Кинетика и катализ, 2022, T. 63, № 1, стр. 110-121
Углеродная эрозия массивного никель-медного сплава как эффективный инструмент синтеза углеродных нановолокон из углеводородов
И. В. Мишаков a, b, *, С. Д. Афонникова a, b, Ю. И. Бауман a, Ю. В. Шубин b, c, М. В. Тренихин d, А. Н. Серкова a, А. А. Ведягин a
a ФБГУН ФИЦ Институт катализа им. Г.К. Борескова СО РАН
630090 Новосибирск, просп. Акад. Лаврентьева, 5, Россия
b ФГАОУВО Новосибирский государственный университет
630090 Новосибирск, ул. Пирогова, 2, Россия
c ФБГУН Институт неорганической химии им. А.В. Николаева СО РАН
630090 Новосибирск, просп. Акад. Лаврентьева, 3, Россия
d ФБГУН Центр новых химических технологий Институтa катализа им. Г.К. Борескова СО РАН
644040 Омск, ул. Нефтезаводская, 54, Россия
* E-mail: mishakov@catalysis.ru
Поступила в редакцию 09.09.2021
После доработки 20.09.2021
Принята к публикации 20.09.2021
- EDN: DHPWGI
- DOI: 10.31857/S045388112201004X
Аннотация
Углеродная эрозия массивных металлов и сплавов в углеродсодержащей атмосфере может служить эффективным инструментом для направленного синтеза углеродных наноматериалов. В представленной работе синтезирована серия массивных сплавов Ni0.89Cu0.11 (11 ат. % меди) методом механохимического сплавления металлических порошков в планетарной мельнице “Активатор 2S”. Полученные образцы исследованы в качестве предшественников катализатора для синтеза углеродных нановолокон (УНВ) при 550°С из этилена. Изучено влияние времени активации на морфологию частиц и фазовый состав сплавов, а также кинетику роста и выход углеродного продукта в разложении C2H4. Для наиболее активных образцов выход УНВ превысил 100 г/гкат за 30 мин реакции. С применением методов микроскопии исследован ранний этап процесса углеродной эрозии массивного сплава Ni0.89Cu0.11. Установлено, что зарождение активных центров роста углеродных нитей происходит в течение краткого контакта образца с реакционной смесью (менее 1 мин), а полная дезинтеграция сплава наблюдается через несколько минут. Углеродный продукт представлен нановолокнами субмикронного диаметра с плотной “стопчатой” и коаксиально-конической упаковкой графеновых слоев. Материал характеризуется развитой удельной поверхностью (140–170 м2/г) и легким насыпным весом (менее 30 г/л).
ВВЕДЕНИЕ
Углеродные наноматериалы (УНМ) уже давно завоевали признание ученых всего мира как одно из самых наукоемких и перспективных направлений развития нанотехнологии [1]. Разработка способов регулируемого синтеза УНМ, наравне с совершенствованием применяемых катализаторов, является важной современной задачей, решаемой на стыке знаний о катализе и материаловедении. Весомый вклад в развитие фундаментальных представлений и практических успехов в данном направлении внес член-корреспондент РАН Буянов Роман Алексеевич, предложивший механизм карбидного цикла (МКЦ) для описания процесса формирования углеродных наноструктур на металлических катализаторах [2–4]. Отличительной особенностью работ, проводимых в Институте катализа под руководством Буянова Р.А., была их нацеленность на изучение механизма каталитического синтеза углеродных материалов и способов управления такими технологиями [5]. В своих последних работах Роман Алексеевич активно развивал концепцию так называемого “физико-химического наноразмерного робота” (ФХНР), в которой в качестве наноробота рассматривается мультифункциональная каталитическая частица никеля, одновременно отвечающая за разложение углеродсодержащего субстрата и атомно-молекулярную “сборку” углеродных наноструктур [6–8]. Успех дальнейшего развития науки в этой области может быть связан с поиском новых путей “программирования” таких нанороботов с целью получения углеродных наноструктур с желаемым набором характеристик.
Катализаторы на основе никеля, пожалуй, стоит отнести к наиболее популярным системам, применяемым на практике для получения УНМ различного типа [9, 10]. В свою очередь, среди сплавных биметаллических катализаторов Ni–M особенно выделяются никель-медные сплавы как наиболее активные, стабильные и доступные по цене [11–13]. Способы синтеза никель-медных катализаторов разнообразны и зачастую сводятся к получению наноразмерных частиц сплава Ni–Cu и их стабилизации на поверхности различных носителей (SiO2, Al2O3, MgO и т.д.) [14–16]. К традиционным недостаткам нанесенных катализаторов можно отнести спекание металлических наночастиц в ходе восстановительной обработки при высокой температуре; ограниченный выход углеродного продукта вследствие скорой дезактивации частиц неоптимального размера, а также трудность удаления примеси минерального компонента (носителя) из состава полученного углеродного материала.
Существует ли способ синтеза катализатора, в котором все активные частицы “от рождения” имели бы нужный состав и оптимальный размер, определяющий максимальную эффективность работы катализатора в конкретных реакционных условиях? И здесь нам на помощь приходит явление углеродной эрозии (УЭ) массивных металлов и сплавов, известное своей способностью медленно разрушать материал стенок промышленных реакторов, выполненных из стали или никелевых сплавов [17–19]. Проблема связана с тем, что железо и никель при температуре 400–800°С способны растворять углерод [20], который затем осаждается в виде графитоподобной фазы в области межблочных границ, приводя к разрушению поликристаллической структуры изделия [21]. В результате дезинтеграции массивного сплава система переходит в иное качество, определяемое возникновением большого количества дисперсных частиц (фрагментов сплава), катализирующих рост нитевидных форм углерода [22–24]. Принято считать, что процесс углеродной эрозии (в зарубежной литературе – “Metal dusting” – распыление металла) является очень медленным и характеризуется продолжительным индукционным периодом, длящимся сотни часов [21, 25]. В то же время при использовании таких коксогенных углеводородов, как бутадиен [24, 26] или этилен [27, 28], а также коррозионно-агрессивных хлорзамещенных углеводородов [29, 30] процесс полного разрушения массивного сплава может происходить в течение нескольких часов и даже минут. В данном случае массивный сплав (например, Ni–M) можно рассматривать как предшественник катализатора, формирующегося в результате спонтанной дезинтеграции сплава в реакционных условиях [31].
