Кинетика и катализ, 2022, T. 63, № 1, стр. 77-85
Технология получения водорода и углеродных нановолокон из природного газа
В. В. Чесноков *
ФГБУН ФИЦ Институт катализа им. Г.К. Борескова СО РАН
630090 Новосибирск, просп. Акад. Лавреньева, 5, Россия
* E-mail: chesn@catalysis.ru
Поступила в редакцию 25.08.2021
После доработки 07.09.2021
Принята к публикации 07.09.2021
- EDN: LJVNHO
- DOI: 10.31857/S0453881122010014
Аннотация
Рассмотрена технология получения водорода и углеродных нановолокон из природного газа. Для достижения высоких конверсий метана разработан катализатор, который активно и стабильно работает при температурах 700–750°С. С помощью электронной микроскопии и рентгенофазового анализа исследован генезис его фазового состава. Модифицирование катализатора 75%Ni–12%Cu/Al2O3 оксидом железа приводит к образованию тройного Ni–Cu–Fe-сплава. Разработанный метод получения водорода эффективно работает не только при использовании в качестве исходного сырья метана, но и природного газа. Установка с вращающимся реактором для получения водорода и углеродных нановолокон из природного газа позволяет проводить процесс на катализаторе 70%Ni–10%Cu–10%Fe/Al2O3 в течение 20–30 ч. Концентрация водорода на выходе из реактора превышает 70 мол. %. Выход водорода с одного грамма катализатора достигает 590 литров.
ВВЕДЕНИЕ
Европейской комиссией принят 11 декабря 2019 г. [1] зеленый пакт для Европы (European Green Deal). Этот план предусматривает достижение нулевого нетто-выброса парниковых газов и нулевого суммарного загрязнения окружающей среды в странах-членах Европейского союза к 2050 г. Переход к жизни в обществе без выбросов парниковых газов требует системных изменений в области получения и использования энергии, а также пересмотра подхода к переработке доступных природных ресурсов. Для решения проблем, возникающих для России от начала реализации Зеленого пакта для Европы, необходимо активно развивать водородную энергетику.
Хотя водород является очень распространенным на нашей планете элементом, его молекула недоступна на Земле в изолированном виде. Производство водорода возможно из богатых водородом молекул, например, воды или углеводородов. Известно несколько способов получения водорода.
Электролиз достаточно известный и хорошо изученный процесс [2]. Водород образуется в ходе реакции:
Чистая вода практически не проводит ток, поэтому к ней прибавляют электролиты (обычно КОН). При электролизе на катоде выделяется водород, а на аноде – эквивалентное количество кислорода, который, следовательно, в этом методе является побочным продуктом. Получающийся при электролизе водород очень чист, если не считать примеси небольших количеств кислорода, который легко удалить пропусканием газа над палладийсодержащем катализатором. Его называют “зеленым водородом” [3], поскольку здесь в процессе не участвует углерод, и CO2 не образуется непосредственно.
Другой способ производства водорода – газификация угля в присутствии водяного пара при температурах 800–900°С [4]. Получающийся газ содержит до 60% водорода в смеси с оксидом углерода.
Реакция газификации угля идет по уравнению:
На сегодняшний день основным промышленным способом производства водорода является паровой риформинг метана (природного газа) [5]. Этот процесс включает реакцию каталитической конверсии метана в парах воды при 700–1000°С с образованием синтез-газа:
(III)
$\begin{gathered} {\text{С}}{{{\text{Н}}}_{4}} + {{{\text{Н}}}_{{\text{2}}}}{\text{О}} \to {\text{ СО}} + 3{{{\text{Н}}}_{2}} \\ (\Delta Н^\circ = 214.5{\text{ кДж/моль}}) \\ \end{gathered} $(IV)
$\begin{gathered} {\text{СО}} + {{{\text{Н}}}_{{\text{2}}}}{\text{О}} \to {\text{С}}{{{\text{О}}}_{2}} + {{{\text{Н}}}_{2}} \\ (\Delta Н^\circ = --41.5{\text{ кДж/моль}}).~ \\ \end{gathered} $Затем следует стадия очистки водородсодержащего газа от СО2.
