Известия РАН. Механика твердого тела, 2022, № 3, стр. 32-39
ВЛИЯНИЕ ТЕМПЕРАТУРЫ И НАГРУЗКИ НА КОЭФФИЦИЕНТ ТРЕНИЯ МЕЖДУ УГЛЕРОДНЫМИ ВОЛОКНАМИ
А. В. Морозов a, *, П. О. Буковский a, А. К. Голубков b
a Институт проблем механики им. А.Ю. Ишлинского РАН
Москва, Россия
b ОАО Авиационная корпорация “Рубин”
Балашиха, Россия
* E-mail: morozovalexei@mail.ru
Поступила в редакцию 15.05.2021
После доработки 17.05.2021
Принята к публикации 24.05.2021
- EDN: QLANQI
- DOI: 10.31857/S0572329922020076
Аннотация
В работе на микротрибометре по схеме контакта “перекрещивающиеся цилиндры” было проведено исследование: влияние температуры в диапазоне от 23 до 300°С и нормальной нагрузки в интервале от 0.2 до 1 Н на коэффициент трения скольжения между углеродными волокнами. Углеродные волокна синтезированы разными способами из полиакрилонитрильного полимера и отличались температурой финишной обработки, а именно: 1400°С и 2800°С. Поверхность волокна до и после трибологических испытаний изучалась при помощи СЭМ- и АСМ- микроскопов. Проведенные трибологические эксперименты показали, что коэффициент трения зависит от природы и технологии изготовления углеродного волокна, а также его термической обработки, которая влияет как на адгезионные свойства, так и на шероховатость поверхности волокна. Уменьшение микрорельефа поверхности исходного волокна с одновременным увеличением его адгезионных свойств является одним из путей повышения коэффициента трения между волокнами и, как следствие, способствует повышению уровня трения для углерод-углеродных фрикционных композитов.
1. Введение. Исследования, направленные на повышение эксплуатационных характеристик современных углерод-углеродных композитных материалов (УУКМ), широко используемых в авиационных тормозных системах, ведутся в настоящее время многими научными группами [1–3]. Одно из приоритетных направлений – улучшение физико-механических и адгезионных свойств углеродных волокон, которые используются при армировании матрицы композита.
Известно [4–7], что с целью повышения жесткости и прочности УУКМ ведутся интенсивные работы по созданию высокомодульных и высокопрочных волокон. При этом наиболее широко распространенным методом оценки прочностных свойств является испытание на растяжение [8], в котором используется одновременно большое количество волокон, объединенных в жгут. Волокна в жгуте невозможно равномерно нагрузить в процессе эксперимента, поэтому появляются работы по исследованию прочностных свойств углеродных волокон, объединенных в жгуты. Например, в работе [9] авторами демонстрируется новый способ закрепления жгута из углеродных волокон в захватах разрывной установки. А в [10] авторы провели исследование по растяжению углеродных волокон, результаты которого показали – прочность волокна зависит от концентрации поверхностных дефектов. Следует отметить, что одним из направлений современного производства углеродных волокон является модификация их поверхности [11, 12], которая приводит как к повышению их прочностных свойств, так и к улучшению адгезии волокна к матрице композита, что в совокупности позволяет улучшить прочностные свойства УУКМ.
Широко применяется барьерный разряд в процессе модификации углеродных волокон. В [13] было исследовано влияние обработки плазмой и азотной кислоты на механические свойства углеродных волокон. В работе отмечается: обработка волокна привела к увеличению его прочности. Применение высокочастотного разряда [14] в процессе обработки кислородной и аммиачной плазмой углеродного волокна привело к положительному эффекту в развитии его поверхности, что позволило улучшить сцепление между углеродным волокном и матрицей композита. В [15] показано, что механические свойства углеродных волокон улучшаются после их плазменной обработки в воздушной и инертной среде. Наблюдается рост предела прочности композита, что объясняется улучшением адгезионных взаимодействий между углеродным волокном и матрицей. Авторами научного исследования [16] продемонстрированы результаты влияния плазменной обработки углеродного волокна на трибологические свойства изготавливаемых тканных композитов. В работе было установлено, что на поверхности волокон, обработанных плазмой, образуются карбонильные функциональные группы, способствующие уменьшению коэффициента трения и скорости износа в сравнении с необработанными волокнами. Проведенные исследования в [13–16] показывают, что модифицирование волокна приводит к улучшению физико-механических характеристик УУКМ.
