Мембраны и мембранные технологии, 2022, T. 12, № 5, стр. 341-350
Коагуляция и ультрафильтрация: гибридный процесс очистки отработанных моторных масел
С. В. Федосов a, b, А. В. Маркелов c, *, А. В. Соколов c, Ю. П. Осадчий d
a Национальный исследовательский Московский государственный строительный университет
129337 Москва, Россия
b Поволжский государственный технологический университет
424000 Йошкар-Ола, Республика Марий Эл, Россия
c Ярославский государственный технический университет
150023 Ярославль, Россия
d Ивановский государственный политехнический университет
153000 Иваново, Россия
* E-mail: aleksandr203.37@mail.ru
Поступила в редакцию 15.03.2022
После доработки 31.05.2022
Принята к публикации 09.06.2022
- EDN: WWCVJF
- DOI: 10.31857/S2218117222050054
Аннотация
В статье представлены экспериментальные исследования гибридного процесса регенерации отработанных масел на основе двух взаимосвязанных процессов коагуляции и ультрафильтрации с целью проверки гипотезы о том, что процесс коагуляции за счет агрегации частиц и органических веществ способствует образованию более пористого слоя осадка, что уменьшает закупорку пор и повышает эффективность фильтрации. Исследование направлено на определение наиболее эффективных параметров баромембранного процесса путем описания изменения свойств отложений в трубчатой керамической мембране при ультрафильтрации отработанных масел. На первом этапе были проведены эксперименты на Джар реакторе с двумя различными коагулянтами: водного раствора диаминометанала и смеси моноэтаноламина и пропан-2-ол, и исследовано влияние коагулянтов на процесс образования хлопьев методом микросъемки капельных проб и бумажной хроматографии. На втором этапе проведены исследования процесса ультрафильтрации. Эксперименты по коагуляции и ультрафильтрации показали различную проницаемость процесса. Влияние на поток пермеата зависит от природы и состава коагулянта. В результате экспериментов было показано, что более устойчивые хлопья образовывались под воздействием водного раствора диаминометанала и как результат более длительная работа мембранного элемента без падения проницаемости.
ВВЕДЕНИЕ
Анализ тенденций на рынке экологически чистых технологий показывает рост научного, технологического и коммерческого интереса к баромембранным процессам и технологиям на их основе во многих отраслях промышленности.
Важнейшее условие организации малоотходного производства – наличие системы обезвреживания неиспользуемых отходов, в первую очередь токсичных неразрывно связано с мембранными процессами разделения, которые эффективнее и экономичнее обычных методов разделения [1, 2].
Накопленный за последние 10–15 лет в РФ и за рубежом опыт использования баромембранных установок свидетельствуют о том, что диапазон применения подобных технологий может быть значительно расширен. Одним из таких направлений является разделение нефти, нефтепродуктов и водомасляных эмульсий [3, 4].
С целью организации малоотходного производства предлагается проводить регенерацию отработанных моторных масел с помощью процессов баромембранного разделения, таких как микрофильтрация (МФ) и ультрафильтрация (УФ), которые эффективнее и экономичнее обычных методов разделения.
Отработанное моторное масло со временем приобретает свойство коллоидного раствора [5–9]. Из-за наличия в масле ПАВ в виде моюще-диспергирующих присадок постоянно идут процессы самопроизвольного растворения (солюбилизация) и расщепления (пептизация) образуемых нерастворимых в базовой основе продуктов старения [26]. Эти явления не позволяют частицам загрязнений образовывать крупные конгломераты, что является положительным моментом для эксплуатации масла, но ухудшает его фильтруемость.
Экономическая целесообразность использования ультрафильтрации для разделения вязких коллоидных систем в значительной степени ограничена явлением закупорки полупроницаемой перегородки [10]. Без разработки специальных условий эксплуатации мембран они будут закупорены за короткое время.
Среди различных процессов, позволяющих уменьшить загрязнения мембраны, многими учеными в своих исследованиях предлагается сочетание этапа фильтрации с этапом коагуляции. Коагуляция за счет агрегации частиц и органических веществ способствует образованию более пористого слоя осадка, что уменьшает закупорку пор и повышает эффективность фильтрации [11–18].
В то же время для удаления продуктов старения имеется необходимость дестабилизировать дисперсную систему отработанных масел и ускорить коагуляционные процессы (слипание и слияние частиц).
В данной работе исследуется гибридный процесс коагуляция-ультрафильтрация на трубчатых мембранных элементах в тангенциальном режиме. Выдвигается гипотеза о том, что большие скорости потока в трубчатом мембранном элементе увеличат эффект коагуляции за счет смыва крупных хлопьев, что будет способствовать уменьшению образованию слоя осадка на поверхности разделения.
