Кинетика и катализ, 2022, T. 63, № 4, стр. 496-505
Ароматизация пропана на Zn-содержащих цеолитах с микро-мезопористой структурой
А. А. Восмериков a, *, Л. Н. Восмерикова a, Я. Е. Барбашин a, А. В. Восмериков a
a ФГБУН Институт химии нефти Сибирского отделения РАН
634055 Томск, Академический просп., 4, Россия
* E-mail: antonvosmerikov@gmail.ru
Поступила в редакцию 04.02.2022
После доработки 25.03.2022
Принята к публикации 25.03.2022
- EDN: AGOCWK
- DOI: 10.31857/S0453881122040128
Аннотация
Изучена конверсия пропана в ароматические углеводороды на цинксодержащих цеолитах типа MFI с микро-мезопористой структурой. Исследовано влияние марки технического углерода, используемого в качестве второго структурообразующего компонента при синтезе цинкалюмосиликатов, на их физико-химические свойства, каталитическую активность и стабильность в процессе ароматизации пропана. С помощью метода термодесорбции аммиака изучены кислотные характеристики катализаторов. Методом сканирующей электронной микроскопии определены морфология и размеры кристаллов синтезированных цинкалюмосиликатов. Методом дифференциального термического анализа установлены природа и концентрация коксовых отложений, образующихся на поверхности цинкалюмосиликатов в ходе протекания реакции ароматизации пропана. Показано, что добавление технического углерода в кристаллизационный гель в процессе синтеза приводит к получению цинкалюмосиликатов, обладающих более высокой стабильностью работы по сравнению с микропористым Zn-содержащим цеолитом.
ВВЕДЕНИЕ
Цеолиты или цеолитоподобные материалы относятся к важнейшим каталитическим системам в нефтепереработке и нефтехимии [1–7]. Широкое применение цеолитов в качестве катализаторов при получении самых разнообразных продуктов объясняется в значительной степени их регулируемой кислотностью и прекрасно структурированными микропорами. Особое внимание в последние годы привлекает процесс конверсии попутного нефтяного газа (ПНГ) в жидкие углеводороды, что отвечает принципам рационального природопользования, обеспечивает сокращение объемов сжигания ПНГ и получение высоколиквидных продуктов. Согласно многочисленным литературным данным для этого процесса наиболее эффективны катализаторы, приготовленные введением в цеолитный материал, обладающий кислотными свойствами, промотирующей добавки, обладающей дегидрирующими свойствами, в качестве которой чаще всего используются соединения галлия и/или цинка [8–11]. Экономически более предпочтительно в процессах ароматизации применять цинк, поскольку галлий дорог и дефицитен. Соединения модифицирующих элементов вводят в состав материала или в ходе его гидротермального синтеза, или последующей пропиткой и ионным обменом, или другим способом. Синтез цеолитных систем с использованием метода изоморфного замещения катионов в цеолитном каркасе представляется перспективным направлением совершенствования и создания новых катализаторов для процессов переработки углеводородного сырья. Однако для реакций с участием крупных молекул с диаметрами бóльшими, чем микропоры цеолита типа MFI, массовый перенос реагентов с внешней поверхности к активным кислотным центрам затрудняется из-за сильного диффузионного сопротивления, что приводит к снижению эффективности работы катализатора. Кроме того, даже если молекулы реагентов достаточно малы, чтобы проникнуть во внутренний объем цеолита, диффузионное сопротивление может привести к увеличению времени контакта с активными центрами внутри кристаллов [12, 13], и, как следствие, к росту скорости протекания побочных реакций и дезактивации катализатора [14–16].
