Химия твердого топлива, 2022, № 1, стр. 43-48
ВЛИЯНИЕ ПОВЕРХНОСТИ УГЛЕРОДНОГО МАТЕРИАЛА НА ПОРООБРАЗОВАНИЕ ПРИ ЕГО ОКИСЛЕНИИ
Б. В. Пешнев 1, *, В. Х. Нгуен 2, **, Н. Н. Гаврилова 3, ***, А. С. Филимонов 1, ****, А. И. Николаев 1, *****
1 ФГБОУ ВО “МИРЭА – Российский технологический университет”
(Институт тонких химических технологий имени М.В. Ломоносова)
119454 Москва, Россия
2 Технологический институт, Главное управление оборонной промышленности
Ханой, Социалистическая Республика Вьетнам
3 ФГБОУ ВО “Российский химико-технологический университет имени Д.И. Менделеева”
125047 Москва, Россия
* E-mail: peshnevbv@mail.ru
** E-mail: nguyenvanhuy281190@gmail.com
*** E-mail: gavrilovann@yahoo.com
**** E-mail: filimonov999@mail.ru
***** E-mail: nicolaevai@mail.ru
Поступила в редакцию 04.06.2021
После доработки 27.06.2021
Принята к публикации 13.10.2021
- EDN: ZRJWHU
- DOI: 10.31857/S0023117722010066
Аннотация
Рассмотрено взаимодействие углеродных материалов (графита, технического углерода, антрацита) с окисляющими агентами (воздухом, диоксидом углерода) с позиций топохимических реакций. Показано, что скорость реакции окисления зависит не только от температуры процесса, природы и расхода окисляющего агента, но и от поверхности активируемого образца. Увеличение размеров кристаллитов углерода в образце приводит к сокращению границ их контактов и снижению скорости реакции окисления. Установлено, что от активных центров, локализующихся на границах кристаллитов, зависит не только скорость реакции окисления, но и количество образующихся пор. Показано, что двухстадийное окисление углеродных материалов (до невысоких степеней активации воздухом, а затем диоксидом углерода или водяным паром) позволяет существенно повысить сорбционные характеристики образца.
Окислительная активация углеродных материалов воздухом, водяным паром, диоксидом углерода широко используется в технологии производства сорбентов [1, 2].
Разрабатывая технологию получения активных углей, основная масса исследователей фокусировала внимание на температурах проведения процесса при активации различного исходного сырья [3], механизме формирования пористого пространства [4–6], особенностей использования тех или иных активирующих агентов [7–11]. Установлено, что существенное влияние на пористые характеристики образующегося материала и на характер протекания процесса оказывает температура. При низких температурах окисляющий агент способен глубоко проникать в углеродную матрицу и формировать объемную пористость и размер пор без изменения внешней геометрии материала. При повышенных температурах скорость реакции окисления на поверхности велика, диффузия окислителя в матрицу практически прекращается и процесс протекает с внешним обгаром материала, сопровождающимся образованием на поверхности крупных пор [12]. Исследовалось влияние скорости подачи окислителя. Показано, что при увеличении расхода активирующего агента увеличивается скорость реакции окисления, но пористость образующегося материала при этом снижается [13, 14].
Следует отметить, что в этих работах практически не затрагивался вопрос о взаимодействии активирующих агентов с углеродными поверхностями, а технология получения углеродных сорбентов базируется скорее на эмпирическом, чем научно обоснованном подходе. Между тем еще в работе П.А. Ребиндера [15] указано, что взаимодействие углеродной подложки с газообразными агентами следует рассматривать как гетерогенный процесс, поэтому на скорость реакции наряду с температурой и расходом окислителя должны влиять и свойства поверхностных атомов подложки.