ЦЕЛИ И ЗАДАЧИ ИССЛЕДОВАНИЯ
Целью данной работы является исследование влияния коагулянтов на процесс ультрафильтрации отработанных моторных масел.
Для достижения поставленной цели необходимо решить следующие задачи:
– разработать методику исследования;
– определить удельную электропроводность водного раствора коагулянтов;
– исследовать укрупнение загрязнений под воздействием коагулянта;
– изучить влияние коагулянта на эффективность ультрафильтрации отработанных моторных масел
1. МЕТОДЫ И ОБЪЕКТЫ ИССЛЕДОВАНИЯ
1.1. Отработанное моторное масло
В качестве исследуемого объекта использовалось отработанное моторное масло высоконагруженных дизельных двигателей марки Лукойл М-14Д2. Пробы взяты с дизельных тепловозов после 300 ч наработки в зонах по техническому обслуживанию в Эксплуатационном Ивановском ДЕПО “Иваново ДЧЭ-5” Северной железной дороги ОАО “РЖД”. Физико-химические свойства отработанного масла представлены в табл. 1.
Таблица 1.
Характеристики моторного масла М-14Д2 и отработанного масла
Определяемый показатель, единица измерения | Масло М-14Д2 | Масло отработанное |
---|---|---|
Кинематическая вязкость при 100°С, мм2/с | 13.77 | 13.32 |
Температура вспышки в открытом тигле, °С | 258 | 225 |
Водородный показатель, рН | Не нормируется | 7.72 |
Щелочное число в мг/КОН на 1 мг масла | 14.3 | 9.02 |
Массовая доля воды, % | Следы | Следы |
Оптическая плотность, см–1 | Не нормируется | 234 |
Массовая доля механических примесей, % | Отсутствие | 0.04 |
Плотность фактическая при 24.5°С, кг/м3 | 889 | 895 |
1.2. Ультрафильтрационные мембраны
В качестве фильтрующего материала использовались ультрафильтрационные керамические монотрубные мембраны с селективным слоем на основе Al2O3 производства ООО “Керамикфильтр” г. Москва.
Полимерные трубчатые мембраны производства ООО “Владипор” г. Владимир на основе фторопласта, поливинилхлорида, полисульфонамида, модифицированного поливинилхлорида и полисульфоновые были исключены в результате предварительных экспериментов по соображениям низкой температуры эксплуатации, небольшой долговечности и невозможности восстановления производительности методом обратной промывки.
Основные технические характеристики керамических мембран приведены в табл. 2.
Таблица 2.
Технические характеристики исследуемых мембран
Тип мембранного элемента | Средний диаметр пор, мкм | Допустимый диапазон, рН |
Удельная производительность по дистиллированной воде при р = 0.5 МПа, м3/(м2 ч) | Термическая устойчивость не более, °С |
Предельное рабочее давление, рmax МПа |
---|---|---|---|---|---|
Керамика Al2O3 | 0.1 | 1–13 | 1.2 | 500 | 0.6–0.8 |
Керамика Al2O3 | 0.05 | 1–13 | 0.8 | 500 | 0.6–0.8 |
Керамика Al2O3 | 0.01 | 1–13 | 0.3 | 500 | 0.6–0.8 |
Выбор мембран производился из интервала селективностей, которые обычно удовлетворяют предъявленным требования к качеству разделения и соответствует отношению [19]
где dмол – средний диаметр молекул задерживаемого вещества; dпор – средний размер пор мембраны.В табл. 3 представлены расчетные данные по выражению (1).
Таблица 3.
Расчетные характеристики мембран
Тип мембран | dпор, мкм | dмол, мкм | dмол/dпор |
---|---|---|---|
КУФЭ-1х500 | 0.5 | 0.009 | 0.02 |
КМФЭ-1х50 | 0.05 | 0.009 | 0.18 |
КУФЭ-1х10 | 0.01 | 0.009 | 0.9 |
Керамическая мембрана марки КУФЭ-1х10 производства ООО “Керамикфильтр” г. Москва имеет лучшие показатели (табл. 2) и использовалась в экспериментах.
1.3. Методика исследования процесса коагуляции
В соответствии с целью и задачами исследования в экспериментах по коагуляции использовались два реактора с разным объемами. Первый реактор имел полезный объем 0.01 м3 (10 л), который использовался для приготовления раствора к ультрафильтрации. Второй объемом 0.001 м3 (1 л) представлял собой реактор для тестирования методом испытания в мерном цилиндре (Джар-тест) и применялся для оценки коагулирующей способности мельчайших частиц загрязнений, находящихся в работающем моторном масле за счет действия коагулирующего раствора (рис. 1).
