Известия РАН. Механика твердого тела, 2022, № 5, стр. 103-113
ИССЛЕДОВАНИЕ МЕХАНИЧЕСКИХ СВОЙСТВ ТОНКОПЛЕНОЧНЫХ МЕМБРАН ИЗ ОКСИДА И НИТРИДА КРЕМНИЯ
Н. А. Дюжев a, Е. Э. Гусев a, *, М. А. Махиборода a
a Национальный исследовательский университет “МИЭТ”
Зеленоград, Москва, Россия
* E-mail: bubbledouble@mail.ru
Поступила в редакцию 11.01.2022
После доработки 12.01.2022
Принята к публикации 13.01.2022
- EDN: KTUFHC
- DOI: 10.31857/S0572329922050063
Аннотация
Изготовлены тонкопленочные мембраны из чередующихся слоев оксида и нитрида кремния по групповой технологии. Исследовано влияние количества составляющих мембрану слоев при сохранении ее толщины на величину механической прочности. Давление разрыва мембранной структуры диаметром 560 мкм изменяется в диапазоне от 0.9 до 1.65 атм для 30 образцов в зависимости от количества составляющих мембрану слоев. Механическая прочность структуры Si3N4/SiO2 изменяется от 10.5 до 19.2 ГПа. Показано, что область разрыва структуры локализована на границе мембрана/подложка.
Введение. Актуальность работы подтверждается постоянно расширяющейся областью применения преобразователей физических величин (сенсоров) за счет миниатюризации конструкции и улучшения выходных характеристик. В качестве ключевой детали значительной части сенсоров используются мембраны, выполненные по кремниевой МЭМС микро- и нанотехнологии. Исследованию влияния уменьшения толщины единичного слоя (при сохранении общей толщины) на механические свойства тонкопленочной мембраны из оксида и нитрида кремния посвящена данная работа.
Пленки SiO2 и Si3N4 обладают сжимающими и растягивающими механическими напряжениями, что приводит к компенсации напряжений и повышению запаса механической прочности. Технологический процесс формирования мембран включает в себя осаждение тонких пленок на подложку с последующим удалением локальных областей кремниевой подложки.
Одной из проблем в процессе разработки сенсоров является достоверность сведений о механической прочности материалов [1], особенно с учетом размерного эффекта между объемными и пленочными материалами [2]. Поэтому необходимо совершенствовать метрологическую базу измерений. В [3] механическая прочность боросиликатного стекла измерена методом ударного сжатия. В [4] механическая прочность слоя нитрида галлия, сформированного методом гидридно-хлоридной парофазной эпитаксии, определена посредством индентора. В данном исследовании авторы применяли бесконтактный метод выдувания тонкой пленки посредством избыточного давления, к достоинствам которого можно отнести отсутствие внесенных дефектов.
Механическая прочность материала зависит от величины остаточных внутренних механических напряжений. Одной из причин возникновения внутренних механических напряжений являются дефекты и скрытые трещины в объеме материала. Поэтому, необходимо анализировать причину их возникновения и находить технологические и конструкционные факторы, направленные на минимизацию количества и размеров дефектов и трещин. Например, известна работа, описывающая закономерность образования дефектов в процессе термообработки кремния [5]. Также интересны работы по анализу трещин в соединении материалов [6, 7].
Из конструкционных решений можно выделить переход от прямоугольной к круглой форме мембраны [8]. Это связано с тем, что разрушение мембраны в большинстве случаев происходит по границе мембрана-подложка. Форма круга обеспечивает значительно меньшие значения упругих деформаций по сравнению с прямоугольной формой мембраны. Значения деформаций равномерно распределены по контуру мембраны и в материале мембраны [8]. Известен метод увеличения механической прочности, заключающийся в изменении стехиометрического соотношения между атомами в материале, например, увеличение концентрации углерода в SiC [9]. К другим факторам повышения механической прочности относят: уменьшение поверхностных дефектов [10]; изменение размера зерен структуры [11]; легирование материала пленки атомами меди, цинка, магния, марганца, кремния [2].
