Кинетика и катализ, 2019, T. 60, № 1, стр. 93-107
Каталитический крекинг смесей циклогексана и гексена-1 на моно-, би- и трицеолитных катализаторах
О. В. Потапенко 1, *, М. С. Худяков 1, Е. О. Алтынкович 1, К. С. Плехова 1, Т. П. Сорокина 1, В. П. Доронин 1
1 ФГБУН Институт проблем переработки углеводородов СО РАН
644040 Омск, ул. Нефтезаводская, 54, Россия
* E-mail: potap@ihcp.ru
Поступила в редакцию 14.05.2018
После доработки 13.08.2018
Принята к публикации 13.07.2018
Аннотация
Исследовано влияние температуры (540–640°С), весовой скорости подачи сырья (1.0–7.0 ч–1) и соотношения водяной пар : сырье (0–2.5) на выход C2–C4-олефинов, конверсию и октановые характеристики при крекинге смеси модельных углеводородов (циклогексана и гексена-1). Изучено влияние структуры цеолитов в моно-, би- и трицеолитных катализаторах на распределение продуктов крекинга. Показано, что комбинирование компонентов катализатора в би- и трицеолитных системах позволяет увеличить эффективность последовательного крекинга углеводородов (С6–С12 → С4–С8 → С3–С6 → С2–С4) по схеме: матрица → ZSM-5 → FER. Максимальный суммарный выход С2-, C3- и C4-олефинов (50.2 мас. % при конверсии 75.5%) был достигнут при использовании бицеолитного катализатора ZSM-5 + FER.
В настоящее время на крупных современных нефтеперерабатывающих предприятиях существует проблема переработки бензиновой фракции 62–85°С и бензина, получаемого на установке замедленного коксования. Легкая бензиновая фракция (62–85°C) содержит более 20 мас. % циклогексана и не может быть использована в процессе риформинга (по топливному варианту) по причине высокого содержания бензола, количество которого в соответствии с текущими требованиями не должно превышать более 1 об. % [1]. Другой низкосортной бензиновой фракцией является бензин коксования, получающийся как побочный продукт процесса замедленного коксования. Эта фракция характеризуется низкими значениями октанового числа (65 ед.), высоким содержанием олефинов (более 25 мас. %) и серы (более 2500 м. д.) [2]. Гидроочистка данной фракции требует больших капитальных и эксплуатационных затрат [3, 4]. Таким образом, каталитический крекинг легких углеводородов может рассматриваться как эффективный способ переработки указанных бензиновых фракций в ценные продукты (легкие олефины и высокооктановый компонент моторных топлив) [5].
Быстрорастущий спрос на легкие олефины может являться дополнительным фактором, определяющим высокую эффективность процесса каталитического крекинга бензиновых фракций. Лучшие мировые образцы катализаторов крекинга позволяют получать при крекинге легких фракций 15 и 35% этилена и пропилена соответственно. Процесс имеет низкую чувствительность к содержанию примесей в сырье и не требует дополнительных предварительных обработок. Соотношение между этиленом и пропиленом может изменяться в очень широких пределах посредством изменения состава катализатора [6] и условий процесса. Классический процесс крекинга вакуумного газойля протекает при температурах 500–545°С, тогда как использование легкого сырья требует увеличения жесткости процесса и, как следствие, повышения температуры до 550–650°C.
Каталитический крекинг легких углеводородных фракций, как правило, протекает на катализаторах, содержащих узкопористые цеолиты. Традиционно при создании катализаторов этого типа в качестве базового компонента используется цеолит ZSM-5. Одним из способов повышения активности катализаторов является качественное изменение цеолитного компонента. При этом могут быть использованы различные комбинации цеолитов. При определенных составах катализатора можно получить распределение требуемых продуктов с преобладанием этилена или пропилена. Так, в работе [7] было отмечено снижение энергии активации крекинга и увеличение выхода легких олефинов при использовании бицеолитных катализаторов на основе ZSM-5 и MOR (морденит).
Молекулярно-ситовые свойства цеолитов ZSM-5 и FER (феррьерит) оказывают большое влияние на каталитические свойства катализаторов на их основе (конфигурационная селективность). Катализаторы, приготовленные на основе узкопористых цеолитов, обладают низкой активностью в реакциях переноса водорода и позволяют получать С2–С4-олефины с высокой селективностью [8].
Цеолиты типов Y и MOR более склонны к дезактивации по причине большого количества образуемых коксовых отложений. Цеолит типа MOR имеет двухмерную систему каналов, но диффузия больших молекул сырья может происходить только через систему параллельных одномерных каналов, которые могут быть заблокированы при частичном разрушении кристаллической решетки. Цеолит типа Y характеризуется максимальным размером окон и полостей среди исследованных образцов и имеет максимальный свободный объем. Эти факторы наряду с высокой кислотностью определяют высокую активность цеолита Y в реакциях переноса водорода (рис. 1). Для повышения стабильности цеолитов используют модификаторы [9]. Цеолит ZSM-5 чаще всего подвергают различным обработкам соединениями фосфора. Фосфор стабилизирует ионы алюминия в решетке цеолитов и предотвращает их выход с образованием неструктурного алюминия. Модифицирование цеолитов фосфором приводит в большей степени к нейтрализации сильных кислых центров [10–12].
Процесс глубокого каталитического крекинга вакуумного газойля также направлен на получение максимального количества легких олефинов (схема 1).
Схема 1. Схема процесса глубокого каталитического крекинга.
Первичный крекинг происходит на матрице катализатора с учетом больших размеров исходных молекул углеводородов. Вторичный крекинг осуществляется на широкопористом цеолите типа Y [13]. Финальным этапом является крекинг полупродуктов на цеолите ZSM-5 с образованием целевых C2–C4-олефинов. Типичное соотношение олефинов составляет 1 : 3.4 : 5.8 (этилен : пропилен : бутилены соответственно).
