Кинетика и катализ, 2022, T. 63, № 1, стр. 33-50
Формирование углеродных материалов при окислительном пиролизе метана на резистивных катализаторах
Д. А. Шляпин a, *, А. В. Лавренов a, Н. Н. Леонтьева a
a Центр новых химических технологий ИК СО РАН, Институт катализа СО РАН
644040 Омск,
ул. Нефтезаводская, 54, Россия
* E-mail: dash@ihcp.ru
Поступила в редакцию 03.09.2021
После доработки 08.09.2021
Принята к публикации 08.09.2021
- EDN: DPYJJX
- DOI: 10.31857/S0453881122010087
Аннотация
В представленном обзоре описаны закономерности синтеза наноструктурированных углеродных материалов (НУМ), основанного на пиролизе метана на поверхности токопроводящих материалов (фехраль, карборунд), выступающих в роли катализаторов разложения метана в условиях резистивного нагрева. На формирование углеродных продуктов пиролиза наряду с составом исходной газовой смеси, температурой, природой катализатора принципиальное влияние оказывает электромагнитное поле, возникающее при протекании электрического тока через резистивный материал. Это дает новые возможности для получения углеродных волокон уникальной морфологии, в том числе, фрактальных структур.
ВВЕДЕНИЕ
Синтез наноструктурированных углеродных материалов, изучение их свойств и областей применения относятся к числу наиболее перспективных направлений современного материаловедения [1]. Как указывают авторы работы [2], каталитический волокнистый углерод известен еще с XIX в. В монографии [3] упоминается патент 1889 г., описывающий процесс получения углеродных волокон путем разложения метана на железе в присутствии водорода. Выраженный интерес к волокнистому углероду как материалу возник на фоне исследований, связанных с негативными эффектами его образования в различных технологических системах, включая ядерные реакторы, металлические конструкции оборудования для парового крекинга, его отложения на катализаторах, используемых при метанировании синтез-газа, реакции конверсии водяного газа, паровом риформинге углеводородов [4].
В.В. Чесноков (V.V. Chesnokov) и Р.А. Буянов (R.A. Buyanov) выделили зауглероживание как один из ключевых процессов, вызывающих дезактивацию катализаторов, применяемых для переработки углеводородного сырья [1]. В то же время целенаправленно зауглероженные неорганические соединения (металлы, оксиды и др.), включая и сам углерод, можно рассматривать как углерод-минеральные и углеродные-углеродные композиционные материалы, обладающие новыми функциональными свойствами.
Y.N. Zhang с коллегами указывают на уникальные свойства наноструктурированных углеродных материалов (НУМ), например, высокую механическую прочность, хорошие электро- и теплопроводность [5]. Эти свойства могут быть сохранены в их макроскопических сборках, таких как жгуты из углеродных нанотрубок (УНТ), пленки из УНТ и углеродные нановолокна (УНВ). Авторы [5] получили волокна, отличающиеся высокой проводимостью (около 400–500 См/см) и прочностью на разрыв (1.2 ГПа). A. Chatterjee, B.L. Deopura в своем обзоре [6] назвали углеродное нановолокно, образующееся при разложении паров углеводородов, уникальной формой углерода, которая служит переходом между более крупными углеродными волокнами на основе полиакрилонитрила или пека и углеродными нанотрубками (рис. 1).
Уникальные свойства НУМ определяют сохраняющийся на протяжении нескольких десятилетий интерес исследователей к разработке новых способов их синтеза и применения в различных отраслях техники. Как функциональные и конструкционные материалы, НУМ могут быть использованы самостоятельно, а также в виде композитов с материалами подложек, на которых они формируются. Известные сегодня способы позволяют синтезировать наноструктурированные углеродные материалы в промышленных объемах. Например, предложенная И.В. Мишаковым и соавторами установка с вращающимся реактором способна производить до 1.5 т углеродных нанонитей в год [7].
Метан является наиболее предпочтительным источником для формирования массивов НУМ. Это определяется его доступностью и, главное, низкой химической активностью в условиях пиролиза. Последнее дает возможность проводить процесс разложения метана на углерод и водород устойчиво в широком интервале значений варьируемых параметров. До сих мало описаны закономерности синтеза наноструктурированных углеродных материалов, основанного на пиролизе метана на поверхности токопроводящих материалов (фехраль, карборунд), выступающих в роли катализаторов разложения метана в условиях резистивного нагрева. На формирование углеродных продуктов пиролиза, наряду с составом исходной газовой смеси, температурой, природой катализатора, принципиальное влияние оказывает электромагнитное поле, возникающее при протекании электрического тока через резистивный материал. Применение резистивных катализаторов дает дополнительные рычаги воздействия на морфологию образующихся НУМ [2, 8–15]. Обзор таких “рычагов” и определяет цель настоящей публикации.
CVD-СИНТЕЗ – ОСНОВНОЙ СПОСОБ ПОЛУЧЕНИЯ НУМ
Суть метода CVD (chemical vapor deposition), заключается в формировании НУМ на поверхности материала-подложки из вещества-предшественника – газообразного органического соединения, способного при повышенной температуре подвергаться термическому или термокаталитическому разложению – пиролизу (рис. 2). Этот метод получения НУМ отличает ряд преимуществ по сравнению с другими способами, разработанными ранее – разложением в дуговом разряде (arc discharge method, ARM) или путем лазерной абляции (laser ablation method, LAM) [16, 17]. Первым преимуществом данного метода является высокая степень чистоты образующихся углеродных материалов. Второе преимущество – более низкая температура (600–1000°C) по сравнению с “физическими” способами синтеза, что делает процесс более эффективным и доступным для лабораторных исследований. В-третьих, для закрепления катализатора на основе переходного металла может быть использован широкий спектр носителей, что расширяет возможности для получения композитных материалов.
В качестве катализатора в методе CVD выступают дисперсные частицы металлов подгруппы железа (Fe, Co, Ni) или их сплавы с другими металлами [1, 4, 10, 16, 18–33]. Разложение органических соединений катализируется и углеродными материалами [34–43]. Каталитическая способность металлов во многом зависит от диффузии и растворимости углерода в них. Кроме того, предполагается, что наночастицы катализатора обладают прочной адгезией к атомам углерода растущих УНТ, что приводит к образованию трубчатой структуры высокой кривизны. Поэтому диаметр УНТ обычно считается равным диаметру наночастиц катализатора [16, 20]. В качестве материалов-подложек для дисперсных металлических частиц в методе CVD используют кремний, оксид алюминия, кварц, карбид кремния и цеолиты [16, 20, 21]. Подложка должна предотвращать агломерацию частиц катализатора, препятствуя их миграции по поверхности и сплавлению, а также выдерживать высокие температуры, не вступая во взаимодействие с металлом-катализатором. В качестве источников углерода для формирования НУМ, как правило, выступают углеводороды CH4, C2H2, C2H4, бензол, а также CO, камфора и этанол [16, 20]. Источник углерода, газ-носитель, скорость потока, давление, температура, материал подложки и природа и морфология частиц катализатора являются ключевыми параметрами, которые влияют на скорость роста, длину, плотность, диаметр, количество стенок и тип проводимости углеродных нанотрубок [16, 44].
Термическая стабильность металлических наночастиц, присутствующих в УНМ после их синтеза, намного выше, чем у металлических катализаторов, нанесенных на оксидные носители MgO, Al2O3, SiO2, ZrO2 [45, 46]. Поэтому НУМ, в которых содержатся частицы металла, предложено использовать в качестве металл-углеродных катализаторов для таких процессов, как полное и селективное гидрирование непредельных углеводородов и непредельных жирных кислот, паровая и углекислотная конверсия метана, метанирование СО, синтез Фишера–Тропша, восстановительное дехлорирование хлорбензола, дегидрирование н-бутана и окисление СО [15, 47, 48]. Ученик Р.А. Буянова, В.В. Молчанов с соавторами сообщали о разработке принципиально новых каталитических систем на основе дисперсных металлических частиц, встроенных в углеродные нити путем каталитического разложения углеводородов на этих частицах [49]. Авторы также продемонстрировали возможность управления процессами разложения с целью получения катализаторов гидрирования.
Перспективным предшественником для синтеза НУМ является метан. Действительно, несмотря на то, что выход НУМ при выборе метана существенно ниже по сравнению с такими предшественниками, как этилен, пропилен, ацетилен, метанол, этанол, бензол, химическая инертность метана – это его преимущество, позволяющее обеспечить контролируемый рост наноматериалов [28]. Так, с использованием природного газа, проходящего через трубку из нержавеющей стали, содержащую Ni и Cr, при 950–1075°C, были получены углеродные волокна длиной от миллиметров до сантиметров и диаметром 5–1000 мкм [50, 51]. Разработан также метод синтеза углеродных волокон на суспензии частиц Fe размером 12 нм в потоке CH4 + H2 при 1100°C [29, 52]. В своих работах Q. Wen и соавт. выбрали метан для выращивания при 900–950°C сверхдлинных двустенных и трехстенных УНТ, длина которых составляла десятки сантиметров, на катализаторе Fe/MgO [53–55]. При такой значительной длине нанотрубки сохранили свои полупроводниковые свойства, что говорило о сохранении их структуры и системы сопряжения.
Метан может выступать в качестве исходного сырья для образования такого популярного сегодня материала, как графен [28]. Исследователями были сформулированы основные условия его синтеза. Реакционная смесь должна состоять из метана, водорода и инертного газа. Процесс пиролиза метана с осаждением графена на подложку происходит при температуре порядка 800°C. В зависимости от растворимости углерода в подложке процесс формирования графена протекает либо через стадию растворения углерода, образовавшегося из метана, с последующей сегрегацией и осаждением, либо через диссоциативную адсорбцию метана. Подложками могут служить переходные металлы Ni, Cu, Pt, кремний и их карбиды [28, 56–58]. Как правило, синтез графена проводят в трубчатой печи, в результате получают материал в виде пленок и твердой “пены”. Более быстрый и простой способ основан на применении лазерного излучения, который в зависимости от типа и мощности лазера позволяет варьировать свойства графена [59, 60].