Существенным недостатком данного процесса, помимо его сложности и наличия большого числа стадий, является загрязнение атмосферы значительными выбросами СО2. По оценкам специалистов суммарное количество СО2 в отходящих газах достигает 0.35–0.45 м3 на 1 м3 водорода [6]. Стоимость водорода, получаемого паровой конверсией метана, для небольших производств (не более 100 кг водорода в день) оценивается в 2–2.5 доллара за кг Н2 [6–8].
В настоящее время мировое производство водорода из ископаемого топлива оценивается в 48, 30 и 18% соответственно из природного газа, нефти и угля [9]. Только 4% водорода вырабатывается из возобновляемых источников [10].
Энергия, необходимая для образования водорода из воды или углеводородов, показана на рис. 1. Соответственно, удельная стоимость водорода, получаемого из угля, природного газа или нефти, значительно ниже, чем из воды [11].
Традиционные методы синтеза водорода имеют свои недостатки. Электролиз воды – процесс дорогостоящий. Водород, производимый газификацией угля и паровой конверсией, требует очистки от оксидов углерода, которые являются ядами для катализаторов гидрирования и катализаторов в топливных элементах. Расходы на очистку образующегося водорода повышают его стоимость.
Разрабатываются также другие способы производства водорода, такие как паровой риформинг глюкозы, паровой риформинг метанола, парциальное окисление спиртов [12]. Ведутся работы по фотокаталитическим методам получения водорода из биомассы и воды [13, 14]. Но внедрение этих технологий в промышленность ограничивается высокими энергетическими затратами и образованием большого количества побочных продуктов, поэтому наиболее перспективными направлениями являются каталитические методы синтеза водорода из углеводородов [15–23].
В последние годы появляется все больше работ [16, 17, 23], посвященных высокотемпературному пиролизу метана без доступа кислорода. Для достижения значительных скоростей реакции и степеней превращения метана в отсутствие катализатора требуются температуры 1000−1200°C и выше [24, 25]. Такие высокие рабочие температуры необходимы, так как молекула метана обладает симметричной молекулярной структурой и прочными C–H-связями. Для снижения температуры реакции и увеличения выхода водорода были разработаны различные неметаллические катализаторы, в качестве которых, как правило, используются углеродные материалы.
Основная идея в этом подходе заключается в превращении углеводородов в водород и полезные углеродсодержащие вещества или материалы посредством их прямого пиролиза по общему уравнению баланса:
Для пиролиза метана с образованием водорода и сажи (x = 1, y = 4) общий баланс выглядит следующим образом:
Неучастие кислорода в процессе предотвращает появление CO2, но при этом происходит формирование большого количества твердого углерода, для которого должно быть применение. В настоящее время такой рынок невелик по сравнению с рынком энергии.
Расшифрованный механизм карбидного цикла разложения углеводородов на углерод и водород [26, 27] позволяет получать углерод в виде углеродных наноматериалов. Раскрытие этого механизма открывает перспективы создания процесса производства водорода, в котором вместо обычной сажи происходит образование углеродных нановолокон или углеродных нанотрубок. В принципе в качестве исходного сырья можно использовать различные парафиновые и некоторые непредельные углеводороды. Однако экономически наиболее целесообразно синтезировать водород из метана (или природного газа).
При получении чистого водорода по механизму карбидного цикла разложения метана на углерод и водород необходимо снизить концентрацию метана в образующейся газовой смеси, ориентируясь на зависимость равновесной концентрации метана от температуры в реакции. На рис. 2 представлена зависимость константы равновесия реакции (VI) и равновесной концентрации водорода от температуры с учетом поправок на неидеальность формирующегося графита [28].
Рис. 2.
Зависимости равновесной концентрации водорода и константы равновесия реакции разложения метана на углерод и водород от температуры.
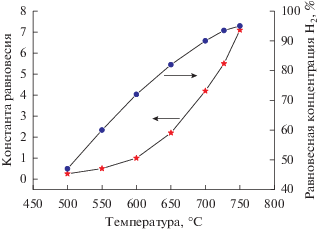
Из рис. 2 следует, что для снижения равновесной концентрации метана необходимо повышать температуру реакции. При температурах 700−750°С можно достигнуть 70−80% конверсии метана.
