Мембраны и мембранные технологии, 2022, T. 12, № 1, стр. 47-56
О влиянии растворителя и предварительной ультразвуковой обработки на свойства мембран Nafion®, полученных методом отливки
Е. Ю. Сафронова a, *, Д. Ю. Воропаева a, С. А. Новикова a, А. Б. Ярославцев a
a Институт общей и неорганической химии им. Н.С. Курнакова Российской академии наук
119991 Москва, Ленинский просп., 31, Россия
* E-mail: safronova@igic.ras.ru
Поступила в редакцию 03.09.2021
После доработки 28.09.2021
Принята к публикации 08.10.2021
- EDN: XPLGLY
- DOI: 10.1134/S2218117222010072
Аннотация
В статье описано влияние природы растворителя на примере полярных протонных (вода) и апротонных (N,N-диметилформамид (ДМФА) и N,N-диметилацетамид (ДМА)) жидкостей на свойства мембран Nafion, полученных из них методом отливки. Влагосодержание и протонная проводимость мембран Nafion, полученных из водной дисперсии, существенно выше, чем из дисперсий в ДМФА и ДМА, однако их механические свойства и стабильность обычно оказываются невысокими. Непродолжительная ультразвуковая (УЗ) обработка дисперсий Nafion в ДМФА и ДМА позволяет повысить проводимость мембран и снизить энергию ее активации. Это происходит из-за улучшения микроструктуры мембран за счет деагломерации макромолекул. Присутствие воды при УЗ обработке дисперсий Nafion приводит к увеличению их вязкости и потере большого количества функциональных сульфогрупп. В результате этого снижается проводимость мембран. Для нивелирования этих процессов целесообразно использовать апротонные жидкости или смеси с небольшим содержанием воды. Предложено объяснение влияния природы диспергирующей жидкости и УЗ обработки на свойства мембран Nafion с точки зрения морфологии полимера в дисперсии и в пленке.
ВВЕДЕНИЕ
Перфторированные сульфокислотные мембраны, самой широко известной из которых является Nafion® (DuPont, США), находят применение в альтернативной энергетике в качестве электролита в водородно-воздушных и метанольных топливных элементах [1–4] и в металл-ионных аккумуляторах [5–8]. Кроме того, Nafion® является одним из компонентов каталитических чернил для мембранно-электродных блоков топливных элементов и обеспечивает перенос протонов от наночастиц катализатора к электролиту [9]. Высокая проводимость и селективность переноса катионов, низкие газопроницаемость и электронная проводимость наряду с хорошими механическими свойствами и химической стабильностью обеспечили интерес исследователей к данному материалу.
Свойства перфторированных сульфосодержащих мембран определяются их микроструктурой. Представления о ней основаны на результатах исследований методами малоуглового рентгеновского и нейтронного рассеяния, а также транспортных свойств мембран [10, 11]. Различие в природе основной и боковых цепочек, входящих в состав полимера, приводит к группировке гидрофильных –SO3H групп в кластеры, в результате гидратации которых в мембране формируется система пор и каналов, по которой осуществляется ионный перенос [12]. Важно отметить, что визуализация морфологии таких мембран напрямую с помощью методов электронной микроскопии затруднена, поскольку исследования проводятся в вакууме, и в результате дегидратации поры исчезают. Низкий контраст между гидрофобной матрицей и ионными кластерами не позволяет получать изображения хорошего качества [13]. О микроструктуре перфторированных сульфосодержащих мембран можно судить по косвенным признакам, например, значениям влагосодержания, ионной подвижности, измеренной различными способами, селективности ионного переноса, а также способности сорбировать объемные молекулы и ионы [11, 14].
Известно, что мембраны типа Nafion® обладают эффектом памяти – их микроструктура, сорбционные и транспортные свойства меняются после обработки при различных температуре, влажности, нагрузке и химическом составе реагентов и зависят от способа формирования пленки [14–19]. В связи с расширением областей применения перфторсульфополимеров, тенденциями к использованию пленок меньшей толщины, а также гибридных мембран, наиболее технологичным способом получения таких материалов является отливка из растворов или дисперсий [20, 21]. Большое количество работ в последние годы посвящено изучению взаимосвязи между морфологией перфторсульфополимеров Nafion® в дисперсиях и тонких пленках (толщиной несколько десятков нанометров, перспективных для использования в электродах топливных элементов, в сенсорах и др.) и свойствами этих пленок [19, 22–24]. Подобные исследования особенно важны при формировании каталитических чернил для топливных элементов, поскольку тонкий слой перфторсульфополимера на поверхности наночастиц катализатора обеспечивает быстрый перенос протона и вносит существенный вклад в эффективность работы каталитического слоя в топливном элементе [25, 26].
