Мембраны и мембранные технологии, 2022, T. 12, № 3, стр. 192-199
Высокопрочные керамические подложки на основе перлита и пеносиликатов для фильтрационных мембран
Н. П. Фадеева a, b, М. В. Павлов c, И. А. Харченко a, f, М. М. Симунин d, e, К. А. Шабанова f, В. Ф. Павлов c, И. И. Рыжков a, e, *
a Институт вычислительного моделирования СО РАН
660036 Красноярск, Академгородок 50, стр. 44, Россия
b Институт химии и химической технологии СО РАН
660036 Красноярск, Академгородок 50, стр. 24, Россия
c Специализированное конструкторско-технологическое бюро “Наука” ФИЦ КНЦ СО РАН
660036 Красноярск, Академгородок 50, стр. 45, Россия
d Федеральный исследовательский центр “Красноярский научный центр СО РАН”
660036 Красноярск, Академгородок 50, Россия
e Сибирский федеральный университет
660041 Красноярск, пр. Свободный, 79, Россия
f Институт физики им. Л.В. Киренского ФИЦ КНЦ СО РАН
660036 Красноярск, Академгородок 50, стр. 38, Россия
* E-mail: rii@icm.krasn.ru
Поступила в редакцию 28.12.2021
После доработки 18.01.2022
Принята к публикации 09.02.2022
- EDN: YDUCSB
- DOI: 10.31857/S221811722203004X
Аннотация
Получены образцы двухслойных керамик на основе полидисперсного порошка минерала перлита и пеносиликатов, обладающие высокой прочностью на сжатие до 50 МПа, термической устойчивостью до 1150°С и проницаемостью по воде 272 м3/ч м2 бар. Материал несущей подложки является рентгеноаморфным по данным рентгенофазового анализа. Средний размер пор несущей подложки составляет 40 мкм, а средний размер пор модифицирующего слоя – 17 мкм по данным метода пузырька и электронной микроскопии. Полученные материалы являются перспективными для использования в качестве подложек при создании микро-, ультра- и нанофильтрационных мембран.
ВВЕДЕНИЕ
Пористые керамические материалы находят широкое применение в мембранных технологиях разделения смесей и получения чистых веществ, а также каталитических процессах очистки [1]. Одним из наиболее важных приложений керамических мембран является водоподготовка и очистка сточных вод [2, 3]. По сравнению с полимерными, керамические материалы имеют бóльшую механическую прочность, химическую и биологическую устойчивость, стабильность в широком диапазоне температур и более продолжительный срок службы [4]. Кроме этого, они зачастую характеризуются более узким распределением пор по размеру и большей пористостью.
В баромембранных процессах (микро-, ультра- и нанофильтрация) используются многослойные керамические мембраны, в которых размер пор и толщина слоя уменьшаются при переходе от слоя к слою [5, 6]. В качестве основы (подложки) применяют крупнопористую керамику, на поверхности которой послойно формируют макро- и мезопористые покрытия. Для фильтрационных приложений основными характеристиками подложки являются пористость, механическая прочность и жидкостная проницаемость. Разработка керамических материалов с оптимальным сочетанием указанных свойств является одной из актуальных задач мембранной науки [7].
