Микроэлектроника, 2022, T. 51, № 6, стр. 478-487
Диэлектрический барьер в субтрактивном процессе формирования системы медной металлизации
А. А. Орлов 1, 2, *, А. А. Резванов 1, 2, В. А. Гвоздев 1, Г. А. Орлов 3, Д. С. Серегин 3, П. И. Кузнецов 1, Т. Блумберг 4, А. А. Веселов 4, Т. Сузуки 4, Е. Н. Морозов 5, К. А. Воротилов 3
1 АО “Научно-исследовательский институт молекулярной электроники”,
124460 Москва, Зеленоград, улица Академика Валиева, 6/1, Россия
2 Московский физико-технический институт (НИУ)
141701 Долгопрудный,
Институтский переулок, 9, Россия
3 МИРЭА – Российский технологический университет
119454 Москва, Проспект Вернадского, 78, Россия
4 Picosun Oy
FI-02430 Masala, Masalantie, 365, Finland
5 ПАО “Микрон”,
124460 Москва, Зеленоград, улица Академика Валиева, 6/1, Россия
* E-mail: aorlov@niime.ru
Поступила в редакцию 21.04.2021
После доработки 12.05.2022
Принята к публикации 12.05.2022
- EDN: EVSUXK
- DOI: 10.31857/S0544126922700107
Аннотация
Статья посвящена исследованию различных способов формирования диэлектрических диффузионных барьеров между открытыми участками меди и органосиликатным low-k диэлектриком в субтрактивном методе формирования системы металлизации, в котором сначала формируют линии металла, а затем осаждают low-k диэлектрик. В качестве low-k диэлектрика использовались пленки плотного и пористого органосиликатного стекла, осажденные методом химического осаждения из растворов. Проведено сравнение барьерных слоев AlN, сформированных методом атомно-слоевого осаждения, и барьеров SiCN, осажденных методом химического осаждения из газовой фазы, стимулированного плазмой. Продемонстрировано успешное формирование модельной структуры медной металлизации с использованием барьеров AlN.
1. ВВЕДЕНИЕ
С уменьшением топологических размеров элементов интегральных схем (ИС) возникает необходимость применения новых материалов и технологий, используемых на этапе формирования системы металлизации, так как RC-задержка, перекрестный шум и потребляемая мощность, связанные с протеканием заряда по близкорасположенным ультратонким проводникам, начинают играть критическую роль в производительности и энергоэффективности конечных элементов [1, 2]. Согласно международной дорожной карте по развитию устройств и систем (IRDS), начиная с технологических норм 90 нм, на замену классической алюминиевой металлизации и диоксиду кремния (SiO2; диэлектрическая проницаемость которого составляет k ≈ 3.9) пришли медь (Cu), удельное сопротивление которой меньше, чем у алюминия (1.7 мкОм см по сравнению с 2.8 мкОм см у алюминия), и low-k диэлектрик (диэлектрик с диэлектрической постоянной ниже, чем у диоксида кремния) [3, 4]. На текущий момент, в качестве low-k диэлектрика обычно используют материалы на основе органосиликатных стекол (OSG диэлектрик), где уменьшение диэлектрической проницаемости материала, согласно уравнению Клаузиуса-Моссотти, происходит за счет снижения поляризуемости вещества на единицу объема. Для этого, первоначально в структуре классического диоксида кремния производилась замена кремний–кислородных связей на кремний–углеродные путем замещения части мостиковых атомов кислорода на терминальные метильные CH3 группы (SiOCH диэлектрик). Однако для дальнейшего уменьшения диэлектрической проницаемости в такой диэлектрический материал вводят искусственную пористость.
Несмотря на успехи в создании высокопористых диэлектрических пленок с очень низким значением диэлектрической проницаемости (k ≈ 2.3), существуют большие трудности с внедрением этих материалов в производство интегральных схем (ИС). Во-первых, пористость резко ухудшает механические и термические свойства материала, что сказывается на стадии сборки ИС и ее последующем функционировании [5]. Во-вторых, в классическом процессе интеграции (Dual Damascene) пористый диэлектрик подвергается плазмохимическому травлению (ПХТ). Во время процесса ПХТ на диэлектрик воздействуют радикалы, ионы и фотоны вакуумного ультрафиолета (ВУФ), что приводит к разрушению гидрофобных Si–CH3 связей и замещению их гидрофильными Si–OH связями. Дополнительно, на стенки сформированных траншей в диэлектрике в технологии Dual Damascene наносятся барьерные слои для предотвращения диффузии Cu в структуру диэлектрика. Более того, нанесение металлических диффузионных барьеров на поверхность диэлектрика может также привести к проникновению атомов металла в пористую структуру диэлектрика [6, 7]. Во всех этих процессах свойства пленки low-k диэлектрика сильно деградируют. Под деградацией диэлектрика понимается увеличение диэлектрической проницаемости, снижение пробойного напряжения low-k материала и уменьшение времени жизни во время эксплуатации прибора (снижение надежности) [8].
