Кристаллография, 2022, T. 67, № 2, стр. 233-238
Структура дисперсно-упрочненных лент-подложек на основе меди для ВТСП-2
А. Ю. Дегтяренко 1, 2, *, Е. А. Головкова 3, А. С. Иванов 3, А. В. Овчаров 3, С. В. Крашенинников 3
1 Центр высокотемпературной сверхпроводимости и квантовых материалов им. В.Л. Гинзбурга ФИАН
Москва, Россия
2 Объединенный институт высоких температур РАН
Москва, Россия
3 Национальный исследовательский центр “Курчатовский институт”
Москва, Россия
* E-mail: ayu.degtyarenko@gmail.com
Поступила в редакцию 14.05.2021
После доработки 06.08.2021
Принята к публикации 06.08.2021
- EDN: NFZWXN
- DOI: 10.31857/S0023476122020047
Аннотация
Проведено исследование некоторых особенностей формирования структуры и механических характеристик дисперсно-упрочненной медной ленты в процессе ее изготовления. Исследовано изменение структуры матричной фазы и характеристик диспергированных в ней упрочняющих дисперсных частиц как после механической деформации, так и в результате рекристаллизационного отжига. Особое внимание уделено возможному влиянию дисперсной фазы на текстуру металлических лент-подложек, поскольку именно совершенная текстура ленты необходима для дальнейшего осуществления роста на ней керамических и сверхпроводящего покрытий. Показано, что легирование медной матрицы частицами железа не ухудшает склонность к образованию острой кубической текстуры.
ВВЕДЕНИЕ
Вопрос выбора более перспективной ленты-подложки для роста буферных и сверхпроводящего слоев остается открытым, поскольку при изготовлении лент-подложек для высокотемпературных сверхпроводников второго поколения (ВТСП-2) необходимо учитывать целый ряд весьма противоречивых критериев. При этом выбор высокотехнологичного и экономически эффективного сплава для изготовления лент-подложек для ВТСП-2 до сих пор привлекает пристальное внимание исследователей [1]. В настоящее время ленты ВТСП-2 в основном изготавливают на подложках из нержавеющей стали и никелевых сплавов. Большинство производителей использует сплавы “Хастеллой” или Ni–W [2]. Конкуренцию этим материалам может составить сплав на основе меди. Медь имеет отличную электропроводность и теплопроводность, что позволит в случае потери сверхпроводимости перевести токовую нагрузку на подложку в нормальном состоянии [3]. Кроме того, медь немагнитна, имеет ГЦК-решетку, согласующуюся с последующими функциональными слоями по параметру решетки, и экономически выгодна.
Чтобы улучшить механические свойства, матрицу меди легируют железом, что позволяет значительно повысить предел прочности за счет дисперсного упрочнения. Влияние выделяющихся в медной матрице ферромагнитных наночастиц железа на магнитную подсистему ленты, по-видимому, незначительно в силу их малой концентрации, что является важным критерием при выборе ленты-подложки. Известно, что чистая медь хорошо текстурируется после холодной деформации в процессе прокатки с последующим рекристаллизационным отжигом [4]. Небольшое содержание частиц железа не должно повлиять на остроту кубической текстуры, которая важна при последующем формировании буферных и сверхпроводящего ReBCO (Re – редкоземельный металл, B – Ba, C – Cu, O – O7 – δ) слоев. Одним из основных недостатков медной подложки является высокая склонность к окислению, поэтому ее покрывают тонким слоем Ni, который посредством последующего отжига повторяет текстуру меди [5].
За счет введения в матрицу второй фазы можно добиться значительного увеличения прочности. Размер и форма частиц, расстояние между ними, равномерное распределение дисперсных частиц в матрице определяют прочностные свойства [6].
Детальное изучение структуры и механических характеристик лент на основе сплава медь–железо описано в [7]. Однако остается ряд важных вопросов, не затронутых в данной работе. В частности, практически не исследованы изменения характеристик дисперсной фазы, структуры и текстуры ленты до и после рекристаллизационного отжига, интересовались в основном конечным результатом. Эти свойства весьма важны для разработки путей оптимизации технологии производства лент и улучшения их характеристик.
Цель настоящей работы заключалась в исследовании особенностей формирования структуры и механических характеристик дисперсно-упрочненной медной ленты в процессе ее изготовления. Для этого необходимо проследить за изменением структуры матричной фазы и характеристик диспергированных в ней упрочняющих дисперсных частиц как после механической деформации, так и в результате рекристаллизационного отжига. Особое внимание следует уделить возможному влиянию дисперсной фазы на текстуру металлических лент-подложек Cu–Fe, поскольку именно совершенная текстура ленты необходима для дальнейшего осуществления роста на ней керамических и сверхпроводникового покрытий.
