Микроэлектроника, 2021, T. 50, № 1, стр. 3-9
Влияние условий нанесения и ионно-плазменной обработки тонких пленок кобальта на их электросопротивление
И. И. Амиров a, *, Р. В. Селюков a, В. В. Наумов a, Е. С. Горлачев a
a Ярославский филиал Физико-технологического института им. К.А. Валиева Российской АН
150007 Ярославль, ул. Университетская, 21, Россия
* E-mail: ldamirov@yandex.ru
Поступила в редакцию 08.07.2020
После доработки 16.07.2020
Принята к публикации 16.07.2020
Аннотация
Проведены исследования удельного электрического сопротивления ρ пленок кобальта толщиной 10–55 нм, полученных в разных режимах магнетронного нанесения на пластины SiO2/Si и последующей их ионно-плазменной обработки. Пленки Со толщиной 42 нм с минимальным ρ, равным 9.8 мкОм ⋅ см, были получены при температуре 600 К, что сравнимо с ρ объемного металла. Обработка поверхности пленок Со в плотной аргоновой плазме с энергией ионов около 20 эВ при комнатной температуре приводила к увеличению удельного сопротивления, в то время как при Т ~ 500 К наблюдалось как уменьшение, так и увеличение ρ. Такое изменение сопротивления обусловлено комплексным воздействием ионной бомбардировки и температуры. Обсуждается механизм влияния ионно-плазменной обработки на электропроводность пленки Co.
ВВЕДЕНИЕ
С переходом в суб‑10 нм область технологии интегральных схем (ИС) становится необходимым использование в качестве материала металлизации Co, Ru [1–3], поскольку при таких размерах элементов удельное электрическое сопротивление ρ обычно используемой меди резко увеличивается из-за размерного эффекта, связанного со средней длиной свободного пробега электрона λ, равного для Cu 39 нм [3]. Значение λ для Co и Ru намного меньше (11.8 и 6.6 нм соответственно). Кроме того, замена меди на более тугоплавкий Со повысит надежность металлизации, что делает Co одним из наиболее перспективных металлов межсоединений элементов ИС [4–9]. Удельное сопротивление тонких пленок металлов зависит от способа их нанесения. Поэтому в настоящее время проводятся интенсивные исследования процессов осаждения тонких пленок металлов с минимальным удельным электрическим сопротивлением. Их наносят методами плазмохимического газофазного осаждения [3, 5, 6] магнетронного распыления [7, 10] и электрохимического осаждения [11–13]. Большой интерес представляет магнетронный метод нанесения пленок, который широко используется в технологии наноэлектроники. Исследование электропроводности пленок Со, полученных импульсным магнетронным нанесением [10] показало, что удельное сопротивление пленок Со толщиной 6 и 40 нм равнялось 35 и 14 мкОм ⋅ см соответственно, т.е. было сравнимо с электропроводностью объемного Со (6.8 мкОм ⋅ см). Одним из подходов к уменьшению сопротивления тонких металлических пленок является проведение их термического отжига в инертном газе или водороде [7, 14]. В результате такого отжига удаляется оксидная пленка металла, изменяются микроструктура и шероховатость, которые определяют сопротивление пленок [15–17]. Шероховатость поверхности пленки можно уменьшить также путем низкоэнергетического ее распыления в плазме инертного газа. Так, было показано, что при распылении пленки платины при энергии ионов Ar+ 200 эВ ее шероховатость уменьшается [18]. Однако ионная бомбардировка может повлиять на проводимость пленки металла в результате привнесенной дефектности [19]. Целью данной работы – исследование условий получения тонких (10–55 нм) пленок Со методом магнетронного нанесения с минимальным удельным электрическим сопротивлением, а также исследование влияния на ρ пленки низкоэнергетической (20–150 эВ) ионной бомбардировки в плотной плазме ВЧИ разряда в Ar.
