Кристаллография, 2019, T. 64, № 1, стр. 120-126
Специфика структуры стали 35 после закалки деформирующим резанием
А. Г. Дегтярева 1, О. М. Жигалина 1, 2, *, Д. Н. Хмеленин 2, В. Н. Симонов 1
1 Московский государственный технический университет
Москва, Россия
2 Институт кристаллографии им. А.В. Шубникова ФНИЦ “Кристаллография и фотоника” РАН
Москва, Россия
* E-mail: zhigal@crys.ras.ru
Поступила в редакцию 20.03.2018
После доработки 20.03.2018
Принята к публикации 12.04.2018
Аннотация
Проведено исследование стали 35 после высокоскоростной обработки деформирующим резанием. Установлены фазовый состав и особенности структуры упрочненного поверхностного слоя, состоящего из областей (ребер) с аналогичными периодическими неоднородностями. В области ребра, прилегающей к резцу, обнаружена мартенситоподобная структура с разной степенью дисперсности (1–3 мкм). В зоне, удаленной от воздействия резца, преобладают ферритные области с зернами размером 1.0–1.5 мкм. Выявленная периодическая неоднородность структуры обусловлена неравномерным распределением температурного поля в процессе деформирующего резания. Методами электронной микроскопии обнаружено частичное растворение, изменение формы и размеров пластин цементита в матрице α-Fe в результате пластической деформации.
ВВЕДЕНИЕ
Скоростные воздействия концентрированными потоками энергии, такие как лазерное излучение, плазменная закалка, электронно-лучевая и ультразвуковая обработка, приводят к изменению свойств поверхностного слоя материалов и характеризуются разнообразием структурных процессов. Особое место среди указанных воздействий занимают скоростные обработки с целью упрочнения поверхности, в результате которых помимо интенсивного теплового воздействия осуществляется пластическая деформация поверхностного слоя. К таким обработкам относятся, например, электромеханическая и фрикционно-упрочняющая закалка шлифованием, специальное точение. Несмотря на различие технологических процессов, все эти методы объединяет следующее: при обработке происходит интенсивное воздействие на локальные объемы материала, что приводит к формированию особых структур, принципиально отличающихся от хорошо известных, полученных в результате традиционной термической обработки.
Специфика теплового воздействия при высокоскоростных обработках материалов приводит к изменению температуры фазовых превращений. Например, превращение α-Fe–γ-Fe в сталях может сдвигаться в область более высоких температур [1, 2], а температурный интервал превращений расширяться с увеличением скорости нагрева [3, 4.] Экстремальные температурно-временные условия могут изменять механизмы фазовых превращений и кинетику формирования структуры в процессе кристаллизации. Например, высокоскоростной нагрев дает возможность, по крайней мере, частично реализовать бездиффузионный сдвиговой механизм образования аустенита [5]. Исследования многих авторов свидетельствуют, что повышение скорости нагрева приводит к увеличению дисперсности структур материалов [6–10], существенно изменяются механизм и скорость процесса рекристаллизации. В [11] экспериментально доказано, что при увеличении скорости нагрева происходит подавление процессов возврата и совмещение их по времени и температуре с процессом рекристаллизации. И хотя изучение природы формирования структур при скоростных обработках ведется достаточно давно, единого мнения на этот вопрос не существует до сих пор.
Метод деформирующего резания относится к высокоскоростной механико-термической обработке, в результате которой значительно упрочняется поверхностный слой материала [12, 13]. Немаловажным преимуществом метода является использование стандартного металлорежущего оборудования и простого инструмента. Технология деформирующего резания является безотходной – образующаяся при резании стружка не отделяется от заготовки, а сохраняет с ней механическую связь. В результате такой обработки на поверхности материала формируется рельеф в виде наклонных ребер (рис. 1), плотно (без зазора) прилегающих друг к другу [14].
Рис. 1.
Типичная микроструктура стали 35 после деформирующего резания: 1 – обработанная поверхность, 2 – необработанная сердцевина.