Ранее в работах [8, 9] были предложены керамические мембраны-подложки на основе порошка марокканского перлита с органическими добавками и водой, обладающие высокой термостойкостью до 1000°С и пористостью до 40%. Нанесение микрофильтрационного слоя методом шликерного литья из более дисперсного порошка перлита позволило добиться высокого сцепления с подложкой. Показано, что полученные мембраны обеспечивали задержание коллоидных красителей, используемых в кожевенной и текстильной промышленности, а также частиц в водных суспензиях, получаемых в процессе резки кремниевых панелей. В работах [10–12] были получены высокопористые проницаемые керамические материалы трубчатой формы с макропористым поверхностным слоем. В качестве исходного материала использовался порошок кристаллического диоксида кремния и применялось алюмосиликатное связующее. Показано, что полученные материалы характеризуются высокой проницаемостью и механической прочностью, гидролитической и кислотной устойчивостью, а также могут эффективно использоваться для удаления ионов трехвалентного железа [13]. Модификация полученных мембран путем нанесения мезопористых селективных слоев с помощью золь-гель метода была осуществлена в работе [14]. Авторы работы [15] разработали методику получения микро- и ультрафильтрационных мембран с использованием суспензий на основе водных и спиртово-водных растворов карбоксиметилцеллюлозы, осаждаемых на алюмосиликатную подложку. Возможность получения нанофильтрационных мембран путем нанесения нанопорошков оксидов титана, алюминия и магния на керамические подложки с макропорами была продемонстрирована в [16]. Методика создания каталитических слоев из оксидов церия и циркония на поверхности трубчатых микрофильтрационных мембранах разработана в [17]. Следует также отметить работу [18], где были получены асимметричные керамические мембраны с промежуточным и активным слоями на основе нановолокон оксида титана и бемита. Использование нановолокнистых материалов приводит к существенному увеличению проницаемости по сравнению с традиционными методиками на основе сферических наночастиц. Симметричные керамические мембраны на основе нановолокон оксида алюминия с проводящим углеродным покрытием были предложены в [19]. Продемонстрирована возможность изменения ионной селективности мембран путем варьирования электрического потенциала, приложенного к проводящей поверхности [20, 21]. Однако, применение подобных технологий в фильтрационных процессах требует размещения проводящего селективного слоя на прочной макропористой подложке.
Целью данной работы является разработка новых типов высокопрочных керамических материалов на основе перлита и пеносиликатов для применения в качестве подложек при создании микро-, ультра- и нанофильтрационных мембран. Выбор исходных материалов обусловлен их высокой термостойкостью, механической прочностью и химической инертностью к слабым кислотам и слабым щелочам. Важным аспектом является коммерческая доступность и распространенность перлита, а также экологичность пеносиликата – материала, полученного в результате переработки техногенного сырья [22, 23]. Проведена характеризация полученных образцов керамик, исследованы их прочностные свойства и проницаемость по воде.
МАТЕРИАЛЫ И МЕТОДЫ
В качестве исходного материала для формирования макропористой подложки использовался перлит следующего химического состава, мас. %: SiO2 – 76.0, Al2O3 – 11.7, Na2O – 2.41, Cl – 0.64, K2O – 6.38, CaO – 1.13, TiO2 – 0.19, Fe2O3 – 1.33. Образцы массой 2 г, диаметром 26 мм и высотой 3 мм были сформованы из полидисперсного порошка перлита фракций 0.315–0.044 мм, прошедших через сита, указанные в табл. 1 при усилии прессования 10 кН на установке ИР-5047-50-03 (ОАО “Точприбор”, г. Иваново). В качестве связующего материала использовалась вода в количестве 5 мас. %. Гранулометрическое распределение частиц порошка определяли методом ситового анализа ГОСТ 9758-86 [24].
Таблица 1.
Распределение масс частиц порошка перлита в граммах по размерам
Размеры ячеек сит, мм | Содержание, мас. %. |
---|---|
+0.315 | 5.0 |
–0.315 + 0.2 | 17.5 |
–0.2 + 0.16 | 19.9 |
–0.16 + 0.1 | 26.2 |
–0.1 + 0.071 | 10.7 |
–0.071 + 0.044 | 9.0 |
–0.044 + 0 | 11.7 |
Обжиг образцов подложек проводили в электропечи типа ВТП 06 М1 00 (ЗАО “ИЭЦ ВНИИЭТО”, г. Истра) при температуре 1100°С с выдержкой 20 мин при заданной температуре в атмосфере печи. Модифицирующий слой пеносиликата наносили накатыванием порошка на подложку с последующей термообработкой при 900°С. Порошок пеносиликата состоял из частиц правильной сферической формы размером 10–20 мкм.
Рентгенофазовый анализ исходного порошка перлита и образцов пористой керамики, полученных после термообработки, проводили на установке ДРОН-3 (АО “ИЦ Буревестник”, г. Санкт-Петербург) с использованием CuKα излучения в диапазоне углов 2Ѳ 10°–70°. Термоаналитические измерения проводились на оборудовании STA-449С компании NETZSCH (Германия) c использованием дифференциально сканирующей калориметрии (DSC) с одновременным измерением изменения массы образца и теплового потока, а также регистрацией масс-спектров выделяемых газов (CO2, H2O).