Рис. 1.
Схема лабораторной установки для коагуляции моторных масел: 1 – термостат; 2, 3 – трубопроводы для подачи и отвода теплоносителя; 4 – реактор с рубашкой; 5 – мешалка; 6 – привод; 7 – сливной кран.
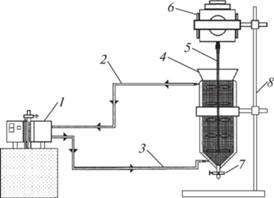
Масло загружается в реактор с рубашкой 4, в который добавляется коагулянт. Отработанное масло перемешивается с помощью мешалки 5 с частотой вращения лопастей 100–200 мин–1. Необходимый температурный режим в реакторе поддерживается с помощью термостата 1. Обработанное масло сливается через сливной кран 7.
Введение в дисперсную среду отработанного масла электролита приводит к уменьшению адсорбционно-сольватного фактора, что способствует снижению электрического барьера вокруг частиц высокомолекулярных продуктов старения масла и слипанию частиц загрязнений в конгломераты [29].
В результате проведенного анализа существующих физико-химических способов очистки отработанных моторных масел [7, 20–29] был сделан вывод о наиболее весомых факторах при выборе коагулянта для укрупнения частиц загрязнений. К ним относятся: экономичность, доступность, технологичность, экологическая безопасность. Указанным критериям наиболее удовлетворяют следующие виды реагентов:
– моноэтаноломин с пропан-2-ол (МЭА + + ИПС);
– водный раствор диаминометанала (ДAМ).
В задачи экспериментов входило определение наиболее эффективной концентрации коагулянтов в растворе.
На первом этапе были подготовлены пробы масла объемом 1000 мл, в которые содержали различные виды коагулянтов с концентрацией 0.1; 0.2; 0.3; 0.4; 0.5; 0.6; 0.7; 0.8; 0.9; 1.0; 2% по массе. После добавления коагулянта проводились кондуктометрические исследования удельной электропроводности полученных растворов, которая влияет на образование ионов. Наиболее эффективное соотношение воды и диаминометанала определялась по показателю удельной электропроводности раствора.
Температурный режим и время перемешивания очень сильно влияет на кинетику укрупнения частиц загрязнений. При проведении предварительных исследований было определено, что наиболее существенно удельная электропроводность повышается начиная с 60°С. Поэтому дальнейшие эксперименты были связаны с определением оптимальной температуры процесса коагуляции и времени перемешивания. В процессе нагрева отбирались капельные пробы через 1, 5 и 10 мин, и методом бумажной хроматографии проводилась оценка эффективности коагуляции продуктов старения масла.
Сущность метода заключается в нанесении на фильтровальную бумагу капли отработанного масла после введения коагулянта и определения величины и характера пятна, получаемого после его впитывания с использованием органолептических способов (рис. 2).
Рис. 2.
Иллюстрация масляного пятна капельной пробы на фильтровальной бумаге: 1 – ядро капли; 2 – зона диффузии нерастворимых органических примесей; 3 – зона диффузии растворимых органических примесей; 4 – зона диффузии чистого масла.
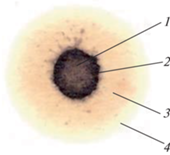
По этому методу на хроматограмме (рис. 2) различают центральное ядро, соответствующее растеканию капли масла на поверхности фильтровальной бумаги, краевую зону, а также зону диффузии, то есть кольцо, очерченное нерастворимыми в масле продуктами загрязнения вокруг ядра. Чем больше площадь диффузии, тем выше оценивается диспергирующая способность (ДС) масла. Количественная оценка ДС производится по площади зоны диффузии на хроматограмме по выражению [27]
где d – средний диаметр центрального ядра, мм; D – средний диаметр внешнего кольца зоны диффузии, мм.При значении ДС = 1 масло полностью сохраняет запас диспергирующих свойств – это свойственно новым или мало сработанным моторным маслам. В отработанных моторных маслах показатель ДС = 0.25–0.35.
Хорошим показателем правильного выбора коагулянта будет ДС → 0, это значит, что запас диспергирующих присадок исчерпан, а значит коагуляция органических примесей наиболее эффективна. В этом случае диффузионная зона 3 уменьшается до размеров ядра, а вокруг него проявляется ярко выраженная светло-желтая окантовка.
Кроме этого, капельные пробы наносились на стекло с целью исследования эффективности процесса коагуляции с помощью электронного микроскопа.
