Кристаллография, 2022, T. 67, № 2, стр. 194-200
Исследование кристаллографической текстуры корундовой керамики, полученной методом искрового плазменного спекания
С. В. Житнюк 1, *, П. Н. Медведев 1, О. Ю. Сорокин 1, А. А. Качаев 1
1 Всероссийский научно-исследовательский институт авиационных материалов
Национального исследовательского центра “Курчатовский институт”,
Государственный научный центр Российской Федерации
Москва, Россия
* E-mail: svzsv@viam.ru
Поступила в редакцию 01.04.2021
После доработки 13.04.2021
Принята к публикации 15.04.2021
- EDN: SELZHM
- DOI: 10.31857/S002347612202031X
Аннотация
Проведены комплексные исследования кристаллографической текстуры корундовой керамики, полученной методом искрового плазменного спекания (ИПС). Установлено формирование характерного типа текстурного состояния вдоль направления приложения сжимающей нагрузки. Показано, что одним из возможных механизмов формирования данного типа текстуры является дислокационное скольжение в базисных плоскостях кристаллографической решетки корунда в ходе пластической деформации. Установлено, что микротвердость керамики, полученной методом ИПС, в параллельном направлении относительно оси приложения сжимающей нагрузки составила 16.2 ± ± 0.8 ГПа, в то время как в перпендикулярном направлении – 14.9 ± 0.8 ГПа.
ВВЕДЕНИЕ
Технологии получения корундовой керамики изучены достаточно хорошо, а совокупность ее свойств (механические, диэлектрические, коррозионная и трибологическая стойкость, биологическая совместимость и др.) позволяет получать изделия, применяемые во многих областях промышленности, электроники, здравоохранения и энергетики. На протяжении нескольких десятков лет керамика на основе оксида алюминия занимает одну треть мирового рынка продаж технической керамики [1–12].
Значительный вклад в развитие технологии получения корундовой керамики и изучения ее свойств внесли В.Л. Балкевич, П.П. Будников, А.С. Власов, Е.С. Лукин, А.В. Беляков, однако исследования в этой области продолжаются. В частности, многие усилия сосредоточены на контролировании плотности, размера зерна и его формы, а также кристаллографической текстуры получаемых материалов с целью регулирования свойств и определения механизмов их формирования [13–18].
Существуют различные методы синтеза, позволяющие получить керамику с необходимой микроструктурой. Среди них следует выделить метод искрового плазменного спекания (ИПС; SPS от англ. Spark Plasma Sintering) – процесс спекания с приложением давления и импульсного тока высокой частоты, при котором консолидация материала осуществляется при более низких температурах и значительно в более короткие временные интервалы по сравнению с традиционными методами [19]. Однако процессы, протекающие во время ИПС, способствуют формированию аксиальной кристаллографической текстуры в направлении приложения нагрузки. Такое явление приводит к анизотропии упругих, тепло- и электрофизических свойств получаемых изделий [20–22].
Намеренное формирование кристаллографической текстуры широко используется для улучшения характеристик анизотропных поликристаллических материалов, особенно когда использование монокристаллов нецелесообразно или невозможно. Применение монокристаллов ограничено в большинстве приложений, так как им не хватает механической целостности поликристаллической керамики, они зачастую дороги и длительны в производстве. Напротив, поликристаллическая керамика механически прочна, широко применяется в качестве основы различных композиционных материалов, а функциональные свойства легче регулируются путем использования ряда легирующих добавок [23].
Для корундовой керамики, синтезированной методом ИПС, характерна текстура с преимущественной ориентацией базисной кристаллографической оси вдоль направления сжатия. Известны различные механизмы, способствующие формированию такого текстурного состояния. Среди них следует выделить межзеренное скольжение, рекристаллизацию, двойникование, а также дислокационное скольжение [24].