Влияние поверхности углеродной подложки (размеров кристаллитов углерода и протяженности границ их контактов) на скорость формирования отложений пироуглерода и его характеристики, а также на закономерности активации дисперсного углерода рассмотрено в работах [16–18]. Показано, что при увеличении протяженности границ кристаллитов подложки (технического углерода) возрастает скорость осаждения пироуглерода и уменьшаются размеры его кристаллитов. При увеличении протяженности границ скорость окисления углеродной подложки возрастает, при этом увеличивается доля реакций порообразования. В работе [19], посвященной исследованию закономерностей образования пироуглерода на поверхности сажи, было высказано предположение, что на границах контактов кристаллитов подложки локализуются активные центры (ненасыщенные С–С связи). На этих центрах из газовой фазы адсорбируются смолы пиролиза, из которых и формируется пироуглерод. В работе [20] изучали нитрование сажи окислами азота и отметили связь между скоростью реакции и активными центрами, образованными двойными связями углерод-углерод.
Взаимодействие углеродного материала с активирующим агентом (окислителем) также начинается с адсорбции последнего на активных центрах. Закономерно предположить, что “концентрация” таких активных центров будет влиять на скорость процесса, на его протекание (обгар или порообразование) и на характеристики формирующегося пористого пространства.
ЭКСПЕРИМЕНТАЛЬНАЯ ЧАСТЬ
Объектами исследования были выбраны мелкозернистый графит марки МГ, технический углерод марок N220 и N234, в том числе термообработанный в инертной среде при 2300–2400°С (N220гр), и антрацит группы А2. Их физико-химические характеристики приведены в табл. 1.
Таблица 1.
Физико-химические характеристики объектов исследования
Образец | Показатель | |||||
---|---|---|---|---|---|---|
плот- ность, г/см3 | удельная поверхность, м2/г | дисперсность | размер кристаллитов, нм | длина контактов кристаллитов, нм/г | ||
La | Lc | |||||
МГ | 2.0790 | 4.5 | 2.85 ± 0.05 мкм | 24.8 | 9.1 | 1.14 ⋅ 102 |
ТУ N234 | 1.7603 | 111 | 32 нм | 3.0 | – | 1.42 ⋅ 106 |
ТУ N220 | 1.7828 | 116 | 27 нм | 3.2 | – | 1.56 ⋅ 106 |
ТУ N220гр | 1.8179 | 98 | 27 нм | 7.6 | – | 6.43 ⋅ 105 |
А2 | 1.9566 | 0.5 | 1–2 мм | – | – | – |
Принципиальный подход к расчету длины контактов кристаллитов для образцов технического углерода изложен в работе [16].
При оценке длины контактов кристаллитов графита делались допущения о том, что частица образца имеет форму куба со стороной 2.85 мкм; кристаллит графита также имеет форму куба, объем которого равен $L_{a}^{2} \times {{L}_{c}}$. Далее, делением поверхности частицы образца (6 ⋅ 2.852) на поверхность грани “кристаллита” определяли число граней, формирующих поверхность частицы и вычисляли их суммарный периметр.
Для образца А2 длина контактов кристаллитов не оценивалась, так как говорить об углях, как об объектах, имеющих кристаллическую структуру, некорректно.
Эксперименты проводились в кварцевом реакторе с внутренним диаметром 8 мм, навеска образца варьировалась от 0.05 до 0.20 г. Активацию проводили в диапазоне температур 450–1000°С воздухом или диоксидом углерода, расход которых варьировался от 5 до 50 мл/мин. В процессе активации фиксировались масса, адсорбционная поверхность и кажущийся объем образца.
Удельная поверхность и другие характеристики пористой структуры определялись методом низкотемпературной адсорбции азота на автоматическом анализаторе удельной поверхности и пористости Gemini VII 2390t фирмы Micromeritics [21]. Распределение мезопор по размерам рассчитывали, пользуясь уравнением Кельвина с учетом формы пор в материале. Объем микропор определяли по уравнению Дубинина-Радушкевича.
ОБСУЖДЕНИЕ РЕЗУЛЬТАТОВ
Типичные зависимости изменения поверхности и массы образца в процессе активации приведены на рис. 1, из которого видно, что, несмотря на существенные изменения поверхности образца (в 4–5 раз), скорость его окисления в ходе процесса практически не изменялась. Повышение температуры активации, расхода окисляющего агента, использование для активации воздуха, а не диоксида углерода приводило к увеличению скорости процесса.