Согласно схеме 1, можно предположить, что первичный крекинг легких углеводородных фракций также будет осуществляться на матрице катализатора или широкопористом цеолите. Финальный же этап крекинга углеводородов будет определяться составом и структурными особенностями узкопористого цеолитного компонента (кислотность центров, размер входных окон, объем микропор и др.). Комбинация различных цеолитов Y и ZSM-5 при глубоком каталитическом крекинге приведет к росту большего количества олефинов, особенно С2 и С3.
Целью настоящей работы являлось исследование влияния условий процесса крекинга и состава цеолитного компонента катализатора на выход C2–C4-олефинов при превращении модельной смеси циклогексан + гексен-1.
ЭКСПЕРИМЕНТАЛЬНАЯ ЧАСТЬ
Приготовление катализаторов
Катализаторы составляли из активного (цеолитного) компонента и матрицы. Матрица содержала два компонента – оксид алюминия и бентонитовую глину (монтмориллонит). Состав цеолитного компонента варьировали с использованием следующих веществ (“Zeolyst International”): морденит (CBV90A), ферриерит (CP914C), ZSM-5 (CBV-3024E, CBV-5524G, CBV-8014, CBV-30014G) и цеолит Y (CBV712). Фосфорсодержащий цеолит P-ZSM-5 получали путем пропитки цеолита HZSM-5 раствором (NH4)2HPO4 с последующим прокаливанием при 650°С. Составы каталитических систем, использованных в настоящей работе, приведены в табл. 1.
Таблица 1.
Компонентный состав катализаторов крекинга
№ катализатора | Компонентный состав | |||||||
---|---|---|---|---|---|---|---|---|
ZSM-5, мас. % | SiO2/Al2O3 в ZSM-5 | FER | MOR | Y | оксид алюминия | монтмо-риллонит | [P]-цеолит | |
мас. % | ||||||||
1 | 50 | 30 | – | – | – | 25 | 25 | – |
2 | 55 | – | ||||||
3 | 80 | – | ||||||
4 | 300 | – | ||||||
5 | 30 | 7.7 | ||||||
6 | – | – | – | 50 | – | 37.5 | 12.5 | – |
7 | – | – | 50 | – | – | 37.5 | 12.5 | – |
8 | – | – | – | – | 50 | 37.5 | 12.5 | – |
9 | 25 | 300 | 25 | – | – | 37.5 | 12.5 | – |
10 | 25 | 300 | – | – | 25 | 37.5 | 12.5 | – |
11 | – | – | 25 | – | 25 | 37.5 | 12.5 | – |
12 | 16.6 | 300 | 16.6 | – | 16.6 | 37.5 | 12.5 | – |
13 | 50 | 300 | – | – | – | 37.5 | 12.5 | – |
Компоненты катализатора гомогенизировали. Полученную суспензию фильтровали на вакуумном фильтре. Пасту формовали с получением частиц размером 2 мм. Далее катализатор сушили на воздухе при комнатной температуре, а затем при 100°С с последующим прокаливанием при 650°С. Всего было приготовлено 13 образцов.
Исследование катализаторов
Пористую структуру образцов исследовали методом низкотемпературной адсорбции азота на приборе ASAP-2020 (“Micromeritics”, США). Удельную площадь поверхности (SБЭТ) определяли методом БЭТ. Общий объем пор адсорбции (Vадс) измеряли методом адсорбции азота при P/P0 = = 0.99. Перед выполнением исследования образцы предварительно прокаливали при 650°С.
Суммарное количество кислотных центров определяли методом температурно-программируемой десорбции аммиака (ТПД-NH3) на высокоточном хемосорбционном анализаторе AutoChem-2920 (“Micromeritics”) с использованием смеси 6 об. % NH3 в гелии. Перед экспериментами образцы нагревали до 650°С в потоке 10 об. % О2 в гелии, выдерживали при этой температуре в течение 1 ч и затем охлаждали в потоке гелия до 100°С. Адсорбцию аммиака проводили при той же температуре в течение 60 мин с последующей продувкой гелием при 100°С в течение 1 ч для удаления физически адсорбированного аммиака. ТПД-NH3 проводили в интервале температур 100–600°С, скорость нагрева измерительной ячейки с образцом составляла 10 град/мин.
Химический состав компонентов и катализаторов определяли, разлагая образцы в минеральных кислотах (серная, хлорная, фтористоводородная) с последующим анализом раствора методами атомно-адсорбционной спектрометрии на приборе Shimadzu AA-6300 (Япония) и атомно-эмиссионной спектрометрии с индуктивно-связанной плазмой (AES-ICP) на приборе Varian 710-ES (США).
Решеточный модуль цеолита (SiO2/Al2O3, М) определяли методом ядерно-магнитного резонанса на ядрах 29Si (29Si ЯМР). Спектры твердых образцов снимали на ЯМР-спектрометре Avance-400 (“Bruker”, Германия, 9.4 Тл) с многоядерным зондом SB4, предназначенном для экспериментов с вращением под магическим углом (MAS) на частоте до 10 000 Гц со следующими параметрами одноимпульсного эксперимента: несущая (ларморовская) частота 79.5 МГц, ширина импульса 2.5 мкс (π/2), время повторения импульсов 2.0 с, общее количество импульсов 32 000.
Каталитические испытания
В качестве модельного сырья была выбрана смесь равных количеств циклогексана (“Sigma-Aldrich”) и гексена-1 (“Sigma-Aldrich”). Выбор этих модельных соединений обусловлен типичным составом промышленных бензиновых фракций. Циклогексан является основным компонентом фракции 62–85°С, а гексен-1 – непредельным соединением, отражающим высокую реакционную способность бензина замедленного коксования.
Исследование каталитических свойств образцов проводили на лабораторной установке с неподвижным слоем катализатора. Катализатор загружали в реактор в количестве 3 г в виде частиц размером 2 мм. Реактор помещали в трехзонную электропечь. Для фиксации образца использовали вставку из кварца. Лабораторная установка аналогична установке, описанной в Сборнике стандартов Американского общества испытания материалов ASTM D3107.