Следует отметить, что феномен УЭ в последнее время все чаще используется для целенаправленного синтеза различных углеродных наноматериалов, включая нанотрубки (УНТ) и нановолокна (УНВ), а также гибридных металл-углеродных композитов и катализаторов [27, 32, 33]. Данный подход оказался особенно эффективным в случае каталитического разложения хлорзамещенных углеводородов (1,2-дихлорэтан, трихлорэтилен и др.) и отходов на их основе с получением УНВ [29, 34]. Было показано, что в результате быстрой дезинтеграции микродисперсных сплавов Ni–M формируются активные частицы близкого размера, на которых в дальнейшем осуществляется переработка хлоруглеводородов в углеродные нити с уникальной сегментированной структурой [35, 36]. Такой “самоорганизующийся катализатор”, формирующийся под воздействием углеродсодержащей реакционной среды, оказался чрезвычайно стабильным и производительным по сравнению с традиционными нанесенными системами [31].
В предлагаемой статье рассмотрен пример использования (в качестве предшественника катализатора) массивных сплавов Ni–Cu (11 ат. % меди), получаемых методом механохимического сплавления порошков индивидуальных металлов в планетарной мельнице. В качестве реакционноспособного углеводорода выбран этилен. Изучено влияние времени активации композитов на их морфологические особенности и каталитическую активность в синтезе УНВ. Подробно исследована ранняя стадия процесса углеродной эрозии сплавов Ni–Cu, в ходе которой зарождаются и формируются активные частицы, катализирующие рост углеродных нитей.
ЭКСПЕРИМЕНТАЛЬНАЯ ЧАСТЬ
Исходные реагенты
Для приготовления массивных Ni–Cu-сплавов применяли порошок никелевый ПНК-УТ3 по ГОСТ 9722-97 (НПО “РУСРЕДМЕТ”) и порошок медный ПМС-1 по ГОСТ 4960-2009 (ООО “СПЕЦПОСТАВКА”). При проведении каталитических экспериментов использовали этилен (“в. ч.”) по ГОСТ 24975.1 (“Нижнекамскнефтехим”), а также аргон и водород высокой чистоты.
Синтез и характеристики предшественников катализаторов
Серия сплавов Ni–Cu (предшественники катализатора) была получена методом механохимического сплавления (МХС) с использованием планетарной мельницы Активатор 2S (ООО “Активатор”, Россия). Перед началом синтеза готовили предварительную смесь (премикс) путем смешения порошков никеля и меди в весовом соотношении Ni/Cu = 88/12. Далее навеску премикса в количестве 10 г загружали в стальной барабан (V = 250 мл) вместе с мелющими шарами (340 г), выполненными из нержавеющей стали. Диаметр мелющих тел составлял 5 мм. Отношение массы шаров к массе мелющих тел во всех опытах было равно 340/10 = 34 г/г.
Регулировку частоты вращения барабанов и платформы осуществляли при помощи промышленного инвертора частоты VF-S15 (“Toshiba”, Индонезия). Частота вращения барабанов составляла 449 об/мин, центральной оси – 956 об/мин. Расчетное ускорение мелющих тел было равным 784 м/с2 (~80 g). В ходе активации применяли водяное охлаждение барабанов во избежание перегрева. Время активации (сплавления) композита варьировали в интервале от 3 до 11 мин. В процессе эксперимента барабаны подвергали периодической остановке через 3, 5, 7, 9 мин для отбора проб в количестве ~100 мг и последующего исследования их морфологии и фазового состава. По окончании процедуры МХС барабаны разгружали на воздухе, полученные образцы Ni–Cu-сплавов отделяли от мелющих тел при помощи сита и взвешивали.
Для удобства серия образцов сплавов была обозначена следующим образом: NiCu_x/y, где x = Dмт (диаметр мелющих тел), y = τ (время активации).
Исследование кинетики накопления углеродного продукта
Исследование кинетики накопления углеродного продукта на катализаторе проводили в режиме реального времени с использованием проточной гравиметрической установки, оснащенной весами Мак-Бена. В корзинку из вспененного кварца помещали навеску массивного сплава в количестве 1.50 ± 0.02 мг, подвешивали за кварцевую пружину и загружали в проточный кварцевый реактор. Далее образец нагревали в потоке аргона до температуры реакции (550°С). Скорость нагрева составляла 10°С/мин. По достижении заданной температуры образец приводили в контакт с реакционной смесью следующего состава: этилен (18 об. %), водород (59 об. %), аргон (остальное). Общая скорость подачи реакционной смеси – 66 л/ч. Изменение массы образца, происходящее в результате отложения углеродного продукта, регистрировали каждые 2 мин при помощи катетометра. Время каталитического эксперимента составляло 30 мин. По окончании эксперимента реактор охлаждали до комнатной температуры в потоке аргона. Полученный образец углеродного материала выгружали, взвешивали и рассчитывали удельный выход УНВ в граммах на грамм катализатора (г/гкат). Также для всех образцов УНВ была измерена насыпная плотность (г/л).
Физико-химические методы исследования образцов
Рентгенофазовый анализ (РФА) проводили на дифрактометре Shimadzu XRD-7000 (“Shimadzu”, Япония) с излучением CuKα (Ni-фильтр) при длине волны 1.54178 Å. Для определения фазового состава выполняли сканирование в диапазоне углов 2θ от 20° до 100° с шагом 0.05°. Идентификацию фаз выполняли с использованием данных из картотеки PDF [37]. Для более точного расчета параметров ячейки осуществляли сканирование в диапазоне углов 2θ = 140°–147° с шагом 0.05° и временем накопления в одной точке 10 с. Параметры кристаллической ячейки твердых растворов определяли по положению рефлекса 331, пользуясь программой PowderCell 2.4 [38]. Средний размер кристаллитов (область когерентного рассеяния, ОКР) вычисляли по уширению рефлексов 111, 200 и 220, используя уравнение Шеррера [39]. Расчет ОКР и описание дифракционных рефлексов функцией Пирсона проводили с помощью программы WinFit 1.2.1 [40]. Кристаллографические параметры для чистых металлов (Ni и Cu) были взяты из базы данных JCPDS-PDF [41].
