Российские нанотехнологии, 2020, T. 15, № 2, стр. 158-163
ЛАЗЕРНАЯ ОБРАБОТКА АЛЮМИНИЕВЫХ СПЛАВОВ ДЛЯ СОЗДАНИЯ АТМОСФЕРОСТОЙКИХ СУПЕРГИДРОФОБНЫХ ПОКРЫТИЙ
Н. Е. Сатаева 1, *, К. А. Емельяненко 1, А. Г. Домантовский 1, А. М. Емельяненко 1, Л. Б. Бойнович 1
1 Институт физической химии и электрохимии им. А.Н. Фрумкина РАН
Москва, Россия
* E-mail: sataeva.nata@yandex.ru
Поступила в редакцию 18.03.2020
После доработки 03.04.2020
Принята к публикации 03.04.2020
Аннотация
В последние годы применение лазерных нанотехнологий позволило получить ряд прорывных результатов в материаловедении для создания полифункциональных покрытий. В данной работе на основе применения лазерных методов обработки поверхности алюминиевого сплава получены полифункциональные покрытия с иерархической шероховатостью, сочетающей в себе микро- и нанотекстуру. Показано, что после хемосорбции фторсиланов разработанные покрытия обладают супергидрофобными свойствами, сохраняющимися при различных механических нагрузках и в условиях УФ-облучения. Обнаружено, что после длительных разрушающих структуру воздействий для покрытий характерно самовосстановление. Благодаря детальному подбору режимов взаимодействия лазерного пучка с материалом удалось значительно повысить скорость получения покрытий без ухудшения функциональных свойств.
ВВЕДЕНИЕ
Технологическое применение алюминиево-магниевых сплавов в различных областях постоянно растет. В настоящее время такие сплавы активно используются в химической промышленности для изготовления сосудов под давлением, при производстве водяных конденсаторов, теплообменников, водоохладителей и морозильных камер. При этом в условиях эксплуатации они подвергаются интенсивному абразивному износу, коррозии, покрываются накипью, маслом, отложениями солей и смол, окисляются и т.д. Поэтому необходимо придавать поверхности материалов дополнительные функциональные свойства, которые позволяют ей противостоять действию отмеченных выше факторов. Один из перспективных способов увеличения срока службы материалов на основе алюминиевых сплавов заключается в придании их поверхности супергидрофобных свойств. Супергидрофобность позволяет значительно улучшить устойчивость к коррозии [1–5], биологическому обрастанию [6–9] отложениям накипи [10] и снизить гидродинамическое сопротивление потоку [11, 12]. Однако основные недостатки супергидрофобных покрытий связаны, как правило, с низкой износостойкостью [13] и слабой химической стабильностью [14] слоя гидрофобного агента поверх текстурированных слоев. В [4, 15] показано, что лазерные нанотехнологии позволяют решить проблему стойкости супергидрофобных покрытий. Так, комбинация лазерного химического модифицирования с лазерным текстурированием и последующей хемосорбцией фторированного гидрофобного агента является перспективным способом повысить абразивную износостойкость при одновременной хорошей химической стойкости покрытий в различных условиях эксплуатации. В проведенном исследовании использованы лазерные методы создания нано- и микротекстурированных покрытий на поверхности алюминиевых сплавов. Показано, что соответствующим подбором параметров и режимов лазерной обработки можно существенно повысить производительность лазерных методов обработки материалов без потери высокой механической и химической стойкости.
ЭКСПЕРИМЕНТАЛЬНАЯ ЧАСТЬ
Образцы для исследования представляли собой пластинки из алюминиево-магниевого сплава, содержащего 95.55 мас. % Al и 2.9 мас. % Mg, а также Fe, Si, Zn, Ti, Cu и Cr.
