Мембраны и мембранные технологии, 2022, T. 12, № 4, стр. 264-275
Испарительно-экстракционный мембранный процесс извлечения лития из соляных озер
Д. О. Калмыков a, *, С. В. Макаев a, Г. С. Голубев a, А. В. Волков a
a Федеральное государственное бюджетное учреждение науки Ордена Трудового Красного Знамени
институт нефтехимического синтеза им. А.В. Топчиева Российской академии наук
119991 Москва, Ленинский пр., 29, Россия
* E-mail: denis.kalmykov@ips.ac.ru
Поступила в редакцию 14.03.2022
После доработки 01.04.2022
Принята к публикации 08.04.2022
- EDN: AEQQQM
- DOI: 10.31857/S2218117222040058
Аннотация
В данной работе исследован процесс пленочной дистилляции с пористой конденсирующей поверхностью (ПД-ПКП) применительно к задачам концентрирования литийсодержащих растворов. Концентрирование растворов является частью трехступенчатого цикла извлечения лития, включающего размягчение рассола путем осаждения катионов Ca2+/Mg2+ карбонатом натрия (рассчитанный в PHREEQC), за которым следует интегрированная система, состоящая из установки мембранной дистилляции, кристаллизатора (осаждение NaCl) и мембранной экстракции (извлечение Li+). Были исследованы потоки производительности пленочного дистилляционного модуля 4.15–7.49 кг/м2 ч при 60 и 80°С нагрева поверхности испарения (соответственно). Комплексная работа трехступенчатой системы была смоделирована в Simulink/MATLAB. Моделирование процесса, основанное на экспериментальных и литературных данных, показало более высокую эффективность пленочной дистилляции с пористой конденсирующей поверхностью в сравнении с мембранной дистилляцией с пористой конденсирующей поверхностью (4.2 кг лития против 1.4 кг за два месяца стационарной работы системы).
ВВЕДЕНИЕ
Начало XXI в. характеризуется стремительным развитием электронных технологий, что привело к резкому увеличению потребления редких и ценных материалов, в том числе лития [1]. За последние два десятилетия производство лития выросло более чем в 5 раз и составило 82000 т в год [2]. Благодаря низкой молярной массе (6.94 г/моль), низкой плотности (0.53 г/см3) и высокому электрохимическому потенциалу (3.04 В) литий пользуется большим спросом в керамической и стекольной промышленности (~14% лития, произведенного в 2020 г.), в производстве смазочных материалов (~4%), в производстве полимерных материалов (~2%), в металлургической промышленности, медицине, очистке воздуха и ядерной энергетике [2–5]. Однако основное применение лития – это литий-ионные аккумуляторы (~71%) для электромобилей, электронных устройств и накопителей энергии, спрос на которые растет с каждым годом [2].
На сегодняшний день общие запасы лития оцениваются в 86 млн тонн [2], причем большая их часть содержится в рассолах (более 60%) [6–8]. К таким рассолам относятся соленые озера, горячие геотермальные воды и рассолы нефтяных месторождений. Соленые озера в основном расположены в Южной Америке (Чили, Боливия и Аргентина) [6], а также в очень засушливых районах Китая [6], где общая соленость колеблется от 320 до 470 г/л (табл. 1) [9, 10]. В соленых озерах литий находится в смеси с большим количеством хлорида натрия или хлорида магния [11], в то время как основными анионами в рассоле являются хлор, карбонаты, сульфаты, и в дополнение к катионам натрия и лития также присутствуют калий, магний и кальций [12]. Высокая соленость, наличие ионов жесткости и высокое соотношение магний/литий (из-за сходства ионных свойств) приводят к трудности извлечения лития из соляных рассолов [12]. Экстракция, мембранная экстракция, кристаллизация, осаждение, ионообменная адсорбция или комбинация этих методов могут быть использованы для извлечения лития из рассолов. Из представленных выше методов наиболее широко используются экстракция и ионная адсорбция [6, 8, 13]. Хотя экстракция является перспективным методом производства лития, но она не лишена недостатков, таких как осуществление дополнительной стадии очистки экстрагента, возможные потери целевого вещества, а также при использовании органических реагентов могут возникнуть проблемы, связанные с загрязнением окружающей среды [14]. Для низких концентраций лития может быть использован метод ионообменной адсорбции, где в качестве адсорбентов выступают ионные сита, содержащие титан и марганец, но их адсорбционная способность со временем значительно снижается из-за блокирования ионных каналов [15], что требует их регенерации или замены.
Таблица 1.
