Кинетика и катализ, 2021, T. 62, № 6, стр. 733-743
Каталитические и структурные свойства поверхностных слоев кобальта, формирующихся в процессе автоколебательных реакций
В. Ю. Бычков a, *, Ю. П. Тюленин a, А. Я. Горенберг a, А. А. Гулин a, В. Н. Корчак a
a ФГБУН ФИЦ химической физики им. Н.Н. Семенова РАН
119991 Москва, ул. Косыгина, 4, Россия
* E-mail: bychkov@chph.ras.ru
Поступила в редакцию 29.03.2021
После доработки 26.05.2021
Принята к публикации 19.06.2021
Аннотация
В результате протекания реакции окисления этана (I) или СО (II) на Со-фольге в автоколебательных
режимах при температурах 620 и 660°С соответственно в течение 1 ч на поверхности фольги
образуется микропористый слой, состоящий из кристаллов СоО размером 0.2–0.4 мкм. В
случае (I) эти кристаллы формируют агломераты размером ~1 мкм, между которыми существуют
поры такого же размера. Толщина микропористого слоя после обработки I типа составляет
~0.7 мкм. После обработки II типа агломераты и поры практически отсутствуют. Измерена
каталитическая активность образцов фольги с такими слоями в реакциях глубокого окисления
этилена, окисления СО, метанирования СО. Показано, что максимальный прирост активности
происходит после обработки I типа. Изучена устойчивость полученных пористых слоев
в инертной (Не), восстановительной (Н2) или окислительной (О2) атмосфере при нагреве до 750°С. В первом случае происходит значительная перекристаллизация
слоя и его растрескивание. После нагрева в водороде образуется слой, прочно связанный
с подложкой и имеющий стабильную каталитическую активность. Наконец, в результате
нагрева в окислительной среде толщина поверхностного слоя увеличивается до 6–8 мкм,
в составе преобладает оксид Со3О4, и его каталитическая активность минимальна по сравнению с первыми двумя образцами.
Графический
реферат
Конверсия этилена при его окислении на исходной Со-фольге (интервал времени 0–60 мин)
и фольге после автоколебательной обработки (интервал 60–120 мин) I или II типа.
ВВЕДЕНИЕ
Кобальт является катализатором различных реакций, включая глубокое или парциальное окисление углеводородов [1–3], углекислотную или паровую конверсию [4, 5], синтез Фишера–Тропша [6–8], разложение закиси азота [9], окисление СО [10] и избирательное окисление СО [11, 12], разложение метанола [13] и др. Приготовление образцов металлического кобальта с развитой поверхностью может представлять интерес с точки зрения получения катализаторов, сочетающих в себе высокую каталитическую активность благодаря большой площади доступной поверхности, относительно быстрый теплообмен через металлическую основу массивных систем и низкое сопротивление газовому потоку образцов, изготовленных на основе фольги или проволоки.
Известно, что каталитическое окисление низших углеводородов [14–17] и СО [18] на металлическом кобальте в форме фольги или проволоки может протекать в автоколебательном режиме. Также было показано, что поверхность кобальта существенно разрыхляется в результате этих реакций [14, 18]. В этом отношении металлический кобальт похож на никель, свойства которого в автоколебательных реакциях изучены более подробно [15, 19–21]. В работах [22, 23] мы изучили влияние автоколебательного режима процесса окисления метана на Ni-фольге на формирование развитого поверхностного слоя и его каталитическую активность в реакциях углекислотной конверсии метана (УКМ) и гидрирования этилена. Методом сканирующей электронной микроскопии (СЭМ) было обнаружено, что такая обработка Ni-фольги в условиях автоколебательного окисления метана (далее, для краткости, автоколебательная обработка) действительно приводит к формированию рыхлого поверхностного слоя, каталитическая активность которого на порядок превышает активность исходной Ni-фольги.
В случае кобальта влияние автоколебательной обработки на каталитические свойства и морфологию поверхности ранее подробно не изучалось. Поэтому в настоящей работе была поставлена задача провести подобные исследования. Автоколебательные режимы мы наблюдали в интервале 860–950°С для реакции окисления метана [16], 600–650°С для окисления этана [17] и 450–800°С для окисления СО [18]. Две последние реакции мы посчитали более перспективными с точки зрения развития поверхности кобальта, так как автоколебания в окислении метана происходят при температурах, когда можно ожидать снижение удельной поверхности катализаторов из-за спекания поверхностных кристаллитов. Исходя из вышесказанного, в представленной работе были выбраны два типа автоколебательной обработки:
I) каталитическое окисление этана в смеси 75% С2Н6–25% О2 (20 мл/мин) при 620°С в течение 1 ч;
II) каталитическое окисление СО в смеси 40% СО–10% О2–Не (20 мл/мин) при 660–680°С в течение 1 ч.