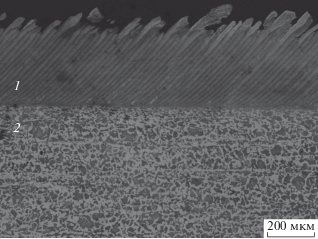
Ранее проведенные исследования стали 35 [15–18] показали, что в результате деформирующего резания на поверхности можно наблюдать структуру как полной, так и неполной закалки в сочетании друг с другом или со структурой деформированной матрицы. Было установлено, что полученное структурное состояние обеспечивает трехкратное увеличение твердости обработанной поверхности материала. В настоящей работе исследованы особенности структурного состояния, формирующегося в процессе деформирующего резания стали 35, для установления его влияния на механические свойства упрочненного слоя.
МАТЕРИАЛЫ И МЕТОДЫ ИССЛЕДОВАНИЯ
Анализ воздействия деформирующего резания на поверхностный слой проводили на образцах стали 35, так как структура этого материала, полученная традиционными способами термической обработки, хорошо известна. В связи с этим можно выявить структурные особенности, вызванные экстремальным воздействием деформирующего резания. В соответствии с диаграммой состояния Fe–C состав стали позволяет эффективно провести такую обработку для получения в зоне резания структурного состояния, обеспечивающего упрочнение поверхности. Применение деформирующего резания для подобных материалов в производстве легко вписать в технологический цикл без дополнительных затрат на модернизацию действующего оборудования.
В качестве заготовки использовали вал диаметром 63 мм после нормализации. Химический состав представлен в таблице. Параметры деформирующего резания определяли из необходимости обеспечения нагрева выше температур фазовых превращений перлит–аустенит и феррит–аустенит по всему поверхностному слою, формируемому в результате обработки. Эти условия выполняются при использовании резца с особой геометрией, высокой скорости резания V ≥ 3 м/c и других параметров [19].
Таблица 1.
Химический состав стали 35
Химический элемент | Fe | C | Si | Mn | Ni | Cr |
---|---|---|---|---|---|---|
Содержание, мас. % | 98 | 0.38 | 0.27 | 0.61 | до 0.03 | до 0.05 |
Исследуемые образцы подвергали высокоскоростной закалке деформирующим резанием на кафедре “Инструментальная техника и технологии” МГТУ им. Н.Э. Баумана. Для сравнения была проведена объемная закалка в режиме нагрева до 860°С, выдерживания в течение 15 мин и охлаждения в воде.
Для исследования структуры и фазового состава образцов использованы следующие методы. Металлографический анализ поверхности шлифов проводили с использованием микроскопа Olympus GX51 с увеличением до 1000 крат. Для выявления структуры поверхность шлифов подвергали травлению 4%-ным раствором HNO3 в C2H5OH. Микротвердость образцов измеряли на автоматическом микротвердомере EMCO-TEST DuraScan 70 при нагрузке 100 г. Рентгенографические исследования выполняли с помощью дифрактометра ДРОН-3 (CuKα-излучение) в диапазоне углов 2θ = 70°–90°, захватывающем отражение от плоскости (211). Изображения поверхности образцов получены с помощью растрового электронного микроскопа (РЭМ) VEGA TESCAN при ускоряющем напряжении 10–20 кВ в режиме детектирования вторичных электронов. Исследования методами просвечивающей электронной микроскопии (ПЭМ), просвечивающей растровой микроскопии (ПРЭМ), энергодисперсионного и дифракционного анализа выполнены с помощью микроскопа Tecnai G230ST при ускоряющем напряжении 300 кВ. Анализ полученных данных проводили с помощью программ Digital Micrograph, JEMS. Образцы для ПЭМ-исследований в виде фольг готовили механической полировкой и электрохимическим травлением.
