Микроэлектроника, 2021, T. 50, № 1, стр. 10-20
Металлизация переходных отверстий в кремниевых пластинах для создания трехмерных микроструктур
А. И. Воробьева a, *, В. А. Лабунов a, Е. А. Уткина a, **, Д. В. Грапов a
a Белорусский государственный университет информатики и радиоэлектроники
220013 Минск, yл. П. Бровки, 6, Беларусь
* E-mail: vorobjova@bsuir.by
** E-mail: outkina@bsuir.by
Поступила в редакцию 14.07.2020
После доработки 28.07.2020
Принята к публикации 28.07.2020
Аннотация
Исследованы процессы электрохимического осаждения меди в матрицу вертикальных отверстий разного диаметра (500–2000 нм) в подложках Si/SiO2 с барьерным слоем TiN на дне отверстий. Морфологические исследования металла в отверстиях показали, что структура кластеров меди достаточно однородна и формируется из кристаллитов размером ~30–50 нм. Повторяемость и стабильность при однородной структуре и 100%-ной степени заполнения отверстий Cu определяют перспективу применения системы Si/SiO2/Cu в качестве базового элемента для создания трехмерных микро- и наноструктур, и для 3D сборки кристаллов ИМС.
ВВЕДЕНИЕ
При изготовлении современных ИМС наиболее серьезные технологические проблемы связаны с формированием металлических межсоединений. Большое количество контактных площадок последнего уровня металлизации при их подсоединении к контактным площадкам корпусов ИС делает эту операцию дорогостоящей, что значительно увеличивает стоимость готового изделия и, кроме этого, снижает надежность такого устройства. Монтаж кремниевых кристаллов по принципу трехмерной сборки кристаллов (3D-технология) позволяет в значительной мере решить эти проблемы. Одним из основных направлений в развитии технологий 3D интеграции является метод “сквозных отверстий через кремний (“Through Silicon Via”, TSV-технология). Такая вертикальная системная интеграция с формированием и последующей металлизацией отверстий в кремнии путем напыления, химического или гальванического осаждения металлов из растворов, позволяет осуществлять более высокую плотность монтажа при сопоставимых размерах пластины, достигать большей функциональности и лучших характеристик. Это технология обеспечивает не только повышение степени интеграции, но и снижает трудоемкость сборки, улучшает быстродействие и энергопотребление систем [1–3].
Алюминий является малопригодным материалом для 3D-технологий из-за деградационных процессов, обусловленных электромиграцией. Наиболее перспективным материалом межсоединений является медь благодаря ряду преимуществ перед алюминием, таких как более низкое сопротивление, стойкость к электромиграции, более высокие скорости переключения элементов ИМС [4, 5]. При выборе материала и способа его осаждения следует учитывать, что технологически создание металлизации и монтаж интегральных схем – сложный многостадийный процесс, включающий последовательное нанесение на кремниевые пластины пленок разнородных материалов (металлов), каждый из которых выполняет определенные функции. Требования к таким последовательно нанесенным слоям сложны и многообразны. К наиболее важным из них относятся хорошее сцепление с полированной поверхностью кремниевых пластин и между собой, мелкозернистость, беспористость, однородность, равномерная толщина.
Традиционно, при изготовлении трехмерных микро- и наноструктур металлы осаждают на кремниевую подложку методами химического осаждения из паровой фазы (CVD, chemical vapor deposition) и физического осаждения из паровой фазы (PVD, physical vapor deposition); однако, данные методы дорогостоящи. Альтернативным становится метод электрохимического осаждения (ECD, electrochemical deposition), который может быть реализован как экономически эффективный низкотемпературный процесс, обладающий всеми преимуществами, характерными для электрохимических процессов: высокой скоростью, дешевизной реагентов, низкими энергозатратами, возможностью обработки больших подложек и сложных профилей [6, 7].
Независимо от способа получения пленок, непосредственное нанесение меди на кремний недопустимо из-за диффузии и электромиграции атомов меди в кремний. Кроме того, непосредственное электрохимическое осаждение на кремниевую подложку из традиционно используемых растворов – проблемная технологическая операция из-за плохой смачиваемости гладкой поверхности кремния. Оптимизация этого процесса позволила бы сократить число слоев на кремниевых пластинах, операций их получения и необходимых материалов, то есть, значительно упростила бы формирование трехмерных микроструктур Сu/Si/SiO2 с переходными отверстиями.
Обычно, вначале на кремнии формируют барьерные слои из нитридов кремния, диоксида кремния, титана, нитрида титана, никеля или его соединений с фосфором и вольфрамом. Некоторые из них (никель или его соединения), выполняют также функции адгезива для упрочнения сцепления пленок металлов с чрезвычайно гладкой поверхностью подложки [8]. Ранее в технологии медной металлизации было предложено осаждать медь электрохимически на барьерный слой, предварительно покрытый затравочным тонким слоем меди (seed layer), который формируют методами PVD или СVD [9–11]. Однако, по мере того, как размеры канавок и отверстий уменьшаются, становится все труднее осаждать непрерывный и не содержащий дефектов затравочный слой. Кроме того, при уменьшении размеров ниже 100 нм затравочный слой становится значительной частью металлизации. В результате были предложены новые стратегии (варианты) непосредственного (прямого) осаждения меди на барьерный слой TiN без затравочного покрытия (seedless copper electrochemical deposition, SECD) [12–14].
