Кинетика и катализ, 2022, T. 63, № 1, стр. 51-60
Сравнительный анализ процессов дегидрирования углеводородов и спиртов в мембранном реакторе
Е. В. Шелепова a, *, А. А. Ведягин a
a ФГБУН ФИЦ Институт катализа им. Г.К. Борескова СО РАН
630090 Новосибирск, просп. Акад. Лаврентьева, 5, Россия
* E-mail: shev@catalysis.ru
Поступила в редакцию 04.10.2021
После доработки 06.10.2021
Принята к публикации 06.10.2021
- EDN: TKEFNH
- DOI: 10.31857/S0453881122010075
Аннотация
Мембранные технологии нашли широкое применение во многих современных технологических процессах. В химической промышленности при помощи мембран решается ряд задач: от повышения эффективности целевых процессов до обеспечения жестких норм экологического законодательства. Особый синергический эффект ожидается в области мембранного катализа, когда появляется возможность не только ускорять целевую реакцию за счет катализатора, т.е. влиять на кинетику процесса, но и смещать равновесие в сторону продуктов за счет мембранного отделения одного или нескольких продуктов от основного реакционного объема. Данное преимущество мембранно-каталитических технологий особенно востребовано для эндотермических процессов. Настоящий миниобзор посвящен дегидрированию углеводородов на примере процессов получения наиболее востребованных мономеров – этилена, пропилена и стирола – и дегидрированию спиртов на примере метанола – ключевого соединения С1-химии.
ВВЕДЕНИЕ
Общая черта всех процессов дегидрирования – неблагоприятная термодинамика. Целевые реакции являются эндотермическими, и для получения существенных значений степени превращения субстрата требуются достаточно высокие температуры. С этим фактом сопряжена и другая проблема – образование кокса и дезактивация катализатора. Разработке процессов дегидрирования и соответствующих катализаторов, а также и детальному исследованию закономерностей коксообразования, механизмам дезактивации катализаторов и способам их регенерации много времени и сил посвятил Роман Алексеевич Буянов [1, 2]. В настоящем обзоре представлены преимущества реализации каталитических процессов дегидрирования в каталитическом мембранном реакторе.
ПРЕИМУЩЕСТВА РЕАЛИЗАЦИИ КАТАЛИТИЧЕСКИХ ПРОЦЕССОВ ДЕГИДРИРОВАНИЯ В МЕМБРАННОМ РЕАКТОРЕ
Хорошо известен тот факт, что основной проблемой при проведении процессов дегидрирования является наличие жестких термодинамических ограничений. Для реализации эндотермических процессов дегидрирования с обеспечением высоких выходов целевых продуктов необходимы высокие температуры. Однако проведение процесса при повышенных температурах способствует не только увеличению конверсии исходного сырья, но и протеканию нежелательных побочных реакций, в том числе интенсивному коксообразованию на поверхности катализатора, в результате чего существенно снижается селективность и эффективность процесса [1].
Один из путей решения данной проблемы – использование каталитических мембранных реакторов. В этом случае образующийся в результате реакции дегидрирования водород должен быть селективно удален из реакционного объема через водородпроницаемую мембрану, что позволит сместить равновесие реакции дегидрирования в сторону образования целевых продуктов. За счет сдвига термодинамического равновесия более высокие значения конверсии достигаются при более низких температурах, чем при проведении процесса в традиционных реакторах, что позволяет существенно снизить вклад процессов коксообразования. Выход по целевому продукту при этом возрастает за счет увеличения как конверсии, так и селективности [3].
В настоящее время существует значительное количество работ, в которых продемонстрирована эффективность применения каталитических мембранных реакторов при проведении процессов дегидрирования углеводородов (этана, пропана, циклогексана, этилбензола и др.) [4–14]. Наряду с дегидрированием углеводородов также достаточно широко исследовалось дегидрирование спиртов в мембранных реакторах [15–20].
Наиболее часто используемая конфигурация мембранного реактора представляет собой трубку, покрытую мембраной, которая помещается в трубку большего диаметра [21, 22]. Реакция дегидрирования может протекать как во внутренней, так и во внешней части реактора, другая часть реактора предназначена для удаления отводимого водорода. Водород из реактора удаляется либо потоком инертного газа, либо за счет реакции с присоединением водорода [22–25].
Ввиду относительно высоких температур процесса на практике применяются неорганические мембраны, которые могут быть металлическими или оксидными, плотными или пористыми.
Отличительной особенностью плотных мембран является высокая селективность, которая зависит от вида транспорта. Однако использование плотных мембран в каталитических мембранных реакторах может быть ограничено в области высоких температур. Наиболее часто применяют металлические плотные мембраны, среди которых широко распространены материалы на основе палладия. При синтезе таких мембран тонкий слой металлического палладия осаждается на пористую подложку. Для палладийсодержащих мембран характерна высокая селективность по водороду [26].
