фазы (CVD). Среди всех этих методов дуговый разряд имеет множество преимуществ, таких как: низкая стоимость производства, высокая эффективность и возможность синтеза без использования какого-либо катализатора [14–17].
Цель данной работы – синтез графеносодержащих наноматериалов методом электродугового разряда из углепродуктов и исследование физико-химических и электрофизических свойств полученных образцов.
В этом исследовании несколько слоев графена и графеносодержащего наноматериала были синтезированы из кокса, полученного на основе угля высокосмолистого каменного длиннопламенного угля месторождения “Шубарколь” марки “Д” с использованием лабораторной камеры дугового разряда, разработанной в ТОО “Институт химии угля и технологии” (г. Нур-Султан). Полученный кокс имеет следующие характеристики (%): W r – 0.60; Ad – 32.16; V daf – 5.35, удельное сопротивление – 3–10 Ом.
Метод электродугового разряда для получения графена и графеносодержащих материалов имеет много преимуществ, таких как низкая стоимость производства, высокая эффективность и возможность синтеза без использования какого-либо катализатора. Способ может быть легко использован в лаборатории, а также масштабирован до промышленного производства.
Суть метода заключается в термическом напылении электрода из кокса в плазме дугового разряда, горящего в атмосфере инертного газа. Синтезированный графен и графеносодержащие материалы образовывались и на внутренней поверхности реактора и на поверхности электрода. Схема установки синтеза графена приведена на рис. 1.
Для получения графена проводился процесс электродугового разряда кокса месторождения “Шубарколь” в инертной атмосфере азота, сила тока при постоянном напряжении 75 В составила 150 и 300 А. Исследование элементного состава, структуры и размерности графена проводили методом энергодисперсионной рентгеновской спектроскопии на приборе SEM (Quanta 3D 200i) с приставкой для энергодисперсионного анализа от EDAX.
Изучение типа модификации углерода проводили с помощью Рамановской спектроскопии с использованием метода комбинационного рассеивания света (КРС). КРС-спектры образцов записывали на зондовом сканирующем микроскопе Integra Spectra, с использованием лазера с длиной волны излучения 473 нм.
Определение электрофизических характеристик (диэлектрической проницаемости ε, электрического сопротивления R) проводились путем измерения электроемкости С образцов на серийном приборе LCR-800 (измеритель L, C, R) при рабочей частоте 1 кГц с базовой погрешностью 0.05–0.1% непрерывно, в сухом воздухе, в термостатном режиме со временем выдержки 3 мин при каждой фиксированной температуре.
Предварительно изготавливали плоскопараллельные образцы в виде дисков диаметром 10 мм и толщиной 5−6 мм со связующей добавкой (∼1.5%). Прессование проводили под давлением 20 кг/см2. Полученные диски обжигали в силитовой печи при 473 К в течение 6 ч. Далее проводили их тщательное двухстороннее шлифование.
Диэлектрическую проницаемость определяли из электроемкости образца и электроемкости конденсатора. Для получения зависимости между электрической индукцией D и напряженностью электрического поля Е использовали схему Сойера-Тауэра. Визуальное наблюдение D (Е-петли гистерезиса) проводили на осциллографе С1-83 с делителем напряжения, состоящим из сопротивлений 6 мОм и 700 кОм, и эталонным конденсатором 0.15 мкФ. Частота генератора 300 Гц. Во всех температурных исследованиях образцы помещали в печь, температуру измеряли хромель-алюмелевой термопарой, подключенной к вольтметру В2-34 с погрешностью ±0.1 мВ. Скорость изменения температуры ∼5 К/мин. Величину диэлектрической проницаемости при каждой температуре определяли по формуле ε = С/С0, где С0 – емкость конденсатора без исследуемого вещества (воздушного).
Результаты КРС- и СЭМ-изображения кокса месторождения “Шубарколь” представляют собой сигналы с характерными пиками D и G (1356 и 1598 см–1). Соотношение интенсивностей D и G пиков показывает количество дефектов рассматриваемого материала, ID/IG составляет 0.63, не наблюдается 2D-полоса, характеризующая образования графена и графеносодержащего материала (рис. 2). Степень графитизации (Gf) составляет 18.18%. СЭМ-изображения представлены на рис. 3.