Непосредственное электрохимическое осаждение меди (SECD) на поверхность диффузионного барьерного слоя TiN, Ta, TaN и др. без медного затравочного покрытия может стать технологией следующего поколения для устройств ультравысокого уровня интеграция (ULSI, ultra large-scale integration). Такой вариант снижает стоимость изготовления металлизации и повышает качество заполнения контактных переходов и канавок (способность заполнять узкие каналы). В зависимости от химического состава электролита, особенно рН, условий осаждения (потенциал осаждения), осадки меди на диффузионных барьерах имеют различные варианты зародышеобразования и роста.
Кроме того, наличие узких отверстий в подложке с оксидным слоем Si/SiO2 приводит к изменению условий диффузии при осаждении. Это связано с неоднородным распределением плотности тока, которая во много раз выше на кромках отверстий, чем в глубине. В результате, при осаждении (особенно при конформном заполнении) узкие глухие отверстия зарастают с образованием пустот, которые могут приводить к выходу из строя систем металлизации в процессе работы ИМС.
Цель данной работы – исследовать влияние способа подготовки (активации) поверхности подложки Si/SiO2 с глухими отверстиями и условий непосредственного (прямого) электрохимического осаждения меди в отверстия с барьерным слоем TiN на дне отверстий на микроструктуру, характер границ раздела и поверхности в системе кремний – матрица столбиков меди. Такие исследования позволят упростить технологию формирования переходных отверстий в ИМС и разнообразить процессы формирования различных микроструктур и комбинированных нано-микроструктур на основе медных столбиков в подложке Si/SiO2.
МЕТОДИКА ЭКСПЕРИМЕНТА
В качестве исходных подложек использовались пластины монокристаллического кремния n-типа марки КЭФ-1.5 (100), легированные фосфором, с удельным сопротивлением 10.5 Ом ⋅ см. Последующее осаждение сплошных слоев Ti и TiN, формирование матрицы упорядоченных вертикальных отверстий в оксиде кремния, барьерного слоя на дне отверстий и маски на поверхности пластины (TiN) осуществляли на ОАО “Интеграл” в кластерной установке вакуумного типа “Endura 5500 PVD” фирмы “Applied Materials”, как описано в патенте [15].
Быстрая термическая обработка (БТО) для формирования силицида титана на границе раздела Si/Ti выполнялась на установке “Heatpulse 8108” фирмы “AG Associates”. В результате проведения отжига пленки Ti на Si в среде азота формировалась структура Si/TiSi2/Ti/TiN. Способ позволяет формировать пленки дисилицида титана модификации С54 с высокой электропроводностью. При этом исключается образование модификации типа С49 с низкой электропроводностью.
Такая технология обеспечивает формирование в слое SiO2 глухих отверстий разного диаметра (см. ниже) в виде усеченных конусов с барьерным слоем TiN на дне [15]. Пленки TiN имеют хорошую адгезию к кремнию и, кроме того, обладают высокой твердостью, химической инертностью и термодинамической стабильностью.
Схема и внешний вид фрагмента исходной тестовой структуры (экспериментального образца) с матрицей глухих отверстий показаны на рис. 1. На одной подложке расположено четыре модуля с матрицей отверстий разного диаметра: 500, 1000, 1500 и 2000 нм.
Рис. 1.
Схематическое изображение (а), РЭМ фотографии поверхности (б) и поперечного сечения (вставка) фрагмента исходного экспериментального образца (модуль с диаметром отверстий 500 нм).
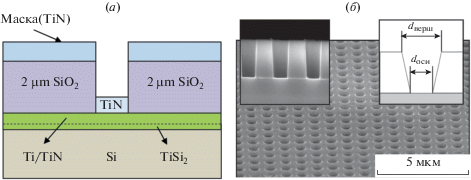
Контакт n-Si/TiN через тонкую прослойку TiSi2 является практически омическим, и такая структура обеспечивает хороший электрический контакт с тонким слоем TiN. Однако, чтобы избежать возможных ограничений в процессах электрохимического осаждения меди в узкие отверстия, связанных с наличием пленки TiN на дне отверстий, и для достижения более равномерного распределения потенциала по поверхности образца, в некоторых образцах дополнительно был изготовлен омический контакт с тыльной стороны кремниевой пластины. Пленку меди толщиной 0.5 мкм осаждали магнетронным распылением на обратную сторону подложки.
Перед электрохимическим осаждением меди кремниевые пластины с матрицей отверстий разного диаметра активировали, варьируя условия проведения этой стадии, в буферном растворе, содержащем в объемных соотношениях HF : NH4F : H2O = = 1 : 2.5 : 5 при комнатной температуре. Такой раствор обычно используется для удаления естественного оксида с поверхности кремниевых пластин. В серии опытов пластины не подвергали обработке. Предполагалось, что такая операция необходима для изменения шероховатости поверхности пленки TiN – получения более развитой поверхности, и, кроме того, она влияет на свойства поверхности стенок (SiO2) переходных отверстий.
Известно также, что при БТО в слое нитрида титана могут формироваться оксиды титана вследствие взаимодействия титана как с кислородом, находящимся в нитриде титана в виде твердого раствора, так и с кислородом, поступающим в нитрид титана из окружающей среды. Кроме того, на поверхности нитрида титана присутствуют органические загрязнения, сформировавшиеся в процессе получения матрицы отверстий [16]. Поэтому такая операция (активация) необходима для удаления оксидов и органики с поверхности барьерного слоя.