Так, при использовании плотной Pd- или Pd/Ag-мембраны было показано увеличение выхода пропилена в реакции дегидрирования пропана [27, 28]. В зависимости от типа подложки выход пропилена может быть повышен на 18% и более [27]. При применении композитной мембраны на основе Pd/Ag, в качестве подложки для которой был выбран материал Vycor glass, в исследуемом температурном интервале было зафиксировано четырехкратное увеличение конверсии пропана [28], а при использовании пористой мембраны значение конверсии пропана в мембранном реакторе оказалось близким к равновесному значению.
Аналогичные результаты были получены и для реакции дегидрирования этана. Его конверсия в мембранном реакторе превышала равновесное значение в 8 раз [29, 30]. Проведенное математическое моделирование этого процесса показало хорошее совпадение расчетных и экспериментальных данных при условии применения азота в качестве продувочного газа. В случае кислорода наблюдалось заметное расхождение, что объясняется возможным окислением Pd-мембраны. Таким образом, использование плотных металлических мембран может быть ограничено в зависимости от состава используемых газовых потоков.
Мембраны на основе Pd и Pd/Ag также хорошо себя зарекомендовали в реакции дегидрирования этилбензола [26]. При применении мембраны на основе Pd выход стирола может быть увеличен более чем на 15% [27]. Сравнительный анализ плотной и пористой мембран был выполнен для процесса дегидрирования этилбензола в работе [31]. Результаты численных расчетов показали, что конверсия в мембранном реакторе при использовании плотной Pd/Ag-мембраны выше, чем в случае микропористой мембраны с селективным слоем. Теоретически, значения конверсии этилбензола и выхода стирола при проведении процесса в мембранном реакторе с применением плотной палладийсодержащей мембраны могут достигать 64.8 и 60.5% соответственно, что превышает равновесные значения [8].
Эффективность использования различных типов мембран для повышения конверсии спиртов за счет удаления водорода из реакционного объема была продемонстрирована в ряде работ на примере метанола [32–36]. Zaspalis с соавт. показал, что выход формальдегида при дегидрировании метанола в мембранном реакторе с мембраной на основе γ-Al2O3 достигает 19% при 500°С, в то время как без мембраны он составляет всего 14.4% [34, 35]. Для процесса синтеза метилформиата в условиях мембранного реактора при 240°С конверсия метанола увеличивается с 43.1% (реактор без мембраны) до 57.3% [36]. Выход метилформиата при этом возрастает с 36.9 до 50.0%.
Таким образом, можно сделать вывод о целесообразности применения мембранных реакторов трубчатой геометрии для процессов дегидрирования углеводородов и спиртов. Проведение дегидрирования в мембранных реакторах дает возможность существенно улучшить показатели процессов. Трубчатая геометрия реактора позволяет достичь высокой площади поверхности мембраны, а также поверхности теплообмена в единице объема реактора. Более того, такой мембранно-каталитический подход может рассматриваться как альтернативный способ получения чистого водорода [37].
МАТЕМАТИЧЕСКОЕ МОДЕЛИРОВАНИЕ ПРОЦЕССОВ ДЕГИДРИРОВАНИЯ В МЕМБРАННОМ РЕАКТОРЕ
Математическое моделирование является одним из методов, с помощью которого можно оценить преимущества проведения конкретного процесса в мембранном реакторе, а также изучить влияние параметров процесса, в том числе и параметров мембраны, на его характеристики и при этом существенно сократить количество натурных экспериментов. В литературе математическому моделированию мембранных реакторов с мембраной трубчатой геометрии уделено достаточно большое внимание [38–40].
С точки зрения описания процессов массопереноса наибольший интерес представляют двумерные математические модели, в которых учитывается перенос вещества по длине и радиусу реактора, а также по подложке/мембране. При моделировании процессов теплопереноса возможно оценить влияние тепловых эффектов на показатели процесса, проводимого в мембранном реакторе. Таким образом, в классе неизотермических задач двумерные математические модели, в которых учитывается перенос тепла по длине и радиусу реактора, а также по подложке/мембране, наиболее предпочтительны.
Объем реакционной среды при осуществлении процессов дегидрирования в мембранном реакторе изменяется за счет отвода водорода через мембрану и за счет реакции, протекающей с увеличением числа молей, что необходимо принимать во внимание при математическом моделировании процессов в реакторе. Далее для сравнительного анализа процессов дегидрирования этана, пропана, этилбензола и метанола будем использовать двумерную математическую модель каталитического мембранного реактора с плотной мембраной [41]. Такая модель рассматривает не только процессы массопереноса, но и процессы теплопереноса в реакторе, по подложке и по мембране, а также учитывает изменение объема реакционной смеси в результате протекания реакций и селективного удаления продуктов. Чаще всего изучают каталитический мембранный реактор трубчатой конфигурации, состоящий из внутренней трубчатой части, покрытой керамической мембраной с нанесенным плотным металлическим слоем, и из внешней части, предназначенной для удаления отведенного водорода [41, 42]. Значения параметров математической модели, использованные для численных расчетов, приведены в табл. 1.
Таблица 1.