С целью улучшения эффективности работы и срока службы цеолитов в различных реакциях разрабатывают методы, основанные либо на уменьшении размеров отдельных цеолитных кристаллов, либо на получении иерархических цеолитов [17–21]. Иерархические цеолиты могут содержать либо микро- и мезо-, либо микро- и макропоры, либо иметь сразу все три уровня пористости [17]. Сегодня для оптимального проектирования и синтеза этих материалов существует множество методов. Одним из них является метод твердого темплата, где в качестве вторичных темплатов применяют наноуглеродные частицы, углеродные нанотрубки, углеродные нановолокна, а также различные виды технического углерода [22–26]. Впервые при синтезе цинкалюмосиликатов структурного типа цеолита MFI в качестве второго темплата нами использован технический углерод, выбор которого обусловлен его доступностью и простотой применения. Частицы углерода по мере роста цеолитного кристалла встраиваются в структуру цеолита. Удаление углеродной матрицы с помощью прокаливания приводит к образованию микро-мезопористого цеолита типа MFI. Цель настоящей работы состояла в получении Zn-содержащих цеолитных катализаторов с микро-мезопористой структурой и исследование их активности и стабильности в процессе превращения пропана в ароматические углеводороды.
ЭКСПЕРИМЕНТАЛЬНАЯ ЧАСТЬ
Цинксодержащий цеолит структурного типа MFI (SiO2/Al2O3 + ZnO = 40, [ZnO] = 0.82 мас. %, [Al2O3] = 3.09 мас. %) был синтезирован гидротермальным методом путем частичной замены ионов алюминия на ионы цинка в исходном алюмокремнегеле по методике, о которой ранее сообщалось в работе [27].
Для создания вторичной мезопористости в цинкалюмосиликате дополнительно на стадии его синтеза в реакционную смесь вводили технический углерод в количестве 2.0 мас. %. В качестве второго темплата использовали технический углерод двух марок – П354 и N660. Технический углерод был предоставлен Центром новых химических технологий Федерального исследовательского центра “Институт катализа им. Г.К. Борескова СО РАН” (г. Омск). Технический углерод марки П354 имеет глобулярную форму со средним диаметром 154 ± 70 нм. Площадь его удельной поверхности составляет 110 м2/г, общий объем пор – 0.034 см3/г. Технический углерод марки N660 представляет собой среднедисперсный низкоструктурный техуглерод (масляное абсорбционное число – 90 ± 5 см3/100 г) с площадью удельной поверхности 36 ± 5 м2/г.
Полученный гель помещали в стальные автоклавы емкостью 0.25–0.5 дм3 и проводили кристаллизацию в стационарном режиме в течение 2 сут при температуре 175°С. Полученную твердую фазу отфильтровывали, промывали, сушили при 100°С в течение 8 ч и прокаливали для удаления темплатов при 550°С в течение 8 ч в атмосфере воздуха.
Перевод цеолитов в активную Н-форму осуществляли декатионированием 25%-ым водным раствором NH4Cl в течение 2 ч при 90°С с последующим промыванием дистиллированной водой и прокаливанием при 550°С в течение 6 ч.
Для образцов введены следующие обозначения: Zn–AC – микропористый образец цинкалюмосиликата, синтезированный без использования технического углерода; Zn–AC/СП354 – цинкалюмосиликат, полученный с использованием технического углерода марки П354; Zn–AC/СN660 – цинкалюмосиликат, приготовленный с использованием технического углерода марки N660.
Качество синтезированных образцов контролировали с применением методов ИК-спектроскопии и рентгенофазового анализа (РФА). ИК-спектры цеолита снимали на ИК-Фурье-спектрометре Nicolet 5700 (“Thermo Electron Corporation”, США) в области 2000–400 см–1 в таблетках с KBr (1.2 мг цеолита на 300 мг KBr) на воздухе. Рентгенофазовый анализ образцов проводили методом рентгеновской дифрактометрии на рентгеновской установке DISCOVER D8 (“Bruker”, Германия) в монохромном CuKα-излучении. Для измерения использовали следующий режим: диапазон углов 2θ = 6°–50°, шаг сканирования − 0.02°, время накопления сигнала в точке – 3 с.