Первые попытки реализовать каталитический процесс были сделаны еще в начале 90-х гг. [29]. Были разработаны высокопроцентные катализаторы 85−90%Ni/MgO и 85−90%Ni/Al2O3, в которых частицы оксида алюминия или магния, равномерно распределенные между частицами никеля, уменьшают число контактов между металлическими частицами и предотвращают их спекание. Экспериментальные исследования показали, что катализаторы Ni/MgO и Ni/Al2O3 имеют высокую каталитическую активность и стабильность в реакции разложения метана при температурах 550−600°С. Важной характеристикой работы катализаторов является их способность накапливать углерод при сохранении каталитической активности. Высокопроцентные катализаторы способны накапливать до 100 г углерода на 1 г (гС/гкат) катализатора при выходе водорода, соответствующем стехиометрии реакции (VI). Однако равновесные степени превращения метана при 550−600°С не превышают 30%. Подъем температуры реакции разложения метана на водород и углерод до 650°С приводит к быстрой дезактивации катализаторов Ni/Al2O3 и Ni/MgO. Съем углерода (масса углерода, отнесенная к массе исходного катализатора) с 1 г катализатора понижается больше чем на порядок.
Известно [30], что углеродные нановолокна растут на высокодисперсных частицах никеля по механизму карбидного цикла. Массоперенос атомов углерода происходит путем их диффузии через объем металлических частиц от места образования к центрам кристаллизации. Из механизма карбидного цикла вытекает, что диффузия атомов углерода происходит под действием градиента концентраций. Этот градиент весьма велик. Наличие высокого пересыщения на передней стороне металлической частицы, контактирующей с газовой фазой, делает систему неустойчивой [31]. Значительно улучшить работу никелевых катализаторов удалось за счет промотирующих добавок, в качестве которых часто использовали медь и палладий [32]. Эти металлы имеют одинаковую кристаллографическую структуру с никелем и легко образуют сплавы. Сами по себе промоторы не активны в каталитической реакции разложения метана на углерод и водород. Их роль в никелевых катализаторах заключается в создании баланса между скоростями диссоциации метана на металлической поверхности и диффузии атомов углерода через объем сплавной частицы. Добавка меди к никелевому катализатору уменьшает скорость диссоциации метана на поверхности сплава и увеличивает скорость диффузии углерода. Таким образом, модификация системы Ni/Al2O3 медью позволяет работать каталитической установке при более высоких температурах без быстрой дезактивации катализатора.
Цель настоящей работы – разработка основных элементов для создания технологии получения водорода и углеродных нановолокон из природного газа. В частности, будет синтезирован катализатор, рассмотрена экспериментальная установка для проведения процесса и режимы ее работы.
ЭКСПЕРИМЕНТАЛЬНАЯ ЧАСТЬ
Катализаторы готовили механохимической активацией (МХА) смеси оксидов (Fe2O3, NiO, CuO) с гидроксидом алюминия (гидраргиллитом) в центробежной планетарной мельнице АГО-2 (ЗАО “Новиц”, Россия) при скорости вращения барабанов 10 с–1. Были приготовлены катализаторы следующих составов: 75%Ni–12%Cu/Al2O3, 70%Ni–10%Cu–10%Fe/Al2O3.
Эксперименты по зауглероживанию катализаторов проводили в проточном кварцевом реакторе. Реактор был оснащен микровесами Мак-Бена, что позволяло следить за изменением массы образца непосредственно в ходе реакции и строить кинетические зависимости [33]. Навеска образца катализатора изменялась в интервале 0.01–0.2 г. Образец в начале эксперимента нагревали в токе водорода (10 л/ч) до требуемой температуры. Затем прекращали подачу водорода и добавляли метан (3 л/ч).
В рамках создания технологии получения водорода и углеродных наноматериалов разработана проточная пилотная установка с вращающимся реактором непрерывного действия [34]. Объем реактора составляет 250 см3. Во время проведения реакции разложения природного газа реактор вращался вокруг своей оси со скоростью 1 об./мин. Установка изображена на фотографии (рис. 3) и схеме (рис. 4).
Рис. 4.
