Микроэлектроника, 2021, T. 50, № 1, стр. 21-26
Влияние растекания резиста при его сухом электронно-лучевом травлении на латеральное разрешение
А. Г. Исаев a, b, *, Ф. А. Сидоров a, **, А. Е. Рогожин a, ***
a Физико-технологический институт имени К.А. Валиева Российской академии наук,
Нахимовский проспект
117218 Москва, 34, корп. 1, Россия
b Московский физико-технический институт (государственный университет)
141701 Долгопрудный, Институтский переулок, 9, Россия
* E-mail: isaev.ag@phystech.edu
** E-mail: fedor.sidorov@phystech.edu
*** E-mail: rogozhin@ftian.ru
Поступила в редакцию 15.04.2020
После доработки 29.06.2020
Принята к публикации 20.08.2020
Аннотация
Дана оценка влияния процесса растекания резиста на снижение латерального разрешения при его сухом электронно-лучевом травлении. Показано, что реальная ширина линий не может быть объяснена рассеянием электронов в образцах. На основе профилей, полученных с помощью атомно-силовой микроскопии и растровой электронной микроскопии, продемонстрировано, что процесс растекания может существенно влиять на изменение ширины линий. При помощи моделирования в программе Surface Evolver было показано, что процесс растекания в значительной степени, объясняет уширение тренчей, сформированных СЭЛТР.
1. ВВЕДЕНИЕ
Сухое электронно-лучевое травление резиста (СЭЛТР) – литографический метод, позволяющий получать синусоидальные и ступенчатые структуры [1–3]. В отличие от классической электронно-лучевой литографии метод СЭЛТР не требует стадии жидкостного проявления – формирование изображения происходит за счет деполимеризации молекул полиметилметакрилата (ПММА) и формировании летучих молекул мономеров при температурах выше 120°С. Метод СЭЛТР имеет целый ряд достоинств, таких как высокое разрешением по вертикали (2–5 нм при шероховатости 1 нм) [1], отсутствие необходимости в органических проявителях, и значительно меньшие дозы экспонирования по сравнению с классической электронно-лучевой литографией и, как следствие, меньшее время экспонирования. К недостаткам СЭЛТР можно отнести сравнительно низкое латеральное разрешение (порядка 100–150 нм), а также невысокую контрастность изображения (0.7–1.5). Среди возможных причин низкого латерального разрешения СЭЛТР рассеяние электронного пучка в ходе экспонирования и растекание резиста при повышенной температуре.
Ранее, с помощью моделирования взаимодействия электронного пучка с веществом резиста на основе прямого Монте-Карло подхода, были рассчитаны пространственные распределения разрывов полимерных цепей, поглощенной резистом энергии и молекулярной массы резиста в слое ПММА [4]. В частности, оценивалось влияние рассеяния электронов в ходе экспонирования на разрешение СЭЛТР с учетом процесса деполимеризации в ходе экспонирования при повышенной температуре, но без учета растекания резиста. На рис. 1 приведены профили, полученные с помощью СЭЛТР и в результате моделирования. Как видно профиль линии, полученный экспериментально, существенно отличается от рассчитанного.
Рис. 1.
Профили линий: 1 – полученные с помощью СЭЛТР; 2 – в результате моделирования СЭЛТР без учета растекания [4].
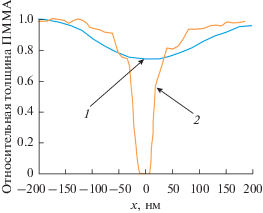
Таким образом, рассеяние электронного пучка в ходе экспонирования не может объяснить уширение линий в процессе СЭЛТР. Необходимо оценить влияние процесса растекания резиста на форму профиля линий.