Параметры мембранного реактора
Параметр | Значение | Параметр | Значение |
---|---|---|---|
Диаметр катализатора $d_{{\text{k}}}^{{{\text{t,s}}}},$ м | 0.15 $ \times $ 10–2 | Длина реактора L, м | 0.15 |
Расстояние до подложки r1, м | 0.39 $ \times $ 10–2 | Входная концентрация O2$C_{{{{{\text{O}}}_{2}},{\text{in}}}}^{{\text{s}}},$ об. % | 5 |
Диаметр реактора dr, м | 0.2 $ \times $ 10–1 | Входная концентрация N2$C_{{{{{\text{N}}}_{2}},{\text{in}}}}^{{\text{s}}},$ об. % | 95 |
Толщина мембраны δ, м | 6 $ \times $ 10–6 | Порозность εt, s | 0.5 |
Толщина подложки δс, м | 0.11 $ \times $ 10–2 | Порозность εc | 0.28 |
Насыпная плотность катализатора ${{\rho }}_{{\text{k}}}^{{{\text{t,s}}}},$ г/м3 | 1 $ \times $ 106 | Давление P t, атм | 1.5 |
Диаметр пор подложки $d_{{\text{p}}}^{{\text{c}}},$ м | 1 $ \times $ 10–6 | Давление P s, атм | 1.0 |
Расход G t, мл/мин | 22 | Расход G s, мл/мин | 75 |
Одним из способов эффективного удаления водорода, отведенного через мембрану во внешнюю часть реактора, является его окисление. Поскольку плотная мембрана исключает возможность диффузии кислорода в зону дегидрирования из внешней части реактора, то окисление водорода является приемлемым в данном случае. Дополнительное окисление отводимого водорода способствует увеличению скорости диффузии водорода через мембрану во внешнюю часть реактора за счет большей разницы парциальных давлений водорода, что позитивно сказывается на протекании дегидрирования ввиду более интенсивного смещения термодинамического равновесия. Окисление водорода описывается уравнением: 2H2 + + O2 → 2H2O. Кинетика этого процесса на катализаторе Rh/α-Al2O3 детально описана в работе [43].
Дегидрирование этана
Уравнение реакции дегидрирования этана имеет вид: C2H6$ \rightleftarrows {\text{\;}}$C2H4 + H2. Кинетические параметры, необходимые для численного моделирования, были получены Gobina и соавт. для катализатора Pd/Al2O3 [30].
Как известно, процесс характеризуется довольно низкими равновесными значениями степени превращения этана. Так как реакция идет с увеличением числа молей, то по принципу Ле Шателье для ее интенсификации необходимо понижать давление. Вследствие эндотермичности процесса для его эффективной реализации необходимы достаточно высокие температуры. Для дегидрирования этана характерна область невысоких конверсий при значениях температуры ниже 600°С и давлениях свыше 1 атм.
В то же время реализация процесса при высоких температурах будет способствовать интенсивному коксообразованию на поверхности катализатора. Поэтому дегидрирование этана в мембранном реакторе представляется выгодным способом получения этилена не только за счет сдвига равновесия реакции, но и, как следствие, за счет снижения температуры проводимого процесса.
Далее будут представлены результаты численных расчетов, полученные при следующих параметрах: TW = 500°C; $T_{{{\text{in}}}}^{{{\text{t}},{\text{s}}}}$ = 100°C; $C_{{{{{\text{C}}}_{{\text{2}}}}{{{\text{H}}}_{{\text{6}}}},{\text{in}}}}^{{\text{t}}}$ = 10 об. %; $C_{{{{{\text{N}}}_{{\text{2}}}},{\text{in}}}}^{{\text{t}}}$ = 90 об. %, где TW – температура наружной стенки реактора, $T_{{{\text{in}}}}^{{{\text{t}},{\text{s}}}}$ – входная температура газовых потоков во внутренней и внешней частях реактора, $C_{{{{{\text{C}}}_{{\text{2}}}}{{{\text{H}}}_{{\text{6}}}},{\text{in}}}}^{{\text{t}}}$ – входная концентрация этана, $C_{{{{{\text{N}}}_{{\text{2}}}},{\text{in}}}}^{{\text{t}}}$ – входная концентрация азота.
Верификация использованной математической модели для процесса дегидрирования этана представлена в работе [44]. Благодаря тому, что математическая модель является неизотермической, возможно исследовать влияние тепловых эффектов на показатели процесса, проводимого в мембранном реакторе. Как следует из рис. 1, в отсутствие диффузии водорода через мембрану (кривая 2) температурный профиль достигает своего постоянного значения. Следует отметить, что в данном случае были заданы высокие значения входных температур газовых потоков ($T_{{{\text{in}}}}^{{{\text{t}},{\text{s}}}}$ = = 500°C) и исключен теплообмен с наружной стенкой реактора. В мембранном реакторе в результате смещения термодинамического равновесия температура снижается вследствие эндотермичности процесса (кривая 1). В результате экзотермической реакции окисления во внешней части мембранного реактора температура после незначительного снижения на начальном участке начинает возрастать, превышая температуру на входе в реактор на 65°C (кривая 3).
Рис. 1.