В настоящее время предложены различные методы для защиты пористого low-k диэлектрика от деградации такие как: метод заполнения пор жертвенным полимером из раствора [9] или газовой фазы [10] (позволяет предотвратить проникновение радикалов вглубь диэлектрика), криогенное травление с предварительным заполнением пор газом, в котором будет производиться травление [11, 12] (основан на абсорбции и десорбции газа при изменении температуры, обеспечивает временное заполнение пор). Однако указанные методы все равно приводят к незначительной деградации диэлектрика и добавлению дополнительных операций в технологический маршрут.
Согласно IRDS, в системе металлизации технологий с топологическими нормами 32 нм и ниже используется SiOCH диэлектрик со значением диэлектрической проницаемости 2.7–3.2, так как, на текущий момент, отсутствуют надежные и эффективные методы интеграции диэлектрических материалов с k < 2.7 [3].
В процессе Damascene формирования уровня системы металлизации электрическое соединение элементов СБИС создается за счет предварительного формирования траншей в диэлектрическом слое и последующем их заполнением металлом [13]. Для исключения деградации диэлектрика рассматривается вопрос о возможном переходе к субтрактивному процессу формирования системы металлизации, который отрасль использовала для создания Al металлизации. В данном процессе предварительно формируют медные проводники, а затем проводят осаждение диэлектрика [14–18].
На рис. 1 схематично показан процесс изготовления медной системы металлизации с использованием субтрактивного процесса.
Рис. 1.
Схема субтрактивного процесса формирования медной металлизации: A, B) формирование жертвенного слоя (тетраэтоксисилан – TEOS), в котором с помощью процесса ПХТ формируются траншеи; C) осаждение барьерного слоя (TaN/Ta) с последующим осаждением меди; D) ХМП полученной структуры и удаление жертвенного диэлектрика (в растворе плавиковой кислоты) и осаждение дополнительного барьера с целью закрыть открытые участки меди; E) заполнение промежутков между проводниками low-k диэлектриком.
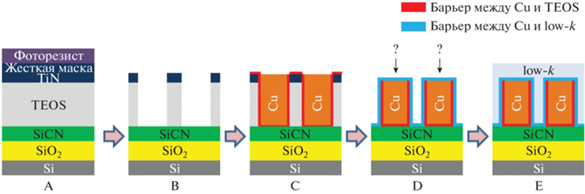
Медь легко диффундирует в диэлектрик под действием теплового или электрического воздействия. Более того, в отличие от алюминия, где электромиграция, в основном, происходит по границе между зернами, у меди электромиграция наблюдается по открытой поверхности [19, 20]. Это происходит, в частности, вследствие того, что после ХМП верхней поверхности медного проводника последняя очень слабо прилипает к диэлектрику, покрывающему проводник [21]. В результате, по этой границе энергия активации атомной (вакансионной) диффузии оказывается значительно меньше, чем на межзеренной границе. В то же время поверхностная диффузия практически невозможна в алюминиевой металлизации, так как ее поверхность всегда покрыта естественным окислом Al2O3.
По этим причинам поверхность меди должна быть окружена хорошим диффузионным барьерным слоем. Обычно, барьерный слой по бокам и снизу линии представляет собой металлический слой Ta/TaN (TaN обеспечивает хорошую адгезию к диэлектрику, а Ta хорошую смачиваемость зародышами медного слоя), а сверху линии диэлектрическую барьерную пленку [22, 23]. Эффективность диэлектрического барьера и его адгезия к слою меди намного хуже, чем у металлического барьера. Однако использование того же слоя TaN/Ta является весьма проблематичным, ввиду технологических сложностей из-за необходимой высокой селективности осаждения на линиях меди [24]. Более того, дополнительное осаждение TaN/Ta существенно увеличит толщину диэлектрического барьера, что, в свою очередь, приведет к нежелательному увеличению RC-задержки.
Таким образом, основной проблемой субтрактивного метода является поиск материала барьера для исключения контакта открытых участков меди с low-k диэлектриком и нового метода осаждения такого материала. К данному барьерному слою предъявляются строгие требования, так как он должен быть достаточно тонким, чтобы избежать существенного роста RC-задержки. С другой стороны, его толщина должна быть достаточной для предотвращения диффузии ионов и атомов меди. Таким образом, было решено исследовать методы формирования потенциальных диэлектрических барьерных слоев между открытыми участками меди и low-k диэлектриком.