2. ЭКСПЕРИМЕНТ
На кремниевую пластину методом центрифугирования при 1000 об./мин в течение 180 с наносился резист ПММА 950 К Microresist A2. Толщина резиста составила 80 нм. Затем образцы подвергались сушке при 180°С в течение 180 с. Экспонирование проводилось в электронном литографе Raith-150 при комнатной температуре. Энергия пучка – 10 кэВ, ток – 100–200 пА, диаметр пучка – 1.5–5 нм. На каждом образце были проэкспонированы линии с различными дозами (50–2500 пкКл/см) и контрольные линии шириной 1 мкм и дозой 150 мкКл/${\text{с}}{{{\text{м}}}^{2}}.$
После этого некоторые образцы в течение 30 с проявлялись в смеси метил изобутил кетона и изопропилового спирта в соотношении 1 : 3. После этого образцы отжигались при температурах в диапазоне 100–150°С в течение 0–15 мин. Готовые образцы исследовались при помощи атомно-силового микроскопа (АСМ) модели Nanopics 2100 а также растрового электронного микроскопа (РЭМ) Zeiss Ultra 50. Оба метода имеют существенные недостатки применительно к данному эксперименту. АСМ может искажать профили линий в следствие конечных размеров зонда, как показано на рис. 2. Несмотря на то, что радиус закругления новой иглы достаточно мал, в процессе использования он может достигать 100 нм. Основной недостаток РЭМ в том, что электронный пучок микроскопа может дополнительно экспонировать образец. В результате полученное изображение может не соответствовать исходной структуре.
3. МОДЕЛИРОВАНИЕ
Теоретическое моделирование растекания резиста проводилось при помощи программы Surface Evolver (SE) [5–7]. При моделировании структурные свойства моделируемого 3D-объекта представляются свойствами 2D-поверхностей. Для этого вся поверхность объекта разбивается на триангулированные 2D-поверхности. Каждый поверхностный элемент (треугольник) является отдельной гранью и определяется тремя вершинами. Каждой грани присваивается значение определенной поверхностной энергии. В случае поверхности полимера, это поверхностное натяжение полимера при соответствующей температуре. Моделируемая структура представляется как бесконечно длинная. Практически это реализуется с помощью особых граничных условий (зеркальными плоскостями) на концах моделируемой области. При моделировании полная энергия системы ${{E}_{{tot}}}$ – это поверхностная энергия свободной поверхности полимера ${{E}_{p}}$ минус энергия, поверхности между полимером и подложкой ${{E}_{{ps}}}$ и в зеркальных плоскостях ${{E}_{m}}$.
Физический смысл этого в том, что растекание уменьшает полную энергию системы путем уменьшения свободной поверхности полимера и увеличивать зоны контакта с поверхностями. Это согласуется с реальным поведением текучих веществ при смачивании.
Соответствующие энергии ${{E}_{x}}$ рассчитываются как сумма энергий ${{E}_{{x,i}}}$ всех n элементарных граней i в трех различных областях свободной поверхности полимера (x = p), области контакта полимер–подложка (x = ps) и зеркальных плоскостях (x = m).
Энергии отдельных граней ${{E}_{{x,i}}}$ вычисляются из поверхностного натяжения γ грани i и площади этой грани:
(3)
${{E}_{{x,i}}} = \frac{{{{\gamma }_{i}}}}{2}\left| {{{{\bar {e}}}_{0}} \times {{{\bar {e}}}_{1}}} \right|,$Сила, действующая на каждую вершину, рассчитывается из градиента энергетического поля, определенного выше, и положения вершины в этом энергетическом поле. SE работает в режиме нормализации площади, где скорость вершины косвенно пропорциональна площади граней, окружающих эту вершину. Поскольку каждая грань i имеет три связанные с ней вершины, относительный вклад площади в силу для одной вершины равен 1/3 площади окружающих граней A. Сила F, приложенная к вершине, позволяет рассчитать скорость движения этой вершины в режиме нормализации площади как
Для расчета вектора перемещения вершин δ в SE используется параметр s, называемый масштабным коэффициентом (scale factor):
Масштабный коэффициент является физическим представлением времени. Общая сумма масштабных коэффициентов, используемых на каждой итерации, соответствует общему времени моделируемого процесса. SE работает таким образом, чтобы оптимизировать масштабный коэффициент на каждой итерации для быстрой и плавной сходимости к конечной форме, соответствующей минимально энергии.