Определение механизмов формирования преимущественной ориентации зерен в поликристаллических материалах необходимо для разработки усовершенствованной керамики с регулируемыми свойствами, которая может быть использована в качестве элементов брони для защиты личного состава и военной техники. Для количественной оценки текстурного состояния материалов разработано несколько методов, наиболее эффективными из которых являются методы дифракции. Таким образом, цель данной работы – исследование кристаллографической текстуры корундовой керамики, полученной методом ИПС, с применением комбинации методов дифракции рентгеновских лучей и дифракции обратноотраженных электронов (EBSD).
МАТЕРИАЛЫ И МЕТОДЫ
В работе использовали порошок оксида алюминия чистотой 99.9%, а также монокристалл лейкосапфира, из которого вырезали образец размером 20 × 20 × 8.5 мм3. Образцы корундовой керамики синтезировали двумя методами: свободного спекания без приложения давления (НТ) и ИПС в вакууме. В обоих случаях спекающие добавки не применялись. Известно, что для получения керамики на основе оксида алюминия с плотностью, близкой к теоретической, методом НТ требуются температуры выше 1800°C [16]. В случае применения ИПС такая температура составляет ~1400°C [19]. Поэтому в работе использовали температуру обжига 1600°C, принятую как среднее значение для получения образцов керамики с плотностью, достаточной для проведения исследований методами EBSD.
Для свободного спекания экспериментальные образцы на основе порошка оксида алюминия формовали в цилиндрической пресс-форме диаметром 30 мм методом двустороннего одноосного сухого прессования под давлением 250 МПа. Обжиг проводили при температуре 1600°C. Подъем температуры до максимальной проводили со скоростью 5°C/мин, выдержка при максимальной температуре составила 2 ч. Также прессование порошка осуществляли на установке ИПС (модель FCT H-HPD 25-SD) в режиме гибридного нагрева (SPS + индукционный нагрев) в графитовой пресс-форме. Консолидацию порошка проводили при температуре 1600°C в вакууме, скорость нагрева составляла 100 град/мин, давление прессования 50 МПа, время выдержки 3 мин.
Определение критического напряжения сдвига базисной плоскости скольжения в монокристалле лейкосапфира осуществляли на установке ИПС (модель FCT H-HPD 25-SD) в режиме SPS + + индукционный нагрев в графитовой прессформе. Подъем температуры проводили со скоростью 100 град/мин до 850°C, затем – 50 град/мин до 1600°C. Начальная нагрузка на образец в процессе нагрева составила 20 МПа. При 1600°C нагрузку на образец увеличивали со скоростью 3 МПа/мин. После фиксирования начала пластической деформации нагружение образца продолжали до усадки по высоте Δh = 2 мм.
Кажущуюся плотность и открытую пористость образцов керамики на основе оксида алюминия определяли по ГОСТ 2409-2014 методом гидростатического взвешивания на электронных весах AND GR-200 с применением дистиллированной воды в качестве насыщающей жидкости. Значения открытой пористости (Потк) и кажущейся плотности (ρкаж) вычисляли как среднее значение по трем образцам по следующим формулам:
(1)
${{\rho }_{{{\text{каж}}}}} = {{m}_{{\text{0}}}}{{\rho }_{{\text{ж}}}}{\text{/}}({{m}_{1}}--{{m}_{2}}),$Образец корундовой керамики, полученной методом ИПС, разрезали в направлении, располагающемся параллельно оси прессования. С целью выжигания углерода, проникшего в поверхность оксидного материала в процессе спекания, образец прокаливали в печи при температуре 1200°C с выдержкой 1 ч. Для получения картин дифракции обратноотраженных электронов высокого качества поверхность образца, располагающуюся параллельно оси прессования, подготовили методом механического полирования с применением алмазных суспензий. Далее на полированную поверхность наносили токопроводящий слой золота толщиной 3 нм на установке для нанесения покрытий Leica EM ACE200. Образец устанавливали в держатель с углом наклона 70° от горизонтали растрового электронного микроскопа FEI Verios 460 XHR, оснащенного детектором EBSD HKL Nordlys Nano производителя Oxford Instruments. Ускоряющее напряжение составило 20 кВ. Автоматическое сканирование EBSD выполнялось с шагом 0.5 мкм. Фазовый состав образца идентифицировали как α-Al2О3 (R3m, база данных ICSD № 85137). Полученные картины дифракции обратноотраженных электронов идентифицированы и обработаны в автоматическом режиме с помощью программного обеспечения Aztec (версия 2.4) и HKL Channel 5 (версия 5.12). Из полученного набора данных рассчитано распределение ориентации кристаллитов с использованием дискретных входных параметров биннинга 10° и сглаживания по Гауссу 20°, что позволило рассчитать прямые и обратные полюсные фигуры. Кристаллографическая ориентация на карте представлена с применением цветокодировки в соответствии с цветами в стандартном стереографическом треугольнике: красный – [0001], зеленый – [$01\bar {1}0$], синий – [$10\bar {1}0$].