В первом эксперименте электродуговой разряд проводился при силе тока 150 А, при постоянном напряжении 75 В. Реактор заполняли инертным газом (N2) в течение 2 мин. Время синтеза составило 2–10 мин.
Результаты анализа на сканирующем электронном микроскопе углеродного материала, образовавщегося в верхней части реактора, показали образование хлопьевидных углеродных частиц, возможно УНТ, с размерами частиц 64.2–69.9 нм (рис. 4). Рамановский спектр образца демонстрирует сигнал с характерными пиками D и G (1364, 1351 и 1582 см–1). Полоса D представляет собой неупорядоченную полосу, связанную со структурными дефектами и аморфным углеродом, в то время как полоса G соответствует связи в плоскости колебаний пар sp2-атомов углерода. Широкий пик D-полосы свидетельствует о том, что образец содержит относительно большое количество неупорядоченной структуры и дефектов. Кроме того, в Рамановском спектре образца 2D-пик, который говорит об образовании УНТ, наблюдается при 2713 см–1.
Рис. 4.
Результаты СЭМ-изображения наноматериала (верхняя часть) на основе кокса “Шубарколь” после электродуговой обработки (150 А, 75 В): (а) ×2000; (б) ×5000; (в) ×10 000; (г) ×50 000.
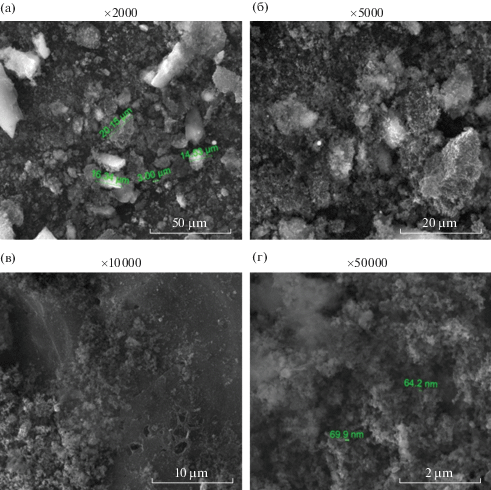
Соотношение интенсивностей ID/IG широко используется для оценки качества углеродных материалов. Соотношение интенсивностей I2D/IG составляет 0.23, что говорит о многослойности материала. По соотношению интенсивностей G и 2D пиков (IG/I2D = 4.3) можно также судить о многослойности УНТ. Соотношение интенсивностей D и G пиков (ID/IG = 0.38) утверждает о немалом количестве дефектов рассматриваемого материала. Степень графитизации составляет 25.4% (рис. 5, а) и 40.65% (рис. 5, б).
Рис. 5.
Результаты КРС наноматериала (верхняя часть) на основе кокса “Шубарколь” после электродуговой обработки (150 А, 75 В): (а) D – 1355 см–1, G – 1585 см–1, Gf – 25.40%; (б) D – 1366 см–1, G – 1584 см–1, 2D – 2716 см–1, Gf – 40.65%.
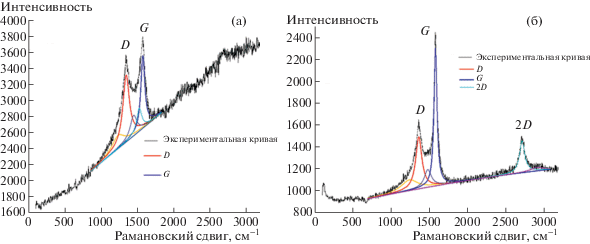
Из СЭМ-изображения (рис. 6) углеродного материала, полученного из нижней части реактора, можно увидеть сферические частицы с размером от 32 до 241.9 нм, а также хлопья графеносодержащих материалов. В Рамановских спектрах (рис. 7, а и б) наблюдаются два типичных пика при 1353 и 1361 см–1 и 1579 и 1581 см–1, соответствующих полосам D и G, соответственно.