Температурные профили по длине реактора: 1 – мембранный реактор; 2 – трубчатый реактор; 3 –мембранный реактор с окислением отводимого водорода. $T_{{{\text{in}}}}^{{{\text{t}},{\text{s}}}}$ = 500°C.
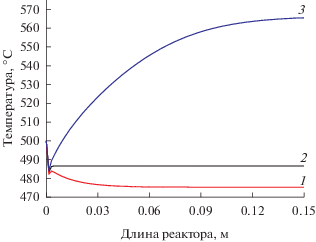
Реализация процесса дегидрирования этана в мембранном реакторе позволяет достигать высоких значений конверсии углеводорода (рис. 2). Так, при переходе от трубчатого реактора (кривая 1) к мембранному (кривая 2) конверсия этана возрастает в 2 раза, в то время как в случае мембранного реактора с окислением водорода этот показатель улучшается в 5 раз и достигает значения 83% (кривая 3). Сопоставимые значения конверсии этана можно получить в мембранном реакторе без окисления, но лишь при условии существенного повышения температуры, а именно до 622°C (кривая 4). Таким образом, окисление водорода способно поддерживать температуру на уровне, необходимом, с одной стороны, для достижения высоких значений конверсии этана, а с другой стороны, недостаточном для интенсивного образования кокса. С этой точки зрения окисление отводимого водорода обладает неоспоримым преимуществом при реализации процесса дегидрирования в мембранном реакторе.
Рис. 2.
Конверсия этана по длине реактора: 1 – трубчатый реактор, TW = 500°C; 2 – мембранный реактор, TW = 500°C; 3 – мембранный реактор с окислением отводимого водорода, TW = 500°C; 4 – мембранный реактор, TW = 622°C. $T_{{{\text{in}}}}^{{{\text{t}},{\text{s}}}}$ = 100°C.
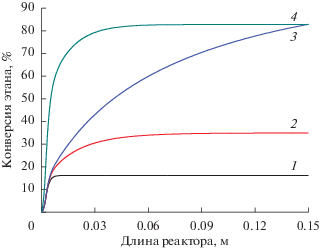
На рис. 3 сопоставлены зависимости конверсии этана от температуры для мембранного реактора (с окислением водорода и без окисления) с равновесным значением конверсии этана при следующих значениях параметров: $T_{{{\text{in}}}}^{{{\text{t}},{\text{s}}}}$ = 100°C, Gt = 6 мл/мин, Gs = 30 мл/мин, Pt = 1.287 атм.
Рис. 3.
Зависимость конверсии этана от температуры: 1 – равновесная кривая, 100% этан; 2 – мембранный реактор, 100% этан; 3 – равновесная кривая, 10% этана в инертном газе; 4 – мембранный реактор, 10% этана в инертном газе; 5 – мембранный реактор с окислением отводимого водорода, 100% этан; 6 – мембранный реактор с окислением отводимого водорода, 10% этана в инертном газе.
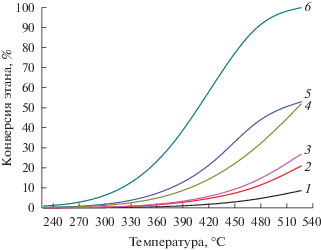
Отвод водорода через мембрану при дегидрировании 100%-ного этана (кривая 2) приводит к смещению равновесия и позволяет увеличить конверсию этана по сравнению с равновесной (кривая 1). При разбавлении газовой смеси инертным газом ($C_{{{{{\text{C}}}_{{\text{2}}}}{{{\text{H}}}_{{\text{6}}}},{\text{in}}}}^{{\text{t}}}$ = 10 об. %) конверсия в мембранном реакторе (кривая 4) превышает равновесное значение (кривая 3). При переходе к мембранному реактору с окислением отводимого водорода конверсия дополнительно возрастает (кривая 5), достигая максимальных значений при дегидрировании разбавленной газовой смеси (кривая 6). Так, при 500°С равновесная конверсия этана находится на уровне 6%, в то время как в мембранном реакторе с разбавлением реакционной среды и окислением отводимого водорода конверсия составляет свыше 90%.
Таким образом, для получения степени превращения этана в диапазоне 95–100% входная концентрации этана не должна превышать 10 об. %, а температура наружной стенки реактора должна находиться в интервале 475–520°С [44].