1.4. Методика исследования процесса ультрафильтрации
Принципиальная схема лабораторной установки показана на рис. 3.
Рис. 3.
Принципиальная схема лабораторной ультрафильтрационной установки: 1 – резервуар с отработанным моторным маслом; 2 – насос, 3 – трехходовой кран; 4, 9 – манометры соответственно на входе и выходе из фильтрующего модуля; 5 – ультрафильтрационный модуль; 6 – мерная колба с пермеатом; 7 – запорная арматура; 8 – кран для залива отработанного масла; 10 – нагревательный прибор; 11 – напорная магистраль; 12 – байпасная магистраль; 13 – вентиль сливной.
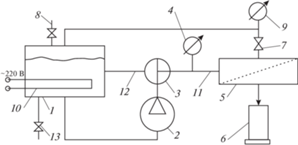
Исходный раствор для разделения подается насосом 2 из резервуара 1 на мембранный элемент трубчатого типа 5. Пермеат собирается в мерную колбу 6. Подогрев раствора производится с помощью электрического тена 10. Давление в системе контролируется по манометрам 4, 9.
Мембранный модуль состоит из одного трубчатого керамического элемента длиной 0.8 м, внутренним диаметром 0.006 м и общей площадью фильтрования 0.015 м2. Отсечение по молекулярной массе составляет 100 кДа при размере пор 0.1–0.01 мкм.
Трансмембранное давление поддерживалось на уровне 0.1–0.5 МПа. Для создания в мембранном трубчатом модуле турбулентного режима течения, скорость потока разделяемого раствора составляла 5–10 м · с–1.
Перед ультрафильтрацией в резервуаре 1 проводили коагуляцию с режимами идентичными с Джар тестами.
2. РЕЗУЛЬТАТЫ ИССЛЕДОВАНИЯ
2.1.1. Определение удельной электропроводности водного раствора диаминометанала
Диаминометанал в водном растворе диссоциирует на положительные и отрицательные ионы. При температуре 298 K константа ионизации водного раствора диаминометанала Ки = 1.15 × × 10–14 моль2/л2. Данный показатель очень близок к константе ионизации воды при той же температуре. Из курса общей химии известно, что при нагреве из диаминометанала образуется водный раствор аммиака в следствие процессов гидролиза. Водный раствор аммиака сильный электролит с константой ионизации Ки ~ 10–5 моль2/л2 и высокой степенью электропроводности. Поэтому данный раствор способен разрушать двойной электрический слой на поверхности частиц продуктов старения масел, подверженных пептизации [28, 29]. В задачи эксперимента входило определение концентрации ДAM с точки зрения увеличения электропроводности. Данные исследований представлены на рис. 4.
Анализ проведенных кондуктометрических исследований (рис. 4) позволяет сделать вывод о том, что наиболее оптимальная концентрация диаминометанала составляет 50%, т. к. дальнейшее увеличение не приводит к резкому увеличению количества ионов. Кроме того, растворимость коагулянта в воде при температуре 293 К составляет 51.8 мас. % [28, 29]. При более высоких температурах растворимость повышается, но увеличиваются затраты на получение раствора, связанные с расходом энергии на подогрев растворителя.
2.1.2. Исследование укрупнения загрязнений
Результаты оценки укрупнения загрязнений по методу бумажной хроматографии и выбору оптимальной температуры и времени перемешивания представлены в табл. 4 . Данные представлены при концентрации коагулянта 1 мас. %.
Таблица 4.
Результаты исследования укрупнения загрязнений от температуры и времени перемешивания
Темпе-ратура, °С | Время переме-шивания, мин. | Вид пятна капельной пробы на бумаге |
---|---|---|
1 | Сплошное серое пятно, коагуляция не наблюдается | |
50–60 | 5 | Сплошное серое пятно, коагуляция не наблюдается |
10 | Сплошное серое пятно, коагуляция не наблюдается | |
1 | Сплошное серое пятно, коагуляция не наблюдается | |
60–70 | 5 | Серое пятно со слабовыраженной светло-желтой окантовкой, коагуляция малозаметна |
10 | Черное пятно со слабовыраженной светло-желтой окантовкой, видимая коагуляция достаточная для удаления загрязнений | |
1 | Серое пятно со слабовыраженной светло-желтой окантовкой, коагуляция малозаметна | |
70–80 | 5 | Черное пятно со слабовыраженной светло-желтой окантовкой, видимая коагуляция достаточная для удаления загрязнений |
10 | Черное пятно с ярковыраженной светло-желтой окантовкой, видимая коагуляция достаточная для удаления загрязнений | |
1 | Черное пятно со слабовыраженной светло-желтой окантовкой, видимая коагуляция достаточная для удаления загрязнений | |
80–90 | 5 | Черное пятно с ярковыраженной светло-желтой окантовкой, видимая коагуляция достаточная для удаления загрязнений |
10 | Черное пятно с ярковыраженной светло-желтой окантовкой, видимая коагуляция достаточная для удаления загрязнений |
Анализируя экспериментальные данные, представленные в табл. 5, можно сделать вывод о том, что наиболее полная коагуляция происходит в диапазоне температур 353–363 К и временем перемешивания 5–10 мин.