Структуру поверхности, морфологию, а также линейные размеры элементов микрорельефа сколов пористых образцов керамики оценивали при помощи сканирующего электронного микроскопа Hitachi ТМ4000 Plus (Япония) в режиме обратно отраженных электронов при ускоряющем напряжении 20 кВ. Механическую прочность на сжатие определяли с помощью установки ИР-5047-50-03 на образцах цилиндрической формы диаметром 10 мм и высотой 20 мм по величине давления, при котором происходит их разрушение. Химический состав перлита установили методом рентгенофлуоресцентного анализа на спектрометре Bruker S2 RANGER (Германия).
Открытую пористость материала измеряли по увеличению массы образца при пропитке водой. Размер пор определяли методом пузырька в воде (ГОСТ Р 50516-93) [25]. Максимальный и средний размеры пор рассчитывались по формуле:
Проницаемость мембран измеряли с помощью установки, прокачивающей дистиллированную воду через мембрану. Давление создавалось компрессором, регулировалось с помощью регулятора давления AW20-F01C-A B (SMC, Япония) и контролировалось с помощью прецизионного датчика давления ISE40A (SMC, Япония). Объем воды, прошедшей через мембрану, определяли по весам GX-800 (AND, Япония) (производилась автоматическая запись массы один раз в минуту). Объемный поток (скорость) воды (м3/c м2) рассчитывали по формуле
где $V$– объем воды, прошедшей через мембрану за одну секунду (м3/с), $S$ – площадь мембраны (м2). Для аппроксимации экспериментальной зависимости объемного потока J от приложенной разности давлений ∆p (Па) использовался закон Дарси или его обобщение на случай нелинейной фильтрации (закон Форхгеймера) [26] Здесь $L$ – толщина мембраны, $\mu $ – динамическая вязкость воды, $k$ – коэффициент проницаемости, $\beta $ – константа пористой среды. Закон (2) описывает отклонения от закона Дарси, связанные с проявлением инерционных сил при высоких скоростях фильтрации. Эти отклонения возникают, когда число РейнольдсаВ области применимости закона Дарси проницаемость мембран (м3/ч м2 бар) рассчитывалась по формуле
C учетом (3) закон Дарси (1) можно переписать в виде $J = K\Delta P.$ В расчетах ниже использовались следующие значения параметров: $L = 3$ мм для подложек из перлита и $L = 3.2$ мм для модифицированных подложек, $\mu = 0.89 \times {{10}^{{ - 3}}}$ Па с.
Физические свойства полученных мембран (механическая прочность, пористость, размер пор, проницаемость по воде) исследовались на основе серии из 5 образцов подложек и 5 образцов двухслойных мембран, изготовленных в одинаковых условиях.
РЕЗУЛЬТАТЫ И ОБСУЖДЕНИЕ
Известно, что на пористость керамических материалов существенно влияет температура термообработки [1, 3]. Для определения оптимальной температуры спекания макропористой подложки из перлита был проведен синхронный термический анализ. На кривой ДСК (рис. 1) наблюдаются несколько тепловых эффектов. В области от 300 до 400°С присутствует слабый экзотермический эффект, обусловленный горением углерода с поверхности образца с выделением углекислого газа (кривая m/z 44). Общая потеря массы в этой области температур, равная 3.1%, состоит из потерь углекислого газа и сорбционной воды (кривая m/z 18). Выделение углекислого газа в широкой области температур 700–1150°С вероятно обусловлено выгоранием углерода с внутренней поверхности образца, что, в свою очередь, связано с недостаточной окислительной способностью окружающей среды. Такое поведение сопровождается растянутостью и пологой формой экзотермического эффекта на кривой ДСК. Как следует из рис. 1, область температур 750–850°С соответствует переходу образца в пиропластическое состояние с изменением его теплоемкости. Из данных термоанализа следует, что в области температур 1000–1150°С не наблюдается изменения массы образца, при этом экзо- и эндотермические эффекты также отсутствуют. Это послужило основанием для выбора температуры обжига образцов в указанном диапазоне (1100°С). Из литературных данных [8, 9, 27–29] известно, что при спекании подложек из перлита при температуре более 1000°С происходит резкая, практически полная, потеря пористости образцов. Это может быть связано, во-первых, с использованием различных связующих и добавок, а, во-вторых, обусловлено более мелкодисперсным фракционным составом исходной шихты. В данной работе применение более высокой температуры отжига связано с использованием более крупных фракций исходного порошка перлита в диапазоне 0.315–0.044 мм.