Известно, что микроструктура и свойства мембран Nafion® зависят от условий получения пленок (диспергирующая жидкость, скорость и температура удаления растворителя) [17, 27–29]. Недостатком мембран, полученных методом отливки, часто является низкая механическая прочность. Повысить ее можно выбором температурного режима формирования пленок и переходом к более высококипящим растворителям [30]. Авторами [31] показано, что в процессе удаления жидкости из дисперсий Nafion® гелеобразование происходит при различной концентрации полимера и по разному механизму в зависимости от природы жидкости. В результате этого механические свойства мембран могут отличаться вплоть до 4 порядков. Наиболее прочными являются пленки, полученные из дисперсий в апротонных растворителях. Выдвинуто предположение о том, что механическая прочность мембран тем выше, чем сильнее переплетаются полимерные цепи при удалении диспергирующей жидкости [32]. Ионная проводимость перфторированных сульфосодержащих мембран, полученных методом отливки, также сильно меняется в зависимости от природы диспергирующей жидкости [33, 34].
Установлено [35–37], что предварительная ультразвуковая (УЗ) обработка водно-спиртовых растворов Nafion® влияет на механические и транспортные свойства мембран, полученных из них методом отливки. Под действием УЗ происходит уменьшение вязкости спиртовых растворов Nafion за счет деагломерации и уменьшения длины макромолекул. Протонная проводимость мембран, полученных из раствора после УЗ обработки, увеличивается вплоть до 40% по сравнению с мембраной, полученной из необработанного раствора [35, 36]. УЗ обработка раствора Nafion в присутствии катализатора Pt/C может приводить к нежелательным реакциям и ухудшению электрохимических характеристик электродов в топливных элементах [37]. Сведений о влиянии природы диспергирующей жидкости на эффект УЗ обработки дисперсий Nafion в литературе найти не удалось.
Данная статья посвящена исследованию влияния природы диспергирующей жидкости (вода, N,N-диметилформамид (ДМФА) и N,N-диметилацетамид (ДМА)) и УЗ обработки дисперсий на свойства мембран Nafion®, получаемых из них методом отливки.
ЭКСПЕРИМЕНТАЛЬНАЯ ЧАСТЬ
В работе использовали водную дисперсию Nafion® (10 мас. %, DuPont, эквивалентный вес – 1100) в H+-форме. Дисперсии в ДМФА и ДМА получали растворением экструзионной мембраны Nafion®212 (Sigma Aldrich, эквивалентный вес – 1100) в Na+-форме. Для этого предварительно кондиционированную и переведенную в Na+-форму мембрану Nafion®212 сушили при комнатной температуре в вакууме в течение суток, измельчали и помещали в соответствующую жидкость из расчета того, что концентрация полимера в полученной дисперсии составит 5 мас. %. После этого смесь выдерживали при постоянном перемешивании на водяной бане при 80°С в течение 6 ч. В результате были получены прозрачные, визуально однородные дисперсии.
УЗ обработку дисперсий полимера проводили с помощью диспергатора Sonics Vibra cell VSX130 (частота 20 кГц) с использованием погружного зонда диаметром 3 мм (амплитуда 50%; мощность УЗ воздействия, определенная с помощью калориметрического метода, составила PУЗ = 5.2 ± 0.2 Вт) в течение 10 и 60 мин. Объем обрабатываемой жидкости составлял 8 мл. Дисперсию полимера помещали в стеклянную емкость диаметром 1.5 см и погружали зонд так, чтобы он находился на расстоянии 2–3 мм от ее дна и равноудален от стенок. В процессе УЗ обработки дисперсии охлаждали с помощью ледяной рубашки, чтобы увеличить интенсивность воздействия (температура жидкости во время обработки составляла 18 ± 1°С). Для доказательства того, что в процессе УЗ обработки происходит кавитация, кусок алюминиевой фольги погружали в воду и подвергали воздействию в течение 30 с в тех же условиях, что и дисперсии полимера. В результате этого на фольге образовывалось множество сквозных отверстий.
В случае, если в жидкости, которую подвергают УЗ обработке, присутствуют молекулы воды, они могут подвергаться сонолизу. С помощью дозиметрии количественно показано формирование OH• радикалов при УЗ воздействии. Эксперимент проводили по методу Вэйслера, описанному в [38]. 0.1 M водный раствор иодида калия обрабатывали ультразвуком в тех же условиях, что и дисперсии полимера в течение 0, 10 и 60 мин. В результате разложения молекул воды под действием ультразвука образуются радикалы водорода (H•), гидроксильные радикалы (OH•) и перекись водорода (H2O2). Взаимодействие иодид ионов с OH• радикалами или молекулами H2O2 приводит к образованию молекул йода (I2). Избыток ионов I– реагирует с I2 с образованием тридиодид ионов $\left( {{\text{I}}_{3}^{ - }} \right).$ Концентрацию ${\text{I}}_{3}^{ - }$ в растворах до и после УЗ обработки определяли с помощью УФ-спектроскопии при длине волны 355 нм (коэффициент молярной экстинкции ${{\varepsilon }_{{{\text{I}}_{3}^{ - }}}}$ = 26303 л/(моль см)) на спектрофотометре PE-5300VI (“Экрос”, Россия). Использовали кварцевые кюветы длиной 1 см. Величину УЗ эффективности (SE, мкмоль/кДж) рассчитывали по формуле:
(1)
$SE = \frac{{{{C}_{{{\text{I}}_{3}^{ - }}}}V}}{{{{P}_{{{\text{УЗ}}}}}t \times {{{10}}^{{ - 3}}}}},$Полученные дисперсии полимера выливали на поверхность чашек Петри (пластиковых в случае водной дисперсии и стеклянных в случае дисперсии в ДМФА и ДМА) и удаляли жидкость. При получении мембран из водных дисперсий Nafion сушку проводили в следующем режиме: на воздухе при 45°С 12 ч, затем последовательно при 60, 70, 80, 85°С по 1 ч и в вакуумном шкафу при 80°С 4 ч. При получении мембран из дисперсий в ДМФА и ДМА сушку проводили на воздухе при 60°С 2 ч, при 80°С – 12 ч, затем в вакуумном шкафу при 110°С 4 ч. После этого пленки аккуратно снимали с поверхности чашек Петри и подвергали горячему прессованию под давлением 5 МПа при температуре 110°С в течение 3 мин для обеспечения лучшей прочности. Все полученные образцы мембран кондиционировали для приведения к стандартным условиям и перевода в протонную форму. Для этого их последовательно обрабатывали при комнатной температуре сначала дважды 5% раствором HCl в течение 1.5 ч, затем промывали деионизованной водой до исчезновения реакции на Cl–-ионы. Ионообменную емкость (ИОЕ), влагосодержание, проводимость и проницаемость водорода определяли для мембран в H+-форме; селективность ионного переноса – в Na+-форме.