2. ИСПОЛЬЗУЕМЫЕ МАТЕРИАЛЫ И МЕТОДИКА
В настоящее время ведется интенсивный процесс поиска новых материалов для диэлектрических барьеров между открытыми участками меди и low-k диэлектриком, а также новых методов их формирования, так как с уменьшением проектных норм толщина барьерных слоев также снижается [25]. Для интеграции в технологический процесс материал должен обладать следующими характеристиками: иметь хорошую адгезию к нижележащим слоям, препятствовать диффузии и электромиграции меди, не пропускать пары воды для предотвращения окисления меди. Потенциальными барьерными слоями могут являться следующие диэлектрические материалы: SiCN (k ≈ 4.8), CuSiN (k ≈ 4.6; используется в качестве дополнительного барьера к SiCN), AlN (k ≈ 9.0). Пленки SiCN и CuSiN были сформированы из газовой фазы (PECVD) на установке AMAT Producer. Для формирования диэлектрической пленки AlN использовался метод атомно-слоевого осаждения (Atomic Layer Deposition – ALD) и установка R-200 Advanced (Picosun). О деталях процесса нанесения исследуемых барьеров будет рассказано далее.
Субтрактивный метод формирования системы металлизации не предполагает плазменного травления low-k диэлектрика. Однако, при этом, требуется равномерное заполнение промежутков между проводниками. Классический метод формирования диэлектрических слоев из газовой фазы не всегда (например, в случае близко расположенных проводников с расстоянием между ними ≤30–40 нм для технологий с проектными нормами 32 нм и ниже) обеспечивает требуемые свойства равномерного и сплошного заполнения промежутка. В данной работе используется метод химического осаждения из раствора (Chemical Solution Deposition – CSD), который позволяет легко формировать пленки с минимальными значениями диэлектрической постоянной, а также отлично подходит для заполнения узких промежутков. Пленкообразующий раствор был приготовлен в результате гидролиза и конденсации тэтраэтоксисилана (TEOS, 99.999%, Sigma Aldrich) и метилтриэтоксисилана (MTEOS, 99.9%, Sigma Aldrich) в спиртовой среде (этанол, 2-пропанол) в присутствии катализатора HCl (37%) в следующем соотношении компонентов: [Si(OC2H5)4 + + CH3Si(OC2H5)3]/H2O/HCl = 1/4/0.002 [26]. Раствор термостатировали при температуре 60°С в течение 3 часов при постоянном перемешивании. После этого часть раствора использовали для формирования плотных пленок органосиликатного стекла (OSG), а в другую часть, добавляли поверхностно-активное вещество (ПАВ) Brij 30 [C12H25(OCH2CH2)4OH] 19.3 вес. % (относительно массы алкоголятов кремния) и использовали для нанесения пористых пленок органосиликатного стекла (p-OSG). Гидроксильные группы конденсируются и образуют кремний-кислородную структуру, в то время как концевые метильные CH3 группы (содержащиеся в MTEOS), которые не подвергаются гидролизу, не участвуют в процессе конденсации. В результате образуется каркас подобный каркасу кремния с мостиковыми атомами кислорода (–Si–O–Si–) вместе с концевыми метильными группами, преимущественно расположенными на стенках пор. Молекулы ПАВ Brij 30 при достижении некой критической концентрации взаимодействуют между собой, образуя органический шаблон для матричного материала, который удаляется путем термодеструкции в процессе отжига пленки. Подробнее методы формирования, структурные и физические свойства пористых органосиликатных силикатных пленок, сформированных с использованием Brij 30, изложены в [27–29].
Нанесение пленок проводилось на пластины диаметром 200 мм с тестовыми элементами в виде параллельных медных змеек (рис. 2) с выведенными контактными площадками (высота проводников 0.2 мкм). Расстояние между параллельными медными проводниками варьируется от 90 до 640 нм (схематичное изображение тестовых медных структур представлено на рис. 3). Отработка нанесений на подложках с тестовыми элементами проводилась на установке нанесения SOG растворов фирмы Brewer Science CBX200, включающей в себя модуль центрифугирования и модуль нагревания (hot-plate). Нанесение раствора осуществлялось вручную путем подачи из дозатора жидкого прекурсора на подложку, расположенной на спиннере. Скорость вращения центрифуги составляла 2500 оборотов/мин. Сушка пленок осуществлялась на hot-plate на первом этапе при 100–150°C (мягкий отжиг) в течение 30 мин; на втором этапе в печи в диапазоне температур 400°C (спекание). В результате мягкого отжига формируется каркас диэлектрика, а высокотемпературный отжиг позволяет сформировать пористую структуру.
Рис. 2.
Схематичное изображение тестового элемента в виде параллельных змеек: общий вид и увеличенный фрагмент дорожек соответственно.