Далее, непосредственно после промывки в проточной и дистиллированной воде в течение 2–3 мин при 22°С, проводили электрохимическое осаждение меди непосредственно на барьерный слой в сульфатном электролите (№ 1) или в пирофосфатном электролите (№ 2), состав которых приведен в табл. 1.
Таблица 1.
Параметры электролитов, используемых для электрохимического осаждения меди
Электролит | Состав | Концентрация, г/л |
---|---|---|
№ 1 | Сульфат меди (CuSO4 · 5H2O) | 180 |
Серная кислота (H2SO4) | 40 | |
Соляная кислота (HCl) | 0.02 | |
№ 2 | Сульфат меди (CuSO4 · 5H2O) | 225 |
Пирофосфат калия (K2P2O7) | 15 |
Использовали стандартную стеклянную двухэлектродную ячейку. Рабочим электродом служила подложка n-кремния, которая жестко фиксировалась в специально разработанном держателе.
Металлизация обратной стороны подложки и конструкция держателя позволяют обеспечить равномерное распределение потенциала по всей поверхности образца. В качестве катода использовали пластину из чистого (марки х. ч.) пиролитического графита размером, превышаюшим площадь поверхности образца, контактирующую с электролитом. Использование инертного (нерастворимого) анода позволяет избежать изменения концентрации никеля в электролите, что дает возможность поддерживать выход металла по току на заданном уровне. Перемешивание электролита осуществлялось магнитной мешалкой.
Толщину и микроструктуру электрохимического осадка (меди) контролировали, изменяя потенциал электрода и время проведения процесса. Потенциал устанавливали в режиме линейной развертки постепенно от нуля до постоянного значения со скоростью 30 мВ/с, и далее поддерживали постоянным в течение определенного времени. Ток появляется не сразу, а при достижении определенного значения потенциала, которое зависит от состояния поверхности образца (времени обработки и электролита). Погрешность измерений потенциала составляла не более 1 мВ, тока – 30 нА.
Микроструктуру, морфологию поверхности и поперечного среза структур SiO2/Cu (стенки отверстий) и Si/TiSi2/TiN/Cu (дно отверстий) изучали методом растровой электронной микроскопии (РЭМ) на разных стадиях изготовления. Использовали сканирующий электронный микроскоп Hitachi S-7800H при нормальной ориентации пучка электронов, и при его направлении под углом к поверхности; увеличение достигало 130 000×, с разрешающей способностью ~10 нм. Особенности локализации металлической фазы в отверстиях SiO2 и ее выхода на поверхность SiO2 изучались на срезах образцов, полученных посредством их резки и полировки поверхности сфокусированным ионным пучком, на микроскопе LYRA 3 TESCAN, максимальное увеличение – 150 000×. Химический анализ элементного состава экспериментальных образцов проводили на этом же приборе с приставкой для энергодисперсионного анализа (EDX – energy-dispersive X-ray spectroscopy) при ускоряющем напряжении 10 кВ (система микроанализа для растровых электронных микроскопов QUANTAX 200, Zeiss A.G., Bruker). Глубина анализируемого слоя ~1.5 мкм.
РЕЗУЛЬТАТЫ И ИХ ОБСУЖДЕНИЕ
Топологические особенности (морфология) матрицы отверстий
Чтобы выяснить особенности процесса заполнения глубоких отверстий в диэлектрике и оценить полученные экспериментальные результаты, сначала были исследованы морфологические особенности исходной матрицы (шаблон из оксида кремния). На рис. 2 представлены РЭМ фотографии поверхности и поперечного сечения исходных кремниевых структур.
Рис. 2.
РЭМ изображения поверхности (а) и скола (б) фрагмента исходной тестовой структуры образца с диаметром отверстий 500 нм и глубиной 2.0 мкм.
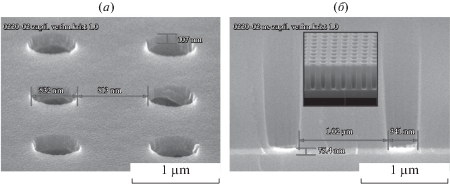
Как видно из фотографий, морфология (форма) отверстий, которая определяется рисунком фотолитографической маски, достаточно регулярная и однородная. Глубина отверстий составляет 2000 ± ± 50 нм и определяется толщиной диэлектрического слоя SiO2. Распределение диаметра отверстий по глубине трапецеидальное, стенки отверстий гладкие. Толщина маски из нитрида титана на поверхности образца равна 110 ± 10 нм; барьерного слоя на дне отверстий ~80 ± 10 нм.
Морфология структур SiO2/Cu и Si/TiSi2/TiN/Cu
Предварительная оценка состояния поверхности структур SiO2/Cu и Si/TiSi2/TiN/Cu, после осаждения металла в отверстия без предварительной обработки проводилась методом оптической микроскопии. Результаты экспресс-анализа показали, что в результате электрохимического осаждения при потенциале –1.6 В в течение 5 мин медь локализуется только в областях некоторых отверстий. Сплошная пленка меди на поверхности не образуется. Детальный анализ сколов таких же образцов методом РЭМ показал, что медь осаждается почти во все отверстия, но неравномерно (см. рис. 3).
Рис. 3.
РЭМ изображения поверхности (а) и скола (б) структур SiO2/Cu (стенки отверстий) и Si/TiSi2/TiN/Cu (дно отверстий).