Дегидрирование пропана
Для дегидрирования пропана, по аналогии с ранее рассмотренным процессом, характерны невысокие равновесные значения степени превращения исходного субстрата. На интенсификации процесса также благоприятно сказываются пониженные давления и высокие температуры [45]. Отличительной особенностью дегидрирования пропана, по сравнению с дегидрированием этана, является наличие побочных реакций. Процесс дегидрирования пропана, с учетом протекания побочных реакций, описывается следующими уравнениями:
Кинетика процесса дегидрирования пропана была исследована Lobera и соавт. на катализаторе Pt–Sn–K/Al2O3 [46]. Рассмотрим результаты моделирования, полученные при следующих параметрах: TW = 500°C; $T_{{{\text{in}}}}^{{{\text{t}},{\text{s}}}}$ = 100°C; $C_{{{{{\text{C}}}_{{\text{3}}}}{{{\text{H}}}_{{\text{8}}}},{\text{in}}}}^{{\text{t}}}$ = 10 об. %; $C_{{{{{\text{N}}}_{{\text{2}}}},{\text{in}}}}^{{\text{t}}}$ = 90 об. %. Аналогично процессу дегидрирования этана, входная концентрация пропана в реакционном потоке является параметром, оказывающим существенное влияние на его конверсию. Максимальные значения конверсии пропана могут быть получены лишь в тех случаях, когда его входная концентрация не превышает 10 об. % (рис. 4). Уменьшение степени разбавления пропана в реакционном потоке затрудняет протекание реакции дегидрирования, идущей, как известно, с увеличением числа молей. Так, если при содержании пропана порядка 1 об. % удается достичь практически 100-процентной конверсии, то при использовании концентрированного реакционного потока (90–100 об. %) конверсия алкана не превышает 50%.
Рис. 4.
Конверсия пропана в зависимости от его входной концентрации. TW = 500°C; $T_{{{\text{in}}}}^{{{\text{t}},{\text{s}}}}$ = 100°C.
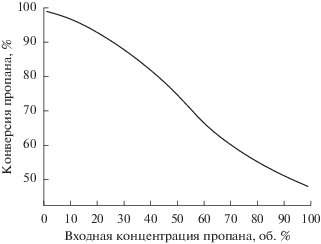
Скорость отвода водорода (диффузии через мембрану) также влияет на конверсию пропана. При проведении процесса в мембранном реакторе (TW = 500°C) минимальное значение степени превращения X = 67% соответствует варианту удаления водорода из внешней части реактора потоком инертного газа (табл. 2). В трубчатом реакторе данный показатель существенно ниже. Степень превращения пропана в мембранном реакторе увеличивается за счет диффузии водорода во внешнюю часть реактора и смещения равновесия реакции дегидрирования пропана в сторону образования продуктов.
Таблица 2.
Сравнение показателей процесса дегидрирования пропана в реакторах различного типа
Тип реактора | TW, °C | X, % | S, % |
---|---|---|---|
Трубчатый (без отвода водорода) | 500 | 41 | 87 |
Мембранный | 500 | 67 | 96 |
637 | 97 | 92 | |
Мембранный с окислением отводимого водорода | 500 | 97 | 99 |
При окислении отводимого водорода во внешней части реактора за счет более интенсивного сдвига термодинамического равновесия конверсия пропана достигает максимального значения 97% [41, 47]. Сопоставимые значения степени превращения пропана при использовании мембранного реактора без окисления водорода можно получить за счет повышения температуры стенки реактора до 637°C. Однако в этом случае не только снижается селективность по пропилену, но и существенно увеличиваются энергозатраты на поддержание температурного режима. Таким образом, максимальный выход пропилена может быть достигнут в температурном интервале 500–550°С [41].
Дегидрирование этилбензола
Промышленный процесс дегидрирования этилбензола существенно отличается от двух ранее рассмотренных тем, что проблема интенсивного коксообразования в данном случае стоит наиболее остро. В связи с этим в качестве разбавителя используют водяной пар. Также для указанного процесса характерно значительное количество параллельных реакций, которые можно описать следующими уравнениями:
Для реакции дегидрирования этилбензола также свойственны невысокие равновесные значения степени превращения исходного субстрата. Результаты кинетических исследований, проведенных Abo-Ghander и соавт. на промышленном железооксидном катализаторе дегидрирования этилбензола [48], позволили провести численные расчеты и смоделировать данный процесс в мембранном реакторе для следующих значений параметров модели: TW = 600°C; $T_{{{\text{in}}}}^{{\text{t}}}$ = 150°C; $T_{{{\text{in}}}}^{{\text{s}}}$ = = 100°C; $C_{{{{{\text{C}}}_{{\text{8}}}}{{{\text{H}}}_{{{\text{1}}0}}},{\text{in}}}}^{{\text{t}}}$ = 30 об. %; $C_{{{{{\text{H}}}_{{\text{2}}}}{\text{O}},{\text{in}}}}^{{\text{t}}}$ = 70 об. %.
Для всех трех вариантов проведения процесса (в трубчатом реакторе, мембранном реакторе и мембранном реакторе с окислением отводимого водорода) наблюдается увеличение значений степени превращения с ростом температуры, характерное для эндотермической реакции дегидрирования (рис. 5а). Степень превращения этилбензола в мембранном реакторе с окислением отводимого водорода (кривая 3) превышает конверсию в мембранном реакторе (кривая 2). Максимальные значения достигаются уже при температурах 600–625°C. Дальнейшее повышение температуры практически не способствует росту конверсии этилбензола.
Рис. 5.
Конверсия этилбензола (а), селективность образования стирола (б) и выход стирола (в) в зависимости от температуры: 1 – трубчатый реактор, 2 – мембранный реактор, 3 – мембранный реактор с окислением отводимого водорода.