Изменение каталитической активности кобальта после автоколебательной обработки тестировали в реакциях углекислотной конверсии метана (УКМ), глубокого окисления этилена, избирательного окисления СО в избытке водорода, метанирования СО. Кроме того, морфологию поверхности кобальта в разных состояниях изучили с помощью сканирующей электронной микроскопии (СЭМ).
ЭКСПЕРИМЕНТАЛЬНАЯ ЧАСТЬ
Опыты проводили с образцами Со-фольги размером 5.5 × 8 × 0.1 мм. Анализ газообразных реагентов и продуктов выполняли с помощью масс-спектрометра Omnistar (“Pfeiffer”, Германия) или хроматографа Кристалл-2000 (Хроматэк, Россия). Каталитические эксперименты осуществляли в проточном кварцевом реакторе (внутренний диаметр – 6 мм) при атмосферном давлении. Образец фольги помещали в вертикально расположенный реактор параллельно направлению течения газа, не деформируя образец. Температуру реактора измеряли снаружи, температуру фольги отдельно не измеряли.
Автоколебательные режимы каталитической реакции получали при пуске на образцы смеси 75% С2Н6–25% О2 (20 мл/мин) при 620°С (обработка I типа в течение 1 ч) или в смеси 40% СО–10% О2–Не (20 мл/мин) при 660–680°С (обработка II типа в течение 1 ч). Автоколебания скорости реакции фиксировали по колебаниям состава газовой смеси на выходе из реактора с помощью масс-спектрометра OmniStar GSD 301 или по колебаниям температуры катализатора с помощью термопары. Кроме того, о наличии автоколебаний можно было судить по периодическому изменению цвета поверхности Со-фольги между светлым металлическим и черным.
Каталитическую активность тестировали в реакциях углекислотной конверсии метана (смеси 50% СН4–50% СО2, 15 мл/мин, 750°С), глубокого окисления этилена (2% С2Н4–15% О2–Не, 20 мл/мин, 650°С), избирательного окисления СО в избытке водорода (2% СО–2% О2–96% Н2, 20 мл/мин, 200–350°С), метанирования СО (6.45% СО–93.55% Н2, 20 мл/мин, 200–400°С). Концентрации газовых реагентов и продуктов находили с помощью газового хроматографа “Кристалл 2000м”. Интервал времени перед первым измерением в каждом опыте составлял 5 мин.
Морфологию исходной Со-фольги и образцов фольги после различной обработки изучали с помощью сканирующего электронного микроскопа JSM-7001F (“JEOL”, Япония) или Thermo Scientific Prisma E (“Thermo Fisher Scientific”, США).
Фазовый состав определяли с помощью рентгеновского дифрактометра Smartlab SE (“Rigaku”, Япония) с излучением CuKα. При измерениях шаг сканирования был 0.005°, скорость сканирования – 5°/мин. Для нахождения фазового состава образцов полученные дифрактограммы сравнивали с дифрактограммами контрольных образцов, содержащих только фазы Со, СоO или Со3О4. Образец Со3О4 готовили прокаливанием нитрата кобальта на воздухе при 500°С, образец СоО – прокаливанием Со3О4 в потоке инертного газа при 900°С. Достоверность фаз подтверждали табличными данными из базы данных Rigaku для Со, СоО, Со3О4.
Величину площади доступной поверхности оценивали с помощью метода, позволяющего измерить количество кислорода, хемосорбированного на поверхности металла. Для этого использовали термовесы SETSYS Evolution (“Setaram Instrumentation”, Франция). Образец фольги Со после автоколебательной обработки помещали в термовесы, восстанавливали в потоке водорода до температуры 350°С, охлаждали до 100°С и окисляли в потоке смеси 4% О2–Не в течение 30 мин. Затем окисленный образец восстанавливали в потоке Н2 в режиме программированного нагрева (10°/мин, 30 мл/мин) и определяли снижение веса образца за счет восстановления оксида кобальта. Применимость такого метода описана нами ранее [16].