Рис. 6.
Результаты СЭМ-изображения наноматериала (нижняя часть) на основе кокса “Шубарколь” после электродуговой обработки (150 А, 75 В): (а) ×2000; (б) ×5000; (в) ×10 000; (г) ×50 000.
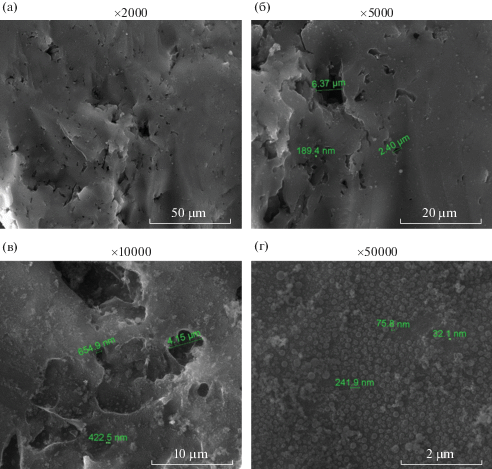
Рис. 7.
Результаты КРС наноматериала (нижняя часть) на основе кокса “Шубарколь” после электродуговой обработки (150 А, 75 В): (а) D – 1353 см–1, G – 1579 см–1, 2D – 2705 см–1, Gf – 54.40%; (б) D – 1361 см–1, G – 1581 см–1, 2D – 2720 см–1, Gf – 48.74%.
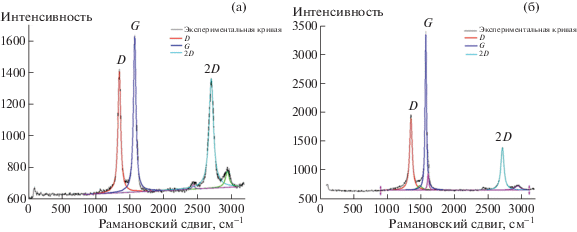
Известно, что 2D-полоса Рамановских спектров более чувствительна к наложению графеновых листов. Например, положение 2D-полосы однослойного графена составляет ∼2679 см–1, в то время как для многослойного графена (содержащего 2–4 слоя) положение 2D-полосы смещается в сторону больших волновых чисел вместе с расширением пика. Кроме того, соотношения интенсивностей I2D/IG для одно-, двух-, трех- и многослойного (>4) слоя графена обычно составляют > 1.6, ∼0.8, ∼0.30 и ∼0.07 соответственно. В данном образце 2D-полоса, расположенная в области ∼2705–2720 см–1, указывает на присутствие в образце малоослойного графена и графеносодержащих материалов. Соотношение интенсивностей I2D/IG составляет 0.702 и 0.27, что указывает на образование дву- и трехслойного графена. Соотношение интенсивностей G и 2D пиков говорит об образовании одно- и многослойного графена. В данном случае IG/I2D составляет 2.75 и 3.65, что подверждает образование двух- и трех- слойного графена (для однослойного графена соотношение составляет 0.6–1).
Относительное соотношение интенсивностей полосы D к полосе G (ID/IG) можно использовать для точной оценки качества современных углеродных материалов. По соотношению интенсивностей полос ID/IG, которое составляет 0.46 и 1.49, можно утверждать о немалом количестве дефектов материала. Степень графитизации образца составляет 39.17–48.7% (рис. 7), что намного выше углеродного материала, образовавшегося в верхней части реактора (рис. 5).
После электродугового разряда углеродный материал показал более высокую проводимость (0.7 Ом), чем исходный (3–10 Ом). Результаты КРС и СЭМ-изображения образца кокса “Шубарколь” после электродуговой обработки (150 А, 75 В) представляют собой сигналы УНТ и аморфного углерода с характерными пиками D и G (1349, 1366 см–1 и 1587, 1589 см–1). Соотношение интенсивностей IG/I2D составляет 3.49 и говорит о трехслойности структуры УНТ, а соотношение интенсивностей I2D/IG, составляющее 0.29 (рис. 8, а), еще раз это подтверждает. Сооотношение интенсивностей полос показывает количество дефектов материала (ID/IG – 1.46 и 0.855). Степень графитизации составляет 38.3 и 24.0% (рис. 8, а и б). Размер сферических частиц варьируется от 39.4 до 466.4 нм (рис. 9, г). Элементный состав кокса после электродуговой обработки составляет (%): C – 90.41; O – 8.17; Na – 0.19; Mg – 0.10; Al – 0.31; Si – 0.23; S – 0.29; Са – 0.17; Fe – 0.13.