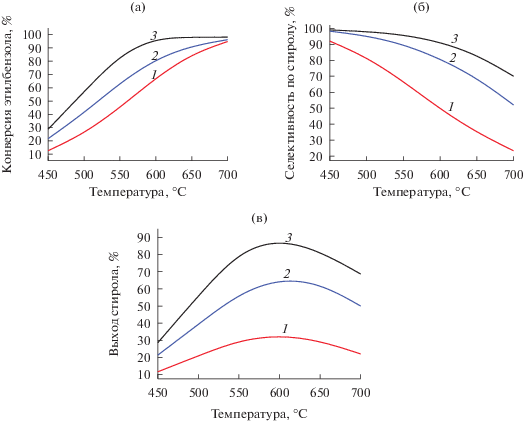
Селективность по стиролу ожидаемо снижается с ростом температуры (рис. 5б). При реализации процесса дегидрирования в мембранном реакторе с повышением температуры на 250°C (с 450 до 700°C) значение селективности уменьшается на 46% (кривая 2), а в трубчатом реакторе этот показатель падает на 70% (кривая 1). В случае проведения процесса в мембранном реакторе с окислением водорода наблюдается наименьшее снижение селективности – на 29% (кривая 3).
Выход стирола в мембранном реакторе (рис. 5в, кривая 2) превышает таковой в трубчатом реакторе (кривая 1) на 33% при температуре 600°C. Окисление отводимого водорода во внешней части реактора увеличивает этот показатель еще на 23% (кривая 3). Таким образом, максимальный выход стирола достигается при проведении процесса дегидрирования этилбензола в мембранном реакторе с окислением отводимого водорода при температуре около 600°C, а дальнейшее повышение температуры приводит к снижению выхода целевого продукта.
При проведении процесса в мембранном реакторе и удалении водорода из внешней части реактора потоком инертного газа конверсия составляет 81.7% (кривая 2), что на 14.2% выше соответствующего значения в трубчатом реакторе (рис. 6). При окислении отводимого водорода степень превращения максимальная – 97.5% (кривая 3). Полученная величина превосходит конверсию этилбензола, наблюдаемую при более высокой температуре (700°C) наружной стенки мембранного реактора без окисления водорода (96.3%, кривая 4). Т.е. для достижения сопоставимых значений конверсии в мембранном реакторе только за счет окисления отводимого водорода возможно снижение температуры наружной стенки реактора на 100°C.
Рис. 6.
Конверсия этилбензола по длине реактора: 1 – трубчатый реактор, TW = 600°C; 2 – мембранный реактор, TW = 600°C; 3 – мембранный реактор с окислением водорода, TW = 600°C; 4 – мембранный реактор, TW = 700°C.
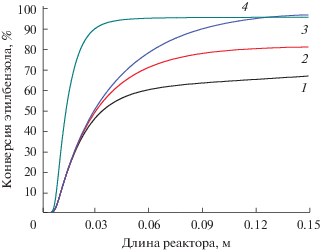
Однако, несмотря на сопоставимые значения конверсии при температурах 600 и 700°C, максимальный выход стирола достигается при 600°C в мембранном реакторе с окислением водорода (рис. 7) и составляет 89.3% (кривая 5), превышая этот показатель в трубчатом (33.5%, кривая 1) и мембранном реакторах (66.4%, кривая 4).
Рис. 7.
Выход стирола по длине мембранного реактора: 1 – трубчатый реактор, TW = 600°C; 2 – мембранный реактор, TW = 530°C, 3 – мембранный реактор, TW = 700°C, 4 – мембранный реактор, TW = 600°C; 5 – мембранный реактор с окислением водорода, TW = 600°C.
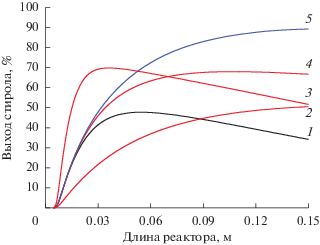
Повышение температуры наружной стенки реактора в данном случае нецелесообразно. Выход стирола при температурах свыше 600°C существенно меньше, что связано с увеличением скоростей побочных реакций и снижением селективности по целевому продукту. В мембранном реакторе без дополнительного окисления водорода повышение температуры с 600 до 700°C приводит к уменьшению выхода стирола на 15% (кривая 3). Полученное значение сопоставимо с таковым при 530°C (кривая 2).
Дегидрирование метанола
При дегидрировании метанола в качестве продуктов образуются водород и метилформиат, который в дальнейшем может разлагаться на CO и водород в соответствии с представленными уравнениями реакций:
Реакция дегидрирования метанола обратима и термодинамически ограничена. Для процесса дегидрирования метанола в метилформиат характерны небольшие значения равновесной концентрации метилформиата в продуктах реакции. С повышением температуры содержание метилформиата в равновесной смеси возрастает, но вместе с тем увеличивается и скорость его разложения, поэтому влияние времени контакта реакционной среды с катализатором становится весьма существенным.