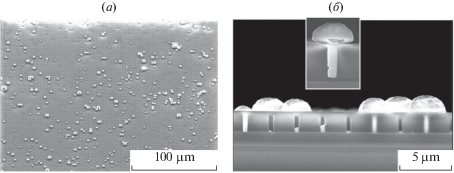
Некоторые отверстия заполнены металлом с избытком (рис. 3), а в некоторых Cu визуально отсутствует (рис. 3а). Чтобы установить наличие или отсутствие осадка в таких отверстиях, проводился рентгеноспектральный анализ вдоль линии, проходящей над визуально незаполненными участками (рис. 4).
Рис. 4.
Результаты рентгеноспектрального анализа структур SiO2/Cu и Si/TiSi2/TiN/Cu вдоль обозначенной линии.
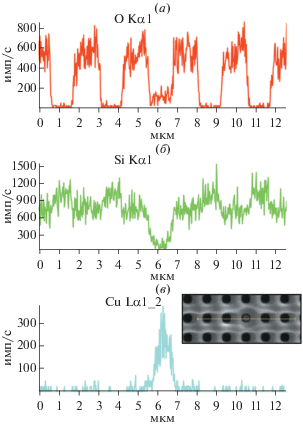
Рефлексы меди регистрируются не во всех отверстиях, а только в тех, которые на РЭМ изображении скола (рис. 3б) выглядят заполненными или полузаполненными. Частично это связано с тем, что глубина анализируемого слоя меньше 1.5 мкм, но есть и незаполненные отверстия. На РЭМ фотографии поверхности, рис. 3а, четко видны шапочки только над полностью заполненными отверстиями.
Анализ РЭМ фотографий сколов на нескольких участках длиной 80 мкм показывает, что на начальном этапе большинство отверстий заполняются. Возможно, в процессе осаждения некоторые из них блокируются пузырьками водорода. Другая причина неравномерного осаждения меди в отверстия, скорее всего, обусловлена особенностями электрохимического осаждения меди на гладкую поверхность плохо смачиваемого барьерного слоя TiN.
Результаты РЭМ исследования сколов обработанных образцов SiO2/Cu и Si/TiSi2/TiN/Cu показаны на рис. 5. Из фотографий видно, что при идентичных условиях осаждения (электролит № 2, потенциал – 1.6 В, время осаждения 5 мин) металл осаждается во все отверстия и выходит на поверхность. Над поверхностью маски происходит более интенсивное латеральное разрастание агломератов меди.
Рис. 5.
РЭМ изображения сколов структур SiO2/Cu и /Si//TiSi2/TiN/Cu для трех одинаковых (0.5 × 2.0 мкм) образцов: а, б – время обработки 20 с; в, г – время обработки 30 с; д, е – время обработки 25 с.
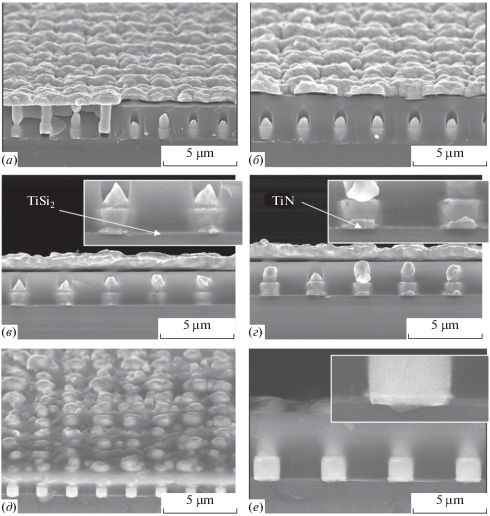
Образовавшиеся столбики меди имеют осевую симметрию, повторяя форму отверстий. Из фотографий видно, что в процессе химической обработки образцов происходит неравномерное травление стенок отверстий из оксида кремния. Донная область отверстий немного шире. Это связано с тем, что оксид кремния состоит из двух слоев: нижний слой – это оксид, полученный методом химического осаждения из паровой фазы (CVD), толщиной (0.6 ± 0.05) мкм. Верхний слой – оксид, полученный методом плазмохимического осаждения из газовой фазы (plasma enhanced chemical vapor deposition, PECVD), толщиной (1.4 ± 0.07) мкм. Термодинамическая неравновесность процессов разложения в газовом разряде при PECVD процессах позволяет проводить осаждение SiO2 и других диэлектриков при более низких температурах, чем в аналогичных процессах химического осаждения из газовой фазы с термическим разложением реакционного газа [17]. В результате, PECVD-оксид проявляет более высокую химическую стойкость в буферном растворе, который предназначен для обработки дна отверстий, а CVD-оксид подтравливается (растворяется).
Таким образом, морфология столбиков меди в переходных отверстиях определяется в большей степени процессом изготовления матрицы (в том числе на этапе активации), чем процессом электрохимического осаждения. В данном варианте с активацией поверхности барьерного слоя медь осаждается во все отверстия равномерно и до поверхности.
Важно отметить, что нитрид титана в используемом буферном растворе не травится. Его вообще сложно стравить химически, и обычно удаляют (или утоняют) ионным травлением. На вставках рис. 5 в, 5г отчетливо видно, что на дне отверстий остается слой нитрида титана (TiN), а также видна тонкая прослойка дисилицида титана (TiSi2) на сплошном слое TiN. Не исключено также образование смачивающего слоя Cu, так как толщина прослойки на дне отверстий несколько больше толщины исходного слоя TiN.