1. Технологический маршрут. Тонкие пленки были осаждены на кремниевую пластину диаметром 150 мм с кристаллографической ориентацией (100) и толщиной 670 мкм. В результате сформировалась круглая мембрана на Si кристалле квадратной формы со стороной 6 мм. Исследуемая мембранная структура состоит из набора чередующихся слоев нитрида и оксида кремния толщиной 0.32 ± 0.02 мкм. Причем толщина единичного слоя SiO2 или Si3N4 варьируется: 80, 160 и 320 нм. Толщина всей тонкопленочной мембраны для каждой из трех пластин с массивом мембран составляет 640 нм.
Технологический маршрут изготовления структуры показан ниже. В качестве примера на рис. 1, а изображена четырехслойная структура SiO2/Si3N4. Особенностью технологического маршрута формирования мембран является формирование маски для глубокого травления кремния (на глубину подложки). Слой фоторезиста толщиной единицы микрон стравливается раньше, чем происходит травление на глубину Si подложки толщиной 670 мкм. В результате значительно возрастает площадь травления и возникает эффект черного кремния. Поэтому стандартный слой фоторезиста заменяется на слой алюминия. Алюминий обладает большей селективностью к кремнию по сравнению с фоторезистом (при травлении кремния).
Таким образом, сначала формируют набор чередующихся слоев SiO2/Si3N4 методом химического осаждения из газовой фазы (PECVD). После этого, магнетронным методом формируют слой алюминия на обратной стороне подложки (рис. 1, b). Затем проводят фотолитографию по алюминию (рис. 1, c). После этого проводят жидкостное химическое травление алюминия и удаление резиста в ДМФА (рис. 1, d). Затем осаждают слой алюминия на лицевой стороне для предотвращения попадания мембран в реакционную камеру. Далее выполняют глубокое травление кремния (Bosch-процесс) на глубину подложки до SiO2 (рис. 1, e). После этого, проводят жидкостное химическое травление алюминия (рис. 1, f).
На рис. 2–4 приведены изображения во вторичных электронах поперечного сечения соответственно образцов тонких пленок Si3N4/SiO2 на кремниевой подложке. Топология набора мембран представляет собой круг, расположенный по центру кристалла квадратной формы со стороной 6 мм. В мембране отсутствуют концентраторы механических напряжений за счет использования шаблона травления круглой формы.
Результат анализа распределения элементов по глубине посредством ВИМС показан на рис. 5. Анализ образцов проводился в системе TOF.SIMS 5 при следующих условиях: травление кратера в мембранах проводилось ионами цезия Cs+ с энергией 1 кэВ на растре 300 × 300 мкм; – анализирующий пучок ионов висмута (Bi+) с током 1.5 пА имел энергию 30 кэВ и растр 100 × 100 мкм; для измерения глубины кратера ионного травления использовался контактный профилометр Alpha-Step D-120 компании KLA-Tencor Instruments (США).
Рис. 5.
Распределение элементов по глубине посредством ВИМС для образца c толщиной единичного слоя 160 нм. По оси Х отложена глубина H в нм. По оси Y отложена интенсивность I в условных единицах.
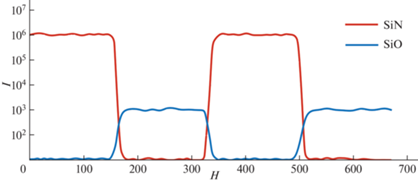
Также для определения элементного состава набора слоев Si3N4/SiO2, получаемых в чередующихся процессах химического осаждения из газовой фазы, и уточнения значений их толщины, образцы исследовались методом ЭОС на оже-спектрометре PHI-670xi компании Physical Electronics (США). Профильный оже-анализ исследуемых образцов проводились при следующих условиях: – ускоряющее напряжение первичного электронного пучка – 10 кВ; – ток первичного электронного пучка – 20 нА; – ускоряющее напряжение пучка ионов аргона (Ar+) – 3 кВ; – ток ионного пучка – 0.6 мкА; – диаметр области усреднения регистрации оже-сигнала – 170 мкм. Расчет концентрации элементов проводится в соответствии с моделью гомогенного распределения с использованием метода относительных коэффициентов обратной элементной чувствительности. Относительные коэффициенты элементной чувствительности для азота, кислорода и кремния были получены ранее на тестовых образцах оксида кремния, нитрида кремния.