Таблица 5.
Результаты анализа исходного раствора, концентрата и пермеата при Kуо = 2.5
Определяемый показатель, единица измерения |
Результаты анализа | ||||
---|---|---|---|---|---|
исходное | ретентат | пермеат | |||
ДАМ | МЭА + ИПС | ДАМ | МЭА + ИПС | ||
Кинематическая вязкость при 100°С, мм2/с | 13.32 | 14.11 | 13.78 | 11.48 | 11.1 |
Температура вспышки в открытом тигле, °С | 225 | 223 | 220 | 238 | 235 |
Водородный показатель, рН | 7.72 | 7.83 | 7.8 | 7.9 | 7.8 |
Щелочное число в мг/КОН на 1 мг масла | 9.02 | 8.14 | 6.05 | 0.57 | 3 |
Массовая доля воды, % | Следы | Отсутствие | Отсутствие | Отсутствие | Отсутствие |
Оптическая плотность, см–1 | 234 | 289 | 295 | 35 | 30 |
Массовая доля механических примесей, % | 0.04 | 0.09 | 0.09 | 0.0001 | 0.0001 |
Плотность фактическая при 24.5°С, кг/м3 | 895 | 898 | 895 | 883 | 878 |
Второй параметр, который был исследован на данном этапе – влияние концентрации коагулянта в отработанном масле на процесс образования хлопьев.
Результаты фото микросъемки капельных проб при температуре 353 К приведены на рис. 5–8.
Рис. 5.
Микрофотография отработанного моторного масла после введения 0.2 мас. % коагулянта (увеличение в 400 крат): (а) – 50% водного раствора диамида угольной кислоты; (б) – моноэтаноламин + пропан-2-ол.
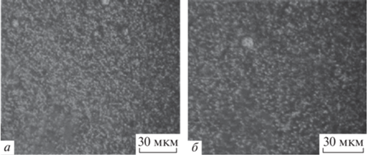
Рис. 6.
Микрофотография отработанного моторного масла после введения 0.5 мас. % коагулянта (увеличение в 400 крат): (а) – 50% водного раствора диамида угольной кислоты; (б) – моноэтаноламин + пропан-2-ол.
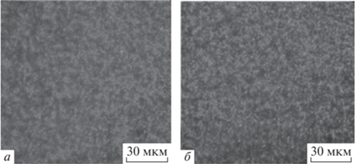
Рис. 7.
Микрофотография отработанного моторного масла после введения 1 мас. % коагулянта (увеличение в 400 крат): (а) – 50% водного раствора диамида угольной кислоты; (б) – моноэтаноламин + пропан-2-ол.
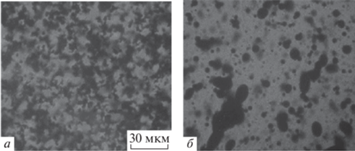
Рис. 8.
Микрофотография отработанного моторного масла после введения 2 мас. % коагулянта (увеличение в 400 крат): (а) – 50% водного раствора diaminomethanal; (б) – моноэтаноламин + пропан-2-ол.
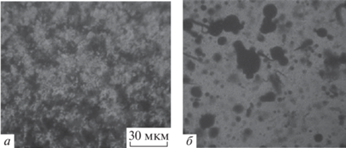
На микрофотографиях приведенных на рис. 5–7 видно, что частицы загрязнений агрегатируют до 1–2 мкм при внесении в отработанное масло 0.2 мас. % коагулянта. В результате дальнейшего увеличения концентрации разделяющего реагента до 1–2 мас. % наблюдалось укрупнение частиц до 5–10 мкм при внесении диаминометанала и до 10–20 мкм моноэтаноламина и пропан-2-ол.
2.2. Результаты процесса ультрафильтрации
Эффективность ультрафильтрационного процесса во многом зависит от удельной производительности мембран G. В проведенных экспериментах исследовались зависимость удельной производительности ультрафильтров от трансмембранного давления и от времени ведения процесса разделения.