Часто используемые для диспергирования катализатора оксидные носители создают определенные ограничения для синтеза НУМ ввиду того, что частицы катализатора находятся в порах носителя. F. Wei с коллегами сформулировали эту проблему как явление “ограниченного роста” [61–64]. Соответственно, авторами были предложены подходы к синтезу носителей со структурой, которую способны разрушить растущие углеродные нити. Следует отметить, что применение подложек из массивных металлов позволяет избежать этого явления.
ПИРОЛИЗ НА РЕЗИСТИВНЫХ КАТАЛИЗАТОРАХ КАК ЧАСТНЫЙ СЛУЧАЙ CVD-СИНТЕЗА
В работе [65] пиролиз метана изучали на платиновой нити диаметром 0.2 мм, нагреваемой электрическим током. Время контакта составляло около 100 мс. При 1310°С степень превращения метана была 19.7%, в продуктах содержалось 32% углерода и 51% углеводородов С2, остальные 17% приходились на более тяжелые углеводороды, главным образом, на бензол и пропилен. В работах [2, 8–15], положенных в основу настоящего обзора, в качестве резистивных катализаторов использовали фехраль и карбид кремния (карборунд). Фехраль – это термостабильный сплав, применяемый традиционно в авиационной и космической технике, марки Х23Ю5Т (ГОСТ 127661–90) следующего элементного состава (мас. %): Fe – 62–72, Cr – 22–24, Al – 5.0–5.8, Ni – до 0.6, Si – до 0.5, Mn –до 0.3, Ti – 0.2–0.5, Ce и Ca – до 0.1, C – до 0.05, P – до 0.03, S – до 0.015. Данный сплав обладает высоким удельным сопротивлением (~1.4 мкОм м–1), что делает возможным разогрев проволоки пропусканием относительно небольшого тока (до 10 А). Карборунд – техническое название синтетического материала состава SiC, соответствующего минералу муассанит. Карборунд – полупроводник с высокими рабочими температурами, прочностью и хорошей теплопроводностью.
На рис. 3 сопоставлены условия классического CVD-синтеза и получение НУМ на резистивном фехралевом катализаторе. Как видно, отличия методов заключаются: 1) в способе формирования каталитически активных частиц металлов; 2) в способе нагрева реакционной зоны. Если для приготовления катализатора CVD-синтеза необходимо нанести на подложку наночастицы активного компонента (путем напыления или нанесения в виде предшественника, например, оксида, с последующим восстановлением до металла), то предварительная обработка фехралевого катализатора состоит в выдерживании его на воздухе при температуре 1000°С. При этом на его поверхности образуется слой оксидов, входящих в сплав элементов – алюминия, железа, хрома. Этот оксидный слой является источником формирования первичных активных частиц катализатора непосредственно в ходе синтеза НУМ. Нагрев реакционной зоны в CVD-синтезе происходит в результате подачи газа необходимой температуры, состоящего либо из чистого углеводорода, либо из смеси углеводорода с газом-разбавителем. При синтезе НУМ на резистивном катализаторе газовая смесь остается холодной, а нагревается за счет тепла, выделяющегося при прохождении электрического тока, сам катализатор. Несмотря на эти различия, общий принцип метода CVD, заключающийся в получении углеродных наноматериалов на некоторой подложке в присутствии катализатора из газообразного предшественника, соблюдается и при синтезе НУМ на резистивном катализаторе. Соответственно, можно определить синтез НУМ в условиях резистивного катализа как частный случай CVD-метода.
Рис. 3.
CVD-синтез и получение УНМ на резистивном фехралевом катализаторе: 1 – подложка; 2 – наночастицы катализатора; 3 – углеродные нановолокна, растущие на наночастицах катализатора; 4 – фехраль; 5 – “островки” оксидов алюминия и железа на поверхности фехраля после предварительной термообработки на воздухе; 6 – углеродные нановолокна, формирующиеся в пространстве между “островками” оксидов алюминия и железа.
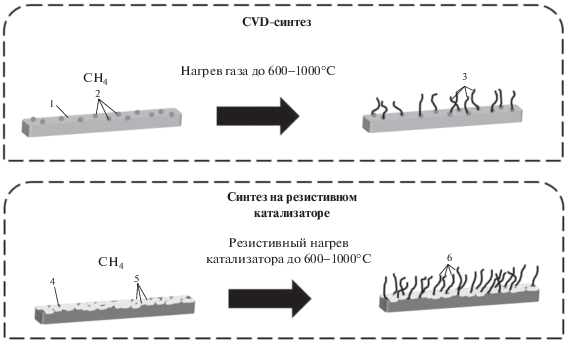
Для CVD-метода описан прием, заключающийся в формировании наночастиц катализатора в условиях воздействия реакционной смеси. W. Qian с коллегами использовал катализаторы на основе оксидов переходных металлов для разложения метана [66]. При этом восстановление оксидов металлов (NiO, CoO, Fe2O3) происходило in situ при температурах 550–850°С. Тепло, выделяющееся при восстановлении, способствовало протеканию эндотермической реакции разложения метана. В результате авторам удалось увеличить скорость превращения метана на катализаторе на основе оксида железа в 3–4 раза, а выход УНТ поднять до 0.14 гС/гкат. Развивая идею тепловой компенсации, данная исследовательская группа осуществила процесс разложения в присутствии ацетилена и этилена, рассматривая возможность их гидрирования образующимся водородом [67].
Массивные металлы также используются в классическом CVD-синтезе в качестве подложек, например Cu/Ta [68], сплав CuAl [69]. S. Talapatra и соавт. сформулировали основные преимущества выращивания НУМ на массивных металлах: 1) отсутствие пространственного ограничения на рост наноматериала, что обеспечивает формирование трехмерно ориентированных массивов НУМ; 2) возможность выращивать нанотрубки любой формы и размера [70]. Авторами получен материал на основе УНТ и никель-хромового сплава “инконель” (72% Ni, 16% Cr, 8% Fe), для которого продемонстрировано низкое контактное сопротивление между УНТ и подложкой – массивным сплавом. При этом снижение контактного сопротивления считается основной проблемой при разработке суперконденсаторов на основе УНТ. Рассчитанное значение емкости составило 18 Ф/г, что вполне приемлемо для практического применения.
Использование резистивного способа нагрева открывает новые возможности для воздействия на морфологию НУМ. На вид и количество образующихся НУМ оказывает влияние природа электрического тока (постоянный или переменный), наличие электромагнитного поля, природа самого резистивного материала. Резистивный материал может выступать и в качестве носителя для предшественника активного компонента, восстановление которого происходит in situ. Компоненты, остающиеся в форме оксидов в условиях синтеза, также оказывают влияние на процесс формирования НУМ.
ОСОБЕННОСТИ ОБРАЗОВАНИЯ НУМ
Р.А. Буянов и соавт. отмечали, что при выдерживании в метане исходно гладкая поверхность сплава подвергается значительному разрушению под воздействием углеродной эрозии, происходит микроструктурирование поверхности сплава, ведущее к формированию активных доменов, которые выступают в роли центров роста углеродных отложений (УО) по механизму карбидного цикла [7]. Авторы работы [15] фиксировали образование на резистивных фехралевых катализаторах слоя УО. Это также приводило к развитию углеродной коррозии, вызванной взаимодействием углерода с металлическими компонентами резистивных катализаторов, сопровождаемой появлением карбидов или трансформацией углерода по механизму карбидного цикла [3, 71]. Снимки НУМ, образующихся на резистивном фехралевом катализаторе, представлены на рис. 4.
Рис. 4.
Фехралевый резистивный катализатор после эксперимента. Фотографии сделаны с помощью оптического микроскопа при увеличении в 25 (а), 67 (б), 40 (в) и 100 раз (г). Диаметр проволоки – 0.25 мм.
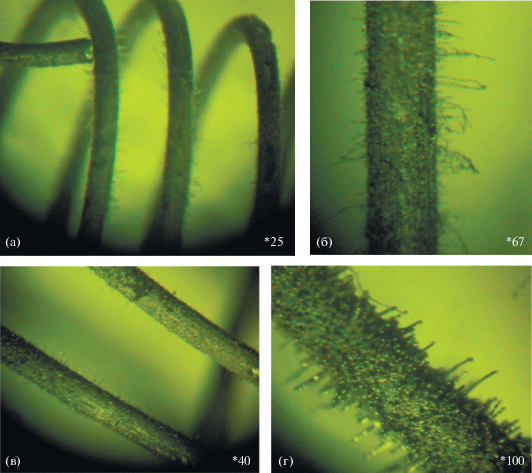
Данные оптической микроскопии, рис. 4, хорошо согласуются с результатами сканирующей электронной микроскопии (СЭМ), согласно которым на поверхности спирали формируются два типа углеродных отложений [15]. Первый тип представляет собой “столбики” высотой не более 30 мкм и диаметром 5–10 мкм. Второй тип – отложения в виде углеродных волокон, почти перпендикулярных поверхности. Эти волокна сложены из близких по размеру округлых частиц толщиной 2–4 мкм и имеют длину ≥100 мкм. Соответственно, фехралевый катализатор после эксперимента покрыт сплошной “корочкой” из УО первого типа, из которых выглядывают углеродные волокна второго типа длиной до 500 мкм. В УО на спирали обнаружены частицы катализатора разной степени дисперсности и разного состава. Присутствуют большие частицы диаметром до 5–7 мкм, частицы поменьше (0.2–2 мкм). Частицы катализатора состоят из углерода, карбидов, оксидов металлов, обнаружены частицы металлического железа, покрытые углеродом. Оксиды металлов и частицы, не содержащие металлического железа, неактивны в процессе образования углерода. По-видимому, эти частицы образуются при взаимодействии поверхности катализатора с углеродом, в результате чего происходит сегрегация входящих в катализатор химических элементов.