Вторичную структуру массивных сплавов и морфологию углеродного продукта исследовали методом растровой электронной микроскопии (РЭМ) на электронном микроскопе JSM-6460 (“JEOL”, Япония) при увеличении от 1.000 до 100.000 раз. Первичную структуру углеродного продукта изучали методом просвечивающей электронной микроскопии (ПЭМ) с использованием микроскопа JEM 2100 (“JEOL”, Япония, ускоряющее напряжение – 200 кВ, разрешение – 0.14 нм).
Текстурные характеристики полученных образцов углеродных наноматериалов определяли методом низкотемпературной адсорбции/десорбции азота. Изотермы адсорбции измеряли при 77 К на автоматизированном приборе ASAP-2400 (“Micromeritics”, США). Предварительную дегазацию образцов УНВ проводили при температуре 250°С в течение 6 ч.
РЕЗУЛЬТАТЫ И ИХ ОБСУЖДЕНИЕ
Исследование морфологии и фазового состава образцов массивных сплавов
На первом этапе работы было изучено влияние времени активации смеси (Ni + Cu) в планетарной мельнице на вторичную структуру, морфологию и фазовый состав получаемых образцов. На рис. 1 приведены микрофотографии РЭМ для исходной смеси порошков никеля и меди (премикс, снимки 1а–1в) и образцов сплавов, прошедших активацию в течении 5 мин (снимки 1г–1е) и 11 мин (снимки 1ж–1и) в одинаковых условиях. Очевидно, что морфология частиц порошка в составе образца претерпевает значительные изменения в ходе механического воздействия. Вторичная структура исходного премикса представлена агломератами неправильной формы, состоящими из множества спеченных между собой первичных частиц, размер которых не превышает 2–3 мкм (рис. 1в). Размер агломератов варьирует в очень широких пределах, что можно видеть на обзорном снимке (рис. 1а).
Рис. 1.
Эволюция морфологии частиц образца сплава Ni–Cu в ходе механохимической активации в течение: (а–в) – 0 мин (исходный премикс); (г–е) – 5 мин (образец NiCu_5/5); ж–и – 11 мин (образец NiCu_5/11). Данные РЭМ.
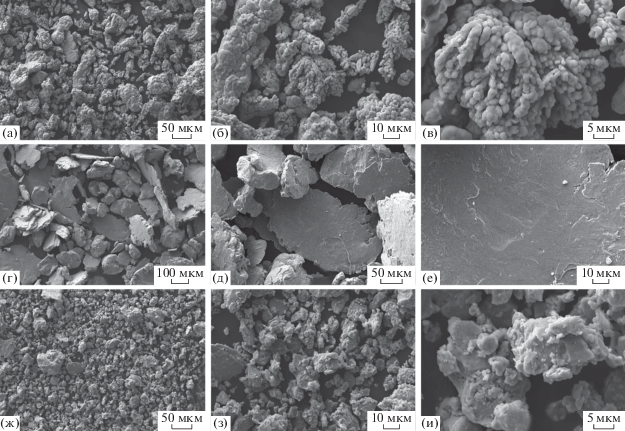
Из рис. 1г–1е следует, что 5-минутная процедура механохимического сплавления приводит к кардинальным изменениям морфологии частиц в составе порошка. В результате активации частицы расплющиваются с образованием характерных пластин толщиной в несколько микрон. Поверхность таких пластин можно назвать условно гладкой, с наличием характерных наплывов, возникающих в результате пластической деформации металла (рис. 1е) [42–44]. Сопоставление снимков (а) и (г) на рис. 1 показывает, что в ходе механического воздействия частицы порошка заметно укрупняются по сравнению с исходным премиксом. Увеличение времени активации образца до 11 мин также вызывает достаточно сильные изменения в морфологии: полностью исчезает пластинчатая форма частиц, наряду с явным уменьшением среднего размера агломератов. На поверхности вторичных частиц отмечается большое количество очень мелких кристаллитов, что, по-видимому, является свидетельством вторичной агломерации частиц (рис. 1и) [42]. Отметим, что наблюдаемые тенденции в изменении размера и морфологии частиц активируемого биметаллического композита хорошо согласуются с литературными данными [43, 44]. В ходе активации композита, состоящего из смеси пластичных металлов, вначале частицы расплющиваются при соударении с мелющими телами, образуя слоистую структуру (пластины), а в дальнейшем подвергаются разрушению с образованием высокодисперсного порошка [44].
На рис. 2 и в табл. 1 представлены результаты рентгенофазового анализа для серии образцов Ni–Cu, отличающихся продолжительностью процедуры МХС (3, 7 и 11 мин активации).
Рис. 2.
Дифрактограммы в областях 2θ = 20°–100° (а) и ~145° (рефлекс 331) (б) образцов Ni–Cu, приготовленных методом МХС при различном времени активации τ: 1 – 0 (премикс); 2 – 3; 3 – 7; 4 – 11 мин.
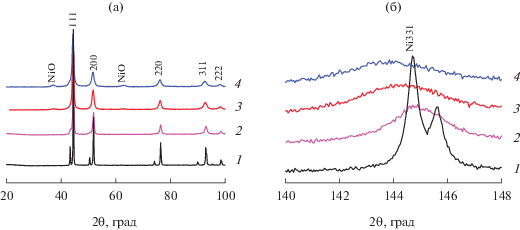
Таблица 1.
