Кинетика и катализ, 2019, T. 60, № 1, стр. 108-117
Активация поверхности углеродных и азот-допированных углеродных нанотрубок нитратом кальция. Каталитические свойства кобальтнанесенных катализаторов процесса Фишера–Тропша на их основе
Е. В. Суслова 1, *, С. В. Савилов 1, А. В. Егоров 1, В. В. Лунин 1
1 ФГБОУ ВО Московский государственный университет им. М.В. Ломоносова,
Химический факультет
119991 Москва, Ленинские горы, 1, стр. 3, Россия
* E-mail: suslova@kge.msu.ru
Поступила в редакцию 05.07.2018
После доработки 28.09.2018
Принята к публикации 20.09.2018
Аннотация
Методами сканирующей и просвечивающей электронной микроскопии (СЭМ и ПЭМ), рентгеновской фотоэлектронной спектроскопии (РФЭС) и спектроскопии комбинационного рассеяния (КР) исследовано влияние концентрации, времени и режима окислительной обработки поверхности углеродных нанотрубок (УНТ) и азот-допированных УНТ (N-УНТ) в смеси с нитратом кальция. Все полученные материалы были протестированы в качестве носителей кобальтнанесенных катализаторов в процессе Фишера–Тропша (ФТ). Показано, что увеличение концентрации Ca(NO3)2 с 15 до 25 мас. % приводит к разрушению структуры УНТ, а время обработки и концентрация кислорода в окислительной смеси практически не влияют на морфологию и физико-химические характеристики материалов. Установлено, что гетерозамещение в нанотрубках и изменение рельефа поверхности углеродного носителя приводят к увеличению конверсии CO, а активность катализаторов возрастает в ряду: Co/УНТ → Co/N-УНТ → Co/УНТ(Ca) → Co/N-УНТ(Ca).
ВВЕДЕНИЕ
В настоящее время углеродные наноматериалы (УНМ) являются одними из самых перспективных носителей катализаторов самого широкого круга процессов [1, 2]. Например, в качестве носителей Co нанесенных катализаторов процесса Фишера–Тропша (ФТ) – получения жидких углеводородов из синтез-газа – описаны как неструктурированные углеродные материалы (активированные угли [3], углеродные волокна [4, 5], углеродные сферы [6], их азот-допированные аналоги [7]), так и структурированные (трубки [8], малослойные графитовые фрагменты [9, 10], графен [11] и др.). Для подобных носителей катализаторов дефектность структуры, состояние поверхности, чистота, а также преимущественное наличие мезопор оказываются чрезвычайно важными характеристиками, т.к. именно они обеспечивают однородность распределения наночастиц металла-катализатора при его нанесении и, как следствие, высокую селективность катализаторов [1].
Многостенные углеродные нанотрубки (УНТ) отвечают всем требованиям, предъявляемым к углеродным носителям катализаторов: они химически инертны, термостабильны, могут быть легко компактизованы. Как правило, для обеспечения эффективной стабилизации наночастиц кобальта на поверхности УНТ осуществляют их предварительную обработку азотной кислотой [12, 13], перекисью водорода [14, 15], допируют атомами азота [16, 17] и фосфора [18] или же осуществляют окисление поверхности уже допированных УНТ [17]. Все эти подходы приводят к образованию функциональных групп и/или дефектов на поверхности УНТ, вследствие чего нанесение металла происходит равномерно, а получаемые катализаторы процесса ФТ отличаются высокой селективностью по целевой фракции C5+ и стабильностью при работе [19]. Описанные подходы при этом нельзя считать единственно возможными. В последнее время для синтеза мезопористых углеродных наноструктур (УНС) разнообразного функционального назначения (материалы для электродов энергонакопительных устройств [20], композиционные материалы [21], адсорбенты для хроматографии и хранения газов [22] и т.д.) широко используется их физическая (обработка CO2, водяным паром или их смесями при 450°С) [23] или химическая (обработка неорганическими солями или щелочами [24]) активация. Достаточно эффективно в каталитическом гидрировании 4-хлорацетофенона показала себя модификация поверхности УНТ нитратом кальция с последующим нанесением никеля [25]. Авторы отмечают, что это привело к формированию на поверхности УНТ луковичных углеродных образований – мест дополнительной стабилизации Ni, вследствие чего катализаторы оказались более активными. Имеются сведения о применении УНТ, полученных пиролитически на (Fe,Co)/CaCO3, в качестве железонанесенных катализаторов процесса ФТ [26], а в работе [27] авторы показали, что наночастицы железа благодаря этому не мигрировали по поверхности УНТ и не спекались в процессе ФТ. Описаны также случаи постактивации поверхности УНТ, например, KOH, с последующим нанесением частиц Pd для каталитического окисления этанола [28]. Вместе с тем, данных об использовании УНТ и их азот-допированных аналогов с рельефной поверхностью в качестве носителей кобальтовых катализаторов процесса ФТ в литературе нет.