Ионы | Концентрация ионов, г/л | ||
---|---|---|---|
Дун-Тайджнар-Нур | Си-Тайджнар-Нур | Дабсан-Нур | |
Li+ | 0.14 | 0.26 | 0.35 |
Mg2+ | 5.64 | 15.36 | 115.2 |
Na+ | 117 | 102.4 | 1.89 |
K+ | 3.79 | 8.45 | 0.78 |
Ca2+ | 0.43 | 0.20 | 0.04 |
B+ | – | – | 0.39 |
S${\text{O}}_{4}^{{2 - }}$ | – | – | 11.62 |
Cl– | 202 | 212 | 334.8 |
Общее содержание солей | 329 | 338.7 | 465.1 |
Среди методов извлечения лития особый интерес представляет метод мембранной экстракции. Его существенными преимуществами являются модульность, отсутствие прямого контакта водной и органической фаз, что предотвращает потерю экстрагента и снижает негативное воздействие на окружающую среду [13, 16]. Для реализации этого метода в литературе используются мембраны на основе этиленвинилового спирта (EVAL), которые демонстрируют высокие разделительные характеристики и селективность. Однако, было показано, что данные мембраны разрушаются при длительном воздействии соляной кислоты [16]. Для решения этой проблемы было предложено использовать устойчивую к кислотам и растворителям мембрану на основе полиэфирэфиркетона (ПЭЭК), что позволило системе сохранять стабильную производительность в течение более 500 ч [17]. Установлено, что максимальная эффективность мембранного контактора достигается при высоких концентрациях лития в исходном растворе (более 2 г/л). Поэтому необходима стадия предварительного концентрирования соляных рассолов.
Для решения задач в области опреснения, очистки и концентрирования водных растворов используется метод мембранной дистилляции (МД). Данный метод демонстрирует высокие потоки, 100% селективность по растворенным солям и способность работать с высококонцентрированными растворами при атмосферном давлении благодаря гидрофобным свойствам мембран [18, 19]. Наиболее подходящей для решения этих задач является конфигурация МД с воздушным зазором из-за низких тепловых потерь [20]. Этот метод уже продемонстрировал свою эффективность в случае концентрирования ионов лития в геотермальных рассолах с 0.14 до 2 г/л [21]. Однако данный процесс не лишен недостатков, в частности, при работе с насыщенными растворами мембраны быстро засоряются, что приводит к снижению производительности. В продолжении развития процесса МД с воздушным зазором недавно был предложен новый метод – пленочной дистилляции с пористой конденсирующей поверхностью (ПД-ПКП) [22], где пористая часть выступает в качестве поверхности для конденсации водяного пара и границы раздела между воздушным зазором и контуром охлаждающей жидкости. Водяной пар конденсируется на пористой поверхности и далее проходит через поры в контур с охлаждающей жидкостью. Такая реализация процесса позволяет получить высокую эффективность процесса независимо от количественного и качественного состава солей в концентрате. Кроме того, данный подход обладает такими преимуществами, как низкая металлоемкость и малая энергоемкость, достигаемая за счет применения низкопотенциального (“бросового”) тепла в качестве движущей силы процесса и проведения процесса при атмосферном давлении.
Ожидается, что объединение процессов предварительной обработки (ПД-ПКП) и экстракции лития (мембранная экстракция) позволит создать завершенный цикл производства лития от соляного рассола до хлорида лития. Но перед внедрением этого цикла в лабораторных и промышленных масштабах необходимо проведение первичных экспериментов и последующего моделирования всего процесса в целом, чтобы обеспечить возможность комбинирования этих методов, а также рассчитать производительность и оптимизировать в дальнейшем условия процесса. Поэтому в данной работе были проведены эксперименты по концентрированию модельных растворов, содержащих соли лития, при варьировании рабочих параметров ПД-ПКП процесса. Кроме того, была смоделирована работа процесса извлечения лития из соляных рассолов с использованием программного обеспечения Simulink (дополнение к MATLAB). Процесс обработки рассола можно разделить на три этапа: 1) удаление солей жесткости путем добавления карбоната натрия; 2) концентрирование обработанного соляного рассола методом ПД-ПКП; 3) извлечение лития методом мембранной экстракции. Важно отметить, что на этапе концентрирования солевого раствора необходимо проводить также кристаллизацию избыточных побочных солей (NaCl). Данная операция обусловлена высоким исходным содержанием данных солей в обрабатываемом растворе, что приводит к скорому насыщению раствора по данной соли во время дистилляции. Избыточная соль начинает осаждаться на составных элементах (испаряющая поверхность, стенки баков), а также в фитингах и коммуникационных трубках, что приводит к засорению и выходу системы из строя. Таким образом, целью данной работы в рамках Российско-Китайского проекта является моделирование многоступенчатого процесса извлечения лития из соленых озер в Китае.
ЭКСПЕРИМЕНТАЛЬНАЯ ЧАСТЬ
Обрабатываемый раствор
В настоящей работе был рассмотрен рассол из соленых озер Си-Тайджнар-Нур с составом, представленным в табл. 1. Данный раствор был выбран в связи с более высоким, относительно других рассматривавшихся рассолов, содержанием ионов лития, а также отсутствием ионов бора и сульфат-анионов. В ходе исследования были проведены эксперименты с многокомпонентными модельными растворами, как с исходным содержанием солей, так и с рассчитанным после предварительной обработки карбонатом натрия. Солесодержание в растворе косвенно определяли по значению электропроводности раствора. Электропроводность измеряли с помощью портативного кондуктометра WTW Cond 3210 с ячейкой WTW TetraCon 325. Текущее солесодержание определяли по электропроводности с применением градуировок χ $\sim f\left( c \right)$. Концентрация ионов в многокомпонентных растворах определялась методом ионной хроматографии (хроматограф “Стайер-М” с детектором CD 510, катионообменная колонка Shodex ICSI-50 4E. Точность измерений по электропроводности 0.1%).