ЭКСПЕРИМЕНТ
При нанесении пленок Co на установке магнетронного распыления SCR‑650 (Alcatel) использовали мишень Со чистотой 99.95% и Ar чистотой 99.995%. Остаточное давление составляло 5 × 10–5 Па, рабочее давление Ar – 2 × 10–3 Па. Мощность ВЧ магнетрона равнялась 300 Вт. Пленки Со толщиной h = = 10–55 нм осаждали на поверхность окисленных (толщина SiO2 980 нм) пластин Si КДБ‑10 (100) диаметром 100 мм в четырех режимах. В режимах 1 и 2 нанесение Со проводили при температуре 600 К без подачи напряжения на подложку (пластина находилась на плавающем потенциале) (режим 1) и с подачей ВЧ смещения, при этом постоянная составляющая напряжения на подложке была –20 В относительно корпуса (режим 2). В режимах 3 и 4 осаждение пленки проводили при температуре 300 К также без смещения (режим 3) и со смещением (режим 4). Образцами служили пластинки Si/SiO2 с нанесенными пленками Со разной толщины, размером 10 × 10 мм, которые вырезались из кремниевых пластин. Время осаждения 50 нм пленок было 680 с.
Анализ морфологии поверхности пленок проводили с использованием сканирующего электронного микроскопа Supra‑40 (Carl Zeiss), а также c помощью атомно-силового микроскопа (АСМ) СММ‑2000ВАК (ОАО “Завод ПРОТОН‑МИЭТ”). Для АСМ измерений использовались кантилеверы CSG01 (НТ‑МДТ). С помощью дифрактометра ДРОН‑3М проводилась съемка θ‑2θ дифрактограмм. Поверхностный состав пленок определяли методом Оже-электронной спектроскопии (PHI‑660, Perkin‑Elmer). Поверхностное сопротивление Rs пленок Co определяли четырехзондовым методом с помощью вольтметра В7‑21 и источника тока П321. Из измерений поверхностного сопротивления Rs и толщины h определяли удельное электрическое сопротивление ρ по формуле:
Погрешность определения ρ определялась, главным образом, погрешностью измерения толщины пленки. Толщину пленки измеряли профилометром TALYSTEP, а также с помощью СЭМ на сколе пластины Si c нанесенной пленкой Co.
Обработку образцов проводили в реакторе плотной аргоновой плазмы высокочастотного индукционного разряда низкого давления (f = = 13.56 МГц, 1 кВт). Конструкция реактора подробно описана в [20]. Образец на Аl держателе (пластина диаметром 150 мм, толщиной 2.2 мм) загружался в реакционную камеру через шлюзовую камеру на электрод, на который подавали ВЧ смещение от отдельного ВЧ генератора (f = 13.56 МГц, 600 Вт). При подаче ВЧ мощности смещения на электроде устанавливался постоянный отрицательный потенциал самосмещения, который определял энергию падающих ионов [20]. В случае обработки поверхности без подачи ВЧ смещения, образец в плазме находился под плавающим потенциалом. При этом энергия бомбардирующих поверхность ионов была ~20 эВ. Ионно-плазменную обработку осуществляли при низкой (~300 K) и высокой температуре (~500 К). Образец нагревался плазмой до такой температуры в процессе обработки, если он лежал на держателе без обеспечения какого-либо теплоотвода. Низкую температуру образца поддерживали путем установления его на Al держателе на теплопроводящей вакуумной смазке. Охлаждение Al держателя осуществлялось путем подачи гелия в зазор между ним и охлаждаемым электродом под давлением около 10 Торр. Условия проведения эксперимента были следующими: рабочее давление было равно 0.08 Пa, расход Ar был равен 10 ст. см3/мин, ВЧ мощность на индукторе составляла 800 Вт.
РЕЗУЛЬТАТЫ И ОБСУЖДЕНИЕ
Измерения ρ пленок Со показали, что в зависимости от режима их нанесения оно изменялось в диапазоне 9.8–19.4 мкОм ⋅ см (табл. 1). Пленки с минимальным ρ были получены при температуре 600 К без смещения и со смещением (режимы 1 и 2). При нанесении пленки без смещения (режим 1) ρ пленки толщиной 42 нм равнялось 9.8 мкОм ⋅ см. Это не намного превышало ρ объемного Со и было меньше ρ пленки такой же толщины, полученной в высокоплотной плазме магнетронного разряда (14 мкОм ⋅ см) [10]. При высокой температуре подача постоянного смещения (режим 2) приводила к увеличению ρ. Сопротивление пленки Со, полученной при низкой температуре (режим 3) было почти в два раза больше ρ пленки, полученной при высокой температуре (режим 1). При Т = 300 К, подача ВЧ смещения, наоборот, приводила к уменьшению ρ (режим 4). Такое различие в электропроводности пленок могло быть обусловлено их разной микроструктурой и/или разной шероховатостью. Однако, как показано далее, шероховатость пленок Co в нашем эксперименте была приблизительно одинаковой.