ЭКСПЕРИМЕНТАЛЬНАЯ ЧАСТЬ
Объекты исследования. В качестве исходных образцов использованы холоднокатаные и после рекристаллизационного отжига металлические ленты-подложки Сu–1.6 ат. % Fe, изготовленные в Институте физики металлов им. М.Н. Михеева УрО РАН [7]. Сплав Сu–1.6 ат. % Fe выплавляли на основе чистой меди 99.997% и карбонильного переплавленного железа чистотой 99.94% в алундовом тигле в атмосфере аргона в вакуумной индукционной печи.
Сплавы предварительно выплавляли в слитки, которые остывали вместе с печью довольно продолжительное время. После этого проводили холодную двухступенчатую деформацию прокаткой, при которой формируется текстура подложки. Холодную деформацию заготовок осуществляли в два этапа: первый на стане с диаметром валков 180 мм (деформация ~ 90%, число проходов 40); второй на двухвалковом прокатном стане с полированными валками до толщины 90 мкм, степень холодной деформации составляла 98.9%. Рекристализационный отжиг ленты для формирования конечной текстуры проводили в вакуумной печи в восстанавливающей среде Ar + 4% H2 при 850°С в течение часа.
Методы исследования. Кристаллическую структуру образцов изучали методом рентгеноструктурного анализа на дифрактометре D8 Advance (Bruker AXS, Германия) c использованием графитового монохроматора на дифрагированном пучке. Использовалось рентгеновское излучение CuKα, фокусировка по Брэггу–Брентано.
Исследования микроструктуры проводили на просвечивающем (растровом) электронном микроскопе Titan 80–300 (FEI, США), снабженном корректором сферической аберрации пробы (Cs-корректор), рентгеновским спектрометром (EDAX, США) и анализатором характеристических потерь энергий электронов (Gatan, США). В проводимых исследованиях ускоряющее напряжение составляло 300 кВ. Поперечные срезы сплавов для исследования микроструктуры методом просвечивающей электронной микроскопии (ПЭМ) были приготовлены с помощью фокусированного ионного пучка Ga+ (ФИП) в растровом электронно-ионном микроскопе Helios (FEI, США). Концентрацию железа в медной матрице определяли методом рентгенофлуоресцентного анализа на рентгеновском спектрометре S4 PIONEER (Bruker AXS, Германия). Анализ текстуры отожженных лент Cu–1.6% Fe проводили на рентгеновском дифрактометре Rigaku Smartlab (Rigaku Corp., Япония). Механические свойства образцов исследовали на разрывной машине 5kN Static Load Cell (Instron, США).
РЕЗУЛЬТАТЫ ИССЛЕДОВАНИЙ И ИХ ОБСУЖДЕНИЕ
Исследование микроструктуры лент-подложек. На рис. 1а представлено электронно-микроскопическое изображение поперечного среза образца после холодной деформации прокаткой. На полученном изображении отчетливо видны структура вытянутых вдоль направления прокатки зерен меди и выделившиеся в медной матрице частицы эллиптической формы со средним размером ~30 нм.
Рис. 1.
Микроструктуры ленты-подложки сплава Cu–1.6% Fe: а – после холодной деформации прокаткой, б – после рекристаллизационного отжига.
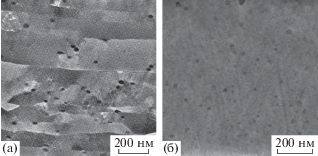
Предел растворимости железа в меди составляет ~1 ат. %. Поэтому при остывании слитка образуется пересыщенный твердый раствор железа в меди, который может частично распасться с выделением дисперсных частиц железа. Характерное время образования железных включений τ можно оценить по среднему расстоянию между включениями и коэффициенту диффузии железа в меди вблизи температуры плавления меди. Предэкспоненциальный множитель D0 объемной диффузии железа в меди согласно [8] равен 0.03 × × 10–4 м2/с, значение энергии активации E = = 187 кДж/моль, температура плавления меди Tпл = 1360 К. В соответствии с законом Аррениуса коэффициент диффузии выражается следующей формулой:
где R = 8.314 Дж/(К моль) – газовая постоянная, T – температура.Таким образом, значение коэффициента диффузии при температуре плавления меди составляет D = 1.95 × 10–13 м2/с. По полученным микроструктурным данным проведем оценку среднего расстояния между частицами. На площади S = = 10–12 м2 количество частиц N ~ 50. Тогда концентрация частиц С на единицу площади составляет
Отсюда можем найти оценку характерного времени образования включений τ: где $l = 1{\text{/}}\sqrt С \approx 1.41 \times {{10}^{{ - 7}}}~$ м.Таким образом, характерное время, при котором происходит выделение частиц при охлаждении, составляет ~0.1 с. Время охлаждения слитка существенно больше. Следовательно, образование наблюдавшихся включений вполне возможно при остывании первоначального слитка. Дополнительному выделению частиц железа в медной матрице способствует холодная деформация прокаткой. В процессе такой деформации в сплаве Cu–Fe происходят механоактивационные процессы, в ходе которых также выделяется дисперсная фаза частиц Fe.