Рис. 1.
Изменение массы образца N234 и его адсорбционной поверхности в процессе активации: 1 – активирующий агент воздух, расход 5 мл/мин, температура 450°С; 2 – активирующий агент диоксид углерода, расход 15 мл/мин, температура 900°С.
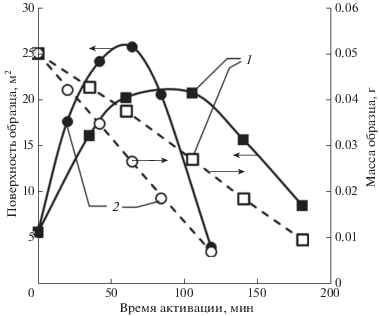
Активация углеродных материалов может протекать с преимущественным обгаром или порообразованием. В работе [22] предложены уравнения, позволяющие по изменению массы образца, его удельной поверхности и кажущегося объема (отношению объема навески образца к его массе) в процессе окисления оценить долю реакций порообразования (α) и количество образующихся пор (N).
(2)
$N = \frac{{{{{(\sqrt[3]{{1 - q}}({{S}^{{{\text{отн}}}}}(1 - {{q}^{2}}) - \alpha ) - (1 - \alpha )(1 - {{q}^{2}}))}}^{3}}}}{{{{q}^{2}}{{\alpha }^{3}}(1 - q)}},$Допущения, принятые при выводе этих уравнений, не предполагали разрушения частиц окисляемого образца в результате слияния пор, а данные о “количестве” пор носят качественный показатель, позволяющий только оценить и сравнить изменения, происходящие при различных условиях активации.
На рис. 2–4 показано влияние температуры активации, природы и расхода окисляющего агента на долю реакций порообразования и количество образующихся пор.
Рис. 2.
Влияние длины контактов кристаллитов на долю реакций порообразования и количество образующихся пор (окисляющий агент – СО2, температура 1000°С): 1 – образец N220, расход СО2 30 мл/мин; 2 – образец N220гр, СО2 30 мл/мин; 3 – образец МГ, расход СО2 15 мл/мин.
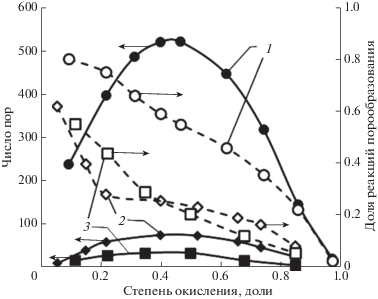
Рис. 3.
Влияние природы окисляющего агента на долю реакций порообразования и количество образующихся пор (образец N234): 1 – температура 900°С, расход СО2 15 мл/мин; 2 – температура 450°С, расход воздуха 5 мл/мин.
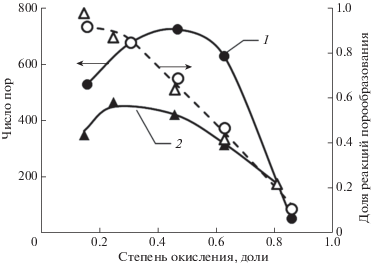
Рис. 4.
Влияние температуры и расхода диоксида углерода (окисляющего агента) на долю реакций порообразования и количество образующихся пор (образец N234): 1 – температура 900°С, расход СО2 5 мл/мин; 2 – температура 1000°С, расход СО2 5 мл/мин; 3 – температура 900°С, расход СО2 40 мл/мин.
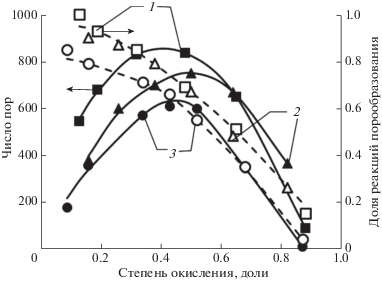
Можно отметить, что доля реакций порообразования очень зависит от поверхности образца. Увеличение размеров кристаллитов подложки, сопровождающееся сокращением границ их контактов, резко снижает долю реакций порообразования. Существенного влияния природы активирующего агента (воздух или диоксид углерода) и температуры активации (900 и 1000°С в случае активации СО2 или 450 и 550°С при активации воздухом) на долю реакций порообразования не зафиксировано. Значительно больший вклад в долю реакций порообразования вносит расход активирующего агента. При увеличении расхода окислителя доля реакций порообразования снижается.