Рентгенометрические характеристики полученных образцов по данным РФА
Образец | Условия приготовления | Параметр ячейки, Å | ОКР, нм | Фазовый состав | ||
---|---|---|---|---|---|---|
Dмт, мм | τ, мин | доп. условия обработки | ||||
Премикс | – | – | – | 3.525 | 52 | Смесь фаз Ni и Cu |
NiCu_5/3 | 5 | 3 | – | 3.524 | 18 | Смесь фаз Ni и Cu |
NiCu_5/7 | 5 | 7 | – | 3.531 | 10 | Твердый раствор Ni–Cu Следы NiO |
NiCu_5/11 | 5 | 11 | – | 3.534 | 8 | Твердый раствор Ni–Cu Следы NiO |
*УНВ_NiCu_5/7_550С_1’ | 5 | 7 | tр = 1 мин; Т = 550°С |
3.532 | 26 | Графит Твердый раствор Ni–Cu |
Сопоставляя дифрактограммы для премикса (рис. 2а, кривая 1) и образца NiCu_5/3 (рис. 2а, кривая 2), следует отметить наличие индивидуальных фаз никеля и меди в обоих образцах. Об этом свидетельствует неизменный параметр ячейки никеля (а = 3.524(1) Å, табл. 1) и присутствие характерных “плеч” в районе 2θ ~ 43° и 50°, соответствующих примесной фазе Cu (гранецентрированной кубической (ГЦК)). Полученный результат говорит об отсутствии фазы взаимодействия – твердый раствор Ni–Cu не образуется. Тем не менее, в результате 3-минутной активации дифракционные пики значительно уширяются, что особенно хорошо заметно в области дальних углов (рис. 2б, кривая 2). Размер ОКР при этом уменьшается почти в 3 раза (с 52 до 18 нм, табл. 1).
При увеличении времени активации до 7–11 мин картина качественно меняется – происходит образование твердого раствора Ni–Cu на основе ГЦК-решетки никеля. В пользу этого вывода говорит исчезновение рефлексов, принадлежащих фазе меди, а также характерное смещение рентгеновских пиков в область малых углов. Наиболее отчетливо данный сдвиг можно наблюдать в области рефлекса 331 (2θ ~ 145°, рис. 2б, кривые 3 и 4). Параметр кристаллической ячейки при этом возрастает с 3.525 до 3.531–3.534 Å (табл. 1). Также следует отметить постепенное уменьшение среднего размера кристаллита (ОКР) с увеличением времени активации (до 8–10 нм, табл. 1). Согласно литературным данным термодинамических ограничений растворимости меди в никеле нет, поскольку система Ni–Cu характеризуется непрерывным рядом растворов [45].
Как видно из дифрактограмм 3 и 4 (рис. 2а), образование сплава Ni–Cu также сопровождается возникновением дополнительных рефлексов в области 2θ ~ 38° и 62°. Эти пики относятся к фазе оксида никеля (NiO). Образование примеси оксида никеля в образцах можно объяснить частичным окислением активированной поверхности сплава, происходящим в результате хемосорбции кислорода при контакте свежеприготовленного образца с воздухом.
Таким образом, метод механохимического сплавления порошков металлов в планетарной мельнице позволяет за сравнительно короткое время (τ > 3 мин) получать массивный никель-медный сплав (твердый раствор Ni–Cu на основе никеля). Данный способ является одностадийным, безотходным и не требует высокотемпературной обработки. Приготовленные образцы массивных сплавов Ni–Cu в дальнейшем были испытаны в качестве предшественников катализатора в реакции разложения этилена с образованием углеродных нановолокон.
Каталитическое разложение этилена на массивных сплавах Ni–Cu
На следующем этапе были изучены кинетические закономерности реакции разложения этилена на полученных сплавах с образованием УНВ. Еще раз подчеркнем, что данные образцы являются предшественниками катализатора, так как в результате интенсивной углеродной эрозии происходит их дезинтеграция с образованием большого количества дисперсных частиц, катализирующих дальнейший рост УНВ по механизму карбидного цикла [46].
На рис. 2а представлены кинетические кривые для процесса накопления углеродного продукта на катализаторе, снятые в режиме реального времени. Время взаимодействия с реакционной смесью для всех образцов составляло 30 мин. В качестве сравнения также был испытан образец премикса, не подвергавшийся процедуре МХС (рис. 3а, кривая 1).
Рис. 3.
Влияние времени активации (τ) сплава Ni–Cu на кинетику накопления углеродного продукта (а) и удельный выход УНВ за 30 мин реакции (б): 1 – премикс; 2 – τ = 11 мин; 3 – τ = 3 мин; 4 – τ = 9 мин; 5 – τ = 5 мин; 6 – τ = 7 мин. Условия реакции: С2Н4/Н2/Ar, Т = 550°С.
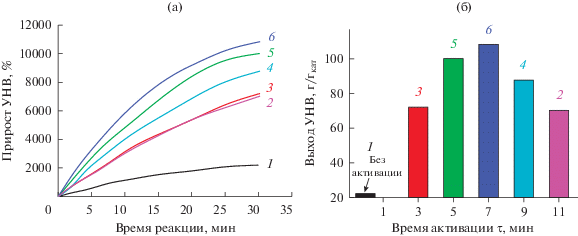
Результаты показывают, что продолжительность сплавления оказывает решающее влияние на каталитическую способность образца Ni–Cu. Так, без активации производительность образца (премикса) оказывается минимальной: он быстро дезактивируется, о чем говорит скорый выход кинетической кривой на плато (рис. 3а, кривая 1); достигнутый выход УНВ не превышает 25 г/гкат (рис. 3б, табл. 2). Полученный результат объясняется отсутствием стабилизирующего действия меди на каталитическую активность никеля, поскольку в составе премикса металлы не взаимодействуют [47].
Таблица 2.