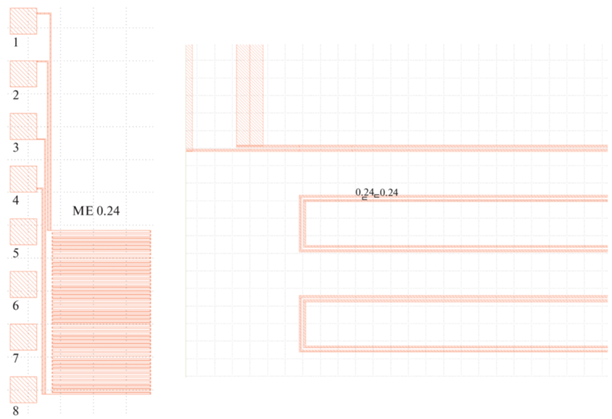
Рис. 3.
Снимок РЭМ в режиме контраста одного уровня медной металлизации со структурой Si/SiO2/TaN/Ta/Cu seed/Cu/CuSiN/пористый low-k диэлектрик.
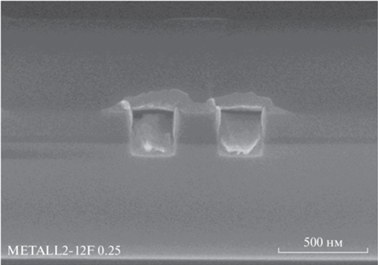
Электрофизические показания снимались на измерительном стенде на базе зондовой установки Cascade Summit 12000B-AP и измерителя полупроводниковых устройств Keysight B1500A. Перед началом измерений образцы подвергались термообработке при 350°С в течение 15 мин для удаления адсорбированной влаги.
3. ПЛАЗМОСТИМУЛИРОВАННОЕ ОСАЖДЕНИЕ ДИЭЛЕКТРИЧЕСКОГО БАРЬЕРА CuSiN ИЗ ГАЗОВОЙ ФАЗЫ
Диэлектрический барьер CuSiN перед осаждением SiCN формировался на открытой поверхности меди для предотвращения диффузии меди в диэлектрик. Для формирования указанного барьера использовалась следующая схема [30]:
– Удаления оксида меди после ХПМ в водородсодержащей плазме аммиака NH3 (T = 350°C, P = 3.9 Торр, W = 150 Вт, 15 с). Продувка в азоте N2;
– Обработка поверхности меди триметилсиланом (CH3)3SiH (T = 350°C, P = 3.2 Торр, 20 с) для образования CuSix в результате твердофазной реакции на поверхности. Продувка в гелии He;
– Экспонирование поверхности в плазме NH3 (T = 350°C, P = 3.9 Торр, W = 500 Вт, 20 с), для формирования диэлектрического слоя CuSiN. Продувка в N2.
На рис. 3 представлен снимок растрового электронного микроскопа (РЭМ) в режиме контраста одного уровня медной металлизации со структурой Si/SiO2/TaN/Ta/Cu seed/Cu/CuSiN/пористый low-k диэлектрик.
Барьер CuSiN обычно используется как дополнительный к основному диффузионному барьеру (например, SiCN, позволяя улучшить адгезию к меди и существенно увеличить срок службы при испытаниях на электромиграцию [31]), так как в своем составе имеет 80% атомов меди (атомов кремния Si 12% и атомов азота N 8%), которые способны диффундировать в low-k диэлектрик, что и наблюдается на рис. 3.
4. ПЛАЗМОСТИМУЛИРОВАННОЕ ОСАЖДЕНИЕ ДИЭЛЕКТРИЧЕСКОГО БАРЬЕРА SiCN ИЗ ГАЗОВОЙ ФАЗЫ
Формирование диэлектрического слоя SiCN включает в себя следующие этапы:
– предварительная обработка этиленом C2H4;
– формирование диэлектрического слоя SiCN на пластине за счет реакции двух потоков газов аммиака NH3 и CH3 на поверхности. Таким образом, на медных проводниках, представляющих собой параллельные линии, был сформирован диэлектрический барьер SiCN толщиной 8 нм.
На рис. 4 представлены снимки растрового электронного микроскопа в режиме контраста сформированных структур с диэлектрическим барьером SiCN.
Рис. 4.
Снимки РЭМ в режиме контраста одного уровня медной металлизации со структурой Si/SiO2/TaN/Ta/Cu seed/Cu/ CuSiN/SiCN (толщина 8 нм)/пористый low-k диэлектрик.
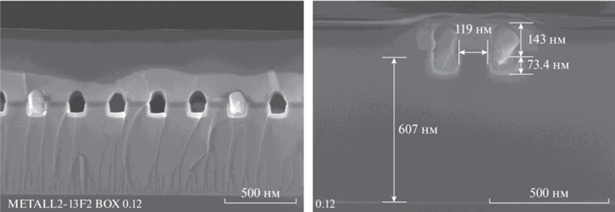
Наличие светлой области над медными проводниками, которая наблюдается на рис. 4, свидетельствует о проникновении в пористый диэлектрик меди (наблюдается атомарная диффузия меди) и необходимости оптимизации режимов формирования барьерного слоя. Отсутствие некоторых медных проводников вызвано технологическими особенностями в процессе скола для получения снимков РЭМ.