При исследовании коэффициента трения различных УУКМ на основе каменноугольного пека, который дискретно армировался отличающимися углеродными волокнами, авторами данной работы было показано [17], что на дорожке трения образуется тонкий модифицированный слой, который влияет на коэффициент трения. При помощи Раман спектроскопии было определено, что образовавшийся модифицированный слой преимущественно состоит из углеродных волокон, которые равномерно распределены по поверхности трения.
Целью данной работы является проведение сравнительного исследования влияния температуры и нормальной нагрузки на коэффициент трения между жгутами углеродных волокон с различными технологиями получения и физико-механическими свойствами.
2. Исследуемые материалы. Для трибологических экспериментальных исследований были выбраны две группы углеродных волокон, которые отличаются конечной температурой финишной обработки, влияющей на их структуру и физико-механические свойства. Первая группа – карбонизованные волокна были получены при конечной температуре T = 1400°С. Вторая группа – графитированные волокна, которые были получены при финишной термообработке T = 2800°С. Следует отметить, что обе группы волокон испытывались в виде жгутов длиной 7 см. В настоящем исследовании использовались коммерчески доступные углеродные волокна двух производителей, а именно: волокно УК (ООО Аргон, г. Балаково, Россия) и волокно Zoltek Panex 35 (Zoltek Inc., Венгрия). В таблице представлены основные механические свойства исследуемых углеродных волокон.
3. Методика микроскопических исследований. Исследования поверхности углеродных волокон до и после трибологических испытаний были проведены на сканирующем электронном микроскопе (СЭМ) Tescan Vega 3 SBH. Для закрепления жгутов на алюминиевом предметном столике микроскопа использовался углеродный токопроводящий скотч. Поверхность образцов исследовалась при помощи детектора вторичных электронов при ускоряющем напряжении 10 кВ, с диаметром пучка 100 нм. Выбранный режим был подобран для получения наиболее достоверной текстуры поверхности волокна с учетом максимально возможного качественного разрешения при данном ускоряющем напряжении. Получаемые изображения давали взаимодополняющую информацию. При исследовании выбирались типичные области на поверхности исследуемых объектов. Особенностью микроскопических исследований являлось изучение поверхности разрушения, которое было вызвано трением, а также изучение микрорельефа поверхности карбонизованных и графитированных углеродных волокон.
Для изучения шероховатости поверхности волокна использовался атомно-силовой микроскоп AIST-NT (Россия). Область исследования поверхности единичного волокна составляла 2 на 2 мкм, а скорость сканирования составляла 1 мкм/с.
4. Методика эксперимента. Исследование влияния температуры и нагрузки на коэффициент трения между волокнами было осуществлено при помощи лабораторного микротрибометра по схеме контакта “перекрещивающиеся цилиндры” (рис. 1). Трибометр оснащен термокамерой, позволяющей проводить испытания в диапазоне температур от 23 до 300°С. Испытание по определению коэффициента трения проводили при постоянной нагрузке, которая варьировалась в интервале от 0.2 до 1 Н. Следует отметить, что столь малые нагрузки были выбраны из соображений осуществимости эксперимента, так как повышение нагрузки приводит к быстрому разрушению одного из жгутов, состоящих из испытываемых графитированных волокон. Жгут 1 в натянутом состоянии закреплялся в неподвижный держатель 4, который через жесткий шток крепился к 2-компонентному датчику сил 6, к которому посредством винтовой передачи (не показан на рис. 1) передавалась нормальная нагрузка. Жгут с волокнами 2 закреплялся в держатель 3, который совершал возвратно-поступательное движение за счет кривошипно-шатунного механизма, вращательное движение к которому передавалось от шагового электродвигателя (не показан на рис. 1). Держатели жгутов 3 и 4 помещались в термокамеру 5. Термокамера закрывалась крышкой и осуществлялся нагрев жгутов волокон до заданной оператором температуры с последующей выдержкой в течение 60 ± 5 минут. Частота возвратно-поступательного движения жгута 3 была постоянно равной 1 Гц, а амплитуда его перемещения составляла 6 мм. Время испытания при каждом уровне нагрузки было выбрано равным 5 мин.