Влияние времени активации композита {Ni + Cu} на скорость роста УНВ и удельный выход УНВ в разложении этилена при 550°С и времени реакции 30 мин
Образец | Время активации (τ), мин | Удельная скорость накопления УНВ*, %/мин | Прирост массы навески, % |
Выход УНВ, г/гкат |
---|---|---|---|---|
УНВ_Премикс | 0 | 70 | 2200 | 22.0 |
УНВ_NiCu_5/3 | 3 | 260 | 7210 | 72.1 |
УНВ_NiCu_5/5 | 5 | 380 | 10 020 | 100.2 |
УНВ_NiCu_5/7 | 7 | 400 | 10 840 | 108.4 |
УНВ_NiCu_5/9 | 9 | 290 | 8780 | 87.8 |
УНВ_NiCu_5/11 | 11 | 240 | 7030 | 70.3 |
В то же время видно, что использование даже кратковременной активации (3 мин) позволяет резко увеличить скорость роста углеродного продукта на сплаве (рис. 3а, кривая 3), что приводит к возрастанию удельного выхода УНВ до 72.1 г/гкат (табл. 2). Столь заметный рост каталитической активности, по-видимому, может быть связан с более тесным взаимодействием никеля и меди, что способствует легкому образованию сплава в восстановительной атмосфере при температуре реакции.
При повышении времени активации сплава до 7 мин (образец NiCu_5/7) достигается максимально высокая скорость роста УНВ (табл. 2); производительность катализатора NiCu_5/7 за 30 мин реакции составила 108.4 г/гкат. Дальнейшее увеличение продолжительности сплавления приводит к резкому снижению активности сплава. Примечательно, что кинетические кривые для образцов NiCu_5/3 и NiCu_5/11 (τ = 3 и 11 мин) практически совпадают (рис. 3а, кривые 2 и 3), а выход УНВ на них примерно в 1.5 раза уступает максимальному значению (табл. 2). Наблюдаемая куполообразная зависимость (рис. 2б) свидетельствует о существовании оптимального времени механохимического воздействия. Недостаточная продолжительность активации композита (равно как и избыточная) негативно влияет на каталитические свойства получаемого образца никель-медного сплава. Таким образом, можно заключить, что существуют границы оптимальных значений, в которых необходимо варьировать параметры механохимического сплавления металлов с целью достижения максимально эффективной производительности сплавного катализатора.
В заключение раздела следует также отметить важную особенность кинетических кривых роста УНВ на массивных сплавах Ni–Cu (рис. 3а): на них практически отсутствует фаза индукционного периода (ИП). В то же время при контакте массивных сплавов на основе никеля с другими реакционными газами (СО + H2 [23, 25], CO + CO2 [48], C2H4Cl2 + H2 [29, 30]) продолжительность ИП может достигать нескольких десятков и даже сотен часов. Наличие фазы ИП объясняется медленным протеканием процесса углеродной эрозии, в результате которого происходит дезинтеграция массивного сплава с последующим ростом углеродных наноструктур [31]. В случае взаимодействия смеси С2Н4/Н2 с образцами Ni–Cu процесс интенсивного роста УНВ начинается практически сразу, без видимой “задержки”, что говорит об очень быстром разрушении массивного сплава под действием углеродной эрозии.
Следующий раздел работы будет посвящен детальному изучению процессов, протекающих на раннем этапе взаимодействия массивных сплавов Ni–Cu с реакционной средой.
Исследование ранней стадии углеродной эрозии сплавов Ni–Cu
На рис. 4 представлены микрофотографии РЭМ для наиболее активного образца NiCu_5/7 до и после контакта с реакционным газом. Как уже отмечалось, исходный образец сплава представлен совокупностью крупных чешуек с условно гладкой поверхностью, имеющей следы сдвигового воздействия стальных мелющих тел, движущихся с ускорением порядка 80 g (рис. 4а–4в).
Рис. 4.
Результат кратковременного воздействия реакционной смеси С2Н4/Н2/Ar при 550°С на вторичную структуру образца NiCu_5/7 (Dмт = 5 мм, τ = 7 мин) в течение: (а–в) – 0 мин (исходный сплав); (г–е) – 30 с; (ж–и) – 1 мин. Данные РЭМ.
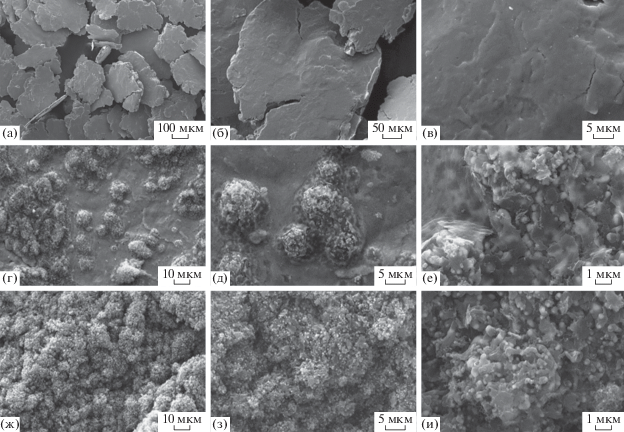
Далее подробно рассмотрим, что происходит с поверхностью этого сплава в результате очень краткого взаимодействия с реакционной смесью (0.5–1 мин). На снимках (рис. 4г–4е) можно видеть при различном увеличении результат воздействия углеродсодержащей атмосферы на массивный сплав при T = 550°C в течение 30 с. Очевидно, что условно гладкая поверхность массивного сплава взламывается и становится более рыхлой (рис. 4е). Увеличение времени контакта до 1 мин приводит к разрыхлению рельефа по всей поверхности образца сплава (рис. 4ж–4и).
Опираясь на данные рентгенофазового анализа, можно утверждать, что наблюдаемые изменения объясняются появлением графитоподобной фазы (рис. 5а, дифрактограмма 2). При этом сохраняются все рефлексы, принадлежащие фазе твердого раствора Ni–Cu, а интенсивность пиков от примеси NiO резко снижается. В области дальних углов (рис. 5б, дифрактограмма 2) отмечается изменение формы пика в результате отжига дефектов и повышения степени кристалличности сплава. Размер ОКР при этом также возрастает с 8 до 26 нм (табл. 1). Также следует отметить дополнительный сдвиг рефлекса 331 в область малых углов (рис. 5б, дифрактограмма 2) по сравнению с исходным образцом, что может объясняться появлением нестехиометрических карбидов (растворов внедрения) за счет вхождения атомов углерода в решетку сплава на ранней стадии УЭ. Образование подобных карбидов отмечалось нами ранее при изучении реакции разложения 1,2-дихлорэтана на сплавах Ni1– xPdx и Ni1– xPtx [36, 49].