При химической обработке пластин изменяется также поверхность маски, она становится более шероховатой. В результате, над поверхностью маски происходит более интенсивное латеральное разрастание агломератов меди, чем в первом случае.
Для изучения условий зарождения меди на поверхности барьерного слоя были изготовлены микроструктуры с частичным заполнением отверстий металлом при потенциале –1.6 В, но в течение более короткого времени (2 мин). На рис. 6 показаны РЭМ изображения кристаллитов меди на начальном этапе осаждения.
Рис. 6.
РЭМ изображения структуры металлического осадка после 2 мин электрохимического осаждения меди в электролите № 2 в отверстия разного диаметра: а – 2.0 мкм, б – 1.5 мкм; в – 1.0 мкм; г – 0.5 мкм.
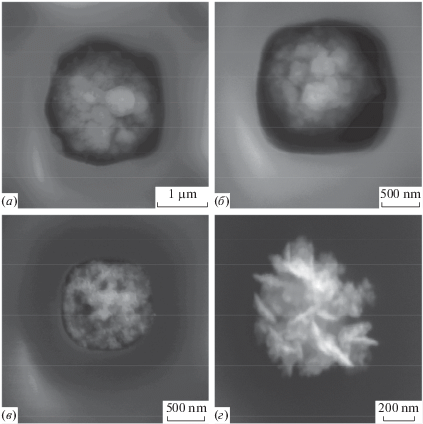
При большем увеличении видно, что поверхность частиц меди не является гладкой, так как они состоят из отдельных кластеров, прилегающих друг к другу. Кристаллы разной формы размером 100–200 нм (рис. 6а, 6б), при большом увеличении представляют собой цепочки кристаллитов размером ~30–50 нм (рис. 6г).
Известно, что только в исключительных случаях формируется кристалл, имеющий геометрически правильную форму – правильного многогранника или полиэдра. Это происходит в тех случаях, когда внешние условия способствуют полному развитию кристалла (во всех направлениях). Фотографии иллюстрирует склонность меди к формированию осадка в виде неправильных многогранников разной формы в отверстиях диаметром 2.0 и 1.5 мкм. В условиях ограниченного пространства (особенно в отверстиях диаметром 1.0 и 0.5 мкм) формируются кристаллы неправильных очертаний, кристаллиты которых имеют ветвистую форму с незаполненными промежутками, напоминающую деревце (дендриты), рис. 6в, 6г [18]. Сравнение фотографий на рис. 6б и рис. 6в позволяет предположить, что, чем меньше диаметр отверстий, тем выше вероятность формирования дендритов. Далее происходит полное и равномерное заполнение обработанных отверстий медью с практически одинаковыми латеральными размерами. Скорость заполнения зависит от типа электролита, времени обработки и диаметра отверстий.
Таким образом, установлено, что активированный слой TiN, который после обработки не содержит оксидов, пригоден для беззатравочного осаждения Cu в отверстия диаметром (500–2000) нм. Осаждение на поверхность TiN с пониженным содержанием оксидов (и органических загрязнений) приводит к образованию смачивающего слоя Cu (рис. 5г) и к более быстрой коалесценции зародышей, а также к улучшению адгезии между Cu и TiN.
Особенности процесса электрохимического осаждения меди в отверстия с барьерным слоем на дне
В зависимости от состава электролита и режимов осаждения меди в отверстия с высоким аспектным отношением, могут наблюдаться два вида заполнения – конформное и снизу-вверх. Конформное и суперконформное заполнение (вдоль стенок отверстия), достигается введением специальных добавок, которые ингибируют осаждение на выступах и ускоряют рост меди в углублениях. В этом случае в межуровневых (переходных) отверстиях с высоким аспектным отношением (аспектное отношение, а.о. больше 5) могут образоваться полости, которые повышают сопротивление проводников и при высоких плотностях тока могут приводить к выходу из строя систем металлизации в процессе работы схем. Другой вариант заполнения без пустот – это заполнение снизу-вверх.
В нашем случае (а.о. равно 4 или меньше) использование сложных электролитов экономически и технологически нецелесообразно. Мы использовали второй вариант и два наиболее известных в гальванотехнике меди электролита.
Так как катодное осаждение может протекать только на проводящей поверхности, то при пропускании тока молекулы электролита сначала равномерно распределяются только на дне предварительно обработанного отверстия. В процессе роста снизу вверх в условиях ограниченного пространства площадь поверхности электрода внутри окна не изменяется, а диффузия ионов меди ускоряется (упрощается). Это приводит к увеличению скорости осаждения в центре окна. Ускоренный рост пленки в центре окна приводит к образованию выступа сначала над столбиком металла, а затем над отверстием (рис. 3). Такие же выступы образуются и при суперконформном заполнении [19].
Наличие выступа на поверхности электрода неизбежно приводит к неоднородному распределению напряженности электрического поля. В окрестности выступов с малым радиусом напряженность поля возрастает. Так как доставка ионов осуществляется совместно посредством электромиграции и диффузии, происходит развитие рельефа (быстрое растекание меди по поверхности образца).
Минимизировать этот эффект позволяют добавки фонового электролита, содержащего катионы с высокой подвижностью [20]. При осаждении меди в качестве фонового электролита чаще всего используется серная кислота (H2SO4). Подвижность ионов Н+ значительно превышает подвижность ионов Cu2+. Поэтому первые вносят основной вклад в дрейфовый ток, а вторые движутся к электроду в основном посредством диффузии.