Для получения распределений элементов по глубине сформированных слоев определялась средняя скорость ионного распыления слоев двуокиси и нитрида кремния. Она рассчитывалась по глубине кратера ионного травления мембраны, измеряемой на контактном профилометре Alpha-Step D-120 компании KLA-Tencor Instruments (США), и времени его формирования. Распределение элементов по глубине посредством метода Оже-спектроскопии показано на рис. 6.
Рис. 6.
Распределение элементов по глубине, полученные оже-анализом, для образца c толщиной единичного слоя 80 нм. По оси Х отложена глубина H в нм. По оси Y отложена концентрация атомов N в относительных единицах.
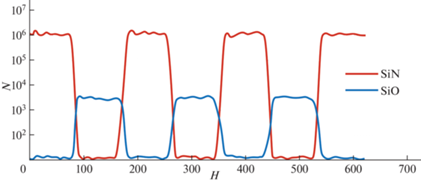
Таким образом, измерения на аналитическом оборудовании подтверждают запланированную толщину и последовательность чередующихся слоев Si3N4/SiO2.
Далее проводился контроль экспериментального диаметра мембраны. Для этого посредством алмазного диска был сделан рез образцов по центру круглой мембраны (рис. 7).
На изображении с РЭМ заметно, что экспериментальный диаметр мембраны составляет 560 мкм. Также заметна линия надреза на глубину 600 мкм при толщине пластины в 670 мкм. Стенки канавок имеют вертикальный профиль травления после Bosch-процесса.
2. Расчет механических напряжений. После формирования набора чередующихся слоев SiO2/Si3N4 на Si подложке проведены измерения механических напряжений в тонких пленках по формуле Стони. Стандартная методика измерения по величине кривизны структуры была модернизована. В результате, получено распределение механических напряжений в локальных областях структуры. Также повышена точность расчета. В программном обеспечении для современных профилометров часто заложен ряд упрощений при расчете величины напряжений: радиус кривизны гораздо больше расстояния между соседними точками, используются функции полинома и производные второго порядка. Следовательно, при увеличении длины шага сканирования возрастает погрешность. Формула (2.1) для расчета механических напряжений:
(2.1)
${{{{\sigma }}}_{0}} = \frac{{{{E}_{{\text{s}}}} \cdot d_{{\text{s}}}^{2}}}{{6 \cdot \left( {1 - {{{{\mu }}}_{{\text{s}}}}} \right) \cdot {{d}_{{\text{f}}}}}} \cdot \frac{1}{{{{R}_{{\text{f}}}}}}$На рис. 8 показано распределение механических напряжений σ0 в восьмислойной пленке SiO2/Si3N4. Измерение рельефа проводилось в направлении перпендикулярном (С-D) и параллельном базовому срезу (A-B). Двухосный модуль упругости составляет 181 ГПа для Si пластины с кристаллографической ориентацией (100). Результирующее механическое напряжение у данного набора пленок – сжимающее. Рассчитанная величина механического напряжения составляет – 50 МПа.
Рис. 8.
Распределение механических напряжений по Si пластине в тонкой пленке SiO2/Si3N4. По оси Х отложена координата оси Х в мм. По оси Y отложена величина механических напряжений σ в МПа. Легенда: 1 – направление перпендикулярное базовому срезу, 2 – направление параллельное базовому срезу.