Газообразные продукты анализировали на газовом хроматографе ГХ-1000, снабженном капиллярной колонкой (SiO2, 30 м × 0.32 мм) и пламенно-ионизационным детектором. Компонентный состав бензинов определяли на хромато-масс-спектрометре Shimadzu GCMS-QP2010, оборудованном колонкой HP-1ms (60 м × 0.25 мм × × 0.25 мкм) и дополнительным пламенно-ионизационным детектором. Октановое число (по исследовательскому методу, ИОЧ) определяли расчетным методом из компонентного состава по ASTM D5154.
Содержание кокса на катализаторе измеряли по потере массы при прокаливании образца катализатора на воздухе при 550–650°C.
Выход газообразных и жидких продуктов рассчитывали по формуле
Конверсию сырья (Х, мас. %) рассчитывали по формуле
где Wж.п – выход жидких продуктов (в мас. %).Для оценки количественного вклада реакций межмолекулярного переноса водорода использовали коэффициент переноса водорода (Hydrogen transfer coefficient – HTC):
где $\Sigma {{{\text{C}}}_{{4 = }}}$ и $\Sigma {{{\text{C}}}_{4}}$ выход бутиленов и бутанов соответственно.РЕЗУЛЬТАТЫ И ИХ ОБСУЖДЕНИЕ
Свойства катализаторов
В табл. 2 представлены свойства компонентов, используемых для приготовления образцов катализаторов. Все компоненты характеризуются низким содержанием оксида натрия. С увеличением силикатного модуля ZSM-5 наблюдается снижение концентрации кислотных центров, что согласуется с результатами работ [14, 15]. Кислотность цеолитов различных типов существенно отличается. Так, цеолит Y характеризуется более высокой концентрацией кислотных центров, что связано с низким значением модуля цеолита и высоким содержанием оксида алюминия в каркасе цеолита. Кислотность цеолитов, исследованная методом ТПД-NH3, уменьшается в ряду Y > > ZSM-5 > FER > MOR. Компоненты матрицы катализатора имеют существенно меньшую концентрацию кислотных центров по сравнению с цеолитами. Бентонитовая глина характеризуется минимальной концентрацией кислотных центров и, как следствие, практически не активна в реакциях крекинга. В то же время глина обладает хорошей связывающей способностью и обеспечивает необходимую прочность катализатора [13]. Оксид алюминия содержит только кислотные центры Льюиса [16] при относительно высокой концентрации кислотных центров, что является достаточным условием для осуществления первичного крекинга углеводородов.
Таблица 2.
Физико-химические свойства компонентов и катализаторов
Образец | Na2O | Al2O3 | РЗЭ2O3* | SБЭТ, м2/г | Vмикропор, см3/г | Кислот-ность**, мкмоль/г | SiO2/ Al2O3*** |
---|---|---|---|---|---|---|---|
мас. % | |||||||
HZSM-5 (M = 30) | 0.051 | 4.98 | – | 405 | 0.140 | 920 | 31 |
HZSM-5 (M = 55) | 0.041 | 2.87 | – | 425 | 0.122 | 785 | 57 |
HZSM-5 (M = 80) | 0.039 | 2.01 | – | 425 | 0.129 | 564 | 81 |
HZSM-5 (M = 300) | 0.054 | 0.57 | – | 415 | 0.070 | 503 | 305 |
MOR (M = 90) | 0.040 | 1.02 | – | 569 | 0.210 | 314 | 90 |
FER (M = 20) | 0.050 | 4.90 | – | 400 | 0.130 | 704 | 20 |
Y (M = 12) | 0.024 | 11.85 | 0.015 | 730 | 0.278 | 946 | 13 |
Оксид алюминия | 0.050 | 98.37 | – | 275 | – | 387 | – |
Монтмориллонит | 0.080 | 23.44 | – | 80 | 0.015 | 72 | – |
Состав сырья для получения легких углеводородов каталитическим крекингом
Влияние состава сырья на распределение продуктов крекинга изучали при крекинге модельной смеси циклогексан + гексен-1 на катализаторе № 4 (ZSM-5, M = 300). Каталитические испытания проводили для индивидуальных компонентов и их смесей (с различным соотношением). Данные о материальных балансах представлены в табл. 3.
Таблица 3.
Влияние состава сырья на материальный баланс процесса крекинга*
Продукты, селективность, конверсия | Выход продуктов, мас. % | |||
---|---|---|---|---|
cодержание гексена-1 в составе сырья, мас. % | ||||
100 | 67 | 33 | 0 | |
С1–С4-алканы | 12.80 | 10.90 | 11.10 | 11.30 |
Этилен | 13.60 | 14.60 | 13.90 | 14.20 |
Пропилен | 24.80 | 22.40 | 21.10 | 19.20 |
Бутилены | 10.80 | 9.20 | 9.50 | 7.80 |
С2–С4-олефины | 49.20 | 46.20 | 44.40 | 41.20 |
С2–С4-олефины (по аддитивности) | 49.20 | 46.56 | 43.84 | 41.20 |
HTC | 0.10 | 0.20 | 0.30 | 0.30 |
Селективность образования C2–C4-олефинов, % | 76.90 | 79.00 | 77.40 | 75.60 |
Жидкие продукты | 36.00 | 41.50 | 42.60 | 45.50 |
– ИОЧ, ед. | 110.00 | 111.00 | 107.60 | 105.40 |
– н-парафины | 0.48 | 0.30 | 0.45 | 0.22 |
– изопарафины | 0.11 | 0.25 | 0.34 | 0.18 |
– олефины | 13.25 | 9.08 | 8.15 | 11.98 |
– нафтены | 2.90 | 7.70 | 16.03 | 19.32 |
– арены | 83.27 | 82.66 | 75.04 | 68.30 |
Селективность образования жидких продуктов, % | 56.30 | 70.90 | 74.20 | 83.50 |
Кокс | 2.20 | 1.40 | 1.90 | 2.00 |
Сумма продуктов | 100.00 | 100.00 | 100.00 | 100.00 |
Конверсия, % | 64.00 | 58.50 | 57.40 | 54.50 |
Состав продуктов при крекинге смесей циклогексана с гексеном-1 полностью соответствует значениям, рассчитанным по аддитивности из превращения индивидуальных компонентов сырья. Трансформация молекул нафтена (циклогексан) и олефина (гексен-1) происходит индивидуально, без какого-либо взаимодействия между компонентами как и при классическом каталитическом крекинге вакуумного газойля или безводородном каталитическом облагораживании. Максимальный выход C2–C4-олефинов был получен при крекинге гексена-1 и составил 49.2 мас. %. Среди углеводородов олефины обладают максимальной реакционной способностью в условиях кислотного катализа. Полученный результат хорошо согласуется с работой [17], где прослеживалось влияние группового состава используемого сырья на состав получаемых продуктов. При этом вклад реакций переноса водорода был значительно выше [17], что обусловлено особенностями приготовления катализатора и его селективностью по отношению к бимолекулярным реакциям.