Помимо фоновых добавок, электролиты осаждения меди содержат компоненты, которые за счет адсорбции на катоде влияют на характер реакции осаждения. Например, буферные добавки, обеспечивающие постоянство значения рН, содержат ионы Cl–, которые активируют процесс образования плоскостей, ориентированных в направлении [100]. Это приводит к формированию характерного рельефа покрытия, состоящего из кристаллитов кубической формы или дендритов. Обе эти добавки присутствуют в электролите № 1.
Электрохимическое осаждение тонких пленок меди на плоскую поверхность подложки проводят, как правило, при постоянном потенциале, близком к равновесному потенциалу осаждения данного металла в данном электролите, который для меди близок к нулю. При электрохимическом осаждении в пористую матрицу (через длинные узкие каналы) на барьерный слой затрудняется подача свежего электролита (циркуляция электролита), и, кроме того, может происходить закупорка пор пузырьками выделяющегося водорода при больших потенциалах (больше равновесного).
Влияние различных промежуточных слоев на потенциал электрохимического осаждения меди обсуждается в ряде работ. В работе [21] исследовался возможный механизм роста пленок меди на поверхности стеклянной подложки с покрытием ITO (оксид индия-олова) при различных потенциалах осаждения. Результаты этого исследования показали, что при более отрицательных потенциалах осаждения в трехэлектродной ячейке, образуются древовидные частицы, а не сплошная пленка, рис. 7.
Рис. 7.
Схематическое изображение (модель) формирования осадков меди в зависимости от потенциала осаждения [21]: а – при потенциале –0.5 В vs. Ag|AgCl; б – при –0.25 В vs. Ag|AgCl.
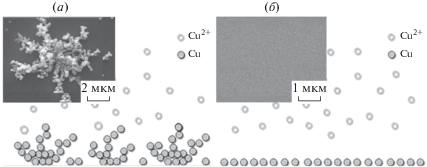
В работе [22] были описаны оптимальные условия осаждения пленок меди на плоскую поверхность слоя TiN. Цель эксперимента заключалась в получении зародышей меди с высокой плотностью однородного размера и полусферической формы. Хороший результат был получен при потенциалах осаждения в диапазоне от –0.5 до –1.0 В относительно электрода сравнения Ag/AgCl (в трехэлектродной ячейке). Традиционно используемые потенциалы, близкие к нулю (для меди), привели к формированию иглоподобных (needle-like) кристаллов неоднородного размера (–0.15 В) или к почковидным (nodular) сфероидальным частицам (–0.25 В). И в том, и в другом случае концентрация зародышей значительно ниже, чем при потенциале –1.0 В. Аналогичных исследований о непосредственном осаждении меди в отверстия с барьерным слоем в открытой печати не обнаружено.
Руководствуясь опытом прикладной гальваники и анализом литературных данных [23–25], мы использовали два известных (типовых) электролита – сульфатный (№ 1) и пирофосфатный (№ 2). В сульфатный электролит были введены ионы хлора (0.02 г/л HCl). Процесс осаждения проводили в удобной для эксплуатации двухэлектродной ячейке при одинаковом постоянном потенциале в обоих электролитах. Режим осаждения (потенциал осаждения) определяли экспериментально для данных условий (двухэлектродная ячейка) и типа образцов – не плоская поверхность, как при планарном осаждении, а матрица с глухими, достаточно глубокими (2000 нм) и узкими (диаметр 500 нм) отверстиями, на дне которых находится барьерный слой.
С учетом известных результатов [21, 22, 26, 27] и собственного опыта работы с двухэлектродной ячейкой, осаждение проводили при постоянном потенциале, близком к –1.6 В (1.6 ± 0.25 В).
На рис. 8 показаны зависимости тока (плотности тока)11 от времени осаждения и типа электролита после предварительной обработки образцов в течение 20 с. На рис. 9 показаны зависимости тока от времени осаждения в электролите № 2 при потенциале –1.6 В до (4) и после (1, 2, 3) обработки образцов при разном времени осаждения.
Рис. 8.
Зависимость тока электрохимического осаждения от времени осаждения и типа электролита: 1 – электролит № 1, 2 – электролит № 2.
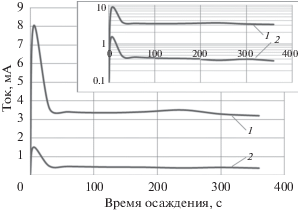
Рис. 9.
Зависимость тока электрохимического осаждения от времени осаждения и от времени обработки образцов: 1 – 10 с, 2 – 20 с, 3 – 30 с, 4 – без обработки.
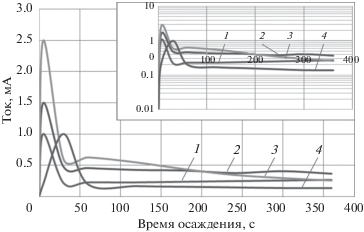
Анализ этих зависимостей показывает, что скорость осаждения, пропорциональная плотности тока, зависит от типа электролита в большей степени, чем от времени обработки поверхности образца. И в первом электролите она значительно выше, чем в электролите № 2.