Как отмечалось выше, в результате холодной деформации имеют место вытягивание медных зерен и лишь небольшая деформация дисперсных включений, приобретающих эллиптическую форму (рис. 1а). По-видимому, это связано с тем, что предел текучести меди существенно меньше предела текучести железа, а их увеличение в процессе прокатки происходит симбатно. Поэтому в процессе деформации “течет” в основном медь, а железные включения деформируются в последнюю очередь, т.е. только тогда, когда при значительном наклепе пределы текучести медной матрицы и железных включений становятся близки друг другу. Кроме того, при размерах включений меньше 100 нм существенную роль может играть размерная зависимость коэффициента текучести ${{{{\sigma }}}_{y}}$, описываемая законом Холла–Петча:
где ${{{{\sigma }}}_{0}}$ – внутреннее напряжение, препятствующее движению дислокации; ${{k}_{y}}$ – коэффициент, связанный с проницаемостью границы зерна движению дислокаций; $D$ – размер зерна. Показатель степени n изменяется от 1/2 (классический закон Холла–Петча) до значений, лежащих в интервале 1/4–1. Каждому значению показателя степени n соответствует свой, характерный механизм взаимодействия дислокаций с границами зерен. Отметим, что при размерах зерен, превышающих 10–6 м, для металлов и сплавов наблюдается достаточно хорошее выполнение классического закона с показателем n = 1/2 [9, 10].На рис. 1б представлено электронно-микроскопическое изображение поперечного среза образца после рекристаллизационного отжига. Согласно изображению, произошла рекристаллизация матричной фазы. Явно видимые на рис. 1а вытянутые вдоль направления деформации границы пропали. Концентрация частиц дисперсной фазы возросла. Кроме того, после рекристаллизационного отжига частицы приобрели более округлую форму. Средний размер частиц снизился до 20 нм за счет дополнительного выделения более мелкой фракции.
Проведен анализ распределения частиц по размерам. Существует несколько методик для оценки такого распределения. Самыми простыми являются локальные методы оптической и растровой электронной микроскопии [11]. Используя метод ФИП, вырезается несколько ламелей с разных участков образца. Микроструктура полученных ламелей (в частности, выделения дисперсных частиц) исследуется в ПЭМ. Далее стандартным металлографическим методом сеток подсчитывается число частиц в заданных интервалах размеров. Для оценки статистического распределения частиц получены изображения микроструктуры поперечных срезов ленты Сu–1.6 ат. % Fe, вырезанных из различных мест образца. Для анализа выбраны и посчитаны более 300 частиц. По полученным оценкам средний размер частиц в матрице составляет 20 ± 2 нм. С помощью статистического анализа получена гистограмма распределения частиц по размерам (рис. 2), на которой видно присутствие более мелкой фракции дисперсных включений, выделившихся в процессе рекристаллизационного отжига. По приведенной гистограмме (рис. 2) происходит рост более мелкой фракции ~ 5–10 нм.
С помощью энергодисперсионного рентгеновского микроанализа найдены профили распределения Fe в медной матрице (рис. 3). Согласно полученным данным наблюдавшиеся дисперсные включения представляют собой частицы железа.
Рис. 3.
ПРЭМ-изображение поперечного среза медной матрицы (а). Увеличенное изображение выделенной области (стрелкой указано направление сканирования) с линейным профилем распределения элементов (б).