РЕЗУЛЬТАТЫ И ИХ ОБСУЖДЕНИЕ
Микроструктура стали 35 после закалки в процессе деформирующего резания и объемной закалки показана на рис. 2. Структура на рис. 2а характерна для стали 35 после объемной закалки при 860°С и охлаждения в воде. Образец представляет собой мартенситные кристаллы игольчатой формы. Как следует из сравнения двух изображений, характерным признаком макроструктуры образца, подвергнутого деформирующему резанию (рис. 2б), является присутствие волокон, направленных преимущественно вдоль ребер поверхностного слоя. Такая картина свидетельствует о деформации и течении металла. Кроме того, можно заметить светлые включения, неравномерно распределенные по сечению ребра (стрелки на рис. 2б).
Рис. 2.
Микроструктура стали 35: а – после объемной закалки (860°С, 15 мин), б – область ребра после деформирующего резания (стрелками отмечены светлые включения).
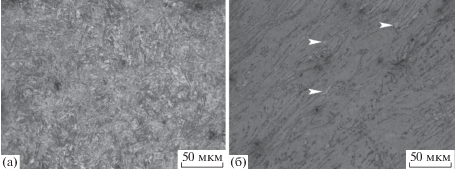
Более детальное изучение структуры с помощью РЭМ (рис. 3) выявило мартенситоподобные кристаллы матричной фазы размером в основном 1–3 мкм и равноосные зерна избыточного феррита размером 1.0–1.5 мкм, заключенного в волокна. По-видимому, феррит претерпевает значительную пластическую деформацию и динамическую рекристаллизацию. Известно, что процессы полигонизации при быстром нагреве подавляются [11]. В связи с этим на изображении отсутствуют субзерна.
Рис. 3.
РЭМ-изображение структуры ребра: а – участок с мартенситоподобной структурой (МП) на прирезцовой зоне ребра, б – участок с ферритными зернами (Ф) на свободной зоне ребра.
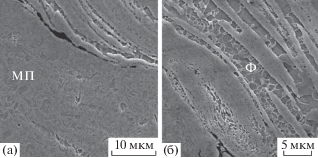
Благодаря такой структуре поверхностный слой имеет высокую твердость. На рис. 4а представлена схема отдельного ребра, на рис. 4б черными квадратами отмечены места, в которых проводили измерения микротвердости – они расположены вдоль линии на середине ребра. Значения микротвердости в поверхностном (обработанном) слое составляли 650–670 HV0.1, а в сердцевине, не подвергнутой обработке, – 250 HV0.1. Средние значения микротвердости мартенситоподобных участков составляли 710 HV0.1, а ферритных – 550 HV0.1.
Рис. 4.
Соотношение различных структурных и термических зон ребер при деформирующем резании: а – схематическое изображение отдельного ребра с различными структурными зонами, б – микрофотография ребра, черными квадратами отмечены места измерений микротвердости; в – схема образования ребер с различными областями структуры (1 – прирезцовая зона ребра, 2 – свободная зона ребра) и распределением температуры по ширине одного ребра (более темный цвет соответствует боле высокой температуре).
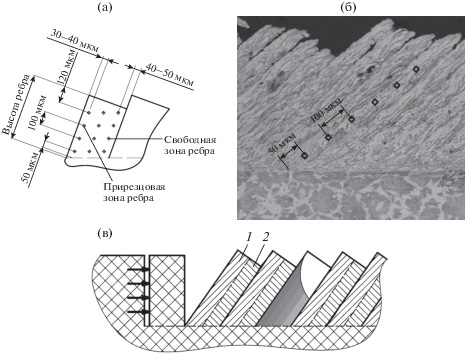
Необходимо отметить интересную особенность: равноосные зерна феррита по большей части концентрируются на свободной зоне ребра и практически отсутствуют в прирезцовой (рис. 4б). Это свидетельствует о полной закалке прирезцовой зоны ребра. Максимальные значения микротвердости в прирезцовой зоне достигали 840 HV0.1, что значительно выше, чем в середине ребра.