Таблица 1.
Параметры осаждения и характеристики пленок Co
Режим | T осаждения, K | Смещение на подложке, В | Скорость нанесения, нм/с | h, нм | ρ, мкОм ⋅ см | I, отн. ед. | β, град |
---|---|---|---|---|---|---|---|
1 | 600 | Плавающий потенциал | 0.06 | 42 | 9.84 ± 0.07 | 148 | 0.65 |
2 | 600 | –20 | 0.06 | 43 | 12.77 ± 0.04 | 32 | 0.70 |
3 | 300 | Плавающий потенциал | 0.08 | 55 | 19.36 ± 0.11 | – | – |
4 | 300 | –20 | 0.07 | 49 | 17.55 ± 0.04 | – | – |
Дифрактограммы не выявили кристаллической фазы в пленках, осажденных при 300 K, что характеризует такие пленки как рентгеноаморфные. На дифрактограммах пленок, осажденных при 600 K, наблюдался пик при 2θ ≈ 44.5°, который может соответствовать дифракционному максимуму (0002) hcp фазы или максимум (111) метастабильной fcc фазы Co [21]. Для режима 1 интегральная ширина пика β равна 0.65°, для режима 2 – 0.7°. Оценка среднего размера области когерентного рассеяния с помощью формулы Шеррера дает для режима 1 значение 15 нм, для режима 2 – 14 нм. Интегральная интенсивность дифракционного пика I для режима 1 оказалась в 4.5 раз выше, чем для режима 2, что свидетельствует о меньшей дефектности пленки, приготовленной в режиме 1. Таким образом, меньшее значение ρ для пленок, осажденных при 600 K, может быть обусловлено большим размером зерна по сравнению с пленками, осажденными при 300 K. Этой же причиной можно объяснить меньшее ρ для пленки, полученной в режиме 1 по сравнению с режимом 2.
Высокая электропроводность полученных в режиме 1 нанометровых пленок Co может свидетельствовать, что пленки имеют достаточно гладкую поверхность. Основной причиной увеличения ρ является рассеяние электронов на поверхности и границах зерен. Зависимость удельного сопротивления пленок от толщины описывается классическими моделями Фукса и Зондхеймера [3, 22] и Мэйадаса–Шатцкеса (МШ) [23]. В рамках упрощенной модели ФЗ удельное сопротивление пленки определяется уравнением (2) [3, 22].
(2)
${\rho \mathord{\left/ {\vphantom {\rho {{{\rho }_{0}}}}} \right. \kern-0em} {{{\rho }_{0}}}} = 1 + \frac{{3\lambda \left( {1 - p} \right)}}{{8h}},$(3)
${\rho \mathord{\left/ {\vphantom {\rho {{{\rho }_{0}}}}} \right. \kern-0em} {{{\rho }_{0}}}} = \frac{1}{{1 - {{3\alpha } \mathord{\left/ {\vphantom {{3\alpha } 2}} \right. \kern-0em} 2} + 3{{\alpha }^{2}} - 3{{\alpha }^{3}}\ln \left( {1 + {1 \mathord{\left/ {\vphantom {1 \alpha }} \right. \kern-0em} \alpha }} \right)}}.$Параметр α в (3) определяется выражением:
где R – коэффициент отражения от границы зерна, d – средний латеральный размер зерна. Расчет зависимости удельного сопротивления пленки толщиной 17–48 нм (λ < h) в рамках модели МШ позволил определить параметр α. Было найдено, что для толщин пленок равных 17–30 нм параметр α = 1.5, а для h = 48 нм α = 1.2. Уменьшение α можно объяснить увеличением d при увеличении h. Если принять λ = 11.8 нм, то для 42 нм пленки при d = 10 нм, получаем значение R = 0.5. Для сравнения, в [10] для тонких пленок Co разной плотности было получено R = 0.33–0.75, причем, большие значения R характерны для более плотных пленок.Необходимо отметить, что на поверхности Со всегда присутствует естественная окисная пленка нанометровой толщины [10]. Наличие такой пленки приводит к увеличению сопротивления пленки Со, например, нами было найдено, что измеренное ρ пленок кобальта толщиной менее 20 нм увеличивается на 9–24% при нахождении на атмосфере. Анализ состава исходных пленок Со методом оже-электронной спектроскопии, а также пленок после плазменной обработки показал, что атомарное содержание C, O, Co на их поверхности было, приблизительно, одинаково и составляло 42, 36 и 23% соответственно. Таким образом, окисление пленки в результате ионно-плазменной обработки можно исключить.