Пленочная дистилляция с пористой конденсирующей поверхностью
Лабораторная установка пленочной дистилляции с пористой конденсирующей поверхностью, используемая для концентрирования водных растворов солей, ранее была подробно описана в патенте [23] и работе Голубева и др. [23, 24]. Исходный солевой раствор циркулировал в модуле пленочной дистилляции при температуре 60 или 80°C со скоростью потока 0.012 м/с. Температура охлаждающей жидкости (дистиллированной воды) в контуре хладагента/пермеата, содержащего пористую конденсирующую поверхность, поддерживалась на уровне 15°C (расход 0.3 л/мин). Модуль пленочной дистилляции был оснащен пластиной из нержавеющей стали с припаянной полиэтиленовой сеткой, обеспечивающей растекание обрабатываемого раствора по поверхности испарения. Параметры сетки: 290 × 70 мм; толщина 1.7 мм; форма ячеек ромбовидная, диагонали 3.5 × 4.0 мм; большая диагональ располагается вдоль движения потока. Оценка рабочей площади испаряющей поверхности проводилась по фотографиям сделанных при помощи тепловизора (Thermal Expert TE-Q1). С использованием программного обеспечения Gwyddion [25] производился расчет площади поверхности, заполненной горячим раствором. На рис. 1 представлен пример оценки площади испаряющей поверхности. Пористая конденсирующая поверхность, толщиной 200 мкм и пористостью 30%, была изготовлена из спеченной нержавеющей стали (ООО “ВМЗ-Техно”, Москва, Россия). Воздушный зазор между испаряющей пластиной и пористой конденсирующей поверхностью был установлен равным 5 мм. Принципиальная схема установки показана на рис. 2.
Рис. 1.
Определение площади поверхности испарения при помощи программного пакета Gwyddion. Область повышенной температуры отмечена красным цветом. На шкале сверху и слева размещена линейка (в метрах), шкала справа описывает “глубину” участков изображения, что в данном случае отражает степень нагрева области горячим раствором.
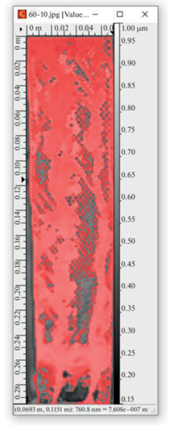
Моделирование этапа предварительной обработки рассола с помощью PHREEQC
Предварительная обработка позволяет удалить ионы кальция и магния из геотермального рассола путем осаждения кальциевых и магниевых солей. Ионы магния сильно влияют на эффективность извлечения лития [28]. Удаление кальция и магния уменьшает массу раствора, снижает энергию, необходимую для нагрева, и увеличивает концентрацию лития. Одним из самых популярных программных средств для геохимических расчетов воды является PHREEQC [26]. Программный расчет проводится с использованием встроенных баз данных. В данной работе для расчета использовалась база, основанная на модели Питцера, так как эта модель используется при расчетах насыщенных и концентрированных растворов солей. Первоначально при помощи PHREEQC была рассчитана плотность модельного литийсодержащего рассола (1215.7 кг/м3 для соленого озера Си-Тайджнар-Нур), молярность и массовые доли компонентов. Затем расчет был использован для определения изменения концентрации ионов в растворе с добавлением кальцинированной соды (рис. 3). При расчете учитывалось парциальное давление CO2, равное содержанию углекислого газа в атмосфере (0.4%).
Моделирование в Simulink/MATLAB процессов пленочной дистилляции и мембраной экстракции лития с сопутствующей кристаллизацией солей
Интегрированные операции мембранной дистилляции и кристаллизации соли были смоделированы с использованием нескольких подсистем в Simulink/MATLAB. Более подробно связь системы дистилляционного модуля с кристаллизующей частью рассматривалась ранее в работе [21]. Солевой раствор подавался в резервуар с системой нагрева, обеспечивающей требуемую температуру, и эта температура поддерживалась системой в пределах ±1°C. Горячий солевой раствор подавался на модуль пленочной дистилляции с пористой конденсирующей поверхностью, где часть воды испарялась, а затем часть раствора (~6 кг/ч) подавалась в кристаллизатор, где после охлаждения до 20°C из раствора осаждалось соответствующее количество соли (NaCl). Оставшийся горячий раствор возвращался обратно из модуля пленочной дистилляции в резервуар с системой нагрева. Кристаллизатор, содержащий 9 кг раствора, считался черным ящиком, предполагая, что был осажден избыток солей, превышающий концентрацию насыщения при 20°C. Время кристаллизации 10 мин было взято из расчета кинетики кристаллизации хлористого натрия в работах [27, 28]. Раствор соли возвращался обратно в резервуар с системой нагрева после кристаллизатора. Основной целью модуля пленочной дистилляции было концентрирование лития до необходимого уровня, достаточного для его эффективного извлечения мембранной экстракцией, т.е. 2 г/л [16, 17, 29].