4. РЕЗУЛЬТАТЫ И ИХ ОБСУЖДЕНИЕ
На рис. 3 приведены профили линий на образце, отожженном при температуре 130°С в течение 5 мин в сравнении с профилями линий на не отожженном образце. Линии с дозой менее 1000 пКл/см стали заметно шире, что можно объяснить растеканием резиста. Вследствие увеличения ширины, увеличилась и глубина проникновения зонда, поэтому глубина тренчей оказалась больше после отжига. Вблизи линий с дозой более 1000 пКл/см по краям наблюдается увеличение толщины слоя ПММА. Можно предположить, что утолщение ПММА связано с процессом переосаждения мономера. С обеих сторон линии существуют проэкспонированные области, в которых молекулярная масса ПММА недостаточно мала для растворения в процессе проявления. При нагреве может происходить самопроявление этих областей, и образовавшиеся мономеры могут осаждаться на поверхности вблизи канавки. Возможны и другие объяснения данного явления, например, «разбухание» резиста при нагреве.
Рис. 3.
Профили линий, полученных экспонированием с разными дозами: (а) на не отожженных образцах; (б) после отжига при температуре 130°С в течение 5 мин.
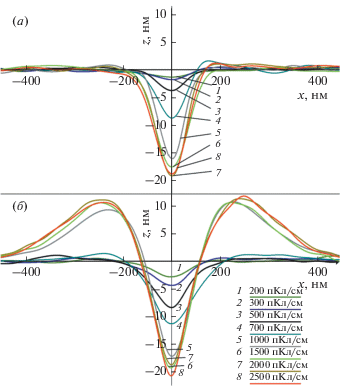
Изображения на РЭМ подтверждают полученные данные (рис. 4). Как видно, ширина тренчей увеличилась, а их края стали более пологими. Помимо этого наблюдается процесс проявления линий, который также вносит вклад в изменение профиля
Рис. 4.
РЭМ изображения профилей линий. Слева: не отожженные образцы; справа: после отжига при температуре 130°С в течение 5 мин.

При температуре отжига 100°С увеличение толщины резиста краям тренча не наблюдаются. Процесс растекания происходит медленно или отсутствует вовсе. Сколько-нибудь заметного изменения профилей линий не наблюдается.
Также были изучены профили растекания контрольных линий шириной 1 мкм (рис. 5). При 110°С процесс растекания происходит довольно медленно (либо отсутствует вовсе), значительного изменения профиля не наблюдается. При 120°С наблюдается слабое увеличение ширины линии (20–30 нм на полувысоте). При 130°С происходит заметное изменение профиля линии (порядка 80 нм). В краевой области происходит описанное выше увеличение толщины слоя резиста. При 150°С этот процесс вносит еще больший вклад в изменение профиля. Ширина линии увеличилась более чем на 150 нм. Следовательно, при 150°С растекание может вызывать значительное уширение линий.
Таким образом, при температурах ниже 120°С заметного изменения профиля не наблюдается. При температурах близких к 120°С можно считать, что изменение профиля обусловлено только растеканием. При температурах выше 120°С процесс растекания также играет существенную роль, однако большой вклад в формирование профиля могут вносить различные неучтенные явления (проявление, переосаждение и др).
5. СРАВНЕНИЕ ПОЛУЧЕННЫХ РЕЗУЛЬТАТОВ С МОДЕЛИРОВАНИЕМ В SURFACEEVOLVER
Было произведено моделирование растекания резиста при помощи программы Surface Evolver. Ширина канавки зависит от дозы экспонирования и определяется из полученных АСМ исходных профилей. Важным параметром моделирования является зависимость текучести резиста от температуры. Теоретический расчет данной зависимости довольно сложен. Поэтому масштабный коэффициент SE считался как функция и времени и температуры, причем зависимость от времени – линейная, а зависимость от температуры – неизвестна.
На рис. 6 приведены АСМ и промоделированные профили для дозы 2500 пКл/см и времени 5 мин при различных температурах. На основе результатов моделирования можно построить зависимость масштабного коэффициента от температуры и времени. Истинный характер данной зависимости не известен, однако в диапазоне температур 120–150°C она хорошо описывается законом Аррениуса:
где $k = \,\,~8.6 \times {{10}^{{ - 5}}}{\text{эВ}} \cdot {{{\text{К}}}^{{ - 1}}}$ – постоянная Больцмана, t – время отжига.Рис. 6.
Промоделированные и АСМ профили с дозой 2500 пКл/см после отжигов при различных температурах в течение 5 мин.