РЕЗУЛЬТАТЫ И ОБСУЖДЕНИЕ
Параметры автоколебаний
Типичные колебания концентраций реагентов и продуктов в автоколебательной реакции окисления этана показаны на рис. 1. Цикл колебаний состоит из фазы с относительно высокой скоростью окисления этана и последующей фазы с относительно низкой скоростью реакции. В первой фазе основными продуктами являются СО и Н2, а во второй – СО2 и Н2О. Период колебаний составляет от долей минуты до нескольких минут в зависимости от температуры реакции. В ходе автоколебаний химический состав поверхности катализатора меняется от восстановленного металлического состояния (фаза с высокой скоростью реакции) до окисленного состояния, при котором поверхность фольги покрыта темным слоем оксида кобальта (фаза с низкой скоростью реакции). Более подробно автоколебания в данной реакции были изучены в работе [17].
Рис. 1.
Колебания концентраций компонентов реакционной смеси при окислении этана на Со при 600°С (C2H6 : O2 : : Ar = 17.5 : 7.5 : 1, 30 мл/мин). Цифры рядом с формулами соединений означают смещения кривых относительно оси Y.
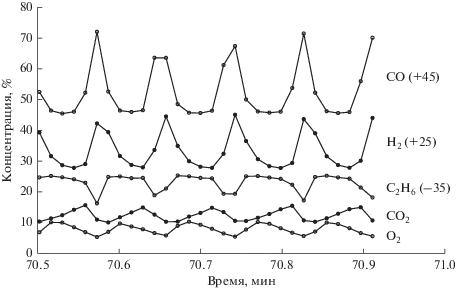
На рис. 2 показаны типичные колебания концентраций при окислении СО на Со-фольге при температуре 700°С. Также можно наблюдать периодическую смену интервалов с относительно высокой и низкой скоростью окисления СО, обусловленную периодическим окислением и восстановлением поверхности металла. Колебания в этой реакции менее регулярные и частые по сравнению с колебаниями в реакции окисления этана. Более детально свойства таких колебаний рассмотрены в статье [18].
Влияние автоколебательной обработки на каталитическую активность
Как было указано выше, в качестве тестовых каталитических реакции пробовали реакции углекислотной конверсии метана (УКМ), глубокого окисления этилена, избирательного окисления СО в избытке водорода, метанирования СО. Каталитическая активность наших образцов в реакции УКМ оказалась мала, и подробно ее не изучали. Каталитическую активность в окислении этилена измеряли в смеси 2% С2Н4–15% О2–Не при температуре 650°С. На рис. 3 показано, как изменяется величина конверсии этилена от времени в эксперименте, в котором сначала тестировали исходную Со-фольгу (0–60 мин на шкале времени), затем образец фольги подвергали автоколебательной обработке I типа в течение 1 ч и далее снова тестировали окисление этилена (интервал времени 60–120 мин). Начальная конверсия этилена составляет 11.3%, постепенно растет в течение 1 ч и стабилизируется при значении ~22.9%. После автоколебательной обработки конверсия этилена повышается на порядок и затем постепенно снижается.
Рис. 3.
Конверсия этилена при его окислении на исходной Со-фольге (интервал времени 0–60 мин) и фольге после автоколебательной обработки (интервал 60–120 мин) I или II типа.
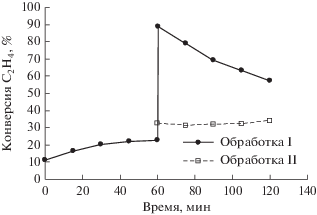
Проведено сравнение конверсии этилена на кобальте после автоколебательной обработки I или II типа в течение 1 ч (рис. 3). Видно, что обработка II (реакция окисления СО) приводит к гораздо меньшему приросту конверсии этилена (до 32–34%) по сравнению с обработкой I (реакция окисления этана). Однако активность кобальта после II практически не меняется со временем в течение 1 ч.
В табл. 1 показаны результаты тестирования исходной Со-фольги и Со-фольги после автоколебательной обработки I типа в течение 1 ч в реакции избирательного окисления СО. Образцы катализаторов продували потоком смеси 2% СО–2% О2–96% Н2 в условиях ступенчатого повышения температуры в интервале 200–350°С. Исходная фольга имеет нулевую каталитическую активность, тогда как образец после автоколебательной обработки демонстрирует заметную активность при температуре ≥ 300°С. Однако в этом температурном интервале происходит также существенное окисление Н2 и метанирование СО, т.е. окисление СО не является избирательным.