В настоящей работе впервые приготовлены кобальтнанесенные катализаторы на основе УНТ и N-УНТ с рельефной поверхностью, причем формирование данного рельефа было изучено в различных условиях. Полученные материалы протестированы в процессе ФТ; исследовано влияние микроструктуры носителя на основные каталитические характеристики.
ЭКСПЕРИМЕНТАЛЬНАЯ ЧАСТЬ
Исходные вещества и материалы
В качестве исходных веществ в работе использовали нитрат кобальта(II) шестиводный (ос. ч.), нитрат кальция четерехводный (х. ч.), нитрат магния (х. ч.), молибдат аммония (х. ч.), соляную кислоту (х. ч.), азотную кислоту (х. ч., плотность 1.4 кг/л), гексан (х. ч.), спирт этиловый (х. ч.), водород (99.99%), азот (99.999%), He (99.995%), CO (99.95%), Ar (99.999). Тетрагидрофуран (ТГФ) (х. ч.) перед применением выдерживали над гранулированным KOH (х. ч.) в течение недели, после чего фильтровали через слой Al2O3 (для хроматографии) и перегоняли над молекулярными ситами марки NaA, отбирая фракцию с Tкип = 66°С.
Методы анализа и физико-химических исследований
Морфологию и состав УНТ определяли методами сканирующей электронной спектроскопии (СЭМ) и энергодисперсионной рентгеновской спектроскопии (EDX) на приборе JEOL JSM-6390LA (“JEOL Ltd.”, Япония). Регистрацию микрофотографий проводили при ускоряющем напряжении 20–25 кВ. Методом просвечивающей электронной микроскопии (ПЭМ) исследовали структуру УНТ, N-УНТ, а также отработанных катализаторов Co/УНМ на приборе JEOL 2100F (“JEOL Ltd.”, Япония) с ускоряющим напряжением 200 кВ.
Для определения состава поверхности N-УНТ использовали рентгеновскую фотоэлектронную спектроскопию (РФЭС). Спектры регистрировали на приборе Axis Ultra DLD (“Kratos Analytical”, Великобритания) с применением монохроматического AlKα-излучения (1486.6 эВ). Обзорные РФЭ-спектры получали при энергии пропускания анализатора, равной 160 эВ, и шаге 1 эВ. Спектры высокого разрешения регистрировали с энергией пропускания анализатора 20 эВ и шагом 0.05 эВ.
Спектры комбинационного рассеяния (КР) регистрировали на спектрометре LabRam HR800 UV (“Horiba–Jobin Yvon”, Япония) с использованием возбуждения 5 мВт аргоновым лазером с длиной волны 514 нм. Для каждого эксперимента КР-спектры получали как минимум в трех точках и усредняли.
Синтез УНТ и N-УНТ
УНТ и N-УНТ синтезировали пиролитически разложением гексана и ацетонитрила, соответственно, согласно методике [9]. Перед началом синтеза MgO, пропитанный водным раствором смеси нитрата кобальта и молибдата аммония, помещали в трубчатый кварцевый реактор (диаметр 50 мм, длина 1.5 м), продували азотом со скоростью потока 200 мл/мин с одновременным повышением температуры до 750°С, после чего скорость потока N2 увеличивали до 500 мл/мин, барботируя его через гексан или ацетонитрил в течение 5 ч. Целевые продукты очищали от примесей (Co,Mo)/MgO кипячением продуктов синтезов с раствором соляной кислоты в течение 5–6 ч, фильтровали на воронке Бюхнера и сушили при 130°С в течение 10 ч. Для удаления аморфных примесей УНТ и N-УНТ отжигали при 400°C в течение 3 ч в атмосфере воздуха.