На рис. 9 и 10 представлены результаты экспериментов по влиянию трансмембранного давления для мембран с размером пор 0.05 и 0.01 мкм после выхода удельной производительности на плато через 120 мин после начала проведения эксперимента. Кривые на рисунках получены аппроксимацией экспериментальных данных методом наименьших квадратов.
Рис. 9.
Динамика изменения удельной производительности керамической мембраны со средним диаметром пор 0.05 мкм с концентрацией коагулянта: 1 – 1% МЭА + ИПС; 2 – 0.5% МЭА + ИПС; 3 – 1% ДАМ; 4 – 0.5% ДАМ; 5 – без коагулянта.
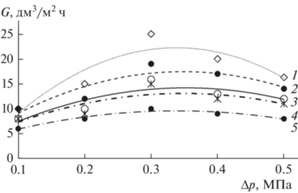
Рис. 10.
Динамика изменения удельной производительности керамической мембраны со средним диаметром пор 0.01 мкм с концентрацией коагулянта: 1 – 1% МЭА + ИПС; 2 – 0.5% МЭА + ИПС; 3 – 1% ДАМ; 4 – 0.5% ДАМ; 5 – без коагулянта.
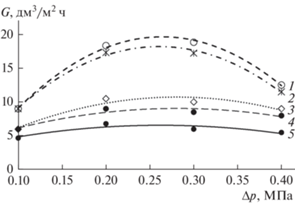
Из графиков на рис. 9 и 10 видно, что в промежутке между значением рабочего давления в 0.2 и 0.3 МПа наблюдается точка экстремума, после которой при увеличении давления удельная производительность падает. Это объясняется уплотнением слоя хлопьев на поверхности мембраны, состоящего из высокомолекулярных продуктов старения масла, под действием нарастающего давления.
При определении степени концентрирования исходного сырья было найдено, что удовлетворительной величиной коэффициента уменьшения его объема следует считать Kуо = 2.5, который рассчитывается по выражению
где VисхОМ – объем исходного отработанного масла в приемном резервуаре; VконцОМ – объем концентрата в приемном резервуаре, образующийся в процессе разделения отработанных масел ультрафильтрацией.Повышение Kуо приводит увеличению КП и ГП на поверхности разделения и проскоку асфальто-смолистых продуктов старения масел в пермеат.
Результаты анализов, полученные при уменьшения исходного объема ОМ в приемном резервуаре до величины Kуо = 2.5 представлены в табл. 5 и 6 .
Анализ данных, представленных в табл. 5 и 6 показывает эффективность ультрафильтрации отработанных масел. Так оптическая плотность уменьшилась почти в 7 раз. Это значит, что из исходного раствора практически были удалены асфальто-смолистые продукты старения масел.
Уменьшения вязкости и понижение щелочного числа говорит об отделении из отработанного масла сработанных вязкостных (загущающих) присадок. В качестве таких присадок применяют полиизобутилены, полиметакрилаты, сополимеры стирола с диенами, сополимеры олефинов [10].
Наличие в масле Мо, Ni, Cu и Cr свидетельствует о наличии в моторных маслах антифрикционных и других типов присадок. Наличие Fe, Pb, Al, Si говорит о наличии механических загрязнений вследствие трения сопряженных поверхностей. Как видно из табл. 6 после ультрафильтрации содержание металлов, вызывающие загрязнения уменьшилось в 2–5 раз, а полезных металлов только на 20–30%. Таким образом, после мембранного разделения получено масло высокого качества с остаточным содержанием антиокислительных и противоизносных присадок.
Таблица 6.
Содержание металлов в разделяемых маслах
Определяемый показатель, единица измерения |
Результаты анализа | ||
---|---|---|---|
исходное | ретентат | пермеат | |
Свинец (Pb), г/т масла, не более | 0.472 | 0.581 | 0.331 |
Олово (Sn), г/т масла, не более | 0.212 | 0.281 | 0.193 |
Хром (Cr), г/т масла, не более | 0.449 | 0.641 | 0.247 |
Молибден (Мо), г/т масла, не более | 1.354 | 1.146 | 0.860 |
Никель (Ni), г/т масла, не более | 0.366 | 0.702 | 0.233 |
Медь (Cu), г/т масла, не более | 2.431 | 3.408 | 2.416 |
Кремний (Si), г/т масла, не более | 13.370 | 5.797 | 5.249 |
Железо (Fe), г/т масла, не более | 65.905 | 90.004 | 45.127 |
Алюминий (Al), г/т масла, не более | 1.210 | 1.957 | 0.464 |
На рис. 11 представлены результаты экспериментов по исследованию зависимости от времени процесса разделения. Кривые на рисунке получены аппроксимацией экспериментальных данных методом наименьших квадратов.