Итогом эксперимента по PECVD формированию диэлектрических барьеров является тот факт, что создание тонкой и равномерной по толщине пленки требует высокой равномерности газовых и плазменных потоков по камере и оптимизации режимов формирования барьерных слоев, описанных в научно-технической литературе. Более того, использование данного метода для формирования диэлектрических барьеров нанометровой толщины, в случае близко расположенных линий может привести к слипанию материала в области краев. В этом случае будет затруднено дальнейшее осаждение диэлектрика в сформированные траншеи.
Одним из перспективных методов для устранения указанных выше проблем может оказаться атомно-слоевое осаждение [32]. Метод ALD позволяет сформировать на поверхности любой структуры равномерную по толщине пленку на большой площади пластины, что особенно важно в узких металлических линиях. Также, данный метод, из-за особенности технологии, позволяет сформировать пленку практически любой толщины (с точностью до атомного слоя) и обладает хорошей воспроизводимостью.
5. АТОМНО-СЛОЕВОЕ ОСАЖДЕНИЕ ДИЭЛЕКТРИЧЕСКОГО БАРЬЕРА AlN
В данной части работы исследовался материал нитрид алюминия AlN в качестве диффузионного барьера между открытыми участками меди и low-k диэлектриком в субтрактивном методе. В патенте [33] материал AlN использовался в качестве диффузионного барьера между медью и low-k диэлектриком в технологии Dual Damascene. В ALD способе нанесения пленки AlN в качестве одного из прекурсоров используется плазма NH3. В статье [34] показано, что воздействие плазмы газа NH3 на SiOCH диэлектрик приводит к замещению гидрофобных Si–CH3 связей гидрофильными Si–OH связями, что, в свою очередь, приводит к изменению свойств диэлектрика (увеличение диэлектрической проницаемости за счет последующей адсорбции влаги). Однако в используемом нами подходе, барьерный слой AlN формируется до заполнения зазоров между медными проводниками, что исключает сам факт воздействия аммиачной плазмы на low-k диэлектрик.
Для нанесения диэлектрической пленки AlN на сформированные параллельные медные проводники использовалось оборудование Rоснащенное генератором сверхвысокочастотной плазмы с частотой 2.45 ГГц. Установка работала в режиме удаленной плазмы (remote plasma); температура ALD процесса составляла 350°С. Продукты реакции удалялись с помощью газа азота N2; в качестве несущего газа для генератора плазмы использовался аргон Ar. Подаваемая на генератор мощность составляла 2000 Вт. В качестве прекурсоров использовались триметилалюминий (ТМА) Al(CH3)3 и плазма аммиака NH3. Процесс нанесения диэлектрической пленки AlN методом ALD представляет собой циклическое повторение следующих последовательных этапов до достижения необходимой толщины:
– обработка пластины прекурсором ТМА в течение 0.1 с и последующая продувка азотом N2 в течение 8 с;
– обработка пластины плазмой газа NH3 в течение 14 с и последующая продувка азотом N2 в течение 4.5 с.
Процесс осаждения слоя AlN был реализован и на структуре (рис. 2), и на сплошном слое меди.
На рис. 5 в качестве примера показана измеренная карта толщины диэлектрической пленки по пластине диаметром 200 мм (целевая толщина AlN составляет 4 и 10 нм соответственно).
Рис. 5.
Карта распределения толщины нанесенной ALD методом диэлектрической пленки по кремниевой пластине с целевым значением толщины AlN 4 и 10 нм соответственно.
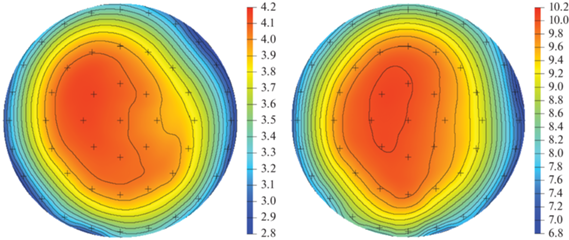
Из рис. 5 видно, что однородность нанесения диэлектрической пленки AlN по центру пластины достаточно хорошая, однако происходит нарушение равномерности по краям пластины. На данном этапе не стояла задача оптимизации процесса нанесения AlN, но, безусловно, на следующих этапах необходимо повысить однородность формирования пленки по поверхности пластины (не хуже 3%).