Рис. 1.
Кривые ТГ и ДСК для образцов перлита, совмещенные с масс-спектром выделяющихся при нагревании продуктов (H2O, CO2).
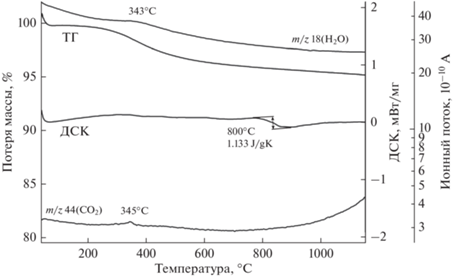
Выбор температуры обжига пеносиликатного слоя обусловлен температурой размягчения пеносиликата в области 750–910°С [30]. В результате спекания при 900°С происходит размягчение пеносиликата, что способствует его хорошей адгезии к подложке. При этом сохраняется сферическая морфология частиц, что позволяет сформировать пористый проницаемый слой (рис. 3б и 3г).
По данным РФА, дифрактограммы образцов перлита до и после отжига при 812°С и 1100°С (рис. 2, кривые 1, 2 и 3 соответственно), не имеют четко выраженных пиков. Таким образом, эти образцы являются рентгеноаморфными.
Рис. 2.
Дифрактограммы образцов перлита до термообработки (кривая 1) и после термообработки при 812°С (кривая 2), 1100°С (кривая 3).
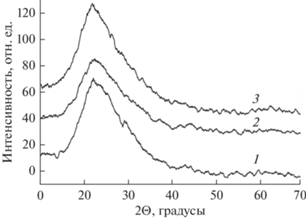
Анализ РЭМ изображений мембран (рис. 3а и 3в) показывает, что зазоры между каркас- образующими частицами подложки расположены относительно равномерно по поверхности образца. Это указывает на однородный характер получаемой пористой структуры. Максимальный размер пор составляет порядка 50 мкм. Кроме того, из представленного снимка видно, что после термообработки наблюдаются многочисленные контакты между частицами. Спекание частиц в жидкофазном состоянии за счет сил поверхностного натяжения без изменения объемного содержания областей твердой фазы свидетельствует о компенсации усадочных явлений при спекании вспениванием образца за счет выделения углекислого газа. Спекание без изменения химического состава частиц, как следует из результатов работы, способствует увеличению прочности пористой керамики.
Рис. 3.
РЭМ изображения поперечного среза (а) и поверхности (в) подложки из перлита, и поперечного среза (б) и поверхности (г) подложки из перлита, модифицированной слоем пеносиликата.
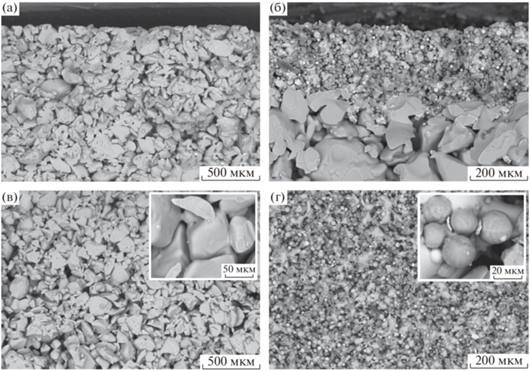
После нанесения на несущие подложки модифицирующего слоя пеносиликата с размером частиц 10–20 мкм достигается равномерное покрытие толщиной около 200 мкм (рис. 3б, 3г), сглаживающее рельеф несущей подложки. В процессе термообработки происходит спекание частиц пеносиликата с образованием пористого слоя.
Данные по измерению размеров пор методом пузырька представлены в табл. 2. Диаметр крупных пор для подложек из пеносиликата составляет 50.1 ± 3.1 мкм, а диаметр средних пор – 39.6 ± ± 3.3 мкм. После модификации подложек пеносиликатом эти значения заметно снижаются и составляют 19.6 ± 0.6 мкм для крупных пор и 16.8 ± ± 0.7 мкм для средних пор, что согласуется с данными электронной микроскопии.
Таблица 2.