Рис. 8.
Результаты КРС кокса “Шубарколь” после электродуговой обработки (150 А, 75 В): (а) D – 1349 см–1, G – 1587 см–1, 2D – 2686 см–1, Gf – 38.34%; (б) D – 1366 см–1, G – 1589 см–1, Gf – 24.0%.
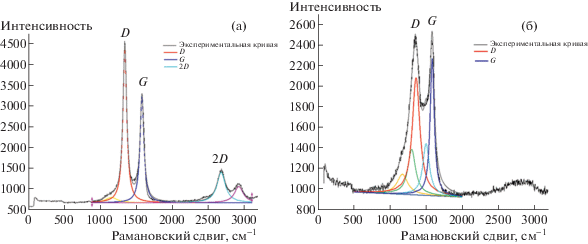
Рис. 9.
Результаты СЭМ-изображения кокса “Шубарколь” после электродуговой обработки (150 А, 75 В): (а) ×2000; (б) ×10 000; (в) ×30 000; (г) ×50 000.
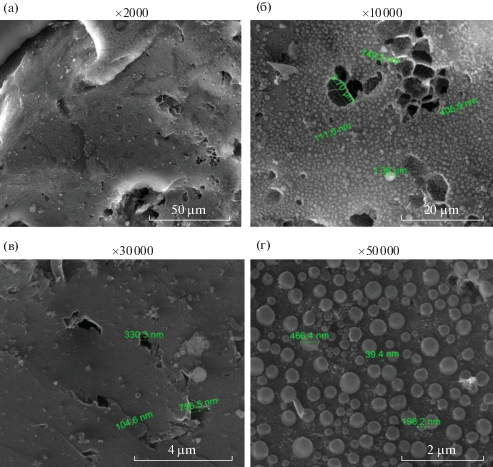
Сравнивая результаты исследований образца, можно предположить, что при силе тока 150 А электродугового разряда графен и графеносодержащие материалы образуются в нижней части реактора. В верхней части реактора, по данным результатов, образуются материалы, которые имеют КРС-спектры, близкие к углеродным нанотрубкам.
Для дальнейшего исследования проводился аналогичный эксперимент, только при силе тока 300 А. Результаты исследования на сканирующем электронном микроскопе образца, образовавшегося на стенках реактора, показали образование хлопьевидных частиц графена (рис. 10) Рамановский спектр образца демонстрирует сигнал малослойного графена с характерными пиками D и G (1353, 1355 см–1 и 1582, 1581 см–1), так же можно наблюдать образование 2D-пика при 2707 и 2724 см–1. Соотношение интенсивностей IG/I2D составляет 1.39 и 3.45, что говорит об образовании графена как с одно- так и многослойной структурой. Соотношение интенсивностей I2D/IG составляет 0.44 и 1.15 и говорит о том же (рис. 11, а и б).
Рис. 10.
Результаты СЭМ-изображения наноматериала на основе кокса “Шубарколь” после электродуговой обработки (300 А, 75 В): (а) ×2000; (б) ×5000; (в) ×10 000; (г) ×30 000.
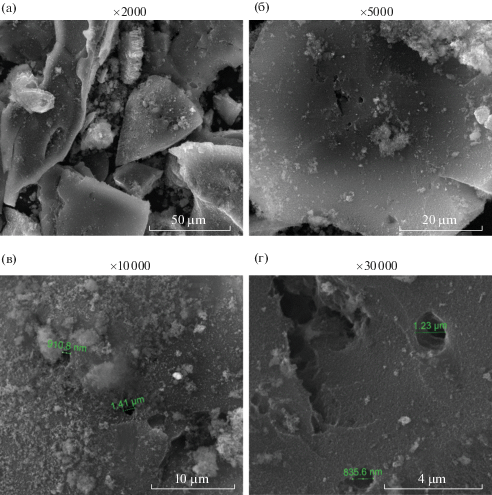
Рис. 11.