На структуру с медными проводниками, которые уже покрыты AlN, была нанесена пленка пористого OSG low-k диэлектрика со значением диэлектрической проницаемости 2.3 (целевое значение, измеренное на спутнике – кремниевая пластина со слоем диэлектрика толщиной 120 нм), а также пленка плотного OSG диэлектрика (без добавления структурообразующего ПАВ) со значением диэлектрической проницаемости 3.3 для формирования пластины спутника. На рис. 6 в качестве примера представлено схематичное изображение итоговой структуры с low-k диэлектриком.
На рис. 7 показана схема электрофизических измерений. Перед измерением емкости C между двумя параллельными медными проводниками проводились измерения емкости и сопротивления между контактными площадками (КП) одной линии с целью определения целостности медных проводников после нанесения диэлектрика. Емкость между проводниками измерялась на частотах 1, 10, 100 и 1000 кГц; ток утечки измерялся между контактными площадками 1 и 3.
На рис. 8 представлены снимки растрового электронного микроскопа в режиме контраста сформированных структур с диэлектрическим барьером AlN толщиной 3, 6 и 10 нм соответственно.
Рис. 8.
Снимки РЭМ в режиме контраста одного уровня медной металлизации со структурой Si/SiO2/TaN/Ta/Cu seed/Cu/AlN (толщина 3, 6 и 10 нм соответственно)/p-OSG low-k диэлектрик.
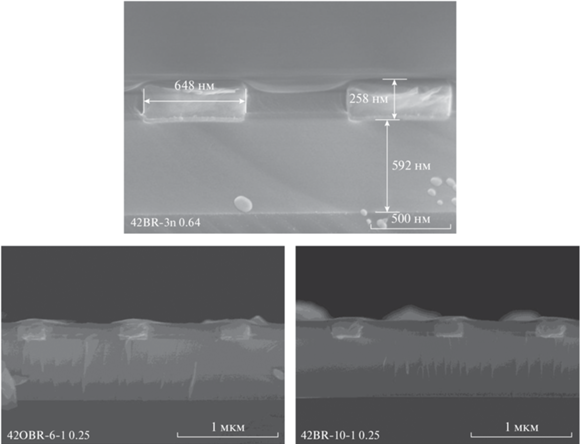
Из рис. 8 видно, что для всех образцов не наблюдается видимой атомарной диффузии меди через диэлектрический барьер AlN.
На рис. 9 приведены данные измерения емкости на нескольких частотах f между двумя близлежащими медными линиями с расстоянием между проводниками 640 нм (толщина AlN составляет 3 нм; измерения проводились при температуре образцов 250°С) для образцов с пористым p-OSG low-k диэлектриком и плотным OSG диэлектриком.
Рис. 9.
Результаты измерений емкости С на нескольких частотах f между двумя близлежащими медными линиями с расстоянием между проводниками 640 нм (толщина AlN составляет 3 нм) для образцов с пористым p-OSG low-k диэлектриком и плотным OSG.
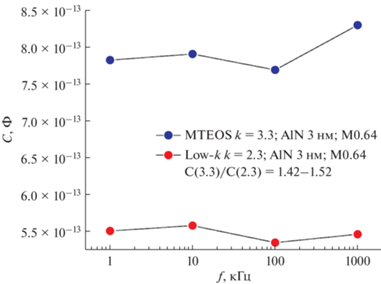
В табл. 1 приведены значения тока утечки, измеренного между контактными площадками 1 и 3, для образцов с пористым p-OSG low-k диэлектриком и плотным OSG диэлектриком (расстояние между медными линиями 640 нм; толщина AlN составляет 3 и 6 нм; измерения проводились при температуре образцов 250°С для удаления адсорбированной влаги из атмосферы.
Таблица 1.
Результаты измерения тока утечки (расстояние между медными линиями 640 нм; толщина AlN составляет 3 и 6 нм) для образцов с p-OSG low-k диэлектриком и плотным OSG диэлектриком
AlN (3 нм) | AlN (6 нм) | ||
---|---|---|---|
OSG | p-OSG | OSG | p-OSG |
ток утечки, А | ток утечки, А | ток утечки, А | ток утечки, А |
1.19E-11 | 1.55E-10 | 6.20E-12 | 5.38E-11 |
Кроме того, по результатам электрофизических измерений видно (рис. 9), что разброс емкости по частоте не превышает ∼5% относительно среднего значения в случае плотного диэлектрика OSG и не превышает ∼2% в случае пористого p-OSG low-k диэлектрика, что свидетельствует о хорошей частотной стабильности сформированных образцов.