Обработка УНТ и N-УНТ нитратом кальция
Обработку нитратом кальция проводили следующим образом. К навеске УНТ или N-УНТ прибавляли раствор нитрата кальция (содержание Ca составило 15 или 25 мас. % относительно УНТ или N-УНТ) в ТГФ, после чего подвергали ультразвуковой (УЗ) обработке в течение 1 ч, растворитель упаривали на роторе, а полученные смеси сушили на воздухе при 130°С в течение 10 ч, помещали в трубчатый кварцевый реактор и нагревали в токе N2 (поток 200 мл/мин) до 500°С. При этом на поверхности УНТ протекали следующие реакции [25]:
Температуру изменяли до 450 или 720°С и продували смесь N2 : O2 с соотношением 95 : 5 или 70 : 30, соответственно, в течение 25 мин. Продукты охлаждали до комнатной температуры в токе N2, после чего кипятили в растворах соляной кислоты для удаления кальция, промывали на воронке Бюхнера до нейтрального значения pH промывных вод и сушили при 130°С в течение 10 ч. Методом EDX установлено, что ни один из образцов не содержал даже следовых количеств кальция. Обозначения образцов, условия их обработки Ca(NO3)2 ⋅ 4H2O и физико-химические характеристики представлены в табл. 1.
Таблица 1.
Обозначения образцов и условия их получения
№ | Обозначение | Массовая доля Ca, % | Tобраб, °С | Cоотношение N2 : O2 |
---|---|---|---|---|
1 | УНТ_исх | –* | –** | –** |
2 | УНТ(15Ca_450) | 15 | 450 | 70 : 30 |
3 | УНТ(15Ca_720) | 15 | 720 | 95 : 5 |
4 | УНТ(25Ca_450) | 25 | 450 | 70 : 30 |
5 | УНТ(25Ca_720) | 25 | 720 | 95 : 5 |
6 | N-УНТ_исх | –* | –** | –** |
7 | N-УНТ(15Ca_720) | 15 | 720 | 95 : 5 |
Приготовления катализаторов и синтез Фишера–Тропша
Катализаторы с содержанием кобальта 15 мас. % готовили методом пропитки носителей [9, 29]. Для этого к навескам УНТ, N-УНТ, а также УНТ, N-УНТ после их обработки нитратом кальция добавляли спиртовой раствор нитрата кобальта, обрабатывали на УЗ-бане при 60°С в течение 2 ч, выпаривали растворитель, после чего сушили при 130°С в течение 13 ч. Затем навеску катализатора 1.5–2.5 г помещали в кварцевый трубчатый реактор (диаметр 10 мм), восстанавливали в токе водорода при 400°С в течение 4 ч, охлаждали в токе водорода до 205°С и пропускали смесь с соотношением CO : H2 : N2 = 1 : 2 : 0.7 (суммарная скорость потока – 1200 ч–1, азот служил внутренним стандартом) при атмосферном давлении, продолжительность опытов составила не менее 3 сут. Определение содержания CO, CO2 и углеводородов в продуктах осуществляли на газовом хроматографе Agilent 6890N (“Agilent”, США), снабженном колонкой DB5 и пламенно-ионизационным детектором для разделения и количественного анализа углеводородов и колонкой HayeSep с сорбентом порапак R для разделения и анализа N2, CO, CO2, CH4. Расчет выходов продуктов осуществляли в соответствии с методикой [29]. В составе фракций C5+ определены углеводороды С5–C15 включительно. Отработанные катализаторы для дальнейшего их исследования методом ПЭМ пассивировали смесью 1% O2/Ar при комнатной температуре.
РЕЗУЛЬТАТЫ И ОБСУЖДЕНИЕ
Физико-химические характеристики УНТ и N-УНТ до и после окислительной обработки нитратом кальция
Морфологию полученных УНТ и N-УНТ исследовали методами СЭМ и ПЭМ. Толщина УНТ, по данным СЭМ, составила 14–17 нм, при этом сами УНТ были спутаны в агломераты ~5 мкм (рис. 1а). Толщина внутреннего канала по данным ПЭМ была равна 7–12 нм, а количество углеродных слоев, параллельных внутреннему каналу, 6–10 (рис. 1б). По результатам СЭМ толщина N-УНТ была 15–20 нм (рис. 1в). N-УНТ имели типичную для азот-допированных УНТ бамбукообразную структуру, характеризующуюся множественными перемычками во внутренних каналах (рис. 1г). Подобная особенность обусловлена напряжением, возникающим из-за встраивания атомов азота в графеновые плоскости: для минимизации поверхностной энергии графеновые слои деформируются и изгибаются [30].
На примере обработки УНТ нитратом кальция выявлены изменения характеристик препаратов в зависимости от концентрации Ca и температуры последующего окислительного отжига. С увеличением содержания кальция от 15 до 25 мас. % в обрабатываемых смесях происходило существенное изменение морфологии образцов УНМ: появлялись “рваные” дефекты вследствие разрушения структуры нескольких верхних слоев УНТ, что было подтверждено методом ПЭМ (рис. 2а–2г), на фоне существенной деградации исходной структуры УНТ. Отметим, что температура и соотношение N2 : O2 в составе окислительной смеси оказали меньшее влияние на природу поверхности УНТ.