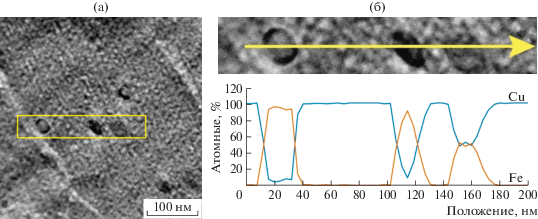
Исследование текстуры лент-подложек. Методом рентгеновской дифрактометрии θ–2θ исследованы образцы лент-подложек Сu–1.6 ат. % Fe после холодной деформации прокаткой со степенью обжатия 98% и после последующего рекристаллизационного отжига. Образцы фиксировались и снимались под скользящим пучком. На рис. 4а представлен спектр ленты-подложки после холодной деформации прокаткой. В ГЦК-металлах с высокой энергией дефектов упаковки способом деформации является скольжение. Данные дифрактограммы свидетельствуют о том, что зерна разориентированы, наблюдаются уширение и смещение пиков, так как система находится в напряженно-деформированном состоянии. Способность зародыша рекристаллизации к росту во многом определяется областями деформированного поликристалла, имеющими различные ориентировки. Следовательно, текстура рекристаллизации развивается из текстуры деформации. На рис. 4б представлена дифрактограмма образца после рекристаллизационного отжига. Приведенная дифрактограмма содержит только один пик, соответствующий отражению (002). Следовательно, образец характеризуется наличием высокой текстурированности ленты-подложки Сu–1.6 ат. % Fe, что свидетельствует об ориентированном росте зерен вдоль плоскости (200) в процессе рекристаллизационного отжига. На рис. 4в приведена линия (002) отожженного образца в увеличенном масштабе. Наблюдается уширение пика при угле 2θ = 52°, возможно, связанное с вкладом линии железа дисперсной фазы.
Рис. 4.
Дифрактограммы лент-подложек Сu–1.6 ат. % Fe: а – после холодной деформации прокаткой, б, в – после рекристаллизационного отжига (в разных масштабах).
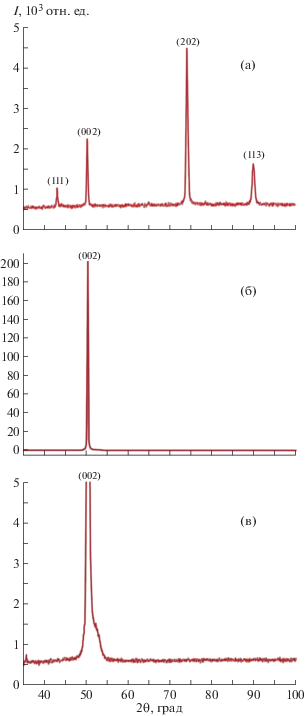
Острая кубическая текстура является важным структурно-чувствительным свойством для последующего ориентированного роста буферных и сверхпроводящего слоев. Поэтому было проведено более детальное изучение текстуры образцов. На рис. 5 представлена полюсная фигура {111} для Сu–1.6 ат. % Fe. Рассеяние кубической текстуры составляет ~5°.
Полученный результат подтверждает вывод о наличии высокой текстурированности ленты, сделанный на основе рентгеноструктурного анализа (рис. 4б). Таким образом, заметного влияния дисперсной фазы железа на текстуру лент Сu–1.6 ат. % Fe не обнаружено.
Механические свойства лент-подложек Cu–Fe. Лента-подложка служит каркасом в ВТСП-2, следовательно, важно учитывать ее механические характеристики. Чистая медь не обладает необходимыми конструкционными свойствами, поэтому для упрочнения ее необходимо легировать железом. В табл. 1 приведены механические свойства холоднокатаных лент чистой Cu и Сu–1.6 ат. % Fe после деформации прокаткой, испытанные на разрывной машине Instron, а также данные лент после отжига [7].
Таблица 1.
Предел текучести лент-подложек Cu–Fe
Образец | Ширина, мм |
Толщина, мкм |
Предел текучести σ0.2, MPa | Погрешность измерения, % |
---|---|---|---|---|
Сu–1.6 ат. % Fe (холоднокатаная) | 10.0 ± 0.5 | 80 ± 2 | 460 | ± 0.5 |
Cu (холоднокатаная) | 10.0 ± 0.5 | 80 ± 2 | 411 | ± 0.5 |
Сu–1.6 ат. % Fe (отожженная) | 10.0 ± 0.5 | 80 ± 2 | 78 | ± 0.5 |
Cu (отожженная) | 10.0 ± 0.5 | 80 ± 2 | 25 | ± 0.5 |
Согласно приведенным результатам, в холоднокатаном состоянии лента нагартована, соответственно, прочностные характеристики увеличены. При этом холоднокатаная лента, содержащая частицы железа, обладает заметно большими значениями σ0.2. После рекристаллизационного отжига предел текучести уменьшается. При этом примесь железа в данных образцах (Сu–1.6 ат. % Fe) позволяет повысить предел текучести в 3 раза по сравнению с чистой медью.