Рис. 11.
Динамика изменения удельной производительности мембран от времени, диаметр пор dp = 0.01 мкм, давление Δр = 0.3 МПа, температура t = 353 K: 1 – 1% МЭА + ИПС; 2 – 0.5% МЭА + ИПС; 3 – 1% ДАМ; 4 – 0.5% ДАМ; 5 – без коагулянта.
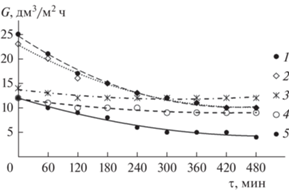
Из рис. 11 видно, что удельная производительность мембраны в начальный период разделения выше с коагулянтом на основе МЭА + ИПС на 150% и составляет 25 дм3/м2 ч. Данное явление можно объяснить образованием более крупных хлопьев, поперечный поток через которые испытывает меньшее сопротивление. Кроме этого, вязкость масла при таком виде коагулянта ниже. Однако уже через 60 мин производительность падает более чем на 30% и затем продолжает снижаться. Это можно объяснить низким сопротивлением сдвигу, легкому разрушению на более мелкие фракции при постоянной циркуляции раствора и образованию плотного слоя геля на поверхности разделения.
Раствор с диаминометаналом хотя и показывает меньшую удельную производительность, но динамика ее падения не превышала 30% за 8 ч наблюдений. Это можно объяснить тем, что хлопья, образованные под воздействием ДАМ более устойчивы к разрушению, и образуют пористый слой отложений и проницаемость выходит на плато в 11 дм3/м2 ч через 120 мин ведения процесса.
ВЫВОДЫ
В результате проведенных экспериментов были получены следующие результаты:
– разработаны экспериментальные установки для исследования процессов коагуляции и ультрафильтрации отработанных масел с использованием керамических трубчатых мембран;
– предложены методики экспериментальных исследований процесса разделения отработанных масел;
– определен состав отработанных масел, с помощью аттестованных методов посредством современного аналитического оборудования, который указывает на высокое качество очищенного продукта;
– исследовано влияние давления на проницаемость и определено, что наибольшая производительность достигается при перепаде давления 0.2–0.3 МПа;
– показано, что наиболее эффективным коагулянтом является водный раствор диаминометанала.
Вместе с тем, имеются предложения для проведения дополнительных исследований.
В случае тангенциальной фильтрации в трубчатом мембранном элементе на первое место выходит устойчивость хлопьев к напряжению сдвига в трубчатом мембранном элементе и при прохождении через питающий насос, т.к. именно эти свойства влияют на повышение сопротивления через слой осадка на поверхности мембраны.
Для более точного анализа влияния скорости потока и напряжения сдвига на разрушение хлопьев необходимо провести ряд экспериментов с использованием реактора Тейлора–Куэтта (Taylor–Couette reactor). С помощью него можно создать условия подобные движению масла в мембранном трубчатом элементе и в питающем насосе. Для этого нужно использовать реакторы с различными диаметрами вращающихся и неподвижных частей, которые способны создавать напряжение сдвига от 0 до 200 Па при скоростях вращения от 0 до 300 рад · с–1.
Список литературы
Первов А.Г. Современные высокоэффективные технологии очистки питьевой и технической воды с применением мембран: обратный осмос, нанофильтрация, ультрафильтрация // М.: Издательство Ассоциации строительных вузов. 2009. 232 с. ISBN: 978-5-93093-691-9.
Осадчий Ю.П. Возврат ценных компонентов из стоков текстильной промышленности с применением катализаторов // Курск: Закрытое акционерное общество “Университетская книга”. 2021. 250 с. ISBN 978-5-907555-01-3. https://doi.org/10.47581/2021/Osadchi.01
Юшкин А.А., Балынин А.В., Нехаев А.И., Волков А.В. // Мембраны и мембранные технологии. 2021. Т. 11. № 2. С. 155–162. https://doi.org/10.1134/S2218117221020097
Фазуллин Д.Д., Маврин Г.В., Шайхиев И.Г., Низамеев И.Р. // Мембраны и мембранные технологии. 2018. Т. 8. № 1. С. 51–58. https://doi.org/10.1134/S2218117217060049
Rudnick L.R. Synthetics, Mineral Oils, and Bio-Based Lubricants: Chemistry and Technology, Third ed. // CRC Press. 2020. 1194 p. https://doi.org/10.1201/9781315158150
Francois A. Waste Engine Oils: Rerefining and Energy Recovery // Elsevier Science. 2006. 340 p. eBook ISBN: 9780080465173.