Код Simulink для подсистемы модуля пленочной дистилляции, которая вычисляет количество растворителя (воды), выпаренного из раствора соли, на основе ряда параметров можно описать уравнением (1). Количество воды, выпаренной из раствора соли за определенное время, кг/мин, можно описать следующим образом:
(1)
$m = J\left( {{{T}_{f}}} \right)SK \times {1 \mathord{\left/ {\vphantom {1 {60}}} \right. \kern-0em} {60}},$(2)
$J\left( {{{T}_{f}}} \right) = 0.0013T_{f}^{2}{\text{\;}} - {\text{\;}}0.0078{{T}_{f}}{\text{\;}} + {\text{\;}}0.1103.$Пленочный дистилляционный модуль использовался один раз в течение 4.5 ч до промывки поверхности испарения (0.5 ч). Внутренняя работа системы была смоделирована с использованием хорошо известного принципа пропорционально-интегрально-дифференциального (ПИД) управления. Simulink выполняет вычисления на основе входных сигналов на каждом этапе, что позволяет избежать необходимости предварительного определения математического описания для долгосрочной работы всей системы.
РЕЗУЛЬТАТЫ И ИХ ОБСУЖДЕНИЕ
Моделирование процесса предварительной подготовки рассола в системе PHREEQC
В случае китайских рассолов, в которых содержание лития колеблется от 0.14 до 0.35 г/л (табл. 1), для эффективной работы мембранного экстрактора потребуется концентрирование обрабатываемого раствора в 6–15 раз, что вызовет образование кристаллов на стенках оборудования. Это обусловлено высоким содержанием солей жесткости (бикарбонатов, сульфатов и хлоридов кальция (Ca(HCO3)2, CaSO4, CaCl2) и магния (Mg(HCO3)2, MgSO4, MgCl2)) в подаваемом рассоле (более 50 г/л). Образование отложений солей на внутренних стенках оборудования приведет к снижению производительности установки, ухудшению теплопередачи и уменьшению проходного сечения системы, увеличивая ее гидравлическое сопротивление [30]. Бороться с выпадением солей жесткости можно путем добавления специальных реагентов (антискалантов), например, соды (Na2CO3) [30]. Повышенное количество карбонат-ионов (CO3) в воде приводит к образованию плохо растворимого карбоната кальция (CaCO3), что уменьшает солеобразование на поверхности установки [31].
На рис. 3 показаны результаты моделирования осаждения катионов Mg2+ и Ca2+ с использованием соды. При добавлении ~0.3 моль/кг Na2CO3 (т.е. суммы молярностей Mg2+ и Ca2+ в исходном растворе) для раствора Си-Тайджнар-Нур концентрация Mg2+ и Ca2+ резко снижается. Дальнейшее выщелачивание не приводит к большим изменениям и его проведение нецелесообразно. Аналогичные результаты были получены при моделировании рассолов Си-Тайджнар-Нур (рис. 3). Таким образом, количество добавленного Na2CO3 было равно сумме молярностей Mg2+ и Ca2+ с превышением 1% (0.73 моль/кг для рассола Си-Тайджнар-Нур), что привело к снижению концентрации Mg2+ и Ca2+ до ~10–4 мас. % (табл. 2). Во время выщелачивания модельного раствора Na2CO3 концентрация NaCl превышает предел его растворимости, и он также начинает выпадать в осадок, что объясняет снижение молярности Cl– во время обработки (рис. 3). Следует также отметить, что молярность Li+ остается неизменной при выщелачивании, но массовая концентрация увеличивается за счет уменьшения плотности и общего веса раствора.
Таблица 2.
Состав модельных рассола Си-Тайджнар-Нур после обработки Na2CO3
Вещество | Li+ | NaCl | Mg2+ + Ca2+ | H2O |
---|---|---|---|---|
Моляльность, моль/кг воды | 0.042 | 6.129 | 10–5 | 55.51 |
Концентрация, мас. % | 0.0215 | 26.4 | 5 × 10–4 | 73.59 |
В результате расчетов был получен раствор, насыщенный NaCl при комнатной температуре (~26.4 мас. %) и с общим содержанием Mg2+ и Ca2+ ~ 10–4 мас. %, который использовался в качестве питающего потока в расчетах Simulink (табл. 2). Из-за низкого содержания катионов Mg2+ и Ca2+ они не были учтены при расчете, но очевидно, что их содержание в растворе постепенно увеличивалось, что могло привести к их выпадению в осадок. Термодинамическое моделирование не было целью данной статьи, поэтому было сделано упрощение для дальнейшего моделирования Simulink. Раствор обрабатывали содой после каждых 500 кг выпаренной воды до достижения концентрации Li+ 1 г/л, а затем дополнительно подкисляли соляной кислотой, поскольку снижение рН значительно увеличивает растворимость карбонатов.