Для того чтобы создать на поверхности образцов текстуру с многомодальной шероховатостью, необходимой для достижения супергидрофобного состояния поверхности, использовали лазерный комплекс Аргент-М (ООО “ЦЛТ”, Россия) на базе инфракрасного иттербиевого волоконного лазера с длиной волны 1.064 мкм и пиковой мощностью до 0.95 мДж в TEM00-моде. Для получения покрытий проводили обработку поверхности лазерными импульсами длительностью 200 нс и частотой 20 кГц при скоростях линейного перемещения луча 400 мм/с с шагом лазерного сканирования поверхности 7 мкм. Процедуру лазерного текстурирования проводили при комнатной температуре (20–25°С), атмосферном давлении и естественной влажности (40–50%). Управление движением лазерного луча осуществляли компьютерной программой с помощью двухосевой отклоняющей системы MS10 (Raylase, Германия). В зоне воздействия лазерного луча происходит нагрев до высокой температуры, плавление и испарение материала. Отдельные атомы и наноразмерные капли обрабатываемого материала агрегируют в факеле абляции, химически взаимодействуют с атмосферой и осаждаются вокруг зоны воздействия в виде микро- и наночастиц. При этом состав и свойства поверхностного слоя в значительной степени определяются как количеством поглощенной энергии, так и режимами нагрева/охлаждения поверхностного слоя. Следовательно, для предлагаемых режимов лазерной обработки ожидается отличие свойств покрытий от полученных ранее [4, 15].
Текстурирование поверхности алюминиевого сплава, обладающего высокой поверхностной энергией, при указанных выше параметрах приводит к многомодальной шероховатости и полному смачиванию поверхности. Нанесение на полученную поверхность слоя молекул вещества с низкой поверхностной энергией – гидрофобизатора – вызывает переход смачивания от супергидрофильного к супергидрофобному состоянию.
В данной работе для гидрофобизации использовали метокси-{3-[(2,2,3,3,4,4,5,5,6,6,7,7,8,8,8-пентадекафторооктил)-окси]пропил}-силан, хемосорбирующийся на поверхность алюминиевого сплава за счет взаимодействия метоксигруппы молекулы гидрофобизатора с поверхностными гидроксильными группами. Для обогащения поверхности материала после лазерной обработки такими группами образцы обрабатывали УФ-излучением в присутствии плазмы озона в течение 60 мин с применением озонатора Bioforce Nanosciences (модель UV.PC.220). Согласно ранее проведенным исследованиям и данным [16, 17], при такой обработке на поверхности формируются хемосорбционно-активные центры в виде гидроксильных или карбоксильных поверхностных групп. Далее образцы помещали в герметичный сосуд с насыщенными парами гидрофобизатора, при 105°С выдерживали в течение 60 мин для хемосорбции молекул гидрофобизатора на поверхностных адсорбционных центрах и для сшивки концевых силанольных групп с образованием силоксановой связи между соседними адсорбированными молекулами гидрофобизатора [14].
После гидрофобизации образцы подвергали дополнительной термообработке в воздушной печи при 130°С в течение 60 мин для завершения процесса формирования силоксановой сетки в адсорбированном слое на поверхности текстурированных образцов.
МЕТОДЫ ИЗМЕРЕНИЯ
Морфологию поверхности образцов изучали с помощью растрового электронного микроскопа Supra 40 VP (Carl Zeiss, Германия). РЭМ-изображения получены при ускоряющем напряжении 2–5 кВ.
Углы смачивания измеряли с использованием разработанной ранее установки, основанной на цифровой обработке видеоизображений сидящих капель [18, 19]. Для измерения углов скатывания каплю помещали на образец, после чего держатель подложки плавно наклоняли до тех пор, пока капля не скатывалась с поверхности. Углы смачивания и скатывания определяли для капель объемом 15 мкл в 10 различных местах на поверхности каждого образца.
Анализ стойкости к абразивным нагрузкам выполняли с использованием методики, разработанной на основе истирания в колеблющемся слое песка, которая подробно описана в предыдущих исследованиях [15].
Прочность покрытий по отношению к механическим напряжениям, связанным с обледенением, оценивали путем анализа изменений углов смачивания и скатывания при многочисленных циклах кристаллизации/плавления по методике, описанной в [4].