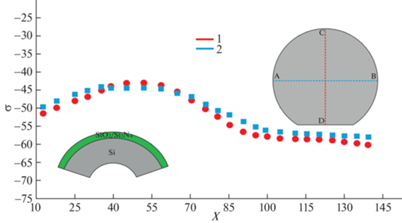
3. Анализ механической прочности структуры. В следующих статьях указан диапазон значений механической прочности пленки оксида кремния: 0.364 ± 0.57 ГПа PECVD SiO2 толщиной 1.0 мкм [13]; 0.89 ± 0.07 ГПа термического SiO2 для слоев толщиной от 507 до 985 нм [14]; от 1.2 до 1.9 ГПа PECVD оксида кремния [12]; 8.4 ГПа для нитевидных структур из SiO2 [15]. Значение механической прочности пленки нитрида кремния составляет 14.0 ГПа [15–17]. В книге 2018 года [18] указано, что механическая прочность пленки нитрида кремния, полученной методом LPCVD, изменяется в диапазоне от 10.8 до 11.7 ГПа, при толщине пленки от 72.6 до 83.4 нм. По результатам работы [19] механическая прочность LPCVD нитрида кремния составляет 5.87 ГПа. Для дальнейших расчетов было использовано значение механической прочности оксида кремния 0.365 ГПа и нитрида кремния 14 ГПа.
Теоретическое значение механической прочности (максимальных механических напряжений) мембраны σт вычисляется по следующей формуле (3.1):
(3.1)
${{{{\sigma }}}_{{\text{т}}}} = \frac{{{{{{\sigma }}}_{{{\text{Si}}{{{\text{O}}}_{2}}}}} \cdot {{h}_{{{\text{Si}}{{{\text{O}}}_{2}}}}} + {{{{\sigma }}}_{{{\text{S}}{{{\text{i}}}_{3}}{{{\text{N}}}_{4}}}}} \cdot {{h}_{{{\text{S}}{{{\text{i}}}_{3}}{{{\text{N}}}_{4}}}}}}}{{{{h}_{{{\text{Si}}{{{\text{O}}}_{2}}}}} + {{h}_{{{\text{S}}{{{\text{i}}}_{3}}{{{\text{N}}}_{4}}}}}}},$Рассчитанное значение σт составляет 7.18 ГПа. Распределение механических напряжений по диаметру мембраны рассчитывается по формуле (3.2) [2]:
(3.2)
${{\sigma }} = \frac{{3 \cdot P}}{{8 \cdot {{h}^{2}}}} \cdot \sqrt {({{{(1 + {{\mu }})}}^{2}} \cdot (2{{a}^{4}} - 8{{a}^{2}}{{r}^{2}}) + {{r}^{4}} \cdot (10 + 12{{\mu }} + 10{{{{\mu }}}^{2}}))} $Результаты расчета по формуле (3.2) распределения механических напряжений по диаметру мембраны при различном избыточном давлении для двухслойной, четырехслойной и восьмислойной мембраны представлены на рис. 9.
Рис. 9.
Распределение механических напряжений в мембране SiO2/Si3N4. По оси Х отложена величина расстояния от центра D в мм. По оси Y отложена величина механических напряжений σ в МПа. Легенда: 1 – избыточное давление 1.65 атм для мембраны из 8 слоев, 2 – избыточное давление 1.25 атм для мембраны из 4 слоев, 3 – избыточное давление 0.9 атм для мембраны из 2 слоев.
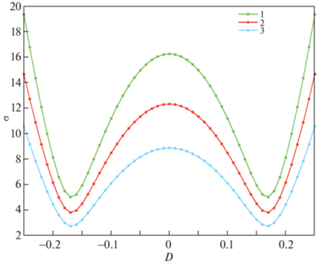
Согласно аналитическому расчету, максимальные механические напряжения ${{{{\sigma }}}_{{{\text{макс}}}}}$ возникают, когда расстояние от центра (середины) мембраны равно радиусу, т.е. r = a. Таким образом, прогнозируемое значение критического избыточного давления Pпр рассчитывают по формуле (3.3) [2]:
(3.3)
${{P}_{{{\text{пр}}}}} = \frac{{{\text{\;}}{{{{\sigma }}}_{{{\text{макс}}}}} \cdot {\text{\;}}{{h}^{2}}}}{{{{a}^{2}} \cdot {\text{\;}}B\left( {{\mu }} \right)}}$Коэффициент В(µ) рассчитывается как $\frac{3}{4}\sqrt {1 + {{{{\mu }}}^{2}}} $. Значение коэффициента Пуассона мембраны µ рассчитывается как среднее арифметическое. Учитывая, что ${{\mu }_{{{\text{Si}}{{{\text{O}}}_{2}}}}}$ составляет 0.2, ${{\mu }_{{{\text{S}}{{{\text{i}}}_{3}}{{{\text{N}}}_{4}}}}}$ 0.23, то коэффициент Пуассона мембраны µ будет равным 0.215. Следовательно, значение коэффициента B(μ) составляет 0.76. Таким образом, согласно расчетам по формуле (3.3) для мембраны диаметром 0.5 мм прогнозируемое значение критического избыточного давления Pпр будет равным 0.6 атм.