Рис. 1.
Принципиальная схема трибометра, где 1, 2 – пучки волокон, закрепленные в своих держателях (3, 4); 5 – термокамера; 6 – 2-компонентный датчик сил.
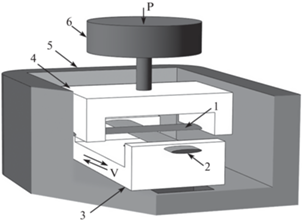
Показателями процесса фрикционного взаимодействия в измерительной системе прибора является непрерывная запись нормальной силы, силы и пути трения. Для получения достоверных результатов в работе использовалось трехкратное повторение опытов, на основе которых по методу среднеквадратичного отклонения вычислялись средние значения коэффициентов трения.
5. Результаты и их обсуждение. На рис. 2, представлены СЭМ- и АСМ- изображения поверхности карбонизованных и графитированных углеродных волокон до и после трибологических испытаний, которые были проведены при нормальной нагрузке P = 1 Н, температуре T = 300°C и пути трения S = 7.2 м.
Рис. 2.
Типичные СЭМ- и АСМ- микрофотографии углеродных волокон до (a–d) и после (e–h) трения, где (a, e) – карбонизованные и (c, g) – графитированные волокна УК; (b, f) – карбонизованные и (d, h) – графитированные волокна Zoltek.
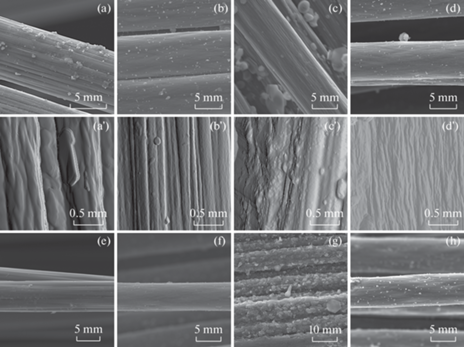
Анализ полученных изображений позволяет сделать следующие выводы. Рельеф поверхности карбонизованных волокон до (рис. 2, a, b) и после (рис. 2, e, f) трения не изменяется и имеет фибриллярную структуру, ориентированную в направлении продольной оси волокна. Шероховатость поверхности волокна Zoltek (рис. 2, b') значительно меньше, чем шероховатость волокна УК (рис. 2, a'). Такая структура и различия шероховатости связаны с технологией изготовления волокна [12, 18–20], при этом фибриллы распределяются в волокне случайным образом, поэтому поверхность волокна также имеет случайную шероховатость [21]. Заметим, что исследуемые поверхности карбонизованных волокон в основном не содержат дефектов, а сами волокна имеет правильное круглое поперечное сечение. На поверхности волокон сохраняются частицы аппрета, который не детектируется в зоне трения (рис. 2, e, f).
Исследования микрорельефа поверхности термообработанного при 2800°С волокна позволяют заключить – шероховатость поверхности после температурной обработки становится сглаженной (рис. 2, c, d) в сравнении с исходной поверхностью (рис. 2, a, b). Следует отметить, что высотные параметры шероховатости поверхности УК-волокон перед термообработкой составляют Ra = 10.6 нм, Rz = 59.5 нм, а после Ra = 6.2 нм, Rz = 27.6 нм, то есть микрорельеф поверхности после термообработки уменьшается в 1.7 раза. При этом параметры шероховатости для Zoltek карбонизованного волокна составляют Ra = 9.7 нм, Rz = 54.1 нм, графитированного Ra = 8.9 нм, Rz = 42.1 нм, то есть микрорельеф поверхности снижается не так значительно, как для УК-волокна. На поверхности графитированных волокон так же, как и на карбонизованном волокне присутствуют частицы аппрета.