Плотность дисперсий определяли до и после УЗ обработки с помощью портативного плотномера Densito (Mettler tolledo) при 25 ± 0.1°C. Вязкость дисперсий определяли непосредственно после обработки, а также через несколько дней с помощью вибрационного вискозиметра SV-1A (A&D) при 25 ± 0.2°C. Значение динамической вязкости (η, мПа с) рассчитывали из отношения экспериментально полученной вязкости к плотности раствора. Калибровку вискозиметра проводили по двум точкам с помощью стандартов вязкости 5 и 10 сП (Brookfield, США). Для всех условий обработки было проведено не менее трех экспериментов. Вязкость определяли по среднеарифметическому значению.
Для определения ИОЕ (мг-экв/г) мембрану в H+-форме предварительно выдерживали при 150°С в течение 30 мин. Затем навеску образца в сухом состоянии массой ~0.3 г выдерживали в 50 мл 0.1 М раствора NaCl в течение 12 ч при постоянном перемешивании. После этого раствор соли с мембраной титровали 0.05 М раствором NaOH.
Термический анализ образцов проводили с использованием термовесов Netzsch-TG 209 F1 в платиновых тиглях в атмосфере аргона в диапазоне температур от 25 до 150°С. Скорость нагрева составляла 10 К/мин. Влагосодержание мембран в H+-форме после их длительного контакта с водой определяли по разнице массы до термообработки и после выдерживания при 150°С.
Протонную проводимость мембран изучали в интервале температур 20–85°C при 100%-ной относительной влажности в контакте с деионизованной водой и на воздухе в диапазоне температур 25–60°С и влажности RH = 30%. Для задания необходимой влажности и температуры использовали климатическую камеру постоянных условий Binder MKF115 (точность задания влажности ±2.5%). Измерения проводили с помощью моста переменного тока Elins E-1500 (в диапазоне частот 10 Гц–3 МГц) на симметричных ячейках углерод/мембрана/углерод с активной площадью поверхности 1 см2. Величину проводимости (Ом–1 см–1) рассчитывали из сопротивления, найденного из годографа импеданса по отсечке на оси активных сопротивлений. Погрешность в определении величины удельной проводимости составляла менее 10%.
Проницаемость водорода через мембраны в H+-форме определяли методом газовой хроматографии с помощью хроматографа Кристаллюкс-4000М с детектором по теплопроводности (ток 30 мА) и набивной колонкой (сорбент Mole Seive 5 Å, 2 м, 30°C, 20 см3/мин, Ar). Для получения водорода использовали генератор водорода ООО “НПП Химэлектроника”. Эксперимент проводили в термостатированной ячейке, в одну часть которой подавался чистый водород, а в другую – аргон со скоростью 20 мл/мин. Для создания необходимого уровня влажности в потоке водорода и аргона каждый газ пропускали через два барботера с водой (100% влажность), которые были термостатированы при той же температуре, что и ячейка. Коэффициент проницаемости водорода P (см2/с) рассчитывали по формуле:
где L – толщина мембраны (см), CH – средняя объемная концентрация водорода в камере, в которую подавали водород (моль/см3), CAr – средняя объемная концентрация водорода в камере, в которую подавали аргон (моль/см3)). Поток газа через мембрану j (моль/(с см2)) рассчитывали из соотношения: где CAr – средняя объемная концентрация водорода в камере, в которую подавали аргон, приведенная к нормальным условиям (моль/см3), Vt – объемная скорость потока газа-носителя (см3/с), S – активная площадь мембраны (см2).