4. Анализ двухосного модуля упругости структуры. Анализируя зависимость (формула (4.1)) прогиба мембраны w от избыточного давления P, можно определить двухосный модуль упругости Е/(1 – µ):
(4.1)
$P = {{C}_{1}} \cdot \frac{{{{{{\sigma }}}_{0}} \cdot h \cdot w}}{{{{a}^{2}}}} + {{C}_{2}} \cdot \frac{{E \cdot h \cdot {{w}^{3}}}}{{\left( {1 - {{\mu }}} \right) \cdot {{a}^{4}}}}$Значения коэффициентов С1 и С2 зависят от формы мембраны. Обычно при работе с круглыми мембранами используют С1 = 4 и С2 = 8/3 [2]. Зависимость P(w) можно разделить на крутую и пологую область. Критерий крутой области выполняется при малых значениях прогиба мембраны w, т.е. первое слагаемое значительно больше второго. Значение двухосного модуля упругости Е/(1 – µ) вычисляют на пологой области зависимости (5) при больших значениях прогиба мембраны w, т.е. значением первого слагаемого можно пренебречь (формула (4.2)):
Модуль Юнга нитрида кремния составляет 225 ГПа [19], модуль Юнга оксида кремния 60.1 ± 3.4 ГПа [13]. Следовательно, модуль Юнга мембраны будет равным 142.5 ГПа. Теоретическое значение двухосного модуля упругости мембраны Е/(1 – µ) составит 182 ГПа при коэффициенте Пуассона мембраны µ равном 0.215 рассчитанном ранее.
Ниже представлена зависимость прогиба мембраны w от избыточного давления P (рис. 10), рассчитанная по формуле, полученной в результате моделирования в Comsol и экспериментальные данные для восьмислойного образца. В формуле (4.1) величина остаточных напряжений в структуре составляет 50 МПа. Для повышения корреляции между расчетом по формуле (4.1), моделированием в среде Comsol и экспериментальными данными величина начального прогиба (при P = 0) будет равной 3.5 мкм при моделировании и в аналитическом расчете.
Рис. 10.
Зависимость прогиба мембраны от избыточного давления. По оси Х отложена величина избыточного давления в атм. По оси Y отложена величина прогиба мембраны w в мкм: 1 – расчёт по формуле при E/(1 – μ) равном 182 ГПа, 2 – моделирование в программе Comsol, 3 – эксперимент.
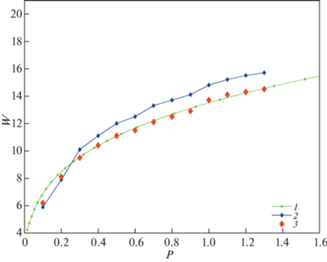
Из рис. 10 можно сделать несколько выводов. Относительная погрешность формулы с экспериментальными данными не превышает 5%, а относительная погрешность моделирования с экспериментальными данными не превышает 10%. Исходная структура имеет значительную величину прогиба мембраны, которая не учитывается в исходной формуле и в модели Comsol. Рассчитывая по формуле (4.2) модуль упругости из экспериментальных данных при давлении P, равном 1.3 атм получим значение 97.6 ГПа, что в несколько раз меньше теоретического значения. Это связано с эффектом использования набора слоев вместо монослоя материала. Предполагается, что модуль Юнга материала, сформированный на подложке, вносит больший эффект на результирующее значение механических свойств набора тонких пленок, входящих в состав мембраны, чем остальные тонкие пленки.