Таким образом, пленки Со с наименьшим ρ можно получить при ее нанесении в режиме 1 при высокой температуре, так как при низкой температуре (режим 3) их электропроводность была почти в два раза меньше. Однако на практике нанесение пленок предпочтительнее выполнять при низкой температуре, хотя при этом их электропроводность меньше (см. табл. 1). Поэтому влияние ионно-плазменной обработки Ar на электросопротивление проводили для пленки толщиной 46 нм и ρ = 30 мкОм ⋅ см, полученной при низкой температуре (режим 3). Эксперименты с ее утонением до 22–24 нм путем распыления ионами с энергией 50, 75, 100 и 150 эВ показали, что их удельное электрическое сопротивление было приблизительно одинаковым и равнялась 32–35 мкОм ⋅ см. Поэтому можно полагать, что бомбардировка поверхности ионами с энергией 50–150 эВ не приводит к изменению шероховатости пленки.
Анализ морфологии поверхности методом сканирующей электронной микроскопии (СЭМ) исходных пленок показал, что в разных режимах нанесенные пленки Со толщиной 42–55 нм были гладкими. На рис. 1 приведены СЭМ изображения поверхности и скола пленки Со толщиной 10 и 42 нм, полученных в режиме 3. Из СЭМ данных для сколов было установлено, что пленка Со толщиной 42 нм была нанокристаллической с характерным размером зерна равным 10–20 нм. Размеры зерен пленки толщиной 10 нм были ~10 нм. Анализ морфологии поверхности методом АСМ показал, что шероховатость поверхности пленки Со толщиной 10 нм не превышала 0.3 нм (рис. 2а). Эти результаты подтверждали, что исходные нанокристаллические пленки Со были достаточно гладкими. Сравнение с литературными данными показало, что их шероховатость была сравнима с шероховатостью поверхности пленок Со, полученных при импульсном магнетронном напылении (0.2 нм) [11] и была намного меньше, чем при газофазном осаждении (1 нм) [8]. Средний латеральный размер зерна согласно АСМ измерениям был равен приблизительно 30 нм, что завышено по сравнению с данными СЭМ. Причиной данного расхождения может быть недостаточная разрешающая способность, достигнутая при АСМ измерениях.
Рис. 2.
АСМ изображения поверхности исходной (а) и подвергнутой серии ионно-плазменных обработок (б) пленки Co толщиной 10 нм. Размер кадров – 500 × 500 нм.
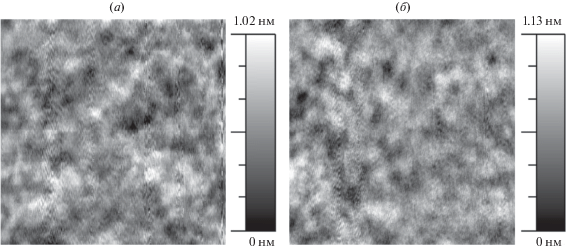
Влияние ионной обработки на электросопротивление пленок определяли также из сравнения ρ исходных пленок разной толщины (10, 20, 30 и 50 нм), полученных в режиме 3 с ρ этих пленок после разной длительности их плазменной обработки при энергии ионов ~20 эВ. При этом утонения пленки Со не происходило, так как энергия ионов была меньше порога распыления металла. Нанесение пленок Со различной расчетной толщиной (10, 20, 30 и 50 нм) в режиме 3 показало, что их удельное сопротивление слабо уменьшалось с увеличением толщины (рис. 3 зависимость 1). Серия кратковременных (по 26 с) распылений этих пленок при энергии 50 эВ, в процессе которых толщина пленок каждый раз уменьшалась на 3–6 нм, показало, что электросопротивление резко увеличилось при толщине пленки <10 нм (рис. 3, зависимость 2). При h > 15 нм удельное сопротивление исходных пленок Со и пленок, полученных в результате распыления совпадали (рис. 3). Эти результаты свидетельствовали, что кратковременная низкоэнергетическая ионная бомбардировка не приводила к изменению их сопротивления.