Рис. 5.
Дифрактограммы сплава NiCu_5/7 (1) и образца УНВ_NiCu_5/7_550С_1’ (2), полученного в результате кратковременного контакта сплава NiCu_5/7 с реакционной смесью (С2Н4/Н2/Ar, 1 мин, Т = 550°С): (а) – область 2θ = = 20°–100°; (б) – область 2θ ~ 145° (рефлекс 331).
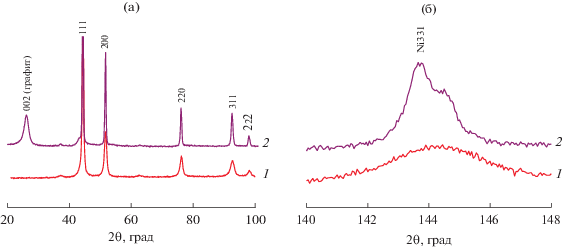
Вернемся к снимкам РЭМ на рис. 4. При ближайшем рассмотрении (рис. 4е, 4и) можно наблюдать очертания уже сформировавшихся активных частиц субмикронного размера (0.1–0.3 мкм), которые в дальнейшем выступают в роли активных центров, катализирующих разложение этилена и рост углеродных нитей. На рис. 6 приведена подборка снимков РЭМ и ПЭМ, на которых довольно отчетливо видна морфология активных частиц, формирующихся в результате дезинтеграции сплава. Снимки РЭМ, записанные в режиме обратно-отраженных электронов (рис. 6а, 6б), позволяют ясно наблюдать массив образовавшихся дисперсных кристаллов (белые контрастные пятна), вышедших на поверхность образца. На рис. 6в представлен снимок ПЭМ, на котором хорошо заметны дисперсные активные частицы, сформировавшиеся в результате фрагментации массивного сплава. Отметим, что каждая дисперсная частица сплава связана как минимум с двумя короткими углеродными нитями (рис. 6б–6г).
Рис. 6.
Морфология активных частиц, сформировавшиеся в результате контакта образца сплава NiCu_5/5 (Dмт = 5 мм, τ = 5 мин) с реакционным газом в течение 1 мин: (а, б) – снимки РЭМ в режиме вторично-отраженных электронов; (в–д) – снимки ПЭМ.
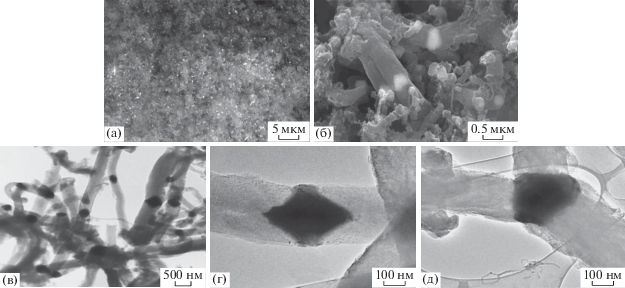
На микрофотографиях ПЭМ, приведенных на рис. 6г и 6д, можно видеть активные частицы различной морфологии. Первая имеет симметричную форму биконуса (рис. 6г) и “отвечает” за формирование углеродных нитей с коаксиально-конической упаковкой графеновых слоев [50]. Вторая частица (рис. 6д) визуально связана с тремя нитями, в структуре которых упаковка базальных плоскостей графита осуществляется параллельно осадительной грани, что соответствует так называемой “стопчатой” структуре УНВ [46].
Таким образом, в результате быстропротекающего процесса углеродной эрозии исходно грубодисперсный сплав (размер частиц достигает 100 мкм и более) буквально за одну минуту превращается в активно работающий катализатор, представляющий собой совокупность дисперсных сплавных частиц, осуществляющих рост УНВ по механизму карбидного цикла. Спонтанное зарождение активных частиц роста УНВ в результате дезинтеграции позволяет называть такие системы “самоорганизующимся катализатором” [35, 36]. В ряде работ других авторов считается, что фрагментация массивных сплавов на основе железа и никеля происходит в результате отложения фазы графита в области межзеренных границ поликристаллической структуры сплава [21, 51]. В ходе разрушения структуры сплава под действием УЭ самопроизвольно формируются дисперсные частицы субмикронного диаметра, размер которых является подходящим для реализации механизма карбидного цикла. Уже в самом начале роста УНВ наблюдается дифференциация функций различных граней кристаллов. Согласно терминологии, предложенной Р.А. Буяновым, первый тип граней отвечает за разложение молекул углеводорода (“лобовые” грани), а другой тип (“тыльные” грани) – за процесс отложения графита и рост углеродных нановолокон [3, 46].
Напомним, что привес углеродного продукта для образца УНВ_NiCu_5/7_550С_1’ составляет примерно 100%, что также видно из результатов кинетических измерений (рис. 3а). Можно предположить, что при увеличении массы образца в 2 раза исходный массивный сплав практически полностью подвергается дезинтеграции с появлением активных частиц – центров роста УНВ. Попробуем оценить примерное количество активных частиц, образующихся из сплава массой 1 г. Приняв средний размер активной частицы равным 250 нм, можно рассчитать теоретическое число центров роста УНВ, формирующихся в результате полной дезинтеграции 1 г исходного сплава Ni–Cu. По нашим оценкам, оно составляет примерно 1.4 × 1013 штук на 1 г предшественника.
Дальнейший рост углеродных нитей, катализируемый активными частицами никель-медного сплава, осуществляется в соответствии с механизмом карбидного цикла. На рис. 7 представлены снимки РЭМ углеродного продукта. Видно, что углеродный наноматериал, образовавшийся в результате получасового взаимодействия массивных сплавов Ni–M с этиленом, представлен совокупностью длинных углеродных нитей субмикронного диаметра (рис. 7в). Как уже было отмечено, нити характеризуются достаточно плотной упаковкой графеновых слоев, образуя структуру двух типов – “стопчатую” и коаксиально-коническую.