Числа переноса ионов через мембраны в Na+-форме определяли при температуре 23 ± 1°С по методике, описанной в [35]. Для перевода мембран в Na+-форму их выдерживали в течение 24 ч в 2 M NaCl и многократно промывали деионизованной водой. Перед экспериментом образцы мембран выдерживали в течение 12 ч в 0.1 М растворе NaCl. После этого образец помещали в двухкамерную ячейку, разделенную мембраной (объем каждой камеры составлял 32 см3). Концентрации растворов NaCl составляли 0.1 М в одной камере и 0.5 М в другой. Два капилляра Луггина и Ag–AgCl электроды помещали в каждую камеру. Мембранный потенциал Emes между электродами измеряли с помощью потенциостата-гальваностата P-8 nano (ООО “Элинс”, Россия). Мембранный потенциал рассчитывали по уравнению Emem = Emes – Ecorr, где Emes – измеренное значение, Ecorr – величина, учитывающая неидеальность электродов сравнения, которую определяли с использованием в качестве внутреннего стандарта мембраны Neosepta CMX© (число переноса в исследуемых условиях – 99.0% [39]). Числа переноса катионов были рассчитаны как отношение найденного потенциала к потенциалу идеально селективной мембраны по уравнению:
где R – универсальная газовая постоянная, T – абсолютная температура, К; F – постоянная Фарадея, a1 и a2 – активности электролита (значения находили интерполяцией непрерывной функцией табличных значений (a1 (0.5 M NaCl) = 0.339, a2 (0.1 М NaCl) = 0.0773). Погрешность определения t+ равнялась ±0.2%.РЕЗУЛЬТАТЫ
Свойства дисперсий
Значения динамической вязкости исследуемых дисперсий Nafion® представлены в табл. 1. Вязкость дисперсий полимера увеличивается в ряду вода $ \ll $ ДМА ~ ДМФА. В результате УЗ обработки вязкость дисперсий Nafion в ДМФА и ДМА уменьшается на 40–50% после 10 мин и на 50–60% после 60 мин (табл. 1). УЗ обработка дисперсий Nafion в ДМФА приводит к более существенному отличию от вязкости исходной дисперсии, по сравнению с ДМА. Следует отметить, что изменения свойств дисперсий Nafion в ДМФА и ДМА после УЗ обработки являются необратимыми и значения вязкости остаются неизменными во времени по крайней мере в течение 200 ч. Аналогичное влияние УЗ обработки спиртовых растворов Nafion® описано в [35, 36].
Таблица 1.
Значения динамической вязкости (η, мПа с, при 25°С) дисперсий Nafion в H+-форме в воде (10 мас. %) и Na+-форме в ДМФА и ДМА (5 мас. %) до и после УЗ обработки
Диспергирующая жидкость |
Время УЗ обработки | ||
---|---|---|---|
0 мин | 10 мин | 60 мин | |
Вода | 4.82 | 5.31 | 7.57 |
ДФМА | 9.25 | 4.50 | 3.67 |
ДМА | 9.19 | 5.48 | 4.64 |
УЗ обработка водной дисперсии Nafion в течение 10 и 60 минут, напротив, приводит к увеличению вязкости на 10 и 65% (табл. 1). Однако после этого она постепенно снижается и через 1 нед. вязкость водной дисперсии, обработанной УЗ в течение 60 мин, уменьшается до 5.37 мПа с. При УЗ обработке коммерческих водно-спиртовых растворов Nafion® увеличения вязкости не наблюдалось [35, 36].
Свойства мембран
Природа диспергирующей жидкости существенно влияет на особенности самоорганизации перфторсульфополимеров, сольватированных различным образом, и возможность формирования пленок. Из водных дисперсий полимера Nafion сложно сформировать пленки большого размера. Напротив, отливка мембран из дисперсий в ДМФА и ДМА приводит к формированию пленок, плотность которых в сухом состоянии составляет ρ ~ ~ 1.5 г/см3. При формировании пленок из тех же дисперсий в ДМФА и ДМА после УЗ обработки плотность образцов увеличивается с ростом продолжительности воздействия до 1.6–1.7 г/см3 после 10 мин и до 1.8–2.0 г/см3 после 60 мин.
ИК спектры мембран, полученных из дисперсий Nafion во всех жидкостях до и после УЗ обработки, качественно похожи. Вместе с тем наблюдаются некоторые отличия в площади пиков: в результате УЗ обработки площадь пиков в области валентных колебаний сульфогрупп (νs ~ 1056 см–1) уменьшается. Изменение ИК спектров мембран, полученных из дисперсий в ДМФА и ДМА, одинаково, и площадь пика при 1056 см–1 уменьшается на 5–7% после УЗ обработки. Наиболее существенные изменения наблюдаются для водной дисперсии Nafion. Площадь пика при 1056 см–1 уменьшается на 10 и 25% после УЗ обработки водной дисперсии в течение 10 и 60 мин соответственно (рис. 1).
Рис. 1.
Фрагменты ИК спектров мембран Nafion в сухом состоянии, полученных из водных дисперсий полимера до и после УЗ обработки, нормированные на колебания CF2 групп основной цепочки νs = 1148 см–1.