Параметры пористой структуры синтезированных цинкалюмосиликатов определяли с помощью изотерм адсорбции–десорбции азота, полученных на автоматическом газо-адсорбционном анализаторе 3Flex (“Micromeritics”, США) при температуре –196°С. Перед измерением удельной поверхности проводили дегазацию образцов (200°С, вакуум) в течение 2 ч. Определение величины площади удельной поверхности (SБЭТ) осуществляли с помощью многоточечного (10–12 точек) метода Брунауэра–Эммета–Теллера (БЭТ) по изотермам адсорбции в интервале относительного давления паров азота P/P0 от 0.05 до 0.30. Исследования были выполнены в Центре коллективного пользования сорбционных и каталитических исследований на базе лаборатории каталитических исследований, входящего в состав Испытательного центра “Томский региональный центр коллективного пользования” Национального исследовательского Томского государственного университета.
Кислотные свойства образцов изучали методом термопрограммированной десорбции аммиака (ТПД–NH3). Данный метод позволяет количественно характеризовать кислотно-оснóвные центры различной природы на поверхности твердых веществ. Навеску образца (0.5 г) помещали в проточный кварцевый реактор и прокаливали в токе газа-носителя Не (170 мл/мин) в течение 1 ч при температуре 600°С. Прокаливание осуществляли для удаления с поверхности образца адсорбированных паров воды и других примесей. После “тренировки” образца реактор охлаждали до 100°С и проводили адсорбцию аммиака до полного его насыщения, затем продували образец гелием при той же температуре в течение 1 ч. Десорбцию аммиака выполняли при линейном подъеме температуры от 50 до 600°С со скоростью 10 град/мин. Концентрацию кислотных центров в исследуемых образцах определяли по количеству аммиака, десорбирующегося в момент фиксации десорбционных пиков, и выражали в микромолях на 1 г катализатора.
Для исследования морфологии синтезированных образцов использовали сканирующую электронную микроскопию (СЭМ). Микроснимки катализаторов были получены на электронном микроскопе JEOL JSM-6610LV (“JEOL”, Япония) с помощью стандартного метода подготовки образцов.
Активность катализаторов в реакции превращения пропана (степень чистоты 99.95 об. %) определяли на проточной установке при следующих условиях: температура реакции − 550°С, объемная скорость подачи исходного сырья − 250 ч–1, атмосферное давление, объем катализатора − 6.0 см3, размер его частиц − 0.5–1.0 мм. Процесс вели непрерывно в течение определенного времени, анализ образующихся продуктов осуществляли через равные для всех образцов промежутки времени. Продукты реакции анализировали методом ГЖХ с использованием хроматографа Хроматэк-Кристалл 5000.2 (“Хроматэк”, Россия). Для нахождения состава жидкой фазы использовали капиллярную колонку BP-1 PONA (100 м × 0.25 мм × × 0.5 мкм), а для определения состава газовой фазы – капиллярную GS-Gas-Pro (60 м × 0.32 мм) и набивную Carbosieve S-II (4 м × 2 мм) колонки. Для оценки каталитической активности образцов рассчитывали степень превращения пропана, а также выход и селективность образования газообразных и жидких продуктов реакции.
Изучение природы коксовых отложений, формирующихся на поверхности исследуемого катализатора в процессе ароматизации пропана, проводили путем нагрева образца на воздухе с применением дериватографа Q-1500 (“MOM”, Венгрия), последующую обработку результатов измерений выполняли с помощью программного продукта “Tanaliz”, обеспечивающего контроль и измерение температуры (Т) и скорости (V) нагрева образца, изменение массы образца (ТГ), тепловых эффектов (ДТА). В опытах нагрев исследуемого образца осуществляли со скоростью 10 град/мин, а его масса составляла 400 мг. В качестве образца сравнения использовали оксид алюминия (α-Al2О3).
РЕЗУЛЬТАТЫ И ИХ ОБСУЖДЕНИЕ
По данным РФА и ИК-спектроскопии все синтезированные образцы имеют структуру цеолита типа MFI и обладают высокой степенью кристалличности (Zn–AC – 88%, Zn–AC/СП354 – 90%, Zn–AC/СN660 – 90%). На рис. 1 представлены дифрактограммы исходного цинкалюмосиликата и цинкалюмосиликатов с микро-мезопористой структурой после удаления углеродного темплата. Как видно из рис. 1, дифрактограммы исследуемых образцов содержат набор линий, характерный для цеолита типа MFI [28], т.е. добавка углеродного темплата в процессе синтеза цеолита не влияет на структуру его алюмосиликатного каркаса.