Рентгенофазовый анализ (РФА) для поликристаллических образцов выполнен с применением дифрактометра Empyrean методом рентгеновской дифракции в монохроматическом CuKα-излучении (λ = 1.5440 Å) в диапазоне 2θ = 10°–145° с шагом Δ2θ = 0.008o и выдержкой 40 с. Расшифровка дифрактограмм проведена с применением специализированной программы HighScore+ и базы данных ICDD PDF-2 (2014). По интенсивности пиков рентгеновского спектра рассчитана обратная полюсная фигура.
Съемку полюсных фигур для монокристаллических образцов проводили с поверхности образцов, располагающейся перпендикулярно оси нагружения, при фиксированном положении рентгеновской трубки и счетчика (2θ = 90° и 117°) в наборах рефлексов ($20\bar {2}10$), ($00012$), ($13\bar {4}4$) и ($23\bar {5}5$), ($10\bar {1}14$), ($14\bar {5}0$) соответственно. Поворот и наклон образца осуществляли с помощью специализированной текстурной приставки. Расшифровка проведена с помощью теоретических стереографических проекций, рассчитанных в программном обеспечении MTEX.
Определение микротвердости проводили на микротвердомере DuraScan 80 при нагрузке 1000 г и времени нагружения 10 с в соответствии с ГОСТ 9450–76 [26]. Измерения проводили на полированных поверхностях образцов керамики, полученной методом ИПС, в перпендикулярном и параллельном направлениях относительно оси приложения сжимающей нагрузки. Значения микротвердости вычисляли как среднее по десяти измерениям.
РЕЗУЛЬТАТЫ И ИХ ОБСУЖДЕНИЕ
Морфология исходного порошка оксида алюминия представлена частицами преимущественно неправильной формы, размер которых не превышает 1 мкм (рис. 1а). Локально наблюдаются как плотные, так и рыхлые агрегаты частиц размером не более 5 мкм. Согласно РФА основной фазой является θ-Al2O3, второй фазой – α-Al2O3 (рис. 1б).
Рис. 1.
Результаты исследования порошка оксида алюминия, используемого в работе: а – морфология исходного порошка; б – результаты РФА исходного порошка.
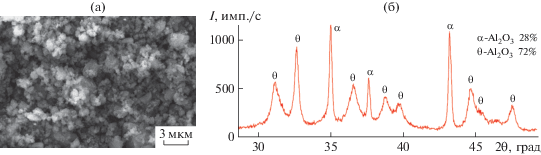
В табл. 1 представлены результаты определения относительной плотности и открытой пористости образцов корундовой керамики, полученной методами HT и ИПС в вакууме при температуре обжига 1600°C.
Таблица 1.