Схема установки с вращающимся реактором для получения водорода и углеродных наноструктур: 1 – емкость для углеродного продукта; 2 – электропечь; 3 – корпус реактора; 4 – камера загрузки; 5 – привод (мотор-редуктор, зубчатая пара); 6 – вал полый; 7 – узел сильфонный; 8 – трубка, d = 10 мм; 9 – трубка, d = 16 мм; 10 – карман термопарный; 11 – рама; 12 – гайка.
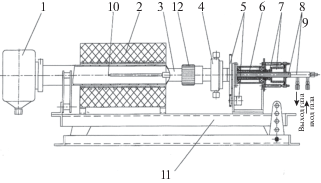
В установку с вращающимся реактором загружали катализатор. После продувки реактора аргоном (30 л/ч) в течение 10 мин катализатор восстанавливали в потоке 25% H2/Ar при нагревании до 700°С. Затем прекращали подачу H2/Ar-смеси и включали подачу природного газа. Состав газовой смеси на входе и выходе из реактора определяли с помощью газовой хроматографии. Конверсию метана (х) рассчитывали из формулы:
где ${{{\text{С}}}_{{{{{\text{H}}}_{{\text{2}}}}}}}$ – концентрация водорода на выходе из реактора.Использовавшийся в работе метан имел чистоту 99.92 об. %, аргон – 99.7 об. %. Природный газ состоял на 97% из метана, остальное – алканы С2 и С3. Для очистки от паров воды и серосодержащих примесей природный газ пропускали через цеолит CaA.
Рентгенографическое исследование образцов проводили на дифрактометре D-500 (“Siemens”, Германия). Использовано монохроматизированное излучение CuKα (графитовый монохроматор на отраженном пучке).
Образцы изучали методом просвечивающей электронной микроскопии высокого разрешения (ПЭМВР) на приборе JEM-2010 (“JEOL”, Япония) с ускоряющим напряжением 200 кВ и разрешением 0.14 нм.
РЕЗУЛЬТАТЫ И ИХ ОБСУЖДЕНИЕ
Получение водорода и углеродных нановолокон на Ni–Cu-катализаторах
Как следует из ранее проведенных исследований, катализаторы Ni–Cu/Al2O3 обладают высокой активностью и достаточно хорошей стабильностью в реакции разложения метана на водород и углеродные нановолокна. Поэтому вначале были изучены каталитические свойства этих систем в вышеуказанной реакции при различных температурах. В табл. 1 представлены данные о влиянии состава катализатора и температуры реакции разложения метана на выход углерода. В соответствие со стехиометрией реакции (VI) выход водорода (по массе) в три раза меньше, чем выход углерода.
Таблица 1.
Зависимость выхода углерода от состава катализатора и температуры в реакции разложения метана
Состав катализаторов, мас. % | Т, °С | Выход углерода, гС/гкат |
---|---|---|
75%Ni–12%Cu/Al2O3 | 550 | 43 |
75%Ni–12%Cu/Al2O3 | 600 | 88 |
75%Ni–12%Cu/Al2O3 | 650 | 76 |
75%Ni–12%Cu/Al2O3 | 700 | 50 |
70%Ni–10%Cu–10%Fe/Al2O3 | 700 | 150 |
70%Ni–10%Cu–10%Fe/Al2O3 | 725 | 152 |
70%Ni–10%Cu–10%Fe/Al2O3 | 750 | 140 |
Из табл. 1 видно, что для катализатора 75%Ni––12%Cu/Al2O3 оптимальные температуры для проведения реакции разложения метана составляют 600–650°С. Следовательно, Ni–Cu/Al2O3-катализаторы разложения метана стабильно работают при более высоких температурах, чем Ni/Al2O3-катализаторы. Однако, как показали термодинамические оценки, для получения высоких конверсий метана необходимо иметь оптимальные рабочие температуры 700–750°С (рис. 2).
На рис. 5 представлена электронно-микроскопическая фотография углеродных нановолокон, образовавшихся из метана на катализаторе 75%Ni–12%Cu/Al2O3 при температуре 750°С. Углеродные нановолокна имеют стопчатое строение. Слои графита расположены перпендикулярно оси роста нановолокна.
Рис. 5.