С помощью сканирующей электронной микроскопии получены данные о форме и размерах кристаллов синтезированных цинкалюмосиликатов (рис. 2). Из рис. 2 видно, что микропористый образец Zn–AC синтезируется в виде сфероидов размером 8–12 мкм, состоящих из сросшихся монокристаллов в форме гексагональных призм. Упаковка монокристаллов в них достаточно плотная. Микро-мезопористый образец Zn–AC/СП354 имеет ту же общую морфологию, что и микропористый цинкалюмосиликат, но упаковка монокристаллов становится менее плотной за счет появления мезопор. Использование в качестве вторичного темплата технического углерода марки N660 приводит к появлению кристаллов цеолита, имеющих орторомбическую форму, с размером грани 1.5–2 мкм, которые образуют крупные сросшиеся агломераты сферической формы размером до 14 мкм. Эти структуры “оболочечного” типа сформировались путем агломерации кристаллов и срастания на поверхности более крупных частиц углерода, введенных в среду при синтезе цеолита.
Текстурные характеристики цинкалюмосиликатов, полученных с добавкой технического углерода и без нее, представлены в табл. 1. Наименьшая площадь удельной поверхности наблюдается у микропористого образца Zn–AC и составляет 304 м2/г. Для цинкалюмосиликатов, синтезированных с техническим углеродом, величина удельной поверхности цеолитов практически не изменяется и равна 307 и 308 м2/г соответственно для образцов Zn–AC/СП354 и Zn–AC/СN660. При добавлении технического углерода в кристаллизационный гель в процессе синтеза цинкалюмосиликатов происходит формирование мезопор, объем которых достигает 0.038 и 0.054 см3/г соответственно для образцов Zn–AC/СП354 и Zn–AC/СN660, при этом объем микропор для них уменьшается до 0.118 и 0.113 см3/г по сравнению с исходным Zn–AC. Различия в текстурных характеристиках цинкалюмосиликатов, приготовленных с добавкой технического углерода и без нее, обусловлены введением углерода в кристаллизационный гель при их синтезе и влиянием его на образование кристаллов. После удаления углеродного шаблона путем прокаливания образцов формируется вторичная мезопористая система и объем мезопор увеличивается. В то же время площадь микропористой поверхности и объем микропор уменьшаются за счет снижения размеров кристаллов.
Таблица 1.
Текстурные характеристики цинкалюмосиликатов
Образец | SБЭТ, м2/г | Sмикро, м2/г | Vобщ., см3/г | Vмикро, см3/г | Vмезо, см3/г | Средний размер пор, нм |
---|---|---|---|---|---|---|
Zn–AC | 304 | 249 | 0.149 | 0.122 | 0.027 | 2.30 |
Zn–AC/СП354 | 307 | 229 | 0.156 | 0.118 | 0.038 | 3.01 |
Zn–AC/СN660 | 308 | 230 | 0.167 | 0.113 | 0.054 | 3.31 |
Таким образом, добавление в процессе синтеза цинкалюмосиликата в качестве вторичного темплата технического углерода не приводит к значительным изменениям в морфологии его кристаллов. Однако при использовании технического углерода марки П354 в качестве мезотемплата образуются более мелкие кристаллы (0.8–0.9 мкм), чем в случае применения углерода марки N660 (1.5–1.8 мкм) и микропористого цинкалюмосиликата (2.0–2.4 мкм).