Физико-технические характеристики керамических подложек, полученных в данной работе (1, 2) и других работах (3–9)
№ | Материал подложки |
Dмакс, мкм | Dср, мкм | Проницаемость, м3/ч м2 бар | Прочность на сжатие, МПа | Открытая пористость, % | Размер фракции, мкм |
Термо-стойкость, °С |
---|---|---|---|---|---|---|---|---|
1 | Перлит | 50.1 ± 3.1 | 39.6 ± 3.3 | 485 | 50 ± 0.6 | 30 ± 1 | 44–315 | 1150 |
2 | Перлит + слой пеносиликата | 19.6 ± 0.6 | 16.8 ± 0.7 | 272 | 50 ± 0.6 | 29 ± 1 | 44–315, 10–20 |
1150 |
3 | Кварцевый песок [31] | 20.6 | 25.3 | 89 | 5.05 | 26–28 | 200–400 | 850 |
4 | Кварцевый песок + + промежуточный слой [31] | 23.1 | 12.6 | 83 | 2.65 | 26–28 | 200–400, 40–70 |
850 |
5 | Кварцевый песок и 30% доломита [32] | – | 18 | 53.6 | 16.2 | 45 | 0.3–60 | 1400 |
6 | Перлит [27] | – | 13 | 0.01 | 28.9 | 24.53 | <180 | 1025 |
7 | Перлит [8, 9] | – | 6.64 | 1.797 | 1.2 | 41.8 | 200 | 1000 |
8 | Перлит [28] | – | 1.70 | 1.433 | 21.68 | 52.11 | <45 | 950 |
9 | Перлит + бентонит [29] | – | 13 × 10–3 | 0.03 | 21 | 52 | – | – |
Предел прочности мембран на сжатие составляет 50 ± 0.6 МПа для подложек из перлита, в то время как образцы из пеносиликата такого же размера имеют предел прочности до 420 ± 5 МПа в зависимости от усилия прессования. Поскольку прочность изделия, как правило, лимитируется пределом прочности на сжатие наиболее хрупкого слоя, то предполагается, что предел прочности подложек из перлита, модифицированных слоем пеносиликата имеет похожее значение прочности на сжатие и составляет также 50 ± 0.6 МПа. Открытая пористость незначительно уменьшается в результате модификации подложек и составляет 30 ± 1 и 29 ± 1% до и после модификации соответственно.
На рис. 4 приведены зависимости объемного потока воды через полученные керамические мембраны от разности давлений в диапазоне 0.01–2 бар. В области малых давлений (до 0.8 бар) результаты для подложек из перлита хорошо описываются законом Дарси (1) (кривая 1, коэффициент проницаемости $k = 3.6 \times {{10}^{{ - 12}}}$ м2, проницаемость по воде $K = 485$ м3/ч м2 бар), однако с увеличением давления наблюдается отклонение от линейного закона. Зависимость объемного потока от разности давлений во всем рассмотренном диапазоне давлений хорошо описывается законом Форхгеймера (2) с параметрами $k = 5.1 \times {{10}^{{ - 12}}}$ м2 и $\beta = 2$ (кривая 2). Значение числа Рейнольдса, соответствующее объемному потоку воды $J = 366$ м3/ч м2 при разности давлений $\Delta P = $ = 0.8 бар и среднему размеру пор подложки $D = 39.6$ мкм составляет $\operatorname{Re} = 4.03.$ Это значение находится в диапазоне критических значений числа Рейнольдса $\operatorname{Re} = 3 - 10,$ определяющих верхнюю границу применимости закона Дарси [26].
Рис. 4.
Зависимость объемного потока воды от разности давлений для подложки из перлита (кривые 1 и 2) и подложки из перлита, модифицированной слоем пеносиликата (кривая 3).
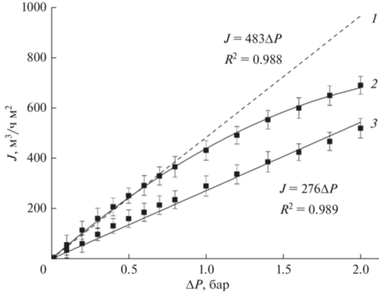
Для подложек, модифицированных слоем пеносиликата, зависимость объемного потока от разности давлений хорошо описывается законом Дарси (кривая 3, коэффициент проницаемости $k = 2.1 \times {{10}^{{ - 12}}}$ м2, проницаемость по воде $K = 272$ м3/ч м2 бар). Таким образом, модификация подложек из перлита слоем пеносиликата приводит к уменьшению жидкостной проницаемости (см. табл. 1). Число Рейнольдса, соответствующее объемному потоку воды при разности давлений $\Delta P = 2$ бар и среднему размеру пор модифицированной подложки $D = 16.8$ мкм, составляет $\operatorname{Re} = 2.36$ и лежит ниже верхней границы применимости закона Дарси.