Свойства экспериментальных образцов керамики на основе оксида алюминия, полученных методами спекания HT и ИПС в вакууме при температуре синтеза 1600°C
Метод спекания | Теоретическая плотность ρт, г/см3 |
Относительная плотность ρотн, % |
Открытая пористость Потк, % |
---|---|---|---|
HT | 4.00 | 74.3 | 21.7 |
ИПС | 4.00 | 98.0 | 0.3 |
Значение относительной плотности 74.3% для образцов, полученных методом свободного спекания, свидетельствует о том, что температура 1600°C недостаточна для получения плотноспекшейся корундовой керамики без применения спекающих добавок. Такой результат является прямым следствием установленных ранее закономерностей процессов диффузии, протекающих в керамических материалах на основе оксида алюминия при высоких температурах [27–29]. Также отметим, что сухое формование пресс-порошков с размером частиц менее 1 мкм имеет ряд недостатков, связанных с большой удельной поверхностью, и зачастую приводит к снижению плотности спеченных образцов [30].
На рис. 2 представлены результаты определения кристаллографической текстуры образцов керамики, полученной различными методами. Для керамики, синтезированной методом свободного спекания, характерно состояние, близкое к бестекстурному с полюсной плотностью Pmax = 1.1. В то время как образцам, полученным методом ИПС, свойственна аксиальная текстура с полюсной плотностью Pmax = 5 в направлении, соответствующем оси приложения нагрузки в процессе консолидации исходного порошка.
Рис. 2.
Обратные полюсные фигуры образцов корундовой керамики, полученной методами спекания HT (а) и ИПС (б).
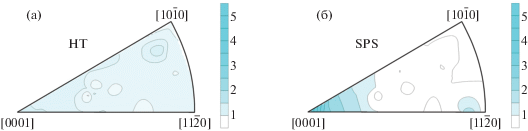
Карта, полученная с помощью EBSD, демонстрирует кристаллографическую ориентацию каждого зерна в плоскости, перпендикулярной оси приложения нагрузки в процессе ИПС (рис. 3). Цветовая кодировка соответствует приведенному там же стереографическому треугольнику. Значительная доля зерен красного цвета (рис. 3) и обратные полюсные фигуры (рис. 4) указывают на преимущественную ориентацию базисных кристаллографических плоскостей (0001) перпендикулярно оси прессования.
Рис. 3.
Карта кристаллографической ориентации зерен в плоскости, перпендикулярной оси приложения нагрузки в процессе ИПС.
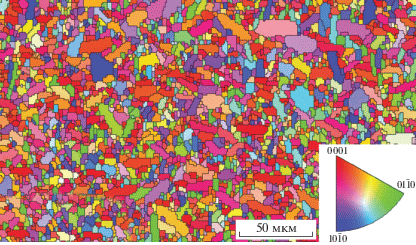
Рис. 4.
Полюсные фигуры, рассчитанные на основе распределения кристаллографических ориентаций: а – плоскость, перпендикулярная оси прессования; б – плоскость, параллельная оси прессования.
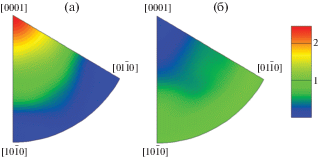
Отметим, что завышенная для корундовой керамики температура ИПС способствует локальному укрупнению зерен и удлинению их формы. Такой эффект является широко распространенным для корундовой керамики, обжиг которой осуществляется без применения спекающих добавок. Для установления причин анизотропного роста на рис. 3 выбрали несколько удлиненных зерен и определили положение их кристаллографических плоскостей с помощью углов Эйлера. Из рис. 5 следует, что удлинение зерен происходит в направлении призматических плоскостей, в то время как рост базисных плоскостей проходит значительно медленнее вне зависимости от ориентации таких зерен относительно внешней нагрузки. Согласно данным [31] призматические плоскости обладают большей кривизной поверхности и, как следствие, бóльшим значением свободной энергии, чем базисные. Таким образом, анизотропный рост зерна обусловлен разницей в подвижности границ зерна в разных кристаллографических направлениях.
Рис 5.
Кристаллографическая ориентация анизотропных зерен в плоскости, перпендикулярной оси приложения нагрузки в процессе ИПС.