Как показывают данные [20], экстремальные условия воздействия деформирующего резания на обрабатываемый материал приводят к тому, что за счет трения и пластической деформации температура в зоне резания может достигать 1100°С, время нагрева составляет 4 × 10–4 с. Высокоскоростной нагрев при деформирующем резании (со скоростью ~106 град/с) позволяет получать температуру более 1100°С в зоне резания. Это происходит за счет действия двух независимых источников деформации и трения, а последующее быстрое охлаждение осуществляется за счет отвода тепла в заготовку и окружающую среду и приводит к закалке поверхности на глубину до 1 мм.
При деформирующем резании распределение температуры в объеме отдельного ребра очень неравномерно. На рис. 4в показано схематическое изображение различных зон ребер и увеличенное изображение распределения температур в одном ребре. Более темные участки соответствуют более высокой температуре.
Максимальный нагрев приходится на прирезцовую зону ребра, она может прогреваться выше температуры АС3 (для стали 35 АС3 = 810°С). По мере отдаления от резца температура прогрева понижается, и свободная зона ребра может быть нагрета только до температуры АС1 (для стали 35 АС1 = 730°С), поэтому в этих зонах структура материала может значительно различаться. Учитывая все сказанное выше, можно заключить, что прирезцовая зона ребра испытывает полную закалку с образованием мартенситоподобной структуры, а дополнительные включения рекристаллизованного феррита в свободной зоне ребра – это результат неполной закалки.
В связи с тем что время нагрева очень мало (тысячные доли секунды), фазовое превращение перлита при АС1 полностью не завершается, так как растворение углерода в таких условиях ограничено. Расчеты диффузионного пути [21] показали, что его длина составляет десятки нанометров. Таким образом, оценка пути диффузии углерода из исходного цементита в феррит зависит от локальных условий и в данном случае лежит в диапазоне от единиц до десятков нанометров. Поэтому полностью раствориться цементит не может. Для проверки этого предположения были проведены исследования структуры поверхностного слоя методами ПЭМ и энергодисперсионного анализа. На рис. 5 представлены ПЭМ-изображения поверхности образца стали 35 после обработки деформирующим резанием. Во всем объеме материала присутствуют пластинчатые выделения, значительно различающиеся по размерам. Их толщина варьируется от нескольких десятков нанометров до десятых долей микрона (рис. 5а). Встречаются прямые и изогнутые ламели переменной ширины, причем последние изогнуты в соответствии с деформацией слоев окружающей матрицы.
Рис. 5.
ПЭМ-изображения структуры стали 35: а – темнопольное изображение мелких ламелей цементита, б – ферритная матрица с дефектами в слабом пучке, в – ее электронограмма, г – темнопольное изображение крупных включений цементита округлой формы.
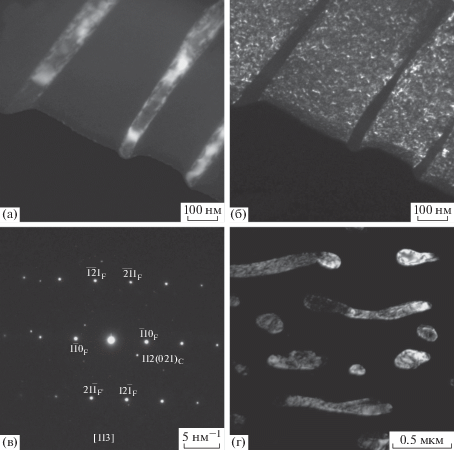
Анализ межплоскостных расстояний на дифракционных картинах показал, что матрица представляет собой фазу α-Fe. Дополнительные, более слабые по интенсивности рефлексы соответствуют межплоскостным расстояниям цементита (Fe3C). На рис. 5в представлена характерная электронограмма, на которой матричные рефлексы α-Fe составляют зону с осью [113], а рефлексы цементита отмечены индексом С. Отметим, что в областях между пластинами на темнопольных изображениях, полученных в режиме слабого пучка, хорошо видна высокая концентрация дефектов кристаллического строения, в основном дислокаций (рис. 5б).