При выполнении численных расчетов реакция разложения метилформиата рассматривалась как необратимая [49]. Кинетические параметры, использованные при математическом моделировании, были получены для катализатора Cu/Sibunit [50]. Значения параметров, при которых были проведены численные расчеты: $T_{{{\text{in}}}}^{{{\text{t}},{\text{s}}}}$ = 25°C, Pt,s = = 1 атм, $C_{{{\text{C}}{{{\text{H}}}_{{\text{3}}}}{\text{OH}},{\text{in}}}}^{{\text{t}}}$ = 10 об. %, $C_{{{\text{He}},{\text{in}}}}^{{\text{t}}}$ = 90 об. %, Gs = = 75 мл/мин.
Максимальное значение выхода метилформиата (77%) может быть получено в довольно узком температурном интервале наружной стенки реактора (150–160°C) при значении времени контакта τ = 20 с (рис. 8). С повышением температуры селективность по метилформиату и, соответственно, его выход снижаются, что обусловлено возрастанием скорости побочной реакции его разложения. Увеличение времени контакта также негативным образом сказывается на селективности по метилформиату. При больших временах контакта вклад побочной реакции разложения метилформиата существенно возрастает.
Рис. 8.
Зависимость выхода метилформиата от температуры (TW) для различных значений времени контакта (τ).
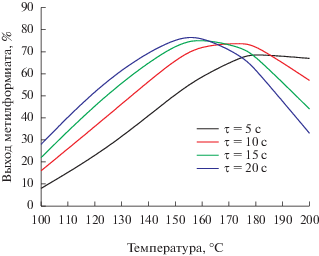
При 150°С максимальный выход метилформиата (78%) достигается в интервале времен контакта от 22 до 26 с (рис. 9, кривая 3). Повышение температуры, с одной стороны, положительно влияет на сдвиг равновесия в реакции дегидрирования, приводя к увеличению конверсии, а с другой стороны, как уже было указано выше, негативным образом сказывается на селективности по целевому продукту и, как следствие, на его выходе. Максимальный выход метилформиата при TW = = 175°С составляет 73–74% в интервале времен контакта от 8 до 14 с (кривая 2). При времени контакта более 14 с выход метилформиата снижается. Скорость побочной реакции разложения метилформиата возрастает как с повышением температуры, так и с увеличением времени контакта. Повышение температуры наружной стенки до 200°С еще сильнее сдвигает область максимальных значений выхода метилформиата в сторону низких значений времен контакта (кривая 1). Максимальный выход метилформиата при этой температуре находится в интервале времен контакта от 3 до 7 с и составляет всего 66% [51].
ЗАКЛЮЧЕНИЕ
Процессы дегидрирования различных субстратов (этан, пропан, этилбензол, метанол) характеризуются различающимся набором побочных реакций, снижающих селективность по целевому продукту. В связи с этим оптимальные реакционные условия для данных процессов также различаются. Среди ключевых факторов можно отметить разбавление реакционного потока инертным газом, что позволяет увеличить конверсию субстрата для всех рассмотренных случаев. Важную роль играет температура процесса, поскольку с ее повышением выход целевого продукта сначала возрастает, но после превышения оптимального значения наблюдается снижение селективности и выхода. В случае дегидрирования спиртов особую важность приобретает также такой параметр, как время контакта, поскольку вклад последовательной побочной реакции разложения целевого продукта существенно растет при больших временах контакта. Как продемонстрировано в представленной работе, методы математического моделирования позволяют достаточно эффективно оптимизировать все перечисленные параметры процессов.
Список литературы
Buyanov R.A. // Kinet. Catal. 1980. V. 21. № 1. P. 189.
Буянов Р.А., Пахомов Н.А. // Кинетика и катализ. 2001. Т. 42. № 1. С. 72.
Shelepova E.V., Vedyagin A.A. // Chem. Eng. Processing: Proc. Intensification. 2020. V. 155. 108072:1-9.
Koutsonikolas D., Kaldis S., Zaspalis V.T., Sakellaropoulos G.P. // Int. J. Hydrogen Energy. 2012. V. 37. P. 16302.
Khademi M.H., Rahimpour M.R., Jahanmiri A. // Int. J. Hydrogen Energy. 2010. V. 35. P. 1936.
Wang L., Murata K., Inaba M. // Catal. Today. 2003. V. 82. P. 99.
Dittmeyer R., Hollein V., Quicker P., Emig G., Hausinger G., Schmidt F. // Chem. Eng. Sci. 1999. V. 54. P. 1431.
Elnashaie S.S.E.H., Abdallah B.K., Elshishini S.S., Alkhowaiter S., Noureldeen M.B., Alsoudani T. // Catal. Today. 2001. V. 64. P. 151.
Yu C., Xu H. // Sep. Purif. Technol. 2011. V. 78. P. 249.
Schafer R., Noack M., Kolsch P., Thomas S., Seidel-Morgenstern A., Caro J. // Sep. Purif. Technol. 2001. V. 25. P. 3.
Schafer R., Noack M., Kolsch P., Stohr M., Caro J. // Catal. Today. 2003. V. 82. P. 15.
Weyten H., Luyten J., Keizer K., Willems L., Leysen R. // Catal. Today. 2000. V. 56. P. 3.
Jowkary H., Farsi M., Rahimpour M.R. // Int. J. Hydrogen Energy. 2020. V. 45. P. 7364.