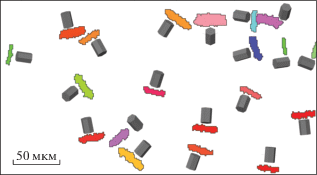
Следовательно, результаты, полученные двумя различными методами анализа, свидетельствуют о формировании аксиальной текстуры с осью 〈0001〉, ориентированной в направлении оси приложения внешней сжимающей нагрузки.
Ранее отмечено, что в некоторых литературных источниках сообщается о нескольких механизмах, способствующих формированию характерного типа текстурного состояния в корундовой керамике. Вероятно, в процессе приложения внешней сжимающей нагрузки действует совокупность таких механизмов, среди которых некий вклад вносит дислокационное скольжение кристаллографических плоскостей отдельных зерен вдоль определенных направлений. Установлено, что в кристаллической решетке корунда существует ряд независимых систем скольжения, активируемых при высоких температурах: ($0001$)〈$1\bar {2}10$〉 (базисная); {$1\bar {1}00$}〈$11\bar {2}0$〉 (призматическая); {$10\bar {1}1$}〈$12\bar {1}0$〉, {$10\bar {1}1$}〈$2\bar {1}\bar {1}\bar {3}$〉, {$2\bar {1}\bar {1}2$}〈${\text{\;}}\bar {2}113$〉 (пирамидальные). Плоскостью, требующей наименьшей температуры и энергии активации, является базисная [12, 32]. В [19] сообщается о теоретически возможном формировании текстуры в направлении (0001) в результате активации базисной плоскости скольжения.
Для создания методического подхода к исследованию процессов пластической деформации в поликристаллическом материале в настоящей работе провели деформирование монокристалла лейкосапфира при температуре 1600°C.
Известно, что пластическая деформация характеризуется критическим напряжением сдвига τс:
где σс – критическое напряжение начала пластической деформации, МПа; ψ – угол между направлением скольжения и направлением деформации; φ – угол между нормалью к плоскости скольжения и направлением деформации [32].При равенстве углов ψ и φ произведение их косинусов (известное как фактор Шмида) имеет максимальное значение, равное 0.5. В таком случае внешние напряжения, необходимые для активации плоскости скольжения, ориентированной подобным образом, будут минимальны.
Для активации базисной плоскости скольжения использовали монокристалл лейкосапфира, базисное направление которого располагалось под углом 50° к оси приложения сжимающей нагрузки. Значение фактора Шмида для системы скольжения ($0001$)〈$1\bar {2}10$〉 составило 0.48. На рис. 6 представлена прямая полюсная фигура монокристалла в исходном состоянии. В ходе приложения одноосной сжимающей нагрузки (направление приложения нагрузки соответствует оси Z на рис. 6 и 7) при температуре 1600°C зафиксировали начало пластической деформации при давлении 41.5 МПа, что соответствует значению критического напряжения сдвига τс = 19.9 МПа. Прямая полюсная фигура после испытаний демонстрирует плавный разворот базисных плоскостей на 15° в направлении оси приложения сжимающей нагрузки (рис. 7). Данные изменения указывают на дислокационное скольжение по системе ($0001$)〈$1\bar {2}10$〉.
Рис. 6.
Рефлексы от кристаллографических плоскостей монокристалла лейкосапфира в исходном состоянии, расположенные на стереографической проекции. Пунктирными линиями обозначены группы рефлексов, объединяющие семейства плоскостей, равноудаленные от базисного направления. Звездочкой обозначена базисная плоскость.
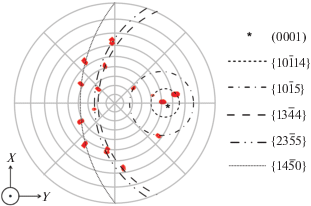
Рис. 7.
Разворот кристаллографических плоскостей в ходе деформации монокристалла лейкосапфира; 1, 2 – рефлексы от кристаллографических плоскостей в исходном и деформированном состоянии соответственно. Стрелками обозначено направление разворота.