Рис. 3.
Зависимость удельного сопротивления пленок Co от их толщины. 1 – исходные пленки, 2 – утоненные в результате ионно-плазменного распыления.
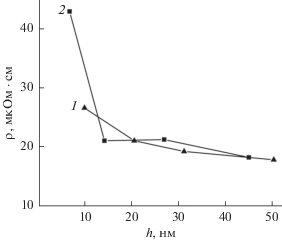
Многократная обработка поверхности пленок Со толщиной 10, 20, 30 нм при Т = 300 К и энергии ионов 20 эВ с длительностью каждой обработки 360 с с последующим выносом образца на атмосферу между циклами обработки, показала, что ρ монотонно увеличивалось (рис. 4). Причем, чем меньше была толщина пленки, тем сильнее было увеличение ρ пленки. Однако при обработке образцов, температура которых в плазме увеличивалась до 500 К, наблюдался другой характер изменения ρ (рис. 5). Многократная обработка поверхности пленок разной толщины в плазме Ar в течение 30 мин с длительностью обработки 240 с на каждом цикле показала, что удельное сопротивление пленок толщиной 40, 50 и 55 нм после каждого цикла обработки могло и увеличиваться, и уменьшаться. Удельное сопротивление пленок Со после первых двух циклов обработки увеличивалось, а затем резко уменьшилось. Далее сопротивление снова увеличивалось, затем падало. С увеличением числа обработок изменение ρ уменьшалось. При этом наблюдалась общая тенденция к увеличению ρ.
Рис. 4.
Зависимость удельного сопротивления пленок Co разной толщины от времени обработки в плазме Ar при комнатной температуре. 1 – h = 10 нм, 2 – h = = 20 нм, 3 – h = 30 нм.
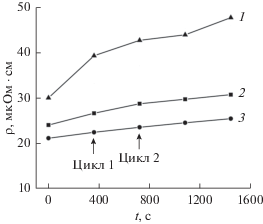
Рис. 5.
Изменение удельного сопротивления пленок Co толщиной: 1 – 40 нм, 2 – 50 нм, 3 – 55 нм от времени циклической обработки их в плазме Ar при энергии ионов 20 эВ при температуре ~500 K.
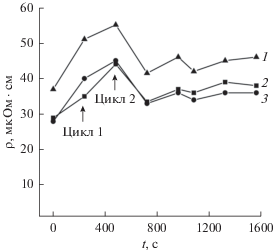
Обработка поверхности более тонких пленок Co в течение 40 мин с длительностью каждого цикла обработки 10 минут показала, что изменения ρ пленок толщиной 10, 20 и 30 нм от цикла к циклу были более сильными (рис. 6). В течение первых четырех циклов обработки наблюдалось периодическое увеличение и уменьшение ρ с общей тенденцией его возрастания. Наибольшее увеличение сопротивления наблюдалось для пленки 10 нм. Оно возрастало почти в три раза, в то время как для пленок толщиной 20 и 30 нм, приблизительно, в два раза. Такое увеличение ρ нельзя объяснить нагревом пленки, так как оно не изменялось, если образцы помещались на подложкодержателе перевернутыми (зависимости 1а‑3а, рис. 6). В этом случае пленка также нагревалась в плазме (вакуумный отжиг) до температуры равной, приблизительно, 500 К, но не подвергались ионной бомбардировке.
Рис. 6.
Изменение удельного сопротивления пленок Co толщиной: 1, 1а – 10 нм, 2, 2а – 20 нм, 3, 3а – 30 нм от времени циклической обработки их в плазме Ar при температуре ~500 K. 1, 2, 3 – плазменный отжиг, 1а, 2а, 3а – термический отжиг.