Исследование процесса пленочной дистилляции при концентрировании рассолов
В табл. 3 указан состав модельного раствора, подготовленного на основе данных, представленных в табл. 2 [9]. Полученный раствор концентрировали на установке ПД-ПКП при температуре 60°С (температура холодного контура – 15°С). Результаты эксперимента представлены на рис. 4.
Таблица 3.
Содержание солей в обрабатываемом модельном растворе
Соединение | Концентрация, г/кг раствора |
---|---|
LiCl | 1.16 |
MgCl2·5H2O | 93.43 |
NaCl | 189.45 |
KCl | 11.69 |
CaCl2 | 0.40 |
Общее содержание солей | 296.13 |
Рис. 4.
Графики зависимости массы смеси солей и раствора (а) и потока испарения (б) при обработке солевого раствора от времени проведения эксперимента.
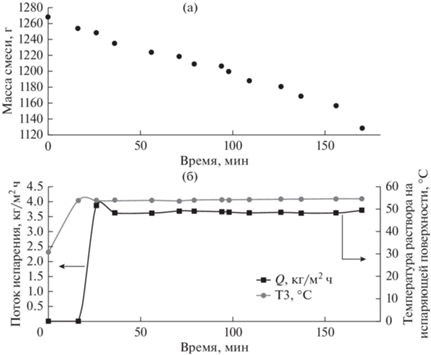
С учетом оценки площади поверхности испарения (S = 110.3 см2) производительность пленочного дистилляционного модуля составила 3.71 кг/м2 ч. При этом общее время проведения эксперимента составило 218 мин, после чего процесс был остановлен, что связано с засаливанием и засорением составных элементов установки, в частности, трубок и фитингов. Концентрация лития при этом возросла с 0.019 до 0.021 мас. %. Засорение связано с содержанием большого количества солей (в том числе солей жесткости) в растворе и потенциально препятствует промышленной обработке подобных солевых растворов. При этом стоит обратить внимание на стабильности потока испарения, что свидетельствует о незначительной зависимости производительности ПД модулей от засорения поверхности. Таким образом, по результатам эксперимента не было выявлено никаких особенностей и отличий при работе системы от теоретических предположений.
При проведении дальнейших экспериментов использовался модельный раствор, близкий по составу к расчетному (табл. 2). При этом, учитывая значительную разницу между концентрациями NaCl (26.4 мас. %) и суммарной концентрацией Mg2+ и Ca2+ (5 × 10–4 мас. %), а также на основании предполагаемой технологии проводимой предварительной обработки раствора Na2CO3, при проведении дальнейших экспериментов Mg2+ и Ca2+ не добавлялись.
При оценке эффективности работы дистилляционного модуля наиболее важной величиной является производительность модуля, измеряемая в килограммах обрабатываемого раствора на квадратный метр поверхности испарения в час. Для определения данного параметра необходимо экспериментально вычислить поток испарения. Для модельного раствора, состав которого представлен в табл. 2 на описанной выше установке (см также [21]) были проведены дистилляционные эксперименты, позволившие оценить поток производительности для данного модуля (рис. 5).
Рис. 5.
Графики зависимости потоков испарения в процессе обработки солевого раствора при температуре нагрева испаряющей поверхности 80°С (а) и 60°С (б).
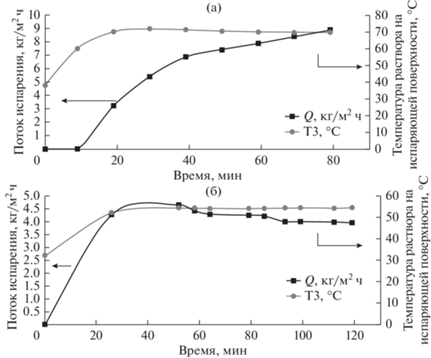
Для представленных случаев производительность составила 7.49 кг/м2 ч для температуры нагрева поверхности испарения до 80°С и 4.15 кг/м2 ч для температуры нагрева поверхности испарения до 60°С. Разница во времени проведения эксперимента связана с тем, что при больших потоках испарения при прочих равных исходных условиях процесс насыщения раствора происходит быстрее. При этом концентрация лития в первом случае возросла с 0.024 до 0.027 мас. %, а вот втором случае с 0.030 до 0.034 мас. %. На основании данных потоков было проведено моделирование трех стадийной установки в системе Simulink MatLab.
Моделирование в системе Simulink
Для оценки эффективности работы трех стадийной системы обработки рассола, включающей стадии предварительной обработки, концентрирования и экстракции лития из рассолов озера Си-Тайджнар-Нур, было проведено моделирование работы всего процесса в целом в системе Simulink MatLab. Модель, используемая для расчета, была аналогична системе, представленной в более ранних работах [21]. При этом система считалась вышедшей на режим с момента достижения концентрации лития установленной концентрации (5 г/кг), при которой начинается экстрагирование лития из системы. Моделирование ограничивалось по времени двумя месяцами работы системы после выхода на режим.
Иллюстративное представление стационарной работы системы представлены на рис. 6.