ЗАКЛЮЧЕНИЕ
В работе экспериментально исследованы методы нанесения диффузионных барьеров в субтрактивном методе между открытыми участками меди и low-k диэлектриком Экспериментально были исследованы диэлектрические диффузионные барьеры, сформированные плазменным PECVD методом (CuSiN и SiCN) и ALD методом (AlN). Установлено, что атомно-слоевое осаждение имеет преимущества перед PECVD, так как позволяет формировать равномерные диэлектрические диффузионные барьеры нанометровой толщины. В случае с PECVD барьерами CuSiN и SiCN наблюдается существенная атомарная диффузия меди через открытые участки, что свидетельствует об отсутствии конформного покрытия металлического проводника диэлектрическим барьером. В случае диэлектрического барьера, полученного методом ALD, с толщиной слоя AlN более 3 нм на снимках растрового электронного микроскопа в режиме контраста не наблюдается видимой атомарной диффузии меди через слой пористого p‑OSG диэлектрика. Электрофизические измерения емкости в диапазоне частот 1–1000 кГц между двумя близлежащими проводниками меди с расстоянием между проводниками 640 нм (при толщине AlN 3 нм) показали, что при использовании пористого p-OSG low-k диэлектрика итоговая емкость снижается в 1.4–1.5 раза, что соответствует отношению диэлектрических постоянных использованных плотного OSG и пористого p-OSG диэлектриков. Токи утечки для этих же структур уменьшаются на порядок при использовании пористого p-OSG low-k диэлектрика. Применение тонкого барьерного слоя AlN дает существенные преимущества для предотвращения атомарной диффузии меди в структуру диэлектрика, однако необходимо провести дополнительные исследования для оценки данного ALD барьерного слоя на предотвращение диффузии ионов меди, что является наиболее актуальным для реальных структур межсоединений.
Работа выполнена при поддержке грантов РФФИ № 18-29-27024 и 18-29-27022.
Список литературы
Taiwan Semiconductor Manufacturing Company. [Online]. Available: https://www.tsmc.com/english/ dedicatedFoundry/technology/logic/l_5nm.
Taiwan Semiconductor Manufacturing Company. [Online]. Available: https://www.tsmc.com/english/ dedicatedFoundry/technology/future_rd.
International Roadmap for Devices and Systems (IRDS), 2020 Edition. [Online]. Available: https://irds.ieee.org/.
Maex K., Baklanov M.R. Shamiryan D., Lacopi F. et al. Low dielectric constant materials for microelectronics // Journal of Applied Physics. 2003. V. 93. № 11. P. 8793–8841.
Ovchinnikov I., Vishnevskiy A., Seregin D., Rezvanov A. et al. Evaluation of Mechanical Properties of Porous OSG Films by PFQNM AFM and Benchmarking with Traditional Instrumentation // Langmuir. 2020. V. 36. № 32. P. 9377–9387.
Michalak D., Blackwell J., Torres J. et al. Porosity scaling strategies for low-k films // Journal of Materials Research and Technology. 2015. V. 30. № 22. P. 3363–3385.
Lionti K., Volksen W., Magbitang T. et al. Toward successful integration of porous low-k materials: strategies addressing plasma damage // ECS Journal of Solid State Science and Technology. 2015. V. 4. № 1. P. N3071–N3083.
Jinnai B., Nozawa T., Samukawa S. Damage mechanism in low-dielectric (low-k) films during plasma processes // Journal of Vacuum Science & Technology B: Microelectronics and Nanometer Structures Processing, Measurement, and Phenomena. 2008. V. 26. № 6. P. 1926.
Frot T., Volksen W., Purushothaman S., Bruce R., Dubois G. Application of the Protection/Deprotection Strategy to the Science of Porous Materials // Advanced Materials. 2011. V. 23. № 25. P. 2828–2832.
de Marneffe J.-F., Yamaguchi T., Fujikawa M., Rezvanov A. et al. Use of a thermally degradable chemical vapor deposited polymer film for low damage plasma processing of highly porous dielectrics // Applied Electronic Materials. 2019. V. 1. № 12. P. 2602–2611.
Zhang L., Ljazouli R., Lefaucheux P., Tillocher T. et al. Damage Free Cryogenic Etching of a Porous Organosilica Ultralow-k Film // ECS Solid State Letters. 2012. V. 2. № 2. P. N5–N7.
Резванов А.А., Гущин О.П., Горнев Е.С., Красников Г.Я. и др. Изобары адсорбции фторуглеродных соединений, выбранных для криогенного плазменного травления low-k диэлектриков // Электронная техника, серия 3, микроэлектроника. 2015. Т. 1. № 157. С. 49.
Kaanta C., Bombardier S., Cote W.J., Hill W.R. et al. In Proceedings of Eighth International IEEE VLSI Multilevel Interconnection Conference (1991), pp. 144–152.
Красников Г.Я., Валеев А.С., Шелепин Н.А., Гущин О.П., Воротилов К.А., Васильев В.А., Аверкин С.Н. Способ изготовления медной многоуровневой металлизации СБИС // Патент на изобретение RU 2420827 C1, 10.06.2011.