5. Экспериментальное измерение механической прочности. Для определения механических свойств мембранных элементов был модернизирован ранее разработанный стенд [2]. Избыточное давление подается с магистрали (вместо компрессора). Таким образом, расширен верхний диапазон величины давления до 6.5 атм, увеличена стабильность значения давления в системе.
Были экспериментально определены значения критического избыточного давления на модернизированном стенде. Избыточное давление разрыва мембраны Si3N4/SiO2 с экспериментальным диаметром 0.56 мм (30 образцов) составляет: для двухслойной структуры 0.9 ± 0.05 атм; для четырехслойной 1.25 ± 0.05 атм; для восьмислойной 1.65 ± 0.1 атм. Заметно, что полученные результаты обладают высокой воспроизводимостью. Экспериментальное значение механической прочности мембраны из Si3N4/SiO2 составляет 10.5 ГПа (двухслойная), 14.3 ГПа (четырехслойная) и 19.2 (восьмислойная).
Выводы. Экспериментальное значение механической прочности мембраны из Si3N4/SiO2 изменяется от 10.5 до 19.2 ГПа, экспериментальный двухосный модуль упругости E/(1 – µ) для восьмислойной мембраны составляет 97.6 ГПа. Экспериментальный размер мембран будет равным 0.56 мм при размере открытой области в шаблоне 0.5 мм. В процессе травления сформировался вертикальный профиль стенок полости. Избыточное давление разрыва мембранных структур из Si3N4/SiO2 на кремниевой подложке изменяется в диапазоне от 0.9 до 1.65 атм для диаметра 0.56 мм. Полученный результат позволяет использовать данные мембраны в сенсорах с хорошим запасом механической прочности. Разработчик может выбрать баланс между затраченным временем на проведение процесса и необходимой величиной механической прочности материала. Повышение механической прочности объясняется уменьшением количества дефектов в объеме пленок Si3N4/SiO2.
Сравнивая полученный эффект с результатами работ других исследователей [20] можно заметить, что подобные эффекты увеличения механической прочности (жесткости) многослойных структур были выявлены ранее, но для других материалов и изготовленных другим методом. Например, в [21] для структуры Mo/NbN, полученной эпитаксиальным методом, с уменьшением толщины единичного слоя с 50 до 1 нм экспериментальная жесткость многослойной структуры увеличилась с 13 до 33 ГПа. При этом теоретическая жесткость, рассчитанная по правилу смесей (как и в текущей работе), составляет 9.5 ГПа. В мировой практике исследования влияния данного эффекта для материалов SiO2 и Si3N4, полученных методом осаждения из газовой фазы (PECVD), проведено ранее не было, что подтверждает новизну данного экспериментального исследования.
Благодарности. Работы выполнены на оборудовании ЦКП “МСТ и ЭКБ” НИУ МИЭТ при поддержке гранта Президента РФ (№ МК-1692.2022.4).