Электронно-микроскопическая фотография углеродных нановолокон, образовавшихся из метана на катализаторе 75%Ni–12%Cu/Al2O3 при температуре 700°С.
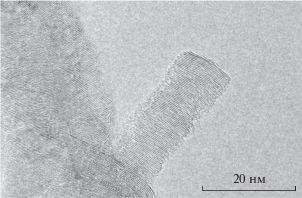
Добавка железа снижает градиент концентраций углерода в каталитически активной частице как за счет уменьшения скорости распада метана на лобовой стороне металлической частицы, так и за счет увеличения скорости отвода атомов углерода от лобовой стороны металлической частицы. Коэффициент диффузии атомов углерода через объем металлического железа почти на три порядка больше коэффициента диффузии через объем металлического никеля, что должно приводить к повышению скорости диффузии атомов углерода через объем сплавной частицы.
Проведены рентгеноструктурные исследования катализаторов 85%Ni/Al2O3, 75%Ni–‒12%Cu/Al2O3 и 70%Ni–10%Cu–10%Fe/Al2O3 после 30 мин работы в разложении метана при температуре 700°С. На рентгенограмме 85%Ni/Al2O3 катализатора наблюдаются рефлексы, относящиеся к фазам графита и металлического никеля (рис. 6).
Рис. 6.
Рентгенограммы катализаторов после восстановления и зауглероживания в метане при 700°C в течение 30 мин катализаторов: 1 – 85%Ni/Al2O3; 2 – 75%Ni–12%Cu/Al2O3; 3 – 70%Ni–10%Cu–‒10%Fe/Al2O3. Обозначения: С – графит; M – металл Ni или Ni–Cu- и Ni–Cu–Fe-сплавы.
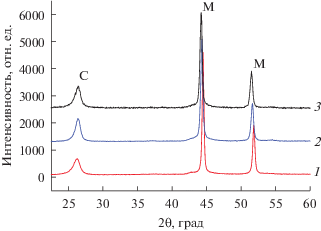
Из рис. 6 видно, что введение меди приводит к смещению рефлексов, относящихся к металлическому никелю, в область меньших углов, что свидетельствует об образовании двойного сплава никеля с медью с параметром решетки а = 0.3539 нм. Исходя из формулы Шеррера, состав сплава описывается химической формулой Ni0.85Cu0.15, что примерно соответствует соотношению металлов в исходном образце. Размер частиц сплава, определенный по уширению дифракционных максимумов, составляет 13 нм. Модифицирование катализатора 75%Ni–12%Cu/Al2O3 оксидом железа способствует тому, что после восстановления в водороде и зауглероживания катализатора 70%Ni–10%Cu–10%Fe/Al2O3 в метане при температуре 700°С в течение 30 мин параметр решетки сплава Ni–Cu возрастает до а = 0.3547 нм. Увеличение параметра свидетельствует об образовании тройного сплава Ni–Cu–Fe.
Формирование высокодисперсных частиц Ni–Cu–Fe-сплава приводит к синтезу активных, стабильных и способных работать при 700–750°С катализаторов разложения метана на водород и углеродные нановолокна.
На рис. 7 представлены кинетические кривые отложения углерода из метана на катализаторах 75%Ni–12%Cu/Al2O3 (кривая 1) и 70%Ni–10%Cu–‒10%Fe/Al2O3 (кривая 2) при температуре 700°С. Как видно, модифицирование Ni–Cu/Al2O3 добавкой железа уменьшает скорость отложения углеродных нановолокон, но стабильность работы катализатора значительно увеличивается.
Рис. 7.
Кинетические кривые отложения углерода на катализаторах 75%Ni–12%Cu/Al2O3 (1) и 70%Ni–‒10%Cu–10%Fe/Al2O3 (2) катализаторах из метана при температуре 700°С.
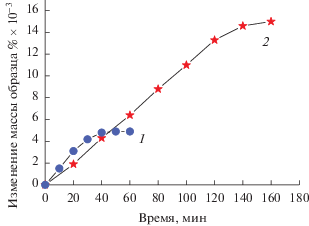
Из данных табл. 1 следует, что добавки железа в катализатор Cu–Ni/Al2O3 повышают оптимальные рабочие температуры до 700–750°С при сохранении высокой стабильности его работы. Выход углеродных нановолокон на модифицированном образце 70%Ni–10%Cu–10%Fe/Al2O3 при температурах 700–750°С составляет 150 гС/гкат.