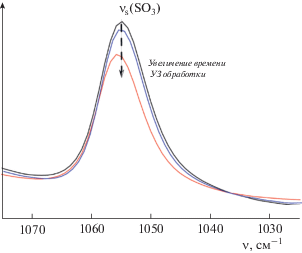
Об отрыве части боковых цепочек свидетельствует и уменьшение ИОЕ мембран, полученных из дисперсий после УЗ обработки. ИОЕ мембран, полученных из дисперсий Nafion в ДМФА и ДМА, после 60 мин УЗ обработки уменьшается с 1.0 до 0.94–0.95 мг-экв/г. Более существенное снижение ИОЕ наблюдается для мембран, полученных из водной дисперсии Nafion (с 1.1 мг-экв/г для исходной до 1.0 мг-экв/г для мембраны после 60 мин УЗ обработки).
Влагосодержание мембран уменьшается в ряду вода > ДМФА > ДМА (табл. 2). УЗ обработка водной дисперсии Nafion приводит к небольшому росту влагосодержания мембран (до 30.5–30.8% по сравнению с 29.2% для мембраны, полученной из водной дисперсии без УЗ обработки). Напротив, влагосодержание мембран, полученных из дисперсий Nafion в ДМФА и ДМА после УЗ обработки, понижается. Например, количество воды в мембранах, полученных из дисперсий в ДМФА, уменьшается с 25.3% (без УЗ обработки) до 24.9% (60 мин УЗ обработки).
Таблица 2.
Влагосодержание (W, %) исследуемых мембран в H+-форме в контакте с водой
Диспергирующая жидкость |
Время УЗ обработки | ||
---|---|---|---|
0 мин | 10 мин | 60 мин | |
Вода | 29.2 ± 0.2 | 30.8 ± 0.1 | 30.5 ± 0.1 |
ДФМА | 25.3 ± 0.1 | 25.1 ± 0.2 | 24.9 ± 0.1 |
ДМА | 23.3 ± 0.1 | 22.5 ± 0.1 | 18.6 ± 0.1 |
Протонная проводимость мембран Nafion в контакте с водой при 30°С, полученных из дисперсий в воде, ДМА и ДМФА, составляет 0.049, 0.030 и 0.023 Ом–1 см–1 соответственно (рис. 2). УЗ обработка водной дисперсии приводит к понижению проводимости. После 60 мин проводимость мембран понижается более чем на 20% (рис. 2а). УЗ обработка дисперсий Nafion в ДМФА и ДМА приводит к немонотонному изменению протонной проводимости полученных мембран. Так после 10 мин УЗ обработки таких дисперсий проводимость полученных мембран возрастает на ~10% (рис. 2б, 2в). Затем для раствора в ДМФА проводимость меняется сравнительно слабо, а для ДМА понижается практически до исходного значения.
Рис. 2.
Зависимость протонной проводимости от температуры, измеренной в контакте с водой, для мембран Nafion, полученных из водных дисперсий (а), дисперсий в ДМФА (б) и ДМА (в).
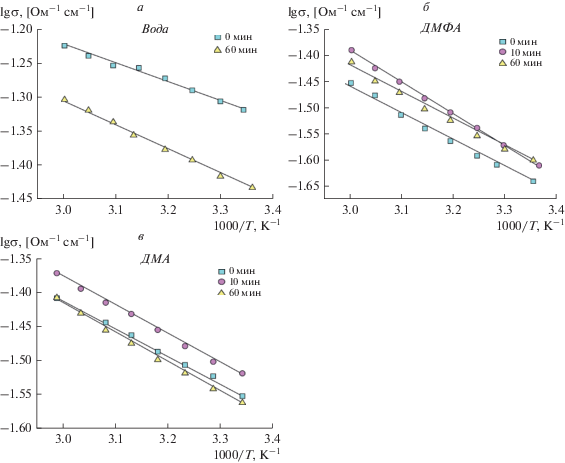
Для ионной проводимости чаще всего наблюдается закономерность – чем выше энергия активации, тем ниже величина проводимости. В соответствии с этим изменяется и энергия активации протонной проводимости мембран. В случае образцов, полученных из водной дисперсии, энергия активации проводимости увеличивается от 4.7 ± 0.1 до 6.5 ± 0.2 кДж/моль после 60 мин УЗ обработки. УЗ обработка дисперсий в ДМФА и ДМА, напротив, приводит к снижению энергии активации проводимости мембран. Так после 60 мин УЗ обработки дисперсии в ДМФА ее значение понижается от 15.1 ± 0.6 до 10.2 ± 0.3 кДж/моль.
Другой естественной закономерностью является снижение протонной проводимости мембран при уменьшении влажности. Так, значения проводимости мембран, полученных из дисперсий в воде и ДМФА без УЗ обработки, при 30°С и относительной влажности RH = 30% составляют 3.5 × 10–3 и 1.3 × 10–3 Ом–1 см–1 (рис. 3). В то же время УЗ обработка во всех случаях приводит к уменьшению негативного воздействия при снижении влажности. Так, проводимость мембран Nafion, полученных из дисперсий в воде и ДМФА после 60 минут УЗ обработки, увеличивается в 1.85 и 2 раза по сравнению с аналогичными мембранами, полученными из исходных дисперсий.
Рис. 3.