Закономерности образования УО на поверхности металлических катализаторов были предметом большого числа исследований [1, 7, 16, 20, 32, 33, 50, 51, 72–81]. Образование углерода на поверхности катализатора происходит через промежуточную стадию формирования карбида железа. Затем углерод растворяется и диффундирует по поверхности или по объему металлических частиц. Когда раствор углерода в металле становится пересыщенным, происходит его сегрегация. Атомы углерода диффундируют к поверхности и объединяются, образуя начальный слой графена. Эта ранняя стадия зарождения углерода на поверхности частиц является общей для НУМ разной морфологии – как для УНТ, так и для УНВ [1, 75, 77, 78].
В работах [1, 7, 32, 50, 80, 81] определены особенности формирования УО различной морфологии на поверхности металлических катализаторов: 1) установлены интервалы размеров, за пределами которых металлические частицы обволакиваются углеродом и теряют возможность проявлять свои каталитические свойства, в частности, для железа этот интервал имеет пределы от ~30 до ~10 000 Å; 2) диаметр растущих нитей определяется диаметром металлической частицы, диаметры нитей для катализатора – железа составляют от 100 до более 10 000 Å; 3) выросшие нити имеют различную форму (петли, спирали, сплетенная масса); 4) время формирования углеродной нити зависит от температуры реакции и может определяться как секундами, так и десятками минут. В процессе роста НУМ происходит вторичное отложение углерода. Этот вторичный, “некаталитический”, углерод имеет иную структуру и ведет к снижению механических свойств НУМ.
Особенности реализации механизма карбидного цикла на железе, отмеченные в [1] (большой коэффициент диффузии углерода в объеме металла, обеспечивающий его быстрое поступление к различным участкам поверхности; склонность металлического железа к образованию карбидов) способствуют развитию углеродной коррозии и отмеченному в [15] разрушению спиралей из фехралевого сплава. Процесс формирования УО, инициированный в начале эксперимента наночастицами железа и хрома, восстановившимися из их оксидов, в итоге приводит к тому, что углерод, проникая через оксидный слой, начинает растворяться в основной массе сплава, разогретого до высокой температуры. Это способствует образованию карбидов, их сегрегации и нарушению сплошности структуры сплава. Определенную роль в развитии процессов углеродной коррозии играет факт направленного движения свободных электронов в структуре сплава, через который протекает электрический ток. Однако соответствующие закономерности из литературы не известны, кроме факта зависимости морфологии углеродных отложений от типа тока, используемого для резистивного нагрева [10].
На примере никелевых катализаторов авторы [1] рассмотрели такой фактор, как присутствие водорода в реакционной смеси, и пришли к выводу, что его наличие приводит к возникновению конкурирующей реакции метанирования атомов углерода и зародышей фазы графита. Углерод в итоге откладывается по границам микрокристаллитов, слагающих наночастицу металла, что вызывает ее дробление и формирование углеродных нитей. В то же время при разбавлении углеводорода инертным газом аргоном высока вероятность формирования углеродных отложений в виде пленки на лобовой стороне частицы, так как конкурирующая стадия разрушения углеродсодержащей нанофазы не реализуется.
Отдельно в работе [1] рассмотрен процесс формирования НУМ в условиях классического CVD-синтеза на частицах железа при температурах 1000°С и выше и отмечено, что в данных условиях длина углеродных нитей может достигать нескольких миллиметров. Структура этих нитей сложена цилиндрическими плоскостями графита с полым каналом посередине, появление которого хорошо трактуется из термодинамических соображений, поскольку формирование полой сердцевины энергетически выгоднее, чем сильно искривленных графитовых плоскостей. Такие температуры реализуются в режиме резистивного катализа [2, 8–15] с образованием НУМ миллиметровой длины (рис. 2).
Важность такого параметра, как температура, исследовали I. Hasanzadeh с коллегами, отметив 400°C как температуру начала процесса активного формирования нанотрубок на железном катализаторе и определив оптимальный температурный интервал для их синтеза 700–750°C [17]. В то же время при резистивном катализе на процессе роста углеродных нитей при их длинах в несколько миллиметров должен сказываться температурный градиент, так как нагретый до высокой температуры резистивный катализатор контактирует с газовой смесью, имеющей температуру близкую к комнатной. Вблизи резистивного катализатора формируется высокотемпературная зона, диаметр которой, очевидно, определяет максимальную длину волокон, если они растут перпендикулярно поверхности катализатора, что выполняется для большинства нитей (рис. 2). Как только частица металла, находящаяся в головке нити, достигает расстояния от поверхности катализатора, на котором температура падает ниже 600°С, процесс разложения метана на ее поверхности прекращается, и рост нити останавливается. Диаметр высокотемпературной зоны определяется теплопроводностью газовой смеси, и, вследствие этого, морфология образующихся на поверхности катализатора углеродных отложений меняется не только при введении в газовую смесь реакционноспособного газа – водорода, но и при разбавлении метана инертными газами – гелием, аргоном, азотом. С другой стороны, из литературы известно, что возможны два механизма роста нитей НУМ [1, 16, 20, 82]. Кроме вышеописанного “tip growth” (концевой механизм) при высокой адгезии частиц металла к носителю рост возможен по механизму “base growth” или “root growth” (базовый или корневой механизм, который носит также название экструзионного). Так R.J. Cartwright с коллегами [82] обнаружил, что в процессе роста НУМ на напыленной на углеродный носитель пленке железа реализуется “root growth” механизм, наночастицы остаются на носителе, в кончиках нанотрубок и нановолокон углерода отсутствуют частицы металла. При реализации “root growth” механизма в условиях резистивного катализа частица металла остается на месте, в высокотемпературной зоне, и размер нитей, соответственно, может быть больше диаметра этой зоны.
L.S. Lobo с коллегами обратили внимание на то, что температура синтеза определяет по какому пути – каталитическому или пиролитическому – пойдет процесс формирования НУМ [83]. Важным в этой концепции является параметр, называемый температурой Таммана и определяемый как 1/2 температуры плавления соответствующего металла (например, для железа авторы определили температуру Таммана равной 632°С). Реализация каталитического пути возможна выше этой температуры. Авторы работы [83] особо отмечают, что наночастицы металла при температуре выше температуры Таммана нельзя рассматривать как находящиеся в расплавленном или жидкоподобном состоянии, поскольку жидкость не имеет постоянной структуры, а “каталитический” механизм роста с диссоциативной адсорбцией метана, растворением углерода в объеме частицы и его сегрегацией в виде графенового слоя возможен только для частиц, сохраняющих определенную структуру [83]. L.B. Avdeeva с коллегами считает, что только путь реакции через разложение нестабильных “виртуальных” карбидоподобных фаз металла приводит к появлению НУМ [23]. Образование стабильных карбидов при высоких температурах (800°C для Fe) способствует быстрой дезактивации металлических катализаторов. В то же время на резистивных катализаторах рост углеродных нитей происходит и при температурах катализатора выше 1000°С, однако это противоречие снимается, если вспомнить, что температура быстро снижается при удалении от поверхности резистивного катализатора [85–88].
В работе [88] авторами была предложена модель, которая хорошо описывает экспериментальные данные по росту углеродных волокон на наночастицах железа из метана при температуре 1050°C. Это близко к температуре, при которой исследовали рост НУМ на резистивных катализаторах [2, 10, 11, 14, 84–87]. Согласно этой модели, длина нитей l связана с концентрацией метана и временем уравнением (1):
где [CH4] – концентрация метана в единицах парциального давления, τ – время от начала роста нити до дезактивации катализатора; a – параметр, определенный авторами величиной 0.0218 см с–1 атм–2. Применение этого уравнения к расчету времени дезактивации в условиях резистивного катализа при концентрации метана 15 об. % и, соответственно, парциальном давлении 0.15 атм, длине нити в 100 мкм [15] дает величину в 20 с. Авторы [2, 8–15] оценивают время формирования углеродных отложений величиной в несколько минут, однако следует учитывать и время, необходимое для восстановления оксида железа до металла, которое, видимо, и определяет период индукции.В.В. Чесноков и Р.А. Буянов предложили формулу для расчета линейной скорости роста нити [1]:
Определения и размерности величин, входящих в формулу, представлены в табл. 1.
Таблица 1.
Линейная скорость роста углеродных нитей при резистивном катализе
Параметр | Размерность | Величина | Ссылка |
---|---|---|---|
V, линейная скорость роста нити | см/с | 1 × 10–5 | [1] |
D, коэффициент диффузии углерода в металле | см2/с | 3.87 × 10–8 | [1] |
С1, концентрация углерода в поверхностном карбидоподобном соединении | г/см3 | 0.52 | Настоящая работа |
С2, концентрация углерода в насыщенном растворе углерода в металле | г/см3 | 1.57 × 10–3 | Настоящая работа |
L, диаметр металлической частицы в конце нити | См | 1 × 10–3 | Настоящая работа |
$\rho ,$ плотность графита | г/см3 | 2 | [1] |
Применение этой формулы к результатам, полученным в [15], с учетом коэффициента диффузии, вычисленного по данным [1], оценки концентрации С1 на уровне концентрации углерода в феррите, а концентрации С2 – на уровне концентрации углерода в цементите, оценки диаметра металлической частицы в 10 мкм [15], приводит к величине линейной скорости роста нити в 10 мкм/с. Это дает длину нити в 200 мкм за время от начала роста до дезактивации в 20 с, рассчитанное по модели [88], что вполне соответствует экспериментальным результатам [15].