Разработанный метод получения водорода и углеродных наноструктур позволяет использовать в качестве исходного углеводородного сырья не только метан, но и природный газ.
Из рис. 8 видно, что для катализатора 70%Ni–‒10%Cu–10%Fe/Al2O3 кинетические кривые отложения углерода как из метана, так и природного газа, близки. Однако следует отметить, что падение каталитической активности в случае природного газа начинается несколько раньше, чем в случае чистого метана.
Рис. 8.
Кинетические кривые отложения углерода на катализаторе 70%Ni–10%Cu–10%Fe/Al2O3 из метана (1) и природного газа (2) при температуре 700°С.
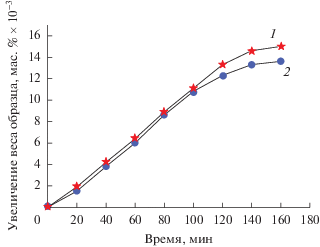
Поскольку оценку возможных степеней превращения метана делали исходя из предположения, что катализатор 70%Ni–10%Cu–10%Fe/Al2O3 будет обеспечивать стабильную работу со степенями превращения метана близкими к равновесным, то представляло интерес проверить это практически. Эксперименты по разложению природного газа в проточной установке с вращающимся реактором проводили при температуре 700°С. Загрузка катализатора 70%Ni–10%Cu–10%Fe/Al2O3 составляла 0.5 г, скорость подачи природного газа – 10 л/ч. Было установлено, что степень превращения природного газа (метана) в этих условиях в течение получаса выходит на стационарное значение и сохраняется на уровне примерно 55% в течение 28 ч (рис. 9), что свидетельствует о стабильной работе катализатора 70%Ni–10%Cu–‒10%Fe/Al2O3.
Рис. 9.
Зависимость конверсии природного газа от времени в присутствии катализатора 70%Ni–10%Cu–‒10%Fe/Al2O3. Температура реакции – 700°С, скорость подачи природного газа – 10 л/ч, масса катализатора – 0.5 г.
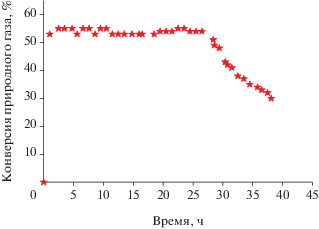
На рис. 10 представлена зависимость концентрации водорода (%) на выходе из реактора от времени. В стационарный период реакции этот показатель составляет около 70%. Красным пунктиром показано значение равновесной концентрации водорода. Видно, что в стационарный период реакции концентрация водорода на выходе из реактора примерно на 15% ниже равновесной.
Рис. 10.
Зависимость концентрации водорода на выходе из реактора от времени. В присутствии катализатора 70%Ni–10%Cu–10%Fe/Al2O3. Температура реакции – 700°С, скорость подачи природного газа – 10 л/ч, масса катализатора – 0.5 г.
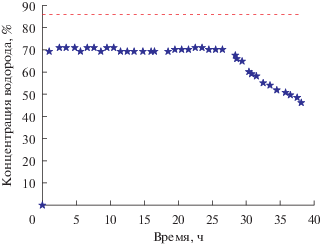
Концентрация примесей углеводородов С2–С3 на выходе из реактора падает больше чем на порядок и в сумме не превышает 0.3%. За 38 ч на катализаторе образуется 78.7 г углерода. Выход углеродных нановолокон с 1 г катализатора составляет 157.4 г. При этом выход водорода должен быть 590 л/г. Ранее указывалось (рис. 8), что в реакторе с весами Мак-Бена выход углеродных нановолокон из природного газа при использовании катализатора 70%Ni–10%Cu–10%Fe/Al2O3 был равен 136 г/г при температуре 700°С. Таким образом, выход углеродных нановолокон в установке с вращающимся реактором выше, чем в реакторе с весами Мак-Бена.
На рис. 11 представлены зависимости изменения концентраций водорода (%) от времени при температурах 700–750°С.