Значительно большее влияние условия проведения активации оказывают на количество образующихся пор и характеристики пористого пространства. Так, при активации воздухом не только образуется меньше пор, но и снижается объем мезопор. Так, объем мезопор образца, полученного окислением N234 воздухом (550°С, 30 мл/мин), был равен 1.553 см3/г, а у образца, полученного окислением СО2 (900°С, 30 мл/мин), – 1.860 см3/г. Степени активации были сопоставимы (0.44 и 0.47), сопоставимы были и доли реакций порообразования (0.51 и 0.59 соответственно). К сокращению числа пор и объема мезопор приводит также повышение температуры активации и расхода окислителя, например, объем мезопор образца, полученного активацией N234 диоксидом углерода при 1000°С (30 мл/мин, степень активации 0.43) был равен 1.672 см3/г.
Следует отметить непостоянство количества пор во времени: их увеличение на начальном этапе развития процесса и снижение при степенях окисления свыше 0.5. Снижение количества пор обусловлено их слиянием в результате увеличения диаметров. Увеличение количества пор на начальных этапах развития процесса может быть связано с образованием поверхностных оксидов [23], которые также могут выступать как активные центры [16]. В таком случае, проводя активацию углеродных материалов в две стадии, можно получить материал с большим количеством пор. На первом этапе целесообразно для активации использовать воздух, так как в этом случае образуется больше поверхностных оксидов, а затем – диоксид углерода или водяной пар.
Можно ожидать, что скорость реакции окисления материала, предварительно активированного воздухом, будет выше, чем у материала, не подвергавшегося такой активации. Образец, полученный при двухстадийной обработке, должен характеризоваться большей удельной поверхностью, большим количеством пор, чем материал, полученный в одну стадию.
Для подтверждения этого предположения образец А2 был подвергнут предварительному окислению воздухом (расход 5 мл/мин) при температуре 450°С, до степеней активации 0.03 (А20.03), 0.08 (А20.08) и 0.16 (А20.16). Основная активация проводилась при температуре 900°С диоксидом углерода, расход которого также составлял 5 мл/мин. Суммарная степень активации во всех случаях достигала ∼ 0.4.
Отмечено, что предварительное окисление образца воздухом приводит к увеличению скорости последующего окисления диоксидом углерода. Так, скорость реакции окисления необработанного образца (А20) составляла 0.171 мг/мин, у образца А20.03 скорость реакции окисления СО2 возросла до 0.216 мг/мин, а у образца А20.16 – до 0.295 мг/мин. Предварительная активация отразилась также и на удельной поверхности образцов. Удельная поверхность А20 составляла 130 м2/г, образца А20.03 – 280 м2/г, а А20.08 – 320 м2/г. Количество пор при этом увеличилось в ∼ 2.1 и 2.6 раза соответственно. Предварительная активация до больших степеней окисления (0.16) приводила к снижению удельной поверхности.
Увеличение адсорбционной поверхности повысило и сорбционную емкость образцов по метиленовому оранжевому, у образца А20.08 она была на 28% выше, по сравнению с образцом А20.
Аналогичные результаты были получены и в случае, когда вторая стадия активации проводилась водяным паром.
ЗАКЛЮЧЕНИЕ
Представленные материалы свидетельствуют о том, что взаимодействие углеродных материалов с паро- и газообразными окислителями хорошо описывается с позиций топохимических реакций. Активными центрами, на которых адсорбируется окисляющий агент, являются ненасыщен-ные связи углерод–углерод и функциональные группы, локализованные на границах контактов кристаллитов исходного образца. Количество этих центров, которое можно регулировать, влияет не только на скорость реакции окисления, но и на сорбционные характеристики получаемого материала.