РЕЗУЛЬТАТЫ И ИХ ОБСУЖДЕНИЕ
Как известно, обработка поверхности лазером [4, 20–23] имеет несколько важных преимуществ по сравнению со многими другими методами текстурирования поверхности, поскольку взаимодействие лазерного излучения с поверхностью позволяет контролируемо изменять не только морфологию, но и химический и фазовый составы поверхностного слоя материала. А именно, взаимодействие излучения высокой мощности с конденсированными средами в присутствии атмосферных газов сопровождается химическими реакциями. Поверхностные соединения, образующиеся при обработке поверхности, существенно влияют на физико-химические свойства поверхностных слоев. Кроме того, быстрый локальный нагрев и быстрое охлаждение упрочняют поверхность за счет уменьшения размеров зерен, а диффузионное спекание нагретой лазером поверхности с осаждающимися наночастицами, сформированными в плазме лазерного факела, обеспечивает высокую механическую стойкость наноэлементов текстуры [21]. Многократная лазерная обработка с соответствующими параметрами приводит к улучшению желаемых функциональных свойств [4]. Влияние многократной обработки на свойства поверхности исследовано в [15], где было показано значительное улучшение механической стойкости при семи- и десятикратной обработке. Однако описанный в [4, 15] способ текстурирования поверхности требует значительного количества времени, скорость обработки поверхности составляет от 0.1 до 1 мм2/с.
После анализа физико-химических условий образования необходимой морфологии, химического и фазового составов провели целенаправленный поиск однопроходных режимов обработки поверхности алюминиевых сплавов, позволяющих получать поверхности с многомодальной шероховатостью значительно быстрее представленных ранее [4, 15]. Был исследован широкий спектр режимов обработки, различающихся скоростью и плотностью линий линейного перемещения пучка лазера. На основании данных о механической стойкости покрытий, полученных с помощью лазерной обработки, найден режим, позволяющий быстро получать покрытия с высокой механической стойкостью. Данный режим характеризуется скоростью линейного перемещения пучка лазера 400 мм/с и шагом сканирования 150 линий/мм (далее обозначен как 400/150).
Морфология образца, полученного с использованием соответствующего режима, была детально изучена, РЭМ-изображения поверхностей образцов при различных увеличениях представлены на рис. 1. Хорошо видно, что для полученной поверхности характерна многомодальная шероховатость. На образце образуется текстура, содержащая чередующиеся гребни и впадины, декорированные по всей поверхности микро- и наноэлементами с малыми радиусами кривизны, обеспечивающими сохранение супергидрофобного состояния на поверхности впадин рельефа при абразивном удалении текстурирующих частиц с гребней поверхности.
Рис. 1.
РЭМ-изображения, показывающие микро- (а) и нано- (б) размерные особенности текстуры поверхностей образцов, текстурированных методом наносекундной лазерной обработки с использованием режима 400/150.
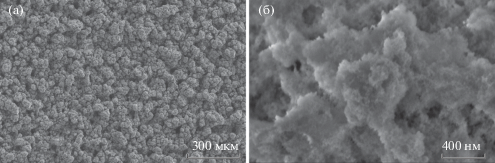
Одним из наиболее важных функциональных свойств материалов, используемых для теплообменников и конденсаторов пара, является способность противостоять абразивному износу, возникающему при воздействии твердых и жидких частиц. Как правило, из-за высокой скорости потоков жидкости и пара в устройстве передача поверхности кинетической энергии ударяющихся частиц может привести к значительному повреждению текстуры, что вызывает потерю супергидрофобного состояния. Поэтому, чтобы выяснить устойчивость покрытия, изготовленного с использованием режима 400/150, было проведено исследование его абразивной стойкости на основе испытания с колеблющимся песком. Количественно стойкость покрытия к абразивному износу характеризовалась изменением углов смачивания и скатывания (рис. 2). Полученные данные показывают, что покрытие выдерживает 10 ч абразивной нагрузки с сохранением высокогидрофобного состояния и частичным гетерогенным режимом смачивания, после 10-часового испытания углы смачивания и скатывания равны 153° и 68° соответственно. В то же время заметное уменьшение угла смачивания и увеличение угла скатывания указывают не только на частичное удаление гидрофобного агента с поверхности, но и на некоторое удаление нанотекстуры покрытия.