Результаты КРС образца на основе кокса “Шубарколь” после электродуговой обработки (300 А, 75 В): (а) D – 1353 см–1, G – 1582 см–1, 2D – 2707 см–1, Gf – 50.70%; (б) D – 1355 см–1, G – 1581 см–1, 2D – 2724 см–1, Gf – 42.84%.
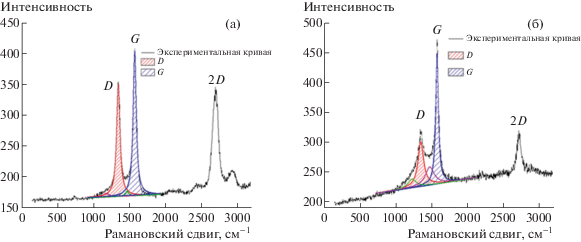
По сооотношению интенсивностей полос ID/IG – 0.34 и 0.78, можно делать выводы о небольшом количестве дефектов материала. Степень графитизации углеродного материала составляет 42.84–50.70%.
Также был приведен анализ электродного материала после электродугового разряда. Рамановский спектр образца показал наличие D- и G-пиков при 1357 и 1598 см–1 соответственно (рис. 12, а и б). После электродугового разряда электроды показывали более высокую проводимость (0.7 Ом) чем до (7–10 Ом). Результаты КРС- и СЭМ-изображения образца представляют собой сигнал графена и графеносодержащего материала с характерными пиками D и G (1346, 1361 см–1 и 1568, 1579 см–1) (рис. 12, а и б). Можно наблюдать ярко выраженный 2D-пик при 2691 и 2725 см–1, доказывающий образование графена и графеносодержащих материалов, о чем свидетельствуют СЭМ-снимки образца, которые представлены на рис. 13. Соотношение интенсивностей IG/I2D составляет 1.77 и 3.82 и говорит об образовании одно- и многослой структуры графена. Соотношение интенсивностей I2D/IG составляет 0.55 и 1.03, что указывает на образование от одного до трех слойного графена. По сооотношению интенсивностей полос ID/IG – 0.1 можно утверждать о малом количестве дефектов рассматриваемого образца. Степень графитизации образца составляет 54.56–85.20%.
Рис. 12.
Результаты КРС кокса “Шубарколь” (800°С) после электродуговой обработки (300 А, 75 В): (а) D – 1346 см–1, G – 1568 см–1, 2D – 2691 см–1, Gf – 54.56%; (б) D – 1361 см–1, G – 1579 см–1, 2D – 2725 см–1, Gf – 85.20%.
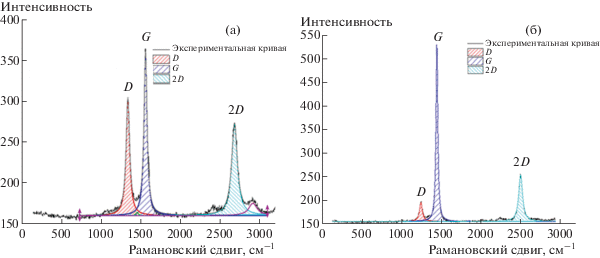
Рис. 13.
Результаты СЭМ – изображения кокса “Шубарколь” после электродуговой обработки (300 А, 75 В): (а) ×2000; (б) ×5000; (в) ×10 000; (г) ×50 000.