Рис. 2.
Микрофотографии ПЭМ образцов УНТ(15Ca_450) (а), УНТ(15Ca_720) (б), УНТ(25Ca_450) (в), УНТ(25Ca_720) (г), N-УНТ (15Ca_720) (д).
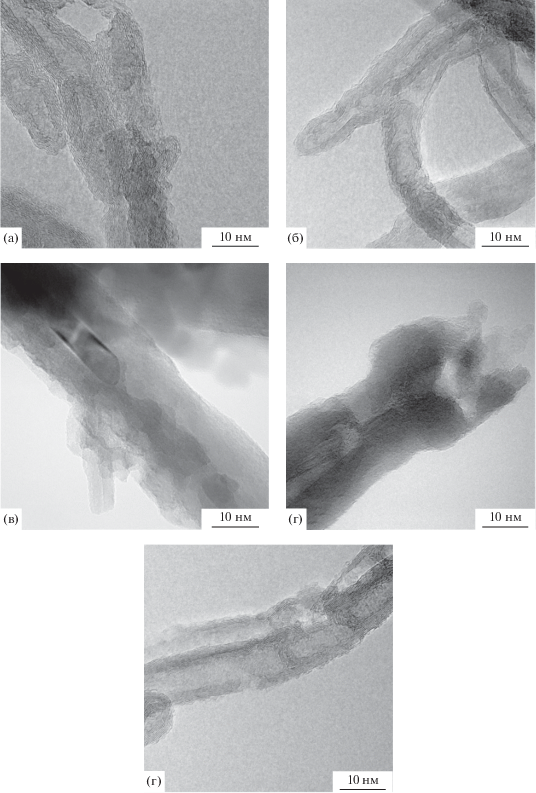
В случае N-УНТ при окислительной конверсии морфология меняется менее значительно (рис. 2г, 2д). Вместе с тем, при обработке N-УНТ существенно модифицируется состав поверхностных графеновых слоев. Согласно данным РФЭС содержание азота после обработки в образце N-УНТ(15Ca_720) уменьшилось с 1.58 до 1.02 ат. % (рис. 3а). Нельзя исключать, что частично к такому результату привело термическое воздействие. Ранее было установлено, что в результате обработки N-УНТ при 1000°С заметно снижается количество азота в составе N-УНТ, что авторы [31] связали с элиминированием молекулярного азота, инкапсулированного между слоями N-УНТ, и азота в пиридиновом состояниях. В РФЭ-спектрах N1s, полученных для наших препаратов, можно выделить пять основных состояний азота: пиридиновый с энергиями 390.1–399.3 эВ, пиррольный (399.8–401.5 эВ), замещающий (401.1–402.7 эВ), оксиды азота (>402.6 эВ) [32], и азот, инкапсулированный между слоями (404.3 эВ) [33]. Азот в этих состояниях присутствует в N-УНТ как до, так и после обработки, а их относительное соотношение практически не меняется (рис. 3б).
Рис. 3.
а – РФЭ-спектры N1s образцов N-УНТ и N-УНТ(15Ca_720); б – соотношение содержания атомов азота в N‑УНТ до и после обработки.
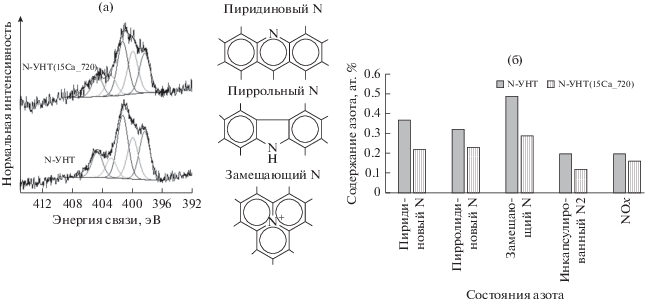
В качестве объемной характеристики всех изучаемых УНС можно использовать данные КР-спектроскопии. В КР-спектре углеродных наноматериалов присутствуют, как правило, три основных линии: G-линия в области 1550–1600 см–1, характеризующая тангенциальные C–C-колебания, и D-линия в диапазоне 1250–1350 см–1 и G '-линия в области 2700 см–1, соответствующие асимметричным колебаниям С–С-связей в области дефектов в структуре УНМ [34]. КР-спектры УНТ и N-УНТ до и после их обработки 15 мас. % Ca(NO3)2 практически не изменились, соотношение интенсивностей (I) D- и G-пиков несколько уменьшилось, а соотношение интенсивностей G'- и G-пиков увеличилось как для УНТ, так и для N‑УНТ, что свидетельствует о совершенствовании структуры (рис. 4). Ранее Чои с соавторами [31] получил подобные результаты: соотношение ID/IG N-УНТ до и после термической обработки при 1000°С осталось почти неизменным.