Рис. 6.
Значение потоков испарения, сброса и экстракции при работе системы в стационарном режиме. Режим моделирования: два месяца работы после выхода на стационарный режим, концентрирование Li+ до 5 г/кг, температура хладагента 15°C, площадь испарителя 2.5 м2.
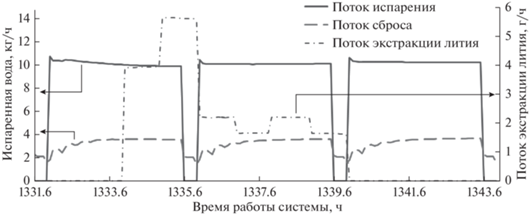
На основании предварительного расчета площадь мембранного модуля была установлена равной 2.5 м2. Температура подаваемого раствора варьировалась в пределах от 50 до 80°C. Согласно полученным экспериментальным данным производительность пленочного дистилляционного модуля не зависела от засорения испаряющей поверхности. Важно уточнить, что одним из основных недостатков процесса МД является засорение мембраны кристаллизующейся солью, причем при восстановлении (очистке) мембран не происходит полного восстановления исходных потоков испарения. Для сравнения предложенной в данной работе системы на основе ПД-ПКП с ранее опубликованной МД-ПКП, моделировалась периодическая промывка испаряющей поверхности дистиллированной водой, однако в отличие от мембранных модулей при пленочной дистилляции отсутствовало снижение потока во время засорения. При этом после очистки поток восстанавливается полностью на исходные показатели. Таким образом, в пленочной дистилляционной системе отсутствует параметр “степени восстановления” (“recovery ratio”) и, следовательно, необходимость в замене каких-либо элементов. Поток испарения и сброса избыточных побочных солей (NaCl), а также изменение экстракции лития изображены на рис. 6. Периодические остановки соответствуют промывке испаряющей поверхности. Продолжительность промывки зависела от температуры испаряющей поверхности и варьировалась от 176 до 236 мин. Также это было связано с дополнительным временем, необходимым для обработки раствора Na2CO3 и осаждения солей жесткости.
Для определения зависимости производительности системы от температуры было проведено моделирование работы системы при различных температурах испаряющей поверхности: при 50, 60, 70 и 80°С. Результаты моделирования представлены в табл. 4.
Таблица 4.
Результаты моделирования для различных температур испаряющей поверхности. Условия моделирования: S = 2.5 м2, C(Li+) = 5 г/кг, доля экстрагируемого Li+ = 90%, два месяца после выхода на режим
Температура испаряющей поверхности,°C | Выход на режим | Два месяца работы в режиме | ||||
---|---|---|---|---|---|---|
общее время работы системы, ч | время выхода на режим, ч | извлеченный литий, кг | испаренная вода, кг | осажденная соль, кг | масса раствора, проведенного через экстрактор, кг | |
50 | 1682 | 242 | 2.5 | 9322 | 3313 | 1341 |
60 | 1605 | 165 | 3.7 | 13 553 | 4828 | 1910 |
70 | 1555 | 115 | 5.0 | 18 596 | 6634 | 2553 |
80 | 1535 | 95 | 6.7 | 24 455 | 8732 | 3289 |
Хорошо заметна зависимость массы извлеченного лития от температуры испаряющей поверхности (2.5 кг за два месяца работы при 50°C и 6.7 кг при 80°C), что позволяет говорить о большей эффективности процесса пленочной дистилляции при более высоких температурах нагрева испаряющей поверхности. Однако стоит также заметить, что при высоких температурах скорость испарения стекающего по поверхности раствора будет выше, что может привести к засаливанию поверхности испарения. При этом установку придется чаще останавливать для промывки.
Немаловажно также сравнить результаты моделирования для одной и той же системы при различных дистилляционных модулей. Для этого было проведено сравнение результатов моделирования для модуля мембранной дистилляции и равного ему по площади модуля пленочной дистилляции. Для этого было проведено моделирование трех стадийного процесса при условиях, рассматривавшихся в работе [21] для шахты “Удачная” республики Саха, Якутия. Результаты сравнения представлены в табл. 5.
Таблица 5.
Результаты моделирования для мембранной дистилляции с воздушным зазором и пленочной мембранной дистилляции. Условия моделирования: Тнагрева = 60°С, S = 2.5 м2, C(Li+) = 2.3 г/кг, доля экстрагируемого Li+ = 90%, два месяца после выхода на режим
Тип дистилляции | Выход на режим | Два месяца работы в режиме | ||||
---|---|---|---|---|---|---|
общее время работы системы, ч | время выхода на режим, ч | извлеченный литий, кг | испаренная вода, кг | осажденная соль, кг | масса раствора, проведенного через экстрактор, кг | |
ПД-ПКП без промывки | 1587 | 147 | 4.2 | 17 063 | 6074 | 2217 |
ПД-ПКП с промывкой | 1605 | 165 | 3.7 | 15 083 | 5373 | 1910 |
МД-ПКП | 1907 | 467 | 1.4 | 2996 | 1068 | 650 |
Данные результаты наглядно показывают, что производственная мощность установок с пленочной мембранной дистилляцией незначительно превосходит широко распространенные системы мембранной дистилляции с воздушным зазором. При этом, как было показано ранее [21], в подобных системах существует необходимость в постоянной замене засоряющихся мембран. Так, для описанного выше случая потребовалось бы заменить мембраны четыре раза.