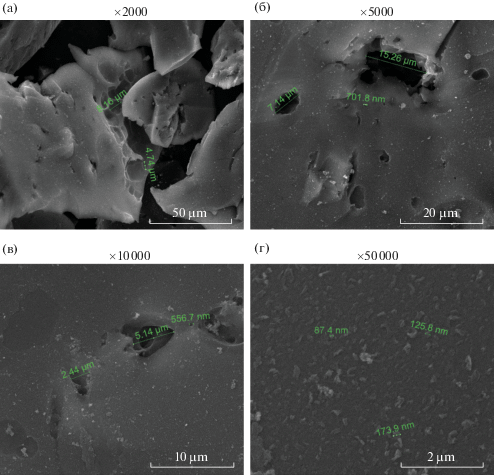
Сравнивая все результаты образца, можно предположить, что при высокой силе тока (300 А) электродугового разряда графен и графеносодержащие материалы образуются и на стенках реактора, и на самом электроде. Самая высокая степень графитизации Gf = 85.20% соответствует графеносодержащему материалу, который образовался на поверхности электрода при 300 А, в связи с чем электрод (кокс) после электродуговой обработки был изучен на электрофизические свойства.
В табл. 1 приведены результаты измерения электрофизических характеристик графеносодержащего материала, полученного при 300 А.
Таблица 1.
Зависимость электросопротивления (R), электроемкости (C) и диэлектрической проницаемости (ε) от температуры
Т, К | C, нФ | R, Oм | ε | lgε | lgR |
---|---|---|---|---|---|
Частота измерений 1 кГц | |||||
293 | 456.3 | 16 020 | 3 284 033 | 6.52 | 4.20 |
303 | 359.45 | 20 570 | 2 586 995 | 6.41 | 4.31 |
313 | 37.634 | 107 300 | 270 855 | 5.43 | 5.03 |
323 | 38.241 | 101 800 | 275 224 | 5.44 | 5.01 |
333 | 144.9 | 26 370 | 1 042 859 | 6.02 | 4.42 |
343 | 300.05 | 11 520 | 2 159 488 | 6.33 | 4.06 |
353 | 291.38 | 9728 | 2 097 089 | 6.32 | 3.99 |
363 | 309.27 | 7107 | 2 225 845 | 6.35 | 3.85 |
373 | 258.32 | 5917 | 1 859 153 | 6.27 | 3.77 |
383 | 227.25 | 4980 | 1 635 539 | 6.21 | 3.70 |
393 | 249.16 | 3936 | 1 793 228 | 6.25 | 3.60 |
403 | 318.07 | 3387 | 2 289 179 | 6.36 | 3.53 |
413 | 366.54 | 3480 | 2 638 022 | 6.42 | 3.54 |
423 | 636.53 | 3419 | 4 581 165 | 6.66 | 3.53 |
433 | 986.01 | 2972 | 7 096 405 | 6.85 | 3.47 |
443 | 1278.6 | 2515 | 9 202 202 | 6.96 | 3.40 |
453 | 1410.8 | 2040 | 10 153 658 | 7.01 | 3.31 |
463 | 1777.6 | 1511 | 12 793 551 | 7.11 | 3.18 |
473 | 2718.8 | 1091 | 19 567 455 | 7.29 | 3.04 |
483 | 6083.4 | 801.4 | 43 782 792 | 7.64 | 2.90 |
Частота измерений 5 кГц | |||||
293 | 24.14 | 16 320 | 173 738 | 5.24 | 4.21 |
303 | 17.695 | 21 590 | 127 353 | 5.11 | 4.33 |
313 | 1.1764 | 127 300 | 8467 | 3.93 | 5.10 |
323 | 1.963 | 106 600 | 14 128 | 4.15 | 5.03 |
333 | 12.684 | 18 860 | 91 288 | 4.96 | 4.28 |
343 | 30.898 | 10 810 | 222 376 | 5.35 | 4.03 |
353 | 34.305 | 9011 | 246 896 | 5.39 | 3.95 |
363 | 43.332 | 6439 | 311 864 | 5.49 | 3.81 |
373 | 40.128 | 5345 | 288 805 | 5.46 | 3.73 |
383 | 43.326 | 4178 | 311 821 | 5.49 | 3.62 |
393 | 56.007 | 3316 | 403 088 | 5.61 | 3.52 |
403 | 68.327 | 2937 | 491 756 | 5.69 | 3.47 |
413 | 69.387 | 3127 | 499 385 | 5.70 | 3.50 |
423 | 102.46 | 3162 | 737 414 | 5.87 | 3.50 |
433 | 143.46 | 2753 | 1 032 495 | 6.01 | 3.44 |
443 | 189.28 | 2352 | 1 362 266 | 6.13 | 3.37 |
453 | 221.6 | 1887 | 1 594 876 | 6.20 | 3.28 |