МЕТАЛЛИЧЕСКИЕ КОМПОНЕНТЫ КАТАЛИЗАТОРА
Изменение природы металлического катализатора позволяет регулировать морфологию УО. Так, в ряде публикаций отмечали возможность воздействовать на морфологию образующихся углеродных материалов путем изменения структуры металлического катализатора [1, 24, 88–90]. Было установлено, что природа катализатора влияет на микроструктуру нити. Это проявляется в изменении угла между графитовыми плоскостями и осью нити от 45° для Ni-катализатора до 15° для Co-катализатора. В отличие от никеля, углеродные волокна, полученные на катализаторах на основе кобальта, имеют графитовые плоскости, параллельные оси волокна с полой сердцевиной, образующей многослойные углеродные нанотрубки. R.T.K. Baker с коллегами отметил важную роль сильного взаимодействия металл–носитель (SMSI-эффект), приводя пример, когда прочное взаимодействие между частицами рутения и носителем (графит, кремнезем) приводит к тому, что каталитически активная частица остается на поверхности носителя, а кристаллографические грани, на которых происходит осаждение углеводорода и выделение углерода, “меняются местами”, и образование углеродных волокон происходит в режиме экструзии [22].
Металлическая компонента резистивного фехралевого катализатора представлена железом и хромом (алюминий на поверхности катализатора находится в фазе оксида), которые также оказывают влияние на процесс пиролиза метана, а формирующиеся НУМ – на превращения и распределение металлов в массиве катализатора.
УО на фехралевой спирали начинают образовываться при температуре выше 800°С [15]. Рентгенофазовый анализ обнаруживает в составе катализатора после эксперимента карбид железа Fe7C3, графит, корунд α-Al2O3, α-Fe и небольшое количество фаз Fe4C0.63 и Cr23C6. Согласно результатам EDX-анализа происходит перераспределение железа и хрома и резкое (в разы) увеличение содержания углерода в объеме фехралевой проволоки. Полученные результаты свидетельствуют в пользу реализации механизма “карбидного цикла” при формировании НУМ. При этом железо выступает, очевидно, катализатором. Хром может быть как катализатором, так и агентом, способствующим восстановлению оксида железа. Так, Zhang Q. и соавт. указывают, что в качестве катализаторов для получения НУМ могут служить железо, хром и оксид алюминия [91]. Авторы [29] упоминают, что мелкие частицы переходных металлов, таких как Ni, Fe или Cr, могут катализировать формирование УНВ при пиролизе углеводородов. G.G. Tibbetts с коллегами [51] отмечал двойственную роль хрома, фиксируя образование карбидов M7C3 (M = Fe или Cr) как фактор, способствующий большей фрагментации поверхности стальной трубки по сравнению с трубкой из стали, не содержащей хром. Эта фрагментация благоприятствует формированию центров роста НУМ, а карбиды выступают в качестве катализаторов пиролиза метана.
Присутствие меди в сплаве с железом приводит к снижению температуры, при которой последнее может быть восстановлено до металлического состояния [92–95]. Недавно описано подобное действие хрома на способность к восстановлению никеля и молибдена [96]. Весьма вероятно, что хром оказывает, подобно меди, влияние на способность к восстановлению железа в фехрале. Это ускоряет процесс генезиса первичных частиц железа из его оксида, присутствующего в слое, сформировавшемся на поверхности фехралевой проволоки в ходе окислительной обработки.
В ряде работ также было отмечено, что при разложении метана на порошке железа образуются два вида НУМ, луковичный углерод и УНТ [75, 76, 97]. Ранее в [15] было описано образование УО двух типов. Согласно [1] для образования центра кристаллизации углерода на металлической частице необходимо преодолеть энергетический барьер в 220–300 кДж/моль. Если энергии недостаточно для зарождения УНТ или УНВ, углерод будет осаждаться в виде пленки, инкапсулирующей частицы металла, и образовывать луковичную структуру, что в конечном итоге дезактивирует катализаторы. В условиях резистивного катализа этот процесс может развиваться, когда растущие углеродные нити проходят через оксидный слой и начинают взаимодействовать с массивным сплавом.
ОКСИДНЫЕ КОМПОНЕНТЫ КАТАЛИЗАТОРА
На первый взгляд оксидная компонента резистивного катализатора не должна играть значительной роли в процессе формирования углеродных отложений. Однако экспериментальные результаты, полученные при исследовании нанесенных на резистивные катализаторы оксидов алюминия, магния, циркония, показали, что на этих фазах также происходит формирование НУМ. Возможность развития такого процесса подтверждается и литературными данными для других систем.
Рассмотрим подробнее процесс формирования оксидного слоя на поверхности фехраля. Подготовка фехраля включала несколько операций [8, 12]. Проволоку массой 0.26–0.28 г скручивали в спираль с внешним диаметром 5 мм, обезжиривали промыванием в ацетоне и прокаливали на воздухе в муфельной печи при температуре 1000°С. Авторы [8] изучали влияние условий нагрева (конвективный и резистивный) на морфологию поверхности фехралевого катализатора и формирование активных центров реакции пиролиза метана. При конвективном нагреве образец выдерживали в муфельной печи с варьированием времени термоокислительной обработки от 2 до 22 ч. При резистивном нагреве на проволоку при помощи источника постоянного тока подавали напряжение в интервале 15–20 В, что позволяло нагревать ее до температуры 1000°С. Время воздействия электрического тока составляло 0.2–10 мин.
В результате такой окислительной термообработки на поверхности сплава образуется оксидный слой, состоящий в основном из α-оксида алюминия, а также гематита [8, 12]. Однако если при конвективном нагреве для завершения формирования активной поверхности было необходимо длительное воздействие в течение 20 ч, то при резистивном нагреве фехралевой проволоки оно сократилось до 5–10 мин. Методом локального химического анализа также подтверждено, что независимо от способа термообработки происходит практически одинаковое изменение химического состава поверхностного слоя фехралевой проволоки. Содержание железа в среднем падает с 54.5 до ~20%, хрома – с 21.5 до ~11–15%, при этом в 4–5 раз возрастает содержание алюминия (до 27%) и кислорода (до 34–36%). Распределение элементов на поверхности неравномерное – алюминий в составе оксидной фазы представлен протяженными объемными образованиями, которые разделяют участки, обогащенные железом и хромом.
Метод термического воздействия на фехралевую проволоку оказывает существенное влияние на морфологию поверхности [8]. Быстрый резистивный нагрев всего объема проволоки (в отличие от постепенного конвективного нагревания, начиная с поверхности образца) приводит к более интенсивному образованию фазы оксида алюминия, которая равномернее распределяется по поверхности катализатора. В результате участки, содержащие оксиды железа и хрома, оказываются разделенными фазой оксида алюминия и в дальнейшем способны к формированию дисперсных частиц активного металла. При использовании катализатора, активированного нагревом электрическим током, рост НУМ происходит интенсивнее по сравнению с образцом, предобработка которого проводилась длительным конвективным нагреванием. Наблюдаемый эффект связан с присутствием большего количества дисперсных частиц железа, равномерно распределенных по поверхности проволочного фехралевого катализатора. Таким образом, оксид алюминия может играть структурообразующую роль, способствуя проявлению каталитических свойств.
В работе [9] в качестве носителя применяли термически обработанный фехраль. Были приготовлены катализаторы SiO2/FeCrAl, ZrO2/FeCrAl и Al2O3/FeCrAl и изучены их свойства в пиролизе метана в режиме резистивного нагрева. Исследование показало наличие характерных НУМ в виде столбиков, сходных с полученными на исходном носителе. Однако НУМ на нанесенных на фехраль катализаторах различались высотой и диаметром углеродных нитей. Поверхность SiO2/FeCrAl была покрыта сплошным слоем УО, на котором выделялись бугорки углерода высотой не более 10–20 мкм. На поверхности ZrO2/FeCrAl на фоне слоя УО наблюдали столбики углерода высотой 100 мкм и больше. НУМ, сформировавшиеся на образце Al2O3/FeCrAl, сходные с НУМ, полученными на поверхности исходного термообработанного фехраля. Таким образом, оксид алюминия принимает участие в образовании углеродных волокон. Но если в случае нанесенных на фехраль оксидов процесс формирования УО можно связать с диффузией метана через оксидный слой и последующим взаимодействием его с кристаллитами железа, то процесс формирования НУМ на оксидах, нанесенных на карборунд (описание этого эксперимента представлено ниже), можно объяснить именно каталитическим действием этих оксидов, поскольку сам карборунд малоактивен в пиролизе метана.
Оксидные материалы могут быть темплатами при образовании графена. В качестве темплатов в литературе предложены MgO, ZnO, CaO и SiO2 [28, 84, 85, 98–101]. Полученный с их применением графен характеризовался высокой удельной поверхностью, чистотой, электропроводностью, что позволяло рассматривать его в качестве перспективного электродного материала для суперконденсаторов. X. Zhu с коллегами использовал систему Fe/MgO для приготовления композиционного углерод-углеродного материала [102]. MgO служил темплатом для выращивания графена, а частицы железа на этом носителе – катализатором для синтеза УНТ. Соотношение графена и УНТ в композитах можно было контролировать, изменяя содержание компонентов катализатора. Композитный материал отличался значительной величиной удельной поверхности (600–1650 м2/г) и высокой порозностью (0.8–0.9).
Z. Dong с соавторами отмечали, что для выращивания УНТ на нанесенном железном катализаторе желательно не применять носитель с кислотными центрами, так как на этих центрах происходит отложение неструктурированного углерода [28]. Y. Liu с коллегами сформулировал три условия для успешного синтеза одностенных УНТ: 1) низкая скорость превращения метана; 2) низкая активность железного катализатора; 3) использование основного носителя для подавления процессов образования аморфного углерода [61]. Низкая скорость образования углерода – ключевое условие, которое, по мнению авторов, позволяло сформировать УНТ, а не аморфный углерод. В работе [103] авторы допировали катализатор синтеза двустенных УНТ Fe/MgO алюминием и связывали образование аморфного углерода с появлением фазы MgAl2O4, отличающейся высокой кислотностью.