ВЫВОДЫ
В рамках совместного российско-китайского проекта было проведено исследование эффективности использования метода пленочной дистилляции с пористой конденсирующей поверхностью (ПД-ПКП) при концентрировании литийсодержащих геотермальных растворов. В этой работе мы смоделировали трехступенчатый процесс извлечения лития, включающий размягчение рассола путем осаждения катионов Ca2+/Mg2+ карбонатом натрия (рассчитано в PHREEQC), далее следует интегрированная система, состоящая из установки мембранной дистилляции (испарение воды), кристаллизатора (осаждение NaCl) и мембранной экстракции (извлечение Li+), которая была смоделирована в Simulink/MATLAB. Simulink/MATLAB позволяет моделировать работу различных устройств, интегрированных в одну систему, в режиме реального времени. Небольшая площадь поверхности мембраны 2.5 м2 для интегрированной системы в 140 кг солевого раствора была выбрана для обеспечения наиболее точного и качественного сравнения с другими, исследовавшимися ранее моделями. На основании полученных результатов можно сделать следующие выводы:
1. Производительность пленочных модулей не зависит от загрязнения испаряющей поверхности, а “восстановление” (очистка) поверхностей происходит полностью. Таким образом, в системах ПД-ПКП полностью отсутствует необходимость в использовании дополнительных комплектующих и расходных материалов для постоянной работы, что потенциально значительно снижает затраты на производство необходимого продукта (в частности, лития).
2. Пленочная дистилляция дает лучшие по сравнению с мембранной дистилляцией результаты (3.7–4.2 кг лития в месяц для ПД-ПКП против 1.4 кг лития в МД-ПКП установке за два месяца работы в стационарном режиме). Системам также требуется меньше времени для выхода на режим: 167–145 ч для ПД-ПКП и 467 для МД-ПКП. Ухудшение характеристик мембраны со временем из-за образования отложений/загрязнения играет решающую роль в производительности системы.
Исследование выполнено при финансовой поддержке РФФИ в рамках научного проекта № 20-58-53038. Работа выполнена с использованием оборудования ЦКП “Аналитический центр проблем глубокой переработки нефти и нефтехимии” ИНХС РАН.
Список литературы
Tarascon J.-M. Is lithium the new gold? // Nature Chemistry. 2010. V. 2. № 6. P. 510–510.
Lithium Statistics and Information: Mineral Commodity Summaries / U.S. Geological Survey, 01.2021.
Coplen T.B. Compilation of Minimum and Maximum Isotope Ratios of Selected Elements in Naturally Occurring Terrestrial Materials and Reagents / Google-Books-ID: vV51C834rq8C. – U.S. Department of the Interior, U.S. Geological Survey, 2002. 112 p.
Kavanagh L., Keohane J., Garcia Cabellos G., Lloyd A., Cleary J. Global Lithium Sources – Industrial Use and Future in the Electric Vehicle Industry: A Review // Resources. 2018. V. 7. Global Lithium Sources – Industrial Use and Future in the Electric Vehicle Industry. № 3. P. 57.
Kudryavtsev P.G., Kudryavtsev N.P. Lithium: resources, production and prospects of world market development // Alternative Energy and Ecology (ISJAEE). 2018. V. 0. LITHIUM. № 10–12. P. 70–81.
Flexer V., Baspineiro C.F., Galli C.I. Lithium recovery from brines: A vital raw material for green energies with a potential environmental impact in its mining and processing // Science of The Total Environment. 2018. V. 639. Lithium recovery from brines. P. 1188–1204.
Vikström H., Davidsson S., Höök M. Lithium availability and future production outlooks // Applied Energy. 2013. V. 110. P. 252–266.
Munk L., Hynek S., Bradley D.C., Boutt D., Labay K.A., Jochens H. Lithium brines: A global perspective // Chapter 14. 2016. V. 18. Lithium brines. P. 339–365.
Sun S.-Y., Cai L.-J., Nie X.-Y., Song X., Yu J.-G. Separation of magnesium and lithium from brine using a Desal nanofiltration membrane // J. Water Process Engineering. 2015. V. 7. P. 210–217.
Xiang W., Liang S., Zhou Z., Qin W., Fei W. Extraction of lithium from salt lake brine containing borate anion and high concentration of magnesium // Hydrometallurgy. 2016. V. 166. P. 9–15.
Kesler S.E., Gruber P.W., Medina P.A., Keoleian G.A., Everson M.P., Wallington T.J. Global lithium resources: Relative importance of pegmatite, brine and other deposits // Ore Geology Reviews. 2012. V. 48. Global lithium resources. P. 55–69.