Интересно отметить, что важным свойством полученного покрытия является способность к самовосстановлению. Исследования показали, что после прекращения абразивной нагрузки происходит постепенное снижение углов скатывания и рост углов смачивания, что соответствует улучшению параметров супергидрофобного состояния (рис. 3).
Такое самовосстановление становится возможным благодаря повторной адсорбции молекул гидрофобного агента на поврежденные участки поверхности, где они были удалены в процессе абразивного воздействия. Основным источником молекул для такой адсорбции является фтороксисилан, капиллярно капсулированный в нанопорах в процессе изготовления супергидрофобного покрытия. Рост угла смачивания до значений ~158° и падение углов скатывания до ~30° указывают на значительное восстановление гетерогенного режима смачивания, что оказывается возможным лишь при слабом удалении наночастиц с поверхности покрытия при механическом испытании. Таким образом, разработанное покрытие демонстрирует высокую стойкость нанотекстуры к абразивным нагрузкам.
Другим чрезвычайно распространенным типом нагрузки, стойкость к которому необходима для длительной эксплуатации в открытых атмосферных условиях, являются механические напряжения, возникающие на поверхности материала вблизи зоны трехфазного контакта вода–воздух–твердое тело при кристаллизации воды. Результаты исследования эволюции смачивания для образцов, обработанных режимом 400/150, для 100 циклов кристаллизации/плавления представлены на рис. 4. Представленные данные указывают на сохранение супергидрофобного состояния даже после 100 циклов кристаллизации/плавления, при этом углы смачивания и скатывания равны соответственно 169.5° ± 1° и 4.9° ± 1.2°.
Еще одним важным фактором, который необходимо учитывать при разработке материалов, ориентированных на работу в открытых атмосферных условиях, является стойкость к воздействию УФ-излучения, присутствующего в солнечном спектре.
Гидрофобный агент связывается с текстурированной поверхностью алюминиевого сплава, образуя связи AlO–SiR, где R – фторуглеродный радикал. Воздействие ультрафиолета может приводить к разрыву связи AlO–SiR с образованием Al–OН. Находящаяся на поверхности гидроксильная группа легко гидратируется, что способствует значительному улучшению смачиваемости материала, поэтому появление на поверхности таких групп приводит к существенной деградации супергидрофобного состояния.
По данным [24] основная доля УФ-излучения, достигающего поверхности Земли, приходится на интервал длин волн 300–380 нм. Для указанного диапазона среднегодовая доза УФ-облучения на территории Москвы составляет 144 МДж/м2.
Для исследования фотохимической стойкости использовали сборку светодиодов с длиной волны 365 нм, соответствующей пику УФ-радиации в упомянутой области спектра, и итоговой мощностью излучения на образце 10 Вт/см2. Таким образом, с помощью используемого источника УФ-излучения годовая доза облучения Земли достигается за 24 мин эксперимента.
Испытания на стойкость к УФ-облучению проводили в течение четырех часов, что соответствует 10 годам облучения в открытых атмосферных условиях. Из полученных данных (рис. 5) следует, что даже при длительном воздействии УФ-излучения, эквивалентном 10 годам атмосферной эксплуатации, деградация супергидрофобного состояния незначительна: углы смачивания и скатывания достигают значений соответственно 169.1° и 1.65°. Это свидетельствует о высокой стойкости полученных покрытий к воздействию ультрафиолета, а значит, и о высокой химической стойкости.
ЗАКЛЮЧЕНИЕ
Для успешного решения проблемы создания долговечных супергидрофобных покрытий на алюминиевых сплавах использована разработанная ранее [4] стратегия, сочетающая лазерную химическую модификацию с лазерным текстурированием и последующей хемосорбцией фторированного гидрофобного агента. Анализ корреляции между химическим составом и параметрами текстуры, полученными для различных режимов лазерной обработки, и износостойкостью покрытий позволил выбрать оптимальный режим, сочетающий высокую скорость изготовления покрытий с их механической и химической стойкостью. Оптимизация режимов лазерной обработки поверхности позволила более чем вдвое увеличить скорость обработки поверхности по сравнению с режимами, представленными в литературе, без существенного снижения функциональных свойств и долговечности, что повышает привлекательность разработанных покрытий для промышленного применения.