При трении термообработанного УК-волокна наблюдается быстрое его разрушение (рис. 2, g), что объясняется низкой прочностью волокна (см. таблицу) в отличие от Zoltek волокна (рис. 2, h), поверхность которого сохраняется. В работе [20] отмечается, что после термообработки появляются существенные изменения и даже дефекты во внутренней структуре Zoltek и УК-волокна. При этом невысокая прочность графитированного УК-волокна связана не только с природой волокна, но и с технологией его получения: при производстве УК-волокна в качестве растворителя используется водный раствор роданида натрия, а при изготовлении Zoltek применяется демитилформамид. Также приведенный в работе рентгенографический анализ показал, что степень графитации УК-волокна при температурной обработке 2800°С выше, чем у Zoltek-волокна. Дополнительно отмечается, что при высокой температуре обработки Zoltek-волокно сохраняет свою форму поперечного сечения, которая близка к форме исходного волокна (наблюдается перерождение фибриллярной структуры в слоистую, с хаотичным расположением слоев внутри волокна), тогда как для УК-волокна наблюдалось изменение формы от круглой к неправильной (звездообразной), а некоторые волокна имели отверстия в центре. При этом волокна приобретали четко выраженную слоистую структуру, характерную для графита. Таким образом, графитация при температуре равной 2800°C волокна марки УК-приводит к гораздо более существенным изменениям его структуры и морфологии, чем у волокна марки Zoltek, что объясняет снижение прочностных свойств УК-волокна и, как следствие, быстрое его разрушение при трении.
На рис. 3 представлены зависимости коэффициента трения µ от нормальной нагрузки P и двух температур T для всех испытанных углеродных волокон.
Рис. 3.
Зависимость коэффициента трения μ от нагрузки P[H] при двух температурах T = 23 и 300°С (серый фон) для карбонизованных (1) и графитированных (2) волокон марок УК (a) и Zoltek (b).
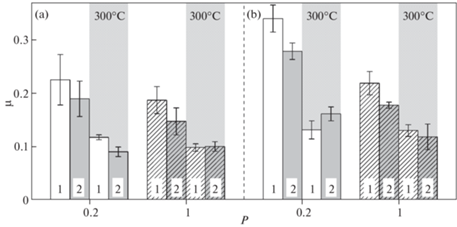
Анализ результатов показывает, что при комнатной температуре T = 23 ± 3°C с увеличением нормальной нагрузки наблюдается снижение коэффициента трения для обоих типов углеродных волокон, при этом очевидно: трение на карбонизованных волокнах выше, чем на обработанных при температуре 2800°С волокнах. Оба эффекта объясняются в ставшей классической работе [22], авторы которой показали – снижение коэффициента с ростом нагрузки вызвано уменьшением влияния адгезионных сил в контакте перекрещивающихся волокон. При этом поверхностная энергия углеродного волокна существенно снижается с увеличением температуры его обработки (авторы рассчитали, что графитированные волокна обладают вдвое меньшей поверхностной энергией, чем карбонизованные). Следует добавить, что согласно приведенным в данной работе измерениям микрорельефа и полученным микрофотографиям (рис. 2) шероховатость поверхности графитированного волокна меньше, чем у карбонизованного волокна, то есть вероятно снижение деформационных потерь, расходуемых при трении на шероховатых волокнах. При этом трение на карбонизованных гладких волокнах марки Zoltek выше, чем на шероховатых волокнах УК. Это вероятно связано с тем фактом, что при предположительно равных адгезионных свойствах поверхностей, трение при малых нагрузках будет выше на той поверхности, чья шероховатость меньше.
Более интересным для практического применения является оценка коэффициента трения при температуре равной 300°С. Анализ полученных данных (рис. 3) показывает, что при повышении температуры наблюдается значительное снижение коэффициента трения для углеродных волокон. Этот механизм можно объяснить снижением капиллярной адгезии. Согласно работам [23, 24] влага, которая содержится в воздухе и адсорбируется на поверхности волокна при его нагреве до 300°С, испаряется наряду с другими возможными поверхностными загрязнениями, то есть нагрев волокна полностью экранирует капиллярное воздействие и, вероятно, дополнительно снижает адгезионное воздействие на силу трения. При этом с увеличением нормальной нагрузки вклад в силу трения адгезии уменьшается. Таким образом, при нормальной нагрузке P = 1 Н и температуре T = 300°С, коэффициент трения карбонизованных и графитированных волокон отличается незначительно и для волокон марки УК μ = 0.1 ± 0.01, а для волокон марки Zoltek μ = 0.13 ± 0.01.