C. Cui с коллегами вырастили нановолокна графена без применения металлического катализатора [100]. Авторы использовали в качестве предшественника темплата MgCO3 ⋅ 3H2O. В процессе медленного нагревания предшественник разлагался, давая высокопористый оксид магния. Далее, при 950°С, в присутствии сформированного темплата проводили разложение метана, при этом на поверхности темплата образовывались волокна графена. Материал представлял собой трехмерную структуру с удельной поверхностью близкой к 1300 м2/г.
Таким образом, оксидные материалы, находящиеся на поверхности фехралевого катализатора, также могут принимать участие в формировании НУМ из метана. В пользу этого говорят результаты исследования катализаторов на основе оксидов кремния, циркония и алюминия на резистивном материале карборунде, где тоже было зафиксировано образование углеродных волокон в отсутствие металлов [9, 11].
ВЛИЯНИЕ СОСТАВА ГАЗОВОЙ СМЕСИ
Углеродные наноматериалы, формирующиеся в процессе пиролиза метана на резистивном фехралевом катализаторе, отличаются разнообразной морфологией. Это могут быть нити, волокна, трубки, “луковицы”. Установлено, что форма полученных частиц определяется не только природой катализатора и условиями процесса пиролиза, но и существенно зависит от вида инертного газа-разбавителя, изменяющего теплопроводность газовой смеси.
В публикации [14] получены зависимости выхода НУМ от времени при температурах 900, 1100, 1300°С в среде метана и его смесей с инертными газами – аргоном и гелием. Показано, что эти зависимости имеют линейный характер для всех исследованных температур, времен контакта и составов газовых смесей. Максимальный выход НУМ в среде 100%-ного метана после 90 мин эксперимента составляет 209 × 10–5 г/см2. Снижение концентрации метана до 40 об. % при разбавлении аргоном или гелием приводит к уменьшению количества НУМ. Наблюдаемый уровень сокращения выхода НУМ зависит от природы инертного газа. В среде CH4–He выход НУМ примерно пропорционален доле метана в газовой смеси. В аналогичных условиях в среде CH4–Ar этот показатель существенно ниже и составляет 40 × 10–5 г/см2. Повышение температуры катализатора от 900 до 1300°С независимо от природы инертного газа способствует монотонному росту скорости образования НУМ, однако наименьшая скорость образования УО наблюдается в присутствии аргона. Авторы связывают такой эффект с различиями в характере взаимодействия аргона и гелия с молекулами метана на поверхности катализатора, которое происходит в соответствии с ударным механизмом. Известно, что энергия, передающаяся при соударении падающей молекулы инертного компонента с молекулой метана, находящейся у поверхности, прямо пропорциональна площади соударения (площади сечения для модели жестких сфер) и числу столкновений молекул с поверхностью. Это можно выразить в виде простого уравнения (3):
где k – константа, отражающая геометрический фактор (долю пересечения площадей (сегментов) соударяющихся молекул на поверхности); M – молекулярная масса молекул; d – кинетический диаметр молекул.Авторы показали, что с учетом величины кинетических диаметров молекул СН4, Ar и He (0.38, 0.34 и 0.26 нм соответственно) и близости констант k этих молекул, поскольку все молекулы имеют сферическую форму, отношение нормированных значений энергий соударения на поверхности для рассмотренных молекул составляет E(CH4) : E(Ar) : E(He) = 1 : 0.5 : 1. Таким образом, соударяющиеся на поверхности катализатора молекулы метана и гелия обладают близкой энергией соударения, вдвое превышающей энергию соударения метана с аргоном. Механизм ударно индуцированной диссоциации (“hammer effect”) предполагает следующее условие разложения молекулы метана на металлических катализаторах [85, 104, 105]. Энергия налетающей на метан молекулы должна быть достаточной для такой деформации молекулы метана, которая обеспечивает необходимое сближение атома углерода с поверхностью металла, ведущее к распаду связей C–H и образованию связи С–М (М – металл). Очевидно, что реализация данного механизма возможна в среде “высокоэнергетических” молекул метана и гелия на поверхности фехралевой проволоки. В этом случае под ударами молекул гелия или метана молекулы метана, находящиеся на поверхности катализатора, подвергнутся диссоциации, а количество образующихся на поверхности НУМ будет определяться содержанием метана в газовой смеси. Именно такой эффект разбавления наблюдали авторы при использовании газовых смесей метана с гелием с содержанием метана 70 и 40 об. %. В то же время энергия соударения аргона с метаном, вероятно, является недостаточной для деформации молекулы метана и ее диссоциации на поверхности, вследствие чего в присутствии аргона процесс формирования НУМ значительно замедляется.
С помощью электронной микроскопии установлено, что при разложении 100%-ного метана образуются углеродные волокна длиной до 150 мкм и диаметром 2–3 мкм [14]. Методом локального химического анализа показано, что волокна состоят преимущественно из углерода, а содержание кислорода и металлов не превышает 3 мас. %. В среде аргона на поверхности проволоки наблюдаются лишь отдельные участки, покрытые углеродом неидентифицируемой морфологии. В присутствии гелия волокна растут из приповерхностного слоя, расположены близко друг к другу и имеют небольшую длину (до 8–10 мкм). Они состоят преимущественно из углерода (97 мас. %). Таким образом, применение смесей метана с инертным газом позволяет варьировать морфологию УО.
В работе [2] изучали УО, полученные в ходе пиролиза метана на фехралевой проволоке выше 1050°С. Они также представляют собой углеродные волокна различного диаметра и морфологии в зависимости от природы инертного газа-разбавителя (содержание метана в реакционной смеси составляло 15 об. %). Авторы отмечают, что, поскольку углеродные волокна обладают электропроводными свойствами, на направление, и, вероятно, скорость их роста влияет электромагнитное поле, образующееся при протекании тока по фехралевой проволоке. В среде аргона формируется волокнистый углерод, диаметр волокон достигает 15 мкм, волокна сильно переплетены друг с другом. Методом ПЭМ установлено наличие канала внутри волокон, что позволяет отнести их к многослойным нанотрубкам. С увеличением продолжительности процесса возрастают длина и диаметр образующихся УНТ. Между тем, влияние аргона на процесс формирования УО из метана неоднозначно и зависит от природы катализатора. Так, авторы [106] установили, что при синтезе одностенных нанотрубок на катализаторе 10%Fe/MgO увеличение доли метана в смеси с Ar дает более неупорядоченный углерод.
В среде азота образуются волокна диаметром 15 мкм, однако они более короткие, чем УНВ, возникающие в среде аргона, и не переплетаются друг с другом [2]. Морфология этих волокон отличается от таковых, формирующихся в среде аргона. Согласно данным ПЭМ, они состоят из овальных образований, каждое из которых сложено сужающимися и расширяющимися концентрическими слоями углерода, вложенными друг в друга. Авторы полагают, что НУМ сложены близкими по размеру, почти сферическими формами вследствие колебаний скорости роста УНВ в ходе эксперимента.
В среде гелия диаметр генерирующихся волокон составлял порядка 5 мкм, при этом не наблюдалось переплетения между волокнами [2]. Как отмечают авторы, различная морфология углеродных отложений может быть обусловлена различной теплопроводностью реакционной смеси. Газ на разогретый катализатор поступает холодным, поэтому в окружающее пространство выходит тепловой поток (аналогичный стефановскому потоку при каталитических экзотермических реакциях). Как следствие, пограничный слой вокруг катализатора будет иметь различную толщину, определяя концентрацию углеводородных радикалов и кластеров углерода, ушедших с поверхности, и градиент температуры от поверхности. В результате будут образовываться наиболее стабильные в данных условиях морфологические формы.
В работе [9] описано разложение метана на резистивном фехралевом катализаторе в смеси 15 об. % CH4 в азоте. Авторы обнаружили на поверхности спирали “столбики” высотой не более 30 мкм и диаметром 5–10 мкм, а также почти перпендикулярные поверхности фехралевой проволоки углеродные волокна длиной ~100 мкм и диаметром 2–4 мкм.
Влияние на морфологию УО оказывает введение в реакционную смесь и других газов. Так, авторами [12, 13] найдено, что кислород при наличии его в газовой смеси задерживает образование карбидов железа на поверхности фехраля, поэтому активное разложение метана на углерод (с появлением НУМ), водород и карбиды металлов на металлических центрах катализатора начинается при достижении температуры 900°С. В присутствии кислорода углеродные отложения имеют вид нитей длиной ≥100 мкм и диаметром до 25 мкм. Нити сложены из близких по размеру округлых плоских частиц толщиной 2–4 мкм.
Оказывать влияние на процесс формирования НУМ может не только молекулярный, но и решеточный кислород. Так, авторы [67] нашли, что выход УНТ в комбинированном процессе восстановления катализаторов (Co–Mo/Al2O3, Cu–Ni/Al2O3, Fe–Mo/Al2O3) и разложения метана примерно в 3–4 раза выше, чем в присутствии восстановленных катализаторов, объясняя наблюдаемый эффект фактором сдвига равновесия разложения метана за счет частичного поглощения водорода и углерода решеточным кислородом.
Пары воды также оказывают положительное воздействие на стабильность катализатора. В публикации [107] авторы описали способ повышения активности и стабильности катализатора. В реакционную смесь добавляли небольшое количество воды, при этом фиксировали удаление отложений аморфного углерода, формирующихся вблизи наночастиц катализатора, и резкий рост скорости роста УНТ (более чем в 4 раза) до 80–90 мкм/с.