На рис. 5г представлены темнопольные изображения округлых включений цементита. По-видимому, исходные частицы подвергались дроблению, места скола и отдельные обломки сфероидизировались в процессе термического воздействия при деформирующем резании.
Проведенные сравнительные исследования дифрактограмм стали 35 после стандартной закалки (860°С, 15 мин) и деформирующего резания показали в обоих случаях только одну фазу α-Fe (рис. 6). Однако линии дифрактограмм образца после деформирующего резания (рис. 6б) характеризуются большим уширением, а интенсивность пика существенно снижается. Обнаружено изменение положения пика после обработки деформирующим резанием – сдвиг линии дифрактограммы в область малых углов, что свидетельствует об увеличении межплоскостного расстояния d(211), которое по расчетам составило 1.173 ± 0.003 Å при деформирующем резании, в то время как после традиционной объемной закалки этот параметр составлял 1.171 ± 0.003 Å.
Рис. 6.
Участок дифрактограммы стали 35: а – после объемной закалки (860°С, 15 мин), б – после обработки деформирующим резанием.
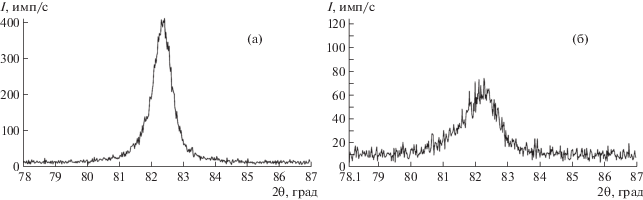
Морфология цементита особенно хорошо видна в темнопольном просвечивающе-растровом режиме (рис. 7а). Протяженность пластин ограничена размером зерен. Энергодисперсионный анализ показал повышенное содержание углерода в светлых областях, которые соответствуют расположению пластин цементита (рис. 7б). Таким образом, ПЭМ-исследования подтверждают предположение о присутствии цементита различной морфологии в упрочненном поверхностном слое после деформирующего резания.
Рис. 7.
Расположение пластин цементита в зернах ферритной матрицы: а – ПРЭМ-изображение участка фольги; б – концентрационные профили Fe и С вдоль линии 1, проведенной на рис. а. Точка на этой линии соответствует вертикальной линии на профиле. Точка расположена в месте локализации пластины цементита, на концентрационном профиле можно наблюдать уменьшение содержания железа и увеличение концентрации углерода. Такие же изменения концентраций элементов наблюдаются в месте расположения других пластин.
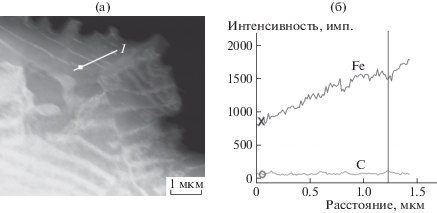
ЗАКЛЮЧЕНИЕ
Методами электронной микроскопии проведено исследование структуры поверхностных слоев стали 35, сформированных при высокоскоростном термическом воздействии в процессе деформирующего резания.
Установлены следующие основные особенности структуры. Ребра, образующиеся на поверхности образцов, имеют неоднородную структуру. В прирезцовой зоне (область ребра, прилегающая к резцу) расположены в основном области размером 2–3 мкм с мартенситоподобной структурой. В свободной зоне (удаленной от резца) они имеют размер менее 1 мкм. Преобладают ферритные области. Зерна в ферритных областях имеют размер 1.0–1.5 мкм. Обнаруженная неоднородность структуры ребер обусловлена распределением температурного поля в процессе обработки деформирующим резанием.
Высокоскоростное термическое воздействие приводит к частичному растворению пластин цементита в матрице α-Fe, они изгибаются, дробятся в результате пластической деформации на фрагменты, может меняться их форма в зоне скола.