Рис. 11.
Зависимости изменения концентраций водорода (%) от времени в присутствии катализатора 70%Ni–10%Cu–10%Fe/Al2O3 при температурах 700 (1), 725 (2) и 750°С (3). Скорость подачи природного газа – 10 л/ч, масса катализатора – 0.5 г.
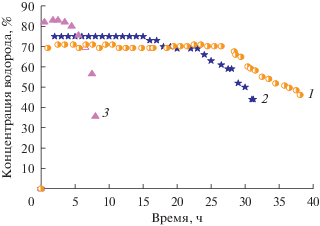
Видно, что концентрация водорода на выходе из реактора с температурой увеличивается. Если при 700°С во время стационарного периода реакции этот показатель составляет около 70%, то при 725°С возрастает до 75%, а при 750°С – до 84%. Однако стабильность работы катализатора падает с повышением температуры реакции: при температуре 750°С стационарный период реакции составляет 4–5 ч.
ЗАКЛЮЧЕНИЕ
1. В результате исследований удалось усовершенствовать катализатор 75%Ni–12%Cu/Al2O3 добавками оксида железа. Для полученного образца 70%Ni–10%Cu–10%Fe/Al2O3 оптимальные температуры проведения реакции разложения метана более высокие (700–750°С), чем для 75%Ni–12%Cu/Al2O3, что позволяет достигать степени превращения метана 55–70%.
2. С помощью электронной микроскопии и рентгенофазового анализа исследован генезис фазового состава катализаторов. Модифицирование 75%Ni–12%Cu/Al2O3 оксидом железа приводит к тому, что после восстановления в водороде и зауглероживания катализатора 70%Ni–10%Cu–‒10%Fe/Al2O3 в метане при 700°С образуется тройной Ni–Cu–Fe-сплав.
3. Разработанный метод получения водорода эффективно работает при использовании в качестве исходного сырья не только метана, но и природного газа.
4. Установка с вращающимся реактором для синтеза водорода и углеродных нановолокон из природного газа позволяет проводить процесс на катализаторе 70%Ni–10%Cu–10%Fe/Al2O3 в течение 20–30 ч. Концентрация водорода на выходе из реактора превышает 70 мол. %. Выход углеродных нановолокон достигает 160 гС/гкат.
5. Разработанная новая комплексная технология получения водорода и углеродных нановолокон открывает новые горизонты в решении проблемы производства “голубого” водорода. С экономической точки зрения комплексная технология более выгодна, чем применяющаяся в настоящее время конверсия природного газа с водяным паром. С экологической точки зрения комплексная технология также весьма привлекательна, так как позволяет вместо парниковых газов получать ценные углеродные наноматериалы.
Список литературы
Андрусевич А., Андрусевич Н., Козак З., Мищук З. Европейский зеленый курс: формирование будущего Восточного Партнерства. Экологическая политика стран Восточного партнерства в условиях ЕЗК. Аналитический документ, 2020, 64 с.
Kalamaras C.M., Efstathiou A.M. // Conference Papers in Energy. 2013. P. 690627.
10 прорывных идей в энергетике на следующие десять лет, голубой водород. Ассоциация по развитию международных исследований и проектов в области энергетики “Глобальная энергия”, 2021. С. 44. https://globalenergyprize.org/ru/10ideas/
Ионе К.Г. // Химия в интересах устойчивого развития. 2003. Т. 11. № 6. С. 907.
Aasberg-Petersen K., Bak Hausen Y.-H., Christensen T.S., Dybkjaer I., Seier Christensen P., Stub Nielsen C., Winter Madsen S.E.L., Rostrup-Nielsen J.R. // Appl. Catal. A: General. 2001. V. 221. P. 379.
Committee on Alternatives and Strategies for Future Hydrogen Production and Use, National Academy of Engineering. The Hydrogen Economy: Opportunities, costs, barriers, and R&D needs. 2004. P. 256. http://www.nap.edu/catalog.php?record_id=10922
Muradov N.Z., Veziroğlu T.N. // Int. J. Hydrogen Energy. 2005. V. 30. № 3. P. 225.