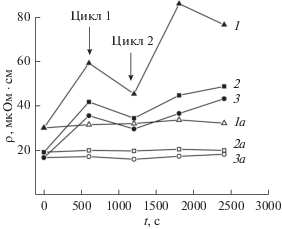
Монотонное увеличение ρ пленки Со с увеличением времени плазменной обработки (рис. 4) при комнатной температуре может быть обусловлено изменением кристаллической структуры пленки, уменьшением размеров зерен Со при ионной бомбардировке. Немонотонный характер изменения ρ, который возникает только при совместном воздействии двух факторов – ионной бомбардировки и температуры (рис. 5, 6) может объясняться релаксационными процессами в пленке, связанными с изменением микроструктуры в результате охлаждения образца при выносе его на атмосферу. Релаксационные процессы, возникающие после прекращения ионного воздействия, наблюдали, например, при исследовании внутренних напряжений в пленке Pt [24], а удельное электрическое сопротивление связано с напряжениями в пленке [16]. Увеличение ρ пленки не могло быть связано с внедрением Ar в пленку, так при энергии ионов ниже порога распыления они не могли проникнуть в пленку.
ЗАКЛЮЧЕНИЕ
Исследование влияния условий нанесения пленок Со толщиной 10–55 нм магнетронным методом на их электросопротивление, а также влияние ионно-плазменной обработки на ρ пленок показало следующее.
Во всех исследованных режимах нанесения пленок Со они были достаточно гладкими. Шероховатость поверхности была не более 0.3 нм. Наименьшее ρ пленки Со толщиной ~40 нм, равное 9.8 мкОм ⋅ см было при ее нанесении при повышенной температуре (600 K). При Т = 300 K и слабой ионной бомбардировке оно было приблизительно в два раза больше.
Низкоэнергетическая ионная бомбардировка поверхности не влияла на шероховатость поверхности пленок Co. Обработка поверхности пленок Со в плотной плазме Ar с энергией ионов ниже порога распыления при Т = 300 K приводила к монотонному увеличению ρ.
Ионно-плазменная обработка пленок Со при Т ≈ 500 К приводила как к уменьшению, так и увеличению ρ после каждого цикла обработки. Такое изменение удельного сопротивления обусловлено комплексным воздействием ионной бомбардировки и температуры, которое происходит в процессе плазменной обработки. Оно объясняется релаксационными процессами в пленке, связанными с перестройкой дефектов, границ зерен, уменьшением их размеров после каждого цикла обработки и выноса образца на атмосферу.
Исследование выполнено при финансовой поддержке гранта РФФИ № 18‑29‑27017 с использованием оборудования Центра коллективного пользования “Диагностика микро- и наноструктур”.
Список литературы
Vyas A.A., Zhou C., Yang C.Y. On-chip interconnect conductor materials for end-of-roadmap technology nodes // IEEE Transactions on Nanotechnology. 2018. V. 17. № 1. P. 4–10.
Gall D. Metals for low-resistivity interconnects // Proceedings of the IEEE International Interconnect Technology Conference (IITC). Santa Clara. 2018. P. 157–159.
Gall D. Electron mean free path in elemental metals // J. Appl. Phys. 2016. V. 119. № 8. 085101.
Van der Veen M.H., Vandersmissen K., Dictus D., Demuynck S., Liu R., Bin X., Nalla P., Lesniewska A., Hall L., Croes K. Cobalt bottom-up contact and via prefill enabling advanced logic and DRAM technologies // IEEE International Interconnect Technology Conference and IEEE Materials for Advanced Metallization Conference (IITC/MAM). 2015. P. 25–28.
Bekiaris N., Wu Z., Ren H., Naik M., Park J.H., Lee M., Ha T.H., Hou W., Bakke J.R., Gage M., Wang Y., Tang J. Cobalt Fill for Advanced Interconnects // IEEE International Interconnect Technology Conference (IITC). 2017. P. 1–3.
Dutta S., Beyne S., Gupta A., Kundu S., Van Elshocht S., Jamieson G., Bömmels J., Wilson C.J., Tőkei Z., Adelmann C. Sub-100 nm2 Cobalt Interconnects // IEEE Electron Device Letters. 2018. V. 39, № 5. P. 731–734.