Для сравнения в табл. 2 приведены характеристики керамических материалов, полученных в работах других авторов. В работе [31] предложены подложки из кварцевого песка с модифицирующим слоем из частиц SiO2. Фракционный состав применяемых материалов близок к использованному в данной работе. Полученные мембраны обладают схожей пористостью и размером пор модифицирующего слоя, но имеют более низкие значения прочности, термостойкости и жидкостной проницаемости. В случае формирования подложек из кварцевого песка и доломита [32] использовалось сырье более дисперсного фракционного состава. Авторам удалось добиться высокой пористости 45% и термостойкости 1400°С. Однако, значения прочности и жидкостной проницаемости были невысокими относительно данной работы. В работе [27] были изготовлены образцы подложек из перлита, имеющего сходный фракционный состав (<180 мкм) и размер пор около 13 мкм, однако существенно меньшее значение водопроницаемости (0.01 м3/ч м2 бар) по сравнению с данной работой. Авторами работы [7] были получены образцы на основе перлита, обладающие высокой пористостью 41.8% и размером пор 6.64 мкм. Они характеризуются относительно низкими значениями прочности и жидкостной проницаемости. Вероятно, эти особенности связаны с применением органических добавок, которые увеличивают пористость, но сильно снижают прочность и проницаемость из-за формирования достаточно узких пор в результате термообработки. В работах [28, 29] получены подложки из перлита с высокой пористостью 52%, достаточно хорошей механической прочностью и низкой водопроницаемостью, которая обусловлена средним размером пор 1.7 мкм. Для синтеза мембран использовалась фракция порошка перлита с размером частиц менее 45 мкм. Далее проводилось нанесение ультрафильтрационного слоя с размером пор порядка 13 нм из бентонитовой глины с последующим использованием полученных мембран для очистки водных растворов от красителей.
ЗАКЛЮЧЕНИЕ
Предложены и отработаны методики получения новых типов высокопрочных и термостойких керамических материалов на основе перлита и пеносиликатов. Установлено, что максимальное значение прочности и пористости имеют подложки, полученные из перлита гранулометрического состава в диапазоне 44–315 мкм с содержанием водного связующего в количестве 5 мас. % и сформованные при усилии прессования 10 кН. Величина пористости после термообработки составляет 30%, а предела прочности на сжатие – 50 МПа. Модификация подложек слоем пеносиликата с размером частиц 10–20 мкм с целью уменьшения размера пор и сглаживания рельефа подложек не приводит к снижению пористости и прочности образцов. Показано, что нанесение модифицирующего слоя вызывает снижение водопроницаемости подложек с 485 до 272 м3/ч м2 бар, что объясняется уменьшением размеров сквозных пор почти в два раза. Зависимость объемного потока от разности давлений в диапазоне до 2 бар для модифицированных подложек хорошо описываются законом Дарси, в то время как для подложек из перлита наблюдаются отклонения от этого закона при давлениях, превышающих 0.8 бар.
По сравнению с аналогичными материалами, представленными в литературе, разработанные керамики характеризуются более высокой проницаемостью по воде, прочностью на сжатие и термической устойчивостью. Полученные материалы могут быть использованы в качестве основы при создании микро-, ультра- и нанофильтрационных мембран.
Работа выполнена с использованием оборудования Красноярского регионального центра коллективного пользования ФИЦ КНЦ СО РАН. Работа частично поддержана грантом РФФИ 18-29-19078. Авторы выражают благодарность к. ф. м. н. Л.С. Тарасовой за выполнение термоанализа образцов, полученных в данной работе, и д. х. н. А.И. Иванцу за обсуждение результатов и полезные замечания.
Список литературы
Li K. Ceramic membranes for separation and reaction. John Wiley & Sons. Chichester. England. 2007. 316 p.
Гороховский А.В., Третьяченко Е.В., Гоффман В.Г. и др. // Стекло и керамика. 2011. № 6. С. 20–23.
Arumugham T., Kaleekkal N.J., Gopal S. et al. // J. Environmental Management. 2021. V. 293. 112925.