Характеристики кобальтнанесенных катализаторов процесса Фишера–Тропша
Все синтезированные катализаторы исследованы в процессе ФТ при атмосферном давлении и 205°С. Были рассчитаны конверсия СО, активность и селективность образования различных продуктов (табл. 2).
Таблица 2.
Конверсия CO и селективность в присутствии кобальтнанесенных катализаторов
Катализатор | Конверсия CO, % | Активность, ${\text{м о л }}{{{\text{ь }}}_{{{{{\text{C}}}_{{{\text{5 + }}}}}}}}$ c–1${\text{г }}_{{{\text{Co}}}}^{{ - 1}}$ × 10–6 | Селективность | |||
---|---|---|---|---|---|---|
CO2 | CH4 | C2–C4 | C5+ | |||
15Co/УНТ* | 4.6 | 0.70 | 6.3 | 18.5 | 13.6 | 61.6 |
15Co/УНТ(15Ca_720) | 11.1 | 1.51 | 4.3 | 20.0 | 8.0 | 69.0 |
15Co/N-УНТ | 13.3 | 2.01 | 7.5 | 16.3 | 8.7 | 67.5 |
15Co/N-УНТ(15Ca_720) | 12.9 | 2.11 | 5.2 | 28.1 | 13.9 | 53.5 |
Примечание. Условия реакции: Т = 205°С, атмосферное давление. *Результаты, ранее опубликованные в [29].
Конверсия CO возросла почти в 2.5 раза в случае модификации поверхности УНТ кальцием (катализаторы 15Co/УНТ и 15Co/УНТ(15Ca_720)) и незначительно уменьшилась при кальциевой обработке N-УНТ (катализаторы 15Co/N-УНТ и 15Co/N-УНТ(15Ca_720)). Отметим, что оба подхода – введение в состав углеродных слоев гетероатомов азота и модификация поверхности УНТ нитратом кальция – привели к существенному повышению конверсии CO. Известно [35, 36], что при увеличении дефектности углеродного носителя, чему, в частности, способствует тубулярная структура УНТ, возрастает количество валентно ненасыщенных атомов углерода, которые участвуют в хемосорбции молекул реагентов. Предложенный в настоящей работе подход как раз направлен на повышение дефектности поверхности.
Активность катализаторов росла как при введении азота, так и при обработке нитратом кальция носителей. Наиболее активным оказался катализатор 15Co/N-УНТ(15Ca_720), при этом значения конверсии CO в присутствии всех трех катализаторов 15Co/УНТ(15Ca_720), 15Co/N-УНТ и 15Co/N-УНТ(15Ca_720) были близки, а минимальной селективностью по целевой фракции C5+ обладал катализатор 15Co/N-УНТ(15Ca_720).
Селективность катализаторов сильно зависит от размера и узости распределения частиц металла [15, 37]. На рис. 5 приведены микрофотографии ПЭМ всех катализаторов процесса ФТ. Отметим, что добиться узкого распределения частиц Co по размерам не удалось ни в одном случае. Во всех образцах присутствовали как частицы диаметром 1–2 нм, так и более крупные агломераты (30–50 нм). Катализатор 15Co/УНТ представлял собой смесь частиц Co размером 6–15 нм, которые находились в порах и пустотах между УНТ (рис. 5а). При использовании УНТ без каких-либо модификаций частицы металла-катализатора слабо взаимодействуют с гидрофобной углеродной поверхностью УНТ, мигрируют и спекаются в процессе ФТ, что заметно ухудшает каталитические характеристики катализаторов [38], однако при слишком сильном взаимодействии, которое достигается, например, высокой дисперсией Co на поверхности УНТ со значительным содержанием кислородсодержащих групп, оказывается, что Co не кристаллизуется и вообще не катализирует процессы восстановительной конверсии CO и CO2 [9, 39]. Для стабилизации нaнoчастиц Co или других металлов на поверхности УНТ, как правило, модифицируют поверхность УНТ, а именно вводят кислородсодержащие группы [5, 40], однако при работе катализатора часть этих групп элиминируется с поверхности УНТ, что приводит к деградации катализатора [40].
Рис. 5.