Таблица 1.
Концентрация СО2 при реакции смеси 2% СО–2% О2–96% Н2 с исходным образцом Со-фольги и образцом Со-фольги после автоколебательной обработки (АО) I типа*
Температура, °С | Концентрация СО2, % | |
---|---|---|
исходная фольга | после АО | |
200 | 0 | 0 |
300 | 0 | 0.14 |
350 | 0 | 0.15 |
В табл. 2 приведены концентрации метана, образующегося при реакции смеси 6.45% СО–93.55% Н2 с исходной Со-фольгой и образцом Со-фольги после автоколебательной обработки I типа в течение 1 ч. Исходная фольга имеет нулевую активность в интервале температур 200–400°С. В присутствии образца после автоколебательной обработки СН4 образуется в заметных количествах при 350–400°С, причем концентрация его при 400°С ниже, чем при 350°С. Концентрация метана довольно быстро уменьшается со временем при обеих температурах (рис. 4), падая в 2–3 раза через 10 мин после достижения температуры реакции. Повторная автоколебательная обработка полностью восстанавливает начальную каталитическую активность.
Исследование морфологии поверхности
Морфологию поверхности Со-фольги изучали с помощью СЭМ. На рис. 5а–5в представлены СЭМ-изображения Со-фольги до и после автоколебательной обработки I или II типа в течение 1 ч. Видно, что относительно гладкая поверхность исходной фольги после автоколебательной обработки превращается в микропористую поверхность, состоящую из кристаллитов размером 0.2–0.4 мкм. В случае автоколебательной обработки I типа (рис. 5б) эти кристаллиты компонуются в более крупные агломераты ~1 мкм, между которыми наблюдаются поры, уходящие в глубину образца. Очевидно, именно такое развитие поверхности кобальта вызывает увеличение его каталитической активности. Причиной образования описанной микропористой структуры являются многочисленные периодические процессы восстановления/окисления поверхности в ходе автоколебательных режимов каталитических реакций. В случае автоколебательной обработки II типа (рис. 5в), кристаллиты имеют такой же размер, но образуют гораздо более ровный слой без крупных агломератов и пор между ними. Это объясняет тот факт, что автоколебательная обработка I типа дает гораздо больший рост каталитической активности кобальта, чем обработка II типа (рис. 3). Причиной может быть сильное различие между периодами автоколебаний в ходе окисления этилена при 620°С (обработка I типа) и окисления СО при 660°С (обработка II типа): ~0.1 мин и ~1 мин соответственно. Вероятно, больший период колебаний говорит о более медленных процессах окисления/восстановления поверхностного слоя, что может давать более “упорядоченную” структуру рекристаллизованного слоя.
Рис. 5.
СЭМ-изображения фольги Со: исходной (а) и после автоколебательной обработки I (б) или II (в) типа в течение 1 ч.
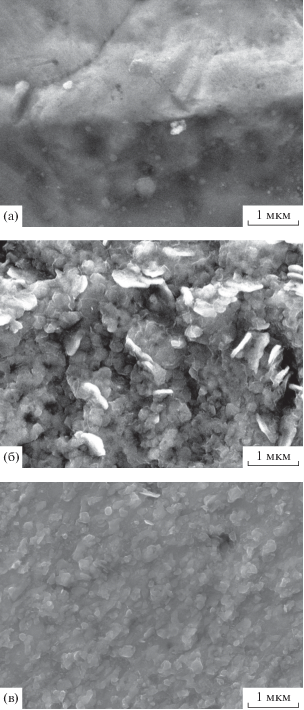
На рис. 6а приведено СЭМ-изображение поперечного излома фольги Со после автоколебательной обработки I типа (образец на рис. 5б). Видно, что толщина пористого слоя на поверхности составляет ~0.7 мкм. Данный пористый слой не очень прочно удерживается на поверхности металлического кобальта и может отслаиваться при поперечном изломе/разрезе фольги (рис. 6б). Это отличает поверхностный слой на Со-фольге от аналогичного слоя, возникающего на Ni-фольге при автоколебательной обработке (рис. 6в), который гораздо прочнее связан с металлом и практически не трескается при изломе образца.