Авторы выражают благодарность В.В. Попцову за обработку образцов методом деформирующего резания и Н.Ю. Табачковой за приготовление фольг для ПЭМ-исследований.
Работа выполнена c использованием оборудования ЦКП “ФНИЦ Кристаллография и фотоника” РАН при поддержке Федерального агентства научных организаций (соглашение № 007-ГЗ/Ч3363/26) и Министерства образования и науки РФ в части исследования структуры методами ПЭМ.
Список литературы
Никишков Н.А., Соколов А.М., Ульянов В.Г. // Металловедение и термическая обработка металлов. 1991. № 8. С. 2.
Залкин В.М. // Металловедение и термическая обработка металлов. 1986. № 2. С. 14.
Лахтин Ю.М. Металловедение и термическая обработка металлов. М.: Металлургия, 1979. 320 с.
Багмутов В.П., Паршев С.Н., Дудкина Н.Г., Захаров И.Н. Электромеханическая обработка: технологические и физические основы, свойства, реализация. Новосибирск: Наука, 2003. 318 с.
Бабей Ю.И. Физические основы импульсного упрочнения стали и чугуна. Киев: Наукова думка, 1988. 238 с.
Гриднев В.Н., Ошкадеров С.П. // Металловедение и термическая обработка металлов. 1987. № 11. С. 19.
Длоуги И., Михаличка П., Шкарек И. и др. // Металловедение и термическая обработка металлов. 1995. № 3. С. 37.
Жигалина О.М., Соснин В.В., Глезер А.М. // Физика металлов и металловедение. 1993. Т. 75. № 2. С. 132.
Ховова О.М., Жигалина О.М., Думанский И.Г. // Металловедение и термическая обработка металлов. 1998. № 9. С. 16.
Ховова О.М., Жигалина О.М., Думанский И.О., Лешковцев В.Г. // Металловедение и термическая обработка металлов. 2000. № 6. С. 13.
Иванов В.И., Осипов К.А. Возврат и рекристаллизация при быстром нагреве. М.: Наука, 1964. 86 с.
Patent 5775187A (USA). Method and Apparatus Producing a Surface with Alternating Ridges and Depressions / Zoubkov N.N., Ovtchinnikov A.I. // № 545640. 1998.
Патент 2556897 (РФ). Способ поверхностного закалочного упрочнения режуще-деформирующим инструментом / Зубков Н.Н., Васильев С.Г., Попцов В.В. // Заявлено 21.01.2014, опубликовано 22.07.2015. Бюл. № 20.
Патент 2015202 (РФ). Способ упрочнения поверхности детали / Зубков Н.Н., Овчинников А.И., Васильев С.Г. и др. // Изобретения. 1994. № 12.
Дегтярева А.Г., Попцов В.В., Симонов В.Н. и др. // Наука и образование. МГТУ им. Н.Э. Баумана. Электрон. журн. 2014. № 9. http://technomag.bmstu.ru/doc/725672.html
Дегтярева А.Г., Симонов В.Н., Иванова А.Ю. // Электрометаллургия. 2017. № 12. С. 31.
Варламова С.Б., Дегтярева А.Г. // Молодежный научно-технический вестн. 2015. № 2. С. 1.
Дегтярева А.Г., Симонов В.Н. Тез. докл. Междунар. науч.-тех. конф. “Инновационные машиностроительные технологии, оборудование и материалы-2015”. Казань, 2–3 декабря 2015.
Зубков Н.Н., Васильев С.Г. // Упрочняющие технологии и покрытия. 2013. № 8. С. 3.
Zubkov N., Poptsov V., Vasiliev S. // Jordan J. Mechan. Industr. Engin. 2017. V. 11. № 1. P. 13.
Бокштейн Б.С. Диффузия в металлах. M.: Металлургия, 1978. 248 с.
Дополнительные материалы отсутствуют.
Инструменты
Кристаллография