Протонная проводимость (при 30°С и относительной влажности RH = 30%) мембран Nafion, полученных из дисперсий в воде и ДМФА.
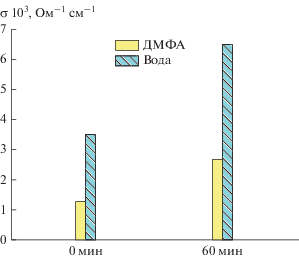
Числа переноса катионов через мембраны в Na+-форме уменьшаются с ростом времени УЗ обработки от t+(Na+) = 94.5 ± 0.4% для исходной Nafion, полученной из дисперсии в ДМФА, до 92.9 ± 0.3% и 91.7 ± 0.4% для мембран после 10 и 60 мин УЗ обработки. При этом проницаемость водорода (при 30°С и 100% RH) увеличивается на 60% от (1.40 ± 0.06) × 10–7 см2/с для исходной Nafion, полученной из дисперсии в ДМФА, до (2.23 ± 0.03) × 10–7 и (2.28 ± 0.04) × 10–7 см2/с для мембран, после 10 и 60 мин УЗ обработки дисперсий соответственно.
ОБСУЖДЕНИЕ РЕЗУЛЬТАТОВ
Изменение вязкости дисперсий, влагосодержания и ионной проводимости мембран Nafion в зависимости от природы диспергирующей жидкости и продолжительности УЗ обработки связано с особенностями морфологии полимеров в присутствии растворителей и в формируемых из них пленках. Основные перфторированные цепочки являются гидрофобными, в то время как боковые цепочки с сульфогруппами на концах – гидрофильными (рис. 4). При формировании мембран ионообменные группы объединяются в кластеры, вокруг которых находится гидрофобная матрица. Высокая склонность сульфогрупп к гидратации приводит к расширению кластеров в присутствии воды и формированию системы пор и каналов по которой осуществляется ионный перенос [12]. Сульфогруппы при этом располагаются по внутренней границе кластеров. Скорость ионного переноса тем выше, чем больше размер пор и чем более разветвленной является система пор и каналов.
Используемые в работе диспергирующие жидкости отличаются друг от друга полярностью и сродством к группам перфторсульфополимеров. В полярных растворителях, таких как вода (диэлектрическая проницаемость ε = 81), макромолекулы перфторсульфополимера Nafion стремятся локализоваться так, чтобы площадь контакта гидрофобных участков макромолекул с растворителем была минимальной. При этом по данным [11, 40], полимер самоорганизуется в структуры типа стержней, образованных гидрофобными основными цепочками, на поверхности которых располагаются гидрофильные функциональные группы. Такая морфология препятствует агломерации макромолекул и вязкость водной дисперсии Nafion гораздо ниже, чем вязкость дисперсий в ДМФА, ДМА (табл. 1) или водно-спиртовой смеси [35].
В связи с этим процесс формирования пленок из водной дисперсии, который сопровождается потерей большого количества воды, осложняется необходимостью обращения кластеров. Как известно, именно гидрофобная матрица обеспечивает высокую механическую прочность мембран Nafion. В частности, для пленок, полученных методом отливки, важное значение имеет переплетение макромолекул [32]. Отталкивание сульфогрупп друг от друга препятствует сцеплению перфторированных цепочек. В результате этого влагосодержание и проводимость мембран Nafion, полученных из водной дисперсии, гораздо выше, чем из дисперсий в ДМФА и ДМА (табл. 2, рис. 2, 3) и других растворителях [35]. По совокупности этих факторов мембраны Nafion, полученные отливкой из водной дисперсии, обладают низкой механической прочностью и стабильностью.
В присутствии полярных апротонных органических растворителей с существенно меньшей по сравнению с водой диэлектрической проницаемостью, таких как ДМФА (ε = 36.7) и ДМА (ε = 37.8), макромолекулы Nafion могут сворачиваться в клубки, а боковые цепочки могут располагаться вблизи от основной перфторированной цепи. Сродство гидрофобной перфторированной цепочки к ДМФА и ДМА способствует более плотному контакту растворителя и полимера. Это обуславливает более высокую вязкость дисперсий Nafion в ДМФА и ДМА по сравнению с водной дисперсией, даже несмотря на двухкратную разницу в содержании полимера (табл. 1). При отливке мембран из дисперсий в ДМФА и ДМА макромолекулы полимера эффективно переплетаются и формируют более связанную полимерную матрицу. Это способствует получению материалов с хорошими механическими свойствами. Кроме того, важна и температура удаления растворителя. Более высокая температура кипения ДМФА и ДМА по сравнению с водой, а также использование Na+ в качестве противоиона при получении дисперсии полимера позволяет формировать пленки при высокой температуре. Это дополнительно способствует увеличению подвижности макромолекул и их запутыванию. Дополнительный небольшой вклад в разницу влагосодержания и проводимости мембран, полученных из дисперсий в воде, ДМФА и ДМА, вносит отличие в составе полимера: ИОЕ мембран Nafion, полученных из водной дисперсии, почти на 10% больше, чем мембран, полученных из дисперсий в ДМФА и ДМА.