Исследование фазового состава поверхностного слоя
На рис. 7 показаны дифрактограммы исходной Со-фольги, а также образцов после автоколебательной обработки I и II типа в течение 1 ч. Исходная фольга представляет собой смесь гексагольной и кубической фаз кобальта. После автоколебательной обработки обнаружено небольшое количество оксида кобальта СоО. Другие оксиды кобальта найдены не были. Таким образом, можно заключить, что пористый поверхностный слой образцов на рис. 5б, 5в и 6а состоит из кристаллов СоО.
Определение площади доступной поверхности
Величину площади доступной поверхности пористого слоя оценивали путем измерения количества кислорода, хемосорбированного на предварительно восстановленной поверхности кобальта при температуре 100°С. Принято считать [24], что в этих условиях на поверхности металла образуется примерно монослойное покрытие из оксида металла. Образовавшийся поверхностный оксид восстанавливали в термовесах водородом и измеряли уменьшение веса за счет удаления кислорода из образца. Для Со-фольги после автоколебательной обработки I типа в течение 1 ч полученная величина составляет 7.4 мкг. Оценка количества хемосорбированного кислорода, исходя из площади геометрической поверхности образца фольги Со (~1 см2), дает величину 0.027 мкг. Таким образом, площадь доступной поверхности микропористого слоя (~270 см2), сформировавшегося на Со-фольге в результате автоколебательной обработки I типа, на два порядка превышает площадь геометрической поверхности фольги. Эксперименты показали также, что площадь поверхности этого слоя снижается после прогрева образца в потоке Н2 1 ч при 500, 700 или 900°С до величин 50, 30 и 20% соответственно от начального значения, что позволяет оценить термостабильность пористого слоя.
Исследование влияния различных газовых сред
Было изучено, как влияют различные газовые среды на каталитические свойства и морфологию поверхностного слоя Со, образовавшегося при автоколебательной обработке. Для этого образцы Со после автоколебательной обработки I типа выдерживали при температуре 750°С в потоке гелия, Н2 или смеси 4% О2–Не в течение 1 ч. Затем образцы охлаждали до 650°С и тестировали каталитическую активность в реакции окисления этилена. Результаты тестирования показаны на рис. 8. Видно, что во всех случаях нахождение фольги при температуре 750°С в потоке газов приводит к снижению начальной величины конверсии этилена на 34% (поток инертного газа), 26% (поток водорода) или 54% (поток смеси О2–Не). Образцы, обработанные в гелии и кислороде, продолжали терять каталитическую активность во времени, тогда как образец, обработанный в водороде, демонстрировал практическую постоянную активность в течение 1 ч.
Рис. 8.
Конверсия этилена при его окислении в смеси 2% С2Н4–15% О2–Не (650°С, 20 мл/мин) на Со-фольге: исходной (5), после автоколебательной обработки I типа (1) и после автоколебательной обработки и последующего ее выдерживания в потоке водорода (2), гелия (3) или смеси 4% О2–Не (4) при 750°С в течение 1 ч.
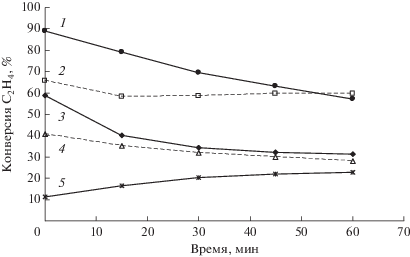
Микроснимки на рис. 9–11 показывают изменение морфологии поверхностного слоя после различных обработок. После выдерживания в потоке гелия поверхностный слой растрескивается и рекристаллизуется (рис. 9). При большом увеличении видно, что он состоит из хорошо ограненных кристаллов размером 0.1–0.2 мкм, плотно прилегающих друг к другу. Дифрактограмма на рис. 12 указывает на присутствие оксида кобальта СоО в данном образце. Интенсивности пиков, соответствующих Со, значительно превышают интенсивности аналогичных пиков для образца сразу после автоколебательной обработки (рис. 7).
Рис. 9.
СЭМ-изображения Со-фольги после автоколебательной обработки I типа и ее последующего отжига при 750°С в потоке гелия (a, б).