Условия процесса (температура, соотношение водяной пар : сырье, весовая скорость подачи сырья)
Исследование влияния температуры, весовой скорости подачи сырья (Weight hour space velocity – WHSV) и разбавления реакционной зоны водяным паром выполняли при каталитическом крекинге легких углеводородов на катализаторе № 4 (ZSM-5, M = 300). Данные о материальных балансах представлены в табл. 4 и 5.
Таблица 4.
Влияние температуры на материальный баланс процесса крекинга*
Продукты, селективность, конверсия | Выход продуктов, мас. % | |||
---|---|---|---|---|
температура процесса, °С | ||||
540 | 570 | 590 | 640 | |
С1–С4-алканы | 21.00 | 17.00 | 17.60 | 23.50 |
Этилен | 7.20 | 8.90 | 11.40 | 18.10 |
Пропилен | 15.40 | 17.10 | 19.10 | 19.30 |
Бутилены | 10.10 | 9.60 | 9.40 | 6.50 |
С2–С4-олефины | 32.70 | 35.60 | 39.90 | 43.90 |
HTC | 0.60 | 0.30 | 0.20 | 0.10 |
Селективность образования C2–C4-олефинов, % | 58.70 | 65.20 | 67.20 | 63.20 |
Жидкие продукты | 44.30 | 45.40 | 40.60 | 30.50 |
– ИОЧ, ед. | 100.40 | 102.30 | 104.0 | 110.90 |
– н-парафины | 0.84 | 0.55 | 0.35 | 0.29 |
– изопарафины | 0.27 | 0.32 | 0.22 | 0.05 |
– олефины | 6.61 | 12.76 | 15.80 | 1.02 |
– нафтены | 40.23 | 33.30 | 26.39 | 6.63 |
– арены | 52.06 | 53.08 | 57.24 | 92.02 |
Селективность образования жидких продуктов, % | 79.50 | 83.20 | 68.40 | 43.90 |
Кокс | 2.00 | 2.00 | 1.90 | 2.10 |
Сумма продуктов | 100.00 | 100.00 | 100.00 | 100.00 |
Конверсия, % | 55.70 | 54.60 | 59.40 | 69.50 |
Таблица 5.
Влияние весовой скорости подачи сырья и разбавления реакционной среды водяным паром на материальный баланс процесса крекинга*
Продукты селективность, конверсия | Выход продуктов, мас. % | |||||||
---|---|---|---|---|---|---|---|---|
WHSV, ч–1 | соотношение водяной пар : сырье | |||||||
1.0 | 2.5 | 5.0 | 7.0 | 0 | 0.5 | 1.45 | 2.5 | |
С1–С4-алканы | 19.20 | 17.60 | 19.70 | 19.00 | 19.70 | 17.70 | 15.50 | 15.20 |
Этилен | 11.80 | 11.40 | 11.30 | 10.00 | 11.30 | 12.10 | 12.70 | 9.10 |
Пропилен | 17.10 | 19.10 | 19.80 | 19.80 | 19.80 | 22.60 | 23.80 | 26.20 |
Бутилены | 7.80 | 9.40 | 10.50 | 11.00 | 10.50 | 10.90 | 11.20 | 12.50 |
С2–С4-олефины | 36.70 | 39.90 | 41.60 | 40.80 | 41.60 | 45.60 | 47.80 | 47.80 |
HTC | 0.20 | 0.20 | 0.20 | 0.30 | 0.20 | 0.20 | 0.10 | 0.10 |
Селективность образования C2–C4-олефинов, % | 64.00 | 67.20 | 65.70 | 67.30 | 65.70 | 71.60 | 74.30 | 75.00 |
Жидкие продукты | 42.70 | 40.60 | 36.70 | 39.40 | 36.70 | 36.30 | 35.70 | 36.30 |
– ИОЧ, ед. | 88.60 | 104.00 | 101.60 | 99.00 | 101.60 | 105.90 | 98.90 | 91.10 |
– н-парафины | 0.19 | 0.35 | 0.71 | 0.38 | 0.71 | 0.27 | 0.34 | 0.29 |
– изопарафины | 0.13 | 0.22 | 0.15 | 0.20 | 0.15 | 0.70 | 0.13 | 0.10 |
– олефины | 1.95 | 15.80 | 3.98 | 3.90 | 3.98 | 2.03 | 2.76 | 3.63 |
– нафтены | 54.05 | 26.39 | 34.80 | 43.35 | 34.80 | 25.28 | 52.69 | 83.06 |
– арены | 43.67 | 57.24 | 60.35 | 52.16 | 60.35 | 71.71 | 44.10 | 12.93 |
Селективность образования жидких продуктов, % | 74.50 | 68.40 | 58.00 | 65.00 | 58.00 | 57.00 | 55.50 | 57.00 |
Кокс | 1.40 | 1.90 | 2.00 | 0.80 | 2.00 | 1.10 | 1.00 | 0.70 |
Сумма продуктов | 100.00 | 100.00 | 100.00 | 100.00 | 100.00 | 100.00 | 100.00 | 100.00 |
Конверсия, % | 57.30 | 59.40 | 63.30 | 60.60 | 63.30 | 63.70 | 64.30 | 63.70 |
Температура оказывает влияние на выходы легких олефинов в соответствии с термодинамикой процесса. Повышение температуры от 540 до 640°C приводит к увеличению выхода более низкомолекулярных углеводородов. В результате резко возрастает выход этилена в диапазоне 590–640°С, а наибольший общий выход C2–C4-олефинов получается при температуре 640°C и составляет 43.9 мас. % (рис. 2а).