Согласно [13] при разложении метана на фехралевом резистивном катализаторе в присутствии в газовой смеси более сильного восстановителя – водорода – восстановление центров МеОх наблюдали сразу по достижении катализатором температуры 600°С. При этой температуре также начинается разложение метана на восстановленных металлических центрах. Авторы отмечали, что образование карбидов железа и рост на карбидах и металлическом железе каталитического волокнистого углерода приводит к коррозии катализатора, однако в условиях водородного пиролиза фехралевая спираль работает значительно дольше, чем в условиях бескислородного. Факт значительного замедления разрушения фехралевой спирали связывают с метанированием водородом УО на поверхности фехраля. Аналогичную роль водороду отводят и авторы [1]. Как сообщается в этой публикации, добавление водорода в реакционную смесь предотвращает отложение углерода в виде пленки и способствует формированию углеродных нитей. В присутствии водорода скорость образования НУМ замедляется, появляется период индукции, так как атомы углерода и зародыши графита, находящиеся на поверхности катализатора, подвергаются гидрированию. В итоге процесс формирования зародышей графита происходит вдоль межкристаллитных границ, куда диффундируют атомы углерода и куда затруднен доступ водорода. Растущие зародыши разрушают частицы по межкристаллитным границам и благоприятствуют росту углеродных нитей, которые водород гидрировать не способен.
Водород играет важную роль, реконструируя поверхность, поддерживая поверхность катализатора свободной от углерода [75]. Авторы [75] считают, что рост НУМ возможен в присутствии водорода, поскольку он инициирует сегрегацию графенового слоя в виде листов графита вместо образования фуллереноподобной “шапки” и поддерживает этот процесс за счет насыщения некомпенсированных связей графитовых листов. Аналогично в [108] отмечают, что в присутствии водорода углерод должен накапливаться в виде открытых форм, на внешнюю поверхность которых выходят торцевые грани графита с ненасыщенными связями (нанотрубки, волокна), а водород насыщает эти связи. В отсутствие же водорода на поверхности катализатора формируются закрытые формы с минимумом ненасыщенных связей, например, пленки. Однако авторы [1] cкептически относятся к данной версии, справедливо полагая, что существуют и иные возможности компенсации свободных валентностей – путем взаимодействия с другими молекулами, за счет контакта графитовых листов между собой, отдавая приоритет кинетическим аспектам, изменению механизма образования зародышей графита, которые формируются не на торцевой поверхности частицы катализатора, а на межкристаллитных границах.
Таким образом, можно заключить, что варьирование состава газовой смеси дает возможность направленного регулирования морфологии НУМ в условиях резистивного катализа.
ВЛИЯНИЕ ПРИРОДЫ ЭЛЕКТРИЧЕСКОГО ТОКА
Из литературы известно, что выход углеродных волокон оказывается почти в 2 раза выше в присутствии электромагнитного поля, а увеличение напряженности этого поля приводит к уменьшению расстояния между растущими углеродными волокнами [87]. Аналогичный эффект можно наблюдать и на резистивном фехралевом катализаторе (рис. 2а) – углеродные нити в пространстве между витками спирали немного длиннее остальных волокон.
Авторы [10] изучали влияние типа электрического тока, пропускаемого через резистивный фехралевый катализатор (постоянный или переменный ток), на природу образующихся при разложении метана УО. Исследования проводили при температуре катализатора 1100°С, время эксперимента составляло 90 мин. В реактор подавали газ (Т = 20°С), который представлял собой либо 100% метан, либо смесь 70 об. % метана и 30 об. % гелия. Расход газа во всех случаях был 40 мл/мин. Электромагнитное поле создавалось электромагнитной катушкой длиной 0.15 м, внутренним диаметром около 0.1 м с количеством витков 2050 ± 15. Напряженность магнитного поля ~ 10 кА/м.
При нагревании резистивного катализатора постоянным электрическим током разбавление метана гелием до 70 об. % приводит к пропорциональному снижению выхода углерода с 1.8 до 1.2 мг/см. Изменение вида электрического тока с постоянного на переменный значительно повышает выход НУМ как для 100% метана, так и для смеси метан–гелий. Возможной причиной роста количества углеродных волокон при нагревании катализатора переменным током авторы считают наличие переменного электромагнитного поля вокруг фехралевой проволоки. Это поле, меняя свое направление 50 раз в секунду, вероятно, способствует активации металлических частиц и их миграции по углеродному волокну. Увеличение напряженности электромагнитного поля при использовании внешней электромагнитной катушки ведет к дополнительному повышению скорости роста углеродных волокон. В результате выходы НУМ для метана и смеси метана и гелия составили 4.5 и 2.8 мг/см соответственно, что в 2.3–2.5 раза выше, чем выходы, достигнутые при нагревании проволоки постоянным током.
Тип используемого электрического тока практически не влияет на морфологию образующихся НУМ [10]. С помощью СЭМ было установлено, что в случае 100% метана изменение тока с постоянного на переменный приводит к увеличению диаметра образующихся плотно прилегающих друг к другу волокон с 2 до 4 мкм при сохранении их морфологии и длины (100 мкм). Путем локального химического анализа было показано, что волокна состоят в основном из углерода и содержат частицы металлов (Al, Fe, Cr) в количестве, не превышающем 3 мас. %. УО, сформировавшиеся в присутствии гелия на фехрале также имеют сходную морфологию, которая, однако, отличается от морфологии УО, сформировавшихся в среде 100% метана. Эти НУМ сложены из частиц, имеющих форму близкую к сферической, размер составляет 8–10 мкм.
Увеличение напряженности электромагнитного поля при использовании внешней электромагнитной катушки привело не только к дополнительному увеличению выхода УО, но и к изменению их морфологии [10]. Образовавшиеся волокна генерируют фрактальную структуру. Это, вероятно, связано с миграцией наночастиц катализатора и соответствующим ростом углеродных волокон в направлении чередующихся силовых линий электромагнитного поля. НУМ, синтезированные в среде 100% метана, имеют диаметр в основании до 90 мкм, который постепенно уменьшается до <10 мкм в головке волокна. Снижение концентрации метана до 70% ведет к образованию более тонких волокон, диаметр которых в основании составляет до 15 мкм и которые также уменьшаются в диаметре от основания к головке. Диаметр самых тонких волокон равен <1 мкм.
Таким образом, электромагнитное поле является одним из факторов, позволяющих управлять морфологией и выходом НУМ на резистивном катализаторе.
КАРБОРУНД КАК РЕЗИСТИВНЫЙ КАТАЛИЗАТОР ДЛЯ СИНТЕЗА НУМ
Как было отмечено в [15], при высоких температурах происходит углеродная коррозия металлов с образованием фаз карбидов, что может приводить к разрушению катализаторов. Соответственно, весьма интересно было в целях повышения стабильности катализаторов и увеличения выхода НУМ найти резистивный материал, устойчивый к углеродной коррозии.
Авторы [9] обратили внимание на материал карборунд. Карборунд отличается от металлических катализаторов тем, что он уже является карбидом, а значит, не будет подвергаться углеродной коррозии. Кроме того, SiC рассматривали в качестве носителя катализаторов, активных в реакции пиролиза метана. Для нанесения на карборунд в качестве активных компонентов были выбраны оксиды, соответствующие оксидам, присутствующим на поверхности подвергнутого окислительной обработке фехралевого сплава: оксиды железа, хрома и алюминия, а также были приготовлены образцы ZrO2/SiC и SiO2/SiC. На чистом карборунде формируется практически однородный слой углерода, на котором редко обнаруживаются агломераты, покрытые игольчатыми углеродными волокнами.
Катализаторы с нанесенными на карборунд оксидами железа и хрома не удалось нагреть до температур выше 1100°С вследствие резкого возрастания электропроводности, что, по мнению авторов, могло быть связано как с восстановлением оксидов до металлов, так и с образованием слоя токопроводящего углерода на катализаторе. Авторы [9] на нанесенных на карборунд оксидах железа и хрома наблюдали картину, очень похожую на результат эксперимента с использованием чистого карборунда: однородное покрытие поверхности катализатора углеродом с редким включением агломератов, сложенных игольчатыми УНВ. На отработавших катализаторах с нанесенными на карборунд оксидами циркония, кремния и алюминия был зафиксирован толстый слой углерода, на котором находились УНВ. Волокна были сходны по морфологии с теми, что были получены на термообработанном фехрале. Результаты исследования методом электронной микроскопии позволили авторам заключить, что на нанесенных на карборунд оксидах железа и хрома формируется пиролитический углерод, в то время как на поверхности катализаторов Al2O3/SiC, ZrO2/SiC и SiO2/SiC появляются волокнистые НУМ.
Как отмечают авторы, механизм роста углеродных волокон на оксидах, очевидно, отличается от механизма “карбидного” цикла и, вероятно, основан на реализации экструзионного режима, а перестройка графеновых плоскостей в волокна связана с действием электромагнитного поля. Оксиды железа и хрома не проявляют каталитических свойств, при этом скорость их восстановления, по всей видимости, ниже скорости образования пиролитического углерода, катализируемого карборундом. В итоге оксиды железа и хрома на поверхности карборунда блокируются пиролитическим углеродом. Проводя аналогию с фехралем, можно предположить, что основной источник металлических частиц катализатора для формирования НУМ – это кристаллиты, появляющиеся при разрушении массивного сплава, а не частицы, образующиеся при восстановлении оксида железа, присутствующего на его внешней поверхности.