Исследования кислотных характеристик цинкалюмосиликатов с микро-мезопористой структурой показали, что на термодесорбционных кривых имеются два пика с четко выраженными температурными максимумами, указывающими на наличие двух типов кислотных центров. Центры, характеризующиеся пиками в интервале 100–300°С, относятся преимущественно к льюисовским кислотным центрам (L-центры), а центры с максимумами в более высокотемпературной области – в основном к сильным бренстедовским кислотным центрам (В-центры) [29]. Из представленных в табл. 2 данных видно, что сила и концентрация кислотных центров полученных цеолитов отличаются, и они зависят от природы вторичного темплата, используемого при синтезе цеолита. Наименьшее количество кислотных центров обоих типов имеет исходный цинкалюмосиликат: концентрация слабых кислотных центров составляет 982 мкмоль/г, а сильных – 356 мкмоль/г. Добавка на стадии гидротермального синтеза цинкалюмосиликата технического углерода марки П354 приводит к увеличению силы высокотемпературных кислотных центров, на что указывает смещение максимума второго пика в область более высоких температур, при этом сила слабокислотных центров почти не изменяется. Смещение максимума в высокотемпературную область можно объяснить возможной реадсорбцией аммиака в мезопорах [30]. При добавлении к цинкалюмосиликату технического углерода марки N660 существенно повышается суммарная концентрация кислотных центров, которая достигает 1718 мкмоль/г, что на 380 мкмоль/г больше, чем для микропористого цинкалюмосиликата. При этом сила кислотных центров остается практически неизменной.
Таблица 2.
Кислотные характеристики цинкалюмосиликатов
Катализатор | Тмакс, °С | Концентрация кислотных центров, мкмоль/г | |||
---|---|---|---|---|---|
ТI | ТII | СI | СII | СΣ | |
Zn–AC | 235 | 460 | 982 | 356 | 1338 |
Zn–AC/СП354 | 230 | 480 | 1196 | 483 | 1679 |
Zn–AC/СN660 | 230 | 465 | 1201 | 517 | 1718 |
На рис. 3 представлены результаты исследования каталитических свойств синтезированных цинкалюмосиликатов с микро- и микро-мезопористой структурой в процессе превращения пропана в ароматические углеводороды. На микропористом цинкалюмосиликате выход ароматических углеводородов при температуре реакции 550°С составляет 55.5% при конверсии пропана 96%. Цинкалюмосиликаты, полученные с использованием технического углерода, обладают несколько меньшей ароматизирующей активностью, при этом общая активность катализаторов, оцениваемая по степени превращения пропана, почти не изменяется. Так, например, на цинкалюмосиликате, синтезированном с углеродом марки N660 (Zn–AC/CN660), конверсия пропана составляет 98%, а выход ароматических углеводородов – 43.6%, что на 11.9% ниже, чем для микропористого цинкалюмосиликата. В то же время селективность образования ароматических углеводородов на всех исследуемых образцах сохраняется довольно высокой (более 45%), что свидетельствует о наличии в них достаточного количества протонных кислотных центров, участвующих в реакции ароматизации пропана.
Рис. 3.
Основные показатели процесса ароматизации пропана на цинкалюмосиликатах с микро- и микро-мезопористой структурой.
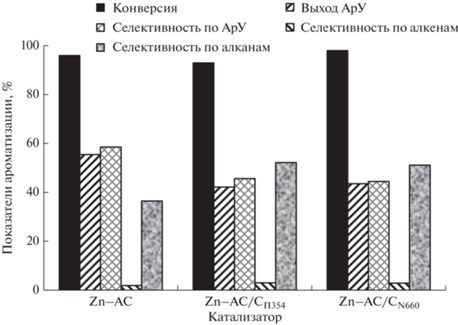
Основными жидкими продуктами превращения пропана на цинкалюмосиликатах являются ароматические углеводороды, состоящие преимущественно из бензола, толуола, ксилола (БТК-фракция) и алкилбензолов, а также более высокомолекулярных ароматических соединений, включая нафталин, метил- и диметилнафталины. Как видно из данных, приведенных в табл. 3, количественные соотношения ароматических углеводородов, образующихся на цинкалюмосиликатах, синтезированных с использованием углеродного темплата и без него, отличаются. Наименьшее количество БТК-фракции получено на микропористом цинкалюмосиликате (Zn–AC) и составляет 70.5%, что связано, по-видимому, с меньшим объемом мезопор и бóльшим объемом микропор по сравнению с другими образцами. Добавление на стадии гидротермального синтеза цинкалюмосиликата технического углерода позволяет синтезировать образцы, в присутствии которых в составе жидких продуктов увеличивается содержание БТК-фракции и уменьшается доля нафталиновых углеводородов, при этом концентрация алкилбензолов изменяется незначительно.