Валеев А.С., Шишко В.А., Ранчин С.О., Воротилов К.А., Васильев В.А. Способ изготовления многоуровневой металлизации интегральных схем с пористым диэлектрическим слоем в зазорах между проводниками // Патент на изобретение RU 2459313 C1, 20.08.2012.
Валеев А.С., Красников Г.Я., Гвоздев В.А. // Патент на изобретение RUS 2486632 07.20.2011.
Валеев А.С., Красников Г.Я. Технология изготовления внутрикристальных и межкристальных межсоединений современных СБИС (обзор, концепция развития) // Микроэлектроника. 2015. Т. 44. № 3. С. 180–201.
Zhang L., de Marneffe J.-F., Heylen N., Murdoch G. et al. Damage free integration of ultralow-k dielectrics by template replacement approach // Applied Physics Letters. 2015. V. 107. № 9. P. 092901.
Khoo K., Onuki J., Nagano T., Chonan Y.H. et al. Aspect Ratio Dependence of the Resistivity of Fine Line Cu Interconnects. // Japanese Journal of Applied Physics. 2007. V. 46. № 7A. P. 4070–4073.
Gupta T. Copper Interconnect Technology. New York: Springer Science+Business Media, 2009. P. 423.
Onuki J., Khoo K., Sasajima Y., Chonan Y. et al. Reduction in resistivity of 50 nm wide Cu wire by high heating rate and short time annealing utilizing misorientation energy // Journal of Applied Physics. 2010. V. 108. № 044302. P. 1–7.
Edelstein D., Uzoh C., Cabral C.Jr., DeHaven P. et al. An optimal liner for copper damascene interconnects. In: McKerrow A.J., Shacham-Diamond Y., Zaima S., Ohba T., editors. Proceedings of the Advanced Metallization Conference 2001. 2002. P. 541–547.
Cheng Y.L., Chiu T.J., Wei B.J., Wang H.J. et al. Effect of copper barrier dielectric deposition process on characterization of copper interconnects // Journal of Vacuum Science & Technology B. 2010. V. 26. № 3. P. 567–572.
Hu C.K., Gignac L., Rosenberg R., Liniger E. et al. Reduced Cu interface diffusion by CoWP surface coating // Microelectronics and Reliability. 2003. V. 70. P. 406–411.
Witt C., Yeap K.B., Leśniewska A., Wan D. et al. Proceedings of 2018 IEEE International Interconnect Technology Conference, Santa Clara, CA, USA. 2018. P. 54–56.
Rezvanov A., Miakonkikh A., Seregin D., Vishnevskiy A. et al. Effect of terminal methyl group concentration on critical properties and plasma resistance of organosilicate low-k dielectrics // Journal of Vacuum Science & Technology A. 2020. V. 38. № 3. P. 033005.
Liu C., Qi Q., Seregin D.S., Vishnevskiy A.S. et al. Effect of terminal methyl groups concentration on properties of organosilicate glass low dielectric constant films // Japanese Journal of Applied Physics. 2018. V. 57. № 7S2. P. 07MC01.
Vishnevskiy A.S., Seregin D.S., Vorotilov K.A., Sigov A.S. et al. Effect of water content on the structural properties of porous methyl-modified silicate films // Journal of Sol-Gel Science and Technology. 2019. V. 97. № 2. P. 273–281.
Nenashev R.N., Kotova N.M., Vishnevskii A.S., Vorotilov K.A. Effect of the Brij 30 porogen on the properties of sol–gel derived thin polymethylsilsesquioxane films // Inorganic Materials. 2016. V. 52. № 9. P. 968–972.
Entire encapsulation of Cu interconnects using self – aligned CuSiN film. US Patent 7524755B2.
Chunn S., Gosset L.G., Michelon J., Girault V. et al. Cu surface treatment influence on Si adsorption properties of CuSiN self-aligned barriers for sub-65 nm technology node // Microelectronic Engineering. 2006. V. 83. № 11–12. P. 2094–2100.
Oviroh P.O., Akbarzadeh R., Pan D., Coetzee R.A.M. et al. New development of atomic layer deposition: processes, methods and applications // Science and Technology of Advanced Materials. 2019. V. 20. № 3. P. 465–496.
Padhi D., Guggilla S., Demos A.T., Kumar B. et al. Aluminum nitride barrier layer // US patent US9646876B2.
Urbanowicz A.M., Shamiryan D., Zaka A., Verdonck P. et al. Effects of He Plasma Pretreatment on Low-k Damage during Cu Surface Cleaning with NH3 Plasma // Journal of The Electrochemical Society. 2010. V. 157. № 5. H565–H573.
Дополнительные материалы отсутствуют.
Инструменты
Микроэлектроника