Микрофотографии ПЭМ кобальтнанесенных отработанных и пассивированных катализаторов 15Co/УНТ (а), 15Co/УНТ(15Ca_720) (б), 15Co/N-УНТ (в), 15Co/N-УНТ(15Ca_720) (г).
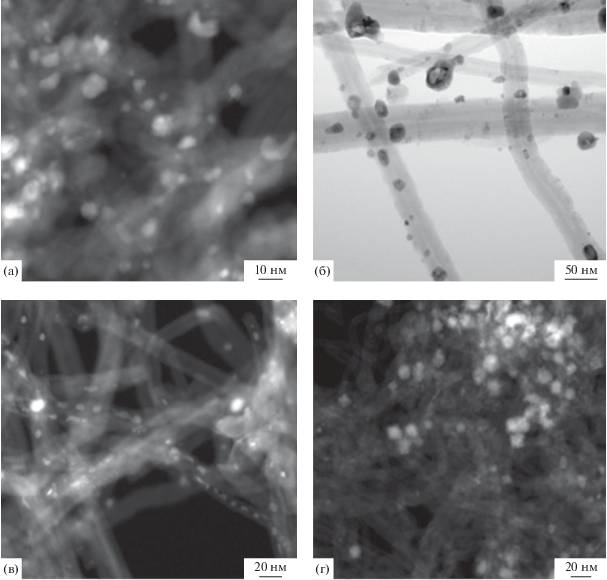
Одной из главных задач при исследовании и оптимизации катализаторов, нанесенных на носители, можно считать поиск баланса между взаимодействием металла-катализатора с носителем и количеством активных центров. При введении атомов азота удается значительно повысить гидрофильность поверхности [41] и добиться существенно большей дисперсии частиц Co или других металлов на поверхности [16, 18, 42–45]. Например, в работе [16] размер частиц Co, диспергированных на поверхность окисленных азотной кислотой УНТ, составил 16.2 нм, а при введении атомов азота дополнительно к окислению поверхности – 5.4 нм. Атомы азота в различных состояниях по-разному участвуют в стабилизации частиц металла. Неподеленная пара электронов в пиррольном азоте в структуре N-УНТ включена в сопряжение π-системы и, следовательно, ее компонента никак или слабо (если принимать во внимание электроноизбыточность цикла) влияет на стабилизацию частиц Co в катализаторе. Неподеленная электронная пара в пиридиновом азоте и нескомпенсированный заряд в замещающем азоте создают дополнительные места координации и стабилизации Co (рис. 3а). Исходя из этого предположения становится очевидно, почему при уменьшении общего содержания азота в носителе от 1.58 ат. % для N-УНТ до 1.02 ат. % для N-УНТ(Ca) снизилась конверсия CO (табл. 2). В настоящем исследовании размер частиц Co в составе катализатора 15Co/N-УНТ составил ~5 нм, часть из них была инкапсулирована внутрь каналов (рис. 5в). Подобные результаты ранее описаны как в случае Co, так и Fe каталитически активных частиц, инкапсулированных внутрь каналов УНТ и N-УНТ [16, 36, 46, 47]. Отметим, что катализатор 15Co/N-УНТ(15Ca_720) практически не содержал инкапсулированного кобальта, дисперсия Co по поверхности была выше, чем у остальных исследованных катализаторов (рис. 5г). Вероятно, это связано с большей концентрацией кислорода на поверхности носителя N-УНТ(15Ca_720) вследствие окисления оксидами азота поверхности N-УНТ при обработке нитратом кальция. По данным РФЭС, образец N-УНТ содержал на поверхности 1.54 ат. % кислорода, а N-УНТ(Ca) – 1.65 ат. %.