Таблица 3.
Состав жидких продуктов превращения пропана на цинкалюмосиликатах
Катализатор | Состав жидких продуктов, мас. % | Выход катализата, мас. % | ||
---|---|---|---|---|
БТК | алкилбензолы C9+ | нафталиновые УВ | ||
Zn–AC | 70.5 | 1.4 | 28.1 | 55.5 |
Zn–AC/CП354 | 72.9 | 1.7 | 25.4 | 42.2 |
Zn–AC/CN660 | 76.9 | 1.2 | 21.9 | 43.6 |
Таким образом, можно отметить, что качественный состав жидких продуктов, образующихся при превращении пропана на микро- и микро-мезопористых цеолитах, остается постоянным, но происходит изменение соотношения отдельных компонентов в катализате.
Отличия в поведении катализаторов в процессе превращения пропана связаны с тем, что при добавлении технического углерода в кристаллизационный гель происходит формирование мезопор внутри кристаллов цеолита, что приводит, благодаря уменьшению диффузионного сопротивления для реагирующих молекул, к пониженному образованию конденсированных ароматических соединений.
Результаты исследований по влиянию продолжительности работы цинкалюмосиликатов в процессе ароматизации пропана на их каталитические свойства представлены в табл. 4. Длительность стабильной работы образцов в одном реакционном цикле определяли при температуре реакции 550°С. Видно, что за 6 ч работы цинкалюмосиликата, синтезированного без добавки технического углерода, происходит заметное снижение как его общей, так и ароматизирующей активности. Так, конверсия пропана через 6 ч работы катализатора составляет 41%, что почти в 2.3 раза меньше, чем вначале процесса, при этом выход ароматических углеводородов сокращается более чем в 3 раза. В составе газообразных продуктов превращения пропана с увеличением времени работы катализатора существенно возрастает содержание олефинов С2–С4. Для цинкалюмосиликатов, синтезированных с добавкой технического углерода, наблюдается более плавное снижение активности и селективности по ароматическим углеводородам. Например, для образца Zn–AC/СП354 через 6 ч непрерывной работы селективность образования ароматических углеводородов составляет 46.7% при конверсии пропана 50%, что превышает соответствующие значения для исходного Zn–AC. Близкие показатели получены для образца Zn–AC/СN660.
Таблица 4.
Изменение каталитических свойств цинкалюмосиликатов в процессе ароматизации пропана со временем их работы
Катализатор | t, ч | Х, % | А, % | Sар, % | Sкр, % | Sдег, % |
---|---|---|---|---|---|---|
Zn–AC | 1 2 4 6 |
96 89 67 41 |
55.5 41.6 31.7 17.9 |
58.6 46.9 47.5 44.1 |
36.6 44.9 38.2 31.0 |
2.0 4.2 9.4 18.9 |
Zn–AC/СП354 | 1 2 4 6 |
93 85 67 50 |
42.2 33.0 29.3 23.0 |
45.7 38.9 44.4 46.7 |
47.5 51.1 41.2 34.3 |
3.4 5.8 9.7 13.7 |
Zn–AC/СN660 | 1 2 4 6 |
95 87 71 50 |
43.9 35.0 28.8 22.8 |
46.9 40.4 41.1 45.6 |
46.8 50.4 45.8 37.3 |
3.0 5.1 8.6 13.9 |
Причиной потери каталитической активности является образование на поверхности катализаторов в ходе реакции конденсированных углеродных отложений, блокирующих его активные центры. Для полного удаления с поверхности цеолитного катализатора продуктов уплотнения путем регенерации необходимо знать скорость их образования, а также структуру, морфологию и преимущественную локализацию различных углеродных форм. С целью изучения коксовых отложений, формирующихся на исследуемых катализаторах в процессе превращения пропана, были проведены термогравиметрические исследования.