В работе [11] пиролиз газовой смеси, состоящей из 15% метана в азоте, проводили на резистивном катализаторе ZrO2/SiC. Авторы установили, что в исходном катализаторе активный компонент, оксид циркония, формирует пленку, состоящую из мелких плоских частиц и практически полностью закрывающую поверхность носителя. В отсутствие кислорода бóльшая часть метана разлагается на катализаторе до углерода. Так, при температуре 950°С в углерод превращается 93% прореагировавшего метана, при 1100°С в виде углерода на катализаторе отлагается более 85%, при 1250°С – более 80%, а при температуре 1300°С в углерод переходит не менее 75% метана.
Авторы также изучили динамику формирования УО при температуре 1300°С. После 10 мин эксперимента катализатор покрыт однородным слоем углерода, редко наблюдаются волокна диаметром 10 мкм и высотой около 50 мкм. Увеличение времени контакта катализатора с реакционной смесью до 60 мин приводит к образованию на поверхности катализатора углеродной “шубы” слоистой структуры, на поверхности которой наблюдаются зародыши будущих углеродных волокон. После 4 ч работы катализатор полностью покрыт углеродом в виде волокон диаметром около 100 мкм и высотой до 500 мкм. Исследование методом рентгенофазового анализа показало, что после 4 ч эксперимента фазовый состав катализатора представлен только графитоподобным углеродом, который обволакивает углеродные волокна и покрывает их полностью.
Таким образом, карборунд является перспективным резистивным катализатором для получения НУМ различной морфологии, которую можно регулировать путем нанесения на него оксидов различной природы.
ЗАКЛЮЧЕНИЕ
Использование резистивных катализаторов дает исследователям новые возможности управления процессом синтеза НУМ с помощью как традиционного набора параметров, известных уже на протяжении нескольких десятилетий, таких как температура и природа предшественника углерода, активного компонента катализатора и газа-разбавителя, так и параметров, связанных с протеканием электрического тока через катализатор. Эти возможности можно реализовывать на стадии предварительной обработки катализатора, когда применение резистивного нагрева позволяет сократить время этой стадии с десятков часов до нескольких минут. Воздействие постоянного или переменного тока в условиях эксперимента делает возможным получение углеродных нитей уникальной морфологии, в том числе фрактальной структуры. Однако следует признать, что условия синтеза НУМ на резистивных катализаторах к настоящему времени изучены недостаточно, о чем свидетельствуют противоречивые данные о морфологии формирующихся НУМ.
Список литературы
Chesnokov V.V., Buyanov R.A. // Russ. Chem. Rev. 2000. V. 69. № 7. P. 623.
Райская Е.А., Сигаева С.С., Цырульников П.Г., Плаксин Г.В. // Химия в интересах устойчивого развития. 2015. Т. 23. № 6. С. 705.
Фенелонов В.Б. Пористый углерод. Новосибирск: Изд-во Ин-та катализа СО РАН. 1995. 380 с.
Zhang T., Amiridis M.D. // Appl. Catal. A: General. 1998. V. 167. № 2. P. 161.
Zhang Y.N., Sun G.Z., Zheng L.X. // J. Nanomater. 2015. V. 16. № 1. P. 68.
Chatterjee A., Deopura B.L. // Fibers Polym. 2002. V. 3. № 4. P. 134.
Мишаков И.В., Буянов Р.А., Чесноков В.В., Стрельцов И.А., Ведягин А.А. // Катализ в пром-ти. 2008. № 2. С. 26.
Raiskaya E.A., Belskaya O.B., Ivlev K.E. // Russ. J. Appl. Chem. 2020. V. 93. № 12. P. 1917.
Sigaeva S.S., Temerev V.L., Kuznetsova N.V., Tsyrul’nikov P.G. // Catal. Ind. 2017. V. 9. № 3. P. 181.
Raiskaya E.A., Belskaya O.B. // AIP Conf. Proc. 2020. T. 2301. №. 1. C. 040013.
Sigaeva S.S., Shlyapin D.A., Temerev V.L., Tsyrul’nikov P.G. // Russ. J. Appl. Chem. 2019. V. 92. № 9. P. 1258.
Sigaeva S.S., Likholobov V.A., Tsyrul’nikov P.G. // Kinet. Catal. 2013. V. 54. № 2. P. 199.
Sigaeva S.S., Temerev V.L., Borisov V.A., Tsyrul’nikov P.G. // Catal. Ind. 2015. V. 7. № 3. P. 171.
Rayskaya E.A., Belskaya O.B., Drozdov V.A., Trenikhin M.V., Likholobov V.A. // Russ. Chem. Bull. 2018. V. 67. № 8. P. 1383.
Borisov V.A., Sigaeva S.S., Tsyrul’nikov P.G., Trenikhin M.V., Leont’eva N.N., Slepterev A.A., Kan V.E., Biryukov M.Yu. // Kinet. Catal. 2014. V. 55. № 3. P. 319.
Ahmad M., Silva S.R.P. // Carbon. 2020. V. 158. P. 24.
Hasanzadeh I., Eskandari M. J. // Surf. Coat. Technol. 2020. V. 381. P. 125109.
Rudneva Y.V., Shubin Y.V., Plyusnin P.E., Bauman Y.I., Mishakov I.V., Korenev S.V., Vedyagin A.A. // J. Alloys Compd. 2019. V. 782. P. 716.
Levitskii V.S., Maksimov A.I., Moshnikov V.A., Terukov E.I. // Phys. Solid State. 2014. V. 56. № 7. P. 1408.
Kumar M., Ando Y. // J. Nanosci. Nanotechnol. 2010. V. 10. № 6. P. 3739.
Seah C.M., Chai S.P., Mohamed A.R. // Carbon. 2011. V. 49. № 14. P. 4613.
Baker R.T.K. // Carbon. 1989. V. 27. № 3. P. 315.
Avdeeva L.B., Reshetenko T.V., Ismagilov Z.R., Likholobov V.A. // Appl. Catal. A: Gen. 2002. V. 228. № 1–2. P. 53.
Li Y., Chen J., Qin Y., Chang L. // Energy Fuels. 2000. V. 14. № 6. P. 1188.
Kuvshinov G.G., Mogilnykh Yu.I., Kuvshinov D.G. // Catal. Today 1998. V. 42. № 3. P. 357.
De Jong K.P., Geus J.W. // Catal. Rev. Sci. Eng. 2000. V. 42. № 4. P. 481.
Halonen N., Sápi A., Nagy L., Puskas R., Leino A.-R., Maklin J., Kukkola J., Toth G., Wu M.-C., Liao H.-C., Su W.-F., Shchukarev A., Mikkola J.-P., Kukovecz A., Konya Z., Kordas K. // Phys. Status Solidi. B. 2011. V. 248. № 11. P. 2500.
Dong Z., Li B., Cui C., Qian W., Jin Y., Wei F. // React. Chem. Eng. 2020. V. 5. № 6. P. 991.
Tibbetts G.G., Devour M.G., Rodda E.J. // Carbon. 1987. V. 25. № 3. P. 367.
Xin B., Gao W., Ji Z., Zhang S., Xin L., Zhao L., Xue H., Wu Q., Zhang L., Liu C., Zhang J., He M. // Carbon. 2020. V. 156. P. 410.
Hu L., Hecht D. S., Gruner G. // Chem. Rev. 2010. V. 110. № 10. P. 5790.
Буянов Р.А., Чесноков В.В. // Химия в интересах устойчивого развития. 2005. Т. 13. № 1. С. 37.
Буянов Р.А., Чесноков В.В. // Катализ в пром-ти. 2006. № 2. С. 3.
Kim S.E., Jeong S.K., Park K.T., Lee K.Y., Kim H.J. // Catal. Commun. 2021. V. 148. P. 106167.
Muradov N. // Catal. Commun. 2001. V. 2. № 3–4. P. 89.
Su D.S., Perathoner S., Centi G. // Chem. Rev. 2013. V. 113. № 8. P. 5782.
Muradov N.Z., Veziroǧlu T.N. // Int. J. Hydrogen Energy. 2005. V. 30. № 3. P. 225.
Pinilla J.L., Suelves I., Lazaro M.J., Moliner R. // Chem. Eng. J. 2008. V. 138. № 1–3. P. 301.
Shilapuram V., Ozalp N., Oschatz M., Borchardt L., Kaskel S. // Carbon. 2014. V. 67. P. 377.
Abbas H.F., Baker I.F. // Int. J. Hydrogen Energy. 2011. V. 36. № 15. P. 8985.
J. Wang, L. Lin, Y. Li, Jia C., Hu H. // Int. J. Hydrogen Energy. 2016. V. 41. № 25. P. 10661.
Kameya Y., Hanamura K. // Carbon. 2012. V. 50. № 10. P. 3503.
Muradov N. // Int. J. Hydrogen Energy. 2001. V. 26. № 11. P. 1165.
Kim K.E., Kim K.J., Jung W.S., Bae S.Y., Park J., Choi J., Choo J. // Chem. Phys. Lett. 2005. V. 401. № 4–6. P. 459.
Chen P., Zhang H.B., Lin G.D., Hong Q., Tsai K.R. // Carbon. 1997. V. 35. № 10–11. P. 1495.
Ermakova M.A., Ermakov D.Yu., Kuvshinov G.G. // Appl. Catal. A: Gen. 2000. V. 201. № 1. P. 61.
Molchanov V.V., Chesnokov V.V., Buyanov R.A., Zaitseva N.A. // Kinet. Catal. 1998. V. 39. № 3. P. 378.
Молчанов В.В., Чесноков В.В., Буянов Р.А. Патент РФ № 2096083, 1997.
Molchanov V.V., Chesnokov V.V., Buyanov R.A., Zaitsev N.A., Zaikovskii V.I. // Kinet. Catal. 2005. V. 46. № 5. P. 660.
Li Y., Chen J., Chang L. // Appl. Catal. A: Gen. 1997. V. 163. № 1–2. P. 45.
Tibbetts G.G. // Appl. Phys. Lett. 1983. V. 42. № 8. P. 666.