Chen Z., Elnashaie S. // Asia-Pac. J. Chem. Eng. 2006. № 1(1–2). P. 5.
Nikolaidis P., Poullikkas A. // Renew. Sustain. Energy Rev. 2017. V. 67. P. 597.
Karchiyappan T. // Energy Sources. Part A. 2019. V. 41 № 7. P. 902.
Machhammer O., Bode A., Hormuth W. // Chem. Eng. Technol. 2016. V. 39. № 6. P. 1185.
Deluga G., Salge J., Schmidt L., Verykios X. // Science. 2004. V. 303. № 5660. P. 993.
Daulbayev C., Sultanov F., Korobeinyk A.V., Yeleuov M., Azat S., Bakbolat B., Umirzakov A., Mansurov Z. // Appl. Surf. Sci. 2021. V. 549. P. 149176.
Daulbayev C., Sultanov F., Bakbolat B., Daulbayev O. // Int. J. Hydrogen Energy. 2020. V. 45. P. 33325.
Vedyagin A.A., Mishakov I.V., Korneev D.V., Bauman Y.I., Nalivaiko A.Y., Gromov A.A. // Hydrogen. 2021. V. 2. № 1. P. 122.
Parmar K.R., Pant K., Roy S. // Energy Convers. Manage. 2021. V. 232. P. 113893.
Fakeeha A.H., Khan W.U., Al-Fatesh A.S., Ibrahim A.A., Abasaeed A.E. // Int. J. Hydrogen Energy. 2016. V. 41. № 19. P. 8193.
Lee E.K., Lee S.Y., Han G.Y., Lee B.K., Lee T-J., Jun J.H., Yoon K.J. // Carbon. 2004. V. 42. P. 2641.
Kim M.H., Lee E.K., Jun J.H., Kong S.J., Han G.Y., Yoon K.J., Lee B.K., Lee T.-J. // Int. J. Hydrogen Energy. 2004. V. 29. № 2. P. 187.
Karakaya C., Kee R.J. // Prog. Energy Combust. Sci. 2016. V. 55. P. 60.
Moliner R., Suelves I., Lazaro M.J., Moreno O. // Int. J. Hydrogen Energy. 2005. V. 30. № 3. P. 293.
Muradov N., Smith F., Raissi A. // Catal. Today. 2005. V. 102–103. P.225.
Musamali R.W., Isa Y.M. // Asia-Pac. J. Chem. Eng. 2021. e2655. P. 1.
Ashik U.P.M., Daud W.M.A.W., Abbas H.F. // Renew. Sustain. Energy Rev. 2015. V. 44. P. 221.
Schneider S., Bajohr S., Graf F., Kolb T. // Chem. Bio. Eng. Rev. 2020. V. 7. № 5. P. 150.
Чесноков В.В., Буянов Р.А. // Успехи химии. 2000. Т. 69. № 7. С. 675.
Буянов Р.А., Чесноков В.В. // Катализ в промышленности. 2006. № 2. С. 3.
Bernardo C.A., Alstrup I., Rostrup-Nielsen J.R. // J. Catal. 1985. V. 96. P. 517.
Chesnokov V.V., Zaikovskii V.I., Buyanov R.A., Molchanov V.V., Plyasova L.M. // Catal. Today. 1995. V. 24. P. 265.
Chesnokov V.V., Podyacheva O.Y., Shmakov A.N., Kibis L.S., Boronin A.I., Ismagilov Z.R. // Chin. J. Catal. 2016. V. 37. № 1. P. 169.
Kriventsov V.V., Kochubey D.I., Goidin V.V., Molchanov V.V., Chesnokov V.V. // Top. Catal. 2002. V. 18. № 1–2. P. 91.
Sánchez-Bastardo N., Schlögl R., Ruland H. // Ind. Eng. Chem. Res. 2021. https://doi.org/10.1021/acs.iecr.1c01679
Chesnokov V.V., Chichkan A.S. // Int. J. Hydrogen Energy. 2009. V. 34. № 7. P. 2979.
Чесноков В.В., Чичкань А.С., Буянов Р.А. Патент РФ № 2009116873, приор. 04.05.2009.
Дополнительные материалы отсутствуют.
Инструменты
Кинетика и катализ