Рис. 2.
Влияние температуры (а, б), весовой скорости подачи сырья (в) и разбавления реакционной
среды водяным паром (г) на выход (диаграмма) и селективность (линия) образования легких
олефинов (◼ – этилен, – пропилен, ◻ – бутилены) и октановое число жидкого продукта крекинга. Условия процесса:
сырье – 50% циклогексана + 50% гексена-1, катализатор № 4.
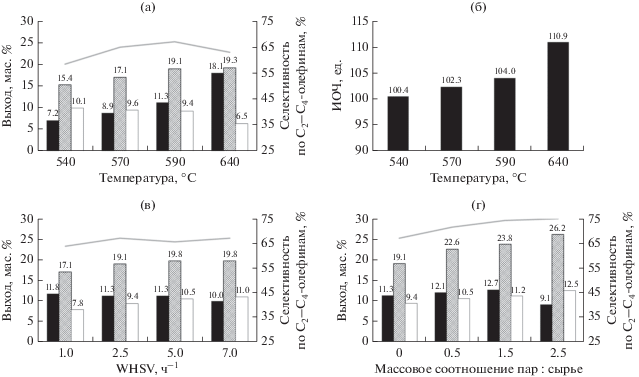
Содержание изопарафинов и ароматических углеводородов повышается с ростом температуры. Это, в свою очередь, оказывает влияние на октановое число жидких продуктов. При повышении температуры от 540 до 640°C ИОЧ увеличивается от 100.4 до 110.9 ед. (рис. 2б). При повышении температуры от 590 до 640°С общий выход С2–С4-олефинов растет незначительно по сравнению с резким ростом конверсии исходного сырья. Это указывает на наличие большого количества побочных продуктов – преимущественно C1–C4 насыщенных углеводородов. Таким образом, с точки зрения максимального значения селективности образования С2–С4-олефинов оптимальная температура крекинга составляет ~590°С.
Исследование влияния весовой скорости подачи сырья (WHSV) в диапазоне 1.0–7.0 ч–1 на состав получаемых продуктов при крекинге модельной смеси показало, что максимальный выход C2–C4-олефинов достигается при WHSV = 5 ч–1 и составляет 41.6 мас. % (рис. 2в). В данных условиях обеспечивается протекание реакции без чрезмерного коксования катализатора и достаточное время контакта сырья и катализатора. Это способствует эффективному крекингу легких углеводородов и высокой селективности процесса по легким олефинам.
Процесс крекинга сырья при соотношении водяной пар : сырье = 1.45 позволяет увеличить выход С2–С4-олефинов на 6.2 мас. % (т.е. на 14.9 отн. %) (рис. 2г). Увеличение отношения приводит к росту селективности реакций крекинга и снижению вклада реакций переноса водорода, что сопровождается увеличением содержания ненасыщенных углеводородов в газообразных продуктах и уменьшением содержания кокса. Такое же влияние разбавления реакционной среды на распределение продуктов при крекинге н-октана было показано в работе [5].
Использование водяного пара в качестве разбавителя реакционной среды приводит к уменьшению выхода кокса на катализаторе. Так, при использовании разбавления реакционной среды водяным паром (соотношение водяной пар : сырье = 1.45) содержание кокса на отработанном катализаторе снижается с 2.0 до 1.0 мас. %. При этом содержание изопарафинов и ароматических углеводородов в жидких продуктах также уменьшается, что сопровождается закономерным снижением октанового числа жидкого продукта.
Тип цеолита в моноцеолитном катализаторе
Исследование влияния типа цеолита, используемого в качестве активного компонента, на распределение продуктов при каталитическом крекинге смеси циклогексан + гексен-1 показало, что выход C2–C4-олефинов уменьшается в ряду ZSM-5 > FER > MOR > Y (рис. 3, табл. 6). Наилучший результат был получен на цеолите ZSM-5 – общий выход олефинов составил 47.7 мас. %. Основной причиной каталитических свойств цеолита этого типа является его микропористая структура, оптимальная для протекания реакций крекинга С6-углеводородов. Состав матрицы катализатора не оказывает существенного влияния на выход легких олефинов (см. табл. 6 и 7).
Рис. 3.
Влияние типа цеолита в моноцеолитных катализаторах крекинга на выход (диаграмма) и
селективность (линия) образования легких олефинов (◼ – этилен, – пропилен, ◻ – бутилены). Условия крекинга: сырье – 50% циклогексана + 50% гексена-1,
соотношение водяной пар : сырье = 1.45, WHSV = 5.0 ч–1, 590 °C.
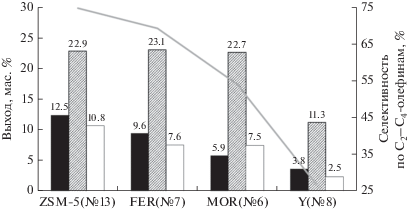
Таблица 6.