Benissad F., Gadelle P., Coulon M., Bonnetain L. // Carbon. 1988. V. 26. № 1. P. 61.
Wen Q., Qian W., Nie J., Cao A., Ning G., Wang Y., Hu L., Zhang Q., Huang J., Wei F. // Adv. Mater. 2010. V. 22. № 16. P. 1867.
Zhang R., Wen Q., Qian W., Su D.S., Zhang Q., Wei F. // Adv. Mater. 2011. V. 23. № 30. P. 3387.
Zhang R., Zhang Y., Zhang Q., Xie H., Qian W., Wei F. // ACS Nano. 2013. V. 7. № 7. P. 6156.
Zhang Y., Gao T., Xie S., Dai B., Fu L., Gao Y., Chen Y., Liu M., Liu Z. // Nano Res. 2012. V. 5. № 6. P. 402.
Li X., Cai W., Colombo L., Ruoff R.S. //Nano Lett. 2009. V. 9. № 12. P. 4268.
Dong J., Zhang L., Zhang K., Ding F. // Nanoscale. 2018. V. 10. № 15. P. 6878.
Wang F., Wang K., Zheng B., Dong X., Mei X., Lv J., Duan W., Wang W. // Mater. Technol. 2018. V. 33. № 5. P. 340.
Park J.B., Xiong W., Gao Y., Qian M., Xie Z.Q., Mitchell M., Zhou Y.S., Han G.H., Jiang L., Lu Y. F. // Appl. Phys. Lett. 2011. V. 98. № 12. P. 123109.
Liu Y., Qian W., Zhang Q., Ning G., Wen Q., Luo G., Wei F. // Carbon. 2008. V. 46. № 14. P. 1860.
Wen Q., Qian W., Wei F., Liu Y., Ning G., Zhang Q. // Chem. Mater. 2007. V. 19. № 6. P. 1226.
Ning G., Liu Y., Wei F., Wen Q., Luo G. // J. Phys. Chem. C. 2007. V. 111. № 5. P. 1969.
Nie J., Qian W., Zhang Q., Wen Q., Wei F. // J. Phys. Chem. C. 2009. V. 113. № 47. P. 20178.
Quiceno R., Perez-Ramirez J., Warnatz J., Deutschmann O. // Appl. Catal. A: Gen. 2006. V. 303. № 2. P. 166.
Qian W., Liu T., Wei F., Wanga Z., Lib Y. // Appl. Catal. A: Gen. 2004. V. 258. № 1. P. 121.
Qian W., Tian T., Guo C., Wen Q., Li K., Zhang H., Shi H., Wang D., Liu Y., Zhang Q., Zhang Y., Wei F., Wang Z., Li X., Li Y. // J. Phys. Chem. C. 2008. V. 112. № 20. P. 7588.
Kreupl F., Graham A.P., Duesberg G.S., Steinhögl W., Liebau M., Unger E., Hönlein W. // Microelectron. Eng. 2002. V. 64. № 1–4. P. 399.
Okuno H., Fournier A., Quesnel E., Muffato V., Le Poche H., Fayolle M., Dijon J. // Comptes Rendus Physique. 2010. V. 11. № 5–6. P. 381.
Talapatra S., Kar S., Pal S.K., Vajtai R., Ci L., Victor P., Shaijumon M. M., Kaur S., Nalamasu O., Ajayan P.M. // Nat. Nanotechnol. 2006. V. 1. № 2. P. 112.
Буянов Р.А. Закоксование катализаторов. Новосибирск: Наука, 1983. 207 с.
Boskovic B.O., Stolojan V., Khan R.U.A., Haq S., Silva S.R.P. // Nature Mater. 2002. V. 1. № 3. P. 165.
Melechko A.V., Merkulov V.I., McKnight T.E., Guillorn M.A., Klein K.L., Lowndes D.H., Simpson M.L. // J. Appl. Phys. 2005. V. 97. № 4. P. 3.
Marchand M., Journet C., Guillot D., Benoit J.-M., Yakobson B.I., Purcell S.T. // Nano Lett. 2009. V. 9. № 8. P. 2961.
Yu Z., Chen D., Totdal B., Holmen A. // J. Phys. Chem. B. 2005. V. 109. № 13. P. 6096.
Dai H., Rinzler A.G., Nikolaev P., Thess A., Colbert D.T., Smalley R.E. // Chem. Phys. Lett. 1996. V. 260. № 3–4. P. 471.
Nagy J.B., Bister G., Fonseca A., Méhn, D., Kónya, Z., Kiricsi, I., Horváth, Z.E., Biró, L.P. // J. Nanosci. Nanotechnol. 2004. V. 4. № 4. P. 326.
Schaper A.K., Hou H., Greiner A., Phillipp F. // J. Catal. 2004. V. 222. № 1. P. 250.
Zaikovskii V.I., Chesnokov V.V., Buyanov R.A. // Appl. Catal. 1988. V. 38. № 1. P. 41.
Buyanov R.A., Chesnokov V.V. // Russ. J. Appl. Chem. 1997. V. 70. № 6. P. 935.
Buyanov R.A., Chesnokov V.V. // Chem. Sustain. Develop. 1995. V. 3. № 3. P. 161.
Cartwright R.J., Esconjauregui S., Weatherup R.S., Hardeman D., Guo Y., Wright E., Oakes D., Hofmann S., Robertson J. // Carbon. 2014. V. 75. P. 327.
Lobo L.S., Carabineiro S.A.C. // C. 2020. V. 6. № 2. P. 18.
Ning G., Xu C., Mu L., Chen G., Wang G., Gao J., Fan Z., Qian W., Wei F. // Chem. Commun. 2012. V. 48. № 54. P. 6815.
Tang C., Li B.Q., Zhang Q., Zhu L., Wang H.-F., Shi J.-L., Wei F. // Adv. Funct. Mater. 2016. V. 26. № 4. P. 577.
Ceyer S.T., Yang Q.Y., Lee M.B., Beckerle J.D., Johnson A.D. // Methane Conversion. 1988. P. 51.
Raghubanshi H., Dikio E.D. // Nanomater. 2015. V. 5. № 2. P. 937.
Reshetenko T.V., Avdeeva L.B., Ismagilov Z.R., Chuvilin A.L., Likholobov V.A. // Eurasian Chem. Technol. J. 2000. V. 2. № 3–4. P. 237.
Avdeeva L.B., Goncharova O.V., Kochubey D.I., Zaikovskii V.I., Plyasova L.M., Novgorodov B.N., Shaikhutdinov Sh.K. // Appl. Catal. A: Gen. 1996. V. 141. № 1–2. P. 117.
Avdeeva L.B., Kochubey D.I., Shaikhutdinov Sh.K. // Appl. Catal. A: Gen. 1999. V. 177. № 1. P. 43.
Zhang Q., Huang J.Q., Qian W.Z., Zhang Y.-Y., Wei F. // Small. 2013. V. 9. № 8. P. 1237.
Cartwright R., Esconjauregui S., Hardeman D., Bhardwaj S., Weatherup R., Guo Y., D’Arsié L., Bayer B., Kidambi P., Hofmann S., Wright E., Clarke J., Oakes D., Cepek C., Robertson J. // Carbon. 2015. V. 81. P. 639.
de Smit E., de Groot F.M.F., Blume R., Hävecker M., Knop-Gericke A., Weckhuysen B.M. //Phys. Chem. Chem. Phys. 2010. V. 12. № 3. P. 667.
Wachs I.E., Dwyer D.J., Iglesia E. // Appl. Cat. 1984. V. 12. № 2. P. 201.
Wielers A.F.H., Koebrugge G.W., Geus J.W. // J. Catal. 1990. V. 121. № 2. P. 375.
Puron H., Pinilla J.L., Saraev A.A., Kaichev V.V., Millan M. // Fuel. 2020. V. 263. P. 116717.
Hafner J.H., Bronikowski M.J., Azamian B.R., Nikolaev P., Rinzler A.G., Colbert D.T., Smith K.A., Smalley R.E. // Chem. Phys. Lett. 1998. V. 296. № 1–2. P. 195.
Tian J., Cui C., Zheng C., Qian W. // Chin. Chem. Lett. 2018. V. 29. № 4. P. 599.
Ning G., Fan Z., Wang G., Gao J., Qian W., Wei F. // Chem. Commun. 2011. V. 47. № 21. P. 5976.
Cui C., Qian W., Yu Y., Kong C., Yu B., Xiang L., Wei F. // J. Am. Chem. Soc. 2014. V. 136. № 6. P. 2256.
Ning G., Ma X., Wang M., Li Y. // Nanoscale. 2017. V. 9. № 34. P. 12647.
Zhu X., Ning G., Fan Z., Gao J., Xu C., Qian W., Wei F. // Carbon. 2012. V. 50. № 8. P. 2764.
Zhang Q., Qian W., Wen Q., Liu Y., Wang D., Wei F. // Carbon. 2007. V. 45. № 8. P. 1645.
Beckerle J.D., Johnson A.D., Yang Q.Y., Ceyer S.T. // J. Chem. Phys. 1989. V. 91. № 9. P.5756.
Beckerle J.D., Yang Q.Y., Johnson A.D., Ceyer S.T. // J. Chem. Phys. 1987. V. 86. P. 7236.
Qingwen L., Hao Y., Yan C., Jin Z., Zhongfan L. // J. Mat. Chem. 2002. V. 12. № 4. P. 1179.
Wen Q., Zhang R., Qian W., Wang Y., Tan P., Nie J., Wei F. // Chem. Mater. 2010. V. 22. № 4. P. 1294.
Nolan P.E., Schabel M.J., Lynch D.C., Cutler A.H. // Carbon. 1995. V. 33. № 1. P. 79.
Дополнительные материалы отсутствуют.
Инструменты
Кинетика и катализ