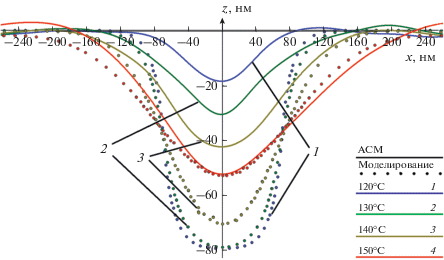
На основе данной зависимости было промоделировано растекание контрольных линий. На рис. 7 приведено сравнение растекания в течение 15 мин при различных температурах промоделированных профилей с профилями АСМ для линий шириной 1 мкм.
Рис. 7.
Профили линий шириной 1 мкм, полученные с помощью моделирования и АСМ (профили после отжигов при различных температурах смещены вдоль оси абсцисс).
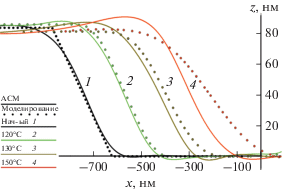
Для температуры 120°С промоделированный профиль совпадает с профилем АСМ. При 130°С существует небольшое расхождение профилей, вызванное, по всей видимости, проявлением резиста в экспонированной области по краям тренча во время отжига. При 150°С проявление происходит значительно быстрее, что объясняет сильное расхождение в форме профилей. Однако полученная при моделировании ширина линии в верхней части тренча совпадает с реальной.
На рис. 8 приведены профили линии с дозой 2000 пКл/см, отожженной 5 мин при 130°С, полученные тремя различными методами: АСМ, РЭМ и моделирование. Как видно, ширина линии, полученная всеми тремя методами, приблизительно одинакова и составляет около 250 нм. То есть имеет место двух-трех кратное увеличение ширины по сравнению с не отожженным образцом. При этом глубина полученных профилей отличается. В случае АСМ, это может быть связано с тем, что зонд не смог достичь дна тренча. Расхождение между РЭМ и моделированием можно объяснить проявлением резиста при отжиге, которое не учитывалось при моделировании. Возможно увеличение глубины профиля произошло вследствие экспонирования резиста электронным пучком РЭМ.
6. ЗАКЛЮЧЕНИЕ
На основе профилей, полученных АСМ, РЭМ и моделированием, показано, что процесс растекания может существенно влиять на изменение формы линий. При высоких температурах (более 120°С) в изменение профиля могут вносить такие явления, как переосаждение и проявление во время отжига. Моделирование процесса растекания было произведено в программе Surface Evolver. Сравнение промоделированных профилей с полученными на АСМ и РЭМ показало, что процесс растекания может приводить к трехкратному снижению латерального разрешения СЭЛТР, что, в значительной степени, объясняет уширение канавок, сформированных СЭЛТР.
Работа выполнена в рамках Государственного задания ФТИАН им. К.А. Валиева РАН Минобрнауки РФ по теме № 0066-2019-0004.
Список литературы
Bruk M.A., Zhikharev E.N., Rogozhin A.E.Formation of micro- and nanostructures with well-rounded profile by new e-beam lithography principle // Microelectronic Engineering. 2016. V. 155. P. 92–96.
Bruk M.A., Zhikharev E.N., Kalnov V.A. A new method of formation of the masking image (relief) directly during the electron-beam exposure of the resist// Russian Microelectronics. 2013. V. 42. № 5. P. 261–269.
Bruk M.A., Zhikharev E.N., Streltsov D.R. Some peculiarities of a new method of microrelief creation by the direct electron-beam etching of resist // Computer Optics. 2015. V. 39. № 2. P. 204–210.
Rogozhin A.E., Sidorov F.A., Bruk M.A. Simulation of dry e-beam etching of resist and experimental evidence // Proc. SPIE 11022. 2018. P. 110221O.
Kirchner R., Schift H. Mobility based 3D simulation of selective, viscoelastic polymer reflow using surface evolver // J. Vac. Sci. Technol. 2014. V. 32. P. 06F701-1-7.
Kirchner R., Schift H. Thermal reflow of polymers for innovative and smart 3D structures: A review // Semiconductor Processing. 2019. V. 92. P. 58–72.
Brakke K.A. Surface Evolver Manual. Susquehanna University. 2013 // http://facstaff.susqu.edu/b/brakke.
Дополнительные материалы отсутствуют.
Инструменты
Микроэлектроника