Влияние типа используемого цеолита в моноцеолитных катализаторах на материальный баланс процесса крекинга*
Продукты, селективность, конверсия | Выход продуктов, мас. % | |||
---|---|---|---|---|
тип цеолита | ||||
ZSM-5 | FER | MOR | Y | |
С1–С4-алканы | 14.50 | 11.50 | 22.00 | 36.10 |
Этилен | 12.50 | 9.60 | 5.90 | 3.80 |
Пропилен | 22.90 | 23.10 | 22.70 | 11.30 |
Бутилены | 10.80 | 7.60 | 7.50 | 2.50 |
С2–С4-олефины | 46.20 | 40.30 | 36.20 | 17.60 |
HTC | 0.10 | 0.10 | 0.90 | 3.30 |
Селективность образования C2–C4-олефинов, % | 74.90 | 69.50 | 54.30 | 27.00 |
Жидкие продукты | 38.30 | 42.00 | 33.30 | 34.80 |
– ИОЧ, ед. | 102.80 | 89.00 | 92.80 | 107.40 |
– н-парафины | 0.52 | 0.23 | 0.27 | 0.27 |
– изопарафины | 1.59 | 0.20 | 2.43 | 0.94 |
– олефины | 10.29 | 2.00 | 4.19 | 16.07 |
– нафтены | 13.06 | 90.79 | 63.30 | 2.13 |
– арены | 74.54 | 6.79 | 29.81 | 80.59 |
Селективность образования жидких продуктов, % | 62.10 | 72.40 | 49.90 | 53.40 |
Кокс | 1.00 | 6.20 | 8.50 | 11.50 |
Сумма продуктов | 100.00 | 100.00 | 100.00 | 100.00 |
Конверсия, % | 61.70 | 58.00 | 66.70 | 65.20 |
Таблица 7.
Влияние типа модуля цеолита ZSM-5 в моноцеолитных катализаторах на материальный баланс процесса крекинга*
Продукты, селективность, конверсия | Выход продуктов, мас. % | |||
---|---|---|---|---|
тип модуля цеолита ZSM-5 | ||||
30 | 55 | 80 | 300 | |
С1–С4-алканы | 30.90 | 34.40 | 36.10 | 17.60 |
Этилен | 7.30 | 8.50 | 10.70 | 11.40 |
Пропилен | 12.30 | 14.10 | 17.20 | 19.10 |
Бутилены | 4.50 | 5.60 | 5.90 | 9.40 |
С2–С4-олефины | 24.40 | 28.20 | 33.80 | 39.90 |
HTC | 0.30 | 0.30 | 0.20 | 0.20 |
Селективность образования C2–C4-олефинов, % | 43.20 | 44.30 | 47.70 | 67.20 |
Жидкие продукты | 43.40 | 36.30 | 29.10 | 40.60 |
– ИОЧ, ед. | 113.40 | 112.90 | 109.40 | 104.00 |
– н-парафины | 0.05 | 0.03 | 0.13 | 0.35 |
– изопарафины | 0.03 | 0.01 | 0.09 | 0.22 |
– олефины | 0.28 | 0.18 | 6.40 | 15.80 |
– нафтены | 1.20 | 0.19 | 14.70 | 26.39 |
– арены | 98.43 | 99.59 | 78.68 | 57.24 |
Селективность образования жидких продуктов, % | 76.80 | 57.10 | 41.00 | 68.40 |
Кокс | 1.30 | 1.10 | 1.00 | 1.90 |
Сумма продуктов | 100.00 | 100.00 | 100.00 | 100.00 |
Конверсия, % | 56.50 | 63.60 | 70.90 | 59.40 |
Существующие стерические ограничения цеолита ZSM-5 ограничивают протекание реакций переноса водорода и увеличивают селективность реакций крекинга углеводородов.
Катализаторы на основе цеолита FER имеют сходные свойства. Ограниченная диффузия молекул сырья в каналах этого цеолита способствует высокой селективности в реакциях крекинга с образованием олефинов [18]. Высокое содержание нафтенов (90.79%) в жидких продуктах указывает на низкую активность FER при крекинге относительно крупных молекул нафтенов. В моноцеолитном катализаторе FER размер каналов цеолита слишком мал.
Катализатор на основе MOR проявляет низкую активность, связанную с плохой термостабильностью этого цеолита [19].
Использование широкопористого цеолита типа Y, не имеющего стерических ограничений для реакций переноса молекулярного водорода, приводит к уменьшению выхода олефинов. Наблюдаемые результаты согласуются с данными, полученными несколькими исследователями в различных экспериментальных условиях [20–22].
Модуль цеолита ZSM-5
Исследования катализаторов крекинга на основе цеолита ZSM-5 с различными модулями (М = 30, 55, 80 и 300) показали, что увеличение модуля приводит к увеличению выхода C2–C4-олефинов (материальные балансы представлены в табл. 7). Увеличение решеточного модуля цеолита ZSM-5 сопровождается ростом его стабильности, уменьшением концентрации кислотных центров и увеличением их силы [14, 15]. В результате вероятность бимолекулярных реакций снижается, поскольку кислотные центры максимально изолированы друг от друга. Максимальный общий выход С2–С4-олефинов (39.9 мас. %) был получен на цеолите ZSM-5 с модулем 300 (рис. 4).
Модифицирование цеолита ZSM-5 фосфором
Использование различных модификаторов повышает стабильность цеолита ZSM-5 и в ряде случаев позволяет существенно увеличить выход целевых продуктов (легких олефинов). Модифицирование цеолита фосфором имеет сходный эффект с процессом деалюминирования, поэтому представляет интерес обработка низкомодульного цеолита (М = 30). Материальные балансы представлены в табл. 8. Образец цеолита с модулем 30, модифицированный фосфором, более стабилен по сравнению с исходным образцом. При модифицировании цеолита фосфором в количестве 7.7 мас. % снижается выход кокса и увеличивается выход целевых продуктов. При этом также наблюдается снижение кислотности с 920.3 до 502.5 мкмоль/г.
Таблица 8.