На рис. 4 и в табл. 5 приведены данные дифференциального термического анализа цинкалюмосиликатов, проработавших в процессе ароматизации пропана в течение 6 ч. Эндотермические эффекты в области 100–160°С и соответствующие им максимумы на кривых ДТГ обусловлены удалением адсорбированной и слабосвязанной воды. Наблюдаемые выше 400°С экзотермические эффекты и пики на кривых ДТГ характеризуют выгорание коксовых отложений. По данным дифференциально-термического анализа наибольшее количество кокса образуется на микропористом цинкалюмосиликате, обладающем максимальной первоначальной ароматизирующей активностью в процессе превращения пропана. Общая масса коксовых отложений для него составляет 8.86%, температура начала и максимума выгорания кокса смещены в более высокотемпературную область по сравнению с другими образцами, что свидетельствует о формировании на нем более плотных (конденсированных) углеродных отложений. Для цинкалюмосиликатов, полученных с добавкой технического углерода, количество содержащегося на них кокса снижается. Наименьшее его количество – 7.95% – зафиксировано на образце, синтезированном с техническим углеродом марки П354 (табл. 5). Отсутствие явно выраженных низко- и высокотемпературных плеч на кривых ДТГ и ДТА данного образца указывает на то, что образующийся на нем кокс довольно однороден и присутствует преимущественно в виде одной формы. Также можно отметить сравнительно невысокую температуру конца горения кокса для цинкалюмосиликатов, синтезированных с техническим углеродом, которая составляет около 680°С, что свидетельствует о формировании углеродных продуктов с относительно невысокой степенью поликонденсации, следовательно, их окислительная регенерация не вызовет особых затруднений.
Рис. 4.
Термограммы цинкалюмосиликатов после их обработки пропаном в течение 6 ч. а – Zn–AC; б – Zn–AC/CП354; в – Zn–AC/CN660.
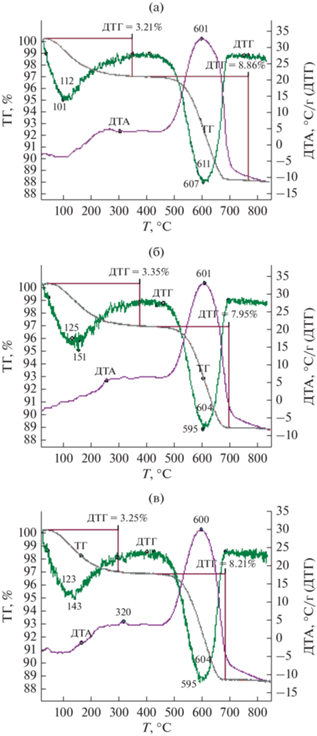
ЗАКЛЮЧЕНИЕ
Таким образом, проведенные исследования показали, что цинкалюмосиликаты с микро-мезопористой структурой являются эффективными катализаторами процесса превращения пропана в ароматические углеводороды. Это обусловлено вторичной мезопористостью, что облегчает доступ реагирующих молекул к активным центрам катализатора и способствует быстрой диффузия продуктов в ходе реакции. Дополнительное формирование мезопор в структуре цинкалюмосиликатов уменьшает количество образующихся полициклических ароматических соединений на их поверхности и в объеме, приводя к снижению интенсивности протекания процесса коксообразования и появлению менее конденсированных продуктов уплотнения.
Список литературы
Травкина О.С., Аглиуллин М.Р., Кутепов Б.И. // Катализ в промышленности. 2021. Т. 21. №. 5. С. 297.
Дементьев К.И., Паланкоев Т.А., Абрамова Д.С., Кузнецов П.С., Золотухина А.В., Максимов А.Л., Хаджиев С.Н. // Нефтехимия. 2019. Т. 59. № 7. С. 768.
Tian H., Zhang Zh., Ma X. // Кинетика и катализ. 2018. Т. 59. № 5. С. 610.
Восмерикова Л.Н., Восмериков А.В. // Нефть. Газ. Новации. 2021. № 6 (247). С. 7.
Martınez C., Corma A. // Coord. Chem. Rev. 2011. V. 255. P. 1558.