ЗАКЛЮЧЕНИЕ
Проведено исследование особенностей формирования структуры и механических характеристик дисперсно-упрочненной медной ленты в процессе ее изготовления. Изучено изменение структуры матричной фазы и характеристик диспергированных в ней упрочняющих дисперсных частиц как после механической деформации, так и в результате рекристаллизационного отжига. Особое внимание уделено возможному влиянию дисперсной фазы на текстуру металлических лент-подложек, поскольку именно совершенная текстура ленты необходима для дальнейшего осуществления роста на ней керамических и сверхпроводящего покрытий.
На электронно-микроскопических изображениях образцов холоднокатаных лент отчетливо наблюдаются структура вытянутых за счет прокатки зерен меди и выделившиеся в медной матрице частицы железа эллиптической формы со средним размером ~30 нм. Оценка характерного времени образования дисперсных включений железа показала, что образование наблюдавшихся включений вполне возможно при остывании первоначального слитка. Дополнительному выделению частиц железа в медной матрице способствует холодная деформация прокаткой. В процессе холодной деформации в сплаве Cu–Fe происходят механоактивационные процессы, в ходе которых также может выделяться дисперсная фаза частиц железа. После отжига наблюдается рекристаллизация медной матрицы, а диспергированные в матричной фазе частицы приобретают округлую форму. При этом средний размер частиц снижается до 20 нм за счет дополнительного выделения более мелкой фракции частиц железа.
Дифрактограмма образца после отжига содержит только один пик, соответствующий отражению (002), что свидетельствует о наличии высокой текстурированности ленты-подложки Сu–1.6 ат. % Fe и ориентированном росте зерен вдоль плоскости (200) в процессе рекристаллизационного отжига. При этом легирование медной матрицы частицами железа не ухудшает склонность к образованию острой кубической текстуры. Согласно рентгенографическим исследованиям рассеяние кубической текстуры составляет ~5°.
Предел текучести лент Cu–Fe после деформации резко возрастает и равен ~450 МПа, после рекристаллизационного отжига снижается до ~78 МПа, но остается в 3 раза выше предела текучести ленты из отожженной меди. Таким образом, ленты-подложки на основе Сu–Fe представляют большой интерес для дальнейшего исследования возможности их использования в качестве лент-подложек для ВТСП-2.
Авторы выражают благодарность Ю.В. Хлебниковой (Институт физики металлов им. М.Н. Михеева УрО РАН) за предоставленные образцы лент.
Список литературы
Goyal A., Arafat M.M. // Encyclopedia of Materials: Technical Ceramics and Glasses Superconducting YBCO Conductors: The RABiTS Approach, 2021. V. 3. P. 174. https://doi.org/10.1016/B978-0-12-803581-8.11565-6
Ichinose A., Horii S., Doi T. // Jpn. J. Appl. Phys. 2017. V. 56. P. 103101. https://doi.org/10.7567/JJAP.56.103101
Aytug T., Paranthaman M., Thompson J.R. // Appl. Phys. Lett. 2003. V. 83. P. 3963. https://doi.org/10.1063/1.1626263
Горелик С.С., Добаткин С.В., Капуткина Л.М. Рекристаллизация металлов и сплавов. М.: МИСиС, 2015. 261 с.
Эванс Ю.Р. Коррозия и окисление металлов. М.: Изд-во машиностроительной лит., 1962. 857 с.
Портной В.К., Новиков А.И., Головин И.С. Дефекты кристаллического строения металлов и методы их анализа. М.: МИСиС, 2015. 508 с.
Khlebnikova Y.V., Gervasyeva I.V., Suaridze T.R. et al. // Tech. Phys. 2015. V. 85. № 3. P. 389. https://doi.org/10.1134/S106378421503
Prokoshkina D.S., Rodin A.O., Esin V.A. // Phys. Metals Metallography. 2012. V. 113. № 6. P. 583. https://doi.org/10.1134/S0031918X12030106
Gao H., Ji B., Jäger I.L. et al. // Proc. Nat. Acad. Sci. 2003. V. 100. № 10. P. 5597. https://doi.org/10.1073/pnas/0631609100
Carlton C.E., Ferreira P.J. // Acta Mater. 2007. V. 55. P. 3749. https://doi.org/10.1016/j.actamat/2007.02.021
Криштал М.М., Ясников И.С., Полунин В.И. и др. Сканирующая электронная микроскопия и рентгеноспектральный микроанализ. М.: Техносфера, 2009. 208 с.
Дополнительные материалы отсутствуют.
Инструменты
Кристаллография