463 | 358.4 | 1301 | 2 579 438 | 6.41 | 3.11 |
473 | 444.4 | 1010 | 3 198 388 | 6.50 | 3.00 |
483 | 747.17 | 739.7 | 5 377 452 | 6.73 | 2.87 |
Частота измерений 10 кГц | |||||
293 | 6.0884 | 17 560 | 43 819 | 4.64 | 4.24 |
303 | 4.4818 | 23 320 | 32 256 | 4.51 | 4.37 |
313 | 0.22448 | 103 400 | 1616 | 3.21 | 5.01 |
323 | 0.82123 | 74 880 | 5910 | 3.77 | 4.87 |
333 | 7.0577 | 15 060 | 50 795 | 4.71 | 4.18 |
343 | 11.448 | 10 210 | 82 392 | 4.92 | 4.01 |
353 | 13.064 | 8540 | 94 023 | 4.97 | 3.93 |
363 | 18.292 | 5910 | 131 649 | 5.12 | 3.77 |
373 | 17.598 | 4920 | 126 654 | 5.10 | 3.69 |
383 | 21.276 | 3803 | 153 125 | 5.19 | 3.58 |
393 | 28.628 | 3050 | 206 038 | 5.31 | 3.48 |
403 | 33.349 | 2784 | 240 016 | 5.38 | 3.44 |
413 | 34.595 | 2970 | 248 983 | 5.40 | 3.47 |
423 | 45.167 | 3024 | 325 071 | 5.51 | 3.48 |
433 | 63.719 | 2591 | 458 592 | 5.66 | 3.41 |
443 | 77.797 | 2258 | 559 912 | 5.75 | 3.35 |
453 | 101.89 | 1783 | 733 312 | 5.87 | 3.25 |
463 | 160.85 | 1239 | 1 157 652 | 6.06 | 3.09 |
473 | 203.42 | 970.7 | 1 464 033 | 6.17 | 2.99 |
483 | 468.43 | 677.2 | 3 371 334 | 6.53 | 2.83 |
Результаты исследований, представленные в табл. 1, показывают, что при исследуемом интервале температур (293–483 К) образец имеет большие значения частот, которые затем убывают от 1 до 5 кГц и 10 кГц: при температуре 293 К – 3.28 ⋅ ⋅ 106 (1 кГц), 1.74 ⋅ 105 (5 кГц), 4.38 ⋅ 104 (10 кГц); а при температуре 483 К – 4.38 ⋅ 107 (1 кГц), 5.38 ⋅ 106 (5 кГц), 3.37 ⋅ 106 (10 кГц). Материал представляет интерес для микроконденсаторной технологии.
Исследование температурной зависимости электросопротивления (R) от температуры показывает, что данный материал в интервале 293–313 К проявляет металлическую проводимость, а при температурах 313–483 К – полупроводниковую (частота 10 кГц).
Результаты исследований показывают, что ширина запрещенной зоны данного материала в интервале 313–483 К равна 0.51 эВ и его можно отнести к узкозондовым полупроводникам.
Таким образом, в результате экспериментов на основе кокса из угля месторождений “Шубарколь” марки “Д” (Казахстан) получены графеносодержащие материалы методом электродугового разряда, который является наиболее перспективным способом получения наноматериалов и обеспечивает получение продукта с относительно высокой чистотой с малым дефектом. Выход графеносодержащего наноматериала составляет 3%.
Использование графена в качестве электродов для аккумуляторов, конденсаторов для замены литий-ионных батарей, а также для получения высокопрочных композитных материалов путем добавления небольшого количества графена, в электронной и строительной промышленности позволит решит экологические проблемы.