Резкого изменения тока при выходе столбиков металла наружу не фиксируется. На одной подложке расположено четыре модуля с матрицей отверстий разного диаметра. Отверстия диаметром больше 500 нм заполнялись медленнее и постепенно, и это затрудняло контроль процесса по току. Чем больше диаметр отверстия, тем медленнее оно заполняется, поэтому ток практически не изменялся по мере постепенного заполнения всех отверстий разного диаметра.
Это хорошо согласуется с предполагаемой моделью роста столбиков снизу вверх, обсуждаемой ранее (см. выше). Увеличение скорости осаждения при подходе к поверхности приводит к быстрому растеканию меди по всей поверхности образца. Это нежелательный эффект22, который невозможно проконтролировать своевременным отключением ячейки (остановкой процесса осаждения). Поэтому скорость осаждения, которая выше в первом электролите, не играет решающей роли в данном процессе. Основное требование – контролируемое равномерное осаждение во все отверстия без пустот, выполняется при меньшей скорости заполнения, то есть в электролите № 2. Таким образом, полученные результаты показывают что, во-первых, достаточно 15–20 с обработки в используемом растворе, и, во-вторых, электрохимическое осаждение лучше проводить в пирофосфатном электролите № 2.
ЗАКЛЮЧЕНИЕ
Исследованы морфологические особенности наноструктур Si/SiO2/TiN/Cu, Si/TiSi2/TiN/Cu, изготовленных локальным электрохимическим осаждением меди в обычных промышленно используемых электролитах меднения.
Установлено, что при определенных условиях активации кремниевых пластин, обработанных в используемом буферном растворе, образуются равномерные (без пустот) столбики меди с хорошей адгезией к барьерному слою.
Подобран режим непосредственного электрохимического осаждения меди на поверхность барьерного слоя в отверстия кремниевых пластин, который позволяет провести 100%-ное (во все отверстия) осаждение металла без внутренних пустот. При одном и том же потенциале электрохимического осаждения (–1.6 В) в электролите № 2 происходит практически равномерное осаждение металла, что дает возможность контролировать степень заполнения путем изменения времени осаждения.
Были созданы структуры с частичным и полным (с шапками над поверхностью SiO2) заполнением отверстий. Морфологические исследования структур с частичным и полным заполнением отверстий показали, что кластеры меди состоят из древовидных кристаллитов размером ~30–50 нм.
Изготовленные экспериментальные кремниевые кристаллы с глухими отверстиями упорядоченной формы и изоляцией на поверхности этих отверстий соответствуют требованиям, предъявляемым к структурам, используемым для реализации на их основе трехмерных металлических межсоединений ИМС [28]. Кроме того массивы упорядоченных микроотверстий в кремнии могут быть использованы в электронике при изготовлении конденсаторов повышенной емкости [29], фотонных кристаллов [30], а также в качестве микроканальных пластин для электронных умножителей [31].
Pабота выполнена в pамках Госудаpственной научно-технической пpогpаммы “Фотоника, опто- и микроэлектроника”, подпрограмма “Микро- и наноэлектроника” Министеpства обpазования Pеспублики Белаpусь.
Авторы благодарны сотрудникам ОАО “Интеграл” за помощь при изготовлении экспериментальных образцов, оказанную в рамках совместного проекта данной ГНТП.
Список литературы
Garrou P., Bower C., Ramm P. Handbook of 3D Integration. Wiley-VCH. 2008. ISBN: 978-3-527-32034-9.https://doi.org/10.1002/9783527623051
Ramm P., Klumpp A., Merkel R. et al. 3D system integration technologies // Mat. Res. Soc. Symp. Proc., 2003. V. 766. P. E5.6.1.
Knickerbocker J.U., Andry P.S., Dang B. et al. Three-dimensional silicon integration // IBM J. Res. Dev. 2008. V. 52. P. 553.https://doi.org/10.1147/JRD.2008.5388564
Wolf M.J., Dretschkow T., Wunderle B. et al. High Aspect Ratio TSV Copper Filling with different Seed Layers // in: ECTC: Electronic Components and Technology Conference, 27–30 May 2008, Lake Buena Vista, FL (IEEE, 2008). P. 563.
Radisic A., Lühn O., Philipsen H.G.G. et al. Copper plating for 3D interconnects // Microelectron. Eng. 2011. V. 88. P. 701.https://doi.org/10.1016/j.mee.2010.06.030
Electroless Plating: Fundamentals & Applications / Ed. by Mallory G.O., Hajdu J.B. Orlando: American Electroplaters and Surface Finishers Society, 1990.
Toimil-Molares M.E., Buschmann V., Dobrev D. et al. Single-Crystalline Copper Nanowires Produced by Electrochemical Deposition in Polymeric Ion Track membranes // Adv. Mater. 2001. V. 13. P. 62. https://doi.org/10.1002/1521-4095(200101)13:1<62:: AID-ADMA62>3.0.CO;2-7
Lane M.W., Murray C.E., McFeely F.R. et al. Liner materials for direct electrodeposition of Cu // Appl. Phys. Lett. 2003. V. 83. P. 2330.https://doi.org/10.1063/1.1610256
Edelstein D., Heidenreich J., Goldblatt R. et al. Full Copper Wiring in a Sub-0.25μm CMOS ULSI Technology. Pages 773–776 // of: Proc. of the IEEE Int. Electr. Dev. Meet. 1997. New York: IEEE. P. 773.