Список литературы
Rodriguez-Reinoso F., Marsh A.C., Martinez M.A. // Carbon. 2000. V. 38. P. 379.
Мухин В.М., Воропаева Н.Л., Карпачев В.В., Дмитрякова Е.Е. // Способ получения активного угля из растительного сырья: Пат. 2527221 РФ // Б.И. 2014. С. 44.
Mui E.L.K., Ko D.C.K., McKay G. // Carbon. 2004. V. 42. P. 2789.
Marsh H., Rodríguez-Reinoso F. Activated carbon. London: Elsevier, 2006. 554 p.
Ferdi Schüth, Sing K.S.W., Weitkamp J. Handbook of porous solids. Weinheim: Wiley-VCH, 2002. 1190 p.
Marsh H., Rand B. // Carbon. 1971. V. 1. P. 47.
Tancredi N., Medero N., Moller F., Píriz J., Plada C., Cordero T. // J. Colloid and Interface Sci. 2004. V. 279. № 2. P. 357.
Milich P., Moller F., Píriz J., Vivó G. // Separation Sci. and Technol. 2002. V. 37. P. 1453.
Юрьев Ю.Л., Штеба Т.В. // Вестн. Технол. ун-та. 2015. Т. 18. № 4. С. 194.
Mohd Saufi Md Zaini, Syed-Hassan Syed Shatir A. // Recent Innovations Chem. Engng. 2018. V. 11. P. 50.
Nabais J.M.V., Nunes P., Carrott P.J.M., Ribeiro Carrott M.M.I., Garcia A.M., DiazDiez M.A. // Fuel Proc. Technol. 2008. V. 89. № 3. P. 262.
El-Genk M.S., Tournier J.M.P. // J. Nuclear Mater. 2011. V. 411 (1–3). P. 193.
Xiaowei L., Jean-Charles R., Suyuan Y. // Nuclear Engng and Design. 2006. V. 236. P. 938.
Herawan S.G., Ahmad M.A., Putra A., Yusof A.A. // The Sci. World J. 2013. V. 5. P. 47.
Ребиндер П.А. Поверхностные явления в дисперсных системах. М.: Наука, 1978. 121 с.
Филимонов А.С., Пешнев Б.В., Суровикин Ю.В., Трофимова Н.Н., Асилова Н.Ю. // Вестн. МИТХТ им. М.В. Ломоносова. 2014. Т. 9. № 6. С. 99.
Пешнев Б.В., Филимонов А.С., Суровикин Ю.В., Асилова Н.Ю. // ХТТ. 2018. № 4. С. 61. [Solid Fuel Chemistry, 2018. V. 54. № 4, p. 269. https://doi.org/10.3103/S0361521918040080]https://doi.org/10.1134/S0023117718040084
Пешнев Б.В., Филимонов А.С., Гаврилова Н.Н., Николаев А.И., Нгуен В.Х. // ХТТ. 2018. № 3. С. 35. [Solid Fuel Chemistry, 2018. V. 52. № 3, p. 173. https://doi.org/10.3103/S0361521918030096]https://doi.org/10.7868/S0033117718030052
Теснер П.А., Городецкий А.Е., Бородина Л.М., Денисевич Е.В., Ляхов А.Г. // Докл. АН СССР. Сер. Физическая химия. 1977. Т. 235. № 2. С. 410.
Тужиков О.О., Хохлова Т.В., Сычев Н.В., Зотов С.Б., Тужиков О.И., Желтобрюхов В.Ф. // Изв. Волгоградского гос. техн. ун-та. 2007. № 10 (36). С. 113.
Печуро Н.С., Песин О.Ю., Эстрин Р.И., Ройтер Л.А. // Промышленность синтетического каучука, шин и резиновых технических изделий. 1987. № 2. С. 16.
Нгуен В.Х., Филимонов А.С., Пешнев Б.В., Николаев А.И. // Тонкие химические технологии. 2018. Т. 13. № 3. С. 57.
Бутырин Г.М. Высокопористые углеродные материалы. M.: Химия, 1976. 192 с.
Дополнительные материалы отсутствуют.
Инструменты
Химия твердого топлива