Влияние модифицирования низкомодульного цеолита ZSM-5 в моноцеолитных катализаторах на материальный баланс процесса крекинга*
Продукты, селективность, конверсия | Выход продуктов, мас. % | |
---|---|---|
содержание фосфора на цеолите, мас. % | ||
0 | 7.7 | |
С1–С4-алканы | 30.90 | 21.10 |
Этилен | 7.30 | 13.50 |
Пропилен | 12.30 | 20.10 |
Бутилены | 4.50 | 6.20 |
С2–С4-олефины | 24.40 | 39.80 |
HTC | 0.30 | 0.20 |
Селективность образования C2–C4-олефинов, % | 43.20 | 64.30 |
Жидкие продукты | 43.40 | 38.10 |
– ИОЧ, ед. | 113.40 | 99.40 |
– н-парафины | 0.05 | 1.37 |
– изопарафины | 0.03 | 0.18 |
– олефины | 0.28 | 14.79 |
– нафтены | 1.20 | 36.97 |
– арены | 98.43 | 46.69 |
Селективность образования жидких продуктов, % | 76.80 | 61.60 |
Кокс | 1.30 | 1.00 |
Сумма продуктов | 100.00 | 100.00 |
Конверсия, % | 56.50 | 61.90 |
Таким образом, повышение эффективности катализаторов на основе цеолита ZSM-5 при крекинге легких углеводородов может быть достигнуто при повышении модуля цеолита или путем модифицирования фосфором низкомодульных образцов. Полученный результат хорошо согласуется с работами [12, 23], которые указали на эквивалентность модифицирования цеолита фосфором и его деалюминирование. Жидкие продукты, произведенные на P-модифицированном цеолите, отличаются высоким содержанием олефинов и низким – ароматических соединений. Согласно групповому составу, продукты имеют низкое значение ИОЧ по сравнению с продуктами, полученными на немодифицированном цеолите.
Би- и трицеолитные катализаторы
Различие в свойствах микропористых структур предполагает возможность создания комбинации цеолитов, обладающей оптимальной структурой для эффективного последовательного крекинга с высоким выходом легких олефинов.
Исследование влияния состава би- и трицеолитных катализаторов на направление превращения смеси циклогексан + гексен-1 показало, что наилучший результат может быть получен при совместном использовании цеолитов ZSM-5 и FER (табл. 9). Максимальный выход олефинов достигает 50.2 мас. %. Бицеолитная каталитическая система позволяет оптимально использовать структурные особенности каждого цеолита и проводить последовательный крекинг (включая стадию димеризации) исходных молекул углеводородного сырья в соответствии со схемой: матрица → → ZSM-5 → FER.
Таблица 9.
Влияние состава би- и трицеолитных катализаторов на материальный баланс процесса крекинга*
Продукты, селективность, конверсия | Выход продуктов, мас. % | |||
---|---|---|---|---|
тип цеолита | ||||
ZSM-5 + FER | ZSM-5 + Y | FER + Y | ZSM-5 + FER + Y | |
С1–С4-алканы | 20.50 | 36.30 | 30.30 | 35.20 |
Этилен | 14.90 | 8.90 | 9.70 | 11.60 |
Пропилен | 25.00 | 18.80 | 16.60 | 20.60 |
Бутилены | 10.40 | 6.30 | 4.20 | 8.40 |
С2–С4-олефины | 50.20 | 33.90 | 30.50 | 41.30 |
HTC | 0.40 | 1.50 | 1.40 | 0.70 |
Селективность образования C2–C4-олефинов, % | 66.50 | 43.10 | 41.90 | 49.30 |
Жидкие продукты | 24.50 | 21.40 | 27.20 | 16.30 |
– ИОЧ, ед. | 103.80 | 104.70 | 95.90 | 97.10 |
– н-парафины | 0.30 | 0.38 | 0 | 0.40 |
– изопарафины | 1.81 | 0.75 | 2.67 | 0.58 |
– олефины | 2.25 | 8.98 | 0 | 8.13 |
– нафтены | 31.71 | 27.02 | 63.46 | 55.84 |
– арены | 63.93 | 62.86 | 33.87 | 35.04 |
Селективность образования жидких продуктов, % | 32.50 | 27.20 | 37.40 | 19.50 |
Кокс | 4.80 | 8.40 | 12.00 | 7.20 |
Сумма продуктов | 100.00 | 100.00 | 100.00 | 100.00 |
Конверсия, % | 75.50 | 78.60 | 72.80 | 83.70 |
Большое влияние на свойства би- и трицеолитных катализаторов оказывает комбинированная система каналов и различная концентрация кислотных центров, что позволяет использовать смесь цеолитов для достижения необходимого выхода и селективности целевых олефинов.
Трицеолитный катализатор ZSM-5 + FER + Y обеспечивает выход C2–C4-олефинов, равный 41.3 мас. % при конверсии сырья 83.7%. Этот катализатор может быть использован для процесса классического каталитического крекинга (при переработке вакуумных газойлей) с целью повышения выхода олефинов.
Из данных рис. 5 следует, что максимальные выходы легких олефинов при крекинге модельной смеси 50% циклогексана + 50% гексена-1 были получены при использовании бицеолитного катализатора с активным компонентом на основе цеолитов ZSM-5 и FER.
Рис. 5.
Влияние состава цеолитного компонента в бицеолитном катализаторе с активным компонентом на основе цеолитов ZSM-5 и FER на выход C2–C4-олефинов. Условия крекинга: сырье – 50% циклогексана + + 50% гексена-1, соотношение водяной пар : сырье = = 1.45, WHSV = 5.0 ч–1, 590°C.
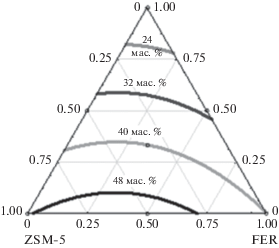
На основании состава продуктов крекинга модельной смеси на моно-, би- и трицеолитных катализаторах можно предположить следующую схему превращений исходных молекул сырья (схема 2).
Схема 2. Схема каталитического крекинга С6-углеводородов.
Исходные молекулы С6-углеводородов крекируются на цеолите ZSM-5 с образованием С2–С4-олефинов. Кроме того, за счет протекания реакций димеризации происходит образование молекул С12+-углеводородов. Большие молекулы крекируются на матрице с образованием C2–C8-углеводородов. Цеолит FER позволяет крекировать линейные н-парафины, обладающие минимальной реакционной способностью и не претерпевающие превращений на других типах цеолитов. При этом цеолит FER не обладает каталитическим действием по отношению к нафтенам и полностью исключает возможность протекания реакций переноса водорода и полимеризации [24].