Edelstein D.C., Sai-Halasz G.A., Mii Y.J. LSl on-chip interconnection performance simulations and measurements // IBM J. Res. Dev. 1995. V. 39. P. 383.https://doi.org/10.1147/rd.394.0383
Song C., Wang Z., Chen Q. et al. High aspect ratio copper through-silicon-vias for 3D integration // Microelectron. Engin. 2008. V. 85. P. 1952 .https://doi.org/10.1016/j.mee.2008.05.017
Radisic A., Cao Yang, Taephaisitphongse Premratn et al. Direct Copper Electrodeposition on TaN Barrier Layers // J. Electrochem. Soc. 2003. V. 150 № 5. P. C362. https://doi.org/10.1149/1.1565137
Moffat T.P., Walker M., Chen P.J. et al. Electrodeposition of Cu on Ru Barrier Layers for Damascene Processing // J. Electrochem. Soc. 2006. V. 153 № 1. P. C37. https://doi.org/10.1149/1.2131826
Park K.S., Kim S. Seedless Copper Electrodeposition onto Tungsten Diffusion Barrier // J. Electrochem. Soc. 2010. V. 157. P. D609. https://doi.org/10.1149/1.3491351
Турцевич А.С., Колос В.В., Адашкевич С.В. и др. Способ формирования пленки дисилицида титана на кремниевой подложке. Пат. BY № 16839, C1. 2013.02.28.
Маркевич М.И., Чапланов А.М., Першукевич П.П. и др. Роль нитрида титана в технологии формирования силицидов титана // 12-я Межд. конф. “Взаимодействие излучений с твердым телом”, 19–22 сентября 2017 г. Минск, Беларусь, С. 464.
Mikolajunas M., Kaliasasa R., Andruleviciusb M. et al. A study of stacked PECVD silicon nitride films used for surface micromachined membranes // Thin Solid Films. 2008. V. 516 № 23. P. 8788. https://doi.org/10.1016/j.tsf.2008.06.063
Brene E.A., Mel’nikov V.I. Pattern selection in two-dimensional dendritic growth // Adv. in Phys. 1991. V. 40. P. 53.https://doi.org/10.1080/00018739100101472
Хмыль A.A., Кушне Л.К. Металлизация отверстий при создании межсоединений элементов в ИМС // Современные электрохимические технологии и оборудование: материалы конференции, Минск, 24–25 ноября 2016 г. / Белорусский государственный технологический университет. Минск: БГТУ. 2016. С. 10.
Власова Е.Г., Петрухин О.М., Кузнецова Л.Б. Аналитическая химия. Химические методы анализа. М: Бином. Лаборатория знаний. 2017. ISBN: 978-5-906828-19-4.
Chenhuinan Wei, Guoxing Wu, SanjunYang et al. Electrochemical deposition of layered copper thin films based on the diffusion limited aggregation // Sci. Rep. 2016. V. 6. P. 1. https://doi.org/10.1038/srep34779
Oskam Gerko, Vereecken P.M., Searson P.C. Electrochemical Deposition of Copper on n-Si/TiN // J. Electrochem. Soc. 1999.V. 146. № 4. P. 1436.https://doi.org/10.1149/1.1391782
Bicelli L.P., Bozzini B., Mele C., D’Urzo L. A review of nanostructural aspects of metal electrodeposition // Int. J. Electrochem. Sci. 2008. V. 3. № 4. P. 356.
Nikolic N.D., Popov K.I., Pavlovic L.J., Pavlovic M.G. Morphologies of copper deposits obtained by the electrodeposition at high overpotentials // Surf. and Coatings Technol. 2006. V. 201. № 3–4. P. 560.https://doi.org/10.1016/j.surfcoat.2005.12.004
Shao W.B., Zangari G. Dendritic growth and morphology selection in copper electrodeposition from acidic sulfate solutions containing chlorides // J. Phys. Chem. C. 2009. V. 113(23). P. 10097.https://doi.org/10.1021/jp8095456
Han Y.J., Zhang X., Leach G.W. Shape control of electrodeposited copper films and nanostructures through additive effects // Langmuir. 2014. V. 30. P. 3589.https://doi.org/10.1021/la500001j
Ivanova Yu.A., Ivanou D.K., Fedotov A.K. et al. Electrochemical deposition of Ni and Cu onto monocrystalline n-Si(100) wafers and into nanopores in Si/SiO2 template // J. Mater. Sci. 2007. V. 42. P. 9163. https://doi.org/10.1007/s10853-007-1926-x
Defforge Thomas, Billoué Jérôme, Diatta Marianne et al. Copper-selective electrochemical filling of macropore arrays for through-silicon via applications // Nanoscale Res. Lett. 2012. V.7. P. 375. http://www.nanoscalereslett.com/content/7/1/375.https://doi.org/10.1186/1556-276X-7-375
Vega Didac, Reina Jordi, Martí Ferran et al. Macroporous silicon for high-capacitance devices using metal electrodes // Nanoscale Res. Lett. 2014. V. 9(473). P. 1.
Жарова Ю.А., Федулова Г.В., Гущина Е.В. и др. Технология получения одномерных фотонных кристаллов с помощью фотоэлектрохимического травления кремния // ФТП. 2010. Т. 44. Вып. 7. С. 986.
Dixit P., Miao J. High aspect ratio vertical through-vias for 3D MEMS packaging applications by optimized three-step deep RIE // J. Electrochem. Soc. 2008. V. 155. P. H85.https://doi.org/10.1149/1.2814081
Дополнительные материалы отсутствуют.
Инструменты
Микроэлектроника