6. Заключение. Проведены исследования фрикционных свойств жгутов, карбонизованных и графитированных углеродных волокон двух производителей (УК от ООО Аргон и Zoltek Panex 35 от Zoltek Inc.) по схеме контакта “перекрещивающиеся цилиндры” с вариацией температур T в диапазоне 23…300°С и нормальных нагрузок P в интервале 0.2 … 1 Н. При помощи СЭМ и АСМ микроскопов проведено исследование микрорельефа поверхностей волокон до и после трибологических испытаний.
По результатам анализа данных, полученных в результате выполненных серий трибологических экспериментов, было установлено: коэффициент трения μ зависит от природы и технологии изготовления волокна, термической обработки, адгезионных свойств, шероховатости поверхности и составляет при T = 300°C и P = 1 Н для карбонизованных и графитированных волокон марки УК μ = 0.1 ± 0.01, для марки Zoltek в случае карбонизованных волокон μ = 0.13 ± 0.01 и для графитированных μ = 0.12 ± 0.02.
Исследование микрорельефа поверхности волокон до и после трибологических испытаний позволило сделать вывод – уменьшением шероховатости поверхности волокна, а также увеличением ее химической активности (адгезионных свойств) возможно повысить фрикционные свойства армируемого композита. В данном исследовании было получено, что шероховатость поверхности карбонизованного волокна Zoltek составляет по Ra = 9.7 нм, что ниже, чем у волока УК (Ra = 10.6 нм). А так как поверхностная энергия карбонизованных волокон выше, чем у графитированных можно ожидать, опираясь на полученные нами ранее данные [17], самый высокий коэффициент трения для фрикционных композитов, армированных карбонизованным волокном марки Zoltek. Следует отметить, что повышение уровня трения может привести к увеличению интенсивности изнашивания композита.
Благодарности. Авторы выражают благодарность В.В. Кулакову (АК “Рубин”) за заинтересованность в результатах данного исследования и предоставление образцов углеродных волокон, которые используются при армировании пековой матрицы современных фрикционных углеродных композитов.
Авторы благодарят Т.И. Муравьеву за измерения шероховатости поверхности волокон, выполненные на АСМ микроскопе.
Работа выполнена при финансовой поддержке гранта РНФ 19-19-00548.
Список литературы
Gadow R., Jimenez M. Carbon fiber-reinforced carbon composites for aircraft brakes // Am. Ceram. Soc. Bull. 2019. V. 98. № 6. P. 28–34.
Wu S., Yi M., Ge Y., Ran L., Peng K. Effect of carbon fiber reinforcement on the tribological performance and behavior of aircraft carbon brake discs // Carbon. 2017. V. 117. P. 279–292. https://doi.org/10.1016/j.carbon.2017.03.003
Rao J.G., Selvam P., Sinnur K.H. Effect of Type of Carbon Matrix on Tribological Properties of C/C Aircraft Brake Discs // Def. Sci. J. 2019. V. 69. № 6. P. 585–590. https://doi.org/10.14429/dsj.69.13688
Тарнопольский Ю.М., Жигун И.Г., Поляков В.А. Пространственно-армированные композиционные материалы: справочник. М.: Машиностроение, 1987. 224 с.
Morgan P. Carbon fibers and their composites. Boca Ration: Taylor & Francis, 2005. 1153 p.
Варшавский В.Я. Углеродные волокна Изд. 2. М.: ВИНИТИ, 2007. 500 с.
Симамура С. Углеродные волокна. М.: Мир, 1987. 304 с.
Лысенко А.А., Гладунова О.И. Мировое производство углеродных волокон // Композитный мир. 2019. Т. 87. № 5. С. 28–31.
Кузякина Д.В., Павлов В.П., Нусратуллин Э.М. Микроструктура композиционного материала на основе углеродных волокон и магниевой матрицы, и экспериментальное изучение прочности углеродных волокон // Молодежный вестник Уфимского государственного авиационного технического университета. 2018. № 2. С. 68–72.