Brinkman D.W., Parry B.J. Recycling, Oil, In Kirk-Othmer Encyclopedia of Chemical Technology. // John Wiley & Sons, Inc. 2005. https://doi.org/10.1002/0471238961.15091202050311.a01.pub2
Firas A. Design Aspects of Used Lubricating Oil Re-Refining // Elsevier, 2006. 122 p. https://doi.org/10.1016/B978-0-444-52228-3.X5000-6
Lashkhi V.L., Fuks I.G., Shor G.I. // Chem Technol Fuels Oils. 1991. V. 27. P. 311–319. https://doi.org/10.1007/BF00718997
Fedosov S.V., Osadchy Y.P., Markelov A.V., Sokolov A.V. // Membranes and Membrane Technologies. 2021. V. 3. № 6. P. 389–399. https://doi.org/10.1134/S2517751621060044
Vyas H.K., Bennett R.J., Marshall A.D. // J. Membr. Sci. 2001. V. 192 (1–2). P. 165–176. https://doi.org/10.1016/S0376-7388(01)00503-8
Lahoussine–Turcaud V., Wiesner M.R., Botero J.Y. // J. Membr. Sci. 1990. V. 52(2). P. 173–190. https://doi.org/10.1016/S0376-7388(00)80484-6
Guigui C., Rouch J.C., Durand-Bourlier L., Bonnelye V., Aptel P. // Desalination. 2002. V. 147(1–3). P. 95–100. https://doi.org/10.1016/S0011-9164(02)00582-9
Park P., Lee C., Choi S., Choo K., Kim S., Yoon C. // Desalination. 2002. V. 145(1–3). P. 237–245. https://doi.org/10.1016/S0011-9164(02)00418-6
Abdessemed D., Nezzal G. // Desalination. 2003. V. 152(1–3). P. 367–373. https://doi.org/10.1016/S0011-9164(02)01085-8
Tansel B., Regula J., Shalewits R. // Desalination. 1995. V. 102. P. 301–311. https://doi.org/10.1016/0011-9164(95)00067-C
Jung C., Son H., Kang L. // Desalination. 2006. V. 197(1–3). P. 154–164. https://doi.org/10.1016/j.desal.2005.12.022
Barbot E. et al. // J. Membr. Sci. 2008. V. 325(2). P. 520–527. https://doi.org/10.1016/j.memsci.2008.07.054
Дытнерский Ю.И. Обратный осмос и ультрафильтрация // М.: Химия. 1978. 352 с.
Reis M.A.R., Jeronimo M.S. // Ind. Eng. Chem. Res. 1990. V. 29(3). P. 432–436. https://doi.org/10.1021/ie00099a019
Roy M., Mortier M.F., Stefan S., Orszulik T. Chemistry and Technology of Lubricants // Springer, Dordrecht. 2010. 560 p. https://doi.org/10.1007/978-1-4020-8662-5
Rincon J., Canizares P., Garcia M.T. // Ind. Eng. Chem. Res. 2005. V. 44. P. 4373–4379. https://doi.org/10.1021/ie040254j
Rincon J., Canizares P., Garcia M.T. // Ind. Eng. Chem. Res. 2005. V. 44(20). P. 7854–7859. https://doi.org/10.1021/ie0580452
Shakirullah M., Ahmed I., Saeed M., Khan M.A., Rehman H., Ishaq M., Shah A.A. // A J. Chemical Society Located in Taipei. 2006. V. 53. P. 335–342. https://doi.org/10.1002/jccs.200600042
Isah A.G., Abdulkadir M., Onifade K.R., Musa U., Garba M. U., Bawa A.A., Sani Y. // Proceedings of the World Congress on Engineering 2013, London, U. K. 2013. V. 1. P. 565–568. https://www.researchgate.net/ publication/290795308
Осадчий Ю.П., Маркелов А.В., Пахотин Н.Е., Маркелова О.А. // Строительные материалы. 2018. № 7. С. 68–70. https://doi.org/10.31659/0585-430X-2018-761-7-68-70
Итинская Н.И., Кузнецов Н.А. Топливо, масла и технические жидкости: справочник // М.: Агропромиздат. 1989. 304 с.
Wittcoff H.A., Reuben B.G., Plotkin J.S. Industrial organic chemicals. 2-nd ed. // Noboken. 2004. 845 p. ISBN: 9781118229811.
Остриков В.В., Бусин И.В. // Техника в сельском хозяйстве. 2011. № 5. С. 23–24. EDN: YLXSBJ.
Дополнительные материалы отсутствуют.
Инструменты
Мембраны и мембранные технологии