Рис. 7.
Снимки РЭМ углеродных нановолокон, полученных в результате взаимодействия этилена с образцом NiCu_5/5 в течение 30 мин при 550°C. Выход УНВ составляет 108.4 г/гкат.

Согласно данным низкотемпературной адсорбции азота (метод БЭТ) полученный углеродный наноматериал характеризуется развитой удельной поверхностью (140–170 м2/г) и достаточно низкой пористостью (0.14–0.22 см3/г). Cледует упомянуть о необычных макроскопических свойствах этого материала. Несмотря на высокий удельный выход УНВ (более 100 г/гкат), синтезированный углеродный продукт имеет очень легкий насыпной вес (не более 30 г/л). По всей вероятности, такая рыхлая упаковка углеродных нитей, плохо спутывающихся между собой, определяется еще на стадии дезинтеграции массивного сплава, в ходе которой формируются пучки параллельно растущих нановолокон (рис. 6б, 6в). Параллельный рост углеродных нитей является характерной особенностью самоорганизующихся катализаторов, работающих по принципу углеродной эрозии массивных металлов и сплавов [31].
ЗАКЛЮЧЕНИЕ
В настоящей работе рассмотрен пример использования массивных никель-медных сплавов для целенаправленного синтеза УНВ из этилена. В качестве метода приготовления массивных сплавов Ni–Cu выбран метод механохимического сплавления (МХС) металлов как наиболее простой, удобный и эффективный способ, позволяющий избежать стадий “мокрой химии” и высокотемпературной прокалки. Метод МХС предоставляет в распоряжение исследователя целый набор параметров (время активации, диаметр мелющих тел, соотношение скоростей вращения барабанов и платформы и т.д.), варьируя которые можно получать сплавные композиты с оптимальными свойствами. В нашем случае было изучено влияние времени активации на морфологию, фазовый состав и каталитическую способность сплавов Ni–Cu и найден оптимальный режим, обеспечивающий высокий выход углеродного продукта (более 100 г/гкат за 30 мин реакции).
Подробно исследована эволюция структуры и состава массивного сплава Ni–Cu на раннем этапе протекания УЭ. Показано, что процесс углеродной эрозии сплава носит стремительный характер, о чем свидетельствует практическое отсутствие фазы индукционного периода на кинетической кривой роста УНВ. В результате дезинтеграции массивного сплава Ni–Cu формируется каталитическая система, состоящая из множества активных частиц субмикронного размера, разделенных между собой растущими углеродными нитями. Особо подчеркнем, что в данном подходе к синтезу катализатора мы как бы опускаем необходимую стадию предварительного диспергирования активного компонента, предоставляя реакционной системе “самой” выбрать для себя оптимальный размер активных частиц. Именно такие активные частицы, рожденные в реакционных условиях из массивного предшественника, имеют все шансы проявить себя в качестве стабильного и эффективного катализатора синтеза УНМ. Также отметим, что в составе полученного углеродного продукта полностью отсутствуют примеси трудноудаляемых минеральных компонентов (например, оксидных носителей).
Дальнейший процесс функционирования каталитических центров роста, сформировавшихся в результате УЭ, происходит в соответствии с хорошо изученным механизмом карбидного цикла. Согласно концепции ФХНР, выдвинутой Р.А. Буяновым, поликристаллическая частица никелевого сплава может рассматриваться в качестве “наноразмерного робота”, совмещающего сразу несколько различных физико-химических функций, начиная от диссоциации молекул углеводородов и заканчивая атомно-молекулярной сборкой углеродных наноструктур [6–8]. В рассмотренном нами случае продуктом такой “сборки” служат углеродные нановолокна с коаксиально-конической и стопчатой структурой.
И здесь мы позволим себе закончить повествование цитатой самого Романа Алексеевича Буянова, взятой из цикла его последних статей о концепции ФХНР: “Природа в своем бесконечном многообразии сама создает функциональные структуры, управляющие нанотехнологиями. При этом в своих творениях она стремится находить самые простые решения. Отсюда и поговорка: “Гениальность в простоте решения”.
Список литературы
Begum S., Karim A.N.M., Ansari M.N.M., Hashmi M.S.J. Encyclopedia of Renewable and Sustainable Materials, 2020. P. 515.
Зайковский В.И., Чесноков В.В., Буянов Р.А. // Кинетика и катализ. 2006. Т. 47. № 4. С. 620.
Буянов Р.А., Чесноков В.В. // Катализ в промышленности. 2006. № 2. С. 3.
Буянов Р.А. // Кинетика и катализ. 1980. Т. 21. № 1. С. 237.
Буянов Р.А., Мишаков И.В. // Химия в интересах устойчивого развития. 2019. Т. 27. № 2. С. 219.
Буянов Р.А., Пармон В.Н. // Химия в интересах устойчивого развития. 2016. Т. 24. № 5. С. 705.
Буянов Р.А., Пармон В.Н. // Российские нанотехнологии. 2015. Т. 10. № 3–4.С. 35.
Буянов Р.А., Пармон В.Н. // Катализ в промышленности. 2013. № 3. С. 11.
Aboul-Enein A.A., Soliman F.S., Betiha M.A. // Int. J. Hydrogen Energy. 2019. V. 44. № 59. P. 31104.
Shen Y., Ge M., Lua A.C. // Catal. Sci. Technol. 2018. V. 8. № 15. P. 3853.
Karimi S., Bibaka F., Meshkania F., Rastegarpanahb A., Dengb J., Liub Y., Daib H. // Int. J. Hydrogen Energy. 2021. V. 46. P. 20435.
Подъячева О.Ю., Шмаков А.Н., Исмагилов З.Р., Пармон В.Н. // Докл. АН. 2011. Т. 439. № 1. С. 72.
Ефремов В.Н., Голосман Е.З. // Кинетика и катализ. 2006. Т. 47. № 5. С. 805.
Torres D., Pinilla J.L., Suelves I. // Catalysts. 2018. V. 8. № 8. P. 300.