Ghadiri M., Hemmati A., Rezakazemi M. // Int. J. Hydrogen Energy. 2021. V. 46. P. 28641.
Lin W.-H., Chang H.-F. // Catal. Today. 2004. V. 97. P. 181.
Schramm O., Seidel-Morgenstern A. // Chem. Eng. Sci. 1999. V. 54. P. 1447.
Xue D., Chen H., Wu G.-H., Deng J.-F. // Appl. Catal. A: General. 2001. V. 214. P. 87.
Keuler J.N., Lorenzen L. // Ind. Eng. Chem. Res. 2002. V. 41. P. 1960.
Keuler J.N., Lorenzen L. // J. Membr. Sci. 2002. V. 202. P. 17.
Liu B., Lian P.Y., Zhao X.H. // Sep. Purif. Technol. 2003. V. 32. P. 281.
Abashar M.E.E., Al-Rabiah A.A. // Chem. Eng. Proc. 2005. V. 44. P. 1188.
Elnashaie S.S.E.H., Moustafa T.M., Alsoudani T., Elshishini S.S. // Comp. Chem. Eng. 2000. V. 24. P. 1293.
Gryaznov V.M. USSR Pat. 274 092, priority 27 August, 1964.
Pfefferle W.C. US Pat. 3 290 406, priority 1 June, 1965.
Gryaznov V. // Catal. Today. 1999. V. 51. P. 391.
Ghasemzadeh K., Zeynali R., Bahadori F., Basile A. // Int. J. Hydrogen Energy. 2018. V. 43. P. 7675.
Quicker P., Höllein V., Dittmeyer R. // Catal. Today. 2000. V. 56. P. 21.
Yildirim Y., Gobina E., Hughes R. // J. Membr. Sci. 1997. V. 135. P. 107.
Gobina E., Hou K., Hughes R. // Catal. Today. 1995. V. 25. P. 365.
Gobina E., Hou K., Hughes R. // Chem. Eng. Sci. 1995. V. 50. №14. P. 2311.
Gobina E., Hou K., Hughes R. // J. Membr. Sci. 1995. V. 105. P. 163.
Wu J., Deng J. // Huaxue Xuebao. 1993. V. 51. P. 475.
Wu J., Deng J. // Acta Chimica Sinica. 1994. V. 52. P. 42.
Zaspalis V.T., Van Praag W., Keizer K., Van Ommen J.G., Ross J.R.H., Burggraaf A.J. // Appl. Catal. 1991. V. 74. P. 223.
Zaspalis V.T., Van Praag W., Keizer K., Van Ommen J.G., Ross J.R.H., Burggraaf A.J. // Appl. Catal. 1991. 74. P. 205.
Mo X., Lu G., Yan J., Wang J. // Chinese J. Catal. 1998. V. 19(1). P. 14.
Shelepova E.V., Vedyagin A.A. // Hydrogen. 2021. V. 2. № 3. P. 362.
Li L., Borry R.W., Iglesia E. // Chem. Eng. Sci. 2001. V. 56. P. 1869.
Abashar M.E.E., Al-Sughair Y.S., Al-Mutaz I.S. // Appl. Catal. A: Gen. 2002. V. 236. P. 35.
Abo-Ghander N.S., Grace J.R., Elnashaie S.S.E.H., Lim C.J. // Chem. Eng. Sci. 2008. V. 63. P. 1817.
Shelepova E.V., Vedyagin A.A., Mishakov I.V., Noskov A.S. // Chem. Eng. J. 2011. V. 176–177. P. 151.
Shelepova E.V., Ilina L.Y., Vedyagin A.A. // Reac. Kinet. Mech. Cat. 2019. V. 127(1). P. 117.
Tavazzi I., Beretta A., Groppi G., Forzatti P. // J. Catal. 2006. V. 241. P. 1.
Shelepova E.V., Vedyagin A.A., Noskov A.S. // Combustion, Explosion, and Shock Waves. 2013. V. 49. P. 125.
Dittrich C.J. // Chem. Eng. J. 2020. V. 381. P. 122492.
Lobera M.P., Tellez C., Herguido J., Menendes M. // Appl. Catal. A: Gen. 2008. V. 349. P. 156–164.
Shelepova E.V., Vedyagin A.A., Noskov A.S. // Combustion, Explosion and Shock Waves. 2011. V. 47. P. 499.
Abo-Ghander N.S., Grace J.R., Elnashaie S.S.E.H., Lim C.J. // Chem. Eng. Sci. 2008. V. 63. P. 1817.
Stull D.R., Westrum E.F., Sinke G.C. The chemical thermodynamics of organic compounds. New York: Wiley, 1969.
Shelepova E.V., Ilina L.Y., Vedyagin A.A. // Reac. Kinet. Mech. Catal. 2017. V. 122(1). P. 385.
Shelepova E.V., Ilina L.Y., Vedyagin A.A. // Chem. Papers. 2018. V. 72. P. 2617.
Дополнительные материалы отсутствуют.
Инструменты
Кинетика и катализ