Gitis V., Rothenberg G. Ceramic membranes: new opportunities and practical applications. Wiley-VCH. Weinheim. Germany. 2016. 396 p.
Almandoz M.C., Pagliero C.L., Ochoa N.A. et al. // Ceram Int. 2015. V. 41. P. 5621–5633.
Гармаш И.П., Крючков Ю.Н., Павликов В.Н. // Стекло и керамика. 1995. Т. 6. С. 19–22.
Zhang X., Bai C., Qiao Y. et al. // Composites Part A: Applied Science and Manufacturing. 2021. V. 150. 106 629.
Majouli A., Alami Younssi S., Tahiri S. et al. // Desalination. 2011. V. 277. P. 61–66.
Majouli A., Tahiri S., Alami Younssi S. et al. // Ceramics International. 2012. V. 38. P. 4295–4303.
Ратько А.И., Иванец А.И., Азарова Т.А. и др. // Защита металлов. 2008. Т. 44. № 2. С. 217–222.
Ратько А.И., Иванец А.И., Степанова Е.А. и др. // Физикохимия поверхности и защита материалов. 2009. Т. 45. № 2. С. 222–227.
Иванец А.И., Агабеков В.Е. // Мембраны и мембранные технологии. 2017. Т 7. № 1. С. 3–13.
Ратько А.И., Иванец А.И., Сахар И.О. и др. // Физикохимия поверхности и защита материалов. 2012. Т. 48. № 5. С. 470–473.
Ратько А.И., Иванец А.И., Кузнецова Т.Ф. и др. // Физикохимия поверхности и защита материалов. 2010. Т. 46. № 2. С. 195–198.
Салихов Т.П., Кан В.В., Уразаева Э.М. и др.// Стекло и керамика. 2014. № 8. С. 22–27.
Аверина Ю.М., Курбатов А.Ю., Сахаров Д.А. и др.// Стекло и керамика. 2020. № 3. С. 22–27.
Гаврилова Н.Н., Назаров В.В., Ситник А.С. и др.// Стекло и керамика. 2015. № 7. С. 11–15.
Ke X.B., Zhu H.Y., Gao X.P. et al. // Advanced Materials. 2007. V. 19. P. 785–790.
Лебедев Д.В., Шиверский А.В., Симунин М.М. и др. // Мембраны и мембранные технологии. 2017. Т. 7. № 2. С. 86–98.
Лебедев Д.В., Солодовниченко В.С., Симунин М.М. и др. // Мембраны и мембранные технологии. 2018. Т. 8. № 3. С. 157–165.
Ryzhkov I.I., Shchurkina M.A., Mikhlina E.V. et al. // Electrochimica Acta. 2021. V. 375. 137970.
Павлов В.Ф., Шабанов В.Ф. // Экология и промышленность России. 2018. Т. 22. № 12. С. 14-18.
Tsybulskaya O.N., Ksenik T.V., Yudakov A.A. et al. // Environmental Technology & Innovation. 2021. V. 23. 101 567.
ГОСТ 9758-86. Заполнители пористые неорганические для строительных работ. Методы испытаний. М.: Стандартинформ. 2006.
ГОСТ Р 50516-93. Мембраны полимерные. Метод определения точки пузырька плоских мембран. М.: Издательство стандартов. 1993.
Басниев К.С., Дмитриев Н.М., Розенберг Г.Д. Подземная гидромеханика. М., 2005.
Al-Harbi O.A., Özgur C., Khan M.M. // J. Ceramic Processing Research. 2016. V. 17. № 4. P. 275–280.
Saja S., Bouazizi A., Achiou B. et al. // J. Environmental Chemical Engineering. 2018. V. 6. № 1. P. 451–458.
Saja S., Bouazizi A., Achiou B. et al. // J. European Ceramic Society. 2020. V. 40. № 6. P. 2453–2462.
Павлов В.Ф., Шефер А.А., Шабанов В.Ф. // Физика и химия стекла. 2008. Т. 34. № 4. С. 610–615.
Ivanets A.I., Azarova T.A., Agabekov V.E. et al. // Ceramics International. 2016. V. 42. P. 16571–16578.
Kadiri C., Harabi A., Bouzerara F. et al. // J. Aust. Ceram Soc. 2020. V. 56. P. 379–387.
Дополнительные материалы отсутствуют.
Инструменты
Мембраны и мембранные технологии