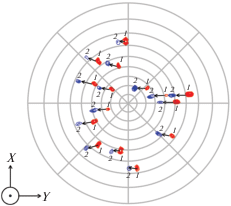
Безусловно, процессы пластической деформации, протекающие в поликристаллическом материале, сложнее и, по всей видимости, носят комплексный характер. Однако согласно полученным результатам дислокационное скольжение базисных плоскостей кристаллографической решетки является одним из возможных механизмов формирования характерного текстурного состояния в корундовой керамике. Поскольку в ходе ИПС формируется текстура в направлении 〈0001〉, параллельном направлению сжатия, основной активируемой является система скольжения ($0001$)〈$1\bar {2}10$〉. Таким образом, происходит разворот плоскостей $(0001)$ в положение, перпендикулярное оси приложения сжимающей нагрузки, чтобы приспособиться к значительной осевой деформации в условиях высоких температур. В то же время нельзя исключать, что наличие процессов межзеренного скольжения, приводящих к смещению и взаимной подстройке зерен, и избирательного роста зерен с благоприятной ориентацией относительно приложенной нагрузки также способствуют формированию текстурного состояния.
Ранее отмечено, что формирование кристаллографической текстуры приводит к анизотропии свойств. Так, определение микротвердости образцов керамики, полученной методом ИПС, показало, что в параллельном направлении относительно оси приложения сжимающей нагрузки значение микротвердости составило 16.2 ± 0.8 ГПа, в то время как в перпендикулярном направлении – 14.9 ± 0.8 ГПа. Анизотропия физико-механических характеристик способствует повышению работоспособности изделий, функциональная нагрузка на которые прикладывается в определенном направлении. Примером таких изделий может стать броневая керамика. Таким образом, исследование влияния кристаллографической текстуры на свойства керамических материалов является перспективным и требует дальнейшего развития.
ВЫВОДЫ
Проведены комплексные исследования кристаллографической текстуры корундовой керамики, полученной методом ИПС. Методами дифракции рентгеновских лучей и дифракции обратноотраженных электронов установлено формирование характерного типа текстурного состояния вдоль направления приложения сжимающей нагрузки. Показано, что одним из возможных механизмов формирования данного типа текстуры является дислокационное скольжение базисных плоскостей кристаллографической решетки корунда в ходе пластической деформации. Установлено, что микротвердость керамики, полученной методом ИПС, в параллельном направлении относительно оси приложения сжимающей нагрузки составила 16.2 ± 0.8 ГПа, в то время как в перпендикулярном направлении – 14.9 ± ± 0.8 ГПа.
Авторы выражают благодарность начальнику сектора лаборатории № 17 ФГУП ВИАМ Е.В. Филоновой за помощь в проведении исследований, а также профессору кафедры химической технологии керамики и огнеупоров РХТУ им. Д.И. Менделеева А.В. Белякову за обсуждение результатов и ценные замечания.
Список литературы
Каблов Е.Н., Фоломейкин Ю.И., Столярова В.Л., Лопатин С.И. // Журн. общ. химии. 2016. Т. 86. № 9. С. 1542.
Каблов Е.Н. // Тез. докл. ХХ Менделеевского съезда по общей и прикладной химии. УрО РАН. 2016. С. 25.
Каблов Е.Н., Жестков Б.Е., Гращенков Д.В. и др. // Теплофизика высоких температур. 2017. Т. 55. № 6. С. 704.
Журавлева П.Л., Щур П.А., Мельников А.А. // Труды ВИАМ: электрон. науч.-технич. журн. 2019. № 6. Ст. 11. http://www.viam-works.ru https://doi.org/10.18577/2307-6046-2019-0-6-104-113
Гриневич А.В., Лавров А.В. // Труды ВИАМ: электрон. науч.-технич. журн. 2018. № 3. Ст. 11. http://www.viam-works.ru https://doi.org/10.18577/2307-6046-2018-0-3-95-102
Рассохина Л.И., Битюцкая О.Н., Гамазина М.В., Кочетков А.С. // Труды ВИАМ: электрон. науч.-технич. журн. 2020. № 2. Ст. 04. http://www.viam-works.ru https://doi.org/10.18577/2307-6046-2020-0-2-31-40
Лебедева Ю.Е., Щеголева Н.Е., Чайникова А.С. и др. // Труды ВИАМ: электрон. науч.-технич. журн. 2020. № 3. Ст. 06. http://www.viam-works.ru https://doi.org/10.18577/2307-6046-2020-0-3-58-65
Балкевич В.Л. Техническая керамика. М.: Стройиздат, 1984. 256 с.