Свойства дисперсий Nafion и формируемых из них мембран меняются в результате УЗ обработки. Основными процессами, протекающими при этом с полимером, являются потеря сульфогрупп и разрыв полимерных цепочек. Безусловно, как в случае водной дисперсии, так и для органических растворителей одновременно протекают оба процесса. Высокая доступность сульфогрупп приводит к безусловному доминированию их отщепления при УЗ обработке водной дисперсии Nafion. Возможно, в существенной мере этому способствует и присутствие продуктов сонолиза. Поэтому в данном случае происходит понижение протонной проводимости мембран при высоком влагосодержании. Вместе с тем, при уменьшении влажности до RH = 30% исчезает сетка непрерывных водородных связей и механизм протонного переноса в мембранах частично меняется на прыжковый. Различные кислородсодержащие группы, включая сульфо- и карбоксильные группы могут участвовать в процессе переноса. В этом случае протонная проводимость мембран, полученных из дисперсий после УЗ обработке оказывается значительно выше, чем из исходной водной дисперсии. Изменение вязкости после воздействия ультразвуком может быть следствием разрушения агломератов и изменения молекулярно-массового распределения. Взаимодействие фрагментов макромолекул, возникающих в результате атаки продуктами сонолиза, может приводить к сшивке и увеличению их длины, что выражается в повышении вязкости водной дисперсии Nafion после УЗ обработки. Необратимое уменьшение вязкости дисперсий Nafion в ДМФА и ДМА свидетельствует об уменьшении длины макромолекул. Сильное различие в скорости движения растворителя и клубков макромолекул приводит к тому, что при попеременном сжатии и разряжении в процессе УЗ воздействия происходит разрыв C–C связей основной цепочки (рис. 4). Причем, по данным [40], разрыв происходит не случайным образом, а вблизи от центра макромолекул. Это способствует более эффективной самоорганизации полимерной матрицы и большей связанности системы пор и каналов, в результате чего при небольших временах обработки протонная проводимость мембран повышается. Однако в дальнейшем потеря функциональных групп неизбежно приводит к понижению протонной проводимости и росту неселективного переноса анионов и газопроницаемости через мембраны, которые проявляются в различной степени в зависимости от природы растворителя.
ЗАКЛЮЧЕНИЕ
Исследовано влияние природы диспергирующей жидкости на примере полярных протонных и апротонных растворителей, а также предварительной УЗ обработки на свойства дисперсий и формируемых из них методом отливки мембран Nafion. Морфология полимера в дисперсиях и мембранах меняется в зависимости от растворителя. Влагосодержание и проводимость мембран Nafion, полученных из водной дисперсии, существенно выше, чем из дисперсий в ДМФА и ДМА. Однако из-за формирования в водных дисперсиях обращенных мицелл процесс формирования обращенной матрицы мембраны при удалении растворителя затрудняется, что приводит к получению пленок с низкими механическими свойствами.
УЗ обработка дисперсий полимера приводит к изменению вязкости и химического состава. Наиболее существенные изменения химического состава полимера наблюдаются для водной дисперсии Nafion из-за взаимодействия с продуктами сонолиза воды, что приводит к уменьшению ИОЕ полученных мембран на 10% и снижению их протонной проводимости. При непродолжительной УЗ обработке дисперсий Nafion в ДФМА и ДМА возможно увеличение влагосодержания и протонной проводимости мембран за счет деагломерации макромолекул полимера, что при формировании пленок приводит к улучшению связанности пор и увеличению подвижности носителей заряда.
Выбор состава дисперсий перфторсульфополимеров и условий УЗ обработки и формирования пленок существенно влияет на свойства формируемых методом отливки мембран. Присутствие большого количества воды в дисперсиях негативно сказывается на стабильности мембран и приводит к значительным изменениям состава полимера при УЗ обработке, что нужно принимать во внимание при получении материалов для дальнейшего использования в различных устройствах, в частности, в топливных элементах.
Список литературы
Guerrero Moreno N., Cisneros Molina M., Gervasio D., Pérez Robles J.F. // Renew. Sustain. Energy Rev. 2015. V. 52. P. 897.
Mekhilef S., Saidur R., Safari A. // Renew. Sustain. Energy Rev. 2012. V. 16. P. 981.
Park J.-S., Shin M.-S., Kim C.-S. // Curr. Opin. Electrochem. 2107. V. 5. P. 43.
Сафронова Е.Ю., Ярославцев А.Б. // Мембраны и мембранные технологии. 2016. Т. 6. № 1. С. 3.
Stenina I.A., Yaroslavtsev A.B. // Pure Appl. Chem. 2017. V. 89. P. 1185.
Cao C., Wang H., Liu W., Liao X., Li L. // Int. J. Hydrogen Energy. 2014. V. 39. P. 16110.
Sanginov E.A., Borisevich S.S., Kayumov R.R., Istomina A.S., Evshchik E. Yu, Reznitskikh O.G., Yaroslavtseva T.V., Melnikova T.I., Dobrovolsky Y.A., Bushkova O.V. // Electrochim. Acta. 2021. V. 373. Art. № 137 914.