Список литературы
Шпейзман В.В., Николаев В.И., Поздняков А.О. и др. Прочность пластин монокристаллического кремния для солнечных элементов // Журнал технической физики. 2020. № 90 (1). С. 79–84. https://doi.org/10.21883/JTF.2020.01.48665.148-19
Gusev E.E., Borisova A.V., Dedkova A.A. et al. The effect of ion beam etching on mechanical strength multilayer aluminum membranes // 2019 IEEE Conference of Russian Young Researchers in Electrical and Electronic Engineering (EIConRus). 2019. № 8657243. P. 1990–1994. https://doi.org/10.1109/eiconrus.2019.8657243
Savinykh A.S., Kanel G.I., Razorenov S.V. Strength and failure of LK7 borosilicate glass under shock compression // Tech. Phys. 2010. V. 55. № 6. P. 839–843. https://doi.org/10.1134/S1063784210060150
Zhilyaev Y.V., Raevskii S.D., Grabko D.Z. et al. Bulk GaN layers grown on oxidized silicon by vapor-phase epitaxy in a hydride–chloride system // Tech. Phys. Lett. 2005. V. 31. № 5. P. 367–369. https://doi.org/10.1134/1.1931770
Верезуб Н.А., Простомолотов А.И. Механика процессов выращивания и термообработки монокристаллического кремния // Изв. РАН. МТТ. 2020. № 5. С. 51–63. https://doi.org/10.31857/S0572329920040157
Перельмутер М.Н. Анализ трещиностойкости соединений материалов // Изв. РАН. МТТ. 2020. № 4. С. 96–114. https://doi.org/10.31857/S057232992004011X
Бабешко В.А., Бабешко О.М., Евдокимова О.В. Трещины нового типа и модели некоторых наноматериалов // Изв. РАН. МТТ. 2020. № 5. С. 13–20. https://doi.org/10.31857/S0572329920050025
Власов А.И., Цивинская Т.А., Шахнов В.А. Анализ влияния формы мембраны на механическую прочность и стабильность параметров МЭМС-сенсоров давления // Проблемы разработки перспективных микро- и наноэлектронных систем (МЭС). 2016. № 4. С. 65–70.
Shikunov S.L., Kurlov V.N. SiC-based composite mterials obtained by siliconizing carbon matrices // Tech. Phys. 2017. V. 62. № 12. P. 1869–1876. https://doi.org/10.1134/S1063784217120222
Mueller M.G., Fornabaio M., Zagar G., Mortensen A. Microscopic strength of silicon particles in an aluminium – silicon alloy // Acta Mater. 2016. V. 105. P. 165–175. https://doi.org/10.1016/j.actamat.2015.12.006
Ramnath Venkatraman, John C. Bravman Separation of film thickness and grain boundary strengthening effects in Al thin films on Si // J. Mater. Res. 1992. V. 7. № 8. P. 2040–2048. https://doi.org/10.1557/JMR.1992.2040
Tsuchiya T., Sakata J., Taga Y. Tensile strength and fracture toughness of surface micromachined polycrystalline silicon thin films prepared under various conditions // MRS Proc. 1998. V. 505. P. 285–290. https://doi.org/10.1557/proc-505-285
Sharpe W.N., Pulskamp J., Gianola D.S. et al. Strain measurements of silicon dioxide microspecimens by digital imaging processing // Exp. Mech. 2007. V. 47. P. 649–658. https://doi.org/10.1007/s11340-006-9010-z
Jinling Yang. Fracture Properties of LPCVD silicon nitride and thermally grown silicon oxide thin films from the load-deflection of long Si3N4 and SiO2/Si3N4 diaphragms // J. Microelectromech. Sys. 2008. V. 17. № 5. P. 1120–1134. https://doi.org/10.1109/JMEMS.2008.928706
Petersen K.E. Silicon as a mechanical material // Proc. IEEE. 1982. V. 70. № 5. P. 420–457. https://doi.org/10.1109/PROC.1982.12331
Tai-Ran Hsu. MEMS and Microsystems: Design and Manufacture. Boston: McGraw-Hill Education, 2002. 436 p.
Madou M. Fundamentals of Microfabrication. L.: Taylor & Francis, 1997. 589 p.
Qing An Huang. Micro Electro Mechanical Systems. Singapore: Springer, 2018. 1479 p.
Edwards R.L., Coles G., Sharpe W.N. Comparison of tensile and bulge tests for thin-film silicon nitride // Exp. Mech. 2004. V. 44. № 1. P. 49–54. https://doi.org/10.1007/bf02427976
Clemens B.M., Kung H., Barnet S.A. Structure and strength of multilayers // MRS Bull. 1999. V. 24. P. 20–26. https://doi.org/10.1557/S0883769400051502
Madan A., Yun-yu Wang, Barnet S.A. et al. Enhanced mechanical hardness in epitaxial nonisostructural Mo/NbN and W/NbN superlattices // J. Appl. Phys. 1998. V. 84. № 2. P. 15. https://doi.org/10.1063/1.368137
Дополнительные материалы отсутствуют.
Инструменты
Известия РАН. Механика твердого тела