Heimann R.B. Classic and Advanced Ceramics: From Fundamentals to Applications. Weinheim: WILEY-VCH Verlag GmbH & Co. KGaA, 2010. 553 p.
Шевченко В.Я. Введение в техническую керамику. М.: Наука, 1993. 112 с.
Мэттьюз Ф., Ролингс Р. Композиционные материалы. Механика и технология. М.: Техносфера, 2004. 408 с.
Carter C.B., Norton M.G. Ceramic Materials: Science and Engineering. Springer Science. 2013. 776 p.
Бакунов В.С., Балкевич В.Л., Власов А.С. и др. Керамика из высокоогнеупорных окислов / под ред. Полубояринова Д.Н., Попильского Р.Я. М.: Металлургия, 1977. 304 с.
Балкевич В.Л., Будников П.П., Булавин И.А. и др. Химическая технология керамики и огнеупоров / под общ. ред. Будникова П.П., Полубояринова Д.Н. М.: Стройиздат, 1972. 552 с.
Лукин Е.С., Макаров Н.А., Козлов А.И. и др. // Конструкции из композиционных материалов. 2007. № 1. С. 3.
Макаров Н.А. Высокопрочная керамика с пониженной температурой спекания на основе оксида алюминия: автореф. дис. … канд. техн. наук. Российский химико-технологический университет им. Д.И. Менделеева; 05.17.11. М., 2000. 16 с.
Абызов А.М. // Стекло и керамика. 2018. № 8. С. 8.
Абызов А.М. // Стекло и керамика. 2018. № 9. С. 23.
Pravarthana D., Chateigner D., Lutterotti L. et al. // J. Appl. Phys. A. 113. 2013.
Noudem J.G., Kenfaui D., Chateigner D., Gomina M. // J. Electron. Mater. 2011. V. 40. № 5. P. 1100.
Bomshtein N., Spiridonov G., Dashevsky Z., Gelbstien Y. // J. Electron. Mater. 2012. V. 41. P. 1546.
Euvananont C., Jantaping N., Thanachayanont C. // Curr. Appl. Phys. 2011. № 11. P. S246.
Messing G.L., Poterala S., Chang Y. et al. // J. Mater. Res. V. 32. 2017. P. 3219.
Guilmeau E., Henrist C., Suzuki T.S. et al. // Mater. Sci. Forum. V. 495–497. 2005. P. 1395.
Огнеупоры. Метод определения кажущейся плотности, открытой и общей пористости, водопоглощения: ГОСТ 2409–2014. Издание официальное. М.: Стандартинформ. 2014. 7 с.
Измерение микротвердости вдавливанием алмазных наконечников. ГОСТ 9450–76. Издание официальное. М.: Издательство стандартов. 1993. 35 с.
Лукин Е.С. // Огнеупоры и техническая керамика. 1996. № 4. С. 2.
Макаров Н.А. // Стекло и керамика. 2003. № 10. С. 31.
Лукин Е.С., Аяди М.Б., Попова Н.А. и др. // Огнеупоры и техническая керамика. 1996. № 10. С. 2.
Беляков А.В. // Новые огнеупоры. 2020. № 1. С. 39.
Horn D.S., Messing G.L. // Mater. Sci. Eng. A. 1995. V. 195. P. 169.
Добровинская Е.Р., Литвинов Л.А., Пищик В.В. Энциклопедия сапфира. Харьков: Институт монокристаллов, 2003. 508 с.
Дополнительные материалы отсутствуют.
Инструменты
Кристаллография