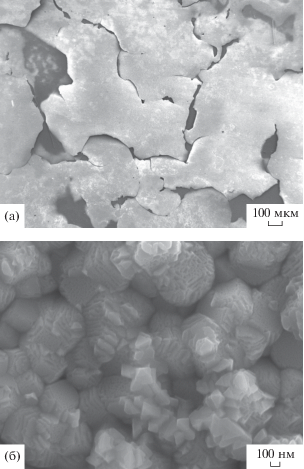
Рис. 10.
СЭМ-изображения Со-фольги после автоколебательной обработки I типа и ее последующего отжига при 750°С в потоке водорода (a, б).
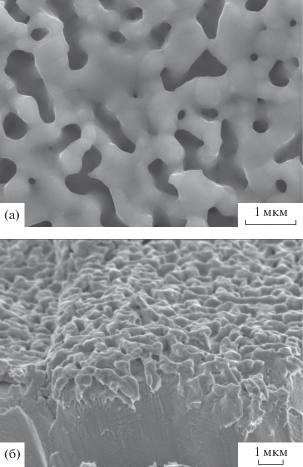
Рис. 11.
СЭМ-изображения Со-фольги после автоколебательной обработки I типа и ее последующего отжига при 750°С в потоке смеси 4% О2–Не (a, б).
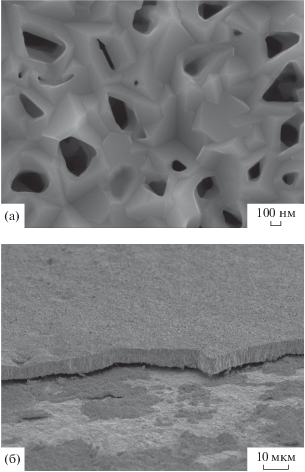
Рис. 12.
Дифрактограммы Со-фольги: исходной (1) и после автоколебательной обработки I типа с последующим выдерживанием при 750°С в Не (2) и смеси 4% О2–Не (3).
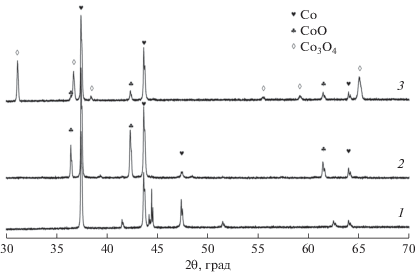
Напротив, после обработки в водороде формируется пористый слой, прочно удерживающийся на массивном кобальте (рис. 10). Его толщина составляет ~1 мкм, а по своей структуре он напоминает “пенометалл”, имеющий поры размером 0.2–1 мкм. Именно такой слой демонстрирует стабильную высокую каталитическую активность в окислении этилена (рис. 8).
Наконец, после выдерживания в кислородсодержащей смеси на поверхности фольги образуется плотный слой толщиной 6–8 мкм (рис. 11), состоящий из хорошо ограненных кристаллов размером 0.3–0.6 мкм, между которыми остаются поры таких же размеров. Данный слой не очень прочно соединяется с металлической основой и при изломе образца может отслаиваться. По результатам рентгеновского анализа (рис. 12) образец содержит значительное количество Со3О4 и относительно небольшое количество СоО и обладает наименьшей каталитической активностью в окислении этилена.
ЗАКЛЮЧЕНИЕ
В результате проведения реакций окисления этилена (I) или СО (II) на кобальтовой фольге в автоколебательном режиме на поверхности фольги формируется микропористый слой, состоящий из кристаллов СоО размером 0.2–0.4 мкм. В первом случае эти кристаллы компонуются в агломераты размером ~1 мкм, между которыми существуют поры такого же размера. Толщина микропористого слоя после обработки I типа составляла ~0.7 мкм. После обработки II типа агломераты и поры практически отсутствуют. Показано, что возникновение такого пористого слоя приводит к росту каталитической активности кобальта в реакциях глубокого окисления этилена, окисления СО и метанирования СО, причем максимальный прирост активности наблюдался после обработки I типа. Изучена устойчивость полученных пористых слоев при их нагреве до 750°С в инертной (Не), восстановительной (Н2) или окислительной (О2) атмосфере. В первом случае происходит значительная перекристаллизация слоя и его растрескивание. После нагрева в водороде образуется слой, прочно связанный с подложкой и имеющий стабильную каталитическую активность. Наконец, после нагрева в окислительной среде толщина поверхностного слоя увеличивается до 6–8 мкм, в его составе преобладает оксид Со3О4, а каталитическая активность минимальна по сравнению с первыми двумя образцами.