Литвинов В.Б., Кобец Л.П., Токсанбаев М.С., Деев И.С., Бучнев Л.М. Структурно-механические свойства высокопрочных углеродных волокон // Композиты и наноструктуры. 2011. Т. 11. № 3. С. 36–50.
Гарифуллин А.Р., Абдуллин И.Ш. Современное состояние проблемы поверхностной обработки углеродных волокон для последующего их применения в полимерных композитах в качестве армирующего элемента // Вестник Казанского технологического университета. 2014. Т. 17. № 7. С. 85–85.
Нурмухаметова А.Н., Хамидуллин А.Р., Зенитова Л.А. Углеродное волокно. Получение, модификация, свойства, области применения // Бутлеровские сообщения. 2020. Т. 62. № 5. С. 1–42. https://doi.org/10.37952/ROI-jbc-01/20-62-5-1
Nie W.Z., Li J. Effects of plasma and nitric acid treatment of carbon fibers on the mechanical properties of thermoplastic polymer composites // Mech. Compos. Mater. 2010. V. 46. № 3. P. 251–256. https://doi.org/10.1007/s11029-010-9143-0
Chang Tao C. Plasma Surface Treatment In Composites Manufacturing // J. Ind. Technol. 1999. V. 15. № 1. P. 1–7.
Гарифуллин А.Р., Абдуллин И.Ш., Галямова К.Н, Скидченко Е.А. Влияние плазменной обработки на механические свойства пропитанных смолой углеродных волокон при растяжении // Вестник технологического университета. 2015. Т. 18. № 13.С. 144–145.
Rhee K.Y., Park S.J., Hui D., Qiu Y. Effect of oxygen plasma-treated carbon fibers on the tribological behavior of oil-absorbed carbon/epoxy woven composites // Composites B. 2012. V. 43. № 5. P. 2395–2399. https://doi.org/10.1016/j.compositesb.2011.11.046
Буковский П.О., Морозов А.В., Кириченко А.Н. Влияние приработки на коэффициент трения углеродных композитных материалов авиационных тормозов // Трение и износ. 2020. Т. 41. № 4. С. 448–456. https://doi.org/10.32864/0202-4977-2020-41-4-448-456
Ribeiro R.F., Pardini L.C., Alves N.P., Brito C.A.R. Thermal Stabilization study of polyacrylonitrile fiber obtained by extrusion // Polímeros. 2015. V. 25. № 6. P. 523–530. https://doi.org/10.1590/0104-1428.1938
Нащокин А.В., Калугин Д.И., Могильный И.М., Малахо А.П., Авдеев В.В. Окисленные ПАН- волокна как наполнитель для безасбестовых уплотнительных материалов // Успехи современной науки. 2018. № 2. 40–45.
Нащокин А.В., Малахо А.П., Галигузов А.А., Кулаков В.В., Селезнев А.Н., Авдеев В.В. Зависимость механических свойств, морфологии и структурных характеристик различных типов углеродных волокон от температурной обработки // Композиционные волокнистые материалы // Химические волокна. 2012. Т. 44. № 3. С. 44–49.
Ji M., Wang C., Bai Y., Yu M., Wang Y. Structural evolution of polyacrylonitrile precursor fibers during peroxidation and carbonization // Polymer Bulletin. 2007. V. 59. № 4. P. 527–536.
Roselman I.C., Tabor D. The friction of carbon fibres // J. Phys. D: Appl. Phys. 1976. V. 9. P. 2517–2532. https://doi.org/10.1088/0022-3727/9/17/012
Албагачиев А.Ю. Триботехнические характеристики углеродных материалов тормозных дисков при попадании на поверхности трения антигололедной жидкости // Приводы и компоненты машин. 2018. Т. 29. № 5. С. 5–8.
Чичинадзе А.В., Албагачиев А.Ю., Кожемякина В.Д., Коконин С.С., Суворов А.В., Кулаков В.В. Оценка фрикционно-износных характеристик отечественных углеродных фрикционных композиционных материалов для нагруженных тормозов самолетов // Трение и износ. 2009. Т. 30. № 4. С. 359–371.
Дополнительные материалы отсутствуют.
Инструменты
Известия РАН. Механика твердого тела