Gutta N., Velisoju V.K., Tardio J., Patel J., Satyanarayana L., Sarma A.V., Akula V. // Energy Fuels. 2019. V. 33. № 12. P. 12656.
Awadallah A.E. // Chem. Papers. 2015. V. 69. № 2. P. 316.
Palsson N.S., Kaewkumsai S., Wongpinkaew K., Khonraeng W. // J. Fail. Anal. Prev. Springer US. 2017. V. 17. № 5. P. 838.
Al-Meshari A., van Zyl G., Al-Musharraf M. // J. Fail. Anal. Prev. Springer US. 2017. V. 17. № 3. P. 363.
Taghipour M., Eslami A., Bahrami A., Ghalambaz M. // Eng. Failure Analysis. 2020. V. 115. P. 104656.
Буянов Р.А. // Химия в интересах устойчивого развития. 2000. Т. 8. № 3. С. 347.
Zhang J., Young D.J. // Corros. Sci. 2007. P. 1496.
Chun C.M., Bhargava G., Ramanarayanan T.A. // J. Electrochem. Soc. 2007. P. 231.
Wu Q., Zhang J., Young D.J. // Mater. Corros. 2011. V. 62. № 6. P. 521.
Буянов Р.А., Мишаков И.В., Ведягин А.А. // Докл. АН. 2013. Т. 448. № 3. С. 314.
Ghorbani H., Rashidi A.M., Rastegari S., Mirdamadi S., Alaei M. // Mater. Res. Bull. 2011. V. 46. P. 716.
Буянов Р.А., Чесноков В.В., Афанасьев А.Д. // Кинетика и катализ. 1979. Т. 20. № 1. С. 207.
Yan X.-L., Wu Y.-L., Wang B.-S., Zhang Q., Zheng R.-T., Wu X.-L., Cheng G.-A. // Appl. Surf. Sci. 2018. P. 38.
Thakur D.B., Tiggelaar R.M., Gardeniers J.G., Lefferts L., Seshan K. // Surf. Coat. Technol. 2009. V. 203. № 22. P. 3435.
Бауман Ю.И., Мишаков И.В., Буянов Р.А., Ведягин А.А., Володин А.М. // Кинетика и катализ. 2011. Т. 52. № 4. С. 557.
Бауман Ю.И., Кенжин Р.М., Володин А.М., Мишаков И.В., Ведягин А.А. // Химия в интересах устойчивого развития. 2012. № 20. С. 157.
Mishakov I.V., Vedyagin A.A., Bauman Y.I., Shubin Y.V., Buyanov R.A. Carbon Nanofibers: Synthesis, Applications and Performance. Nova Science Publishers, 2018. P. 77.
Camilli L., Scarselli M., Gobbo S.D., Castrucci P., Nanni F., Gautron E., Lefrant S., Crescenzi M.D. // Carbon. 2011. P. 3307.
Varanasi C.V., Bulmer J., Brunke L., Burke J., Baca J., Yost K., Barnes P. // J. Vac. Sci. Technol. A: Vacuum, Surfaces, and Films. 2008. V. 26. № 4. P. 832.
Бауман Ю.И., Мишаков И.В., Ведягин А.А., Дмитриев С.В., Мельгунов М.С., Буянов Р.А. // Катализ в промышленности. 2012. № 2. С. 18.
Bauman Y.I., Shorstkaya Y.V., Mishakov I.V., Plyusnin P.E., Shubin Y.V., Korneev D.V., Stoyanovskii V.O., Vedyagin A.A. // Catal. Today. 2017. V. 293–294. P. 23.
Bauman Y.I., Mishakov I.V., Rudneva Y.V., Popov A.A., Rieder D., Korneev D.V., Serkova A.N., Shubin Y.V., Vedyagin A.A. // Catal. Today. 2020. V. 348. P. 102.
Powder Diffraction File. PDF_2/Release 2009: International Centre for Diffraction Data, USA.
Nolze G., Kraus W. // Powder Diffr. 1998. V. 13. P. 256.
Cullity B.D. Elements of X-Ray Diffraction. 2nd ed. Massachusetts, USA: Addison–Wesley Publishing Company, 1978.
Krumm S. // Mater. Sci. Forum. 1996. V. 228–231. № 1. P. 183.
JCPDS – PDF Database – International Centre for Diffraction Data, PCPDFWIN v. 2.02, 1999.
Болдырев В.В. // Успехи химии. 2006. Т. 75. № 3. С. 203.
Suryanarayana C. // Prog. Mater. Sci. 2001. V. 46. № 1–2. P. 1.
Charlot F., Gaffet E., Zeghmati B., Bernard F., Niepce J.C. // Mater. Sci. Eng. 1999. V. A262. P. 279.
Хансен М., Андерко К. / Структуры двойных сплавов. Москва: Металлургиздат, 1962. С. 644.
Чесноков В.В., Буянов Р.А. // Успехи химии. 2000. Т. 69. № 7. С. 675.
Fenelonov V.B., Derevyankin A.Yu., Okkel L.G., Avdeeva L.B., Zaikovskii V.I., Moroz E.M., Salanov A.N., Rudina N.A., Likholobov V.A., Shaikhutdinov Sh.K. // Carbon. 1997. V. 35. № 8. P. 1129.
Chang J.-K., Tsai H.-Y., Lin K.-Y., Tsai W.-T., Wang C.-Y., Yu M.-S. // ECS Transact. 2008. V. 6. № 17. P. 45.
Bauman Y.I., Mishakov I.V., Rudneva Y.V., Plyusnin P.E., Shubin Y.V., Korneev D.V., Vedyagin A.A. // Ind. Eng. Chem. Res. 2019. P. 685.
Зайковский В.И., Чесноков В.В., Буянов Р.А., Плясова Л.М. // Кинетика и катализ. 2000. Т. 41.№ 4. С. 593.
Schmid B., Aas N., Grong Ø., Ødegård R. // Appl. Catal. A: General. 2001. P. 257.
Дополнительные материалы отсутствуют.
Инструменты
Кинетика и катализ