Список литературы
Choya A., de Rivas B., Gonzalez-Velasco J.R., Gutierrez-Ortiz J.I., Lopez-Fonseca R. // Appl. Catal. A: General. 2019. V. 582. P. 117099.
Moral A., Reyero I., Llorca J., Bimbela F., Gandia L.M. // Catal. Today. 2019. V. 333. P. 259.
Исупова Л.А., Куликовская Н.А., Сапутина Н.Ф., Герасимов Е.Ю. // Кинетика и катализ. 2018. Т. 59. № 4. С. 474.
Tuti S., Pepe F. // Catal. Lett. 2008. V. 122. P. 196.
Osaki T. // Кинетика и катализ. 2019. Т. 60. № 6. С. 797.
Маркова М.Е., Гавриленко А.В., Степачева А.А., Молчанов В.П., Матвеева В.Г., Сульман М.Г., Сульман Э.М. // Кинетика и катализ. 2019. Т. 60. № 5. С. 624.
Суслова Е.В., Савилов С.В., Егоров А.В., Лунин В.В. // Кинетика и катализ. 2019. Т. 60. № 1. С. 108.
Яковенко Р.Е., Зубков И.Н., Нарочный Г.Б., Папета О.П., Денисов О.Д., Савостьянов А.П. // Кинетика и катализ. 2020. Т. 61. № 2. С. 278.
Иванова Ю.А., Сутормина Е.Ф., Исупова Л.А. // Кинетика и катализ. 2020. Т. 61. № 4. С. 577.
Bae J., Shin D., Jeong H., Kim B.-S., Han J.W., Lee H. // ACS Catal. 2019. V. 9. P. 10093.
Grzybek G., Ciura K., Gryboś J., Indyka P., Davó-Quiñonero A., Lozano-Castelló D., Bueno-Lopez A., Kotarba A., Sojka Z. // J. Phys. Chem. C. 2019. V. 123. P. 20221.
Zhong L., Kropp T., Baaziz W., Ersen O., Teschner D., Schlögl R., Mavrikakis M., Zafeiratos S. // ACS Catal. 2019. V. 9. P. 8325.
Chen J., Guo Q., Wu J., Yang W., Dai D., Chen M., Yang X. // J. Phys. Chem. C. 2019. V. 123. P. 9139.
Zhang X.L., Lee C.S.-M., Mingos D.M.P., Hayward D.O. // Appl. Catal. A: General. 2003. V. 248. P. 129.
Zhang X.L., Lee C.S.-M., Mingos D.M.P., Hayward D.O. // Catal. Today. 2005. V. 105. P. 283.
Bychkov V.Yu., Tyulenin Yu.P., Slinko M.M., Korchak V.N. // Appl. Catal. A: General. 2007. V. 321. P. 180.
Bychkov V.Yu., Tyulenin Yu.P., Slinko M.M., Korchak V.N. // Catal. Lett. 2007. V. 119. P. 339.
Bychkov V.Yu., Tulenin Yu.P., Slinko M.M., Gorenberg A.Ya., Shashkin D.P., Korchak V.N. // React. Kinet. Mech. Catal. 2019. V. 128. P. 587.
Bychkov V.Yu., Tyulenin Yu.P., Korchak V.N., Aptekar E.L. // Appl. Catal. A: General. 2006. V. 304. P. 21.
Kaichev V.V., Teschner D., Saraev A.A., Kosolobov S.S., Gladky A.Yu., Prosvirin I.P., Rudina N.A., Ayupov A.B., Blume R., Hovecker M., Knop-Gericke A., Schlogl R., Latyshev A.V., Bukhtiyarov V.I. // J. Catal. 2016. V. 334. P. 23.
Сараев A.A., Косолобов С.С., Каичев В.В., Бухтияров В.И. // Кинетика и катализ. 2015. Т. 56. № 5. С. 606.
Bychkov V.Yu., Tulenin Yu.P., Slinko M.M., Sokolov S., Korchak V.N. // Catal. Lett. 2017. V. 147. P. 1019.
Бычков В.Ю., Тюленин Ю.П., Горенберг А.Я., Корчак В.Н. // Кинетика и катализ. 2021. Т. 62. № 1. С. 120.
Benson J.E., Boudart M. // J. Catal. 1965. V. 4. № 6. P. 704.
Дополнительные материалы отсутствуют.
Инструменты
Кинетика и катализ