На поверхности УНТ и N-УНТ после обработки нитратом кальция частицы Co размером 1–2 нм стабилизированы в том числе и в местах “рваных” дефектов (рис. 5б, 5г). Можно предположить, что именно такие частицы способствуют сильному увеличению активности катализатора, что ранее установлено в исследовании [27]. В настоящей работе именно в присутствии катализаторов 15Co/УНТ(15Ca_720) и 15Co/N-УНТ(15Ca_720) наблюдалась наибольшая селективность по метану. Отметим, что в работе [16] был установлен повышенный выход метана в присутствии катализатора, нанесенного на азот-допированные УНТ, по сравнению с катализатором на основе окисленных азотной кислотой УНТ. Снижение конверсии CO в присутствии катализатора 15Co/N-УНТ(15Ca_720) по сравнению с 15Co/N-УНТ, вероятно, связано с образованием агломератов кобальта (рис. 5г) и, как следствие, с уменьшением количества активных центров. Катализатор 15Co/УНТ(15Ca_720) оказался наиболее селективным по целевой фракции C5+ из всех образцов, исследованных в настоящей работе. Селективность по CO2 выше на 31–32% для обоих обработанных Ca(NO3)2 носителей катализаторов 15Co/УНТ(15Ca_720) и 15Co/N-УНТ(15Ca_720) по сравнению с их необработанными аналогами. При этом для катализаторов 15Co/УНТ(15Ca_720), 15Co/N-УНТ и 15Co/N-УНТ(15Ca_720) селективность по CO2 увеличивалась с ростом конверсии CO. Такие же результаты ранее получены в работах [37, 48] и могут быть объяснены повышением выхода воды – одного из продуктов гидрирования CO, которая затем вступает в реакцию конверсии водяного газа (РКВГ).
ЗАКЛЮЧЕНИЕ
В заключение необходимо отметить, что реакция ФТ структурно-чувствительная [49] и зависит практически от всех физико-химических параметров катализаторов и их носителей. В настоящей работе было показано, как гетерозамещение в структуре УНТ на атомы азота, а также химическая активация поверхностей УНТ и N-УНТ нитратом кальция с последующей окислительной термической обработкой влияют на каталитические параметры кобальтнанесенных катализаторов. При обоих подходах удалось добиться увеличения активности катализаторов.
БЛАГОДАРНОСТИ
Авторы выражают благодарности к.х.н. С.А. Черняку и к.ф.-м.н. К.И. Маслакову за получение СЭМ-изображений и спектров РФЭС, а также к.х.н. А.С. Иванову за ценные замечания и обсуждение. Работа выполнена при финансовой поддержке Российского Научного фонда (проект № 18-13-00217) и с использованием оборудования, приобретенного за счет средств Программы развития Московского университета.
Список литературы
Su D.S., Perathoner S., Centi G. // Chem. Rev. 2013. V. 113. P. 5782.
Fu T., Li Z. // Chem. Eng. Sci. 2015. V. 135. P. 3.
Fu T., Lv J., Li Z. // Ind. Eng. Chem. Res. 2014. V. 53. P. 1342.
Xiong H., Motchelaho M.A.A., Moyo M., Jewell L.L., Coville N.J. // Catal. Today. 2013. V. 214. P. 50.
Bezemer G., Bitter J., Kuipers H., Oosterbeek H., Holewijn J., Xu X., Kapteijn F., Dillen F., Jong K. // J. Am. Chem. Soc. 2006. V. 128. P. 3956.
Díaz J.A., Romero A., García-Minguillán A.M., Giroir-Fendler A., Valverde J.L. // Fuel Proc. Technol. 2015. V. 138. P. 455.
Yang Y., Jia L., Hou B., Li D., Wang J., Sun Y. // J. Phys. Chem. C. 2014. V. 118. P. 268.
Trépanier M., Dalai A.K., Abatzoglou N. // Appl. Catal. A. 2010. V. 374. P. 79.
Суслова Е.В., Черняк С.А., Егоров А.В., Савилов С.В., Лунин В.В. // Кинетика и катализ. 2015. Т. 56. № 5. С. 655.
Karimi S., Tavasoli A., Mortazavi Y., Karimi A. // Chem. Eng. Res. Design. 2015. V. 104. P. 713.
Karimi S., Tavasoli A., Mortazavi Y., Karimi A. // Appl. Catal. A. 2015. V. 499. P. 188.
Xiong H., Motchelaho M., Moyo M., Jewell L., Coville N. // J. Catal. 2011. V. 278. P. 26.
Trépanier M., Tavasoli A., Dalai A.K., Abatzoglou N. // Fuel Proc. Technol. 2009. V. 90. P. 367.
Davari M., Karimi S., Tavasoli A., Karimi A. // Appl. Catal. A. 2014. V. 485. P. 133.
Karimi A., Nasernejad B., Rashidi A.M., Tavasoli A., Pourkhalil M. // Fuel. 2014. V. 117. №. P. 1045.
Fu T., Li Z. // Catal. Commun. 2014. V. 47. P. 54.
Fu T., Liu R., Lv J., Li Z. // Fuel Proces. Technol. 2014. V. 122. P. 49.
Savilov S., Ivanov A., Suslova E., Egorov A., Antonov P., Lunin V. // Adv. Mat. Res. 2012. V. 364. P. 444.
Tavasoli A., Nakhaeipour A., Sadaghiani K. // Fuel Process. Technol. 2007. V. 88. P. 461.