Masalska A., Jaroszewska K., Grzechowiak J.R. // Кинетика и катализ. 2019. Т. 60. № 6. С. 825.
Григорьева Н.Г., Аглиуллин М.Р., Костылева С.А., Бубеннов С.В., Бикбаева В.Р., Гатаулин А.Р., Филиппова Н.А., Кутепов Б.И., Нарендер Н. // Кинетика и катализ. 2019. Т. 60. № 1. С. 81.
Xu X., Zhang Y., Li X., Xia X., Jiang H., Toghan A. // Micropor. Mesopor. Mater. 2021. V. 315. P. 110926.
Lee B.J., Hur Y.G., Kim D.H., Lee S.H., Lee K.-Y. // Fuel. 2019. V. 253. P. 449.
Зайковский В.И., Восмерикова Л.Н., Восмериков А.В. // Кинетика и катализ. 2012. Т. 53. № 6. С. 778.
Liang T., Fadaeerayeni S., Toghiani H., Xiang Y., Shan J., Wang H., Cheng J., Li T. // Ind. Eng. Chem. Res. 2019. V. 58. P. 17699.
Al-Khattaf S., de Lasa H. // Ind. Eng. Chem. Res. 1999. V. 38. P. 1350.
Al-Sabawi M., Atias J.A., de Lasa H. // Ind. Eng. Chem. Res. 2008. V. 47. P. 7631.
Christensen C.H., Johannsen K., Törnqvist E., Schmidt I., Topsøe H. // Catal. Today. 2007. V. 128. P. 117.
Perez-Ramırez J., Christensen C.H., Egeblad K., Christensen C.H., Groen J.C., // Chem. Soc. Rev. 2008. V. 37. P. 2530.
Corma A. // Chem. Rev. 1997. V. 97. P. 2373.
Chen H., Zhou S., Chen M., Wu L. // J. Mater. Chem. 2012. V. 22. P. 25207.
Князева Е.Е., Шкуропатов А.В., Засухин Д.С., Добрякова И.В., Пономарева О.А., Иванова И.И. // Журн. физ. химии. 2019. Т. 93. № 10. С. 1538.
Linares N., Silvestre-Albero A.M., Serrano E., Silvestre-Albero J., García-Martínez J. // Chem. Soc. Rev. 2014. V. 43. P. 7681.
Lopez-Orozco S.A., Inayat A., Schwab A., Selvam T., Schwieger W. // Adv. Mater. 2011. V. 23. P. 2602.
Степанов А.А., Коробицына Л.Л., Восмериков А.В. // Химия в интересах устойчивого развития. 2020. Т. 28. № 3. С. 300.
Schmidt I., Boisen A., Gustavsson E., Stahl K., Pehrson S., Dahl S., Carlsson A., Jacobsen C.J.H. // Chem. Mater. 2001. V. 13. P. 4416.
Boisen A., Schmidt I., Carlsson A., Dahl S., Brorson M., Jacobsen C.J.H. // Chem. Commun. 2003. P. 958.
Selvaraj K. // Micropor. Mesopor. Mater. 2010. V. 135. P. 82.
Janssen A.H., Schmidt I., Jacobsen C.J.H., Koster A.J., de Jong K.P. // Micropor. Mesopor. Mater. 2003. V. 65. P. 59.
Wang H., Du G., Jia J., Chen S., Su Z., Chen R., Chen T. // Front. Chem. Sci. Eng. 2021. V. 15. P. 1444.
Восмериков А.А., Восмерикова Л.Н., Барбашин Я.Е., Восмериков А.В., Романова Е.В. // НефтеГазоХимия. 2021. № 1–2. С. 72.
Su L., Liu L., Zhuang J., Wang H., Li Y., Shen W., Xu Y., Bao X. // Catal. Lett. 2003. V. 91 P. 155.
Shu Y., Xu Y., Wong S., Wang L., Guo X. // J. Catal. 1997. V. 170. P. 11.
Kapustin G.I., Brueva T.R., Klyachko A.L. // Appl. Catal. 1988. V. 42. P. 239.
Дополнительные материалы отсутствуют.
Инструменты
Кинетика и катализ