Экологический эффект предлагаемого способа заключается в создании экологически чистой технологии, основанной на переработке угля и углепродуктов, для получения продуктов с высокой добавленной стоимостью. Предложенный способ уникален тем, что сырьем, которое используется для синтеза графена и графеносодержащих материалов, является углепродукт (кокс), запасов которого достаточно в Казахстане, по сравнению с технологией получения графена и графеноподобных материалов из множества других прекурсоров (HNO3, HCl, H2SO4 и др.) и с использованием других методов (метод Хаммерса, микромеханическое расщепление, термическое разложение SiC). Перспективность данных исследований заключается в возможности масштабного производства графена из углепродуктов, что приведет к появлению на рынке Казахстана материалов и композитов на их основе отечественного производства.
Список литературы
Novoselov K.S., Fal’ko V.I., Colombo L., Gellert P.R., Schwab M.G., Kim K. // Nature. 2012. V. 490. P. 192. https://doi.org/10.1038/nature11458.
He X., Li H., Ma J., Han H., Zhang C., Yu N., Xiao J. Qiu // Power Sources. 2017. V. 340. P. 183–191. https://doi.org/10.1016/j.jpowsour.2016.11.073
Chen Sh., Oyadiji S.O. // Mater. Today Phys. 2020. V. 15. P. 100257. https://doi.org/10.1016/j.mtphys.2020.100257
Mattevi C., Kim H., Chhowalla M. // J. Mater. Chem. 2011. V. 21. P. 3324–3334. https://doi.org/10.1039/c0jm02126a
Neto A.H.C., Guinea F., Peres N.M.R., Novoselov K.S., Geim A.K. // Rev. Mod. Phys. 2009. V. 81. P. 109. https://doi.org/10.1103/RevModPhys.81.109
Chen J.H., Jang C., Xiao S., Ishigami M., Fuhrer M.S. // Nat. Nanotechnol. 2008. V. 3. P. 206–209. https://doi.org/10.1038/nnano.2008.58
Du X., Skachko I., Barker A., Andrei E.Y. // Nat. Nanotechnol. 2008. V. 3. P. 491. https://doi.org/10.1038/nnano.2008.199
Qiu L., Liu J.Z., Chang S.L. // Nat. Commun. 2012. V. 3. P. 1–7. https://doi.org/10.1038/ncomms2251
Worsley M.A., Pauzauskie P.J., Olson T.Y., Biener J., Satcher J.J., Baumann T.F. // J Amer. Chem. Soc. 2010. V. 132. P. 14067. https://doi.org/10.1021/ja1072299
Olabi A.G., Abdelkareem M.A., Wilberforce T., Sayed E.T. // Renewable and Sustainable Energy Rev. 2020. V. 135. https://doi.org/10.1016/j.rser.2020.110026
Ren X., Zhang S.S., Tran D.T., Read J. // J. Mater. Chem. 2011. V. 21. P. 10118. https://doi.org/10.1039/c0jm04170j
Wang X., Zhi L., Müllen K. // Nano Lett. 2008. V. 8. P. 323. https://doi.org/10.1021/nl072838r
Ramanathan T., Abdala A., Stankovich S., Dikin D. // Nat. Nanotechnol. 2008. V. 3. P. 327. https://doi.org/10.1038/nnano.2008.96
Cotul U., Parmak D.S.,Kaykilarli C., Saray O., Uzunsoy D., Colak O. // Acta Physica Polonica A. 2018. V. 134. P. 288.
Qin B., Zhang T., Chen H., Ma Y. // Carbon. 2016. V. 102. P. 494. https://doi.org/10.1016/j.carbon.2016.02.074
Zhang Y.H., Chen Z.Y., Ge X.M., Liang Y.J., Hu S.K., Sui Y.P., Yu G.H. // Materials Letters. 2018. V. 211. P. 258. https://doi.org/10.1016/j.matlet.2017.09.100
John U., Michael U. // Vacuum. 2020. V. 182. P. 109767. https://doi.org/10.1016/j.vacuum.2020.109767
Дополнительные материалы отсутствуют.
Инструменты
Химия твердого топлива