Показано, что особая иерархическая морфология высокопористого поверхностного слоя способствует устойчивости к различным механическим нагрузкам и придает покрытиям способность к самовосстановлению. На такую стойкость однозначно указали данные проведенных экспериментов с абразивным износом покрытий как в условиях колеблющегося песка, так и в циклах кристаллизации/плавления воды, контактирующей с покрытием. Также высокая стойкость к воздействию УФ-облучения свидетельствует о чрезвычайно высокой химической стабильности покрытий.
Работа выполнена при финансовой поддержке Российского фонда фундаментальных исследований (грант № 19-29-13011) и Министерства науки и высшего образования Российской Федерации.
Список литературы
Montemor M.F. // Surf. Coat. Technol. 2014. V. 258. P. 17.
Boinovich L.B., Emelyanenko A.M., Modestov A.D. et al. // Mendeleev Commun. 2017. V. 27. P. 254.
Drelich J., Marmur A. // Surf. Innovations. 2014. V. 2. P. 211.
Boinovich L.B., Modin E.B., Sayfutdinova A.R. et al. // ACS Nano. 2017. V. 11. P. 10113.
Zhang L., Zhang J.Q., Liu R.P. // Surf. Innovations. 2016. V. 4. P. 51.
Vanithakumari S.C., Yadavalli P., George R.P., Mudali U.M.K. // Surf. Innovations. 2015. V. 3. P. 115.
Genzer J., Efimenko K. // Biofouling. 2006. V. 22. P. 339−360.
Salta M., Wharton J.A., Stoodley P. et al. // Philos. Trans. R. Soc. 2010. V. 368. P. 4729.
Gule N.P., Begum N.M., Klumperman B. // Crit. Rev. Environ. Sci. Technol. 2016. V. 46. P. 535.
Li H., Yu S.R., Han X.X., Zhao Y.A. // Colloids Surf. A. 2016. V. 503. P. 43.
Golovin K.B., Gose J.W., Perlin M. et al. // Philos. Trans. R. Soc. 2016. V. 374. № 20160189.
Lee C., Choi C.H., Kim C.J. // Exp. Fluids. 2016. V. 57. № 176.
Milionis A., Loth E., Bayer I.S. // Adv. Colloid Interface Sci. 2016. V. 229. P. 57.
Boinovich L.B., Emelyanenko A.M. // Adv. Colloid Interface Sci. 2012. V. 179. P. 133.
Boinovich L.B., Emelyanenko K.A., Domantovsky A.G., Emelyanenko A.M. // Langmuir. 2018. V. 34. P. 7059.
Boinovich L.B., Emelyanenko A.M. // Colloids Surf. A. 2015. V. 481. P. 167.
Moradi S., Kamal S., Hatzikiriakos S.G. // Surf. Innovations. 2015. V. 3. P. 151.
Emelyanenko A.M., Boinovich L.B. // Colloids Surf. A. 2001. V.189. P. 197.
Kray D., Fell A., Hopman S. et al. // Appl. Phys. A: Mater. Sci. Process. 2008. V. 93. P. 99.
Emelyanenko A.M., Boinovich L.B. // Instrum. Exp. Tech. 2002. V. 45. P. 44.
Kusinski J., Kac S., Kopia A. et al. // Bull. Pol. Acad. Sci.: Tech. Sci. 2012. V. 60. P. 711.
Kray D., Fell A., Hopman S. et al. // Appl. Phys. A: Mater. Sci. Process. 2008. V. 93. P. 99.
Moradi S., Kamal S., Hatzikiriakos S.G. // Surf. Innovations. 2015. V. 3. P. 151.
Abakumova G.M., Gorbarenko E.V., Nezval E.I., Shilovtseva O.A. // Int. J. Remote Sensing. 2014. V. 29. P. 2629.
Дополнительные материалы отсутствуют.
Инструменты
Российские нанотехнологии