Ji P.-Y., Ji Z.-Y., Chen Q.-B., Liu J., Zhao Y.-Y., Wang S.-Z., Li F., Yuan J.-S. Effect of coexisting ions on recovering lithium from high Mg2+/Li+ ratio brines by selective-electrodialysis // Separation and Purification Technology. 2018. V. 207. P. 1–11.
Song J., Huang T., Qiu H., Li X.-M., He T. Recovery of lithium from salt lake brine of high Mg/Li ratio using Na[FeCl4*2TBP] as extractant: Thermodynamics, kinetics and processes // Hydrometallurgy. 2017. V. 173. Recovery of lithium from salt lake brine of high Mg/Li ratio using Na[FeCl4*2TBP] as extractant. P. 63–70.
Song J.F., Nghiem L.D., Li X.-M., He T. Lithium extraction from Chinese salt-lake brines: opportunities, challenges, and future outlook // Environmental Science: Water Research & Technology. 2017. V. 3. Lithium extraction from Chinese salt-lake brines. № 4. P. 593–597.
Wang S., Chen X., Zhang Y., Zhang Y., Zheng S. Lithium adsorption from brine by iron-doped titanium lithium ion sieves // Particuology. 2018. V. 41. P. 40–47.
Xing L., Song J., Li Z., Liu J., Huang T., Dou P., Chen Y., Li X.-M., He T. Solvent stable nanoporous poly (ethylene-co-vinyl alcohol) barrier membranes for liquid-liquid extraction of lithium from a salt lake brine // J. Membrane Science. 2016. V. 520. P. 596–606.
Huang T., Song J., He S., Li T., Li X.-M., He T. Enabling sustainable green close-loop membrane lithium extraction by acid and solvent resistant poly (ether ether ketone) membrane // J. Membrane Science. 2019. V. 589. P. 117273.
Drioli E., Ali A., Macedonio F. Membrane distillation: Recent developments and perspectives: State-of-the-Art Reviews in Desalination // Desalination. 2015. V. 356. Membrane distillation. P. 56–84.
Khayet M. Membranes and theoretical modeling of membrane distillation: A review: Membrane Separation and Colloid Science // Advances in Colloid and Interface Science. 2011. V. 164. Membranes and theoretical modeling of membrane distillation. № 1. P. 56–88.
Khayet M., Cojocaru C. Air gap membrane distillation: Desalination, modeling and optimization: Special Issue in honour of Professor Takeshi Matsuura on his 75th Birthday // Desalination. 2012. V. 287. Air gap membrane distillation. P. 138–145.
Kalmykov D., Makaev S., Golubev G., Eremeev I., Vasilevsky V., Song J., He T., Volkov A. Operation of Three-Stage Process of Lithium Recovery from Geothermal Brine: Simulation // Membranes. 2021. V. 11. Operation of Three-Stage Process of Lithium Recovery from Geothermal Brine. № 3. P. 175.
Volkov A.V., Novitsky E.G., Borisov I.L., Vasilevsky V.P., Volkov V.V. Porous condenser for thermally driven membrane processes: Gravity-independent operation // Separation and Purification Technology. 2016. V. 171. Porous condenser for thermally driven membrane processes. P. 191–196.
Дистилляционный модуль для концентрирования и опреснения водного раствора и способ концентрирования и опреснения водного раствора с его применением: пат. 2737524 / В.П. Василевский и др.; заявл. 07.02.2020; опубл. 01.12.2020.
Golubev G., Eremeev I., Makaev S., Shalygin M., Vasilevsky V., He T., Drioli E., Volkov A. Thin-film distillation coupled with membrane condenser for brine solutions concentration // Desalination. 2021. V. 503. P. 114956.
Gwyddion – Free SPM (AFM, SNOM/NSOM, STM, MFM, …) data analysis software. – URL: http://gwyddion.net/ (дата обращения: 17.02.2022).
PHREEQC Version 3: Techniques and Methods. – URL: https://www.usgs.gov/software/phreeqc-version-3
Al-Jibbouri S., Ulrich J. The Influence of Impurities on Crystallization Kinetics of Sodium Chloride // Crystal Research and Technology. 2001. V. 36. № 12. P. 1365–1375.
Gryta M. Concentration of NaCl solution by membrane distillation integrated with crystallization // Separation Science and Technology. 2002. V. 37. № 15. P. 3535–3558.
Sun S., Yu X., Li M., Duo J., Guo Y., Deng T. Green recovery of lithium from geothermal water based on a novel lithium iron phosphate electrochemical technique // J. Cleaner Production. 2020. V. 247. P. 119178.
Prisyazhniuk V.A. Physico-chemical principles of preventing salts crystallization on heat-exchange surfaces // Applied Thermal Engineering. 2009. V. 29. № 14. P. 3182–3188.
Rosenberg Y.O., Reznik I.J., Zmora-Nahum S., Ganor J. The effect of pH on the formation of a gypsum scale in the presence of a phosphonate antiscalant // Desalination. 2012. V. 284. P. 207–220.
Дополнительные материалы отсутствуют.
Инструменты
Мембраны и мембранные технологии