Milosevic E., Kerdsongpanya S., McGahay M.E., Zangiabadi A., Barmak K., Gall D. Resistivity scaling and electron surface scattering in epitaxial Co(0001) layers // J. Appl. Phys. 2019. V. 125. № 24. P. 245105.
Wislicenus M., Liske R., Gerlich L., Vasilev B., Preusse A. Cobalt advanced barrier metallization: A resistivity composition analysis // Microelectronic Engineering. 2015. V. 137. P. 11–15.
Pacco A., Akanishi Y., Le Q.T., Kesters E., Murdoch G., Holsteyns F. Controlled cobalt recess for advanced interconnect metallization // Microelectronic Engineering. 2019. V. 217. 111131.
Jablonka L., Riekehr L., Zhang Z., Zhang S.-L., Kubart T. Highly conductive ultrathin Co films by high-power impulse magnetron sputtering // Appl. Phys. Lett. 2018. V. 112. № 4. P. 043103.
Hu Y., Huang Q. Effects of dimethylglyoxime and cyclohexane dioxime on the electrochemical nucleation and growth of cobalt // J. Electrochem. Soc. 2019. V. 166. № 1. D3175-D3181.
Kelly J., Kamineni V., Lin X., Pacquette A., Hopstaken M., Liang Y., Amanapu H., Peethala B., Jiang L., Demarest J., Shobha H., Raymond M., Haran B. Annealing and impurity effects in Co thin films for MOL Contact and BEOL metallization // J. Electrochem. Soc. 2019. V. 166. № 1. D3100-D3109.
Wu J., Wafula F., Branagan S., Suzuki H., van Eisden J. Mechanism of cobalt bottom-up filling for advanced node interconnect metallization // J. Electrochem. Soc. 2019. V. 166. № 1. D3136–D3141.
Ezzat S.S., Mani P.D., Khaniya A., Kaden W., Gall D., Barmak K., Coffey K.R. Resistivity and surface scattering of (0001) single crystal ruthenium thin films // J. Vac. Sci. Technol. 2019. V. A. 37. № 3. 031516.
Namba Y. Resistivity and temperature coefficient of thin metal films with rough surface // Jap. J. Appl. Phys. 1970. V. 9. № 11. P. 1326–1329.
Чопра К.Л. Электрические явления в тонких пленках. М.Мир. 1972. Р. 434.
Josell D., Brongersma S.H., Tokei Z. Size-dependent resistivity in nanoscale interconnects // Annu. Rev. Mater. Res. 2009. V. 39. P. 231–254.
Амиров И.И., Наумов В.В., Изюмов М.О., Селюков Р.С. Влияние энергии ионов на морфологию поверхности пленки платины при высокочастотном ионно-плазменном распылении // Письма в ЖТФ. 2013. Т. 39. Вып. 2. С. 68–75.
Chowdhury A., Bhattacharjee S. Experimental investigation of change in sheet resistance and Debye temperatures in metallic thin films due to low-energy ion beam irradiation // J. Phys. D: Appl. Phys. 2013. V. 46. № 43. 435304.
Амиров И.И., Изюмов М.О., Наумов В.В. Низкоэнергетическое, селективное травление пленок металлов в плотной аргоновой плазме с добавками кислорода // Поверхность. Рентгеновские, синхротронные и нейтронные исследования. 2016. № 8. С. 82–86.
Джумалиев А.С., Никулин Ю.В., Филимонов Ю.А. Влияние давления аргона и отжига на микрокристаллическую структуру текстурированных пленок Со, осаждаемых магнетронным распылением // ЖТФ. 2018. Т. 18. Вып. 11. С. 1734–1742.
Sondheimer E.H. The mean free path of electrons in metals // Advances in physics. 1952. V. 1. № 1. P. 1–42.
Mayadas A.F., Shatzkes M. Electrical-resistivity model for polycrystalline films: the case of arbitrary reflection at external surfaces. // Phys. Rev. B. 1970. V. 1. № 4. P. 1382–1389.
Chason E., Sheldon B.W., Freund L.B., Floro J.A., Hearne S.J. Origin of compressive residual stress in polycrystalline thin films // Phys. Rev. Lett. 2002. V. 88. № 15. 156103.
Дополнительные материалы отсутствуют.
Инструменты
Микроэлектроника