По сравнению с процессом глубокого каталитического крекинга соотношения продуктов этилен : пропилен : бутилены могут быть получены в более широких диапазонах, что делает этот процесс более гибким. Так, соотношение легких олефинов составляет 1 : (1.67–3.85) : (0.62–1.40), соответственно, при каталитическом крекинге легкого сырья и может быть изменено путем варьирования состава катализатора и условий процесса.
ЗАКЛЮЧЕНИЕ
Превращение углеводородов, входящих в состав сырья, в процессе крекинга легких углеводородных фракций происходит индивидуально, без взаимодействия между компонентами. Относительно инертные углеводороды (нафтены) за счет присутствия олефинов не активируются по сравнению с процессами традиционного крекинга вакуумного газойля и безводородного каталитического облагораживания. Максимальный выход С2–С4-олефинов (54.2 мас. %) был получен при крекинге гексена-1, обладающего максимальной реакционной способностью.
Повышение температуры от 540 до 640°C приводит к увеличению выхода легких олефинов при крекинге смеси циклогексан + гексен-1 на цеолитсодержащем катализаторе. При температуре крекинга 590°С максимальная селективность процесса составляет 67.2%, а выход легких олефинов – 39.9 мас. %. Октановое число жидких продуктов также увеличивается на 10 ед. с ростом температуры в исследованном диапазоне.
Повышение соотношения водяной пар : сырье приводит к увеличению селективности реакций крекинга и снижению вклада реакций переноса водорода, что способствует повышению содержания ненасыщенных углеводородов в газообразных продуктах и уменьшению выхода ароматических углеводородов и кокса. Максимальный суммарный выход С2–С4-олефинов при этом достигает 47.7 мас. %.
Увеличение модуля цеолита ZSM-5 от 30 до 300 сопровождается повышением стабильности катализатора и выхода C2–C4-олефинов на 15.5 мас. %. Вероятность протекания бимолекулярных реакций и активность катализатора в реакциях переноса водорода снижаются с ростом модуля цеолита.
При использовании моноцеолитного катализатора (цеолит ZSM-5) в оптимальных условиях процесса выход олефинов достигает 47.7 мас. % при конверсии 78.8%. На бицеолитном катализаторе на основе цеолитов ZSM-5 и FER максимальный выход C2–C4-олефинов составил 50.2 мас. % (при конверсии 75.5%). Сочетание узкопористых цеолитов в активном каталитическом компоненте позволяет эффективно превращать легкие фракции в олефины с максимальным выходом.
Список литературы
Ясакова Е.А., Ситдикова А.В., Морозов А.Н., Ахметов А.Ф. // Технологии нефти и газа. 2011. Т. 2. С. 3.
Potapenko O.V., Doronin V.P., Sorokina T.P., Talsi V.P., Likholobov V.A. // Appl. Catal. B. Environ. 2012. V. 117–118. P. 177.
Кривых В.А., Сливкин Л.Г. // Нефтепереработка и нефтехимия. 2003. Т. 8. С. 15.
Зубер В.И., Нигматуллин Р.Г. // Нефтепереработка и нефтехимия. 2015. Т. 5. С. 17.
Je Sik Jung, Tae Jin Kim, Gon Seo // Korean J. Chem. Eng. 2004. V. 21. № 4. P. 777.
Bari Siddiqui M.A., Aitani A.M., Saeed M.R., Al-Khattaf S. // Top. Catal. 2010. V. 53. P. 1387.
Al-Shammari A.A., Ali S.A., Al-Yassir N., Aitani A.M., Ogunronbi K.E., Al-Majnouni K.A., Al-Khattaf S.S. // Fuel Process. Technol. 2014. V. 122. P. 12.
Breck D.W. Zeolite Molecular Sieves: Structure, Chemistry, and Use. Wiley, 1973. 771 p.
Rahimi N., Karimzadeh R. // Appl. Catal. A. General. 2011. V. 398. P. 1.
Liu D., Choi W.C., Lee C.W., Kang N.Y., Lee Y.J., Shin C.-H., Park Y.K. // Catal. Today. 2011. V. 164. P. 154.
Jiang G., Zhang L., Zhao Z., Zhou X., Duan A., Xu C., Gao J. // Appl. Catal. A. General. 2008. V. 340. P. 176.
Li J., Ma H., Zhang H., Sun Q., Ying W. // International J. Chemical, Molecular, Nuclear, Materials and Metallurgical Engineering. 2015. V. 9. № 5. P. 636.
Доронин В.П., Сорокина Т.П. // Рос. хим. журн. 2007. Т. 51. № 4. С. 23.
Bhattacharya D., Chaterjee M., Sivasanker S. // React. Kinet. Catal. Lett. 1997. V. 60. № 2. P. 395.
Bortnovsky O., Sazama P., Wichterlova B. // Appl. Catal. A. General. 2005. V. 287. P. 203.
Wojciechowski B.V., Corma A. Catalytic Cracking: Catalysts, Chemistry, Kinetics. N.Y.: Marcel Dekker Inc., 1986. P. 152.
Verstraete J., Coupard V., Thomazeau C., Etienne P. // Catal. Today. 2005. V. 106. P. 62.
Anderson B.G., Schumacher R.R., van Duren R., Singh A.P., van Santen R.A. // J. Mol. Catal. A. Chem. 2002. V. 181. P. 291.
Biswas J., Maxwell I.E. // Appl. Catal. 1990. V. 58. № 1. P. 1.
Buchanan J.S. // Appl. Catal. 1991. V. 74. P. 83.
Arandes J.M., Abajo I., Fernandez I., Azkoiti M.J., Bilbao J. // Ind. Eng. Chem. Res. 2000. V. 39. P. 1917.
Lu J., Zhao Z., Xu C., Duan A., Wang X., Zhang P. // J. Porous Mat. 2008. V. 15. P. 213.
Jiang G., Zhang L., Zhao Z., Zhou X., Duan A., Xu C., Gao J. // Appl. Catal. A. General. 2008. V. 340. P. 176.
Bastiani R., Lam Y.L., Henriques C.A., da Silva V.T. // Fuel. 2013. V. 107. P. 680.
Дополнительные материалы отсутствуют.
Инструменты
Кинетика и катализ