Воропаева Д.Ю., Новикова С.А., Ярославцев А.Б. // Успехи Химии. 2020. Т. 89. № 10. С. 1132.
Majlan E.H., Rohendi D., Daud W.R.W., Husaini T., Haque M.A. // Renew. Sustain. Energy Rev. 2018. V. 89. P. 117.
Mauritz K.A., Moore R.B. // Chem. Rev. 2004. V. 104. P. 50.
Kusoglu A., Weber A.Z. // Chem. Rev. 2917. V. 117. P. 987.
Haubold H.-G., Vad T., Jungbluth H., Hiller P. // Electrochim. Acta. 2001. V. 46. P. 1559.
Yakovlev S., Downing K.H. // Phys. Chem. Chem. Phys. 2913. V. 15. P. 1052.
Safronova E., Safronov D., Lysova A., Parshina A., Bobreshova O., Pourcelly G., Yaroslavtsev A. // Sensors Actuators B Chem. 2017. V. 240. P. 1016.
Kuwertz R., Kirstein C., Turek T., Kunz U. // J. Memb. Sci. 2016. V. 500 P. 225.
Alberti G., Narducci R., Sganappa M. // J. Power Sources. 2008. V. 178. P. 575.
Collette F.M., Thominette F., Mendil-Jakani H., Gebel G. // J. Memb. Sci. 2013. V. 435. P. 242.
DeBonis D., Mayer M., Omosebi A., Besser R.S. // Renew. Energy. 2016. V. 89. P. 200.
Gao X., Yamamoto K., Hirai T., Uchiyama T., Ohta N., Takao N., Matsumoto M., Imai H., Sugawara S., Shinohara K., Uchimoto Y. // Langmuir. 2020. V. 36. P. 3871.
Примаченко О.Н., Кульвелис Ю.В., Лебедев В.Т., Одиноков А.С., Байрамуков В.Ю., Мариненко Е.А., Гофман И.В., Швидченко А.В., Вуль А.Я., Иванчев С.С. // Мембраны и мембранные технологии. 2020. Т. 10. № 1. С. 3.
Wong C.Y., Wong W.Y., Ramya K., Khalid M., Loh K.S., Daud W.R.W., Lim K.L., Walvekar R., Kadhum A.A.H. // Int. J. Hydrogen Energy. 2019. V. 44. P. 6116.
Tesfaye M., Kushner D.I., Kusoglu A. // ACS Appl. Polym. Mater. 2019. V. 1. P. 631.
Berlinger S.A., Dudenas P.J., Bird A., Chen X., Freychet G., Mccloskey B.D., Kusoglu A., Weber A.Z. // ACS Appl. Polym. Mater. 2020. V. 2. P. 5824.
Karan K. // Curr. Opin. Electrochem. 2017. V. 5. P. 27.
Sharma R., Grahl-Madsen L., Andersen S.M. // Mater. Chem. Phys. 2019. V. 226. P. 66.
Ngo T.T., Yu T.L., Lin H.L. // J. Power Sources. 2013. V. 238. P. 1.
Loppinet B., Gebel G., Williams C.E. // J. Phys. Chem. B. 1997. V. 101. P. 1884.
Welch C., Labouriau A., Hjelm R., Orler B., Johnston C., Kim Y.S. // ACS Macro Lett. 2012. V. 1. P. 1403.
Tarokh A., Karan K., Ponnurangam S. // Macromolecules. 2020. V. 53. P. 288.
Moore R.B., Martin C.R. // Anal. Chem. 1986. V. 58. P. 2569.
Kim Y.S., Welch C.F., Hjelm R.P., Mack N.H., Labouriau A., Orler E.B. // Macromolecules. 2015. V. 48. P. 2161.
Kim Y.S., Welch C.F., Hjelm R.P., Mack N.H., Labouriau A., Orler E.B. // Macromolecules. 2015. V. 48. P. 2161.
Crothers A.R., Radke C.J., Weber A.Z. // J. Phys. Chem. C. 2017. V. 121. P. 28262.
Lin H.-L., Yu T.L., Huang C.-H., Lin T.-L. // J. Polym. Sci. Part B Polym. Phys. 2005. V. 43. P. 3044.
Safronova E.Y., Pourcelly G., Yaroslavtsev A.B. // Polym. Degrad. Stab. 2020. V. 178. Art. № 109229.
Сафронова Е.Ю., Ярославцев А.Б. // Мембраны и мембранные технологии. 2021. Т. 11. № 1. С. 10.
Pollet B.G. // Electrocatalysis. 2014. V. 5. P. 330.
Son Y., Lim M., Ashokkumar M., Khim J. // J. Phys. Chem. C. 2011. V. 115. P. 4096.
Güler E., Elizen R., Vermaas D.A., Saakes M., Nijmeijer K. // J. Memb. Sci. 2013. V. 446. P. 266.
Caruso M.M., Davis D.A., Shen Q., Odom S.A., Sottos N.R., White S.R., Moore J.S. // Chem. Rev. 2009. V. 109. P. 5755.
Дополнительные материалы отсутствуют.
Инструменты
Мембраны и мембранные технологии