Pagketanang T., Artnaseaw A., Wongwich P., Thabuot M. // Ener. Proc. 2015. V. 79. P. 651.
Ihsan M., Meng Q., Li L., Li D., Wang H., Seng K., Chen Z., Kennedy S., Guo Z., Liu H. // Electrochim. Acta. 2015. V. 173. P. 172.
Labus K., Gryglewicz S., Machnikowski J. // Fuel. 2014. V. 118. P. 9.
Frakowiak E., Beguin F. // Carbon. 2001. V. 39. P. 937.
Souza L., Wickramaratne N., Ello A., Costa M., Costa C., Jaroniec M. // Carbon. 2013. V. 65. P. 334.
Landau M., Savilov S., Ivanov A., Lunin V., Titelman L., Koltypin Y., Gedanken A. // J. Mater. Sci. 2011. V. 46. P. 2162.
Motchelaho M., Xiong H., Moyo M., Jewell L., Coville N. // J. Mol. Catal. A. 2011. V. 335. P. 189.
Graham U.M., Dozier A., Khatri R.A., Bahome M.C., Jewel L.L., Mhlanga S.D., Coville N.J., Davies B.H. // Catal. Lett. 2009. V. 129. P. 39.
Dong W., Xia W., Xie K., Peng B., Muhler M. // Carbon. 2017. V. 121. P. 452.
Chernyak S., Suslova E., Egorov A., Lu L., Savilov S., Lunin V. // Fuel Proc. Technol. 2015. V. 140. P. 267.
Podyacheva O., Ismagilov Z. // Catal. Today. 2015. V. 249. P. 12.
Choi H., Park J., Kim B. // J. Phys. Chem. B. 2005. V. 109. P. 4333.
Wang H., Maiyalayan T., Wang X. // ACS Catal. 2012. V. 2. P. 781.
Liu H., Zhang Y., Li R., Sun X., De’silets S., Abou-Rachid H., Jaidann M., Lussier L.S. // Carbon. 2010. V. 48. P. 1498.
Dresselhaus M.S., Dresselhaus G., Saito R., Jorio A. // Phys. Rep. 2005. V. 409. P. 47.
Rodriguez-Reinoso F. // Carbon. 1998. V. 36. P. 159.
Chen W., Fan Z., Pan X., Bao X. // J. Am. Chem. Soc. 2008. V. 130. P. 9414.
Черняк С.А., Селяев Г.Е., Суслова Е.В., Егоров А.В., Маслаков К.И., Харланов А.Н., Савилов С.В., Лунин В.В. // Кинетика и катализ. 2016. Т. 57. С. 645.
Tavasoli A., Trepanier M., Dalai A., Abatzoglou N. // J. Chem. Engineer. Data. 2010. V. 55. P. 2757.
Chernyak S., Suslova E., Egorov A., Maslakov K., Savilov S., Lunin V. // Appl. Surf. Sci. 2016. V. 372. P. 100.
Chernyak S.A., Suslova E.V., Ivanov A.S., Egorov A.V., Maslakov K.I., Savilov S.V., Lunin V.V. // Appl. Catal. A. 2016. V. 523. P. 221.
Ayala P., Arenal R., Rümmeli M., Rubio A., Pichler T. // Carbon. 2010. V. 48. P. 575.
Bae G., Youn D.H., Han S., Lee J.S. // Carbon. 2013. V. 51. P. 274.
Lu J., Yang L., Xu B., Wu Q., Zhang D., Yuan S., Zhai Y., Wang X., Fan Y., Hu Z. // ACS Catal. 2014. V. 4. P. 613.
Xiong H., Motchelaho M., Moyo M., Jewell L., Coville N. // Appl. Catal. A. 2014. V. 482. P. 377.
Li Z., Liu R., Xu Y., Ma X. // Appl. Surf. Sci. 2015. V. 347. P. 643.
Trépanier M., Tavasoli A., Anahid S., Dalai A. // Iran. J. Chem. Chem. Eng. 2011. V. 30. P. 37.
Xing C., Yang G., Wang D., Zeng C., Jin Y., Yang R., Suehiro Y., Tsubaki N. // Catal. Today. 2013. V. 215. P. 24.
Tavasoli A., Sadagiani K., Khorashe F., Seifkordi A.A., Rohani A.A., Nakhaeipour A. // Fuel Proc. Technol. 2008. V. 89. P. 491.
Khodakov A. // Catal. Today. 2009. V. 144. P. 251.
Дополнительные материалы отсутствуют.
Инструменты
Кинетика и катализ